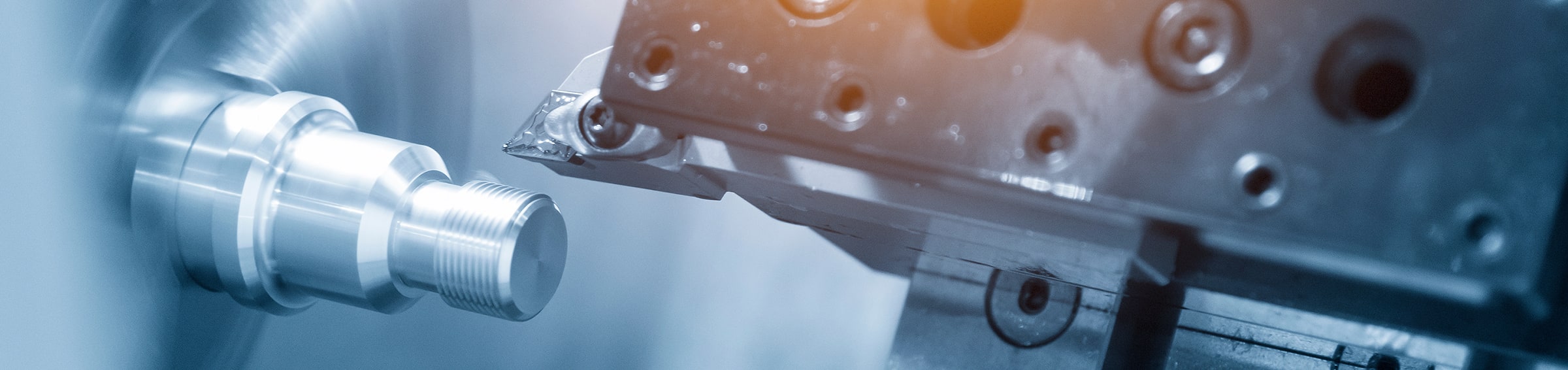
コラム column
プロが伝授!鉄製品製造におけるフライス加工の種類とその鍵点
プロが伝授!鉄製品製造におけるフライス加工の種類とその鍵点について、今回は詳しく解説します。鉄製品の製造において、フライス加工は非常に重要な工程の一つです。この記事では、様々なフライス加工の種類やその鍵点についてご紹介します。鉄製品の製造に携わる皆さんにとって、フライス加工がどのように進化してきたのか、そしてどのように最大限の効果を発揮するのか、そのポイントを知ることが重要です。さあ、一緒に深掘りしていきましょう。
1. フライス加工入門
1-1. フライス加工とは?
フライス加工は、鉄製品製造において欠かせない技術の一つです。この加工法の鍵点は、精密な形状を実現するための多様な種類と方法にあります。その中でも、特に代表的なのは、平面加工、側面加工、溝加工、ギア加工などです。例えば、平面加工では、製品の表面を平滑にするために用いられ、高い平面度が求められる部品製造に不可欠です。側面加工では、製品の側面を削ることで精度を出し、溝加工では、部品に必要な溝を加工することができます。ギア加工は、歯車などの精密部品を作る際に用いられる技術です。これらの加工方法を駆使することで、様々な形状の鉄製品を精密に製造することが可能になります。
フライス加工の種類を理解し、適切に選択することは、製品の品質を左右する重要な要素です。日本においても、この加工技術は広く利用されており、高い技術力が求められます。最終的に、適切なフライス加工を選択し、適用することで、求められる品質と精度の高い鉄製品を製造することが、製造業の大きな目標となっています。
1-2. 鉄製品とフライス加工の関係
鉄製品製造において、フライス加工は欠かせない技術の一つです。この加工法は、鉄製品の精度向上や形状の複雑化に寄与し、多種多様な製品の生産に不可欠です。主に、面取り、溝切り、形状加工などの種類がありますが、それぞれの適用には鍵点が存在します。
例えば、面取り加工では、製品のエッジを滑らかにすることで、取扱い安全性や組み立て易さを向上させます。溝切り加工では、部品同士の結合部や、潤滑油の通路など、精密な寸法制御が求められる場合に重宝します。複雑な形状加工では、コンピュータ数値制御(CNC)技術を駆使し、高い精度と複雑な形状を実現しています。
要するに、フライス加工の種類とそれぞれの鍵点を理解することは、鉄製品製造における品質向上と生産効率の向上に直結します。技術の進歩と共に、より高度なフライス加工方法が開発されており、これらを適切に選択し活用することが、競争力のある鉄製品を生み出すための鍵となるのです。
1-3. 金属加工におけるフライス加工の重要性
フライス加工は、金属製品製造において不可欠な工程の一つです。その重要性は、鉄製品の精密な形状や複雑なデザインを実現するために必要不可欠だからです。この加工方法では、カッターを回転させて材料を削ることにより、鉄製品に所望の形を与えます。特に、日本においては、高品質な鉄製品を製造するための技術として、長年にわたり研究され、発展してきました。
フライス加工の種類には大きく分けて、平面加工、側面加工、溝加工などがあります。例えば、平面加工は、鉄板の表面を平滑に仕上げるために使用され、側面加工は、製品の側面を整形するのに用いられます。溝加工は、鉄製品に溝や穴を開ける際に必要とされます。これらの加工方法を適切に選択し、組み合わせることで、複雑な形状や高い精度を要求される鉄製品を製作することが可能になります。
重要な点は、これらのフライス加工を行う際に、加工機械の精度やカッターの選定、さらには加工条件の設定が鍵となります。日本では、こうした技術の向上により、世界でも類を見ない高品質な鉄製品を生み出しています。
結論として、フライス加工は鉄製品製造における重要な工程であり、その種類と適切な技術の選択が高品質な製品を実現する上で極めて重要です。日本における高度な技術力は、世界的にも高く評価されており、これからもその技術の発展とともに、より精密で複雑な鉄製品が生み出されていくことでしょう。
1-4. 初心者が知るべきフライス加工の基礎
フライス加工は、鉄製品製造において欠かせない技術の一つです。この技術にはいくつかの種類があり、それぞれに重要なポイントが存在します。まず、フライス加工の成功の鍵は、適切な種類の選択にあります。例えば、平面加工には平面フライスが、輪郭加工には端面フライスが最適です。加工品の精度や仕上がりは、使用するフライス加工の種類によって大きく左右されるため、製品の要件に応じて最も適切なものを選択する必要があります。
具体的な例として、精密な鉄製部品を製造する場合、球面フライスや角フライスなど、細かい加工が可能な種類を選ぶことが重要です。これらは、複雑な形状や細部の加工に適しており、高い精度を要求される製品製造に不可欠です。
結論として、フライス加工は鉄製品製造の効率と品質を向上させるための重要な技術です。その多様な種類から最適なものを選択し、製品の要件に合わせた加工を行うことが、高品質な製品製造の鍵となります。適切なフライス加工の選択と適用は、製造業者にとって欠かせない知識と技術です。
2. 鉄のフライス加工の種類
2-1. 平面加工
平面加工は、鉄製品製造において汎用性が高いフライス加工の一種です。この技術は、製品の表面を均一で滑らかな状態に仕上げることが目的であり、精密な部品製造には欠かせない工程とされています。その成功の鍵点には、適切な刃の選択と加工速度の調整があります。
例えば、鉄道の車輪や機械部品など、耐久性と精度が求められる製品において、平面加工はその基盤となる工程です。特に、硬い材料を加工する際には、強度の高いカッターを選び、加工にかかる時間と精度のバランスを考える必要があります。
日本では、高度な技術力を要するこのフライス加工が多くの製造業で採用されており、製品の品質向上に大きく貢献しています。最終的に、適切なフライス加工を施すことで、耐久性に優れ、より精密な鉄製品を製造することが可能となります。このように、平面加工は鉄製品製造の不可欠な部分であり、その技術の向上が求められています。
2-2. 形状加工
フライス加工は、鉄製品製造における重要な技術の一つです。これは、精密な形状やサイズの部品を作るために不可欠であり、その種類と適用する鍵点を理解することが、高品質な製品を生産する上で極めて重要です。主に、平面加工、溝加工、輪郭加工などの種類があります。たとえば、平面加工は平らな面を作るのに用いられ、溝加工は部品の溝やキー溝を作るのに適しています。輪郭加工では、複雑な形状や曲線を加工することができます。
日本における鉄製品の製造では、これらのフライス加工技術の選択が製品の品質を大きく左右します。例えば、高精度を要求される自動車部品や機械部品を製造する際には、適切なフライス加工方法の選択が不可欠です。また、加工する鉄材料の種類によっても、最適な加工方法が異なります。このように、フライス加工の種類とその適用の鍵点を正確に把握し、適切な技術を選択することが、高品質な鉄製品製造には欠かせません。
結論として、鉄製品製造におけるフライス加工は、多様な種類があり、それぞれの技術が製品の品質に大きな影響を与えます。製造工程において正しい加工方法を選択することが、効率的かつ高品質な製品生産に繋がるのです。
2-3. 穴あけ加工
鉄製品製造におけるフライス加工は、精密さと効率性を追求する上で欠かせない工程です。この加工方法は、鉄の表面を削り取りながら形状を整えることに特化しており、製品の品質と生産性を大きく左右します。日本において、この技術は特に自動車産業や建築材料の製造において重要な役割を果たしています。
フライス加工の種類は多岐にわたりますが、特に平面加工、側面加工、溝加工が基本とされる三つの主要な方法です。平面加工は、製品の表面を平らにするために使用され、側面加工は製品の側面の形状を整えるのに役立ちます。溝加工は、ネジの溝や装飾的な溝を製品に加える時に使用されます。これらの加工方法は、それぞれ特有の刃物やフライス盤を使用し、鉄製品の精度と美しさを極限まで高めることができます。
例えば、自動車のエンジン部品では、高い精度が求められるため、主に平面加工と側面加工が用いられ、部品の形状とサイズが厳密に制御されます。また、建築材料では、溝加工によって特殊な形状の溝を加えることで、材料の強度を増すと同時に、見た目の美しさも追求されます。
結論として、鉄製品製造におけるフライス加工の種類とその選択は、製品の用途と求められる品質によって大きく左右されます。日本におけるこの技術の精緻さは、世界でも高い評価を受けており、製品の品質向上と生産効率の向上に寄与しています。
2-4. 特殊フライス加工
フライス加工は、鉄製品製造における最も基本的かつ重要な工程の一つであり、その種類と適用の鍵点を理解することが品質向上に直結します。特に、特殊フライス加工はその精度と効率性から、多様な製品の生産に不可欠です。
この加工法の主な鍵点は、使用する刃の種類と加工する材料の特性に適した設定を行うことです。例えば、鉄製品には硬質の刃を用い、精密な加工を可能にするため、刃の速度や材料への当て方を細かく調整します。具体的な例として、高速度鋼や超硬合金を使ったエンドミルが挙げられ、これらは難加工材料に対しても高い加工精度を実現します。
また、特殊フライス加工においては、加工する表面の仕上げ具合を重視し、そのためには正確な工具の選定が必要不可欠です。例を挙げると、航空機部品や精密機械部品の製造では、微細な表面粗さを実現するために、特別に設計されたフライスカッターが使用されます。
結論として、特殊フライス加工は鉄製品製造において、その精度と効率性から非常に重要な役割を担います。適切な工具の選定と加工条件の設定により、高品質な製品の生産が可能となります。これらの理解と適用が、製品品質向上の鍵となります。
3. フライス加工の基本的な工程
3-1. 材料の選定
鉄製品製造におけるフライス加工は、その精密さと多様性から多くの産業で重宝されています。フライス加工の種類としては、面取り、溝切り、プロファイリングなどがあり、製品の用途や求められる精度に応じて適切な加工方法が選ばれます。特に日本では、高度な技術と厳しい品質管理基準により、フライス加工技術が高いレベルで展開されています。
例えば、自動車産業では、エンジン部品やシャシーの加工にフライス加工を用いることが多いです。これらの部品は、安全性と性能に直接関わるため、極めて高い精度が要求され、フライス加工の精度が製品の品質を左右する重要な要素となります。
また、電子機器の製造においても、微細なパーツの加工にフライス加工が使われることがあります。ここでは、特に小型で精密な部品を扱うため、高度な技術力と加工技術が求められ、日本のような技術力のある国でのみ可能な加工が行われている例も少なくありません。
これらの例からも分かるように、フライス加工は鉄製品製造において不可欠な技術であり、その種類や適用範囲の広さが鍵点となります。日本では、特に精度と技術力が求められる分野でのフライス加工が高く評価されており、これからもその需要は高まることが予想されます。
3-2. 加工機械の設定
フライス加工は、鉄製品製造において重要な技術です。この加工法は、鉄の表面を削ることで、製品の形を整えたり、精密な部品を作成したりするのに役立ちます。主に、平面加工、溝加工、輪郭加工の3つの種類があります。
まず、平面加工は、製品の表面を平らにするのに使われます。これにより、部品の安定した取り付けが可能になるのです。次に、溝加工は、鉄製品に溝や穴を開けるのに使用されます。この加工法は、組み立てに必要な部品の固定や、潤滑油の流れを作る際に重要です。最後に、輪郭加工は、製品の外形を削り出す加工で、複雑な形状の部品製造に欠かせません。
これらのフライス加工の種類を理解し、適切に選択することが、鉄製品製造の成功の鍵を握ります。例えば、日本の自動車産業では、高品質なエンジン部品を製造するために、これらの加工技術が活用されています。正確な加工が要求されるため、適切な加工方法の選択と精密な機械設定が不可欠です。
このように、フライス加工の各種類を適切に利用することで、高品質な鉄製品の製造が可能となります。鉄製品製造におけるフライス加工の理解と活用は、製品の品質を向上させ、製造業の発展に貢献する重要な要素です。
3-3. カッティングツールの選択
フライス加工は、鉄製品の製造において不可欠な技術です。この加工方法には様々な種類があり、それぞれに適したカッティングツールの選択が成功の鍵を握ります。日本においても、厳しい品質基準を満たすためには、この技術の理解が必要不可欠です。
まず、フライス加工の基本として、端面加工や側面加工などが挙げられます。端面加工では、材料の表面を平滑にするために使用され、側面加工では、材料の側面を整形するのに適しています。これらの加工には、それぞれ異なる形状のカッティングツールが必要であり、正確な選択が必須です。
例えば、側面加工には、平らな面を作り出すために、大きな直径のエンドミルが選ばれることが多いです。一方、複雑な形状や細かいディテールが必要な場合は、小さな径のボールエンドミルが適しています。これらのツールを適切に選択し、加工条件を最適化することで、高品質な鉄製品の製造が可能になります。
結局のところ、フライス加工の成功はカッティングツールの選択に大きく依存します。適切なツール選択により、効率的かつ高精度な加工が実現し、日本の鉄製品製造業界の競争力を高めることができます。
3-4. 加工パラメータの決定
フライス加工は、鉄製品製造の際に不可欠な工程であり、その種類と適切なパラメータの選択が製品品質に大きく影響します。フライス加工の種類には、平面加工、側面加工、溝加工などがあり、それぞれに最適な加工条件が存在します。例えば、平面加工では、広い面を効率良く削るためには大きな切削幅と低い進行速度が推奨されますが、溝加工では、精密さが求められるため、より細かい切削幅と高い進行速度が必要となります。
鉄製品のフライス加工において最も重要なのは、加工する材料の特性と目的に合った加工パラメータを選定することです。この選定により、加工時間、コスト、そして最終的な製品の品質が大きく左右されます。日本においては、高度な技術と精密な加工が求められるため、フライス加工のパラメータ選定は特に慎重に行われます。
合理的な加工パラメータの選定は、長期的に見て生産性の向上、コスト削減、そして製品品質の向上に直接つながります。したがって、フライス加工におけるパラメータの選定は、鉄製品製造における成功の鍵と言えるでしょう。
4. 初心者が押さえるべき加工技術の基礎知識
4-1. ツールの基本的な特性
フライス加工は、鉄製品製造において欠かせない技術です。この技術の鍵点を理解することで、製品の品質と製造効率が大幅に改善されます。フライス加工は、主に平面、溝、歯車などの加工に用いられ、その種類には平面フライス加工、端面フライス加工、形状フライス加工などがあります。例えば、平面フライス加工は、製品の表面を平滑にするのに適しています。一方、端面フライス加工は、製品の端の部分を加工するのに用いられ、精度の高い仕上がりが求められる場合に効果的です。さらに、形状フライス加工は、複雑な形状や細部の加工に適しており、高度な技術を要します。これらの加工方法を適切に選択し、適用することで、鉄製品の品質向上と生産効率の向上が図れます。結論として、フライス加工の種類とその特徴を正確に理解し、製品ごとに最適な加工方法を選択することが、鉄製品製造における品質と効率の向上に不可欠であることがわかります。
4-2. 切削速度とは
鉄製品製造においてフライス加工の種類とその鍵点を理解することは非常に重要です。フライス加工は、鉄をはじめとする金属を加工する上で広く利用されている技術です。これには、平面加工、溝加工、歯車加工など様々な種類があります。各種類の加工方法は、製品の用途や求められる精度によって選ばれます。
たとえば、平面加工は、一般的に鉄製品の表面を平らにするために使用されます。これは、機械部品の組み立てにおいて正確な平面が求められる場合に特に重要です。一方、溝加工は、部品に特定の形状の溝を加工するために用いられ、歯車加工は、歯車などの精密部品を製造する際に不可欠です。
フライス加工の鍵点としては、加工する材料の性質を正確に理解し、適切な工具を選択することが挙げられます。また、加工速度や送り速度といった条件も、加工精度や効率に大きく影響します。例えば、加工速度が適切でないと、鉄製品の表面が荒れたり、工具が早く摩耗したりする可能性があります。
結論として、フライス加工は鉄製品製造において多様な加工方法を提供し、製品の用途や求められる精度に応じて、適切な加工方法の選択が必要です。加工する材料の性質を理解し、適切な工具の選択と加工条件を最適化することが、高品質な鉄製品を製造する上での鍵となります。
4-3. 送り速度の重要性
フライス加工において、鉄製品の品質を左右する重要な要素の一つが送り速度である。送り速度が適切でないと、加工される鉄製品の表面に傷がついたり、精度が落ちたりする可能性がある。日本においても、精密な鉄製品の製造には、この送り速度の設定が鍵となる。
例えば、日本の自動車産業では、エンジン部品や車体の一部に使用される鉄製品の品質が非常に重視される。これらの部品の加工にフライス加工が用いられる際、送り速度は部品の仕上がり品質に直接影響を与える。適切な速度で加工することにより、部品の表面が滑らかになり、寸法精度も高まる。その結果、自動車の性能と耐久性が向上し、最終的な製品の品質に貢献する。
しかし、送り速度を設定する際には、加工する鉄製品の種類や形状、使用するフライス加工機の特性など、多くの要因を考慮する必要がある。適切な送り速度の決定は、経験と知識が必要とされる専門的な作業である。
このように、フライス加工における送り速度の適切な設定は、鉄製品製造の品質を保つ上で非常に重要である。特に、高品質な鉄製品が求められる日本においては、送り速度の最適化が一層重視されている。そのため、プロの技術者が常に送り速度の最適化に努めているのである。
4-4. 切りくずの管理
フライス加工は、鉄製品の製造において欠かせない技術であり、その種類と適切な切りくずの管理は製品の品質を左右します。フライス加工には、平面加工、溝加工、輪郭加工など多様な種類があり、それぞれに最適な切りくずの管理方法が存在します。例えば、平面加工では大量の切りくずが発生しやすいため、連続して切りくずが排出されるよう工夫することが重要です。また、溝加工では切りくずが工具や加工部品に絡みつきやすいため、適切な潤滑と冷却が鍵となります。
具体的な例として、ある日本の製造業者は、フライス加工中に発生する切りくずを効率よく管理するために、自動切りくず排出システムを導入しました。このシステムは、加工中に発生した切りくずを即座に機械外へ排出することで、加工精度の向上と作業効率のアップを実現しています。このように適切な切りくずの管理を行うことで、鉄製品の品質向上はもちろん、生産性の向上にも寄与するのです。
結論として、鉄製品製造におけるフライス加工は多様な種類があり、それぞれに最適な切りくずの管理方法が求められます。日本の製造業者が示したように、効率的な切りくず管理は製品の品質向上に不可欠であり、生産性の向上にもつながる重要な鍵点であると言えます。
5. 金属加工の種類とその特徴
5-1. 旋削加工との比較
鉄製品の製造において、フライス加工はその精密性と効率から、業界内で広く採用されています。フライス加工は、素材の表面を削り取ることで所望の形状を作り出す加工方法の一つであり、その種類と鍵点を理解することが品質向上のカギとなります。旋削加工と比較した場合、フライス加工は平面や曲面の加工において優れた柔軟性を誇ります。例えば、ギアや溝の切削には、フライス加工の方が適しています。
フライス加工の種類には大きく分けて二つあります。一つ目は平面を加工するための平面フライス加工、二つ目は曲線や曲面を加工するための形状フライス加工です。特に、形状フライス加工は複雑な形状を実現するために重要で、精密機器や自動車部品など、高い精度が求められる製品に不可欠です。
フライス加工の鍵点としては、適切な工具選定と加工速度の管理が挙げられます。工具の材質や形状、切削速度が製品の品質に大きく影響するため、製造過程での細心の注意が必要です。また、最新のCNC(コンピュータ数値制御)技術を活用することで、より高精度で効率的な加工が可能となります。
結論として、フライス加工は鉄製品製造における不可欠な技術であり、その種類と鍵点を理解することが、製品品質の向上につながります。適切な工具選定と加工速度の管理、そして最新技術の活用が、成功への道と言えるでしょう。
5-2. 研削加工との違い
フライス加工は、製造業で非常に普及している鉄製品の加工方法の一つであり、その種類と適用性の広さが鍵となっています。研削加工とは異なり、フライス加工では、回転する工具を使用して材料から余分な部分を削り取ることで形状を作り出します。これにより、非常に精密な作業が可能となり、平面や溝、歯車など、様々な形状の加工が可能です。
例えば、平面フライス加工は、表面を平滑に仕上げるのに使用され、溝加工では、特定の形状の溝を材料に作り出すことができます。また、歯車加工には、歯車の精密な形状を作出するために特化したフライス工具が用いられます。これらの加工方法は、自動車や機械部品、建設用具など、幅広い分野で採用されています。
フライス加工の重要性は、その多様性と対応可能な加工範囲の広さにあります。研削加工と比較しても、より大きな材料を効率的に、かつ高精度で加工できる点が、特に日本の製造業において重宝されています。この柔軟性と精度の高さが、鉄製品製造におけるフライス加工の不可欠性を物語っているのです。
5-3. その他の金属加工技術
鉄製品の製造におけるフライス加工は、高度な技術と繊細な工程を要するため、プロフェッショナルから特に注目されています。フライス加工は、素材から不要な部分を削り取ることで、製品の形状を整える加工方法の一つです。これには様々な種類があり、それぞれが製品の品質に大きく影響を与えるため、鉄製品製造における重要な鍵を握っています。
具体的には、平面加工、溝加工、輪郭加工などがあります。平面加工は、製品の表面を平滑に仕上げることが目的で、一般的に厚みの調整にも用いられます。溝加工は、製品に特定の溝や穴を加工することで、部品の組み立てや機能の向上に寄与します。輪郭加工では、製品の外形を精密に削り出すことができ、複雑な形状の製造に不可欠です。
これらの加工方法を適切に選択し、適用することで、耐久性や機能性の高い鉄製品を製造することが可能になります。日本では、優れたフライス加工技術を持つ職人が多く、高品質な鉄製品が数多く生産されています。そうした背景から、フライス加工は鉄製品製造における不可欠なプロセスであり、その技術の向上と革新が今後も求められていくでしょう。
6. フライス加工の注意点とトラブルシューティング
6-1. 加工精度を左右する要因
フライス加工において、製品の質を決める重要な要素は加工精度です。この精度を確保するためには、適切な種類のフライス加工を選択することが鍵となります。日本において鉄製品の製造は、その高い技術力で世界的にも評価されていますが、その背景には、フライス加工の技術の進歩があります。
フライス加工には、平面加工、溝加工、歯切り加工など、様々な種類が存在します。例えば、平面加工は、製品の表面を平らにするために用いられ、精密な表面仕上げが求められる場合に選ばれます。また、溝加工は、部品に溝や穴を加工する際に使用され、機械の組み立てに不可欠な工程です。歯切り加工は、歯車などの歯を切り出す作業で、高い精度が要求されるため、適切な技術選択が重要です。
これらの加工方法を適切に選択し、実行することで、鉄製品の製造における加工精度は大きく向上します。日本製の鉄製品が高品質である理由の一つは、このような加工技術の細やかな選択と適用にあります。どの加工方法を選択するかによって、製品の品質が左右されるため、製造過程での正しい選択が不可欠です。加工精度の向上は、製品の品質向上に直結し、それが最終的には製品の市場競争力を高めることにつながります。
6-2. よくある問題と解決策
フライス加工は、鉄製品製造において欠かせない技術の一つです。この加工方法には複数の種類があり、それぞれに重要なポイントが存在します。鉄製品の精度や生産効率を高めるためには、適切なフライス加工の選択が鍵となります。
まず、フライス加工の種類には、平面加工、側面加工、溝加工、歯車加工などがあります。例えば、平面加工は、鉄の表面を平らにするために用いられ、製品の基盤となる部分の加工に重要です。一方、溝加工は、部品同士を組み合わせる際に必要な溝やキー溝を作るために使用されます。
特に、日本の鉄製品製造では、精密な加工が求められることが多いです。そのため、加工する際の精度や仕上がりの品質に高い要求があります。例えば、自動車部品や電子機器の部品などは、微細な誤差でも製品の性能に大きく影響するため、フライス加工における精度の管理が特に重要になります。
そのためには、加工機械の選定や刃の種類、加工条件の設定など、細かな調整が必要です。加工機械には、対象となる鉄製品のサイズや形状、加工する部位に応じて、最適なものを選ぶ必要があります。また、刃の種類によっても加工できる材料や加工速度が変わるため、製品の要求仕様に合わせた適切な選択が求められます。
結論として、フライス加工は鉄製品製造において多様な形状を実現するための重要な技術です。その種類を理解し、製品に合った加工方法を選択することが、高品質な鉄製品を効率良く生産するための鍵となります。適切な機械と加工技術の選定は、製品の品質を決定づけるとともに、製造コストの削減にも繋がります。
6-3. 長寿命のカッティングツールを保つコツ
フライス加工は鉄製品の製造において重要な役割を果たします。この工程では、製品の精度や品質が大きく左右されるため、適切なフライス加工の種類を選択し、その鍵点を把握することが欠かせません。平面加工、溝加工、形状加工など、フライス加工にはさまざまな種類があります。例えば、平面加工は、製品の表面を平らに仕上げるのに用いられ、溝加工は、特定の形状の溝を製品に加えるのに適しています。形状加工では、複雑な形状を持つ製品を製造することができます。これらの加工方法を適切に選び、加工条件を最適化することで、製品の品質を高め、長寿命のカッティングツールを保つことが可能になります。したがって、フライス加工における種類の理解と、それぞれの鍵点を把握することは、鉄製品製造の品質と効率を向上させるために不可欠です。
7. 製造業での加工試作への挑戦
7-1. 試作の準備と計画
鉄製品の製造において、フライス加工は欠かせない技術です。この加工法の種類には様々あり、それぞれが製品の品質や生産効率に大きく影響します。日本の製造業では、特に精度と効率を追求するため、適切なフライス加工の選択が鍵となります。たとえば、平面加工には面フライス加工が、複雑な形状の加工には球形フライス加工が用いられます。また、高速フライス加工は、生産性の向上に貢献する一方で、切削条件の選択が重要です。具体的な例として、ある自動車部品製造企業では、高速フライス加工を導入することで、部品の生産時間を大幅に短縮し、コスト削減に成功しました。このように、フライス加工の種類とその特性を理解し、製品ごとに最適な加工法を選択することが、高品質な鉄製品を効率よく生産する上での鍵となります。
7-2. 加工試作の実行手順
鉄製品の製造分野においてフライス加工は不可欠な技術です。この加工方法は素材の表面を滑らかにしたり、特定の形状を削り出すために使用されます。フライス加工の種類には、平面加工、スロット加工、形状加工、穴加工などがありますが、その中でも特に重要な鍵点は精度と仕上がりの質です。
日本における鉄製品製造業界では、これらの加工技術を極めることが競争力の源泉となっています。例えば、精密な機械部品や自動車部品の製造においては、ミクロン単位での精度が求められることが多く、そのための正確なフライス加工が不可欠です。また、美しい仕上がりは、製品の外観だけでなく耐久性にも大きく影響するため、こちらも非常に重要です。
特に、日本では伝統と革新が融合した製造技術が発展しており、フライス加工も例外ではありません。先進的なCNC(コンピュータ数値制御)技術を駆使することで、より高速で精密な加工が可能になり、製品の品質向上に貢献しています。
結論として、鉄製品製造におけるフライス加工の種類とその鍵点は、製造業の競争力を高める上で非常に重要です。精度と仕上がりの質を確保することで、より優れた製品を市場に提供し、製造業の発展に貢献しています。
7-3. 試作品の評価と改善点
試作品の評価と改善点の発見は、製品開発の過程で非常に重要なステップです。この段階で、製造前の最終確認として、製品の機能性や品質が検証されます。特に、鉄製品の製造においては、フライス加工の精度が製品の品質に直結するため、試作品を通じてその加工法の選択と調整が鍵となります。
フライス加工には大きく分けて、平面加工、溝加工、輪郭加工などの種類があります。各加工法は、製品の形状や要求される精度に応じて選ばれます。例えば、複雑な形状の製品には輪郭加工が適しており、高精度が求められる場合には、切削条件の最適化が必要です。
試作品を評価する過程で見つかった改善点は、製品の品質向上に直接繋がります。例えば、フライス加工で生じた微細なひずみが見つかった場合、加工条件の見直しや、より適した加工法への変更が検討されます。これにより、最終製品の品質が保証されることになります。
結論として、フライス加工の種類とその選択は、鉄製品製造における品質を決定づける重要な要素です。試作品の評価を通じて改善点を見つけ出し、それに基づいて加工法を選択・調整することが、高品質な製品を生産するための鍵となります。
まとめ
鉄製品の製造において、フライス加工は極めて重要な要素です。異なる種類のフライス加工を正確に理解することが、製造プロセスを最適化し、製品の品質を向上させる鍵となります。各種類のフライス加工には独自の特性があり、それぞれが異なる製品や部品に最適化されています。この知識を活用することで、鉄製品の製造プロセスを効率化し、高品質な製品を提供することが可能となります。
