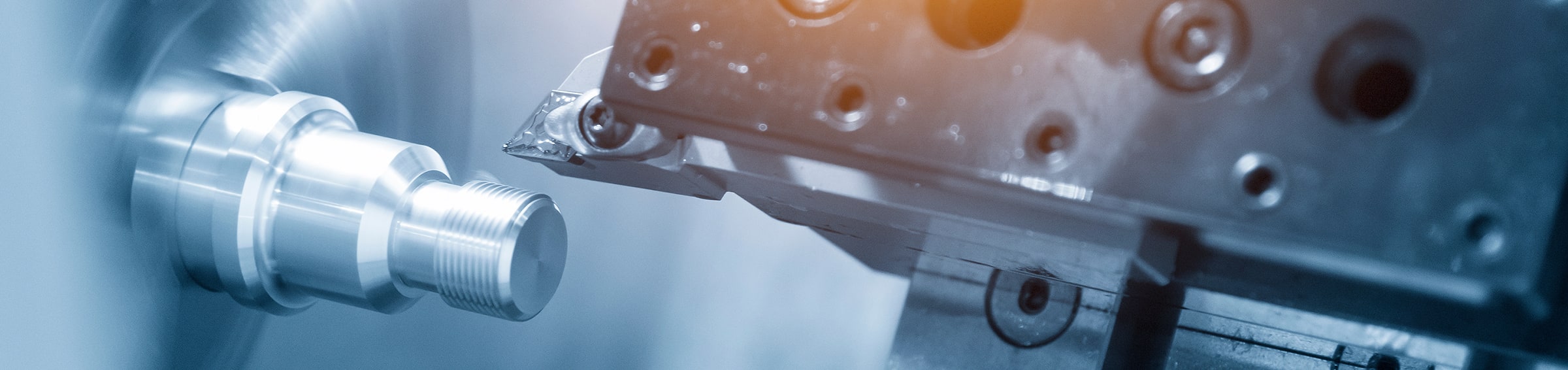
コラム column
【工業技術】鉄のフライス加工で精度を高めるためのテクニック
工業技術分野において、鉄のフライス加工は精密な作業が求められる重要な工程です。このテクニックを利用することで、製品の精度を向上させることが可能となります。加工技術の向上は、製品品質や効率を大幅に改善することができるため、産業界において欠かせない要素となっています。
鉄のフライス加工における技術の習得は、専門的な知識や経験が必要とされるため、初心者にとっては一筋縄ではいかないかもしれません。そこで、本記事では鉄のフライス加工における精度向上のためのテクニックに焦点を当て、実践的なアドバイスや具体的な手法について紹介していきます。
精度を高めるためのさまざまな工夫や注意点、実際の作業手順を通して、鉄のフライス加工における重要性や効果的な手法を理解していただけるよう努めます。工業技術分野における鉄のフライス加工に興味をお持ちの方々にとって、有益な情報が提供できることを心より願っています。
1. 鉄のフライス加工とは
1-1. フライス加工の基本
鉄のフライス加工で精度を高めるためには、いくつかの重要なテクニックがあります。まず、鉄のフライス加工を成功させるための最も基本的なポイントは、適切な切削速度と送り速度の選択です。これらの速度を適切に設定することで、加工面の仕上がりが大きく向上します。例えば、速度が速すぎると切削面に細かい傷がついたり、逆に遅すぎると加工時間が不必要に長くなります。
次に、フライス加工においては、使用する刃の種類も重要です。硬質の鉄を加工する際には、耐久性に優れた超硬質の刃を使用することが推奨されます。これにより、刃の摩耗を抑えることができ、長期間にわたって高い加工精度を保つことが可能となります。
また、鉄のフライス加工では、加工する前に材料の予熱を行うことも一つの方法です。予熱により材料を均一に加熱することで、材料の内部応力が減少し、加工中の変形を最小限に抑えることができます。
これらのテクニックを適切に使用することで、鉄のフライス加工における精度を高めることができます。適切な速度設定、適切な刃の選択、そして必要に応じた予熱処理が、高い加工精度を実現する鍵となります。これらの方法を適用することで、加工効率と製品品質の両方を向上させることが可能です。
1-2. 鉄という材料の特性
鉄のフライス加工における精度向上のテクニックは、鉄の加工を成功させるために不可欠です。鉄はその耐久性と加工しやすさから、多くの工業製品に使用されますが、加工時の精度は製品の品質に直結します。精度を高めるためには、適切な工具選び、加工条件の最適化、そして定期的なメンテナンスが重要です。例えば、超硬材料やコーティングされた工具を使用することで、耐久性を向上させることができます。また、切削速度や送り速度の調整によっても精度は大きく変わります。具体的には、鉄の種類や形状に応じてこれらの条件を変えることが推奨されます。さらに、工具や機械の定期的なメンテナンスを行うことで、常に最高の状態で加工を行うことができます。これらのテクニックを駆使することで、鉄のフライス加工における精度向上を図ることが可能です。結論として、鉄のフライス加工で高い精度を実現するためには、適切な工具の選択、加工条件の最適化、そして定期的なメンテナンスが鍵を握ります。
1-3. 鉄のフライス加工における一般的な問題点
鉄のフライス加工で精度を高めることは、多くの製造業にとって重要です。精度向上のためのテクニックを適用することで、製品の品質を大幅に改善することが可能になります。特に日本の製造業界では、微細な加工技術が求められるため、これらのテクニックは極めて重要です。
一つの理由として、鉄は加工時に発生する熱によって物性が変化しやすいため、加工精度に影響を及ぼすことがあります。そのため、熱影響を最小限に抑える冷却技術や、加工時の振動を軽減する工夫が必要になります。
具体的な例としては、適切な切削油の選定が挙げられます。切削油は、加工時の熱を効率的に逃がす役割を果たし、また、刃と材料の間の摩擦を減らすことで、加工精度を向上させます。さらに、高速でかつ小刻みに加工を行う「ハイスピードカッティング」も、加工精度を高めるテクニックの一つです。これにより、熱の影響を受けにくく、より緻密な加工が実現可能になります。
結論として、鉄のフライス加工において精度を高めるためには、熱管理と振動の抑制が鍵を握っています。適切な切削油の使用や、ハイスピードカッティングのような加工方法の選択により、製品品質の向上が期待できます。これらのテクニックを駆使することで、日本の製造業がさらなる高みを目指すことができるでしょう。
2. 加工精度の基本概念
2-1. 加工精度とは
鉄のフライス加工において、加工精度を高めることは重要です。これは、製品の品質を向上させ、後工程の作業を容易にするためです。高精度を実現するためには、まず加工条件の適正化が必要です。具体的には、適切な切削速度の選定や、フライスカッターの種類と刃の数を考慮することが挙げられます。たとえば、粗加工では大きな切削量で素早く材料を除去するために多刃のカッターを使用し、仕上げ加工では精度を求めるために少刃のカッターを選択することが一般的です。
また、工具の振動を抑えることも精度向上のカギとなります。振動低減のためには、工具とワークの固定方法を見直したり、カッターのバランスを良好に保つことが効果的です。日本の製造業では、このようなテクニックを駆使して精密なフライス加工を実現しています。例えば、自動車部品や家電製品など、日常生活に密接な製品の製造において、これらの技術が活用されています。
結論として、鉄のフライス加工で加工精度を高めるには、加工条件の最適化や工具の振動抑制が重要です。これにより、製品の品質を向上させることができます。日本の製造業では、これらのテクニックが広く採用されており、高品質な製品づくりに貢献しています。
2-2. 加工精度を決定する要因
鉄のフライス加工において、加工精度を高めることは製品の品質向上に直結します。そのために重要なテクニックを理解し適用することが必要です。まず、フライス加工の精度を左右する大きな要因として、適切な工具選択、加工速度、そして工具の経年劣化への対応が挙げられます。
具体的な例として、加工時に生じやすい振動を抑えるためには、工具の刃の数を増やす、または減らすことで、振動を最小限に抑えることが可能です。この振動の抑制は、加工面の仕上がりに直接影響を与え、結果として精度を高めることに繋がります。さらに、加工速度を適切に設定することも重要で、速すぎると工具の摩耗が早まり、遅すぎると加工時間が不必要に長くなり、効率が悪くなります。工具の摩耗については、定期的な交換やメンテナンスを行うことで、常に最適な状態で加工ができるように心掛けるべきです。
これらのテクニックを適切に実行することで、鉄のフライス加工における精度を向上させることが可能です。加工技術の向上は、製品の品質を高め、結果として顧客満足度を向上させることに繋がります。
2-3. 加工精度の範囲とその重要性
鉄のフライス加工で加工精度を高めることは、多くの工業製品の品質向上に直結します。加工精度が高いほど、部品同士の組み合わせがスムーズになり、製品全体の性能が向上します。そのため、精度を高めるテクニックの習得は非常に重要です。
まず、加工する前に材料の状態を正確に把握することが重要です。鉄は熱によって伸縮するため、加工前の材料温度を一定に保つことが精度向上に寄与します。次に、工具の選択と保守に注意を払うことが大切です。適切な工具を選び、定期的にメンテナンスを行うことで、工具の摩耗や変形を防ぎ、安定した加工が可能になります。
特定の例として、日本の一部の製造業者は、フライス加工の際に、超精密な測定機器を使用して材料の温度変化をリアルタイムで監視する技術を導入しています。これにより、加工中の材料の微妙な変化を捉え、即座に調整することで、非常に高い精度を実現しています。
結論として、鉄のフライス加工における精度を高めるためには、材料の状態を管理し、適切な工具を選択・維持することが重要です。加えて、最新の技術を取り入れることで、さらなる精度向上が期待できます。これらのテクニックは、製品の品質を高め、製造業の競争力を強化するために不可欠です。
3. 切削加工の精度を高めるための条件
3-1. 適切な切削工具の選択
鉄のフライス加工において、精度を高めるためには適切な切削工具の選択が重要です。なぜなら、フライス加工では素材の硬度や加工する形状に最適な工具を使うことで、効率よく高精度な加工が可能になるからです。日本では、特に精度が求められる機械部品や工業製品の製造において、この原則が厳しく守られています。例えば、鉄のフライス加工には、硬い素材に適した超硬合金製のエンドミルや、加工面の仕上がりを良くするためのコーティングされた工具がよく用いられます。また、加工速度や送り速度を適切に設定することも、精度向上に不可欠です。これらのテクニックを駆使することで、日本の製造業は国際市場での競争力を維持し続けています。総じて、鉄のフライス加工で高い精度を実現するためには、適切な切削工具の選択が基本であり、これが品質向上への第一歩となります。
3-2. 切削条件の最適化
鉄のフライス加工では、加工の精度を高めることが非常に重要です。そのためには、切削条件の最適化が鍵を握ります。この最適化を実現するためには、具体的なテクニックを理解し適用する必要があります。
例えば、切削速度、送り速度、切削深さなど、各パラメータを適切に設定することが肝心です。特に、鉄のような硬い材料を加工する際には、切削速度を適切に選択することが重要です。速すぎると工具の摩耗が早まり、遅すぎると加工時間が不必要に長くなります。また、送り速度と切削深さを調整することで、仕上がりの精度を向上させることができます。
実際に、日本の製造業では、これらのテクニックを用いてフライス加工の精度を大幅に向上させています。例として、ある自動車部品製造会社では、切削条件を最適化することにより、部品の寸法精度を向上させるとともに、生産効率を20%以上改善することに成功しました。
結論として、鉄のフライス加工で精度を高めるためには、切削条件の最適化が不可欠です。具体的なテクニックを適用することで、加工精度の向上と生産効率の改善が期待できます。
3-3. 機械の精度とメンテナンス
鉄のフライス加工で精度を高めるためには、適切なテクニックの適用が欠かせません。その理由は、フライス加工の精度が最終製品の品質に直接影響を及ぼすからです。例えば、正確なフライス加工によって、部品の寸法精度が向上し、組み立ての容易さや製品の耐久性が高まります。日本では、特に精密な加工が要求される工業製品が多く、そのための高度な技術開発と知識が求められています。
具体的なテクニックとしては、まず、適切な切削工具の選択が挙げられます。鉄材の硬さや加工する形状に応じて、最適な工具を選ぶことが精度を保つ上で重要です。さらに、工具の摩耗を定期的にチェックし、必要に応じて交換することも、一貫した精度を維持するために不可欠です。また、フライス加工機の定期的なメンテナンスを行うことで、機械自体の精度を保つことができます。
結論として、鉄のフライス加工で精度を高めるためには、適切な工具の選定と定期的なメンテナンスが重要であると言えます。これらのテクニックを適切に適用することで、製品の品質向上に貢献し、高い精度の実現が可能です。日本の工業技術は、このような細部にまでこだわる姿勢が世界でも高く評価されています。
4. フライス加工精度向上のテクニック
4-1. 切削速度の調整
鉄のフライス加工で精度を高めるためには、切削速度の調整が非常に重要です。理由としては、切削速度が適切でないと材料の熱処理に影響を与え、最終的な製品の品質に悪影響を及ぼす可能性があるからです。具体的な例として、速度が遅すぎる場合は加工時間が長くなり、不経済であるだけでなく、鉄の表面に不要な硬化を引き起こすことがあります。一方で、速度が速すぎる場合は、切削工具の摩耗が激しくなり、精度が低下する恐れがあります。日本では、特に精密な部品を製造する際に、このバランスを取ることが求められます。したがって、フライス加工においては、材料の種類や加工する部品の形状に応じて、最適な切削速度を見つけることが精度向上の鍵となります。結論として、鉄のフライス加工において精度を高めるためには、切削速度の適切な調整が不可欠であり、これにより高品質な製品の製造が可能となります。
4-2. 送り速度と切り込み深さの最適化
フライス加工で鉄の精度を高めるためには、送り速度と切り込み深さの最適化が重要です。これら二つの要素は加工精度に大きく影響し、適切に設定することで、より高品質な仕上がりを実現できます。
送り速度が速すぎると、鉄の加工面に細かい傷がついたり、仕上がりの品質が低下する原因となります。一方で、遅すぎる送り速度は加工時間が過剰に伸び、生産効率が低下します。また、切り込み深さが深すぎると、工具への負荷が増大し、工具の寿命を短くしてしまいます。しかし、浅すぎる切り込みでは、複数回にわたって加工を行う必要があり、これもまた効率を下げる原因になります。
例えば、日本のある工場では、これらの要素を徹底的に検証し、鉄のフライス加工において最適な送り速度と切り込み深さを見つけ出したところ、加工品質が大幅に向上しました。この工場では、具体的な数値を元に調整を行い、加工精度の向上に成功しています。
結論として、送り速度と切り込み深さを最適化することで、鉄のフライス加工における精度を高めることが可能です。これにより、製品の品質向上に直結し、生産効率の向上にも繋がります。
4-3. 冷却剤の使用
鉄のフライス加工で精度を高める重要なテクニックの一つは、冷却剤の適切な使用です。これにより、加工中の摩擦を効果的に低減し、鉄の熱変形を防ぐことができます。具体的な例として、水溶性の冷却剤は鉄の温度を均一に保ちながら、加工面の滑らかさを向上させるのに役立ちます。また、冷却剤は切削工具の寿命を延ばす効果もあり、結果的に加工コストの削減にも繋がります。
加工精度を高めるためには、冷却剤の流量や噴射の方向にも注意が必要です。適切な量を適切な場所に噴射することで、最大限の効果を発揮させることが可能です。日本の製造現場では、このようにして冷却剤の管理を徹底することで、世界でもトップクラスの加工精度を実現しています。
まとめると、鉄のフライス加工において精度を高めるためには、冷却剤の適切な使用が不可欠です。これは摩擦と熱変形を低減し、工具の寿命を延ばし、結果的に高品質な加工を実現するための鍵となります。
5. 材料ごとの加工性と鉄の特性
5-1. 鉄の加工性とは
鉄のフライス加工で精度を高めることは、製品の品質向上に直結する重要な工程です。この加工における精度を向上させるためには、いくつかのテクニックがあります。まず、適切な切削条件の選定が必須です。これには、切削速度、送り速度、切り込み深さが含まれます。例えば、鉄を加工する際には比較的低い切削速度を選択することが推奨されます。これは、鉄が硬い材料であるため、高速での加工は刃の摩耗を早め、精度を下げる可能性があるからです。
また、使用するフライスカッターの選択も精度に大きく影響します。高品質なカッターを使用することで、加工面の仕上がりが良くなり、精度が向上します。日本には高品質な工具を供給するメーカーが多く存在し、これらの利用が推奨されます。
さらに、鉄のフライス加工では、加工機械の振動を抑えることが非常に重要です。機械の振動は加工精度に悪影響を及ぼし、製品の品質にばらつきを生じさせる原因となります。この問題を解決するために、加工機械の定期的なメンテナンスや、適切な固定具の使用が推奨されます。
結論として、鉄のフライス加工で精度を高めるためには、適切な切削条件の選定、高品質なカッターの使用、機械の振動を抑える対策が必要となります。これらのテクニックを適切に実施することで、製品の品質を大きく向上させることができます。
5-2. 他の材料との比較
鉄のフライス加工において、他の材料と比較して精度を高めることは極めて重要です。鉄はその耐久性と加工性に優れ、多くの工業製品の基礎として使用されています。しかし、その硬度のために正確な加工を行うには特別な注意が必要です。例えば、適切な切削速度の選定や、冷却剤の使用は鉄のフライス加工の精度を上げるうえで不可欠です。さらに、使用する工具の材質にも注意が必要で、鉄を加工する際には特に硬い材質の工具を選ぶことが推奨されます。これらのテクニックを適用することで、加工中の鉄の変形や工具の摩耗を減少させ、結果として高い精度の製品を生産することが可能になります。最終的に、これらの対策を講じることによって、鉄のフライス加工の品質と効率は大幅に向上することが明らかです。
5-3. 材料特性に応じた加工条件の調整
鉄のフライス加工における精度を高めるためのテクニックには、材料特性に応じた加工条件の調整が欠かせません。鉄は硬度が高く、耐久性に優れているため、加工時には特に注意が必要です。高精度を実現するためには、まず、適切な切削速度の選定が重要です。速すぎると工具の摩耗が早まり、遅すぎると加工時間が過剰になります。例えば、一般的な低炭素鋼であれば、切削速度を中程度に設定することが多いです。
さらに、工具の材質も精度に大きく影響します。硬質の材料を加工する際には、超硬合金やコーティングされた工具が推奨されます。これらは摩耗に強く、より長い期間、安定した加工が可能です。また、工具の冷却も重要なテクニックの一つです。鉄の加工時には、適切な冷却液を使用することで、工具の摩耗を抑え、加工面の品質を向上させることができます。
このように、材料特性に応じた加工条件の調整を行うことで、鉄のフライス加工の精度を高めることが可能です。適切な切削速度の選定、工具の材質の選択、適切な冷却方法の採用が、その鍵を握ります。これらのテクニックを駆使することで、精度の高い加工が実現し、製品の品質向上につながります。
6. 切削加工における変形への対応
6-1. 加工中の変形とその原因
鉄のフライス加工において精度を高めることは、製品の品質を向上させる上で非常に重要です。加工精度を上げるためには、加工中の変形を理解し、適切な対策を講じる必要があります。鉄は硬くて加工しにくい特性を持っているため、フライス加工中に生じる熱や力によって変形しやすいのです。例えば、フライス加工中に発生する熱は、材料の膨張を引き起こし、結果として寸法の不精度につながります。また、切削力が大きすぎると材料が歪む原因となり得ます。
このような変形を避けるためには、適切な切削条件の選定が重要です。例えば、切削速度、送り速度、切削深さを適切に設定することで、発生する熱を抑制し、変形を最小限に抑えることができます。また、高品質の工具を使用することや、冷却液を適切に使用することでも、熱の影響を軽減し、精度を高めることが可能です。
結論として、鉄のフライス加工で精度を高めるためには、加工中の変形を理解し、それに対する適切な対策を講じることが極めて重要です。切削条件の適切な選定や高品質の工具の使用、冷却液の効果的な利用などが、そのための具体的な手段となります。これらのテクニックを駆使することで、鉄のフライス加工品の品質向上につながるでしょう。
6-2. 変形を最小限に抑えるための工夫
鉄のフライス加工では、精度を高めることが重要です。そのためには、加工における変形を最小限に抑える工夫が必要です。変形を抑制する理由は、加工された鉄製品の品質を保つためです。高い精度を維持するためには、カットする際の力のかかり方を均等にし、熱による影響を最小限に抑える必要があります。たとえば、フライス加工を行う際に使用する刃の速度や鉄材への冷却方法の調整が挙げられます。具体的には、刃の回転数を適切に設定することや、加工中に冷却液を適切な量で供給し続けることが、変形を最小限に抑え精度を高める上で効果的です。最終的に、これらのテクニックを駆使することで、フライス加工後の鉄製品の精度が向上し、より高品質な製品を製造することが可能になります。このように、変形を抑制するための工夫は、鉄のフライス加工における精度向上に不可欠です。
6-3. 加工後の仕上げ処理
鉄のフライス加工において精度を高めるテクニックは、製品の品質向上に直結します。そのため、加工後の仕上げ処理は非常に重要です。まず、フライス加工の精度を高める一つの方法として、適切な工具の選択があります。鉄加工に最適なフライス工具を使用することで、加工面の滑らかさと精度が向上します。また、加工条件の最適化も重要です。切削速度、送り速度、切り込み量を適切に設定することで、振動を抑え、精度の高い加工が可能になります。
具体例として、高速度鋼や超硬合金製のフライスカッターは、鉄加工において良好な仕上がりを得るために推奨されます。これらの工具は耐久性に優れ、鉄の硬い材質にも対応できるため、加工時の精度が保たれます。
さらに、冷却液の使用も重要です。加工中に発生する熱を効率的に排出することで、材料の変形を防ぎ、仕上がりの品質を保つことができます。例えば、合成冷却液は、加工精度を高めるために良く使用されます。
結論として、鉄のフライス加工で精度を高めるためには、適切な工具の選択、加工条件の最適化、そして効果的な冷却方法の適用が不可欠です。これらのテクニックを適切に実施することで、加工後の仕上げ処理の品質を向上させることができます。
7. 実践的な問題解決
7-1. よくある加工精度の問題とその対策
鉄のフライス加工において、加工精度を高めることは製品の品質に直結します。そのため、加工精度を高めるテクニックを理解し、適用することが重要です。まず、鉄のフライス加工で精度を高めるためには、適切な工具選択が欠かせません。例えば、加工する鉄の種類や硬度に合わせて、切削速度やフィード速度を調整することが挙げられます。具体的には、硬い材料を加工する際には低い切削速度を選択し、軟らかい材料では高い切削速度が適しています。
さらに、工具の摩耗を定期的にチェックし、必要に応じて交換することも精度向上に寄与します。工具が摩耗すると、加工面に微細な傷が発生しやすくなり、結果として加工精度が低下します。例として、フライス加工中に生じた工具の摩耗を見落とし、そのまま加工を続けた結果、製品の寸法が規定値から大きく外れたケースがあります。
また、加工機械の定期的なメンテナンスも重要です。機械が正確に動作しない場合、精密な加工は不可能になります。例えば、フライス機のガイドウェイにガタがあると、工具の位置精度が低下し、製品の寸法精度に影響します。
結論として、鉄のフライス加工で加工精度を高めるためには、適切な工具選択、工具の摩耗管理、そして機械の定期的なメンテナンスが欠かせません。これらのテクニックを適切に実施することで、高品質な製品を効率的に生産することができます。
7-2. ケーススタディ:加工誤差のトラブルシューティング
鉄のフライス加工では、精度を高めるためのテクニックが不可欠です。高い精度を達成することは、製品の品質を大きく左右するため、非常に重要です。そのためには、具体的なテクニックの適用が求められます。
まず、適切な切削工具の選定が重要です。鉄の加工には硬質の材料を使用した工具が適しています。また、工具の摩耗を最小限に抑えるため、定期的な交換やメンテナンスが必要です。さらに、フライス加工の速度や送り速度の調整も精度に影響を与えます。適切な速度設定により、加工中の材料の熱変形を防ぎ、精度を保つことができます。
具体例として、ある製造業者はこれらのテクニックを採用し、製品の不良率を大幅に減少させました。切削工具の選定に注意を払い、定期的なメンテナンスを実施することで、加工誤差を劇的に減らすことができました。また、加工速度の最適化により、熱変形による誤差も最小限に抑えることが成功しました。
結論として、鉄のフライス加工で高い精度を達成するには、適切な工具の選定とメンテナンス、そして加工速度の調整が非常に重要です。これらのテクニックを適用することで、製品の品質を向上させることが可能です。
7-3. 継続的な品質改善のためのプロセス管理
鉄のフライス加工における精度向上は、製品品質を高め、製造コストを削減する上で欠かせない要素です。精度を高めるためには、適切なプロセス管理が必要となります。その理由は、フライス加工の精度が製品の性能や寿命に直接影響を与えるからです。例えば、正確な寸法が要求される自動車のエンジン部品などでは、わずかな寸法の違いが製品全体の性能低下を招く可能性があります。そのため、加工中に発生する熱の管理や、切削工具の選定、さらには機械の振動を抑制する技術が重要となります。具体的には、クーラントの使用や、高品質な切削工具の選択、そして適切なフィードレートの設定が挙げられます。これらの取り組みにより、鉄のフライス加工の精度を大きく向上させることが可能です。結論として、鉄のフライス加工で精度を高めるためには、プロセス管理を徹底し、適切な技術を用いることが重要であると言えます。
8. フライス加工の将来と革新的な技術
8-1. 高精度加工のための新しい技術