鉄材のフライス加工入門:必見の加工方法とその適用
鉄材のフライス加工という言葉を聞いたことがありますか?鉄を使った製品や部品を作る際に欠かせないフライス加工は、どのような方法で行われるのでしょうか?この記事では、鉄材をフライス加工する際の必見の加工方法やその適用について詳しく解説します。
鉄材のフライス加工は、どのように行われるのか気になる方も多いことでしょう。加工方法や種類によって作業の効率や精度が異なるため、正しい知識を持っていることが重要です。この記事では、初心者から上級者まで幅広いニーズに応える情報を提供しています。
鉄材をフライス加工することで、どのようなメリットがあるのか、どのような場面で活用されるのか。さまざまな視点から解説し、読者の皆様にとって有益な情報をお届けします。鉄材のフライス加工に興味をお持ちの方は、ぜひこの記事をご覧ください。
1. 鉄材のフライス加工入門
1-1. フライス加工とは:基本概念の解説
フライス加工とは、鉄などの金属材料を削ることで形状を整える加工技術の一つです。日本においても、多岐にわたる産業で必要不可欠な技術として広く用いられています。その理由は、フライス加工が高精度かつ複雑な形状の部品製造に適しているからです。例えば、自動車や航空機の部品、精密機械など、日常生活で使われる多くの製品にこの技術が活かされています。
加工方法には、大きく分けて平面加工、溝加工、輪郭加工などの種類があります。平面加工では、材料の表面を平らにすることができ、溝加工は溝や穴などの特定の形状を作り出すのに適しています。輪郭加工では、材料の外形を整えることができます。これらの加工方法によって、製品の要求される正確な寸法や形状を実現することが可能です。
結論として、フライス加工は、その精度の高さと形状の多様性により、日本の製造業で広く採用されている技術です。自動車から家電製品に至るまで、私たちの生活を支える様々な製品の製造に不可欠な役割を果たしています。この技術により、複雑で高品質な製品を効率良く生産することができるのです。
1-2. 鉄材の特性とフライス加工の関係
鉄材はその耐久性と加工しやすさから、多種多様な産業で使われています。フライス加工は、このような鉄材を精密に加工するのに必須の技術です。フライス加工を使うと、鉄材を任意の形に加工することが可能になり、製品の精度と品質を大きく向上させることができます。例えば、自動車の部品や建築用の素材など、日々の生活に欠かせない多くの物が、フライス加工によって生み出されています。この加工方法は、特に精密を要する部品製造において、その価値を発揮します。そのため、鉄材を使用する様々な分野でフライス加工は重要な位置を占めているのです。結論として、鉄材のフライス加工は、高品質な製品を生産する上で欠かせない技術であり、その適用範囲は極めて広いと言えます。
1-3. フライス加工の種類とその特徴
鉄材のフライス加工は、精密な部品製造や機械加工において重要な方法の一つです。この加工法は、鉄を含む多種多様な材料に適用可能であり、その種類と応用範囲の広さから、様々な産業で広く利用されています。フライス加工の方法には、平面加工、形状加工、溝加工、歯車加工などがあり、それぞれ特有の特徴と適用範囲を持っています。例えば、平面加工は主に材料の表面を滑らかにするために使われ、溝加工は部品に特定の溝を刻むのに用いられます。歯車加工は、精密な歯車を製造するのに不可欠です。
日本では、これらの加工方法が自動車産業や電子機器産業のような高度工業製品の製造に活用されています。特に、高い精度と複雑な形状が求められる部品製造において、フライス加工はその能力を発揮します。例えば、自動車のエンジン部品や航空機の構造部材など、精度が重要とされる分野での使用が挙げられます。
結論として、鉄材のフライス加工は、その種類の多様性と広い適用範囲により、様々な産業で不可欠な技術となっています。特に、日本の高度な製造業においては、高精度な部品製造に欠かせない方法であり、この加工技術の理解と適用は、品質と効率を高める上で重要です。
2. フライス加工の基礎知識
2-1. 加工方法の選定基準
鉄材のフライス加工は、精密な部品製造に不可欠な技術であり、その適用範囲は広いです。この技術を理解することで、より効率的かつ高品質な製品の製造が可能となります。フライス加工の方法は多岐にわたりますが、適切な加工方法の選択が重要です。その理由は、材料の種類、加工する部品の形状、必要な精度、そして製造コストに大きく影響されるからです。例えば、粗加工では大量の材料を迅速に除去するために大きな切削力を用いるが、仕上げ加工では精密さが求められ、細かい工具を使用します。また、複雑な形状を持つ部品には、5軸フライス加工が適しています。これにより、一度の設定で多方向からの加工が可能となり、加工時間の短縮と精度の向上が見込めます。日本では、特に自動車や電子機器の部品製造において、このフライス加工技術が活躍しています。結論として、鉄材のフライス加工を成功させるためには、加工する部品の特性を理解し、適切な加工方法を選ぶことが重要です。適切な選択により、効率的かつコスト効果の高い製造プロセスを実現することができます。
2-2. 使用する工具の種類と選び方
鉄材のフライス加工は、精密な部品製造に不可欠な技術です。この加工方法が選ばれる理由は、その高い精度と多様性にあります。特に、日本の製造業でよく利用されるため、種類と選び方を理解することが重要です。
フライス加工には、平面や溝、歯車など、様々な形状の加工が可能な点が特徴です。例えば、自動車の部品や電子機器の精密部品など、日常生活に密接に関わる製品の製造にも使われています。この加工方法では、カッターの種類を適切に選ぶことが、求められる製品の品質を左右します。
具体的には、鉄材の種類や加工する製品の形状に応じて、エンドミルやフェイスミルなどのカッターを選択します。また、精密な加工を要する場合は、微細な加工が可能な小径のカッターや、特殊なコーティングが施されたカッターを使用することで、加工精度を高めることができます。
結論として、鉄材のフライス加工はその適用範囲の広さと高い精度から、製造業において重要な技術です。適切な工具を選択することで、高品質な製品製造が可能となり、日本の製造業のさらなる発展に寄与します。
2-3. カッターと切削条件の基礎
フライス加工は、製造業における最も一般的な加工方法の一つであり、特に鉄材の加工において重要な役割を果たします。この方法は、精度が高く、複雑な形状を作ることが可能で、幅広い産業で利用されています。しかし、その効果を最大限に引き出すためには、適切なカッターや切削条件の選定が不可欠です。
カッターの選択は、加工される材質や形状、仕上がりの品質に大きく依存します。例えば、鉄材には硬質のカッターが推奨されます。また、切削速度、送り速度、切削深さなどの切削条件も、材質や加工される物のサイズに応じて調整する必要があります。例として、精密な加工が求められる場合には、低い切削速度を選択することがあります。
具体例として、自動車業界では、エンジンの部品など非常に精度の高い加工が必要とされるため、適切なカッターと切削条件の選定が重要となります。
結論として、鉄材のフライス加工においては、適切なカッターの選択と切削条件の慎重な調整が、高品質な製品を効率良く生産する鍵となります。これにより、製造業全体の生産性向上にも寄与することができるでしょう。
3. NCフライス加工の基本
3-1. NCフライス加工の概要
鉄材のフライス加工は、精密な部品製造や機械加工において不可欠な技術です。特に、NC(数値制御)フライス加工は、その高い精度と効率性から、日本の製造業において広く採用されています。この加工方法は、プログラムされたデータに基づいて自動で材料を削ることができ、複雑な形状や細かい加工も可能にします。
鉄材のフライス加工には様々な種類がありますが、NCフライス加工の適用例としては、自動車のエンジン部品や航空機の構造部材などが挙げられます。これらの部品は、高い精度と強度が求められるため、NCフライス加工による製造が不可欠です。例えば、エンジン部品では、微細な耐熱性や耐摩耗性が必要とされる部位を正確に加工することができ、製品の品質と性能を向上させることが可能です。
また、NCフライス加工は、加工プログラムの作成により、一度に多数の部品を同時に加工することが可能です。これにより、生産効率を大幅に向上させることができ、日本の製造現場ではコスト削減や納期短縮に大きく貢献しています。
結論として、鉄材のフライス加工、特にNCフライス加工は、その高い加工精度と効率性から、日本の製造業における重要な技術となっています。自動車や航空機などの高品質な部品製造には欠かせない手法であり、今後もその需要は高まることが予済されます。
3-2. NCプログラミングの基本
鉄材のフライス加工は、多様な製品の製造において重要な手法です。この加工方法は、特に精密さが求められる部品製作において、その価値を発揮します。鉄材を用いたフライス加工には、種類や方法が多岐にわたりますが、その中でも特に注目されるのが、平面加工、溝加工、側面加工です。
平面加工は、製品の表面を平らにする基本的な加工方法で、材料のサイズ調整や仕上げに用いられます。次に溝加工は、鍵や歯車など特定の形状を削り出す際に使用され、高い精度が求められる作業です。また、側面加工は、製品の側面を削り、形状を整える工程で、複雑な形状の製品製造に不可欠です。
これらの加工方法は、製品の用途や必要とされる精度に応じて選択されます。例えば、自動車や航空機の部品製造では、極めて高い精度が求められるため、適切なフライス加工が重要となります。日本では、これらの加工技術の高度化により、製造業の競争力が支えられています。
結論として、鉄材のフライス加工は、多岐にわたる製品の製造において不可欠であり、正確な加工方法の選択が、製品の品質を左右すると言えます。加工技術の進展により、今後もさらに多様な製品の開発が期待されます。
3-3. 加工データの作成と入力
鉄材のフライス加工は、精密な部品制作や機械加工に不可欠な技術です。この加工法は、高い精度と複雑な形状を実現するために使われています。その理由は、フライス加工によって、鉄材を任意の形に削り出すことができ、さまざまな種類の加工が可能となるからです。たとえば、平面や溝、歯車など、様々な形状がこの方法で加工されます。特に、日本の製造業界では、精度が要求される部品の加工において、この技術が頻繁に用いられています。
日本において、フライス加工は自動車や電子機器、航空宇宙産業など、幅広い産業で活用されています。例えば、自動車のエンジン部品や電子機器の筐体など、精密な加工が求められる部品製造において、フライス加工の技術が重要な役割を果たしています。これらの産業では、鉄材だけでなく、アルミニウムやチタンなどの非鉄金属も加工されることがありますが、鉄材の加工では特にフライス加工の利点が活かされます。
フライス加工の広範な適用性と精密性は、日本の製造業の競争力を支える要因の一つです。この技術により、高品質な製品を効率良く生産することが可能となり、国内外の市場で高い評価を受けています。そのため、鉄材のフライス加工に関する理解を深め、適切な加工方法を選択することは、製造業に携わる者にとって非常に重要です。
結論として、鉄材のフライス加工は、その精密性と多様性から、日本の製造業において不可欠な技術であり、様々な産業で利用されています。この技術を理解し、適切に活用することで、高品質な製品の製造が可能となります。
4. 加工機械の操作方法
4-1. 機械の主要部分とその機能
鉄材のフライス加工は、精密部品の製造や機械加工において欠かせない技術です。その適用範囲は広く、自動車から家電製品まで、多岐にわたります。この加工方法は鉄材の表面を削り、所望の形状や仕上がりにすることができます。フライス加工の種類には、平面加工、溝加工、歯車加工などがあり、それぞれ異なる加工方法によって、製品の精度や生産効率が向上します。
例えば、自動車のエンジン部品やギアなどの製造には、高い精度が求められるため、適切なフライス加工が不可欠です。また、家電製品の筐体を作る際にも、美しい仕上がりと正確な形状が求められます。これらの例からも分かるように、フライス加工は多くの製品の品質を決定づける重要な工程であることが理解できます。
さらに、技術の進展により、フライス加工はより高速かつ高精度に進化を遂げています。これにより、製造コストの削減や生産性の向上が実現し、日本の製造業の競争力を支えています。
結論として、フライス加工は鉄材を用いた製品製造において不可欠な技術であり、その種類と適用範囲の理解は、高品質な製品を効率良く生産する上で極めて重要です。技術の進化とともに、これらの加工方法がさらに発展していくことが期待されます。
4-2. 操作パネルの理解と使い方
鉄材のフライス加工は、精密な部品製造に不可欠な技術です。この方法は、様々な種類の鉄材に適用でき、高い精度と良好な表面仕上げを実現します。主に、機械部品の加工や工具製造に使用され、その適用範囲は非常に広いです。
フライス加工の主な利点は、複雑な形状や細部の精密加工が可能であることです。例えば、ギアやエンジン部品など、細かい凹凸が必要な部品の加工に適しています。この加工方法により、製品の品質が向上し、製造コストの削減にも繋がります。
日本では、高度な技術を要するフライス加工が重視されています。特に、自動車産業や航空機産業では、精密部品の需要が高く、フライス加工の技術が欠かせません。日本国内の加工技術の高さは、これらの産業の国際競争力を支える要素の一つです。
最終的に、鉄材のフライス加工は、その精密さと適用の幅広さにより、製造業において重要な役割を担っています。日本では、この加工技術のさらなる発展が期待されており、高品質な製品製造のために引き続き重要視されていくでしょう。
4-3. 加工前の準備と安全対策
鉄材のフライス加工は、高精度な部品を製造するための重要な工程です。この工程は、特に精密な部品を必要とする機械工業や自動車産業で広く利用されています。しかし、加工前の準備と安全対策が適切に行われていなければ、品質の低下や作業者の安全に重大な影響を与える可能性があります。
まず、加工前の準備として、使用する鉄材の品質を確認し、フライス加工機の設定を適切に行う必要があります。加工機の状態が良好であることを確認し、必要な工具が正確に取り付けられていることを確かめることも重要です。例えば、日本で製造される自動車部品において、このような準備工程を徹底することで、高い品質保持が可能になっています。
安全対策に関しては、適切な保護具の着用や、作業中の注意点を理解することが不可欠です。また、緊急時の対処法を事前に学び、常に安全を最優先に考えることが求められます。特に、機械の動作中は、予期せぬ事故が発生する可能性があるため、高い注意を払うことが必要です。
結論として、鉄材のフライス加工において、加工前の準備と安全対策は非常に重要です。これらを徹底することで、高品質な製品の製造と作業者の安全を確保することが可能になります。日本の製造業での成功例は、これらの工程の大切さを物語っています。
5. 金属加工の基本手順
5-1. 加工プロセスの計画
鉄材のフライス加工は、精密な部品製造に不可欠な工程であり、その適用範囲は広く、多くの産業で利用されています。鉄材をフライス加工することで、必要な形状やサイズの部品を正確に作り出すことができます。この加工方法は、その高い精度と効率性から、特に重要視されています。例えば、自動車や航空機の部品製造、建設機械や精密機器の部品作りにおいて、フライス加工は欠かせない技術です。
理由として、フライス加工は多様な種類のカッターを使用でき、複雑な形状や細かい加工も可能にするからです。例えば、平面や曲面、溝など、様々な形状の加工が可能であり、これにより設計の自由度が高まります。また、硬い材質の加工にも強く、精度の高い仕上がりを実現できる点も、その魅力の一つです。
特に日本においては、精密加工技術への要求が高く、フライス加工の技術開発も進んでいます。このため、日本製のフライス加工機械や技術は、世界的にも高い評価を受けています。
結論として、鉄材のフライス加工は、その精度と多様性から、様々な産業で不可欠な技術です。日本におけるこの技術の高い技術力と進化は、世界中の製造業に影響を与え続けています。これらの点から、鉄材のフライス加工に関する理解を深めることは、製造業に携わる多くの人々にとって、非常に重要であると言えるでしょう。
5-2. 材料のセットアップ
鉄材のフライス加工は、様々な種類の中でも特に精密な製品作りに適しています。これは、フライス加工が高い精度と柔軟性を提供するためです。日本において、鉄材は機械部品や建築材料など、多岐にわたる産業で使用されており、その加工方法もまた多様化しています。
フライス加工の最大の特徴は、複雑な形状や細かなディテールを持つ部品も高い精度で製造できる点にあります。例えば、自動車のエンジン部品や航空機の構造部品の加工には、この方法がよく適用されます。これは、鉄材を使用した細かく複雑な形状を必要とする製品の製造には、フライス加工が欠かせないからです。
さらに、フライス加工は種類が豊富であり、平面、曲面、溝加工など、製品に応じた加工が可能です。日本では技術の進歩により、より高速で精密なフライス加工が行えるようになり、製造業の生産性向上に大きく寄与しています。
結論として、鉄材のフライス加工はその高い精度と柔軟性から、日本の製造業において必要不可欠な技術です。多岐にわたる加工方法とその適用例を理解することで、より質の高い製品製造への道が開かれます。
5-3. 加工パスの確認と調整
鉄材のフライス加工は、精密な部品製造において欠かせない技術です。この技術の魅力は、その高い加工精度と多様な適用可能性にあります。具体的には、フライス加工を通じて、鉄材を任意の形状に削り出すことが可能であり、機械部品や工具など、様々な製品の製造に活用されています。
フライス加工の種類には、平面加工、溝加工、複雑形状加工などがあり、それぞれの用途に応じて選ばれます。例えば、平面加工は、部品の表面を平らにするのに適しており、溝加工は、歯車などの溝を加工するのに用いられます。また、複雑形状加工では、3Dモデリングデータを基にして、複雑な形状の部品を製造することが可能です。
このように、フライス加工はその適用範囲の広さと精度の高さから、製造業において重要な役割を果たしています。特に、精密な部品が求められる現代の産業において、この技術の重要性はますます高まっています。結論として、鉄材のフライス加工は、その多様な加工方法と適用の幅広さから、幅広い製品製造において不可欠な技術であると言えます。
6. 鍛造と塑性加工の基本
6-1. 鍛造加工の原理と適用
鉄材のフライス加工は、精密な部品製作に不可欠な技術であり、その適用範囲は広いです。フライス加工により、鉄材から様々な形状の部品を効率良く、高精度に製造することが可能です。この加工方法の種類には、平面加工、溝加工、歯車加工などがあります。例えば、自動車のエンジン部品や家電製品の小さな金属部品など、私たちの日常生活に欠かせない多くの製品がフライス加工によって作られています。日本では、特に精密機械工業が発展しているため、フライス加工技術の重要性は非常に高いです。そのため、この技術を理解し、適切な方法を選択することは、製品の品質向上と生産効率の向上に直結します。結論として、鉄材のフライス加工は、その種類を理解し、適用することで、様々な分野での製品製造において重要な役割を果たします。
6-2. 塑性加工の方法と特徴
鉄材のフライス加工は、製造業で広く用いられる重要な技術です。この加工方法は、高い精度と複雑な形状を実現することができるため、さまざまな分野での利用が可能です。フライス加工には、平面、溝、複雑な曲面など、多岐にわたる加工が行える点が大きな特徴です。
例として、自動車産業では、エンジンの部品やギアなど、精度が要求される部分にフライス加工が採用されています。また、ロボット技術の分野では、関節部分などの複雑な形状を持つ部品の加工にも使用されています。これらの具体例からも分かるように、フライス加工はその適用範囲の広さと、製品の品質向上において非常に重要な役割を果たしています。
結論として、鉄材のフライス加工はその精度の高さと多様な加工が可能であるため、製造業をはじめとする多くの分野で活用されています。この加工方法を理解し、適切に利用することで、製品の品質向上と生産効率の向上が期待できます。
6-3. フライス加工と鍛造・塑性加工との比較
フライス加工は鉄材を加工する方法の一つであり、特に精密な部品製造などに適しています。これは、フライス加工が高い精度と複雑な形状の加工が可能であるためです。例えば、機械部品や自動車のエンジン部品など、細かい寸法と形状が要求される場合に、フライス加工が活用されます。一方、鍛造や塑性加工は、大量生産に適しており、材料の強度を高めることができる方法ですが、フライス加工ほどの精度は出しづらいという特徴があります。
鉄材のフライス加工は、その精度の高さから多岐にわたる分野での応用が可能です。例を挙げると、航空宇宙産業における部品製造や、医療機器の精密部品など、非常に高い技術を要求される分野でも活躍しています。これらの分野では、数ミクロン単位の誤差も許されないため、フライス加工が重宝されるのです。
総じて、フライス加工は鉄材を含む多様な材料に対応可能で、高い精度と複雑な形状の実現が可能な加工方法であり、その適用範囲は広いです。これに対し、鍛造や塑性加工は、特に強度が要求される部品の大量生産に適していますが、複雑な形状や極めて高い精度を必要とする場合にはフライス加工の方が適していると言えるでしょう。
7. フライス加工におけるトラブルシューティング
7-1. よくある問題とその解決策
鉄材のフライス加工は、精密な部品製造において重要な役割を果たします。その理由は、フライス加工が高い精度と複雑な形状を実現できるからです。例えば、自動車や機械部品の製造には、厳密な寸法と形状が求められますが、フライス加工によってこれらの要求を満たすことが可能になります。特に、鉄は硬度が高く加工しにくい材料ですが、適切なフライス加工方法を用いることで、精密な加工が行えます。
鉄材をフライス加工する際には、様々な種類のカッターが使用されます。例として、エンドミルやフェイスミルがあり、これらは加工する表面や形状に応じて選ばれます。また、加工条件(カッターの回転速度、送り速度など)を適切に設定することも、高品質な加工を実現する上で欠かせません。
日本では、精密機器や自動車産業など、フライス加工が不可欠な分野が数多く存在します。これらの分野では、鉄材のフライス加工技術が製品の品質向上に直結するため、技術の進歩と熟練した技術者の育成が常に求められています。
結論として、鉄材のフライス加工は多岐にわたる産業で重要な技術です。その適用には、正確な加工方法の選択と、厳格な加工条件の管理が必要です。これらを実践することで、高い品質と精度を持つ製品を製造することが可能になります。
7-2. 加工精度を向上させるポイント
鉄材のフライス加工は、その高い精度と多様性から、製造業における重要な技術の一つとされています。フライス加工とは、主に金属を削る加工法であり、鉄材の形状やサイズを正確に加工するために用いられます。その適用範囲は広く、自動車部品から産業機械まで、さまざまな製品に対応しています。
加工精度を向上させるポイントとしては、まず適切な工具選択が挙げられます。鉄材の硬度や加工する形状に応じたフライス刃を選ぶことが、理想的な加工結果を得るための第一歩です。例えば、粗加工用と仕上げ加工用では、使用する刃の種類が異なります。また、切削条件の最適化も重要です。切削速度、送り速度、切削深さを材料の性質や加工の目的に合わせて調整することで、加工精度は大きく向上します。
具体的な例として、自動車のエンジン部品の加工では、フライス加工の精度がその性能に直結します。正確な加工により、部品の組み合わせがスムーズになり、エンジンの性能向上に繋がるのです。
加工精度を向上させることは、製品の品質向上だけでなく、製造コストの削減にも寄与します。正確な加工により製品の再加工や廃棄が減少し、生産効率が向上するからです。フライス加工はその高い加工精度と適用範囲の広さから、今後も多くの産業で重要な役割を果たし続けるでしょう。
7-3. 長期間の機械保守管理
鉄材のフライス加工は、精密な部品製作に不可欠な技術です。この加工法は、特に日本の製造業で広く採用されています。フライス加工により、鉄材を所望の形状やサイズに削り出すことができます。この技術の利点は、その精度と多様性にあります。例えば、機械部品や自動車のコンポーネントなど、複雑な形状を持つ製品の製造にしばしば用いられます。
フライス加工には様々な種類がありますが、平面加工や形状加工、溝加工などが特に一般的です。これらの方法を用いることで、製品の設計に応じた精度の高い加工が可能になります。日本の製造業者は、これらの技術を駆使して、高品質な製品を世界市場に供給しています。
フライス加工の重要性は、その適用範囲の広さにも見られます。例えば、航空宇宙産業や自動車産業だけでなく、日常生活における家電製品の製造にも欠かせない技術です。これらの産業では、耐久性と精度が求められるため、フライス加工が重要な役割を果たしています。
結論として、鉄材のフライス加工は、その精度と多様性により、多くの製造業で欠かせない技術です。様々な種類の加工方法があり、それぞれの製品の設計に合わせて最適な加工が選択されています。日本の製造業者にとって、この高度な加工技術は、世界市場で競争する上での大きな強みとなっています。
8. さまざまなフライス加工応用例
8-1. 鉄材フライス加工の実際の事例
鉄材のフライス加工は、製造業で不可欠な技術の一つです。この加工方法によって、鉄材を正確な形状やサイズに加工することが可能になります。具体的には、切削工具を回転させながら鉄材を動かすことで、余分な部分を削り取ります。この方法は、様々な種類の鉄材に適用可能であり、その精度と効率性から多くの場面で採用されています。
例えば、自動車産業ではエンジン部品やフレームの加工にフライス加工が利用されます。また、建築業界では、構造鋼の加工にも用いられており、強度と精度が求められる部分の加工に欠かせません。さらに、小規模な工房では、オーダーメイドの工具や部品製造にもこの技術が活用されています。
このように、鉄材のフライス加工はその適用範囲の広さと、加工の正確性により、多岐にわたる分野で重宝されています。特に、精密な加工が要求される現代の製造業において、この技術の重要性はますます高まっています。結論として、鉄材のフライス加工は、その多様な適用可能性と高い精度により、現代社会における製造業の発展に不可欠な技術であると言えるでしょう。
8-2. 複雑形状の加工方法
鉄材のフライス加工は、製造業で必要不可欠な工程であり、その種類と適用は幅広いです。その理由は、フライス加工が鉄材を精密に、かつ効率的に加工できる方法だからです。例えば、ギアやエンジン部品などの複雑な形状は、フライス加工によって高い精度で製造されます。日本では、特に高い技術力を要する精密部品の製造において、フライス加工が欠かせない技術となっています。
フライス加工には、平面、側面、溝、歯車など、様々な加工があります。これらは、使用するカッターの種類や加工方法によって分類されます。例として、平面加工ではエンドミルを使用し、一定の深さで鉄材を削り取っていきます。また、複雑な形状の加工には、ボールエンドミルやコーナーラジアスエンドミルが用いられることが多いです。こうした様々な工具を駆使することにより、幅広い形状の精密加工が可能になります。
また、鉄材のフライス加工は、その精度と効率性から、自動車産業や航空機産業といった、高度な技術を要する分野で特に重宝されています。これは、複雑な部品を短時間で、かつ大量に製造する必要があるためです。日本の技術力が世界に誇る一因でもあります。
結論として、鉄材のフライス加工は、その種類と適用が広く、精密な部品製造に不可欠です。特に日本のような高度な製造業が盛んな国では、この技術はさらに発展し続けることでしょう。
8-3. 革新的なフライス加工技術の紹介
鉄材のフライス加工は製造業で欠かせない技術です。この技術により、精密な形状やサイズの加工が可能となり、多様な製品の製造に寄与しています。その中でも特に注目される加工方法には、平面加工、スロッティング、側面加工などがあります。例えば、平面加工は鉄材の表面を滑らかに仕上げるのに適しており、スロッティングは溝を切るのに、側面加工は材料の側面を整えるのに用いられます。これらの方法は、それぞれが持つ特性を生かし、自動車部品や機械部品など、高度な精密さが求められる製品に適用されています。加工方法を適切に選択することで、製品の品質向上と製造効率の向上が期待できます。鉄材のフライス加工を理解し、適切な方法を選ぶことは、製造業における品質と効率の両方を高めるために不可欠です。
まとめ
鉄材をフライス加工する際、主に面取り、穴あけ、溝切り、複雑形状の加工など、さまざまな方法があります。これらの方法は、鉄材の種類によって適用されるべき加工方法が異なります。また、フライス加工は精度が求められるため、正確な測定と計画が必要不可欠です。これらの基本的な加工方法と適用について理解しておくことが、鉄材のフライス加工において重要です。
工作機械を使った鉄のフライス加工:種類とその応用範囲
工作機械を使った鉄のフライス加工に興味を持っていますか?鉄のフライス加工は、工業製品や部品などの製造に欠かせない技術であり、その種類や応用範囲について知っておくことは重要です。本記事では、鉄のフライス加工に焦点を当て、その種類と応用範囲について詳しく解説します。加工技術に興味がある方や製造業に携わる方々にとって、きっと興味深い情報が含まれています。さあ、鉄のフライス加工の世界にご一緒に足を踏み入れてみましょう。
1. フライス加工の基礎
1-1. フライス加工とは
フライス加工は、工作機械を使用して鉄などの材料から特定の形状を削り出す加工方法です。この技術は、精密な部品製造に不可欠であり、その種類と応用範囲は非常に広いです。フライス加工には、平面、曲面、溝など、様々な形状を作り出すことができる「平面フライス加工」や「エンドミル加工」など多くの種類があります。例えば、自動車のエンジン部品や航空機の構造部材など、日常生活で広く利用されている製品の多くが、これらの加工技術によって作られています。
特に日本では、高い技術力を背景にした精密加工が可能なフライス加工機械が開発されており、世界中のさまざまな産業で需要が高まっています。自動車産業や航空宇宙産業だけでなく、電子機器や医療機器など、高度な技術を要する製品の製造にも欠かせない技術です。
このように、フライス加工の種類とその応用範囲は広く、日本の製造業において重要な役割を果たしています。高精度で複雑な形状の部品を効率的に生産することができるため、今後も様々な分野での活用が期待されています。結論として、フライス加工はその多様性と応用の幅広さから、製造業の進化とともにさらに発展していく技術であると言えるでしょう。
1-2. 鉄のフライス加工のメリット
鉄のフライス加工は、精密な部品製造に不可欠な方法の一つとして、その利侠を広く認識されています。その理由は、フライス加工が提供する高い精度と柔軟性にあります。例えば、鉄を使ったフライス加工では、複雑な形状や細かい溝を正確に削り出すことが可能です。加えて、フライス加工機械は様々な種類が存在し、それぞれ特定の用途に合わせて設計されています。水平型や垂直型のフライス機は、大きさや形状の異なる鉄のブロックを加工するのに適しており、その応用範囲は自動車業界から宇宙航空産業まで広がっています。
フライス加工のもう一つの大きなメリットは、生産効率の向上です。最新のCNC(コンピュータ数値制御)技術を利用したフライス機械は、手作業による加工よりも遥かに速く、かつ一貫した品質で鉄の加工が可能です。このように、フライス加工は効率的かつ多様な形状の加工が可能であり、製造業における生産性の向上に大きく貢献しています。
まとめると、鉄のフライス加工は、その高い精度、柔軟性、そして生産効率の向上のおかげで、多岐にわたる産業で重宝されています。この加工方法により、技術の進展とともに、より高度な製品の開発が期待できます。
1-3. フライス加工の歴史と発展
鉄のフライス加工は、製造業や機械工業において重要な役割を果たしています。その理由は、フライス加工により、鉄材料を高精度かつ効率的に加工できるからです。フライス加工にはさまざまな種類があり、それぞれに応用範囲が存在します。例えば、平面フライス加工は、主に平らな面を削るのに使用されます。また、側面フライス加工は、材料の側面を削るのに適しており、溝や段差を作るのに役立ちます。
日本では、高度な技術力を背景に、これらフライス加工技術が幅広い産業で活用されています。自動車産業では、エンジン部品や駆動系の精密部品を製造する際に、フライス加工が不可欠です。また、電子機器の小型化が進む中で、微細な部品を製造するための微細加工技術としてもフライス加工が用いられています。
このように、鉄のフライス加工はその種類に応じて様々な産業で応用されており、日本の製造業の発展に大きく貢献しています。フライス加工技術の進化は、これからも日本のものづくりの可能性を広げ、産業全体の競争力強化に寄与することでしょう。
2. 金属材料の選び方
2-1. 鉄の特性と選定基準
工作機械を活用した鉄のフライス加工は、その優れた強度と加工性により、多岐にわたる産業で利用されています。鉄は、硬度と耐久性のバランスが優れており、精密な部品作成に最適です。この加工方法には、面取り、溝切り、形状加工など、様々な種類があり、それぞれ特定の応用範囲に適しています。例えば、面取り加工は、部品の端を滑らかにするのに使用され、機械の組み立てを容易にします。一方、溝切り加工は、機械部品内で液体やガスを導くための溝を作成するのに役立ちます。そして、形状加工は、複雑な形状やデザインを実現するために用いられます。これらの加工技術は、自動車、航空宇宙、建設など、さまざまな産業で広範囲に応用されており、製品の信頼性と性能を高めています。最終的に、鉄のフライス加工は、その多様性と高い適応性により、現代の製造業において不可欠なものとなっています。
2-2. 鉄以外の金属材料との比較
鉄のフライス加工は、その耐久性と加工のしやすさから、産業界で広く使用されています。鉄は加工が容易なため、さまざまな種類のフライス加工技術が適用可能で、その応用範囲は極めて広いです。たとえば、航空機の部品から日用品に至るまで、私たちの生活のさまざまな場面で鉄が使用されています。この広範な応用は、鉄が他の金属材料と比較して優れた機械的性質を持ち、かつ経済的であることに起因します。
例えば、アルミニウムやチタンなどの軽量材料は航空宇宙産業で好んで使用されますが、これらの材料は鉄に比べて加工コストが高い傾向にあります。また、鉄は再生可能な資源であり、リサイクルが容易な点も、その普及に貢献しています。これらの理由から、鉄のフライス加工は今後も多岐にわたる産業分野で重要な役割を果たし続けるでしょう。
要するに、鉄のフライス加工技術は、その経済性と広範な応用可能性により、さまざまな産業で不可欠なものとなっています。その多様な応用は鉄が持つ優れた特性によるものであり、これからも私たちの生活を支える重要な技術としての地位を保ち続けるでしょう。
2-3. 材料の物理的性質と加工性
鉄のフライス加工は、その種類によって応用範囲が広がっています。フライス加工とは、工作機械を用いて鉄などの材料から余分な部分を削り取り、必要な形状に仕上げる工程です。この方法は精密な加工が可能で、様々な産業で活用されています。
その理由は、鉄のフライス加工が多様な種類を持ち、それぞれ特有の特性と応用範囲を有するためです。例えば、平面を削る平面フライス加工、溝を削る溝削り加工、複雑な形状を作る形状フライス加工などがあります。これらの加工方法により、自動車部品や建築材料、機械部品など、さまざまな製品の製造が可能となっています。
特に、日本の製造業では、高度な技術を要する精密部品の製造にフライス加工が重要な役割を担っています。例えば、自動車のエンジン部品や電子機器の精密部品など、高い精度が求められる部品の加工には、種類に応じたフライス加工技術が不可欠です。
したがって、鉄のフライス加工は、その種類によって様々な産業で広く応用されており、その精度と多様性が日本の製造業の競争力を支えていると言えます。
3. 工作機械の種類とフライス加工への応用
3-1. 汎用フライス盤とCNCフライス盤
工作機械を使った鉄のフライス加工は、その精度と多様性で多くの産業で重要な役割を果たしています。フライス加工には主に汎用フライス盤とCNCフライス盤の2種類があり、それぞれの応用範囲は異なります。
まず、汎用フライス盤はオペレーターが直接操作する機械で、単一の作業や小ロット生産に適しています。その柔軟性から、様々な形状の加工が可能で、特に一点物の製品製作や修理部品の製作に用いられます。例えば、特殊な形状のギアや機械部品の加工に適しており、製造業の現場で重宝されています。
一方、CNCフライス盤はコンピューターによって制御される機械で、複雑な形状や大量生産に非常に効率的です。プログラミングによる自動操作で高精度な加工が可能であり、一貫した品質の製品を迅速に生産できるため、自動車産業や航空機産業で広く利用されています。例えば、エンジン部品や航空機の構造部材など、精密度が要求される部品の製造に欠かせません。
結論として、フライス加工の種類によって応用範囲が異なり、汎用フライス盤は柔軟な対応が可能な一方で、CNCフライス盤は大量かつ高精度な生産に適しています。このように、工作機械を使った鉄のフライス加工は多方面での応用が期待される技術であることがわかります。
3-2. 垂直型と水平型フライス盤
鉄のフライス加工は製造業において重要な役割を果たしています。フライス加工には主に垂直型と水平型のフライス盤があり、それぞれに応用範囲が異なります。垂直型フライス盤は、回転する工具が垂直方向に動くことで、平面や曲面を加工するのに適しています。これに対して、水平型フライス盤は工具が水平方向に動くため、重い物体や大きな部品の加工に向いています。
例えば、自動車や航空機の部品製造において、精密な平面が必要な場合は垂直型フライス盤が用いられます。一方で、船舶の大型エンジン部品など、重さやサイズが大きな物の加工には水平型が選ばれることが多いです。
最終的に、加工する物の特性を考慮して、適切なフライス盤を選択することが重要です。垂直型と水平型のフライス盤を適切に活用することで、多様な鉄の加工が可能となり、製品の品質向上に寄与することができます。
3-3. 多軸フライス盤の紹介
工作機械を用いた鉄のフライス加工は、多様な種類の中でも特に多軸フライス盤が注目を集めています。この技術の応用範囲は広く、精密な加工が求められる多岐の分野で活用されています。多軸フライス盤は、その名の通り、複数の軸を持ち、これにより複雑な形状や細部まで精密に加工することが可能になります。例えば、自動車産業ではエンジン部品の加工、航空宇宙産業では機体の部品製造に不可欠です。さらに、電子機器の小型化が進むにつれ、微細な部品加工にもこの技術は大きな役割を果たしています。
こうした多軸フライス盤の利点は、ただ精密な加工が可能であるだけでなく、加工時間の短縮や効率の向上にも寄与しています。多軸で同時に加工することにより、従来の単軸フライス盤と比較して作業時間を大幅に減少させることが可能であり、コスト削減にも繋がります。これらの利点から、多軸フライス盤はただの加工技術を超え、産業全体の生産性向上に寄与しているのです。
結論として、多軸フライス盤を用いた鉄のフライス加工は、その精度の高さと効率の良さから、多岐にわたる産業で重宝されています。自動車から航空宇宙、さらには電子機器産業に至るまで、この技術の応用範囲は広大であり、今後もその重要性はますます高まっていくことでしょう。
4. マシニング加工とフライス加工の違い
4-1. マシニング加工の概要
工作機械を使用した鉄のフライス加工は、製造業で広く応用されている技術です。この加工技術は、精密な部品を効率良く生産するために不可欠です。フライス加工の種類には、平面加工、溝加工、輪郭加工などがあり、それぞれ特定の応用範囲があります。例えば、平面加工は主に部品の表面を平滑にするために用いられ、溝加工は部品に溝やキー溝を加えるのに適しています。また、輪郭加工は複雑な形状を持つ部品の外形を削り出すのに使用されます。
日本では、自動車産業や電子機器産業でこのフライス加工が特に重要視されています。自動車部品やスマートフォンの内部部品など、精密さが求められる製品には、この加工技術が欠かせません。フライス加工により、高い生産効率と精度を実現できるため、日本の製造業の競争力を支えています。
結論として、鉄のフライス加工はその種類に応じてさまざまな製品の製造に応用されており、日本の製造業において重要な役割を果たしています。特に、自動車産業や電子機器産業では、この加工技術によって製品の品質と生産性が大きく向上しているのです。
4-2. フライス加工との技術的差異
フライス加工は、鉄などの金属を精密に加工するための重要な技術であり、その種類と応用範囲は広いです。この工程では、回転する刃を使って金属から余分な部分を削り取ることで、必要な形状やサイズに仕上げます。フライス加工には、平面、曲面、溝など多様な加工が可能であり、その精度と効率性から多くの製造業で採用されています。
特に、日本では自動車や航空機の部品製造をはじめとする精密工業分野での需要が高く、フライス加工の技術進化は止まることを知りません。例えば、コンピュータ数値制御(CNC)フライス加工機は、極めて高い精度で複雑な形状を加工できるため、特に重宝されています。これにより、時間とコストを大幅に削減しながら、より高品質な製品の生産が可能になります。
加えて、環境への配慮から、廃材を減らす工夫やリサイクル可能な材料の使用など、持続可能な製造プロセスへの意識も高まっています。これに応える形で、フライス加工技術も進化を続けており、よりエコフレンドリーな製造方法へと変化しているのです。
結論として、鉄をはじめとする金属のフライス加工はその種類と応用範囲の広さ、そして技術進化により、今後も多くの製造業で不可欠な役割を担うことでしょう。この技術的差異は、より効率的で高品質、かつ環境に優しい製品製造を可能にしています。
4-3. 各加工法の適用シナリオ
工作機械を使った鉄のフライス加工は、その種類に応じて幅広い応用が可能です。フライス加工は、金属の平面や曲面を削る作業であり、精密な部品作成に不可欠です。日本においても、この技術は自動車や機械製造業界で広く用いられています。主に、平面加工、彫込み加工、ギア加工などの種類があり、それぞれ特定の用途に適しています。例えば、平面加工は機械のベースやフレーム製作に用いられ、彫込み加工は複雑な形状や模様を作るのに適しています。また、ギア加工は自動車のトランスミッションや機械の動力伝達部分に必要な部品を作る際に重宝されます。
このように、フライス加工の種類を理解し、適切に選択することで、製造の効率化や品質の向上が図れます。日本の製造業は、この技術を駆使して世界市場での競争力を保っており、様々な産業での応用が期待されています。結論として、フライス加工の種類とその応用範囲を把握することは、技術の可能性を最大限に引き出し、より良い製品を生み出すために重要です。
5. 鉄の切削加工方法
5-1. 鉄フライス加工の工程
鉄のフライス加工は、その多様性と幅広い応用範囲で知られています。この加工方法は、鉄を精密な形状やサイズに加工するために使用され、様々な業界で不可欠な技術となっています。フライス加工の種類には、平面削り、側面削り、溝削りなどがあり、これらは使用する工作機械や切削条件、加工する製品によって選ばれます。例えば、自動車部品の製造には精密な溝削りが求められる場合が多く、建設機械の部品では大きな平面削りが必要とされることもあります。日本では、技術の高さと精密な加工能力で、フライス加工は広く利用されており、その適用範囲は航空機の部品から家電製品、そして日常生活に欠かせない様々な製品まで及んでいます。これらの具体的な例を見ることで、鉄のフライス加工の重要性とその多様な応用がよく理解できます。結論として、鉄のフライス加工は多種多様な産業で重要な役割を果たしており、その技術は今後も発展し続けることが期待されます。
5-2. 切削条件の選定
工作機械を使用して鉄のフライス加工を行う際、適切な切削条件の選定が重要です。フライス加工は、鉄などの金属材料を加工するための方法の一つで、加工精度や仕上がりに大きく影響します。選定する際のポイントとして、加工する材料の種類、加工する形状、そして必要な精度を考慮する必要があります。例えば、鉄の場合、硬度が高いため、切削速度を調整したり、適切なフライスカッターを選択することが求められます。また、形状によっては、特殊なフライス盤やカッターを使用することで、加工時間を短縮し、コストを削減することが可能です。これらの選定を正しく行うことで、フライス加工の効率が大きく向上し、高品質な製品を生産することが可能になります。したがって、適切な切削条件の選定は、鉄のフライス加工における最初で最も重要なステップであると言えます。
5-3. 表面仕上げと精度向上のテクニック
鉄のフライス加工は、精密な製品を生み出すために欠かせない工程の一つです。この加工方法には様々な種類があり、それぞれが異なる応用範囲を持っています。フライス加工を選択する際には、製品の用途や必要な精度、表面仕上げの質を十分に考慮する必要があります。
例えば、粗加工用のフライスでは大量の材料を迅速に除去できますが、仕上がりの精度は高くありません。これに対して、仕上げ加工用のフライスを使用すると、より滑らかな表面仕上げと高い精度を実現できます。特に、日本製の精密工作機械を使用することで、更に細かい加工が可能になり、自動車部品や電子機器など、高度な技術を要する製品の製造に適しています。
また、特殊なフライス加工、例えば球面加工や複雑な形状の加工には、特定の形状を持ったフライスカッターが必要となります。これらのフライスは、一般的な製品には適用できない特殊な用途に使用されます。
結論として、鉄のフライス加工にはさまざまな種類があり、それぞれに特定の応用範囲が存在します。製品の用途や必要な精度、表面仕上げの質に基づいて適切な加工方法を選択することが、高品質な製品を生み出す鍵となります。
6. フライス加工の種類と特徴
6-1. 平面加工と形状加工
工作機械を使った鉄のフライス加工は、製造業において不可欠な技術の一つであり、種類に応じて幅広い応用範囲を持っています。平面加工と形状加工の二つに大きく分けられ、それぞれが特有の利点を持ちます。平面加工は、主に鉄の平面を削って平滑にする工程であり、部品の基礎となる面を作る際に用いられます。例えば、機械のベースプレートやフレームなど、精度を要する大きな面積の加工に適しています。一方、形状加工は、複雑な形状や溝、歯車などの加工に用いられ、精密な寸法と形状を持つ部品の製造に不可欠です。この技術を使えば、自動車のエンジン部品や航空機の部品など、高度な技術を要する製品の製造が可能となります。
これらの加工方式は、製品の品質と生産効率を大きく左右するため、適切な加工技術の選択が重要です。特に、日本のように精密機械製造が盛んな国では、フライス加工技術の進化と応用が、製造業の競争力を支える重要な要素となっています。結論として、工作機械を使った鉄のフライス加工は、その種類と応用範囲の広さにより、現代の製造業における中心的な役割を果たしていると言えるでしょう。
6-2. エンドミルとフェイスミルの違い
フライス加工は、鉄などの金属を削るために使用される工作機械の一つであり、主にエンドミルとフェイスミルの2種類があります。どちらも鉄の加工に欠かせない道具であり、その選択は加工する製品の種類によって異なります。
エンドミルは、主に複雑な形状や細かい部分の加工に優れています。たとえば、溝や穴を加工する際に使用され、その精度の高さから多くの工業製品の製造に不可欠です。一方、フェイスミルは、表面加工や大きな平面を削るのに適しています。大きな鉄板を均一に削りたい場合などに使用され、効率的に加工が行えます。
これらの工作機械を使用することで、鉄製品の製造はより効率的かつ正確になります。エンドミルとフェイスミルを適切に選択し使用することで、さまざまな種類の鉄製品を高品質に加工することが可能です。日本の製造業においても、これらの工作機械は重要な役割を果たしており、その適用範囲は広がり続けています。
6-3. 特殊フライス工具の紹介
工作機械を使った鉄のフライス加工は、精密な部品製造に不可欠です。この技術は、その多様な種類と応用範囲の広さから、幅広い産業で活用されています。フライス加工には、平面、曲面、溝など、さまざまな種類があり、それぞれ特定の用途に適しています。例えば、自動車のエンジン部品や航空機のフレーム製造には、高精度な平面フライス加工が用いられます。また、電子機器の小型部品では、細かい溝を切るのに溝加工フライスが選ばれます。
日本では、特に製造業の高度化が進む中で、フライス加工技術の重要性が高まっています。複雑な形状や極めて狭い部分の加工に適した特殊フライス工具も開発され、これにより、従来では困難だった加工が可能になりました。さらに、耐久性や加工速度の向上を求める声に応える形で、高機能なフライス工具も登場しています。
総じて、工作機械を用いた鉄のフライス加工の種類と応用範囲は、製品の品質向上や生産性の向上に直結します。日本の製造業にとって、これらの技術は競争力の源泉の一つとなっており、今後もその進化と応用範囲の拡大が期待されます。
7. フライス加工の応用範囲
7-1. 一般的な製品での使用例
工作機械を使った鉄のフライス加工は、精密部品の製造など、多岐に渡る分野でその価値を発揮しています。フライス加工の種類には、平面加工、溝加工、輪郭加工などがあり、それぞれ特定の応用範囲が存在します。例えば、平面加工は部品の平らな面を削り出す際に用いられ、機械のベースなどに使われます。一方、溝加工はギアやキー溝の製造に適しており、輪郭加工は複雑な形状を削り出すのに最適です。
これらの加工方法により、自動車の部品や建設機械、電子機器など、日常生活で広く使用されている製品の製造が可能になります。日本では、高い技術力を背景に、これらのフライス加工技術がさらに進化しており、より複雑で高品質な製品の需要に応えています。
結論として、鉄のフライス加工はその種類によって様々な製品製造に活用され、日本の製造業における重要な技術の一つとして位置づけられています。その応用範囲の広さと高い技術力は、今後も多くの分野での発展を支えるでしょう。
7-2. 精密機械加工分野での応用
鉄のフライス加工は、精密機械加工分野で広く応用されています。フライス加工とは、回転する工具を用いて材料から余分な部分を削り取る加工方法です。この技術は、その精度と効率性から、多岐にわたる産業で利用されています。特に、日本においては、自動車や電子機器などの製造における重要なプロセスとして位置づけられています。
フライス加工にはいくつかの種類があり、それぞれ異なる特徴と応用範囲を持っています。例えば、平面を加工するための平面フライスや、曲面加工に用いられる球面フライスなどがあります。これらの工具を使うことで、高い精度で複雑な形状の部品を製造することが可能になります。
日本では、特に精密機械加工技術が高い評価を受けており、フライス加工によって製造される部品は、国内外の多くの産業で用いられています。例えば、自動車産業では、エンジンの部品やシャシの加工に、電子機器産業では、スマートフォンやパソコンの内部構造の加工に、この技術が活用されています。
このように、鉄のフライス加工は、その種類と応用範囲の広さから、精密機械加工分野で非常に重要な役割を果たしています。今後もこの技術の発展が期待されており、より高度な加工技術の開発が進むことで、さらに多くの産業での応用が見込まれます。
7-3. 大量生産とカスタム製品の加工
鉄のフライス加工は、工作機械を使用して鉄を削り、形を整える工程です。この技術は、その精度の高さと多様な種類の加工方法により、幅広い産業で利用されています。フライス加工には、平面加工、溝加工、歯車加工など、様々な種類があり、それぞれ特定の応用範囲を持っています。例えば、平面加工は部品の表面を平滑にするのに使用され、溝加工は機械部品に必要な溝やスロットを作るのに適しています。歯車加工は、正確な歯車を製造するために不可欠です。
日本では、自動車産業や電子機器製造など、多岐にわたる分野で鉄のフライス加工が活用されています。これらの産業では、部品の精度が製品の品質を大きく左右するため、高度なフライス加工技術が求められます。また、カスタムメイドの部品製造にもフライス加工は欠かせない技術であり、特殊な形状やサイズの部品を正確に製造する能力が、多くの企業にとっての競争力となっています。
結論として、鉄のフライス加工はその種類の豊富さと応用の幅広さにより、現代の製造業において不可欠な技術です。日本における自動車産業や電子機器製造など、様々な分野でのその活用は、製品の品質向上と製造効率の向上に寄与しています。特に、精密な部品の製造が求められる現代において、フライス加工技術の重要性は益々高まっています。
8. 安全なフライス加工のためのガイドライン
8-1. 個人保護具と安全対策
鉄のフライス加工は、精密な部品製造において不可欠な工程であり、その種類と応用範囲は広い。フライス加工とは、回転する刃を用いて材料から不要な部分を削り取る加工方法で、鉄をはじめとする様々な金属に対応している。日本では、自動車産業や航空機産業など、高度な技術を要求される分野で特に重宝されている。
この加工方法には、平面・形状・溝などを加工するための様々な種類があり、それぞれ特定の用途に適している。例えば、エンドミルは平面加工に適しており、ボールエンドミルは曲面加工に最適である。これらの工具により、非常に複雑な形状も精密に加工することが可能となる。
また、最近では、CNC(コンピュータ数値制御)技術の進展により、より高度で複雑な加工が求められるようになっている。CNCフライス加工機を使用することで、従来手作業で行っていた繊細な作業も正確かつ迅速に実施できるようになり、生産性の向上に大きく貢献している。
結論として、鉄のフライス加工はその多様な加工方法と応用範囲により、日本の製造業における中核技術の一つとして位置づけられている。技術の進歩と共に、その重要性は今後もさらに高まることが予想される。
8-2. フライス盤のメンテナンスとトラブルシューティング
工作機械を使用して鉄のフライス加工を行うことは、製造業において非常に重要な役割を果たします。その理由は、フライス加工によって、鉄を含む多種多様な材料を正確かつ効率的に形状加工できるからです。特に日本においては、精密機械製造の伝統があり、この加工技術が高度に発展しています。
フライス加工の種類には、平面加工、溝加工、歯車加工などがあります。これらは、自動車の部品から、家電製品、さらには時計の小さな部品に至るまで、幅広い製品の製造に欠かせない技術です。例えば、自動車業界では、エンジン部品の精密な加工に平面フライス加工が用いられます。さらに、複雑な形状の金型を作成する際にも、フライス加工は不可欠です。
このように、フライス加工は多様な種類があり、それぞれが特定の応用範囲を持っています。加工技術の進歩により、より複雑で精密な部品の製造が可能になり、製品の品質向上に大きく寄与しています。日本の製造業が世界で競争力を持ち続けるためには、これらの加工技術の継続的な発展が不可欠です。フライス加工の種類と応用範囲を理解することで、より効率的で高品質な製品製造へと繋がるのです。
8-3. 加工中のリスク管理
工作機械を使った鉄のフライス加工には、多種多様なタイプがあり、それぞれ応用範囲が広がっています。これは、精密な形状を作り出す能力と、鉄という素材の持つ堅牢さから、工業製品の製造に不可欠であるからです。例えば、自動車のエンジン部品や、機械装置のギアなど、日常生活に密接に関連した製品の製造にも使用されています。このようなフライス加工は、特に高精度が求められる部品製造において、その真価を発揮します。加えて、フライス加工により、鉄の表面を滑らかにすることができるため、製品の耐久性や品質向上にも寄与しています。
さらに、フライス加工の技術進化により、より複雑で精密な設計の実現が可能になっており、これが新たな産業の発展を支えています。例えば、航空宇宙産業や医療機器産業では、この技術を利用して、高度な要求スペックを持つ部品を製造しています。
結論として、鉄のフライス加工はその種類の多様性と、幅広い応用範囲により、現代の製造業において欠かせない技術であると言えます。技術の進歩に伴い、その応用範囲はさらに広がっていくことでしょう。
9. 今後のフライス加工技術の展望
9-1. 自動化とロボティクスの影響
鉄のフライス加工は、多様な種類が存在し、その応用範囲は広いことが特徴です。フライス加工とは、回転する工具を用いて材料から不要な部分を削り取る加工方法であり、鉄を始めとする金属加工に欠かせない技術です。日本においても、工作機械を利用したこの方法は、自動車や電子機器、建築材料など、さまざまな産業で活用されています。
例えば、精密な部品を要求される自動車産業では、フライス加工によってエンジン部品やギアなどの加工が行われます。これらの部品は、高い耐久性と精密さが求められるため、特にフライス加工の精度が重要視されます。また、建築材料の加工においても、鉄骨の切断や穴あけなどにフライス加工が利用され、建築物の安全性と美観を高めるために欠かせない技術となっています。
このように、フライス加工はその多様な種類と応用範囲により、日本の産業において広く利用されています。精密な加工が可能なため、今後もさまざまな分野での応用が期待されます。そのため、フライス加工技術のさらなる発展と、これを取り巻く環境の整備は、日本の製造業を支える重要な要素となるでしょう。
9-2. 環境に優しい加工技術の開発
鉄のフライス加工は、多様な工業製品の生産に不可欠な技術です。この加工法が広範囲に応用される主な理由は、その精度と効率性にあります。鉄をはじめとする金属を正確に加工できるフライス加工は、自動車部品から建築材料まで、さまざまな製品の製造に不可欠です。たとえば、自動車のエンジン部品やギアなど、高い精度が求められる部分の加工には、この技術が欠かせません。また、フライス加工は種類が豊富で、平面、溝、歯車など、様々な形状を加工することが可能です。このようにフライス加工の種類と応用範囲の広さが、多岐にわたる製品の製造にとって重要な役割を果たしています。結論として、鉄のフライス加工の技術は、その精度と多様性により、現代の製造業において不可欠な存在であると言えます。
9-3. 教育と人材育成の重要性
鉄のフライス加工は、日本の製造業において基礎的かつ重要な技術であります。フライス加工は、金属製品の形やサイズを精密に加工するために用いられ、特に鉄の加工においてその利用範囲は広いです。この加工方法は、その種類に応じて異なる応用が可能であり、製品の品質向上に直結します。
鉄を用いたフライス加工には、平面加工、溝加工、ギア加工など多様な種類があります。例えば、平面加工は鉄の平らな面を削り出すことで、機械のベースやフレームなどの基礎部品を製造します。溝加工では、ピンやネジが収まる溝を製品に加え、部品同士の組み立てを可能にします。ギア加工は、精密な歯車を作り出し、機械の動力伝達部分に用いられます。
これらの加工技術は、自動車、航空機、建設機械など、幅広い分野において重要な役割を担っています。特に、精密さが求められる製品において、フライス加工の品質は製品全体の性能を左右するため、加工技術の進化に伴い、その応用範囲はさらに広がっています。
結論として、鉄のフライス加工は、多様な種類と応用範囲を持ち、日本の製造業における製品品質の向上に不可欠な技術です。この技術を活用することで、より高品質な製品の製造が可能となり、日本の製造業の競争力を高めることができます。
まとめ
工作機械を使った鉄のフライス加工には、さまざまな種類があります。これらの種類は、それぞれ異なる応用範囲を持っており、様々な目的に使用されています。これらの種類を理解し、適切に選択することで、鉄のフライス加工を効果的に行うことができます。
フライス加工で鉄を削る!初心者向けの加工種類と選び方
「フライス加工で鉄を削る!初心者向けの加工種類と選び方」へようこそ!