鉄のフライス加工で精度を上げる技術は、製品の品質を保証し、製造コストを削減するために非常に重要です。フライス加工の精度を高めるためには、適切な工具選択、切削条件の最適化、そして最新技術の活用が必要です。例えば、多層コーティングされたカッターや超硬材料を使用することで、耐久性と切削性能が向上し、精度の高い加工が可能になります。また、振動を抑制する技術や、加工時の熱影響を最小限に抑える冷却方法の選定も、精度向上に寄与します。日本では、これらの技術が積極的に研究され、実際の製造現場での応用が進んでいます。これにより、鉄のフライス加工の精度は飛躍的に向上しており、高品質な製品の製造に貢献しています。結論として、適切な工具の選択、切削条件の最適化、そして最新技術の導入は、鉄のフライス加工の精度を高める上で不可欠であり、これらを通じて、製造業の競争力強化に繋がっています。
8-2. 自動化と精密加工の組み合わせ
鉄のフライス加工において精度を高めるテクニックは、製品品質の向上と効率的な生産活動に不可欠です。実際、日本の製造業では、この技術を駆使して世界トップクラスの製品を生み出しています。まず、精度を高める主な理由は、製品の性能や耐久性を向上させるためです。例えば、自動車部品や建設機械など、鉄を使用した製品は精密な加工が求められます。
特に有効なテクニックの一つが、適切な切削工具の選択です。工具の材質や形状を加工する鉄の種類に応じて選び、摩耗を最小限に抑えることで、一貫した精度を維持できます。また、切削条件(切削速度、送り速度、切り込み量)の最適化も重要で、これにより加工時の振動を減らし、精度を高めることができます。
実際の例として、日本のある自動車部品製造会社では、これらのテクニックを組み合わせることで、製品の不良率を大幅に減少させ、生産性を20%向上させることに成功しました。このように、鉄のフライス加工で精度を高めることは、製品の品質向上はもちろんのこと、製造コストの削減にも繋がるのです。
結論として、鉄のフライス加工における精度の向上は、適切な切削工具の選択と切削条件の最適化により実現可能です。日本の製造業が世界で競争力を持続させるためにも、これらのテクニックの習得と活用が今後も重要であると言えます。
8-3. 環境に優しい持続可能な加工技術
鉄のフライス加工において精度を高めることは、製造業の重要な課題の一つです。適切な技術を用いることで、製品の品質向上と生産効率の向上が期待できます。特に日本では、高品質な製品への需要が非常に高いため、フライス加工の精度向上は業界全体にとって重要なテーマとなっています。
精度を向上させるためのテクニックの一つは、適切な切削工具の選定です。切削工具には様々な種類があり、加工する材料の種類や形状によって最適なものを選ぶ必要があります。たとえば、鉄の加工には、高い耐久性と切削能力を持つカーバイド製の工具が適しています。
また、工具の正しい取り付け方と適切な切削条件の設定も精度を左右します。工具が正しく固定されていないと、加工中に工具が振動してしらみ加工が発生し、精度が低下する可能性があります。切削速度、送り速度、切削深さなど、条件を最適に設定することで、加工精度を向上させることができます。
具体的な例として、鉄をフライス加工する際には、冷却液を適切に使用することが推奨されます。冷却液は、加工中の摩擦熱を減少させ、工具の摩耗を抑制し、結果として加工精度を向上させます。
最終的に、これらのテクニックを適切に組み合わせることで、鉄のフライス加工における精度を大幅に向上させることが可能です。高精度な加工技術は、製品の品質を保証し、製造業における競争力を高めるために不可欠です。
まとめ
鉄のフライス加工において精度を高めるためには、適切な切削条件と工具選定が重要です。適切な切削条件を確立することで、加工品質を向上させることができます。また、適切な切削速度や切削深さを設定することで、加工時の振動や切屑の排出を抑えることができます。これにより、加工精度を高めることができます。さらに、適切な工具選定も重要であり、刃先形状やコーティングの特性によって加工精度が大きく左右されます。これらのテクニックを活用することで、鉄のフライス加工における精度向上が可能となります。
フライス加工の基礎知識:アップカットとダウンカットの違いとは?
鉄やその他の金属を加工する際、フライス加工は欠かせない技術の一つです。しかし、初めて聞く人には、「アップカット」と「ダウンカット」の違いがわかりにくいかもしれません。本記事では、フライス加工の基礎知識に焦点を当て、その中でもアップカットとダウンカットの違いについて解説します。この違いを理解することで、あなたのフライス加工技術が向上し、より効率的な加工が可能になるでしょう。加工技術における重要なポイントを探求する旅に出発しましょう。
1. フライス加工とは
1-1. フライス加工の歴史
フライス加工では、金属などの素材から所望の形状を削り出すために、アップカットとダウンカットの二つの方法が一般的に用いられます。これらの加工方法の違いを理解することは、効率的で正確な加工を行ううえで非常に重要です。具体的には、アップカット加工は、カッターが素材に対して上から下へと進む方法で、これにより切りくずが上向きに排出されます。この方法は特に、切りくずの除去が容易であるため、清潔な加工環境を保ちやすいという利点があります。一方、ダウンカット加工は、カッターが素材に対して下から上へと進む方法で、切りくずが素材に押し込まれるため、仕上がりが非常に滑らかになるという特徴があります。日本においても鉄をはじめとする金属加工でこれらの方法が採用されていますが、加工する素材や目的に応じて適切な方法を選択することが重要です。たとえば、鉄の精密な部品を製造する場合、ダウンカット加工が好まれることが多いです。これらの違いを理解し適切に適用することで、フライス加工の精度と効率を大幅に向上させることができます。
1-2. フライス加工の基本原理
フライス加工は、鉄などの材料を削ることで形を整える加工技術です。この加工には主に二つの方法、アップカットとダウンカットがあります。これらの違いを理解することは、加工の質を向上させる上で非常に重要です。
アップカット加工では、カッターが材料に対して下から上へと削り取る方法です。この方法の利点は、切削時に材料が持ち上がりにくいため、加工精度が向上する点にあります。一方で、ダウンカット加工は、カッターが上から下へと材料を削る方法で、表面が非常に滑らかに仕上がることが特徴です。しかし、材料が押し下げられるため、薄い材料の加工には不向きである場合があります。
例えば、精密な加工が求められる電子部品の製造には、アップカット加工が選ばれることが多いです。一方で、見た目が重要な家具の表面加工などには、ダウンカット加工が用いられることがあります。
結論として、アップカットとダウンカットの違いを適切に理解し、それぞれの特性を活かした加工方法の選択が、高品質な製品を作り出す上で重要です。各プロジェクトの要件に応じて最適な方法を選び、効率的かつ効果的な加工を実現しましょう。
1-3. 鉄のフライス加工の特徴
フライス加工におけるアップカットとダウンカットの違いは、加工の品質と効率に大きく影響します。具体的には、アップカット加工は切削時にカッターが材料を持ち上げる動きをし、これによりクリーンな仕上がりが得られることが多いです。一方、ダウンカット加工は材料を押し付ける形で切削を行い、加工面に対する圧力が大きくなります。これは、特に鉄のような硬い材料を加工する際に、滑らかな表面を得るために有効です。
例えば、アップカット加工は、比較的軽い切削が可能で、特に薄い材料や精密な加工が求められる場合に適しています。これに対し、ダウンカット加工は、鉄を含む硬い材料の加工において、優れた表面仕上がりを実現することができます。これは、ダウンカット加工が材料への圧力を利用して、切削時に発生するバリの形成を抑えるためです。
このように、フライス加工においてアップカットとダウンカットを適切に選択することは重要です。アップカットが精密な加工に、ダウンカットが硬い材料の滑らかな仕上げに有効であることを理解することは、加工品質の向上と効率化への大きな一歩となります。
1-4. フライス加工機の種類と選び方
フライス加工において、アップカットとダウンカットの違いを理解することは重要です。これらの加工方法は、加工する素材の種類や目的によって選ばれます。アップカット加工では、カッターが回転する方向と同じ方向に素材を送ります。これにより、カッターが素材に食い込む力が増し、鋭い切削が可能になります。特に、金属やプラスチックのような硬い素材の加工に適しています。一方、ダウンカット加工は、カッターの回転方向と逆の方向に素材を送る方法です。この方法では、加工面が滑らかになるため、木材加工に適していると言えます。例えば、木材を加工する際にダウンカット加工を選ぶことで、仕上がりの美しさを保ちながら、加工を行うことができます。要するに、アップカットとダウンカットの選択は、加工する素材や仕上がりの品質に大きく影響します。この知識を持つことで、より良い加工結果を得ることが可能になります。
2. フライス加工の工程
2-1. 加工前の準備
フライス加工におけるアップカットとダウンカットの違いは、加工の効率と仕上がりの質に大きく影響します。アップカットは、工具が回転する方向と同じ方向に素材を送る方法で、切りくずが上方に排出されます。これは、主に金属の削り取りが容易で、加工速度が速くなるという利点があります。一方、ダウンカットは、工具の回転方向と反対に素材を送る方法で、切りくずが下方に押し込まれるため、仕上がりの表面が非常に滑らかになります。これは、特に表面精度を要求される加工に適しています。
例えば、鉄のフライス加工を行う際、アップカットでは素早く粗削りを行うことができ、その後ダウンカットを用いて仕上げ加工をすることで、加工速度と仕上がりの質のバランスを取ることができます。こうしたアップカットとダウンカットの適切な使い分けは、加工の効率化と製品の品質向上に寄与します。
結論として、フライス加工におけるアップカットとダウンカットの違いを理解し、適切に使い分けることは、工具の寿命を延ばし、加工効率を高め、製品の品質を向上させる鍵となります。
2-2. 加工プロセスの概要
フライス加工において、アップカットとダウンカットは重要な概念です。フライス加工は、鉄などの材料をカッターで削ることで形をつくる加工方法ですが、このときカッターの回転方向と材料への進行方向の関係によって、アップカットとダウンカットに分けられます。アップカットはカッターの回転が材料の進行方向と同じで、材料を持ち上げるように削ります。これに対し、ダウンカットはカッターの回転が材料の進行方向と反対で、材料を押し下げながら削ります。
アップカットは、カッターが材料を引き上げる作用により、切削が容易であるというメリットがありますが、材料が持ち上がることで加工精度が落ちる可能性があります。一方、ダウンカットは、材料を押し下げる作用により、加工面が滑らかになりやすく、高い加工精度を期待できますが、切削抵抗が大きくなることが欠点です。
例えば、木材加工において、アップカットは荒削りに適しており、ダウンカットは仕上げ加工や精密な加工に適しています。また、鉄などの金属加工においても、加工する材料の種類や目的に応じて、アップカット、ダウンカットを選択することが大切です。
結論として、フライス加工におけるアップカットとダウンカットの違いを理解し、加工する材料や目的に応じて適切な方法を選択することが、高品質な製品を製造する上で極めて重要です。
2-3. 加工後の仕上げ
フライス加工において、アップカットとダウンカットはその基本的な違いを理解することが重要です。まず、アップカット加工は、工具の回転方向が仕上げ面から材料を持ち上げる方向になっている加工方法です。これにより、切削時に材料が引き上げられ、清らかな仕上がりが期待できます。一方、ダウンカット加工は、工具の回転が材料を押し下げる方向に進むため、材料が固定され、より安定した加工が可能になります。特に、鉄などの硬い材料を加工する際には、この差が大きな影響を与えることがあります。
具体例として、アップカット加工では、木材やプラスチックのような軽い材料で細かい仕上がりが必要な場合に適しています。一方で、ダウンカット加工は、鉄を始めとする重い材料に適しており、加工時の振動を抑え、滑らかな仕上げ面を確保するのに有効です。
結論として、フライス加工におけるアップカットとダウンカットの選択は、加工する材料の特性や仕上がりの要求によって異なります。各方法の特徴を理解し、適切な加工方法を選択することが、高品質な製品を生産する上で非常に重要です。
3. アップカットとダウンカットの基本
3-1. アップカット加工法の概要
フライス加工において、アップカットとダウンカットの違いを理解することは重要です。これらの加工法は、鉄などの材料を削る際に用いられ、仕上がりの質や加工速度に大きな影響を与えます。まず、アップカット加工では、カッターが材料を持ち上げながら削る方法です。これにより、切削抵抗が少なくなり、比較的クリーンな仕上がりが得られます。一方、ダウンカット加工は、カッターが材料を押し付けながら削る方法で、材料の固定がしやすく、加工中の材料の動きが少ないため、精度の高い加工が可能です。
例えば、アップカット加工は、薄い材料や、加工時に材料が動きやすい場合に適しています。一方で、ダウンカット加工は、厚みのある材料や、より高精度な仕上げが求められる場合に有効です。
このように、アップカットとダウンカット加工はそれぞれ特徴があり、加工する材料や目的に応じて適切な方法を選択することが重要です。この基本的な知識を理解することで、フライス加工の効率と品質を大きく向上させることができます。
3-2. ダウンカット加工法の概要
フライス加工において、アップカットとダウンカットは重要な違いを持ち、それぞれが適している材料や加工方法に差があります。簡単に言えば、アップカット加工は切削工具が材料を持ち上げるように切り込む方法で、ダウンカット加工は材料を押し下げる形で切り込みます。この基本的な違いが、加工品質や効率に大きく影響します。
具体的に、アップカット加工では、切削時に材料が持ち上がるため、鉄などの硬い材料の加工に向いています。これにより、切削面が滑らかになり、精度の高い加工が可能です。一方、ダウンカット加工は、材料を押し付けながら加工するため、薄い材料や柔らかい材料の加工に適しています。これにより、材料が振動しにくく、加工中の材料の安定性が向上します。
例えば、木材の加工には、切断面の仕上がりを重視するため、ダウンカット加工が好まれます。逆に、鉄などの金属加工では、精度と切削速度を重視するため、アップカット加工が多用されます。このように、アップカットとダウンカットはそれぞれに適した用途があり、加工する材料や目的に応じて選択することが重要です。
まとめると、アップカット加工とダウンカット加工は、それぞれ異なる特性を持ち、加工する材料や目的に合わせて適切に選択することが加工品質を向上させる鍵となります。適切な加工方法を選択することで、効率的で高品質な加工を実現できます。
3-3. アップカットとダウンカットの比較
フライス加工において、アップカットとダウンカットは重要な選択肢です。この2つの方法は、加工される素材や目的によって使い分けられます。具体的に、アップカットは工具が回転する向きと同じ方向に素材を切り取る方法で、これにより切削力が上向きに働きます。一方、ダウンカットは工具の回転と反対方向に素材を切り取り、切削力が下向きになります。これらの違いが加工品質に大きな影響を与えるのです。
例えば、アップカット加工は切り屑の排出が良く、深い切り込みが可能ですが、素材が持ち上がることがあるため、加工品の表面が荒れやすいです。これに対して、ダウンカット加工では切削力が素材を押さえつけるため、加工品の表面が非常に滑らかに仕上がりますが、切り屑の排出が悪くなることが欠点です。
日本においてフライス加工は多岐にわたる産業で利用されており、特に精密な仕上がりが求められる場合には、これらの特性を理解し適切な方法を選択することが重要です。合理的な選択をすることで、効率的かつ高品質な加工が可能になります。したがって、アップカットとダウンカットの違いを知り、それぞれの長所と短所を踏まえた上で、最適な加工方法を選択することが、高品質な製品を生み出す鍵となるのです。
4. アップカット加工の詳細
4-1. アップカットのメカニズム
フライス加工におけるアップカットとダウンカットの違いは、加工品への切削方向に基づいています。アップカットでは、刃が材料の下から上へと切り込むことで、切り屑を上方向に排出します。これは、主に木材や軟質の金属加工に適している方法で、切削時の材料の引っ掛かりを減らし、滑らかな仕上がりを実現します。一方、ダウンカットは、刃が材料の上から下へと切り込む動きをします。この方法は、主に鉄を含む硬質の材料加工に適しており、加工面の仕上がりをよりきれいに保つことができます。例えば、精密なフライス加工が求められる電子部品などの製造において、ダウンカット加工が好んで用いられます。
結論として、アップカットとダウンカットの違いは切削方向にあり、それぞれ異なる材料や加工要求に応じて選択されるべきです。アップカットは材料の引っ掛かりを減らし滑らかな仕上がりを求める場合に、ダウンカットは加工面の仕上がりを重視する硬質材料に適しています。適切な方法を選択することで、フライス加工の質を高めることが可能です。
4-2. アップカットの利点
フライス加工におけるアップカットとダウンカットは、それぞれ異なる利点を持っていますが、今回はアップカットの特徴とその有用性に焦点を当てましょう。アップカット加工では、切削工具が回転する方向と同じ方向に仕事を進めるため、材料を持ち上げながら切削することが特徴です。この方法の最大の利点は、加工中に出る切削屑が効率よく排出される点にあります。特に、粘り気がある材料や、温度が上昇しやすい金属の加工において、この特性はクリーンな加工面を維持するのに役立ちます。例えば、鉄などの金属加工では、アップカットによって切削屑が加工エリアから迅速に除去され、工具の摩耗や加工物の品質低下を防ぐ効果が期待できます。結論として、アップカットは切削屑の効率的な排出を可能にし、その結果、加工品質の向上や工具寿命の延長に寄与する有効な加工方法であると言えるでしょう。
4-3. アップカットの適用例
フライス加工において、アップカットとダウンカットが存在することは、素材の仕上がり品質に大きく影響します。アップカットは、刃が素材を持ち上げながら切削する方法で、特に鉄のような硬い素材に適しています。これに対して、ダウンカットは、刃が素材を押し下げながら切削する方法で、仕上がりの滑らかさを重視する場合に選ばれます。
例えば、鉄を加工する際にアップカットを用いると、素材が固いため刃の持ち上げる力で素材の切削が容易になり、加工精度が向上します。一方で、ダウンカットは、木材やプラスチックなどの柔らかい素材に使用されることが多く、表面の仕上げを滑らかにしたい場合に適しています。
したがって、フライス加工を行う際は、加工する素材の特性を考慮し、アップカットとダウンカットのどちらを使用するかを選ぶことが重要です。鉄のように硬い素材ではアップカットが、仕上げの美しさを求める場合にはダウンカットが適しています。この選択により、加工の効率化と製品の品質向上が期待できます。
5. ダウンカット加工の詳細
5-1. ダウンカットのメカニズム
フライス加工において、アップカットとダウンカットは重要な概念であり、加工の品質や効率を大きく左右します。アップカットとダウンカットの主な違いは、切削方向にあります。この違いによって、加工される材料の仕上がりや加工速度が変わります。
ダウンカット加工は、カッターが回転する方向と同じ方向に材料を送る方法です。この方法では、切削力が材料を押さえ付けるため、加工表面の仕上がりが非常に良くなります。特に、鉄などの硬い材料を加工する際に有効です。例えば、表面が滑らかで精密な加工が必要な部品製造において、ダウンカット加工は優れた選択肢となります。
一方、アップカット加工は、カッターが回転する方向と逆に材料を送る方法です。この加工法は、切りくずを効率的に排出するため、深い切削や大量の材料を迅速に削り取る場合に適しています。しかし、アップカット加工は、加工表面に少々の荒れが生じる可能性があります。
結論として、フライス加工におけるアップカットとダウンカットの選択は、加工する材料の種類や求められる仕上がり、加工速度を考慮して行う必要があります。ダウンカットは高い仕上がりを重視する場合、一方アップカットは加工速度や切りくずの排出を優先する場合に選ばれます。適切な方法を選ぶことで、効率的かつ高品質な加工が可能となります。
5-2. ダウンカットの利点
フライス加工における「アップカット」と「ダウンカット」の違いを理解することは重要です。そもそも、これらは鉄をはじめとした金属加工において、切削方向が異なる二つの方法を指します。アップカットでは、カッターが材料を持ち上げながら切削するのに対し、ダウンカットでは材料を押し込みながら切削する方式です。それぞれの方法には特徴があり、加工する材料や求められる仕上がりによって使い分けられます。
たとえば、アップカット加工は切屑の排出が容易であるため、深い溝の加工や粗加工に適しています。一方、ダウンカット加工は、カッターが材料を下に押し込むことで、表面を滑らかに仕上げることができます。このため、仕上げ加工や精密加工において優れた性能を発揮します。
例を挙げると、精密な部品を製造する際や、美しい表面仕上げが求められる製品には、ダウンカット加工が用いられることが多いです。逆に、大量の材料を素早く取り除く必要がある場合や、切削時の熱を効率的に逃がす必要がある場合は、アップカット加工が選ばれます。
結論として、アップカットとダウンカットはそれぞれ異なる利点を持ち、加工する材料や求められる仕上がりに応じて選択すべき方法です。適切な選択により、加工効率の向上や製品品質の向上が期待できます。
5-3. ダウンカットの適用例
フライス加工では、アップカットとダウンカットの違いを理解することが非常に重要です。結論から言うと、これらの違いは加工する材料の仕上がりや加工効率に大きく影響します。アップカット加工は、カッターが材料を持ち上げながら切削する方法であり、ダウンカット加工はカッターが材料を押し付けながら切削する方法です。
アップカット加工の特徴は、切削時に発生する力が材料をテーブルから持ち上げようとするため、固定が不安定になりやすいという点です。しかし、この方法は切りくずを効率良く排出できるため、切削速度を速めることができます。一方、ダウンカット加工は、切削力が材料をテーブルに押し付けるため、より安定した加工が可能となります。これにより、仕上がりの精度が高まるという利点があります。
例として、精密な表面仕上げが求められる場合や薄い材料の加工には、ダウンカット加工が適しています。逆に、速い切削速度での加工を優先する場合や、切りくずの排出が難しい材料を加工する際には、アップカット加工が選ばれることが多いです。
結論として、アップカットとダウンカットの選択は、加工する材料の性質や加工の目的によって変わります。各方法の特徴を理解し、適切な加工法を選択することが、効率的で高品質なフライス加工を実現する鍵となります。
6. 鉄のフライス加工におけるアップカットとダウンカット
6-1. 鉄材料の特性と加工性
フライス加工は、鉄などの材料を加工する際に用いられる重要な技術です。この技術には、「アップカット」と「ダウンカット」という二つの主要な方法がありますが、それぞれが持つ特徴と違いを理解することは、加工品の品質を高める上で非常に重要です。
アップカット加工は、工具が材料を持ち上げるように切削する方法で、切削時に発生する力が材料をテーブルに押し付けるため、加工中の材料の固定が比較的容易です。これにより、加工精度が向上することが一般的です。特に、薄い材料や形状が複雑な部品の加工に適しています。
一方、ダウンカット加工は、工具が材料を押し下げるように切削する方法で、切削時に発生する力が材料をテーブルから離れやすくするため、加工中の材料の固定にはより注意が必要です。しかし、この方法は切削面の仕上がりが非常に滑らかになるという利点があります。したがって、外観が重要な製品や、仕上げ加工にはダウンカット加工が好まれます。
結論として、アップカットとダウンカットの選択は、加工する材料の特性や、求められる製品の品質によって決まります。小さな違いですが、これを理解し適切に選択することで、加工品の品質を大きく向上させることができます。
6-2. 鉄フライス加工における切削条件
フライス加工では、切削の向きが製品の仕上がりに大きく影響します。特に、鉄などの硬い素材を加工する際には、アップカットとダウンカットの違いを理解しておくことが重要です。アップカット加工では、カッターが回転する際に素材からチップを引き上げる形で切削を行います。これにより、比較的クリーンな切断面が得られ、加工精度が向上します。一方、ダウンカット加工の場合は、カッターが素材に押し付ける形でチップを切削し、これが素材を固定しやすくするため、仕上がりが安定します。
例えば、鉄のフライス加工で複雑な形状や細かい仕上がりが求められる場合、アップカット加工を選択すると良いでしょう。しかし、加工面の安定性や素材の固定が難しい場合には、ダウンカット加工が適しています。実際、多くの加工現場では、これらの特徴を理解した上で、加工する製品の要求仕様に合わせて最適な切削方法を選択しています。