加工や製造の世界に初めて足を踏み入れる方々にとって、フライス加工はどのようなものか興味深いテーマとなることでしょう。鉄を削るという作業は、まるで工業の魔法のような印象を受けるかもしれませんが、その背後には様々な加工種類や選び方が存在します。
この記事では、フライス加工における基本的な情報から始め、初心者の方々が理解しやすいように加工の種類や選び方について詳しく解説していきます。鉄という素材を削るプロセスに興味がある方、またフライス加工に挑戦してみたい初心者の皆様にとって、このガイドはきっと役立つ情報源となることでしょう。
さあ、フライス加工の世界に踏み出して、鉄との相互作用を体験しましょう!
1. フライス加工の基本
1-1. フライス加工とは?基礎知識の解説
フライス加工は、鉄などの材料を削り、形を整える加工技術です。この技法は、特に初心者にとって選びやすい方法の一つと言えます。理由は、フライス加工が多様な種類の中で比較的安全で、容易に取り組めるからです。例えば、平面や曲面、さらには複雑な形状まで、幅広く加工が可能です。これは、様々なカッターが利用できるため、多くのニーズに対応できることを意味します。日本においても、フライス加工は工業製品の製造に欠かせない技術の一つとされています。
選び方のポイントとしては、まず加工したい鉄の種類や厚みを考慮することが大切です。それに応じて、適切なフライス加工機やカッターを選ぶ必要があります。また、加工の精度や速度も重要な要素です。これらを踏まえた上で、自分のプロジェクトに最適な機械と技術を選択することが、成功への鍵となります。
結論として、フライス加工は、鉄を含む様々な材料を加工する上で非常に便利で効率的な手法です。初心者でも取り組みやすく、多様な加工が可能であるため、選び方を理解し、適切な機械と技術を選択することが重要です。これにより、望む形状に鉄を加工することができるでしょう。
1-2. 鉄のフライス加工の特徴
フライス加工による鉄の削り方を学ぶことは、初心者にとって非常に意義深いスキルです。フライス加工とは、回転する工具を使用して材料から部品を削り取る加工方法です。特に鉄の加工においては、その硬さと耐久性から様々な産業で重宝されています。適切な加工種類を選び、効率良く加工を行うことが大切です。
フライス加工の種類には、平面加工、側面加工、溝加工などがあります。例えば、平面加工は鉄の表面を平らにするのに適しており、側面加工は側面の形状を整えるのに用いられます。一方、溝加工は、部品に溝や穴を開ける際に使用されます。これらの加工方法を適切に選ぶことで、求められる形状や精度の部品を効率良く製造できます。
選び方のポイントとして、加工する鉄の特性や加工後の用途を考慮することが挙げられます。硬度や耐久性が高い鉄を加工する場合には、切削抵抗が強いため、耐久性のある工具を選ぶ必要があります。また、加工後の部品がどのように使用されるかを考慮し、適切な加工方法を選択することが重要です。
結論として、フライス加工で鉄を削る際には、加工種類の理解と適切な選び方が鍵となります。初心者でも、種類の特徴を把握し、鉄の特性や用途を考慮して選ぶことで、高品質な部品を効率的に製造することが可能です。フライス加工のスキルを身につけることは、多様な分野での応用が期待できるため、非常に価値のある学びと言えるでしょう。
1-3. 加工種類の概要
フライス加工は、鉄を含む多くの材料を削るのに適した加工方法です。この技術は、特に初心者にとって、様々なプロジェクトで利用しやすい加工の一つです。その理由は、フライス加工が幅広い種類の中から選べる柔軟性を持っているからです。例えば、平面加工や溝加工、歯車加工など、目的に合わせて適切なフライス加工を選べます。重要なのは、加工したい鉄の形状や精度、加工後の仕上がりを考慮して選ぶことです。たとえば、細かいディテールが必要な場合は、小さなエンドミルを使用すると良いでしょう。また、大量生産には、高速で大きな材料を削れるカッターが適しています。最適な道具を選ぶことで、作業の効率化と品質の向上が期待できます。このようにフライス加工を活用することで、初心者でも様々な材料を自在に加工することが可能になり、プロジェクトの幅が広がります。フライス加工に適した種類を選び、その可能性を最大限に活用してみましょう。
2. フライス加工の種類と特徴
2-1. 平面加工とは
フライス加工において、鉄の削り方を学びたい初心者にとって、最初に理解すべきは加工種類の多様性と適切な選び方です。フライス加工は、工作機械を使用して鉄などの材料から不要な部分を削り取る加工方法です。この技術は精密な部品製作に不可欠で、特に日本の製造業で広く利用されています。
主なフライス加工には、平面加工、側面加工、溝加工などがあります。平面加工は、材料の表面を平らにする基本的な加工方法です。例えば、機械の基盤となる部品の表面加工に用いられます。側面加工は、材料の側面を削ることで、部品の幅や深さを調整します。溝加工は、ギアや連結部分などの溝を削り出すのに適しています。
適切な加工方法を選ぶには、製作したい部品の形状や寸法、そして仕上がりの精度が重要なポイントになります。例えば、非常に平滑な表面が必要な場合は平面加工を、複雑な形状の溝を必要とする場合は溝加工を選ぶことが適切です。
結論として、フライス加工における鉄の削り方を学ぶ初心者は、まず加工の種類とそれぞれの特徴を理解し、製作する部品の要件に最も合致した加工方法を選ぶことが大切です。これにより、効率的かつ精度高い加工が可能となります。
2-2. 形状加工の基本
フライス加工は、鉄などの金属を削り形を整える際に非常に役立つ技術です。特に初心者にとって、適切な加工方法と道具の選び方を理解することは重要です。フライス加工には様々な種類がありますが、適切なものを選ぶことで、作業効率が大幅に向上します。
まず、理由としては、フライス加工の種類によって加工できる形状や精度が異なり、作業の目的に最適な方法を選択することができるからです。例えば、平面を削る場合は面取りカッターを、複雑な形状を削る場合はボールエンドミルを使用します。これらの具体例からわかるように、加工する物の形状や求める精度に応じて適切なカッターを選ぶことが重要です。
また、材料の種類によって選ぶべきフライスの種類も変わってきます。鉄を加工する場合は、硬度が高く耐久性に優れたカッターを選ぶ必要があります。これにより、長時間の加工にも耐えられるようになり、作業効率が向上します。
結論として、フライス加工で鉄を削る際は、加工したい形状や材料の種類に応じて適切な加工方法と道具を選ぶことが肝心です。これにより、初心者でも効率的かつ精度高く加工作業を行えるようになります。選択肢が多く存在する中で、目的に合った方法を選ぶことが、成功の鍵となります。
2-3. 穴あけ加工の方法
フライス加工は、鉄などの金属を削ったり形を整えたりする際に用いられる重要な方法の一つであり、特に初心者にとって適切な加工種類を選ぶことが大切です。この加工方法の選び方を理解することで、作業の効率性と品質が大きく改善されます。具体的には、フライス加工には平面加工、側面加工、溝加工などがあり、それぞれ加工する物の形状や必要な精度に応じて選ばれます。例えば、平面加工は主に物の表面を平らにするのに用いられ、側面加工は物の側面を整えるのに適しています。溝加工は、部品に溝や穴を加工する際に使用されます。これらの加工種類を適切に選び、使用することで、鉄などの金属の加工がより簡単かつ効率的に行えるようになります。結論として、フライス加工を行う際には、加工する物の形状や必要な精度を考慮して最適な加工種類を選ぶことが重要です。これにより、初心者でも高品質な加工が可能となり、作業の効率も向上します。
3. 切削条件の考慮ポイント
3-1. フライス加工の切削条件とは
フライス加工による鉄の削り方を理解することは初心者にとって重要です。この加工種類は、精密な部品を作り出す際に不可欠であり、適切な方法を選ぶことが成功の鍵となります。フライス加工は、回転するカッターを使用して鉄などの材料から不要な部分を削り取る方法です。この加工は、その精度と効率性から多くの工業分野で用いられています。
フライス加工を選ぶ際に重要なのは、加工する材料の種類、必要な精度、および仕上がりの質です。例えば、粗加工では大きなカッターを使用して素早く材料を削り取りますが、仕上げ加工ではより小さなカッターを用いて細かい仕上げを行います。これにより、必要な精度と仕上がりを実現できます。
特定の例として、自動車部品の製造においてフライス加工が頻繁に用いられます。この分野では、部品の寸法精度が極めて重要であり、フライス加工によって高い精度を実現しています。加えて、フライス加工は複雑な形状の部品を効率的に製造することも可能で、製品の品質向上に寄与しています。
結論として、フライス加工は鉄を削る際に多くの利点をもたらします。初心者は、材料の種類、求める精度、仕上がりの質を考慮して加工種類を選ぶべきです。適切なフライス加工方法を選ぶことで、高品質な部品の製造が可能になります。
3-2. 鉄を削る際の条件設定
フライス加工は、様々な材料を加工する際に使用される方法の一つであり、特に鉄などの金属を削るのに適しています。初心者が鉄のフライス加工を行う際、適切な加工種類の選び方を知ることが重要です。理由は、鉄の性質に合わせた適切な加工種類を選択することで、加工精度の向上や効率的な作業が可能になるからです。
例えば、鉄の加工には、荒加工や仕上げ加工といった種類があります。荒加工は大量の材料を素早く削り取るために使用され、仕上げ加工は精密な表面仕上げを目的としています。また、鉄の硬さや加工する部品の形状に応じて、エンドミルやフェイスミルなどの工具を選択することも大切です。
フライス加工の種類を適切に選択することで、鉄の加工精度が向上し、仕上がりの品質を高めることができます。特に初心者にとって、加工する材料の特性を理解し、目的に応じた加工種類と工具を選択することが、成功への鍵となります。このように、鉄のフライス加工では、加工種類の選び方が重要であることがわかります。
3-3. 加工精度を高めるためのコツ
フライス加工で鉄を削る際の初心者向けの加工種類と選び方について、このような加工方法は高精度な部品を製造するために非常に重要です。フライス加工は、旋盤加工と並び鉄を削る代表的な方法の一つであり、様々な形状を持つ部品を加工することが可能です。
まず、フライス加工の種類には、平面加工、溝加工、ギア加工などがあります。これらは使用するフライス盤の種類やカッターによって異なります。例えば、平面加工にはエンドミルを使用し、溝加工にはスロットドリルを用います。初心者は、加工したい部品の形状と必要な精度を考慮しながら、適切なフライス加工の種類を選ぶことが重要です。
特に日本では、精密な工業製品が多く、フライス加工の需要も高いです。例えば、自動車産業や電子機器産業では、非常に高い精度が求められるため、フライス加工での丁寧な作業が不可欠です。
このように、フライス加工には様々な種類があり、それぞれに最適なカッターやフライス盤が存在します。初心者は、加工したい部品の形状や必要な精度、そして加工材料を考慮して、最適な加工方法を選択することが大切です。その選択が、最終的な部品の品質を左右するため、慎重に行う必要があります。
4. 初心者が学ぶべき機械加工の基礎
4-1. 機械加工の流れ
フライス加工により鉄を削ることは、初心者にとっても基本的な加工方法の一つです。この方法は、多様な形状を精密に削り出すことが可能で、特に金属加工において広く利用されています。その選び方にはいくつかのポイントがあり、適切な加工種類を理解することが重要です。
まず、フライス加工の種類には、平面、側面、形状など多岐にわたります。これらは加工する鉄の形状や必要な精度、加工する量によって選ばれます。例えば、複雑な形状を加工する場合は、形状加工が適しています。また、大量の鉄を一度に加工する必要がある場合は、高速で大量に削り取ることができる平面加工が適しています。
具体的な例として、自動車の部品や機械の歯車などは、フライス加工で精密な形状を削り出すことで製造されます。これらの部品は高い精度が要求されるため、適切な加工方法の選択が非常に重要です。
結論として、フライス加工で鉄を削る際は、加工する鉄の種類や形状、必要な精度に応じて加工方法を選択することが重要です。初心者でも基本を理解し、適切な加工種類を選ぶことで、幅広い金属加工に対応することができます。
4-2. 切削工具の選び方
フライス加工で鉄を削るとき、適切な切削工具の選び方は非常に重要です。この選び方を理解することで、効率的かつ正確に作業を行うことが可能になります。まず、フライス加工とは、回転する刃を使用して材料を削り取る加工方法です。この加工には、材料の種類や加工の精度に応じて多様な種類の切削工具が存在します。
鉄を削る場合、硬度や耐熱性に優れた工具を選ぶことが肝心です。例えば、超硬合金製のエンドミルは、その硬度と耐久性から鉄加工に適しています。さらに、刃の形状にも注目しましょう。鉄加工には、粗加工用のラフィングエンドミルや、仕上げ加工用のフラットエンドミルなど、目的に応じて選ぶ必要があります。
このように、鉄をフライス加工する際には、加工する材料の特性を考慮しながら、適した切削工具を選ぶことが重要です。この選択が作業の効率と品質を大きく左右します。適切な工具を選び、正確なフライス加工を行うことで、理想的な加工結果を得ることができます。
4-3. 加工機の種類と特性
フライス加工で鉄を削る際の初心者向けの加工種類と選び方について、分かりやすくご説明します。フライス加工は、金属などの材料を削って形を作る加工方法の一つで、特に鉄の加工において重要な役割を果たします。この加工方法は、精度が高く、複雑な形状も作り出すことができるため、さまざまな製品の製造に用いられています。
選び方のポイントとしては、加工する鉄の種類、加工の精度、そして加工する形状に合わせたフライス加工機を選ぶことが重要です。たとえば、軟鉄や硬鉄といった鉄の種類によって最適な切削条件が異なり、加工の精度にも影響します。また、直線的な形状を加工する場合はエンドミル、複雑な形状や曲線を加工する場合はボールエンドミルといった、目的に応じた刃物を選ぶことが大切です。
加工機の種類には、手動のものからCNC(コンピュータ数値制御)による自動加工機まであり、加工の複雑さや量に応じて選ぶ必要があります。初心者の方は、まずはシンプルな手動のフライス盤から始め、徐々に操作方法や特性を学びながら、より高度なCNCフライス加工機に移行するのがおすすめです。
このように、鉄を削るフライス加工には、適切な加工機の選び方があり、それによって加工の品質が大きく変わります。適切な加工種類を選び、正しく加工機を使うことで、高品質な製品を作り出すことができるでしょう。
5. NCプログラムの基礎
5-1. NCプログラムとは
フライス加工とは、鉄などの金属を削り、所望の形状に加工する技術です。初心者にとって、この手法を習得するのは非常に有益であり、加工種類の選び方を理解することが重要です。まず、フライス加工の目的は、製品の精度を高め、美しい仕上がりを実現することにあります。この技術にはいくつかの種類があり、代表的なものに平面加工、溝加工、輪郭加工などがあります。各々の加工方法は異なる特性を持ち、使用する工具や加工法によって最終製品の品質が大きく変わります。
例えば、平面加工は最も基本的なフライス加工で、平らな面を作るのに適しています。溝加工は、V字型やU字型の溝を作るのに用いられ、複雑な形状も加工可能です。輪郭加工は、製品の外形を整えるのに用いられ、高い精度が求められます。これらの加工種類を適切に選ぶことで、製品の品質を大きく向上させることができます。
しかし、加工種類を選ぶ際には、加工したい鉄の種類、加工機械の性能、そして最終製品の用途を考慮する必要があります。これらの要素を総合的に判断し、最適な加工方法を選択することが重要です。
結論として、フライス加工で鉄を削る際は、加工種類の選び方が非常に重要です。加工方法を適切に選ぶことで、高品質の製品を効率良く生産することが可能になります。初心者は、さまざまな加工種類を理解し、それぞれの特性を活かした選択を心がけるべきです。
5-2. 初心者向けプログラムの書き方
フライス加工は、鉄などの金属を削って形を整える技術で、初心者でも取り組みやすい加工方法の一つです。この加工法を選ぶ理由は、その汎用性と、特定の形状への加工が比較的容易である点にあります。たとえば、平面や溝、歯車など、様々な形状を作り出すことが可能です。これは、フライス加工機の多様な刃や、加工方法によって実現されます。初心者にとって重要なのは、使用する機械の種類と目的に応じた適切な刃を選択することです。例えば、大きな平面を削る場合には面取りカッターを、細かい溝を加工する際にはエンドミルを選ぶなど、作業内容に合わせた選択が必要です。このようにフライス加工は、適切な刃と加工方法を選ぶことで、多様な形状の鉄製品を製作することが可能です。これらの点から、フライス加工は初心者でも取り組みやすく、様々な創造的な可能性を秘めた加工技術であると結論づけることができます。
5-3. NCプログラムのトラブルシューティング
フライス加工を学び始めた初心者にとって、鉄を削ることは基本中の基本です。この加工方法は、精密な形状を作り出すために欠かせません。フライス加工の種類は多岐にわたりますが、選択する際のポイントを理解することが重要です。
フライス加工には、平面加工や溝加工、輪郭加工などがあり、それぞれ鉄を削る目的と適用範囲が異なります。例えば、平面加工は主に平らな面を作るのに使用され、溝加工は溝やキー溝などを作るのに適しています。選択する際は、加工したい製品の形状や精度要求を考慮することが肝心です。
特に日本製のフライス機を使用する場合、精度の高さや操作性の良さから、初心者でも比較的簡単に扱うことができます。しかし、初心者が最も注意すべき点は、適切なカッターの選択です。カッターには様々な形状や材質があり、加工する鉄の種類や硬さによって最適なものを選ぶ必要があります。
結論として、フライス加工で鉄を削る際、加工種類の理解と正しいカッターの選択が重要であると言えます。これらに注意を払いながら技術を磨けば、初心者でも高品質な加工が可能になります。
6. 半導体部品の金属加工入門
6-1. 半導体部品の加工の概要
フライス加工において鉄を削ることは、多くの工業製品を製造する上で不可欠な技術です。特に初心者にとって、適切な加工種類を選ぶことは重要であり、その理解を深めることが成功への鍵を握っています。鉄のフライス加工にはいくつかの種類があり、それぞれ特定の用途に最適化されています。例えば、平面加工は鉄の表面を平滑にするのに適しており、端面加工は材料の端を整えるのに用いられます。また、穴あけ加工は、正確な位置に穴を開ける必要がある場合に重宝されます。
これらの加工種類を理解し、プロジェクトの要件に応じて最適なものを選択することが、効率的かつ効果的な加工のための基本です。例えば、精密な部品を製造する場合、表面仕上げの質を重視し、平面加工や端面加工が適しているかもしれません。一方、機械部品においては、穴あけ加工の精度が重要視されることがあります。
結論として、フライス加工で鉄を削る際には、加工種類の理解と選択が重要です。適切な加工方法を選ぶことで、製品の品質を向上させることができ、効率的な製造プロセスを実現することが可能となります。これは、特に加工の初心者にとっては、成功のための重要なステップと言えるでしょう。
6-2. フライス加工による半導体部品の製造
フライス加工で鉄を加工することは、初心者にとってもアクセスしやすい方法の一つです。フライス加工とは、回転する工具を使用して材料から不要な部分を削り取る加工技術のことを指します。この加工方法は、特に鉄などの金属を扱う際に有効であり、精密な形状や平滑な表面を実現することが可能です。さまざまな種類のフライス加工が存在し、それぞれに適した材料や用途があります。
例えば、平面を加工する場合には、エンドミルを使用した平面加工が適しています。また、曲面や複雑な形状を加工したい場合には、ボールエンドミルを用いた曲面加工が選ばれることが多いです。さらに、溝や穴を加工する場合には、ドリルやリーマといった工具が使用されます。
初心者がフライス加工で鉄を加工する際には、まず加工したい形状や精度、そして材料の特性を考慮して、適切な加工種類を選択することが重要です。この選択によって、加工の効率や品質が大きく変わるため、事前にしっかりとした計画を立てることが推奨されます。
フライス加工は、多様な加工が可能なため、鉄をはじめとする多くの材料を精密に加工することができます。初心者でも、基本的な知識を身につけ、適切な種類を選ぶことで、思い通りの製品を作り出すことが可能です。
6-3. 精密加工のポイント
フライス加工を用いて鉄を削る方法は初心者にも親しみやすい加工技術の一つです。この技術は、特定の種類の加工に適しており、選び方を理解することが重要です。理由は、適切なフライス加工を選択することで、作業の効率が大きく向上し、加工品の品質も高めることができるからです。たとえば、鉄を平滑に削りたい場合、エンドミルやフェースミルといった加工種類が適しています。エンドミルは、細かい部品の仕上げに最適で、フェースミルは大きな面を均一に削るのに適しています。
さらに、フライス加工機の選び方も重要です。加工する鉄の種類や形状、加工の精密度によって、最適な機械が異なります。例えば、より複雑な形状を加工する場合は、多軸のフライス加工機が適しています。これにより、加工の幅が広がり、より高度な技術を必要とする部品の製造も可能になります。
結論として、フライス加工で鉄を削る際には、加工する鉄の特性を理解し、適切な加工種類および機械を選択することが、加工技術の向上に繋がります。初心者は、基本的な加工種類から始めて徐々に高度な技術に挑戦し、適切な機械を選ぶ知識を深めていくことが重要です。
7. 実践!鉄のフライス加工
7-1. 初心者が始める前の準備
フライス加工で鉄を削ることは、工業分野で広く行われている技術の一つです。初心者にとって、適切な加工種類を選ぶことが重要です。フライス加工の中でも、特に鉄を削るには、適した種類の選択が必須です。この選択プロセスには、加工物のサイズ、形状、そして加工後の用途が大きく影響します。たとえば、平面を加工する際は平面フライスが適している一方で、複雑な形状や細かい部品の加工には、エンドミルやボールエンドミルが適切です。また、大量生産には、能率的に加工できるカッターの選択が重要になります。
加工種類の選択を適切に行うことで、加工精度の向上、加工時間の短縮、そしてコスト削減に繋がります。これらの点を考慮し、初心者はまず、加工したい鉄の特性を理解し、加工目的に合ったフライス加工の種類を選ぶことから始めるべきです。その上で、具体的な加工方法やカッター選びに進むことが、成功への第一歩となります。フライス加工で鉄を削る作業は、適切な知識と工夫により、初心者でも高い品質の加工を実現することができます。
7-2. ステップバイステップの加工プロセス
フライス加工で鉄を削る際、初心者が知っておくべき加工種類と選び方について解説します。フライス加工は、鉄などの金属を削って形を作る加工方法です。この技術は、精密な部品作りに欠かせないものであり、正しい種類の選択が重要です。
理由として、鉄のフライス加工には、平面を削る「平面加工」、溝をつける「溝加工」、複雑な形状を削り出す「形状加工」など、様々な種類があります。それぞれの加工方法には最適な機械やツールが存在し、適切な選択が加工品質に直結します。
例えば、平面加工にはエンドミル、溝加工にはスロットドリル、形状加工にはボールエンドミルなど、目的に応じた工具を選ぶことが大切です。また、硬い鉄を加工する場合、耐久性に優れたカーバイド製の工具が推奨されます。
結論として、フライス加工において鉄を削る作業は、適切な加工種類の知識と、それに応じた工具の選択が品質向上に繋がります。初心者でもこれらの基本を押さえておくことで、加工技術の向上につながるでしょう。
7-3. 加工後の仕上げと検査
フライス加工を用いて鉄を削ることは、初心者にとっても非常にアクセスしやすい方法です。これは、使用する機械の種類によって、さまざまな形状やサイズの鉄を加工できるからです。加工の種類には、平面加工、溝加工、歯車加工などがあり、それぞれ特定の用途に適しています。例えば、平面加工は、板材の表面を平らにするのに用いられます。溝加工は、部品を組み立てる際に必要な溝や穴を作るのに使われます。そして、歯車加工は、機械の動力伝達部分に必須な歯車を製造するのに不可欠です。
フライス加工の機械選びでは、加工したい鉄の形状や大きさ、そして加工の精度が重要なポイントになります。初心者は、操作が比較的簡単で、多様な加工が可能な機械を選ぶと良いでしょう。加えて、機械のメンテナンスや安全性についても考慮する必要があります。具体的には、小型のテーブル型フライス機械が初心者には扱いやすく、また幅広い加工が可能です。
結論として、フライス加工は鉄を削るための非常に効果的な方法であり、様々な種類の加工が可能です。初心者が機械を選ぶ際には、加工の目的、機械の操作性、メンテナンスのしやすさなどを考慮することが大切です。適切な機械を選ぶことで、高品質な加工が期待できます。
まとめ
鉄を削るフライス加工は、初心者でもさまざまな種類の加工方法を選択できることが特長です。各種加工方法における適切な工具や技術を理解すれば、より効果的な加工が可能となります。また、適切な工具選びが成功の鍵となります。初心者におすすめの適切な加工方法を選び、安全かつ効果的な鉄の削り方を学びましょう。
鉄をどう削る?フライス加工の方法と種類についてのアドバイス
鉄をどう削るか、それはフライス加工の本質です。鉄を加工する際、どのような方法や種類があるのか気になりますよね。本記事では、鉄を効果的に削るためのフライス加工の方法と種類について詳しくご紹介します。鉄という素材の特性を踏まえて、どのようにフライス加工を行うか、そのポイントやアドバイスを解説します。鋼鉄の世界に足を踏み入れる前に、ぜひこのガイドを参考にしてみてください。
1. 金属加工の世界へようこそ
1-1. 金属加工とは?