結論として、アップカット加工とダウンカット加工は、それぞれにメリットと適用シーンがあります。フライス加工におけるこれらの選択は、加工する素材の種類や求められる製品の品質、仕上がりに大きく依存します。適切な切削方法の選択は、効率的かつ高品質な製品製造への鍵となります。
6-3. 鉄加工におけるアップカットとダウンカットの選択基準
フライス加工におけるアップカットとダウンカットの違いを理解することは、鉄加工の品質と効率を向上させる上で欠かせません。この二つの加工方法は、カッターが材料を切削する方向の違いによって区別されます。アップカットでは、カッターは材料に対して下から上に向かって切削を行い、ダウンカットでは上から下へと切削します。この違いが加工の結果に大きな影響を及ぼします。
アップカットの場合、カッターが材料を持ち上げるように切削するため、切削面がきれいで、特に薄い材料の加工に適しています。しかし、材料が持ち上げられることで工具や材料に負担がかかりやすくなります。一方、ダウンカットはカッターが材料を押し下げる形で切削するため、材料の固定が必要ですが、仕上がりが非常に滑らかになり、特に外観が重要な製品に適しています。
例えば、精密な装飾品や外観に影響が出やすい部品の加工には、ダウンカットが選択されることが多いです。一方で、高速で大量の材料を削り取る必要がある場合には、アップカットが用いられます。
最終的に、アップカットとダウンカットのどちらを選択するかは、加工する製品の種類、必要な精度、仕上がりの質、加工速度など、多くの要因に基づいて判断されます。適切な切削方法を選択することで、鉄加工の品質と効率を大きく向上させることができるのです。
7. アップカットとダウンカットの適用
7-1. 素材と加工精度の関係
フライス加工では、素材の種類や加工方法によって仕上がりに大きな差が生まれます。特に、鉄を加工する際のアップカットとダウンカットの違いは、加工精度に直接影響を及ぼします。アップカットとは、カッターが回転する方向と同じ方向に素材を送る方法で、この方法では削りカスが上に押し出されます。これに対して、ダウンカットはカッターの回転方向とは逆向きに素材を送る方法で、削りカスが素材に押し込まれるため、より滑らかな表面を実現します。
たとえば、鉄をフライス加工する際にダウンカットを使うと、カッターが素材を押さえつけることで、素材の振動を抑え、より高い加工精度を得ることができます。この技術は、精密な部品製造や美しい仕上がりが求められる工芸品などに特に有効です。アップカットでは、特に深い加工を行う場合に削りカスの除去がスムーズになるため、加工速度を上げることが可能ですが、仕上がりの精度はダウンカットに劣ることがあります。
したがって、鉄のフライス加工においては、アップカットとダウンカットを適切に選択することが重要です。仕上がりの美しさと精度を重視する場合はダウンカットを、加工速度を優先する場合にはアップカットが適しています。このように、加工方法の選択によって、最終製品の品質を大きく左右することができるのです。
7-2. 加工速度と仕上がりの質
フライス加工は、金属工作の基本技術の一つであり、特に鉄などの硬質材料を精密加工する際に重宝されます。この加工法の中でも特に重要なのが、アップカットとダウンカットの違いです。簡単にいうと、これらの違いは切削方向にあります。アップカットは素材を持ち上げながら削る方法で、ダウンカットは素材を押し下げながら削る方法です。
アップカット加工は、切削抵抗が少なく、精密な加工が可能ですが、加工中に素材が持ち上がることがあるため、固定が難しい場合があります。一方、ダウンカット加工は、素材をしっかりと固定でき、表面仕上げが綺麗になりやすいですが、切削抵抗が大きくなりがちです。
例えば、薄い板材を加工する際には、ダウンカット方式がよく使用されます。これは、加工中に材料が振動したり、持ち上がったりするのを防ぐためです。一方で、精密な内部形状を加工する場合には、アップカット方式の方が適していることが多いです。
これらの違いを理解することで、加工する材料や目的に応じて最適な方法を選択することができます。フライス加工の違いを理解し、適切な加工方法を選択することは、製品の品質を大きく左右します。
7-3. アップカットとダウンカットの効率比較
フライス加工におけるアップカットとダウンカットの違いを理解することは、加工品質や効率を向上させる上で非常に重要です。アップカット加工とは、工具の回転方向が被加工物を持ち上げる方向になっている加工方法であり、一方、ダウンカット加工は、工具の回転が被加工物を押し下げる方向である加工方法です。この二つの方法は、加工する材料や求める仕上がりによって使い分けられます。
たとえば、アップカット加工は、被加工物から切削屑を効率よく排出できるため、切削抵抗が少なくなり、加工精度を高めることができます。これは、特に粘り気がある材料や、切削屑の詰まりやすい鉄などの加工に適しています。一方、ダウンカット加工は、工具が材料を押し固めながら加工するため、仕上がり面が非常に滑らかになります。これは、仕上げ加工や、見た目にも影響する加工品に適しています。
しかし、ダウンカット加工は切削屑の排出がしにくいため、加工時に切削屑が残りやすくなるというデメリットもあります。そのため、加工条件や材質によっては、アップカットとダウンカットを組み合わせて使用することもあります。
結論として、アップカット加工とダウンカット加工はそれぞれに特性があり、加工品質や効率を最大限に引き出すためには、これらの違いを理解し、適切に選択することが重要です。
8. トラブルシューティングとヒント
8-1. アップカット加工の問題点と対策
フライス加工において、アップカットとダウンカットは加工方法の重要な違いを示しています。この二つの方法は、加工される材料の切削品質や加工速度に大きな影響を及ぼします。具体的には、アップカット加工は切削時に材料を持ち上げる力を生じさせ、これが時に材料の固定不良や仕上がりの精度に影響を与える可能性があります。一方、ダウンカット加工は材料を押し下げる力を生じさせるため、仕上がりが平滑になりやすいという利点があります。しかし、ダウンカット加工は切削抵抗が大きくなるため、工具の摩耗が早まるデメリットも存在します。
例えば、鉄を加工する際、アップカット加工を採用すると、切りくずの排出が良好であるという利点がありますが、仕上がり面に細かい傷が生じやすくなります。これに対して、ダウンカット加工を採用すれば、表面が滑らかに仕上がるものの、切りくずの排出問題に直面することがあります。
結論として、アップカットとダウンカットの選択は加工する材料の性質や仕上がりに求められる品質によって異なります。アップカットは切りくず排出が良い一方で、ダウンカットは仕上がりの平滑さが魅力です。これらの特性を理解し、目的に応じて最適な加工方法を選択することが重要です。
8-2. ダウンカット加工の問題点と対策
フライス加工では、アップカットとダウンカットという二つの方法がありますが、それぞれに特徴と適用する場面が異なります。ダウンカット加工は、加工面の仕上がりを良くするためによく用いられます。しかし、この方法にはいくつかの問題点があり、注意が必要です。
ダウンカット加工の最大の問題点は、加工時に生じる力がワークをテーブルから押し上げるため、ワークが固定されていない場合、精度が低下したり、ワークが動いてしまうリスクがあることです。特に、薄い材料や軽い材料の加工において、この問題は顕著に現れます。
この問題に対処するためには、ワークをしっかりと固定する必要があります。例えば、より強力なクランプを使用する、あるいはワークをテーブルに直接固定する方法などがあります。また、加工パスを工夫して、加工時に加わる力を分散させることも有効な手段です。
ダウンカット加工は、適切な対策を講じれば、より高い仕上がり品質を得ることができます。ワークの固定方法や加工パスを工夫することで、この加工法の問題点を克服し、加工効率と品質を高めることが可能です。それにより、ダウンカット加工のメリットを最大限に活かすことができます。
8-3. 長寿命のカッター選びとメンテナンス
フライス加工におけるアップカットとダウンカットの違いを理解することは、加工品質を向上させる上で非常に重要です。アップカットとは、カッターの回転方向が被削材を持ち上げる方向になっている加工方法で、これは切削時に材料を引き上げ、清潔な切断面を得やすくする効果があります。一方、ダウンカットはカッターの回転が材料を押し下げる方向になっており、これは材料が固定されやすく、特に薄い材料の加工に適しています。
例えば、アップカットは木材やプラスチックの加工において、スムーズな表面仕上げが求められる場合に適しています。しかし、薄い材料や、加工中に材料が動かないように固定するのが難しい場合には、ダウンカットの方がより適切です。特に、鉄などの金属加工においては、ダウンカット方式が多用されることがあります。
このように、アップカットとダウンカットの選択は、加工する材料の性質や加工後の仕上がりに大きく影響します。適切な方法を選ぶことで、加工効率の向上や品質の高い仕上がりが期待できます。フライス加工においてこれらの違いを理解し、適切な加工方法を選択することが、高品質な製品を生み出す鍵となります。
9. 最新技術と将来の展望
9-1. 革新的なフライス加工技術
フライス加工におけるアップカットとダウンカットの違いを理解することは、加工の品質を向上させる上で非常に重要です。アップカット加工では、カッターが回転する方向と同じ方向に材料を送ります。これにより、切削時に材料が持ち上がることを防ぎ、きれいな仕上がりを実現します。一方、ダウンカット加工では、カッターの回転方向と反対に材料を送るため、切りくずが材料に押し込まれ、より滑らかな表面を得ることが可能です。
たとえば、鉄のフライス加工を行う場合、精度が求められる仕上げ工程ではダウンカット加工が好まれます。これは、ダウンカットの方が切りくずが材料の表面を傷つけにくく、仕上がりが滑らかになるからです。アップカット加工は、大きな切りくずを排出する必要がある荒加工に適しています。
結論として、フライス加工におけるアップカットとダウンカットの選択は、加工する材料の種類や仕上がりに求められる品質によって異なります。適切な方法を選択することで、加工の効率を上げ、求められる品質を実現することが可能です。
9-2. 環境に優しい加工方法
フライス加工において、アップカットとダウンカットの違いは重要な知識の一つであり、加工の品質や効率を大きく左右します。アップカット加工では、工具の回転方向が材料を持ち上げる方向になります。これにより、切削時に材料がクリアされやすくなり、加工面の仕上がりが良くなるという利点があります。一方、ダウンカット加工では、工具の回転が材料を押し付ける方向であり、加工中に材料が安定しやすく、特に薄い材料の加工に適しています。
例えば、鉄などの硬い材料を加工する場合、アップカットを使うと、切削時の材料の持ち上げにより、仕上がりの精度が高まります。しかし、薄い鉄板を加工する際は、ダウンカットが適しており、材料が振動することなく、安定した加工が可能になります。
結論として、フライス加工におけるアップカットとダウンカットの選択は、加工する材料の種類や加工後の仕上がりに大きく影響します。適切な方法を選択することで、効率的かつ高品質な加工が可能になります。
9-3. フライス加工の未来動向
フライス加工は、金属製品の製造に不可欠な工程の一つですが、特に鉄を加工する際には「アップカット」と「ダウンカット」という二つの異なる方法があります。これらの違いを理解することは、加工の品質を向上させる上で非常に重要です。
まず、アップカット加工は、切削工具が回転する際に、材料を持ち上げるようにして切削する方法です。この方式では、切れ味が良く、加工面の仕上がりが非常に綺麗になります。特に、薄い材料や柔らかい材料の加工に適しています。
一方、ダウンカット加工は、切削工具が材料を押し下げながら切削する方法です。この方式は、材料を固定する力が強くなるため、厚い材料や硬い材料の加工に適しています。加工中の材料の動きが少なく、精度が要求される作業に最適です。
例えば、鉄のような硬い材料を加工する場合、ダウンカット加工は材料のずれを最小限に抑えつつ、精度の高い加工を実現します。しかし、複雑な形状や細かい加工を行う場合は、アップカット加工の方が向いている場合もあります。
結論として、フライス加工におけるアップカットとダウンカットの選択は、加工する材料の種類や求められる加工品質によって異なります。適切な方法を選択することで、効率的かつ高品質な製品製造が可能となります。
まとめ
フライス加工において、アップカットとダウンカットは重要な要素です。アップカットは切削時にチップが削られる方向と同じ向きに回転することで、切削抵抗を減らし、熱や振動を抑制します。一方、ダウンカットは逆向きに回転し、表面の仕上がりを向上させる効果があります。
鉄のフライス加工においては、適切な切削方法を選択することが重要です。アップカットとダウンカットの違いを理解し、それぞれの利点を活かして加工を行うことで、工程効率や加工精度の向上が期待できます。
鉄を使ったフライス加工:品質を左右する精度向上のポイント
鉄を使ったフライス加工は、製品の品質に大きな影響を与えます。精度向上は、製品の耐久性や性能を決定する重要な要素の一つです。本記事では、鉄を素材としたフライス加工に焦点を当て、精度向上のポイントについて詳しく解説します。どのようにして鉄を使用し、どのようにして精度を向上させるか。それらの疑問にお答えすることで、フライス加工の世界に一歩踏み出す皆様のお手伝いを致します。製品の品質向上に向けて重要な情報が満載ですので、ぜひご一読ください。
1. 切削加工の加工精度とは
1-1. 加工精度の基本概念
鉄を使ったフライス加工において、製品の品質を左右する最も重要な要素は加工精度です。加工精度が高ければ高いほど、製品の品質も向上します。これは、加工された鉄部品が最終的な製品に組み込まれる際、その精度が直接的に機能性や耐久性に影響を及ぼすためです。例えば、自動車や電化製品の部品では、微細ながらも高い精度が求められます。これらの部品が正確な寸法で加工されていなければ、組み立て時に問題が生じ、最悪の場合、製品の性能に重大な影響を与える可能性があります。
加工精度を高めるためには、適切な工具の選定、加工条件の最適化、そして定期的な機械のメンテナンスが不可欠です。特に、鉄のフライス加工においては、切削工具の摩耗が早く進むため、常に最適な切削条件を保つことが重要です。また、高度な技術を持つオペレーターによる精密な加工も、精度向上のカギを握ります。
結論として、鉄を使ったフライス加工における加工精度の向上は、適切な工具の選定、加工条件の管理、機械のメンテナンス、そして熟練したオペレーターによる操作が重要です。これらの要点を抑えることで、製品の品質を大きく向上させることが可能になります。
1-2. 加工精度を左右する7つの条件
鉄を使ったフライス加工において、品質を左右する最も重要な要素は加工精度です。この精度を向上させることで、製品の性能や耐久性が大きく改善されます。具体的には、切削工具の状態、加工機械の精度、操作者の技術などが加工精度に影響を及ぼします。例えば、切削工具が適切にメンテナンスされていないと、不均一な加工面や加工誤差が発生しやすくなります。また、加工機械自体の精度が低いと、製品の寸法精度や形状精度が維持できません。さらに、操作者の技術によっても大きな差が生じるため、熟練した技術者による正確な加工が求められます。これらの要素を適切に管理し、改善することが、フライス加工における品質の向上には不可欠です。結論として、鉄を使ったフライス加工の品質を左右する加工精度を向上させるには、切削工具、加工機械、操作者の技術の3点に注目し、それぞれの管理と改善を行うことが重要であると言えます。
1-3. 鉄のフライス加工における精度の重要性
鉄のフライス加工において、品質を大きく左右するのは「精度」です。精度が高ければ高いほど、製品の品質も向上し、その逆もまた真なります。では、なぜ精度がこれほどまでに重要なのでしょうか?
まず、鉄のフライス加工における精度とは、加工された部品が設計図通りの寸法や形状をしているか、ということに他なりません。精度が高い加工を実現するためには、機械の性能の維持向上や、加工環境の管理、オペレーターの技術など、多くの要素が関連しています。
例えば、ある部品をフライス加工で製造した場合、その寸法が微妙に異なるだけで、組み立てられる製品全体の品質に影響を及ぼすことがあります。特に、精密機械や自動車などの分野では、寸法の誤差が許されない部品が多く、高い精度が求められます。そのため、精度を向上させることは、製品の信頼性や耐久性を高めることに直接繋がります。
このような理由から、鉄のフライス加工における精度は非常に重要であり、精度を上げることが品質向上の鍵となります。最終的には、高い精度の実現が製品の品質を大きく左右し、消費者からの信頼を獲得しやすくするため、製造業者にとって重要なポイントとなるのです。
2. 切削加工におけるビビりとその対策
2-1. ビビりとは
鉄を使ったフライス加工では、製品の品質を左右する重要な要素として、精度が挙げられます。精度の向上は、製品の性能や耐久性に直接関係しており、これを高めるポイントを理解することが重要です。特に、鉄のような硬い素材を使用する場合、加工における細かな誤差も製品の品質に大きな影響を及ぼすため、加工技術の向上と正確な機械の調整が必要となります。
例えば、フライス加工機の定期的なメンテナンスと精密な調整を行うことで、加工時の振動を抑え、より高い精度を実現することができます。また、鉄加工専用の高品質なカッターやエンドミルを選択することも、精度向上に寄与します。これらの工具は、鉄を加工する際の摩耗や熱に強く、加工面の滑らかさや寸法の正確さを保つことが可能です。
日本においてフライス加工は、自動車や電子機器など、多岐にわたる産業で重要な役割を果たしています。精度の高い加工が求められるこれらの分野では、上記のような精度向上のポイントを押さえることが、製品品質の向上に直結します。
結論として、鉄を使ったフライス加工における品質を左右する精度の向上は、適切な機械の調整、適切な工具の選択、並びに定期的なメンテナンスによって実現できます。これらのポイントに注意を払うことで、高品質な製品製造が可能となり、さまざまな産業においてその価値を高めることができます。
2-2. ビビりの発生原因
品質の高い鉄を使ったフライス加工は、多くの製造業で重要な工程の一つです。その中でも特に、加工の精度は製品の品質を左右する重要な要素です。高い精度を確保することで、部品の寸法精度や形状精度が向上し、結果的に製品全体の品質が向上します。
精度向上のためには、フライス加工機の定期的なメンテナンスが不可欠です。これには、切削工具の状態のチェックや、フライス盤のキャリブレーションが含まれます。例として、日本のある自動車部品メーカーでは、フライス加工機の定期的なメンテナンスにより、加工精度の向上だけでなく、加工中の振動や音の低減にも成功しました。これにより、製品の品質向上と同時に、作業環境も改善され、製造効率の向上にも寄与しました。
また、加工条件の最適化も精度向上には欠かせません。切削速度、送り速度、切削深さなどの条件を製品の材質や形状に合わせて最適化することで、より高い精度の加工が可能になります。さらに、最新技術の導入、例えば、AIを活用した加工条件の自動調整機能も精度向上に寄与しています。
結論として、鉄を使ったフライス加工の品質を左右する精度向上には、機械の定期的なメンテナンスと加工条件の最適化が重要です。これらを徹底することで、製品全体の品質向上を図ることができます。加えて、最新技術の活用が、さらなる精度向上の可能性を広げています。
2-3. ビビりを防ぐための対策
精確なフライス加工は、製品の品質を大きく左右します。特に、鉄を用いた加工では、その硬さと耐久性から精度の維持が重要となります。この精度を向上させるためには、加工機械の定期的なメンテナンスや、適切な切削工具の選択が不可欠です。例えば、加工中の振動を最小限に抑えるために、高品質な切削工具を選ぶことが挙げられます。また、正確なフライス加工を行うためには、工具の摩耗を定期的にチェックし、必要に応じて交換することが重要です。このように、適切な機械の管理と工具の選択によって、鉄を用いたフライス加工の精度は大きく向上します。結論として、高い品質を保つためには、機械と工具の適切な管理が欠かせないということです。
3. 切削加工による変形への注意
3-1. 加工中の変形とその影響
鉄を使ったフライス加工では、加工の精度が最終製品の品質に大きく影響を及ぼします。精度を向上させることは、製品の品質を左右する重要なポイントです。その理由は、フライス加工によって生じる部品の寸法誤差や表面の仕上がりが、製品の機能性や耐久性に直接的な影響を与えるからです。例えば、精密な機械部品では、微細な寸法のずれも機械全体の性能低下を招く可能性があります。また、鉄などの材料を使用する場合、材料の硬さによってフライス加工の難易度が変わり、精度を保つための工夫が必要になります。具体的には、適切なカッターや切削条件の選定、工具の摩耗に注意しながらの加工などが挙げられます。これらの対策を講じることで、フライス加工の精度は大きく向上します。結論として、鉄を用いたフライス加工において精度を高めることは、製品の品質を保証する上で不可欠です。そのためには、材料の特性を理解し、適切な加工技術を選択・適用することが重要となります。
3-2. 変形を抑制するための工夫
フライス加工において、鉄という材料を扱う際、その精度は製品の品質を大きく左右します。この精度を向上させるためには、加工中の変形を抑制する工夫が必要です。特に、鉄は加工熱による伸縮や、加工力による変形が起こりやすい特性を持っています。そのため、温度管理や適切な切削条件の設定が、精度向上の鍵を握ります。
例えば、加工前の鉄材を適切な温度まで予熱することで、材料の伸縮を抑え、加工中の変形を最小限に抑えることができます。また、切削速度や送り速度など、加工条件を細かく調整することで、鉄材にかかる負荷を適切に管理し、精度を高めることが可能です。
日本においてフライス加工は、多くの製造業で必要とされる技術であり、こうした工夫を行うことで、より高品質な製品を生産することが期待されます。つまり、変形を抑制するための工夫は、フライス加工における鉄の精度向上に不可欠であり、結果として製品全体の品質向上に繋がるのです。
4. 旋盤加工とフライス加工の精度
4-1. 旋盤加工における精度
鉄を使ったフライス加工では、製品の品質を大きく左右するのが加工精度です。この精度を向上させることが、高品質の製品を生み出す鍵となります。精度を高めるためには、工具の選定、加工条件の最適化、そして機械のメンテナンスが欠かせません。
例えば、鉄を加工する際には、硬度や摩耗に強い工具を選ぶことが重要です。適切な工具を選ぶことで、加工時の精度が大きく改善されます。また、切削速度や送り速度などの加工条件を最適化することで、加工精度を保ちながら効率良く作業を進めることが可能です。さらに、機械の定期的なメンテナンスを行い、常に最良の状態で加工を行うことが重要です。これらの工夫により、高い加工精度を維持することができます。
日本においても、フライス加工の精度向上に向けた技術の進化が続いています。特に、精密な部品を必要とする自動車産業や電子機器産業では、加工精度が製品品質に直結するため、常に高いレベルが求められています。
結論として、鉄を使ったフライス加工で高品質な製品を生み出すには、加工精度の向上が不可欠です。適切な工具の選定、加工条件の最適化、機械の定期的なメンテナンスにより、この精度を実現することが可能です。これらの取り組みにより、技術の進化を支え、製品品質の更なる向上に繋がるでしょう。
4-2. フライス加工の精度向上のためのポイント
鉄を使ったフライス加工では、製品の品質を決定づける要素として精度が非常に重要です。精度を向上させることは、製品の性能向上に直結するため、加工技術の向上が求められています。この精度を高めるためのポイントにはいくつかありますが、特に重要なのが、適切な工具の選定、加工条件の最適化、そして定期的なメンテナンスです。
適切な工具の選定では、加工する鉄の種類に応じて、最も適した切削工具を選ぶことが重要です。例えば、硬い材料を加工する際には、耐摩耗性に優れた工具を選ぶことで、精度の高い加工が可能になります。また、加工条件の最適化としては、切削速度や送り速度、切り込み量を材料の特性に応じて調整することで、加工時の振動を抑え、精度向上が期待できます。
定期的なメンテナンスも欠かせません。加工機械の定期的な点検や、工具の摩耗状態のチェックを行うことで、常に最適な状態で加工を行うことができ、結果として精度が保たれます。
こうしたポイントを抑えることで、鉄を使ったフライス加工の精度は大幅に向上し、製品の品質向上に直結します。精度の高い加工技術は、製品の競争力を高める上で不可欠であり、その重要性は今後も高まっていくことでしょう。
5. 切削条件の設定と決定方法
5-1. 切削条件とその役割