フライス加工は、鉄をはじめとした金属材料を削って形を作る一般的な方法です。結論から言うと、フライス加工の方法と種類を理解することは、工業製品の製造において不可欠です。理由は、フライス加工によって、精密な部品作りが可能となり、製品の質と効率を高めることができるからです。たとえば、自動車のエンジン部品や家電製品の内部構造など、私たちの日常生活に欠かせない多くの製品が、フライス加工によって作られています。
具体的には、フライス加工には「平面加工」「側面加工」「形状加工」などの種類があります。それぞれの加工方法には適した用途があり、例えば平面加工は、材料の平らな面を削り出すのに適しています。側面加工は、材料の側面を整えるのに、形状加工は複雑な形状を作り出すのに適しています。これらの加工方法を適切に選ぶことで、目的に合った高精度な製品を効率よく製造することが可能となります。
結論として、フライス加工はその方法と種類の理解を通じて、製品製造の精度と効率を大きく向上させることができる重要な技術です。日本の製造業が世界で競争力を維持するためにも、この加工技術のさらなる研究と活用が期待されます。
1-2. 鉄を中心とした金属の特性
鉄をどう削るかは、製造現場で常に問われる課題です。フライス加工はその解決策の一つであり、多様性と精密性が求められる場所において特に重宝されています。フライス加工の方法は大きく分けて二つあり、平面を削るための「平面フライス加工」と、複雑な形状を削り出す「形状フライス加工」です。これらは鉄をはじめとする金属の加工に幅広く用いられ、特に日本の製造業では欠かせない技術となっています。
例えば、自動車の部品製造では、エンジン部分のボディやギアなど、精密な加工が必要な部分にフライス加工が用いられます。この加工法により、耐久性が高く、精度の高い部品を製造できるため、品質の向上に大きく貢献しています。さらに、フライス加工は種類が多岐にわたるため、それぞれの製品に適した方法を選択することができ、加工の柔軟性が高いという特長があります。
このように、フライス加工は鉄をはじめとする金属の加工において、その方法の選択肢の広さと、加工の精度の高さから、製造業で広く採用されている技術です。これらの理由から、フライス加工を理解し、適切な方法を選択することは、製品の品質向上に不可欠です。
1-3. 金属加工の種類と特徴
鉄の加工方法の中でもフライス加工は、精度が高く複雑な形状を実現できる技術として重宝されています。主に、鉄などの金属を削るために用いられるフライス加工には、さまざまな種類があります。例えば、平面を加工するための平面フライス加工や、溝を作るための溝加工フライス、曲面を加工するための形状加工フライスなどが挙げられます。これらのフライス加工の方法により、高い精度と複雑な形状の加工が可能になります。
日本では、製造業の高度な技術力が求められる中、フライス加工はそれを支える重要な技術の一つとされています。特に、自動車や航空機の部品製造において、その精密さと高い加工能力が重宝されています。フライス加工の技術が進化することで、より効率的で精度の高い製品製造が可能になり、製品の品質向上に貢献しています。
結論として、フライス加工は鉄をはじめとする金属を加工する上で欠かせない技術であり、その種類や方法を理解することは、製造業において高い品質の製品を提供するために非常に重要です。日本の製造業が世界的に競争力を保つためにも、フライス加工の技術の更なる発展が期待されています。
2. フライス加工の基本
2-1. フライス加工とは?
フライス加工は、金属素材、特に鉄を精密に削るための加工法の一つであり、その方法と種類は多岐にわたります。この加工法の最大の利点は、複雑な形状や細かい部品でも高い精度で加工できる点にあります。たとえば、機械部品や自動車のコンポーネントなど、日本の製造業で広く用いられている技術です。
フライス加工の種類には、大きく分けて平面加工、側面加工、形状加工などがあります。平面加工は、主に物の表面を平滑にするのに用いられ、側面加工は物の側面を削り出すのに用いられます。形状加工では、ギアのような複雑な形状を作り出すことができます。これらの技術を駆使することで、精密な部品製作が可能となります。
特に日本では、高度な技術力を要するフライス加工が、製造業の品質向上に不可欠な役割を果たしています。例えば、自動車産業では、エンジン部品やトランスミッションなどの重要なコンポーネントを製造する際に、この加工法が用いられています。これらの部品は、車の性能に直結するため、高い精度が求められます。
結論として、フライス加工は多様な種類と高度な技術を要する加工法ですが、それによって複雑で精密な部品製造が可能となり、日本の製造業において重要な位置を占めています。
2-2. フライス加工の歴史
フライス加工は、鉄などの金属を削るための効率的な方法であり、その種類も多岐にわたります。この加工法は、精密な部品製造に不可欠で、その有効性の背景には、特定の道具と技術の組み合わせがあります。たとえば、エンドミルやフェースミルなどの異なるカッターがあり、それぞれに特定の用途があります。エンドミルは細かい加工に適しており、フェースミルは表面を均一に削るのに用いられます。また、CNCフライス加工機を使用することで、高度な精度と複雑な形状の部品を効率的に製造することが可能になります。フライス加工のこのような種類と方法を適切に選択し活用することで、製造業はより質の高い製品を市場に提供できるようになります。したがって、鉄を削る方法としてのフライス加工の理解と活用は、現代の製造業における重要な要素であると言えるでしょう。
2-3. フライス加工のメリットとデメリット
フライス加工は、鉄を削るための有効な方法の一つですが、そのメリットとデメリットが存在します。フライス加工の最大の利点は、その高い精度と柔軟性にあります。複雑な形状や細かい部品も、フライス加工によって正確に製造することが可能です。例えば、自動車のエンジン部品や、精密機器のコンポーネントなどがこの方法で加工されています。
しかし、フライス加工にはデメリットもあります。特に、加工にかかるコストが高い点や、大量生産には向かない場合があることです。加工時間が長くかかるため、短期間で大量の部品を生産する必要がある場合には、他の加工方法が選ばれることが多いです。
結論として、フライス加工は鉄を含む多様な材料を高精度に加工できる点で大きなメリットがありますが、コストや生産効率を考慮する必要があります。適切なプロジェクトにフライス加工を選択することで、その利点を最大限に活かすことができるでしょう。
3. 鉄のフライス加工の種類
3-1. 平面フライス加工
フライス加工は、鉄をはじめとする金属材料を削ることで形を整える加工技術です。特に日本において、精密な部品製造に欠かせない技術として重宝されています。この技術の中でも、平面フライス加工は最も基本的かつ広く用いられる方法の一つです。
平面フライス加工の特徴は、回転する刃を用いて材料の表面を平らに削ることにあります。この方法によって、非常に滑らかで精密な表面が得られるため、機械部品の基盤として理想的です。例えば、自動車のエンジン部品や工具の製造においては、この加工法によって精度の高い製品が生産されています。
また、平面フライス加工は、その種類によって様々な特性を持っています。例えば、エンドミルを用いた加工では、深い溝や複雑な形状の加工が可能です。一方、フェイスミルを使用する方法では、より広い面積を一度に加工できるため、効率的に作業を進めることができます。
最終的に、平面フライス加工はその適用範囲の広さと加工精度の高さから、様々な産業分野で不可欠な技術となっています。精密な部品製造が求められる現代において、この加工技術を習得し、活用することが、より高品質な製品を市場に提供する鍵となるでしょう。
3-2. 形状フライス加工
鉄を削る方法の中でも、フライス加工はその精度と効率から広く採用されています。この加工方法は、特定の回転刃を使用して鉄などの材料から不要な部分を削り取る技術です。その種類には、面取りから複雑な形状の作成に至るまで多岐にわたります。具体例として、平面を削る平面フライス加工や、溝を切る溝切り加工などがあります。これらは、製品の精度を向上させるためや、特定の機能を持たせるために不可欠です。また、最近では、コンピュータ制御によるCNCフライス加工が人気を集めており、より複雑で精密な形状の製作が可能になっています。このように、フライス加工はその種類に応じて多様な用途に利用されており、製造業の現場では欠かせない技術となっています。その適切な方法と種類の選択によって、製品の品質と生産効率が大きく向上します。
3-3. 端面フライス加工
鉄を削る方法には様々ありますが、フライス加工はその中でも特に重要な技術です。この加工技術には多くの種類があり、それぞれに適した用途があります。例えば、端面フライス加工は、鉄の平らな面を削るのに特に適しています。この方法を使用することで、非常に滑らかな表面を得ることができます。
端面フライス加工の主な理由は、精度の高い表面を必要とする部品の製造にあります。たとえば、機械の部品など、細部にわたる精密さが求められる場合には、この加工方法が選ばれます。この加工は、フライス盤の回転するカッターを使用して、鉄の表面を削り取ることで実現されます。特に、フライス盤に装着された多数の刃が鉄の表面を均一に削ることで、非常に平滑な仕上がりを実現します。
日本においても、この端面フライス加工は多くの製造業で採用されています。自動車や電子機器の部品製造では、この加工技術によって高い品質が保証されています。これは、製品の信頼性と性能を向上させる上で非常に重要です。
結論として、端面フライス加工は、鉄を削る方法の中でも特に重要な技術です。その多様な種類と精密さが、多くの製造業での利用を可能にしています。日本の製造業においても、この加工技術は品質向上のために広く使われており、その重要性は今後も変わらないでしょう。
3-4. 特殊フライス加工
フライス加工は、精密な形状やサイズの鉄を加工する際に欠かせない方法の一つです。この技術は、鉄を削るために使用される多様な種類のカッターによって、さまざまな形状やサイズの加工が可能になります。具体的な例としては、平面加工用のエンドミルや、溝加工用のスロットドリル、複雑な形状を作り出すためのボールエンドミルなどがあります。これらのカッターは、それぞれ異なる形状の鉄を削り出すために最適化されています。例えば、エンドミルは、主に表面を平らにする加工に用いられ、スロットドリルは、内部に溝を刻む作業に適しています。このように、フライス加工の種類は多岐にわたり、用途や加工する鉄の形状によって適切なカッターを選択する必要があります。最終的に、フライス加工を通じて、精度の高い鉄製品を製造することが可能になります。この加工方法は、日本の製造業においても重要な役割を担っており、高品質な製品を効率よく生産するために不可欠です。
4. フライス加工の技術的ポイント
4-1. 切削条件の設定
フライス加工は、金属などの材料を削ることで形を整える加工方法の一つです。特に、鉄のフライス加工には様々な種類が存在し、それぞれに最適な切削条件があります。これには、切削速度、送り速度、切り込み深さなどが含まれ、正確な設定が求められます。例えば、粗加工では高い切削速度と大きな切り込み深さが可能ですが、仕上げ加工ではより低い切削速度と浅い切り込みで精度を高める必要があります。日本においても、このようなフライス加工の技術は高い精度が求められるため、各種類に応じた適切な切削条件の選定が不可欠です。この選定を正しく行うことで、効率的かつ高品質な加工が可能になります。結論として、フライス加工には様々な種類があり、それぞれに最適な切削条件の設定が重要です。これにより、鉄などの材料を精密に加工することが可能になるため、日本における製造業での応用が広がっています。
4-2. フライス刃の選択
フライス加工は、鉄などの金属を削り形を整える工程で、その方法と種類は多岐にわたります。この加工方法の選択は、加工する物の材質、形状、そして必要な精度によって変わってきます。例えば、粗い加工であれば、大きな切削量で素早く削り取ることが可能な粗加工用のフライス刃が適しています。一方で、仕上げ加工では、精度を要するため、細かい切削が可能な仕上げ用のフライス刃を選ぶ必要があります。日本では、特に精密な加工が求められる場合には、超硬フライスやダイヤモンドコーティングされたフライスなど、特殊なフライス刃が用いられることもあります。これらの選択によって、加工の効率や完成度が大きく変わってきます。そのため、目的に応じたフライス刃の選択は、フライス加工において非常に重要なポイントとなります。
4-3. 加工精度を高める方法
フライス加工は、鉄などの金属を削って形を作る工程であり、その精度は製品の品質に大きく影響します。加工精度を高める方法には、適切な種類のフライス加工機を選ぶことが重要です。日本では、様々な種類のフライス加工機があり、それぞれ特定の目的に最適化されています。例えば、立型フライス盤は複雑な形状の加工に適しており、横型フライス盤は大きなワークを効率的に加工できます。
加工精度を高めるためには、加工条件を適切に設定することも重要です。切削速度、送り速度、切り込みの深さなど、細かい条件を製品の材質や形状に応じて調整する必要があります。さらに、鋭い切削工具を使用し、定期的に交換することで、加工面の仕上がりを向上させることができます。
日本の製造業では、これらの方法を駆使してフライス加工の精度を高めています。特に、高精度な加工が求められる自動車産業や航空宇宙産業では、最新のフライス加工技術の研究開発が積極的に行われています。結論として、適切なフライス加工機の選定、加工条件の最適化、鋭い切削工具の使用は、鉄の加工精度を高める上で不可欠です。これらの方法を踏まえ、日本は引き続き高品質な製品の製造を目指しています。
5. 切削工具の種類と特徴
5-1. フライス工具の種類
フライス加工は、鉄などの金属を削るために広く用いられている技術です。この方法は、精密な形状を作り出すことが可能で、様々な種類のフライス工具があります。フライス加工の方法と工具の種類を理解することは、効率的で高品質な製品を製造する上で重要です。
フライス加工には主に、平面を削るための平フライスや、溝を加工するためのエンドミル、複雑な曲線を加工するためのボールエンドミルなどがあります。例えば、エンドミルは様々な材質の金属を加工することができ、細かい部品製造に適しています。また、ボールエンドミルは3次元の複雑な形状を加工する際に用いられ、高い精度を要求される製品に不可欠です。
これらの工具を適切に選択し、使用することで、製品の品質を向上させることができます。フライス加工の技術と工具の種類を理解し、それぞれの特性を生かすことが、高品質な製品を効率的に製造する鍵です。
5-2. 工具材質の種類と特性
フライス加工は、鉄などの材料を削るために広く用いられる加工方法です。この技術は、多種多様な形状を精密に作り出すことが可能で、その用途は非常に広範囲にわたります。フライス加工の効果的な使用は、その種類を理解することから始まります。
フライス加工には、平面を削るための平フライス、溝を削るためのエンドミル、複雑な形状を加工するためのボールエンドミルなど、目的に応じた多くの種類があります。たとえば、エンドミルは、内側の角を持つ溝を削るのに適しています。一方、ボールエンドミルは、曲面や立体的な形状を加工する際に用いられます。
また、材質にも注目する必要があります。鉄を加工する場合には、硬質のカーバイド製のフライス刃が一般的に使われます。このような刃は、耐久性が高く、精密な加工が可能です。
フライス加工の種類と適切な工具を選ぶことで、鉄などの材料を効率良く、精密に加工することができます。特に、日本の製造業においては、高い技術力を要する部品の製造にフライス加工が不可欠です。この技術を理解し、適用することで、製品の品質向上につながります。
5-3. 工具の保守と管理
フライス加工は、鉄などの材料を削って形を整える加工技術の一つです。この方法は精密な部品作成に欠かせないため、多くの工場で採用されています。フライス加工には様々な種類があり、それぞれ異なる特徴を持ちます。例えば、平面を削るための平面フライス加工や、溝を削るための溝フライス加工、複雑な形状を作るための形状フライス加工などがあります。これらの方法を適切に選択することで、求める形状や精度の部品を効率よく製造できます。
フライス加工の種類を理解し、それぞれの特性に応じた選択を行うことは、製造プロセスの最適化に繋がります。日本では特に、精密機械部品の製造においてこの技術が重宝されています。例えば、自動車や飛行機の部品、電子機器の小型部品など、私たちの生活に密接に関わる製品の多くが、フライス加工によって作られています。
フライス加工の適切な方法と種類を選択することで、効率的かつ高品質な製品の製造が可能になります。この技術の理解と適用は、製造業においてますます重要になってきており、日本の高い製造技術を支える基盤の一つと言えるでしょう。
6. 金属の切削性に関する考察
6-1. 鉄の切削性とは?
フライス加工は、鉄を含む多様な材料を削るために用いられる加工方法です。この技術は、精密な形状やサイズの部品製造に不可欠であり、日本を含む世界中の製造業で広く採用されています。フライス加工には様々な種類があり、それぞれに特徴があるため、適切な方法を選択することが重要です。
フライス加工の理由としては、その高い精度と柔軟性が挙げられます。例えば、平面、溝、歯車など、複雑な形状を持つ部品もこの加工により作成することが可能です。また、使用するカッターの種類によって、大量生産にも対応することができ、経済性も優れています。
具体例として、エンドミルと呼ばれるカッターを使用する方法があります。これは、比較的に小さい平面や溝を加工する際に適しており、精密な作業が要求される電子部品などの製造に活用されています。別の例として、フェースミルを使用する方法があり、これは大きな平面を効率良く加工するのに適しています。
結論として、フライス加工はその精度と柔軟性により、多様な製造ニーズに対応することができる技術です。適切なカッターの選択により、様々な種類の加工が可能になり、日本の製造業を支える重要な役割を果たしています。
6-2. 切削性を左右する要因
フライス加工は、鉄を含む多種多様な材料を削るための重要な方法です。この加工手法の優れた点は、さまざまな形状を精密に加工できる点にあります。フライス加工の種類には、平面加工、側面加工、形状加工などがあり、それぞれの用途に応じて最適な方法が選ばれます。例えば、平面加工は、材料の表面を平らに仕上げるのに適しており、機械部品の基盤となる面を作る際に用いられます。側面加工は、材料の側面を加工する際に利用され、溝や段差のあるデザインを実現できます。形状加工では、複雑な曲線や角度を持つ部品を削り出すことが可能です。これらの加工方法を適切に選択し、用いることで、高精度で複雑な形状の部品を効率良く製造することができます。フライス加工の技術は、自動車産業や航空機産業をはじめとする多くの分野で重宝されています。結論として、フライス加工はその多様性と精密さから、製造業で不可欠な技術であり、適切な種類の選択がその成功を左右します。
6-3. 切削性向上のためのアプローチ
鉄を削るフライス加工は、製造業で広く使用される重要な技術です。この方法は、精密な部品の加工や、複雑な形状を持つ製品の生産に不可欠であり、その種類と適用方法によって、加工の質や効率が大きく変わります。フライス加工には、主に平面加工、溝加工、歯車加工などの種類があり、それぞれに適した工具や技術が必要です。例えば、平面加工にはエンドミルを使用し、溝加工にはスロットドリルが適しています。特に日本では、高度な精密加工技術の発展に伴い、フライス加工の需要が高まっています。
フライス加工の効率と品質を上げるためには、適切な工具の選択と、加工する物質の性質を理解することが重要です。鉄などの硬い材料を加工する場合には、耐久性の高いカーバイド製の工具が推奨されます。実際の生産現場では、被加工物の材質や形状、求められる精度に応じて、最適なフライス加工方法と工具が選ばれています。
このように、フライス加工は多種多様な技術を駆使して鉄を削り、製品を作り出すために不可欠な工程です。それぞれの加工方法と工具の選択が、最終製品の品質に直結するため、技術者は常に最適な方法を模索し、適用しています。フライス加工の理解と適切な技術の適用により、日本の製造業は高品質な製品を効率的に生産することができるのです。
7. 安全かつ効率的なフライス加工のために
7-1. 加工時の安全対策
フライス加工は、鉄などの材料を削って形を整える技術であり、工業製品の製造に不可欠です。この方法は種々の材料に適用可能で、特に日本では多くの工場で用いられています。フライス加工の適切な方法と種類を理解することは、高品質な製品を効率的に生産する上で非常に重要です。
フライス加工には、主に平面を削る平面加工、溝やキー溝を作る溝加工、複雑な形状を作る形状加工など、様々な種類があります。また、使用する切削工具によっても、エンドミルで行うエンドミリング、フェースミルで行うフェースミリングなどの方法に分かれます。
例えば、自動車のエンジン部品や機械のギアなど、精密な形状が求められる製品は、複合的なフライス加工を必要とします。これらの製品では、平滑な表面や正確な寸法が必須であり、適切な加工方法の選択が品質に大きく影響します。
結論として、フライス加工はその種類や方法の選択が製品の品質に直結します。特に日本のように製造業が盛んな国では、様々な材料や製品に適した加工技術の知識が求められます。フライス加工の適切な使用は、効率的な製造プロセスと高品質な製品の生産の鍵となります。
7-2. 効率的な作業の進め方
フライス加工は、鉄などの金属を削る加工方法の一つで、その種類や使い方によって、多様な形状を生み出すことができます。具体的には、フライス加工には平面を削る平面加工、溝を削る溝加工、複雑な形状を削る形状加工など、様々な種類があります。例えば、平面加工は機械の部品の基盤を作る際に用いられ、溝加工は歯車などの細かいパーツを加工するのに適しています。また、形状加工は三次元的な複雑な形状を削り出す際に用いられ、製品のデザイン性を高めることができます。これらの加工方法を適切に選択し、組み合わせることで、効率的かつ精度高く鉄を削ることが可能になります。したがって、目的に応じたフライス加工の方法と種類を理解し選択することが、効率的な作業の進め方に繋がります。
7-3. 注意すべきトラブルと対策方法
フライス加工は、鉄などの材料を削って形を作る技術の一つです。この加工法は精密かつ柔軟性が高いため、多種多様な製品の製造に欠かせません。フライス加工には様々な種類があり、適切な方法を選ぶことが品質向上の鍵となります。
まず、フライス加工には主に平面加工、溝加工、形状加工などがあります。平面加工は、主に材料の表面を平らにするために使用されます。一方、溝加工は、歯車やキー溝などの溝を切ることに特化しています。形状加工では、複雑な形状や曲線を加工することができます。これらの加工方法を選ぶ際には、加工する製品の形状や精度、そして生産効率を考慮する必要があります。
例えば、高精度が要求される航空機の部品製造では、形状加工がよく使われます。また、大量生産で効率を重視する場合は、平面加工や溝加工が適しています。このように、加工方法を製品の要求に合わせて選ぶことが大切です。
最終的に、フライス加工の方法と種類を適切に選択することで、高品質な製品を効率良く生産することが可能です。各種類の特徴を理解し、用途に応じて最適な加工方法を選ぶことが、製造工程の成功に繋がるでしょう。
まとめ
鉄を加工する際、フライス加工はさまざまな種類があります。鉄の特性や加工する部品によって、適切なフライス加工の方法を選択することが重要です。鉄の硬さや形状によって、エンドミルやボーリングツールなど異なる種類のフライス加工が使用されます。適切な工具選びと正確な加工技術によって、効率的で精密な加工が可能となります。
効率化のカギ!鉄を使ったフライス加工向けエンドミルの種類と特徴
効率的なフライス加工を行う際に欠かせない道具、エンドミル。特に鉄を使ったフライス加工において、正しい種類のエンドミルを選ぶことは極めて重要です。本記事では、鉄を使ったフライス加工向けエンドミルの種類と特徴について詳しく解説していきます。エンドミルの選び方や使い方によって、加工効率や品質に大きな影響が及ぶことをご存知でしょうか。さまざまなエンドミルの種類を理解し、効率的な鉄のフライス加工を実現するためのカギを握りましょう。
1. フライス加工の基礎知識
1-1. フライス加工とは
フライス加工は、鉄などの金属材料を削ることで形を整える加工技術です。この加工において、エンドミルと呼ばれる切削工具の種類と特徴を理解することは効率化のカギを握ります。エンドミルは、材料を削り取るための重要なツールであり、その種類によって加工の品質や速度が大きく変わります。たとえば、高速度鋼(HSS)製のエンドミルは一般的に耐久性が高く、多くの鉄加工現場で利用されています。しかし、より硬度の高い材料や精密な加工が求められる場合には、超硬合金製のエンドミルが選ばれることが多いです。また、最近では、コーティング技術の進化により、耐熱性や摩耗抵抗が向上したエンドミルも登場しており、長時間の加工でも性能を維持できるようになっています。このように、目的や材料に応じて適切なエンドミルを選択することで、加工の効率化が図れるのです。エンドミルの選択が、鉄を用いたフライス加工の品質向上と効率化に直結していることが分かります。
1-2. 切削加工とフライス加工の違い
フライス加工は、切削加工の一種であり、鉄などの金属を加工する際に欠かせない技術です。特に、エンドミルを使用したフライス加工は、その精度や効率性から多くの産業で重宝されています。エンドミルは、その材質や形状によってさまざまな種類があり、それぞれ特徴が異なります。このため、加工する鉄の種類や目的に応じて適切なエンドミルを選ぶことが効率化のカギとなります。
例えば、一般的な鉄の加工には、耐久性と切削能力に優れた高速度鋼(HSS)製のエンドミルが適しています。さらに、より硬い鉄や高精度が求められる場合には、カーバイド製のエンドミルが選ばれます。これらカーバイド製のエンドミルは、切れ味が鋭く長持ちするため、複雑で精密な加工が必要な場合に特に有効です。
また、最近では、加工効率を高めるために、表面処理が施されたエンドミルも登場しています。これらは、加工中の摩耗を減少させることで、工具寿命を延ばし、より長時間の連続加工を可能にします。特に、チタンやアルミニウムなど特殊なコーティングは、鉄の加工において摩擦熱を軽減し、切削性能を向上させる効果があります。
結論として、鉄を使ったフライス加工において、エンドミルの選択は非常に重要です。加工する鉄の種類や目的に合わせて適切なエンドミルを選ぶことで、加工効率の向上と高い精度の製品を実現することができます。エンドミルの種類と特徴を理解し、効率的なフライス加工を目指しましょう。
1-3. 鉄を使用する際のフライス加工のメリット
鉄を使用したフライス加工が注目されているのは、その効率性と加工品質の高さにあります。鉄は硬度が高く耐久性に優れているため、精密な部品作成に最適です。この加工には様々なエンドミルが利用されるが、それぞれに特徴があります。たとえば、高速鋼(HSS)製のエンドミルは、比較的安価で一般的な鉄加工に適しています。また、超硬エンドミルは、硬度が非常に高く、長寿命であるため、難削材の加工や高精度加工に最適です。さらに、コーティングされたエンドミルは、耐摩耗性を高め、長期間の使用を可能にします。これらの特性を理解し、材料や加工内容に応じて適切なエンドミルを選択することが、鉄を使ったフライス加工の効率化の鍵となります。最終的に、適切なエンドミルの選択は、加工時間の短縮とコスト削減に繋がり、高品質な製品を効率的に生産することが可能です。
2. 鉄フライス加工向けエンドミルの種類
2-1. エンドミルの基本形状
フライス加工においてエンドミルは鉄などの金属加工に不可欠な工具であり、それぞれ異なる種類が特定の用途に適しています。適切なエンドミルの選択は、加工の効率化のカギを握っています。例えば、平面加工には平形エンドミル、曲面加工にはボールエンドミルが適しており、それぞれが素材への負担を減らしつつ、精度高く加工を行うために最適化されています。また、鉄のように硬い材料を加工する際には、耐久性と切削効率に優れたコーティングが施されたエンドミルが選ばれます。