鉄を使ったフライス加工では、製品の品質を大きく左右するものとして、加工の精度が挙げられます。精度を高めることは、仕上がりの美しさだけでなく、機能性の向上にも直結します。そのためには、適切な切削条件の選定が非常に重要です。
切削条件とは、フライス加工における切削速度、送り速度、切り込み量など、加工時の各種設定を指します。これらの条件を最適化することで、加工時のバリの発生を抑え、表面の滑らかさを向上させることができます。例えば、鉄のフライス加工においては、硬い素材であるために、適切な切削速度の設定が特に重要です。速すぎると工具の摩耗が激しくなり、遅すぎると加工時間が不必要に長くなります。
日本では、特に精密な部品製造において、フライス加工の精度が重視されます。自動車や電子機器の部品など、微細な寸法公差を要求される製品は数多く存在し、これらの要求を満たすためには、切削条件の適正化が欠かせません。
結論として、鉄を使ったフライス加工において品質を左右する精度を向上させる鍵は、切削条件の適切な選定にあります。適正な条件で加工することで、バリの発生を抑え、製品の品質を高めることが可能です。このような工夫を行うことで、高品質な製品を効率良く生産することができるのです。
5-2. 理想的な切削条件の決め方
フライス加工における品質の向上は、主に精度の高さによって左右されます。精度の向上は、鉄などの材料を使用する際に特に重要です。この精度を高めるためには、理想的な切削条件の選定が不可欠です。具体的には、適切な切削速度、送り速度、および切削深さの組み合わせが求められます。例えば、鉄をフライス加工する際には、硬さや加工する形状に応じて、これらの条件を細かく調整する必要があります。
特に、適切な切削速度の選定は、加工面の仕上がりに大きな影響を与えます。速すぎる速度では材料が燃えやすく、遅すぎる速度では加工時間が過剰にかかり、経済性が低下します。また、送り速度や切削深さも、加工する材料の性質によって最適化することが、高精度な仕上がりを実現する鍵となります。
日本においてフライス加工は精密部品製造など、多くの工業製品の生産において重要な役割を果たしています。例えば、自動車産業や電子機器の部品製造において、高い精度が求められる部分の加工には、このような技術が不可欠です。
したがって、理想的な切削条件を見極め、適切に適用することは、鉄をはじめとする材料を使用したフライス加工において、品質の向上を左右する決定的なポイントです。これにより、製品の品質向上はもちろん、生産効率の改善にも繋がります。
5-3. 鉄を使ったフライス加工における切削条件の最適化
鉄を使ったフライス加工において、製品の品質を左右する最も重要な要素の一つが精度です。精度を高めることは、製品の性能向上とコスト削減に直結します。そのため、切削条件の最適化が非常に重要となります。例えば、切削速度、送り速度、切削深さといった切削条件を適切に設定することで、加工時の振動を抑え、仕上がりの精度を向上させることが可能です。特に、鉄は硬度が高い材料なので、適切な切削条件の選定が不可欠です。日本では、鉄を使ったフライス加工技術が高く評価されており、自動車や電機製品の部品製造において、高い精度が求められています。具体的な例として、自動車のエンジン部品では、マイクロメートル単位での精度が要求されるため、切削条件の最適化が極めて重要です。結論として、鉄を使ったフライス加工において、精度向上のためには切削条件の適切な設定が欠かせません。これにより、高品質な製品を効率的に生産することが可能となり、製造業の競争力をさらに高めることができます。
6. 鉄フライス加工の精度向上のための実践的アプローチ
6-1. 適切な工具選定の重要性
鉄を使ったフライス加工において、品質を左右する重要なポイントは精度の向上にあります。精度を高めることで、製品の品質を向上させることが可能となり、結果的に顧客満足度の向上に繋がります。そのためには、適切な工具選定が非常に重要です。
使用する工具の種類によって加工の精度は大きく変わります。たとえば、鉄加工専用に設計されたフライスカッターを使用することで、硬い材料でも高い精度で加工を実現することができます。また、切削速度や送り速度などの加工条件を適切に設定することも、精度向上には欠かせません。
具体的な例として、日本のある部品製造企業では、鉄製の部品を高精度で加工するために、特殊なコーティングが施されたフライスカッターを導入しました。その結果、従来に比べて加工誤差が大幅に減少し、製品の品質が向上したという報告があります。
このように、鉄を使ったフライス加工における品質を左右する重要なポイントとして、適切な工具選定と加工条件の最適化が挙げられます。これらを徹底することで、高い精度と品質の製品を提供することが可能になります。
6-2. 機械のメンテナンスと精度維持
鉄を使ったフライス加工では、精度が最終製品の品質を大きく左右します。高い精度を保つことは、部品の寸法や形状が設計通りに仕上がることを意味し、それによって製品全体の性能や信頼性が向上します。このため、加工精度の向上は非常に重要なポイントとなります。
精度向上のためには、機械のメンテナンスが欠かせません。例えば、フライス盤の定期的な点検や調整を行うことで、機械の摩耗による精度の低下を防ぐことができます。また、切削工具の選択や交換のタイミングも精度に影響します。切れ味が落ちた工具を使用し続けると、加工面にバリが出たり仕上がり精度が落ちたりするため、適切な管理が必要です。
特に、日本のフライス加工では、細部にわたる高い精度を求められることが多く、そのためには上記のようなメンテナンスや工具管理が不可欠です。例えば、自動車部品や精密機器の製造では、数ミクロン単位の誤差も許されないため、高精度加工が求められます。
結論として、鉄を使ったフライス加工における品質を左右する重要なポイントは、機械のメンテナンスと精度維持です。これらを徹底することで、設計通りの高品質な製品を生産することが可能になります。
6-3. 加工プロセスの監視と品質管理
精度向上は鉄を使ったフライス加工において品質を左右する重要なポイントです。フライス加工の際、鉄の性質と加工機械の精度が最終製品の品質に大きく影響を及ぼします。日本での製造業では、この点に特に注意が払われています。たとえば、自動車産業や家電製品の部品製造において、ほんのわずかな誤差も許されないため、加工プロセスの監視と品質管理が極めて重要になります。
具体的な例として、高精度を要求される自動車のエンジン部品では、フライス加工により数ミクロン単位の誤差管理が求められます。これを実現するためには、加工機械の定期的な校正とメンテナンスが不可欠です。また、温度や湿度などの環境条件も製品の精度に影響を与えるため、適切な環境下での加工が求められます。
このように精度を保つためには、加工機械の性能維持だけでなく、加工環境の管理も重要です。日本では、これらの要素を厳しく管理することにより、高い品質の製品製造が可能になっています。結論として、鉄を使ったフライス加工における精度向上は、加工機械のメンテナンスと加工環境の管理を徹底することにより、製品の品質を大きく向上させることができます。
まとめ
鉄を使用したフライス加工では、精度向上が重要です。素材の硬さや熱伝導率によって工具の選択や切削速度を調整する必要があります。また、加工中の振動や加熱を避けるために、冷却剤や適切な工具の選定が重要です。加工精度を左右するポイントを押さえ、高品質な加工を実現しましょう。
CNCフライスで重要!アップカットとダウンカットの切削条件の違いとは?
CNCフライス加工は、産業界において非常に重要な役割を果たしています。特に、鉄などの硬材料を加工する際には、切削条件を適切に設定することが欠かせません。そこで、アップカットとダウンカットという2つの切削方法が登場します。これらの違いを正しく理解することは、高品質な加工を実現するために不可欠な要素となります。本記事では、CNCフライスでのアップカットとダウンカットの切削条件の違いについて掘り下げ、その重要性や実践的な利点について詳しく解説していきます。加工技術における次のステップに進むために、ぜひこの情報を活用してみてください。
1. アップカットとダウンカットの基本
1-1. アップカット加工の概要
CNCフライス加工において、鉄をはじめとする素材の加工にアップカットとダウンカットという二つの切削方法があります。これらの方法は、加工の品質と効率に大きな影響を与えます。アップカットとダウンカットの主な違いを理解することは、加工プロセスを最適化するために重要です。
アップカット加工では、切削工具が回転する際に素材から切り屑を上に引き抜くように加工します。この方法の利点は、切り屑が作業エリアから効率的に排出されるため、切削部がクリアに保たれやすくなることです。例えば、薄い鉄板の加工において、アップカット加工は素材が振動するのを防ぎ、より精密な加工を可能にします。
一方、ダウンカット加工では、切削工具が素材に押し付ける形で加工を行います。この方法の利点は、素材の表面が滑らかに仕上がる傾向があることです。特に、鉄などの硬い素材を加工する際に、ダウンカット加工は優れた仕上がりを実現します。
結論として、アップカットとダウンカット加工はそれぞれにメリットがあり、加工する素材や目的に応じて適切な方法を選択することが重要です。アップカットは切り屑の排出が良く、ダウンカットは仕上がりの滑らかさが特徴です。この二つの切削条件の違いを理解し、適用することで、CNCフライス加工の品質と効率を高めることができます。
1-2. ダウンカット加工の概要
CNCフライス加工において、アップカットとダウンカットは鉄加工の際に重要な切削条件の違いを持っています。アップカット加工では、カッターが材料の下から上へと切り込むことで、チップが上方向に排出されます。これに対し、ダウンカット加工では、カッターが上から下へと材料を切削し、チップが材料に押し込まれる形で排出されます。この基本的な違いにより、加工品質や作業効率に影響を及ぼします。
例えば、アップカット加工は、材料の表面を滑らかに仕上げるのに適しており、特に複雑な形状や細部の加工に優れています。一方で、ダウンカット加工は、材料の裂けや欠けを抑える効果があり、比較的厚手の材料の加工や直線的な加工に適しています。
結論として、アップカットとダウンカットのどちらを選択するかは、加工する鉄の材料の種類、目的の仕上がり、加工の複雑さなど、プロジェクトの特性によって決まります。適切な切削条件の選択により、高品質な加工結果を得ることができます。
1-3. 鉄フライス加工における両者の特徴
CNCフライス加工において、アップカットとダウンカットは加工品質を左右する重要な切削条件です。この二つの方法は、加工時の鉄の挙動を異ならせ、それぞれ独特の利点を持ちます。アップカット加工では、カッターが材料を持ち上げながら切削するため、切り屑が排出しやすくなり、清潔な加工面を得やすいです。一方で、ダウンカット加工はカッターが材料を押しつけながら切削することで、材料の押し出しを防ぎ、より滑らかな加工面を実現します。例えば、細かい仕上がりを要求される精密部品の加工にはダウンカットが適しています。しかし、切り屑の排出が難しくなるため、加工中の材料の熱が上がりやすくなる点には注意が必要です。結論として、アップカットとダウンカットの選択は、加工する鉄製品の用途や要求される加工品質に応じて慎重に行うべきです。この理解を深めることで、より効率的で高品質のフライス加工を実現することができるでしょう。
2. アップカットとダウンカットの違い
2-1. 切削方向の基本的な違い
CNCフライス加工におけるアップカットとダウンカットの違いは、精密な加工において非常に重要です。これらの切削方法は、鉄をはじめとする材料の加工品質や効率に大きく影響します。アップカット加工では、カッターが回転する方向と同じ方向に材料を送るため、材料を持ち上げる力が発生します。この方法は、特に粗加工時に適しており、切削スピードを高めることができますが、仕上がり面にバリが出やすいというデメリットがあります。一方、ダウンカット加工では、カッターの回転方向と逆に材料を送るため、材料を押し下げる力が働きます。これにより、仕上がりの面質が向上し、きれいな加工面を実現できますが、反面、切削抵抗が大きくなるため、加工効率がやや低下する可能性があります。
例えば、鉄の精密な部品を製作する場合、最終的な仕上がりを重視するならダウンカット加工が選ばれることが多いです。しかし、大量に素早く加工する必要がある場合は、アップカット加工が採用されることもあります。両者を適切に使い分けることで、加工の効率と品質を最適なバランスで保つことができます。