特に日本では、精密な金属加工技術が求められることが多く、それぞれのエンドミルが持つ特徴を理解し、用途に応じて適切なものを選択することが重要です。例えば、長寿命で耐熱性に優れたカーバイドエンドミルは、連続して高負荷の加工を行う際に適しています。
結論として、エンドミルの種類と特徴を理解し、加工する材料や加工内容に最適なものを選ぶことが、効率的なフライス加工を実現する上で極めて重要です。適切な選択を行うことで、加工時間の短縮、コスト削減、そして製品品質の向上が期待できます。
2-2. 材質によるエンドミルの分類
フライス加工での効率化には、適切なエンドミルの選択が欠かせません。特に鉄を加工する場合、その材質に適したエンドミルを選ぶことが重要です。日本においても、鉄加工用のエンドミルは多種多様に展開されており、それぞれに特徴があります。本文では、鉄加工向けのエンドミルの種類とその特徴を簡潔に紹介します。
例えば、高速度鋼(HSS)製のエンドミルは、その耐久性と加工速度のバランスが良いため、一般的な鉄加工に適しています。また、超硬質合金製のエンドミルは、硬度が非常に高く、長時間の使用に耐えることができますが、その分、価格も高くなります。さらに、コーティングされたエンドミルは、耐摩耗性を高めることで長寿命を実現し、効率的な加工を可能にします。特に、チタンやアルミニウムなどの特殊なコーティングは、特定の加工条件下での性能を向上させることが期待されます。
これらのエンドミルは、それぞれに特定の加工条件や材質に適した利点を持っています。適切なエンドミルを選択することで、加工の効率化はもちろん、工具の耐久性を高め、コスト削減にも繋がります。したがって、加工を行う際には、加工材料の特性を十分に理解し、最適なエンドミルを選択することが鍵となります。
2-3. 加工ニーズに合わせたエンドミルの選択
フライス加工における効率化の鍵は、使用するエンドミルの種類と特徴を理解して、加工する材料に合わせた選択をすることにあります。特に鉄を加工する場合、エンドミルの選び方一つで加工速度や仕上がりのクオリティが大きく変わります。鉄向けエンドミルには、粗加工用、仕上げ加工用、高硬度材加工用など、目的に応じた様々な種類があります。例えば、粗加工用エンドミルは、大量の材料を高速で削り取ることができる反面、仕上がりの精度は高くないため、初期の形状を作り出す段階で使用されます。一方、仕上げ加工用エンドミルは、精度の高い仕上がりが求められる最終工程に適しています。このように、加工ニーズに合わせてエンドミルを選ぶことで、効率性はもちろん、加工品質の向上にも寄与するのです。結局のところ、フライス加工で求められるのは、加工効率と品質のバランスです。それを実現するためには、鉄加工に適したエンドミルの特徴を把握し、目的に応じて最適なものを選択することが不可欠です。
3. フライス加工の効率化テクニック
3-1. 正しいエンドミルの選択方法
フライス加工において鉄材を扱う際、適切なエンドミルの選択は効率化のカギとなります。鉄は硬くて頑丈な材料であるため、特定のエンドミルの種類と特徴を理解することが重要です。例えば、高速度鋼(HSS)製のエンドミルは、一般的な加工に適しており、コストパフォーマンスに優れています。一方、超硬エンドミルは硬度が高く、耐久性に優れているため、鉄を含む硬質材料の加工に適しています。また、コーティングされたエンドミルは、摩耗や熱への抵抗力が高く、長寿命を実現します。適切なエンドミルを選択することで、加工時間の短縮、精度の向上、工具コストの削減といった多くの利点があります。したがって、加工対象の材料や加工条件を考慮して、最も適したエンドミルを選ぶことが、効率的な加工を実現する上で重要です。
3-2. 加工パラメータの最適化
鉄を用いたフライス加工向けエンドミルは、製造業における効率化の鍵を握っています。その理由は、鉄加工に特化したエンドミルが持つ、材料の特性に合わせた切削性能と耐久性にあります。例えば、高速度鋼(HSS)製のエンドミルは、一般的な鉄加工に適しており、複雑な形状の加工にも対応可能です。さらに、超硬合金製のエンドミルは、硬度の高い材料や、高速加工に最適で、長寿命を実現します。さらに、コーティング技術の進歩により、耐熱性や摩耗耐性が向上したエンドミルも登場しており、加工効率のさらなる向上が期待できます。これらの特長を活かし、適切なエンドミルを選択することで、鉄加工の精度と効率は大きく向上します。結論として、鉄を使ったフライス加工において、エンドミルの選択は極めて重要であり、種類と特徴を理解することが、効率化への第一歩と言えるでしょう。
3-3. 効率的な工具経路の設計
鉄を使ったフライス加工において、エンドミルは効率化のカギとなります。鉄加工向けエンドミルは、その形状や材質により様々な種類があり、それぞれ特徴が存在します。これらの違いを理解することで、作業の質と速度を向上させることができます。
例えば、平面加工には平底のエンドミルが使用されます。このタイプは底面がフラットであるため、底面仕上げが綺麗になります。一方、側面加工には、球形やラジアス付きのエンドミルが適しており、曲線や斜面の加工が可能です。また、硬い材質の鉄を加工する場合には、耐久性の高い超硬素材を使用したエンドミルが推奨されます。
さらに、エンドミルの刃数も加工の効率に影響します。多刃数のエンドミルは、細かい仕上がりが要求される精密加工に適していますが、切りくずの除去が難しくなることがあります。一方、少刃数のエンドミルは、粗加工や切りくずの除去が容易ですが、仕上がりが荒くなりがちです。
このように、鉄を使ったフライス加工向けエンドミルの種類と特徴を理解することは、工程の効率化に不可欠です。適切なエンドミルの選択によって、作業の速度と品質を同時に向上させることが可能となります。
4. フライス加工の問題点と解決策
4-1. カッターマークの除去方法
鉄を使ったフライス加工におけるエンドミルの種類と特徴は、加工の効率化に不可欠です。エンドミルは、鉄などの金属を削るための工具であり、その種類や特徴を理解することが、高品質な製品を効率的に生産する鍵となります。例えば、平面加工に適したフラットエンドミル、曲線や斜面加工に適したボールエンドミル、そして、高硬度材料の精密加工に適したカーバイド製のエンドミルなどがあります。特に、カーバイド製のエンドミルは、耐摩耗性や耐熱性に優れており、長時間の加工作業にも耐えることができます。これらのエンドミルを適切に選択し使用することにより、加工時間の短縮や製品の精度向上を実現できます。結論として、鉄を使ったフライス加工で求められる効率化と高品質な成果を得るためには、エンドミルの種類と特徴を理解し、適切なものを選択することが重要です。
4-2. 切削加工におけるビビりの原因と対策
切削加工においてビビりは、製品の品質に大きな影響を及ぼす問題の一つです。ビビりの原因は多岐にわたりますが、主なものは工具と加工物の振動による不安定な接触です。この問題に対処するためには、適切な工具の選択が重要であり、特に鉄のフライス加工においてはエンドミルの種類と特徴を理解することがカギとなります。
例えば、粗加工用エンドミルは大きな切削力に耐えうるよう設計されており、素早い材料の除去が可能です。一方で、仕上げ加工用エンドミルは細かいフルートを有しているため、より滑らかな表面仕上げを実現します。また、硬質材料用エンドミルは特殊なコーティングが施されており、耐摩耗性に優れています。
これらエンドミルの選択により、ビビりを抑制し、高い加工品質を保持することができます。つまり、鉄を用いたフライス加工では、エンドミルの種類と特徴を適切に選択することが、効率化及び品質向上のカギとなるのです。
4-3. 加工精度を向上させるためのポイント
鉄を使ったフライス加工において、加工精度を向上させる鍵となるのは適切なエンドミルの選択です。エンドミルは、材料を削るための刃物であり、その種類と特徴を理解することが非常に重要です。例えば、粗加工用エンドミルは、大量の材料を迅速に除去することに特化しています。一方、仕上げ加工用エンドミルは、精密な表面仕上げを目指す際に適しています。また、特殊な形状を加工する場合には、ボールエンドミルやラジアスエンドミルが有効です。これらは曲面加工に最適で、滑らかな表面を実現できます。
日本では、高品質なエンドミルが豊富に提供されており、正確な加工が要求される多くの産業で活用されています。特に、耐久性と精度を兼ね備えたエンドミルの選択によって、効率的かつ経済的な加工が可能になります。したがって、加工精度を向上させるためには、加工する鉄の種類や目的に応じたエンドミルの選択が不可欠です。このように、適切なエンドミルの選択を通じて、鉄を使ったフライス加工の効率化と精度向上を実現することが、非常に重要です。
5. SS400の切削加工特性
5-1. SS400とは
鉄を使ったフライス加工において、エンドミルは重要な役割を果たしています。その中でも、特にSS400などの材質に適したエンドミルの種類と特徴を把握することは、加工効率化のカギとなります。SS400は、一般的な構造用鋼材として広く利用されているため、その加工には適切なエンドミルの選択が欠かせません。
まず、SS400を加工する際によく使用されるのが、2枚刃や4枚刃のエンドミルです。これらは、一般的な溝加工や側面加工に適しており、特に4枚刃は仕上げ加工にも優れた結果を示します。さらに、コーティングされたエンドミルは、耐摩耗性が高く、長寿命であるため、繰り返しの加工作業にも最適です。
具体的な例として、SS400の加工には、チタンコーティングやアルミニウムコーティングが施されたエンドミルが有効です。これらのコーティングは、エンドミルの耐熱性を高め、鉄の加工中に発生しやすい熱からエンドミルを保護します。その結果、加工精度が向上し、製品の品質も高まります。
結論として、SS400などの鉄を加工する際には、適切なエンドミルの選択が不可欠です。特に、コーティングされたエンドミルは、耐久性と加工能力の向上に寄与し、結果的に加工効率を大幅に高めることができます。適切なツールを選ぶことで、高品質な製品を効率的に生産することが可能になります。
5-2. SS400の加工に適したエンドミルの選定
鉄を使ったフライス加工では、適切なエンドミルの選定が効率化のカギを握っています。特に、加工によく使われるSS400などの一般的な鋼材に対しては、その硬さや加工性に合わせたエンドミルが必要です。例えば、SS400の加工には、切削抵抗が低く、長寿命であることが求められるカーバイド製のエンドミルが適しています。これにより、精度の高い加工が可能となり、加工時間の短縮やコスト削減にも繋がります。さらに、加工面の仕上がりを向上させたい場合には、コーティングされたエンドミルを選ぶと良いでしょう。コーティングは、摩耗を減らして切削性能を保つことで、より滑らかな表面を実現します。したがって、SS400のような鉄のフライス加工においては、カーバイド製やコーティングされたエンドミルの選定が、効率と品質の向上に不可欠です。これにより、加工効率の高い生産活動が可能となり、結果的に生産性の向上に寄与します。
5-3. SS400切削時の注意点と対策
鉄を使ったフライス加工でエンドミルを効率的に使用することは、製造業にとって非常に重要です。特に、SS400のような一般的な鋼材を加工する際には、適切なエンドミルの選択が鍵を握ります。SS400を加工する際の主な問題点は、材料の硬さによってエンドミルが摩耗しやすいことです。これを解決するためには、材質やコーティングが施されたエンドミルを選ぶことが効果的です。例えば、チタンコーティングされたエンドミルは、耐摩耗性に優れ、長い寿命を実現できます。また、カーバイド製のエンドミルは、高硬度の材料加工に適しており、SS400のような材質でも滑らかな加工面を実現できます。
結論として、SS400のフライス加工においては、エンドミルの材質やコーティングに注目することで、摩耗を抑え、効率的な加工を実現できます。適切なエンドミルを選択することが、コスト削減と生産性向上に直結するため、製造現場における重要なポイントとなります。
まとめ
鉄を使ったフライス加工向けエンドミルには様々な種類と特徴があります。これらを理解することで、フライス加工の効率化において重要な要素を把握することができます。それぞれのエンドミルがどのような鉄材料に適しているのか、その特性や利点を把握することが重要です。また、積極的な情報収集と正しい使用法を身につけることで、作業効率を向上させることが可能です。
フライスによる鉄加工:種類別アプローチとその利点
鉄加工の中でも、フライス加工は非常に重要な技術の一つです。フライスによる鉄加工は、さまざまな種類があり、それぞれ異なる利点や特性を持っています。本記事では、鉄のフライス加工に焦点を当て、異なる種類のアプローチについて紹介します。鉄のフライス加工における種類別のアプローチやその利点を理解することで、この重要な加工技術についてより深く理解し、効果的に活用することができるでしょう。さまざまなフライス加工の技術について知識を深め、鉄加工における可能性を広げていきましょう。
1. フライス加工の基礎知識
1-1. フライス加工とは
フライス加工とは、鉄を含む様々な材料を削ることで形状を整える加工方法の一つです。この技術は、精密な寸法と形状を必要とする部品製造において、非常に重要な役割を果たします。フライス加工にはいくつか種類があり、それぞれに特徴と利点があります。例えば、平面フライス加工は、主に平らな面を削るのに使用され、精度の高い平面を得ることができます。また、形状フライス加工では、複雑な形状やカーブを加工することが可能であり、より複雑な部品の製造に適しています。さらに、溝加工フライスは、溝やキー溝などを削るのに用いられ、部品同士の組み合わせ部分の加工に不可欠です。これらの加工方法は、製品の機能性や信頼性を高めるために、日本の製造業において広く利用されています。フライス加工の種類に応じた適切なアプローチを選択することで、製品の品質向上と生産効率の向上が期待できます。このように、フライス加工は、精密な部品製造に不可欠な技術であり、その種類別にアプローチを理解することが、製造プロセスの成功につながります。
1-2. 鉄を使ったフライス加工のプロセス
鉄を使ったフライス加工は、精密さと効率性を追求する製造業にとって非常に重要な工程の一つです。この加工方法は、機械の性能を最大限に活用し、鉄材料を特定の形状に加工するために用いられます。さまざまな種類のフライス加工が存在し、それぞれが独自の利点を持っています。例えば、平面フライス加工は大きな表面を平らに仕上げるのに適しており、形状フライス加工は複雑な形状やプロファイルを作成するのに用いられます。また、正確な穴を開けるためには、穴あけフライス加工が選ばれます。
これらの加工方法は、製品の品質を向上させるだけでなく、生産効率を高めるという大きな利点があります。特に、日本のような高度な製造技術を持つ国では、精密加工が求められる場面が多く、フライス加工はその要求を満たす重要な技術です。例えば、自動車産業やロボティクス分野では、部品の精度が非常に重要とされており、フライス加工によってその精度を実現しています。
結論として、フライス加工は鉄を使用した製造業において不可欠な工程であり、その種類に応じて様々な利点をもたらします。日本の製造業者にとって、これらの技術を採用し、さらに精度の高い製品を生産することは、国際競争力を保つ上で極めて重要です。
1-3. フライス加工機の概要と種類
フライス加工による鉄加工は、精密さと柔軟性を兼ね備えた技術であり、日本における製造業において重要な役割を果たしています。フライス加工には多様な種類があり、それぞれが特定の利点を持っています。この加工方法が広く利用される理由は、その高い精度と効率性にあります。例えば、平面フライス加工は大きな面を平らに仕上げるのに適しており、溝加工や形状加工には端面フライス加工が用いられます。この技術の特徴は、切削の精度が非常に高く、複雑な形状や細部の加工も可能であることです。さらに、CNCフライス加工機を使用することで、プログラミングされた通りに精密な加工が可能となり、製品の品質向上に貢献しています。結論として、フライス加工はその種類に応じて様々な利点を持ち、日本の製造業において不可欠な技術となっています。その精密さと多様性により、高品質な製品の製造が可能となっているのです。
1-4. フライスの種類と特徴
フライス加工は、鉄を含むさまざまな材料を切削するための重要な技術です。特に日本において、精密な鉄加工が求められる場面は多く、フライス加工の役割は非常に大きいです。この技術にはいくつかの種類があり、それぞれに独特の利点があります。
まず、フライス加工の主な種類には、面フライス、端フライス、スロットフライスなどがあります。面フライスは、大きな平面を効率良く仕上げることができる点が特徴です。一方、端フライスは、細かい部分や複雑な形状を加工するのに適しています。スロットフライスは、溝やキー溝を加工する際に用いられ、精密な作業には欠かせません。
具体的な例として、自動車のエンジン部品や航空機のフレームなど、高い精度と強度が求められる製品の加工に、これらのフライス加工技術が活用されています。特に日本の製造業では、これらの技術を用いて、世界市場で競争力を持つ製品を生み出しています。
結論として、フライス加工はその種類によってさまざまな利点を持ち、日本の製造業における重要な技術の一つです。これらの技術を適切に選択し、活用することで、高品質で競争力のある製品を製造することが可能になります。
2. フライス加工の種類別アプローチ
2-1. 平面フライス加工
フライス加工は、鉄などの金属を削って形を整える工程であり、特に日本では精密な加工が求められる場面で頻繁に使用されます。この加工方法の中でも、平面フライス加工は最も基本的かつ広く利用されている種類の一つです。このアプローチの利点は、その高い精度と効率性にあります。たとえば、機械部品や工具など、平面が必要とされる製品を製造する際には、この方法が選ばれます。高速で動作するフライスカッターは、一度に大きな面積を均一に削ることができ、その結果として生産効率が大幅に向上します。さらに、最新のCNC(コンピュータ数値制御)技術を用いることで、複雑な形状や細かい仕上がりが求められる部品でも、高い精度で加工することが可能となります。このように、平面フライス加工は、その高い精度と効率性により、幅広い工業製品の製造に不可欠な技術として、今後も日本を含む世界各地で積極的に利用されていくことが予想されます。
2-2. 形状フライス加工
フライス加工において、鉄はその多様な用途と加工のしやすさから、広く利用される素材の一つです。特に、形状フライス加工は鉄製品の精密さと機能性を高めるのに不可欠です。この加工方法には、平面、側面、溝、歯車など、様々な種類があり、それぞれに特徴があるため、使用される場面も異なります。たとえば、平面フライス加工は、主に鉄板の表面を平滑にするのに用いられます。側面フライス加工は、鉄のブロックの側面を加工するのに適しています。また、溝加工は、機械部品に溝を作る際に重宝され、歯車加工は、精密な歯車を製造するために欠かせません。これらの加工方法は、製品の品質と機能を向上させるために重要です。例えば、鉄道車両や自動車、機械設備の部品には、これらの加工技術が活用されています。結論として、形状フライス加工は、鉄を使用した製品の性能を高め、幅広い分野での利用を可能にするために不可欠な技術です。
2-3. 端面フライス加工
端面フライス加工は、鉄加工の中でも特に重要な方法の一つであり、その利点は多岐にわたります。この加工方法では、カッターの端面を用いて材料の表面を削り取ることで、平滑な面を作り出すことができます。端面フライス加工の最大の利点は、高い精度と速い加工速度を実現できる点にあります。例えば、大量生産が必要な自動車部品や建築材料の加工には、この方法が頻繁に利用されています。また、端面フライス加工は、複雑な形状や大きなサイズの鉄材にも柔軟に対応できるため、用途の幅が広いという特長があります。総じて、端面フライス加工は、その高精度と効率性により、鉄加工における重要な役割を果たしているのです。
2-4. 特殊フライス加工
フライス加工は、鉄を含む多種多様な材料の加工に利用される方法の一つであり、その種類には様々なアプローチが存在します。特に、日本における精密な鉄加工において、その技術の進展は著しいです。フライス加工の主な利点は、高い精度や複雑な形状の実現可能性にあります。この加工法により、幅広い産業分野でのニーズに応えることができるため、非常に重要な技術と言えます。
例えば、端面フライス加工は、鉄の平面を削るのに適しており、機械の部品製作などに用いられます。一方で、円筒フライス加工は、軸や穴などの円形の加工に適しています。これらの方法により、高い精密度が要求される部品の製造が可能になります。また、特殊なカスタムフライスを使用し、特定のプロファイルを持つ部品の製作も行われています。これにより、従来の方法では難しかった複雑なデザインの実現が可能になりました。
結論として、フライス加工は鉄を始めとする多様な材料の加工に不可欠な技術であり、種類に応じて様々な利点があります。これにより、日本の製造業は高い競争力を保ちつつ、様々な産業での要求に応えることができます。フライス加工の更なる技術進化が期待される中、その利用範囲は今後も広がり続けるでしょう。
3. フライス加工の利点とデメリット
3-1. フライス加工の利点
フライス加工は日本において鉄などの金属を加工する際に広く利用されています。この技術の利点は多岐にわたり、それには様々な種類が存在します。まず、フライス加工による精密さが挙げられます。この方法では、非常に細かい部分まで正確に加工することが可能になります。例えば、複雑な形状の部品や細かい溝を持つ部品など、精密な作業が求められる場合に非常に有効です。
また、フライス加工には大量生産に適した種類も存在します。特に、CNCフライス加工機を使用することで、プログラミングにより一定の品質を持つ部品を短時間で大量に生産することが可能です。これにより、生産コストの削減にも繋がります。
さらに、フライス加工は多様な材質に対応可能であり、鉄だけでなく、アルミニウムや銅など、様々な金属材料の加工に適用することができます。これにより、さまざまな産業での利用が可能になります。
結論として、フライス加工はその精密さ、大量生産能力、そして多材質への対応力という三つの大きな利点を持っています。これらの利点は、日本の製造業において非常に重要な役割を果たしており、今後もその需要は高まることが予想されます。
3-2. フライス加工のデメリット
フライスによる鉄加工は、その精密さと柔軟性から多くの産業で利用されています。この加工法の利点は、加工種類の多様性と高い精度にあります。例えば、平面加工、溝加工、歯車加工など、さまざまな加工が一台のフライス機で可能です。これにより、製造工程が簡素化され、生産性が向上するという利点があります。
特に、日本の製造業では、フライス加工が重要な役割を果たしています。小ロット多品種の生産に適しており、短納期での製品供給が可能です。また、フライス加工は、加工面の仕上がりがきれいで、高精度な部品製造に不可欠です。
しかし、フライス加工には、専門的な技術と知識が求められるという点も見逃せません。操作が複雑で、熟練した技術者による管理が必要とされます。このため、技術者の育成と維持が、フライス加工を効果的に活用する上での重要な課題となっています。
結論として、フライスによる鉄加工はその多様性と高い精度で多くの利点を持ちますが、技術者の育成がその効果を最大限に引き出す鍵となります。
3-3. 金属加工におけるフライスの利点とデメリットの比較
フライス加工は鉄をはじめとする金属加工に広く用いられており、その種類に応じて様々な利点があります。フライス加工では、異なる形状のカッターを使用して鉄を削ることで、精密な形状を作り出すことができます。この技術の利点は、高い精度と柔軟性にあります。例えば、平面加工、側面加工、溝加工など、多様な加工が一つの機械で可能です。さらに、CNC(コンピュータ数値制御)技術の組み合わせにより、複雑な形状でも高い再現性と効率を実現しています。
しかし、フライス加工にはデメリットも存在します。特に、硬い材料の加工時にはカッターの摩耗が早く、精度の維持やコスト面での課題があります。また、大量生産には向かない場合もあります。しかし、適切な種類のフライスと最適な加工条件の選定により、これらのデメリットは最小限に抑えることが可能です。
結論として、フライス加工はその高い精度と柔軟性により、鉄を含む金属加工において重要な役割を果たしています。種類に応じたアプローチにより、多様な加工が実現可能であり、その利点は多岐にわたります。適切な技術選定と条件設定により、フライス加工はさらにその可能性を広げることでしょう。
4. フライス加工の適用場面と注意点
4-1. フライス加工の適用場面
フライス加工は、日本の鉄加工業界で広く使用されている技術です。この方法は、精密な部品作成から大型の構造物まで、幅広い用途に利用されます。その理由として、フライス加工は種類に応じて多様な利点を提供するからです。例えば、平面フライス加工は大きな面を均一に仕上げるのに適しており、角フライス加工は複雑な形状や溝の加工に優れています。また、立型フライス加工機を使用することで、狭い箇所や特殊な形状の加工も可能になります。
これらのフライス加工の種類によって、鉄加工業者は様々な製品のニーズに応えることができるのです。具体的には、自動車部品や建築材料、さらには精密機械の部品製造など、幅広い分野でフライス加工が活躍しています。この技術の応用により、製造業の生産性と品質が向上し、結果として日本の工業全体の競争力が高まっています。
総じて、フライス加工はその種類別のアプローチによって、日本の鉄加工業界における多様なニーズに対応しています。この技術が持つ幅広い適用性と、それによってもたらされる利点は、今後も多くの産業での発展に寄与することでしょう。
4-2. フライス加工の際の注意点
フライス加工は、鉄や他の金属を削るために使われる加工技術の一つですが、その種類やアプローチは多岐にわたります。効率よく、正確な加工を行うためには、適切なフライス加工方法を選択することが重要です。フライス加工には、平面加工、側面加工、溝加工などがあり、それぞれに利点があります。例えば、平面加工では、広い面を効率的に削ることができます。この方法は、素材の表面を平滑化する際に最適です。側面加工では、素材の側面を綺麗に仕上げることができ、溝加工は、特定の形状を素材に加える際に用います。これらの方法を適切に選択することで、目的に合った加工が可能になり、作業の効率化や精度の向上を実現できます。日本においても、精密な鉄加工が求められる場面は多く、フライス加工の技術は幅広い産業で活用されています。結論として、フライス加工はその種類に応じて多様な利点を持ち、適切な加工方法を選択することで、効率的かつ精密な鉄加工を行うことが可能です。
5. フライス加工と旋盤加工の比較
5-1. フライス加工と旋盤加工の基本的な違い
フライス加工は、鉄などの金属を削るために用いられる精密加工技術の一つです。これは、特に日本の製造業で広く利用されており、種類に応じてさまざまな利点があります。具体的には、平面、溝、複雑な形状などを加工するのに適していることが挙げられます。その利点の一つは、フライス加工により、非常に精密な仕上がりが可能であることです。例えば、エンジン部品や医療機器など、高い精度が要求される製品の製造において重宝されています。
一方、旋盤加工は主に円形の物体を加工するのに適していますが、フライス加工はそれ以上の多様性を提供します。フライス加工機には、垂直型と水平型の二種類があり、加工する製品の形状に応じて適切なタイプを選択できるのも大きな利点です。特に、複雑な形状や多様な面を持つ部品の製造において、その柔軟性が発揮されます。
結論として、フライス加工はその種類に応じて多彩な利点を持つ重要な加工技術であり、日本の製造業において不可欠な役割を果たしています。精密な加工が可能であり、また、加工する部品の形状に合わせた機械選択の柔軟性を持つことで、さまざまな製品の製造が可能となります。これらの特性により、フライス加工は今後も幅広い産業で重宝されることでしょう。
5-2. 加工方法における違い
フライス加工による鉄の加工は、その精度と効率性から多くの製造現場で重宝されています。この方法は、特に日本の製造業において、部品の形状やサイズに応じた様々な種類の加工が可能であるという点で非常に重要です。フライス加工の最大の利点は、複雑な形状や深い溝も正確に加工できることにあります。
たとえば、平面加工や溝加工、歯車の加工など、具体的な加工方法に応じて使用されるフライスカッターも様々です。平面を加工する際には、エンドミルと呼ばれるカッターが使用され、溝や穴加工には、スロットカッターやボールエンドミルが適しています。また、歯車を加工する場合には、特別な形状のギヤカッターが用いられます。
これらの種類ごとに最適なフライス加工方法を選択することで、加工の精度を向上させるとともに、時間とコストの削減にもつながります。日本では、高度な技術力を持つ技術者がこれらの加工方法を駆使して、世界に誇る高品質な製品を生産しています。フライス加工による鉄加工の適用範囲は広く、その利点を活かした製造が今後も益々求められることでしょう。
5-3. 選択する際の考慮点
フライス加工は、鉄などの金属を精密に加工するための主要な方法の一つです。この技術を用いることで、高い精度と複雑な形状の部品を効率よく製作することが可能です。その効率性と精密性は、種類別のアプローチによってさらに向上します。フライス加工には、平削り、側削り、形削りなど、様々な種類があり、それぞれに特徴と利点があります。
例えば、平削りは平面的な部品の加工に用いられ、高い表面精度を実現します。側削りは、側面の加工に適しており、深い溝や段差の加工が可能です。形削りは、複雑な形状を持つ部品に対して使用され、非常に精密な加工を行うことができます。これらの方法を適切に選択することで、加工の効率性と部品の品質を大幅に向上させることが可能です。
日本では、繊細で精密な加工が求められる産業が多く、フライス加工の技術が非常に重要視されています。車両部品や電子機器など、日常生活に密接に関わる製品の製造にも、この技術が利用されています。適切な種類のフライス加工を選択することで、高品質な製品を効率的に生産することができるのです。
結論として、フライスによる鉄加工は、その種類別のアプローチを理解し適用することで、製造業における精密加工の効率性と品質の向上に大きく寄与します。日本の製造業においても、この技術の重要性は高く、多様な産業でその利点が生かされています。
まとめ
フライスによる鉄加工は、様々な種類があります。それぞれの種類には、異なる利点があります。例えば、面取りフライスは、鋭利な角を取り除くために使用され、加工した部品の耐久性を高めます。また、ボールエンドミルは、複雑な形状を作成するのに適しており、精密な加工が可能です。フライス加工を行う際には、それぞれの種類に応じて最適なアプローチを選択することが重要です。
鉄を使ったフライス加工の種類と特徴一覧
鉄を使ったフライス加工は、工業製品や建設資材などの生産において欠かせない工程です。様々な種類のフライス加工が存在し、その特徴や使い方によって異なる成形が可能となります。本記事では、鉄を素材としたフライス加工の種類やそれぞれの特徴について詳しく紹介します。ユーザーが適切なフライス加工方法を選択し、効率的かつ品質の高い製品を生産するための一助となる情報を提供しています。鉄を使ったフライス加工の魅力と可能性について一緒に探っていきましょう。
1. フライス加工とは
1-1. フライス加工の定義と基本
フライス加工は、鉄などの金属を削ることで形を整える工程の一つです。この工程は、精密な部品製造に不可欠であり、主に製造業で利用されています。鉄を使ったフライス加工の種類には、平面加工、溝加工、歯車加工などがあります。これらの加工方法は、使用する機械やカッターの形状によって異なり、それぞれに特徴があります。例えば、平面加工は最も基本的なフライス加工で、平らな面を作るために用いられます。溝加工は溝やキー溝を作る際に使用され、歯車加工は歯車やウォームギアなどの精密な形状を加工するのに適しています。これらの加工方法は、鉄を含む様々な材料に適用可能で、製品の仕様や用途に応じて選択されます。結論として、鉄を使ったフライス加工は多様な種類があり、それぞれが特定の用途に合わせて開発されています。正しい加工方法を選択することで、高品質な製品を効率良く製造することが可能です。
1-2. フライス加工の歴史と発展
フライス加工は、鉄を含む様々な材料を加工するのに用いられる重要な技術です。この技術は、精密な部品製造において欠かせないものとなっています。特に、日本において鉄を使ったフライス加工は、その高い技術力と精度で多くの産業で活用されています。まず、フライス加工の特徴は、複雑な形状や細かい部品も精密に加工できる点にあります。例えば、自動車や電子機器の部品など、日常生活に密接に関わる製品の多くが、この技術によって製造されています。
鉄を使ったフライス加工には、平面加工、側面加工、溝加工など様々な種類があります。平面加工では、材料の表面を均一に削り、滑らかな面を作り出します。側面加工では、材料の側面を加工して形状を整えます。溝加工は、材料に溝や穴を加工することで、部品同士を組み合わせる際の接合部や、機械内での動きをスムーズにするための部分を作り出します。
これらの技術によって、多様な形状や機能を持った部品が製造され、日本の製造業の発展に大きく貢献しています。最終的に、鉄を使ったフライス加工の技術は、その高い精度と多様な加工方法により、日本のものづくり産業の品質向上に不可欠なものとなっています。
2. 鉄を使ったフライス加工の基礎知識
2-1. 鉄の特性と加工の適性
鉄はその耐久性と加工しやすさから、幅広い産業で使用されています。特に、フライス加工においては、その特性が最大限に活かされるため、多くの種類が存在します。鉄のフライス加工は、精密な形状を作り出すことが可能であり、工業製品の製造に欠かせない技術です。
まず、フライス加工には平面加工、溝加工、歯車加工などがあります。例えば、平面加工では、鉄の表面を滑らかに仕上げることができ、溝加工では、部品同士を組み合わせる際に必要な溝や穴を正確に加工することができます。また、歯車加工では、機械の動きを伝えるための歯車を製造することが可能です。
これらの加工方法は、それぞれに特徴があり、用途に応じて選ばれます。たとえば、高精度が要求される機械部品では、精度の高い溝加工や歯車加工が選ばれることが多いです。逆に、大きな面を均一に仕上げる必要がある場合は、平面加工が利用されます。
結論として、鉄のフライス加工は多岐にわたり、その加工方法は製品の用途や求められる精度に応じて選ばれます。これにより、様々な産業で鉄が重要な役割を果たしており、その技術の進展は今後も続くことでしょう。
2-2. 金属加工における切削加工の基礎
鉄を使ったフライス加工は、多様な種類が存在し、それぞれに特徴があります。フライス加工とは、回転する刃を用いて材料を削り取る工法で、精密な加工が可能です。この技術は、日本の製造業において欠かせない役割を担っています。
具体的には、平面加工、側面加工、溝加工などがあります。平面加工は、材料の表面を平らにする作業であり、製品の基礎となる重要な工程です。側面加工では、製品の側面を削り出し形状を作り出します。溝加工は、特定の形状の溝を材料に加工する方法で、ギアやキー溝などの製造に用いられます。
これらの加工方法は、鉄などの硬質材料の精密加工に適しており、自動車や機械部品など、幅広い分野で活用されています。特に、日本の高度な製造技術は、これらの精密加工を通じて、世界中から高い評価を受けています。
結論として、鉄を使ったフライス加工は、その種類の多様性と精密な加工能力により、日本の製造業において不可欠な技術です。これらの技術を駆使することで、高品質な製品が生産され、日本製造業の競争力が支えられています。
2-3. フライス加工用の鉄材料の選定
フライス加工において、鉄材料の選定は製品の品質やコストに大きく影響します。この選定プロセスには、鉄の種類ごとの特徴を理解することが不可欠です。例えば、一般的な鉄鋼材料としてSS材やS45Cなどが挙げられますが、これらは加工しやすさや耐久性が異なります。SS材は比較的柔らかく加工しやすいため、複雑な形状の加工に適しています。一方、S45Cは硬度が高く耐摩耗性に優れているため、長期にわたる使用に耐える部品作りに向いています。
また、フライス加工では、加工する鉄の種類によって適した加工方法が異なることもポイントです。例えば、精密な加工が必要な場合や大量生産を前提とした場合、適した鉄材料の選定が異なります。精密加工には、加工精度が高くなるような材料が求められ、大量生産では、コストパフォーマンスが良い材料が選ばれることが多いです。
このように、フライス加工を行う際には、製品の要求条件に合わせて、最適な鉄材料を選定することが重要です。材料ごとの特性を理解し、それに基づいて鉄の種類を選ぶことで、コスト効率の良い高品質な製品製造が可能になります。結局のところ、フライス加工における鉄材料の選定は、製品の成功を左右する重要な要素であり、慎重に行う必要があります。
3. フライス加工のメリットとデメリット
3-1. フライス加工のメリット
フライス加工は、鉄などの金属を削ることで形を整える加工方法の一つであり、その種類と特徴は多岐にわたります。この方法は、精密な寸法と形状を実現することができるため、機械部品や工具などの製造に広く利用されています。特に、鉄を使ったフライス加工は、その耐久性と加工の容易さからさまざまな産業で重宝されています。
例えば、平面を加工するための平面フライス加工、溝やキー溝を作る溝フライス加工、複雑な形状を持つ物体を加工するための形状フライス加工などがあります。これらのフライス加工の方法を選択することで、製品の精度を大幅に向上させることが可能です。日本では、特に製造業の精度要求が高いため、これらの加工技術が積極的に用いられています。
さらに、CNC(Computer Numerical Control)技術の導入により、フライス加工はさらに進化を遂げています。CNCフライス加工では、コンピュータによって制御されるため、非常に高い精度で複雑な加工が可能になり、生産効率も大きく向上しています。
結論として、鉄を使ったフライス加工はその種類と特徴によって、製造業における多様なニーズに応えることができる技術です。日本のように、高い技術力が求められる製造業が盛んな国にとって、フライス加工のさらなる技術開発と応用拡大が期待されています。
3-2. フライス加工のデメリット
フライス加工は、多様な材料に対応できる加工方法の一つですが、特に鉄を用いた加工にはいくつかのデメリットが存在します。まず、鉄は硬いため、加工する際に必要なエネルギーが多く、工具の摩耗が激しいことが挙げられます。これにより、フライス加工のコストが上昇する可能性があります。また、鉄の加工中には大量の熱が発生するため、精密な作業を行う際には冷却液を適切に使用する必要があり、その管理も一つの課題となります。さらに、鉄は錆びやすい素材であるため、加工後の表面処理にも注意が必要です。これらのデメリットを踏まえた上で、フライス加工を行う際には、工具の選択や冷却方法、表面処理の技術などに工夫を凝らすことが求められます。結局のところ、鉄を使ったフライス加工は、その特有の課題を理解し、適切な対策を講じることで、高品質な製品を生産することが可能です。
3-3. 他の加工方法との比較
鉄を使ったフライス加工は、精密な部品製造に欠かせない技術であり、日本でも広く利用されています。この加工方法は、その種類の豊富さと特有の特徴により、多様な工業製品の生産に適しています。例えば、平面フライス加工は、大きな平面を平滑に仕上げるのに最適であり、Tスロットフライス加工は、特定の形状の溝を加工するのに使用されます。これらの方法は、鉄のような硬い材料でも高精度の加工を可能にし、製品の品質を向上させることができます。
他の加工方法と比べて、フライス加工は複雑な形状や細部の加工に優れている点が特長です。例えば、旋削加工では難しい非円形の加工もフライス加工では容易に行えます。さらに、CNC(コンピュータ数値制御)技術の導入により、より複雑で精密なデザインの実現が可能になりました。
結論として、フライス加工はその種類の豊富さと高い柔軟性により、鉄を含む多様な材料の加工に欠かせない方法です。特に日本においては、高度な技術力と精密加工への需求が高いため、フライス加工の重要性は今後も増していくことでしょう。
4. 鉄のフライス加工の種類と特徴
4-1. 平面フライス加工
鉄を使ったフライス加工には様々な種類があり、それぞれが工業製品の製造において重要な役割を担っています。中でも平面フライス加工は、その代表的な方法の一つです。この加工技術は、材料の表面を平らにすることを目的としており、精度の高い平面を実現することができます。
平面フライス加工の特徴は、大量生産に適している点にあります。鉄などの金属を用いた部品の製造では、同じ形状の部品を短時間で大量に生産することが求められます。この方法では、フライスカッターを用いて材料の表面を削り取ることで、効率よく平面を作り出すことが可能です。例えば、自動車のエンジン部品や建築用の金属材料など、さまざまな製品に利用されています。
加えて、平面フライス加工はその精度の高さから、要求される仕上がりの質が高い製品にも適用可能です。具体的には、機械的な強度が求められる部品や、高い平滑さが必要な製品の加工に有効です。
このように、平面フライス加工はその効率性と精度の高さから、鉄を使った部品製造において広く利用されています。この加工方法によって、多くの工業製品が高い品質で大量生産されているのです。
4-2. 形状フライス加工
形状フライス加工は、鉄を使ったフライス加工の種類の中でも特に多くの工業製品の製造で活用されています。この加工方法の最大の特徴は、複雑な形状や細部まで正確に加工できる点にあります。なぜなら、特殊なカッターを使用し、多軸の制御が可能なフライス加工機を用いることで、立体的な形状やインターネットが必要な部品も高精度で作り出せるためです。例を挙げると、自動車のエンジン部品や航空機の構造部材など、耐久性と精度が求められる分野での利用が挙げられます。これらの部品は、鉄の優れた物性を活かしつつ、形状フライス加工によってその機能を最大限に引き出しています。結論として、形状フライス加工は、その高い加工精度と複雑な形状への対応能力により、工業製品の製造において欠かせない技術であると言えるでしょう。
4-3. 隅切りフライス加工
隅切りフライス加工は、鉄などの金属材料を加工する際に非常に一般的に利用される技術です。この技術の最大の特長は、材料の角を滑らかに削り取ることができる点にあります。その理由は、特殊な形状の刃を用いることで、精密な角度や形状の加工が可能になるからです。例えば、機械部品や工業製品においては、部品同士がきちんと組み合わさるためには、角の加工精度が非常に重要になります。隅切りフライス加工によって、このような部品の精密な加工が実現され、製品の品質向上に寄与しています。
また、この加工方法は、鉄以外にもさまざまな材料に対応可能で、加工速度が速いことも大きな利点です。これにより、生産効率の向上にもつながり、多くの製造現場で採用されています。結論として、隅切りフライス加工はその特長として、材料の角を精密に加工する能力、さまざまな材料への適応性、そして高い加工速度によって、多岐にわたる産業で重要な役割を果たしています。材料の角を滑らかにし、部品の組み立てや製品の品質向上に貢献しているのです。
4-4. 穴あけフライス加工
鉄を使った穴あけフライス加工は、その精密さと効率性から多くの工業分野で重宝されています。この加工方法の最大の特徴は、様々な形状や大きさの穴を正確に開けることができる点にあります。具体的には、直径数ミリメートルの小さな穴から、数十センチメートルに及ぶ大型の穴まで、ニーズに応じた加工が可能です。
一例として、自動車産業ではエンジン部品やフレームの組み立てにこの技術が用いられています。また、建設業界では、構造体に必要な固定穴の加工に活用されることが多いです。これらの例からもわかるように、穴あけフライス加工は精度が求められる多くの場面でその有効性を発揮しています。
この加工技術のもう一つの大きな利点は、加工時間の短縮とコスト削減に寄与することです。高度な機械制御により、一度に複数の穴を正確に、そして迅速に開けることができるため、生産効率を大幅に向上させることが可能です。
これらの理由から、鉄を使った穴あけフライス加工は、今後も多くの製造業で重要な役割を担い続けることでしょう。この技術の進展により、さらに多様な製品の製造が可能になり、その品質や生産性においても大きな進歩が期待されます。
4-5. 特殊フライス加工
特殊フライス加工は、鉄を用いた加工方法の中でも、その高度な技術と多様な応用によって注目されています。この加工方法の特徴は、精密な形状や細かいデザインを鉄に施すことが可能である点にあります。例えば、歯車や複雑な曲線を持つ部品の製造において、特殊フライス加工は重宝されます。さらに、高い耐久性と精度を要求される航空宇宙産業や自動車産業でも、この技術は不可欠です。
特殊フライス加工が可能にする細かい加工は、従来のフライス加工では難しかった複雑な形状や精細な模様を実現します。例えば、マイクロ加工を用いた部品製造では、数ミクロン単位の精度が求められることがあり、特殊フライス加工によってこれを実現できます。また、硬質材料への加工も、特殊な刃物や技術を用いることで可能となり、加工の幅が広がっています。
このように、特殊フライス加工はその高度な技術と多様な応用により、現代の製造業において不可欠な技術の一つとなっています。日本においても、精密な加工技術は伝統的に重視されており、特殊フライス加工の技術開発と応用は今後も重要な分野であると言えるでしょう。
5. フライス加工機の種類と選定
5-1. 水平フライス盤
鉄を使ったフライス加工には様々な種類があり、それぞれ特徴があります。特に、水平フライス盤を使用した加工は、その汎用性の高さで知られています。この種類のフライス加工では、カッターが水平に配置されており、主に平面や溝の加工に適しています。具体的な例としては、キー溝やT溝の加工が挙げられます。これらの加工は、鉄を含む多くの金属に対して行うことができ、精密な加工が可能です。
また、水平フライス盤は、大きなワークピースの加工にも適しており、その柔軟性から多種多様な製造業で利用されています。日本では、特に精密機械や自動車産業での需要が高く、製品の品質向上に寄与しています。
結論として、鉄を使ったフライス加工の中でも、水平フライス盤を使用した加工は、その適用範囲の広さと高い精度から、多くの製造業で重宝されています。この加工方法により、様々な形状の金属部品を効率良く、かつ精密に加工することができるのです。
5-2. 垂直フライス盤
鉄を用いたフライス加工には様々な種類があり、それぞれ特徴が異なります。特に、垂直フライス盤を用いた加工は、精度の高い部品製造に不可欠です。この加工方法の最大の特徴は、刃が垂直に回転することにより、さまざまな形状の加工が可能になる点です。例えば、平らな面の加工だけでなく、溝や穴あけなど複雑な形状も正確に加工できます。日本では、自動車や電子機器の部品製造においてこの垂直フライス盤が頻繁に利用されています。その精密さから、高い品質が求められる製品には欠かせない技術です。結論として、鉄を使ったフライス加工の中でも、垂直フライス盤を用いた加工はその精度と多様性から、幅広い産業で重宝されており、今後もその需要は高まることが予想されます。
5-3. ユニバーサルフライス盤
鉄を使ったフライス加工は、その高い精度と多様性から、製造業において不可欠な技術の一つです。この加工方法は、特に硬い材料である鉄を加工する際、その優れた能力を発揮します。鉄のフライス加工には様々な種類があり、それぞれが特有の特徴を持っています。
まず、フライス加工の中でも特に一般的なのが、平面を削るための平フライス加工です。この方法は、鉄の平らな表面を作り出すのに適しており、機械部品の基礎加工として広く利用されています。例えば、機械のベースとなる部分の加工に使われます。
次に、より複雑な形状を作り出すことが可能なのが、型フライス加工です。この方法では、特殊なカッターを使用して、鉄のブロックから複雑な形状を削り出します。自動車のエンジン部品やロボットの関節など、精密な部品製造に欠かせない技術です。
また、穴あけ加工に特化したドリルフライス加工もあります。この方法は、鉄の板やブロックに正確な位置とサイズの穴を開けるために利用されます。機械の組み立てに必要なボルト穴の開ける際などに用いられます。
各種フライス加工の技術は、その適用範囲の広さと加工精度の高さから、日本の製造業において極めて重要な役割を果たしています。高い技術力を持つ日本では、これらの加工方法を駆使して、世界に誇れる高品質な製品を生み出し続けています。鉄を使ったフライス加工は、その可能性の広がりとともに、今後も多くの製造現場で活用されるでしょう。
5-4. CNCフライス盤
鉄を使ったフライス加工には多様な種類があり、それぞれが特有の特徴を持っています。この加工技術は、精密な部品製造や複雑な形状の加工に不可欠で、日本では特に高い技術力が要求されます。例えば、CNCフライス盤を用いることで、高度な精度と複雑な形状の加工が可能になります。CNCフライス盤は、コンピュータによる数値制御を特徴とし、プログラムされた指示に従って自動的に加工を行います。これにより、人の手による加工では難しい、高い再現性と精度を実現しています。
また、多軸フライス加工も鉄加工における重要な方法の一つです。この技術を用いることで、一度の設定で多方向からの加工が可能になり、加工時間の短縮や効率の向上に寄与します。さらに、表面処理技術も鉄を用いたフライス加工の重要な部分であり、耐摩耗性や耐蝕性を向上させることができます。
これらのフライス加工技術は、自動車産業や航空機製造、精密機械製造など、幅広い分野で活用されています。特に日本では、これらの技術を駆使して高品質な製品を生産することが求められています。結論として、鉄を使ったフライス加工は多様な種類と特徴を持ち、高度な技術力と精密さが求められる加工方法です。これらの技術の進化は、日本の製造業の競争力を高める上で不可欠な要素となっています。
6. フライス加工と旋削加工の違い
6-1. フライス加工の特徴と応用
フライス加工は、金属加工の一手法であり、特に鉄などの硬い材料を加工する際に広く用いられています。この加工法の主な特徴は、その高い精度と複雑な形状を実現できる柔軟性にあります。鉄を使ったフライス加工には、平面加工、溝加工、歯車加工など様々な種類があります。例えば、平面加工では、鉄板の表面を平滑に仕上げることができ、溝加工では、部品に溝や穴を正確な位置に加工することが可能です。また、歯車加工では、精密な歯車を製造することができ、このようにフライス加工は機械部品の製造に不可欠です。日本では、高度な技術力を要するフライス加工が盛んであり、自動車やロボットなどの産業で重要な役割を果たしています。結論として、鉄を使ったフライス加工は、その多様性と高精度な加工能力により、幅広い産業で利用されており、日本の製造業の発展に寄与しています。
6-2. 旋削加工の特徴と応用
鉄を使用したフライス加工は、その多様性と精密さで知られています。フライス加工とは、回転する刃を使用して材料を削り取る加工方法であり、鉄などの金属加工に欠かせない技術の一つです。この加工法の特徴は、複雑な形状や非常に精密な部品も製造できる点にあります。特に日本において、フライス加工は精密機器や自動車産業など、多岐にわたる分野で利用されています。例えば、自動車のエンジン部品や機械のギアなどが、この加工技術によって製造されています。さらに、日本の技術者は特に高度な技術を有しており、微細な部分の加工も可能です。これらの理由から、鉄を使ったフライス加工は、その精度と多様性で多くの産業分野において重要な役割を果たしています。結論として、鉄のフライス加工は、技術の進歩とともにさらに進化していくことが予想され、日本の製造業の競争力を支える基盤技術としての位置づけは今後も変わらないでしょう。
6-3. 両加工方法の比較と注意点
鉄を使ったフライス加工の種類は多岐に渡り、それぞれ独自の特徴を持っています。この加工技術の理解は、より効率的で精密な製品製造に不可欠です。例えば、平面フライス加工では大きな平面を高い精度で加工することができ、側面フライス加工では、製品の側面を整えることが可能です。また、形状フライス加工を用いると、複雑な形状や曲線を実現できます。
日本における鉄のフライス加工技術は、精密機械製造業にとって重要な役割を担っています。そのため、各種フライス加工の正確な知識と適用は、製品の品質向上に直結します。例として、自動車業界では、エンジン部品やフレームの加工にこれらの技術が活用されています。これにより、耐久性や性能が大幅に向上しています。
最終的に、鉄を使ったフライス加工の種類とその特徴を理解することは、製造業における効率性と品質の向上に直結します。日本の製造業者は、各加工技術の適切な選択と適用によって、国際競争力を高めることができます。
7. フライス加工の工程と技術
7-1. 加工前の準備
鉄を使ったフライス加工は、その高い強度と加工のしやすさから、多様な産業で利用されています。フライス加工の種類には、平面加工、溝加工、輪郭加工などがあり、それぞれに特徴があります。たとえば、平面加工は鉄の表面を滑らかにするのに適しており、部品の仕上げによく用いられます。溝加工は、部品に溝やキー溝を加工するのに適しているため、機械の組み立てに不可欠です。輪郭加工では、複雑な形状を作ることができるため、カスタムメイドの部品製造に役立ちます。これらの加工方法は、製品の精度や耐久性を高めるために重要であり、日本の製造業において広く採用されています。結論として、鉄を使ったフライス加工は、その多様性と高い技術力により、多くの産業で欠かせない加工方法となっています。
7-2. 切削条件の設定
鉄を使ったフライス加工は、その耐久性と加工のしやすさから、工業分野で広く利用されています。フライス加工の種類と特徴を理解することは、製品の品質向上や生産効率の向上に直結します。まず、フライス加工には平面加工、溝加工、歯車加工など様々な種類があります。それぞれの加工方法には特徴があり、使用する機械や加工物に適した種類を選択することが重要です。
例えば、平面加工はその名の通り、物体の平面を削る加工で、主に表面の仕上げに用いられます。溝加工は溝やキー溝を作るのに適しており、歯車加工は歯車を製造する際に不可欠です。これらの加工方法により、鉄などの材料から精密な部品や製品を製造することが可能になります。
特に日本では、精密機械産業が非常に発展しているため、フライス加工の技術は高く評価されています。日本製の機械や部品は、その高い品質と精密さで世界中で重宝されています。
結論として、鉄を使ったフライス加工の種類と特徴を理解し、適切な加工方法を選択することは、製品の品質を保つだけでなく、生産効率を向上させる上で非常に重要です。日本の精密機械産業の発展には、これらの加工技術が欠かせません。
7-3. 加工精度と品質管理
鉄を使用したフライス加工は、その高い精度と品質管理の容易さから、様々な産業で広く利用されています。フライス加工において重要なのは、加工する鉄の品質を維持しつつ、必要な形状と寸法に正確に仕上げることです。この過程では、特に加工精度と品質管理が重要視されます。
例えば、自動車産業では、エンジン部品やシャシーなど、高い強度と精密さが求められる部品の加工に鉄が用いられます。これらの部品は、車両の性能や安全性に直接影響するため、非常に厳しい品質基準のもとで製造されます。フライス加工を通じて、これらの基準を満たす精度の高い部品を生産することが可能になるのです。
また、建築業界でも、鉄は構造材料や装飾品の加工に頻繁に使用されます。フライス加工では、建築物のデザインに合わせた複雑な形状や細かい装飾を鉄に施すことができます。これにより、強度と美観を兼ね備えた建築物の制作が可能となります。
こうした鉄を使ったフライス加工の種類と特徴を理解することは、各産業での材料選定や加工方法の選択において非常に重要です。加工精度と品質管理の向上により、より高品質な製品の製造が可能になります。その結果、鉄を使ったフライス加工は、多岐にわたる産業での応用が期待されています。
7-4. アフターケアとメンテナンス
フライス加工は、鉄などの金属を削って形を作る重要な工程であり、その種類と特徴を理解することは、高品質な製品を製造する上で欠かせません。この工程は、使用する鉄の種類によっても異なる特徴を持ち、それぞれに適した加工方法があります。たとえば、一般的な鉄のフライス加工には、平面加工、角加工、溝加工などがあります。平面加工では、大きな平面を均一に削ることが可能で、主に板材の加工に用いられます。角加工では、材料の角やエッジを正確に削りだすことができ、溝加工は、ギアやキー溝などの細かい部品製作に重宝されます。これらの加工方法は、製品の用途や求められる精度に応じて選ばれ、鉄の優れた加工性能を最大限に活かした製品作りに貢献しています。このように、鉄を使ったフライス加工の種類を知ることで、製品の設計から製造に至るまで、より効率的で高品質な方法を選択することができます。結論として、鉄を使ったフライス加工方法の理解は、精密な製品製造において不可欠であり、その多様な種類と特徴を把握することが極めて重要です。
8. 安全なフライス加工のためのガイドライン
8-1. 安全装置と保護具
鉄を使ったフライス加工は、その耐久性と加工のしやすさから、幅広い産業で利用されています。この加工方法にはいくつかの種類があり、それぞれ特徴があります。まず、フライス加工の最も一般的な形式は、平面加工です。これは、鉄の表面を平滑に仕上げるために使用されます。たとえば、機械の基盤やフレームを製造する際に必要とされる平面度を実現するために重宝されています。また、溝加工もフライス加工の一種で、鉄のピースに溝やキー溝を切り込むために使われます。これは、機械部品の組み立てにおいて重要な役割を果たします。
さらに、複雑な形状や曲線を加工するために、3Dフライス加工があります。これは、より高度な技術を要求される加工方法で、具体的な例としては、自動車のエンジン部品や航空宇宙産業の部品などが挙げられます。これらの部品は、非常に精密な寸法と形状が求められるため、3Dフライス加工によって高い精度を達成することが可能です。
結論として、鉄を使ったフライス加工はその種類が豊富であり、それぞれの加工方法によって特有の特徴があります。平面加工は表面を滑らかにするのに、溝加工は部品の組み立てに不可欠であり、3Dフライス加工は複雑な形状の製造に用いられます。これらの加工方法は、日本の製造業において非常に重要な役割を果たしています。
8-2. 操作上の注意点
鉄を使ったフライス加工は、その精度の高さと強度によって、多くの製造業で重宝されています。この加工方法には、面削り、スロッティング、ギア加工など、様々な種類があり、それぞれ特徴があります。例えば、面削りは鉄板の表面を平滑にするのに適しており、スロッティングは溝や穴を作るのに用いられます。一方、ギア加工は、機械の部品など精密な形状を必要とする場合に選ばれます。
これらの加工方法が選ばれる理由は、鉄の加工における高い耐久性と精度にあります。鉄は硬い材料であるため、加工時における耐久性が求められる場合に適しています。また、フライス加工機械の高精度な制御により、細かな部品作りにも対応可能です。
日本では、特に製造業の分野で鉄のフライス加工が活用されています。自動車産業や電機産業など、精密な部品が必要とされる分野での需要が高いです。たとえば、自動車のエンジン部品や、家電製品の小さなギアなど、日常生活に密接に関連する製品にも、この加工技術が用いられています。
結論として、鉄を使ったフライス加工の種類とその特徴は、製造業における多様なニーズに応えるために不可欠です。それぞれの加工方法が持つ特性を理解し、適切に選択することが、製品の品質を高め、効率的な生産を実現する鍵となります。
8-3. 緊急時の対処法
フライス加工は、工業製品の製造において重要な役割を果たしています。特に、鉄を使ったフライス加工は、その高い強度と加工のしやすさから、多くの分野で採用されています。フライス加工にはいくつかの種類があり、それぞれが特有の特徴を持っています。
まず、平面フライス加工は、主に平らな面を作るために用いられます。この加工は、鉄製の部品の表面を滑らかにしたり、正確な寸法に加工するのに適しています。例えば、機械のベースとなる部分の加工に多く使用されます。
次に、側面フライス加工は、部品の側面を加工するために使われます。この方法は、特に溝を切る際や、側面に形状をつける必要がある場合に効果的です。自動車のエンジン部品や建築用の鉄骨など、精密な加工が求められる部品の製造に利用されています。
また、複合フライス加工は、平面や側面だけでなく、複雑な形状を一度に加工することが可能です。この種類のフライス加工は、高度な技術を要するものの、効率的に多様な形状を創出できるため、航空機の部品や精密機器の部品製造に使用されることがあります。
結論として、鉄を使ったフライス加工は、その種類に応じて様々な特徴があり、それぞれ異なる用途に適しています。平面フライス加工、側面フライス加工、複合フライス加工といった手法を駆使することで、幅広い工業製品の製造が可能になります。日本においても、この技術は多くの分野で活用され、製品の品質向上に寄与しています。
9. フライス加工の未来と革新的技術
9-1. 自動化とロボティクスの活用
鉄を使ったフライス加工は、その多様性と精密性で注目されています。この加工方法は、鉄を削り、形を作る過程で、多くの種類があり、それぞれに特徴があります。例えば、平面フライス加工では、大きな平面を高い精度で削り出すことができ、輪郭フライス加工では、複雑な形状や曲線を精密に削ることが可能です。また、穴あけフライス加工は、鉄の板やブロックに正確な位置に穴を開けるのに適しています。
これらの加工方法には、それぞれ使用する機械や刃の種類も異なり、加工する物の形状や精度、製作する部品の用途によって選ばれます。例えば、精密部品を製造する場合は、より細かく精度の高い加工が求められるため、適したフライス加工方法を選択する必要があります。
結論として、鉄を使ったフライス加工は、その種類の多様性と各々の技術の特徴を理解することで、より効率的で高品質な製品製造につながります。これは、日本の製造業の技術力を高め、より良い製品を生み出す上で欠かせないプロセスであると言えるでしょう。
9-2. 新しい材料と加工法の開発
鉄はその耐久性と加工性の良さから、さまざまな工業製品の材料として広く利用されています。特に、フライス加工においては、鉄の特性を活かした多様な方法が開発されており、それぞれが独自の特徴を持っています。フライス加工とは、回転する刃を使用して材料から余分な部分を削り取る加工技術であり、精密な形状を実現するために不可欠です。
例えば、一般的に用いられる平面フライス加工では、鉄板を平滑に仕上げることが可能です。また、立体フライス加工では、複雑な形状や溝を鉄に加工することができ、部品の機能性を高めます。さらに、微細フライス加工によっては、極めて小さな部品でも高精度に仕上げられるため、電子機器などの精密部品製造に欠かせません。
これらのフライス加工技術は、鉄の物理的特性に適応することで、製品の耐久性や機能性を向上させることに貢献しています。また、加工技術の進化により、更に複雑で高機能な鉄製品の開発が可能になっています。これにより、日本を含む世界の多くの産業で、高品質な鉄製品が求められ続けています。結論として、鉄を使用したフライス加工の種類と特徴は、その適用範囲の広さと、技術の発展可能性により、産業にとって不可欠な要素であると言えます。
9-3. 環境に配慮した加工技術
鉄を使ったフライス加工は、その多様性と高い精度で重工業から精密機械製造に至るまで幅広く活用されています。この加工方法の特徴として、鉄の強度を活かしつつ、必要な形状やサイズに正確に加工できる点が挙げられます。加工の種類には、平面フライス加工、側面フライス加工、形状フライス加工などがあり、それぞれ特有の用途があります。例えば、平面フライス加工は、主に平らな面を作成するのに用いられ、側面フライス加工は、鉄の側面を削って形を整えるのに適しています。また、形状フライス加工は、複雑な形状や細かいディテールが必要な場合に選ばれます。これらの加工方法は、自動車の部品から建築材料まで、日本の製造業の多くの場面で重要な役割を担っています。結論として、鉄を使ったフライス加工は、その種類の豊富さと加工の精度から、日本の産業における基礎的な技術の一つと言えるでしょう。
まとめ
鉄を使用したフライス加工は、さまざまな種類があります。それぞれの特徴や利点を理解することで、適切なフライス加工方法を選択できます。例えば、エンドミルを使用した切削は、高精度で複雑な形状を作ることができます。一方でフェースミルを使用した切削は、大きな面積を効率的に削ることができます。さらに、スロッティングカッターを用いた切削は、溝や溝を作るのに適しています。これらの種類を理解し、適切に活用することで、効率的な鉄のフライス加工が可能となります。
工業用SKD材のフライス加工・タップ加工術
工業用のSKD材を使用した加工技術について知識を深めたいと思っていますか?本記事では、フライス加工やタップ加工におけるスキルアップに役立つ情報をご紹介します。SKD材を使った加工の基礎から応用手法まで、幅広く解説いたします。工業界でのスキル向上や新しい知識習得を目指す方にとって、必読の内容となっています。
1. SKD タップ加工・フライス加工の基礎知識
1-1. SKD材とは何か?
SKD材とは、金型や工具などの製作に使用される特殊鋼の一種です。耐摩耗性や耐熱性に優れることから、工業用に広く利用されています。その加工技術であるフライス加工とタップ加工は、精密部品製造に不可欠な技術です。フライス加工は複雑な形状を持つ部品を削り出すことができ、一方のタップ加工はネジ穴を形成するために使われます。例えば、自動車のエンジン部品や電子機器の微細なコンポーネントなど、精緻なデザインが求められる製品の加工において、これらの技術が活用されています。それゆえ、SKD材のフライス加工・タップ加工術は、製造工程の効率化や高品質な製品の生産に寄与しており、日本の製造業の競争力を支えていると言えます。
1-2. タップ加工とフライス加工の概要
工業用SKD材の加工において、タップ加工とフライス加工は非常に重要です。これらの技術を駆使することで、精密な部品製作が可能になります。例えばタップ加工では、ねじの山を切ることで部品同士を固定する際に不可欠な内ねじを作成します。フライス加工では、平面や曲面、溝などの形状を削り出すことができ、複雑な形状の部品にも対応可能です。特に、高硬度のSKD材を扱う場合、正確な寸法や形状を維持するためには、これらの加工技術の適切な運用が求められます。そうした技術の進歩により、より複雑なデザインの部品が日本国内で効率良く生産されるようになりました。結論として、タップ加工とフライス加工は、現代の工業生産における精度と効率を向上させるために不可欠な技術であり、その技術力の高さが日本の製造業の競争力を支えています。
1-3. SKD タップ加工とフライス加工の適用分野
SKD材のフライス加工とタップ加工は、その耐摩耗性や耐熱性の高さから、工業用途で広く利用されています。例えば自動車産業や機械部品製造での使用が挙げられます。フライス加工は材料の表面から所望の形状を削り出す加工方法で、精密な寸法を実現するために不可欠です。タップ加工は、ネジ穴を切るために用いられ、組み立てにおいて重要な役割を果たします。フライス加工で成形された部品にタップ加工を施すことで、高品質なネジ接合が可能となり、製品の信頼性が向上します。特に、高強度を要求される部品では、これらの加工技術が製品の性能を左右するため、技術の精度と加工の品質管理が非常に重要となります。したがって、高品質なSKD材の加工を行うことは、工業製品の耐久性と機能性を保証する上で欠かせない工程といえるでしょう。
2. SKD11とSKD61の特性と違い
2-1. SKD11の特性
SKD11は、耐摩耗性や硬さ、加工性に優れた工業用鋼材として高い評価を受けています。この材料は、特にフライス加工やタップ加工に適しており、精密な部品製造に不可欠です。例えば、金型や工具などの製造には、耐久性と正確性が求められ、SKD11はその両方を併せ持つ材質として選ばれることが多いです。さらに、加工時の熱処理を適切に行うことで、その特性を最大限に引き出すことができます。このような特性から、SKD11は多くの産業で重宝されており、フライス加工やタップ加工技術の進化と共に、その利用範囲はさらに広がっていくことでしょう。結論として、SKD11の持つ特性を理解し、適切な加工技術を用いることで、耐久性に優れた高品質な製品を効率良く生産することが可能です。
2-2. SKD61との比較
SKD材のフライス加工やタップ加工は、精密な製品製造において欠かせない技術です。例えば、SKD61は工業用途に広く利用される高耐熱鋼で、加工性に優れています。このSKD61と他のSKD材との比較を行うことで、それぞれの材質に応じた適切な加工方法を選択することができます。具体的には、SKD61の場合、硬度が高く耐熱性に優れているため、切削速度や送り速度を調整し、工具の摩耗にも注意しながら加工を行う必要があります。フライス加工では、カッターの刃の数を増やし、タップ加工では、旋削油を適切に使用することで、摩擦を減らし精度を高めることができます。このように、SKD材を用いた加工技術は、製品の品質向上に直結するため、材質の特性を理解し、適切な加工条件を選定することが重要です。
3. SKD11のメーカーと供給情報
3-1. 主要SKD11メーカーの紹介
工業用SKD材のフライス加工およびタップ加工は、精密部品の製造において欠かせない技術です。SKD材料は硬度が高く耐摩耗性に優れているため、フライス加工では正確な切削が求められ、タップ加工においては緻密なねじ切りが必要とされます。たとえば、金型製造においては、SKD材を使用した部品はその耐久性のため広く利用されています。また、自動車産業などでは、ギアやエンジン部品の加工にSKD材が選ばれることが多いです。正しい工具選択と加工条件の設定が重要となり、これによりSKD材の特性を最大限に活かし、長寿命の部品を実現することができます。最終的に、フライス加工・タップ加工を行う上での専門的技術と経験が、高品質な工業用製品の生産に不可欠となっています。
3-2. 購入時のポイント
工業用SKD材のフライス加工やタップ加工は、精密な製品製造に不可欠です。SKD材は特に硬度が高いため、加工する際は専門的な技術が求められます。具体的には、フライス加工ではカッターの選択や送り速度、回転数の適切な設定が重要です。タップ加工においては、事前に正確な穴開けが求められる他、SKD材の硬さに合わせたタップの種類や潤滑油の使用が鍵を握ります。実例では、自動車部品や金型などの製造現場で、これらの加工技術が活躍しています。適正な加工技術を用いることで、耐久性や精度が非常に高い工業製品の生産が可能になり、結果として業界全体の品質向上に貢献しているのです。
4. 冷間鍛造用SKD11のフライス加工技術
4-1. 冷間鍛造金型の特徴
冷間鍛造金型の加工において、特に工業用SKD材はその優れた耐摩耗性と強度から選ばれることが多いです。フライス加工によって精密な部品を製造することが可能になる一方、タップ加工においては精密なねじ加工が重要となります。たとえば、自動車産業においては、エンジン部品やギアなどの製造にSKD材が用いられることがあり、これらの部品は高い精度が要求されます。フライス加工では、材料の硬度に合わせた適切な切削工具や条件を選定することが重要であり、タップ加工では、切削速度や冷却剤の選択がその品質を左右します。加工技術の進歩により、SKD材に求められる精度や複雑な形状も増え続けています。これらを踏まえSKD材の加工技術を習得することは、品質の高い製品を市場に提供する上で不可欠と言えるでしょう。
4-2. SKD11フライス加工の方法論
SKD11のフライス加工には特殊な技術が要求されます。この材料は硬度が高く、耐摩耗性に優れているため、一般の工具材では加工が難しいです。しかし、適切な工具選びと加工条件の調整により、精度の高い加工が可能になります。例えば、超硬質のカッターを使用し、回転数や送り速度を材料の特性に合わせて最適化することで、SKD11も効率良く加工できます。さらに、タップ加工においては、適切な潤滑剤の使用が必須です。これにより、タップの折損を防ぎながら、綺麗なねじ山を形成することができます。結論として、SKD11のフライス加工もタップ加工も、材料の特性を理解し、適切な工具と条件で加工することが重要です。このようにして、工業用SKD材に適した加工技術を習得することで、高品質な製品製造に寄与することができます。
5. 特殊鋼材フライス加工のポイント
5-1. 特殊鋼材の加工難易度
特殊鋼材として知られるSKD材のフライス加工やタップ加工は、一般の鋼材よりも技術が求められる。なぜなら、SKD材は硬度が高く耐磨耗性に優れているため、通常の加工方法では工具の摩耗が激しく、精度良い加工が困難だからである。しかし、適切な工具の選定と加工条件の調整により、高品質な加工を実現することができる。例えば、フライス加工では超硬合金やコーティングされた工具を用い、低速での加工を心掛ける。一方、タップ加工では、SKD材専用に設計されたタップを選び、潤滑油を適切に使用することが重要である。こうした工夫により、SKD材も精度高く加工することが可能になり、広範な産業での利用が見込まれる。したがって、高度な技術を要するSKD材の加工は、工業製品の品質向上に不可欠であり、その技術の習得は極めて価値があるといえる。
5-2. SKD材のフライス加工テクニック
SKD材は工業用に広く利用され、そのフライス加工・タップ加工は精密な技術を要します。なぜなら、SKD材は硬度が高く、耐摩耗性に優れているため加工が困難であるからです。具体的な例としては、フライス加工ではSKD材の硬さに適したカッターを選定し、適切な送り速度や回転数を見極めることが重要です。タップ加工の際には、高品質のタップと適正な潤滑を選ぶことで、ねじの精度を損なうことなく加工することが可能です。これらの加工技術は製品の品質を左右するため、高い専門性が要求されます。結論として、SKD材のフライス加工・タップ加工を成功させるには、材質に見合った適切な工具選びと加工条件の精密な管理が不可欠であり、これによって産業の発展にも寄与しています。
5-3. 材料卸における注意点
工業用SKD材のフライス加工およびタップ加工は、精密な部品製造には不可欠な技術です。SKD材は耐摩耗性や硬度が高く優れた材料であるため、適切な加工方法を用いることが重要です。フライス加工では、工具の刃先が常に材料に接触するため、切削抵抗を考慮し、適切なスピードと送り速度の設定が求められます。具体的な例として、硬質のSKD材を加工する際には、小さな切削深さを設定し、工具の刃先の磨耗を抑えることで、長寿命を実現します。一方、タップ加工では、正確なピッチのねじを切る技術が必要で、SKD材の硬さに応じた適切なタップと潤滑油の使用が不可欠です。これにより、ねじ山が綺麗で強度のある加工を可能にします。最終的に、これらの加工技術をマスターすることで、耐久性と精度の高い工業用部品が製造できるのです。
6. マシニング加工とフライス加工の相違点
6-1. 加工方法の基本理解
工業用SKD材のフライス加工およびタップ加工は、精密機器や自動車部品など、幅広い分野での製品製造に不可欠です。結論から言えば、適切な加工技術を用いることで、材料の特性を最大限に活用し、製品の品質を高めることが可能です。フライス加工においては、SKD材の硬度や耐摩耗性に配慮した切削工具の選定が重要であり、タップ加工では、材料に応じた適切な切削速度や液体の使用が鍵となります。たとえば、自動車のエンジン部品を製造する際には、耐熱性や強度が求められるため、フライス加工では正確な寸法と滑らかな表面仕上げが、タップ加工では精密なねじの形成が不可欠です。このように、それぞれの加工技術を適切に適用することで、製品の信頼性と寿命を保証することができるのです。最終的には、この加工技術の精度が、製品の品質を左右すると言えるでしょう。
6-2. SKD材加工における選択肢
工業用SKD材のフライス加工やタップ加工は、精密さと効率性が要求されるため、特に製造業において重要である。SKD材は硬く耐摩耗性に優れた特性を有しているが、これらの特性が加工の難しさをもたらしている。例えば、フライス加工では、SKD材の硬さに適した切削工具を選定することが重要であり、またタップ加工の場合は、材料の硬さに合わせて適切な速度や潤滑油を選ぶことが不可欠である。最適な工具や条件の選定によって、加工精度を高めることが可能となり、製品の品質向上にも寄与する。よって、SKD材のフライス加工・タップ加工技術を習得し、適切な方法を選択することは、製造業における品質保持と生産性向上のために不可欠であると結論づけられる。
まとめ
工業用SKD材のフライス加工やタップ加工は、正しい切削条件や刃具の選定が重要です。適切な刃具や工具の選択と加工条件の設定を行い、正確な加工を実施することがポイントです。また、材料の特性や硬さに応じて適切な切削速度や刃先形状を選定することが重要です。正しい加工技術を習得することで、高品質な製品を生産することが可能となります。
タップ加工のプロが明かす!SKD材穴あけのコツと注意点
「SKD材穴あけのコツと注意点」を知りたい方々に向けて、プロが厳選した情報をお届けします。タップ加工やフライス加工における正しい手法や注意すべきポイントについて解説します。SKD材の特性を理解し、効率的な加工を行うために必要な情報をまとめています。タップ加工のプロの視点から、貴重なノウハウをご紹介します。
1. SKD タップ加工の基礎知識
SKD材へのタップ加工は、製品品質に大きな影響を与える重要な工程です。その成功の秘訣は適切な工具選びと加工条件の設定にあります。SKD材は硬度が高く、耐摩耗性に優れているため、タップ加工には専用の工具が必要です。具体例として、高品質なタップと刃の材質を選択し、切削速度や送り速度を材質の硬度に応じて調整することが挙げられます。また、フライス加工によってあらかじめ穴をあけておくことで、タップ加工の負荷を減らし、加工精度を高めることができます。これらのポイントを押さえることで、SKD材穴あけにおけるネジ山の品質を保ちつつ、工具の寿命を延ばし、効率的な生産活動を実現できます。最後に、常に最新の加工技術を取り入れ、品質管理に努めることが重要です。
2. SKD材の特性と加工上の課題
SKD材の加工においては、その特性を理解することが成功の鍵となります。SKD材は耐摩耗性に優れる一方で、硬度が高いためタップ加工やフライス加工が困難であるという課題があります。具体的には、タップ加工では切削抵抗が大きいことによるタップの損傷や破断のリスクが挙げられます。これを回避するためには、工具の選定に加えて加工速度や切り込み深さを適切に設定することが重要です。例えば、高硬度用のタップや、耐熱性に優れたコーティングが施されたタップの使用が有効です。また、切削油の利用で摩擦を低減させることもポイントです。これらのコツと注意点を押さえることで、SKD材の加工精度を高め、工具の耐久性も向上させることができます。
3. HRC60以上の高硬度鋼材へのタップ加工テクニック
SKD材へのタップ加工には特別なコツと注意が必要です。まず、SKD材は高硬度で知られており、そのため加工には耐摩耗性に優れた工具の選択が重要となります。フライス加工においても、工具の摩耗を抑えるためには、適切な切削速度と冷却剤の使用が必須です。例えば、硬度が高い材料には、低い切削速度で加工し、チップの発熱を防ぐために多量の冷却剤を使用することが推奨されます。また、正確な穴あけ位置を保つためには、事前のセンタリング作業を念入りに行うこともポイントです。こうしたコツを把握しながら注意して作業を行えば、SKD材へのタップ加工も成功へと導くことができます。要は、材料特性を理解した上で適切な工具選びと加工条件の調整がSKD材穴あけの成功の鍵を握るのです。
4. SKD フライス加工による穴あけのコツ
SKD材におけるタップ加工の成功は、正しい技術と知識があれば確実に向上します。特にフライス加工においては、加工精度を保つためのポイントを押さえることが重要です。具体例として、先ず回転速度や送り速度などの加工パラメータを適切に設定することが挙げられます。これらは材質の硬さや工具の特性に合わせて微調整する必要があります。また、SKD材の場合、冷却液の使用は適切な温度管理を行い、切削による発熱を抑制するために不可欠です。適切な冷却液の選定と適量の供給を心掛けることで、工具の寿命を延ばし、加工精度も向上します。結論として、SKD材のタップ加工では、加工パラメータの適正と冷却管理が成功の鍵となります。これにより、長期的に安定した加工精度を維持し、製品品質を向上させることができるのです。
5. 斜め穴あけ加工のためのSKDタップ加工のヒント
SKD材の穴あけにおけるタップ加工は、正確な技術が要求され、多くのプロフェッショナルにとって重要な作業です。効率よく丁寧に行うことで、加工物の品質を高めることができます。そのコツとして、まず加工前の正確な位置決めが不可欠です。また、SKD材の硬さを考慮し、適切な切削油の使用により切削抵抗を低減することが重要です。さらに、フライス加工で先に案内穴を開け、その後タップ加工を行うことで、ねじ山が正確に形成されやすくなります。注意点としては、SKD材特有の硬度によるタップの損傷や、切削油の不適切な使用が挙げられます。これらを避けるためにも、加工機の速度や圧力の調整に注意を払い、常に切削状態を監視することが必要です。以上のポイントを押さえておくことで、SKD材のタップ加工はより精度高く、そして効率的に行えるでしょう。
6. 放電タップ加工とSKD材の相性
SKD材におけるタップ加工は精密な技術を要します。この加工に欠かせないのが適切なフライス加工です。SKD材は硬度が高いため、通常の材料よりも加工が難しいですが、正しい方法を理解し実践することで問題なく穴あけが可能です。具体的には、工具の選定に注意し、切削速度を適切に設定することが重要です。加えて、常に工具の状態を確認し、摩耗が進んだ場合は早めに交換する必要があります。これらのポイントを押さえておくことで、SKD材のタップ加工でも高い精度を実現できるでしょう。最終的には、これらのコツと注意点を踏まえた加工を行うことが、SKD材加工の成功に不可欠です。
7. 超硬上下異形状精密加工品のSKDタップ加工
SKD材におけるタップ加工は、適切な技術と知識が必要です。SKD材は硬度が高いため、タップ加工では独特なコツと注意点を把握しておくことが肝心です。まず重要なのは、タップと材料との相性を見極めること。SKD材の硬度に合わせたタップを選ぶことで、折れや摩耗を防ぎ、精度高い加工を実現できます。また、切削液の利用は、摩擦を減らしタップの寿命を延ばす上で欠かせません。加えて、フライス加工で予め穴をあけ、バリや段差を取り除くことは、タップ加工を滑らかに行うための下準備として重要です。上記のポイントを押さえることで、SKD材におけるタップ加工の品質と効率を大幅に向上させることが可能です。
8. マシニングセンタを用いたSKDタップ加工のポイント
SKD材の穴あけにおけるタップ加工は、その耐摩耗性と強度の高さから特別な注意が必要です。正確で長寿命のタップ加工を実現するためには、適切な工具選択と加工条件の設定が欠かせません。例えば、SKD材のフライス加工と比較して、タップ加工では切削速度を落とし、冷却液を十分に使うことがコツです。具体的には、硬いSKD材の場合、加工時の熱による影響を避けるために、低速で安定した回転速度を保ち、断続的な切削を行うことが重要です。このように適切な加工方法を心掛けることで、タップの損傷や破損を防ぎながら、精度の高いねじ加工が可能になります。SKD材の加工においては、こうした細かい点に気を配ることで、長期にわたる安定した生産性と品質の維持が実現します。
まとめ
SKD材におけるタップ加工やフライス加工においては、適切な刃先や切削速度、切削深さなどが重要です。また、冷却や潤滑のための適切な加工液の使用も欠かせません。適切な工具を使用し、正確な設定を行うことで良好な加工が可能です。加工条件を正確に把握し、適切な工具や技術を活用することが成功の鍵となります。