まとめると、アップカットとダウンカットのどちらを選択するかは、加工する材料の種類や目的によって異なります。両者の特徴を理解し、適切に使い分けることで、高品質で効率的なCNCフライス加工を実現することが可能です。
2-2. 切削条件の違いとその影響
CNCフライス加工では、アップカットとダウンカットという二つの切削方法が重要です。この二つの方法は、加工される素材の仕上がりや効率に大きな影響を与えます。具体的には、アップカットは刃が材料の下から上に向かって材料を削り取る方法で、ダウンカットはその逆で上から下に向かって材料を削り取ります。
アップカット加工は、切削時に生成される力が材料を持ち上げるため、特に鉄のような硬い材料の切削に適しています。この方法では、材料が固定されているため、加工面が安定しており、精度の高い加工が可能です。例えば、複雑な形状や細かい部品の加工において、アップカットは優れた仕上がりを実現します。
一方で、ダウンカット加工は、刃が材料に押し付けられるため、材料の割れや欠けが少なく、表面仕上げが非常に滑らかになります。これは、特に木材加工やデリケートな材料において顕著ですが、鉄のフライス加工においても、表面の仕上がりを重視する場合に選択されます。
結論として、アップカット加工とダウンカット加工はそれぞれに適した用途があり、選択することで加工品の品質を大きく左右します。特に鉄のフライス加工では、加工する部品の用途や仕上がりに求められる品質に応じて最適な方法を選択することが重要です。
2-3. 適用する材料と形状の違い
CNCフライス加工で重要なのが、アップカットとダウンカットの切削条件の違いを理解することです。これらの違いを理解することで、加工の質を向上させることが可能になります。アップカットは、工具が材料を持ち上げるように切削する方法で、特に鉄などの硬い材料の加工に適しています。これに対してダウンカットは、工具が材料を押し下げるように切削する方法で、仕上がりの面の品質を高めたい場合に有効です。たとえば、アップカット加工では、鉄の板を加工する際に発生するバリを最小限に抑えることができます。一方、ダウンカット加工は、表面の滑らかさを重視する木材加工などにおいて、優れた仕上がりを実現します。結論として、CNCフライス加工におけるアップカットとダウンカットの選択は、加工する材料の種類や求められる仕上がりの品質によって決まるべきです。この理解を深めることが、加工技術の向上へと繋がります。
3. フライス盤でのアップカットとダウンカットの使い分け
3-1. アップカットの適切な使用状況
CNCフライス加工におけるアップカットとダウンカットの違いを理解することは、加工品質の向上に欠かせません。アップカット加工は、切削工具が材料を持ち上げるように削り取る方法です。この方式は、特に粗加工時において、素早く大量の材料を除去するのに適しています。一方、ダウンカット加工では、切削工具が材料を押し付けながら削るため、仕上げ加工に適しており、より滑らかな表面が得られます。
例えば、鉄などの硬い材料を加工する際、アップカットを用いれば、効率的に材料を除去できる一方で、ダウンカットは最終的な表面の仕上げに役立ちます。実際に、鉄のフライス加工では、これらの方法を適切に使い分けることが、製品品質の向上に直結します。
結論として、CNCフライス加工におけるアップカットとダウンカットの適切な使用は、材料や加工内容によって異なります。アップカットは粗加工や大量の材料除去に、ダウンカットは仕上げ加工や滑らかな表面仕上げに適しています。これらの切削条件の違いを理解し、適切に適用することで、加工品質の向上が期待できます。
3-2. ダウンカットの適切な使用状況
CNCフライス加工において、アップカットとダウンカットはそれぞれ異なる切削条件を持ち、適切に使用することで加工の品質や効率を大きく向上させることができます。この二つの切削方法の違いを理解することは、鉄をはじめとするフライス加工において非常に重要です。
アップカット加工では、カッターが回転する方向と同じ方向に材料を送ります。この方法の最大の利点は、チップの排出がスムーズに行われることです。これにより、特に深い溝の加工や長時間の加工において、切削部の温度上昇を抑制しやすくなります。しかし、材料の引っかきやすさが強まるため、加工面に残る仕上げ面の質が低下する可能性があります。
一方で、ダウンカット加工では、カッターの回転方向と反対の方向に材料を送ります。この方法の利点は、加工面の仕上がりが非常に良くなることです。材料を下から押さえつける形で切削するため、表面のなめらかさを良くし、高い仕上がり品質を得ることが可能です。しかしながら、チップの排出がしにくくなるため、切削部の温度上昇やチップの詰まりが発生しやすくなります。
結論として、アップカットとダウンカットのどちらを選択するかは、求める加工品質や材料の性質、加工条件によって異なります。アップカットはチップの排出がよく、長時間の加工や深い溝の加工に適していますが、仕上がりの精度はやや劣ります。一方、ダウンカットは加工面の仕上がりが非常に良くなりますが、チップの管理に注意が必要です。適切な切削方法の選択により、効率的かつ高品質なフライス加工を実現することができます。
3-3. 作業の安全性と品質への影響
CNCフライス加工では、アップカットとダウンカットという二つの切削方法がありますが、これらの違いを理解することは非常に重要です。これらの切削条件は、加工される材料の品質や作業の安全性に大きく影響します。それでは、具体的な違いとそれがなぜ重要なのかを見ていきましょう。
まず、アップカット加工では、カッターが回転する向きと材料を送る向きが同じです。この方法は、特に鉄などの硬い材料の加工に適しており、切りくずを効率的に排出することができます。一方で、ダウンカット加工では、カッターの回転方向と材料の送り方向が逆になります。これにより、より滑らかな表面仕上げを実現することができ、特に見た目が重要な製品の加工に適しています。
例えば、鉄製の部品を作る場合、アップカット加工を選択することで硬い材料でもスムーズに切削でき、作業効率が向上します。また、製品の表面仕上げが重要な場合は、ダウンカット加工が推奨されます。これは、ダウンカット加工の方が滑らかな仕上がりを実現できるためです。
このように、アップカットとダウンカットの切削条件を適切に選択することは、加工品の品質を高め、また作業の安全性を確保する上で非常に重要です。それぞれの特徴を理解し、加工する材料や求められる製品の品質に応じて最適な方法を選択することが、効率的かつ安全な加工作業を行うための鍵となります。
4. フライス加工の切削条件とその調整
4-1. 切削速度と送り速度の設定
CNCフライス加工において、切削条件を選択する際、アップカットとダウンカットは重要な要素です。この二つの手法の違いを理解することで、より品質の高い加工が可能になります。アップカット加工は、工具が回転する方向と反対に素材を削る方法で、主に粗加工に適しています。一方、ダウンカット加工は、工具の回転方向と同じ方向で素材を削り取り、仕上げ加工に適しているとされています。鉄などの硬い素材をフライス加工する場合、アップカットでは強力な切削力が得られるため、素材を素早く大量に削り取ることができます。しかし、ダウンカットを用いると、切削時の振動が少なく、より滑らかな表面仕上げが実現できます。例えば、精密な部品加工や美しい表面仕上げが求められる場合にダウンカット加工が選ばれることが多いです。結論として、アップカットとダウンカットの選択は加工する素材の種類や求められる仕上がりによって異なり、適切な切削条件を選択することが重要です。
4-2. 切削深さと切り込み幅の選択
CNCフライス加工において、鉄などの材料を加工する際に重要なのが、アップカットとダウンカットの選択です。これら二つの切削条件には大きな違いがあり、適切に選択することが加工品質の向上に直結します。
アップカット加工では、カッターが材料を持ち上げながら切削を行います。この方法の利点は、加工時の切り屑が効率よく排出されることです。これにより、切削部の清潔さが保たれ、加工品の仕上がりが向上します。例えば、薄い材料の加工や、精密を要する部品の加工に適しています。
一方、ダウンカット加工は、カッターが材料を押し付けながら切削を行います。この方法の利点は、加工面が非常に滑らかに仕上がる点です。特に、表面仕上げが重要な製品や、材料が割れやすい場合に適しています。しかし、切り屑の排出がアップカット加工に比べて劣るため、切削条件の管理が重要になります。
結論として、アップカットとダウンカットのどちらを選ぶかは、加工する材料の特性や、求められる仕上がりによって異なります。適切な切削条件を選択することで、CNCフライス加工の効率と品質を大幅に向上させることができます。
4-3. ツールの選択とその特性
CNCフライス加工において、アップカットとダウンカットはそれぞれ異なる切削条件を持つため重要です。アップカット加工は、刃が材料の下から上へと切り込む方法で、主に鉄などの硬い材料の加工に適しています。これは、切削時に発生する力が材料をテーブルに押し付けるため、加工中の材料の動きが少なくなるためです。例えば、精密な部品を製造する際には、この特性が非常に有効です。
一方、ダウンカット加工は、刃が材料の上から下へと切り込む方法で、これは主に薄いまたは柔らかい材料の加工に適しています。ダウンカット加工の場合、切削力が材料をテーブルに引き込む作用を持つため、材料が持ち上がりにくく、加工表面の仕上がりが良くなります。たとえば、木材やプラスチックの加工においては、ダウンカット加工が好まれます。
結論として、CNCフライス加工におけるアップカットとダウンカットの選択は、加工する材料の種類や求められる加工品質によって異なります。硬い材料や精密な加工が必要な場合はアップカットを、薄い材料や良好な表面仕上げを求める場合はダウンカットを選択することが重要です。このように適切な切削条件を選ぶことで、効率的かつ高品質な加工が実現します。
5. 工作機械におけるアップカットとダウンカットのメリット
5-1. アップカットのメリットと効率的な加工
フライス加工において、アップカットとダウンカットはそれぞれ重要な役割を担っています。これらの切削方法の違いを理解することは、鉄をはじめとした材料の加工において効率的かつ精密な成果を得るために不可欠です。アップカット加工では、カッターが材料に入るときに材料を持ち上げるように切削が行われます。これにより、特に薄い材料の加工時における切削面の仕上がりが良くなります。一方、ダウンカット加工はカッターが材料を押し下げるように切削を行うため、材料が固定されやすく、特に厚みがある材料の加工で安定した仕上がりを期待できます。
たとえば、アップカット加工は、鉄などの硬い材料を加工する際に、精度の高い仕上がりが要求される細かな部品製作に適しています。対照的に、ダウンカット加工は、鉄板のような比較的厚みのある材料を加工する際に、材料のずれを防ぎながら滑らかな表面を実現するのに有効です。
これらの加工法を適切に選択し、利用することで、材料の特性に応じた最適な加工結果を得ることができます。結論として、フライス加工におけるアップカットとダウンカットは、それぞれ異なる状況での材料加工において重要な役割を果たします。適切な切削条件を理解し、選択することが、高品質な製品製作の鍵となるのです。
5-2. ダウンカットのメリットと滑らかな仕上がり
CNCフライス加工において、アップカットとダウンカットは、それぞれ異なる切削条件を持ち、加工する材料や目的によって選択することが重要です。アップカット加工は、刃が材料の下から上へ向かって切り込む方法で、特に鉄などの硬い材料を加工する際に適しています。これは、切り屑を効率よく排出できるため、切削抵抗を減少させることができます。一方、ダウンカット加工は、刃が材料の上から下へ切り込む方法で、特に仕上げ加工に適しています。この方法は、材料を押し下げる力が働くため、加工面が非常に滑らかになります。
例えば、鉄のフライス加工を行う場合、大まかな形状を削り出す際にはアップカット加工を選択し、最終的な仕上げにはダウンカット加工を選択すると、効率的かつ高品質な加工が可能になります。このように、アップカットとダウンカットはそれぞれ利点があり、加工する物の材質や目的に応じて適切に使い分けることが、高品質な製品を生産する上で非常に重要です。
結論として、CNCフライス加工におけるアップカットとダウンカットの選択は、加工品質を大きく左右します。それぞれの加工法の特徴を理解し、目的に応じて適切な方法を選択することで、効率的かつ高品質な加工が実現します。
5-3. 各加工法のコスト効率と適用例
CNCフライスにおけるアップカットとダウンカットの切削条件の違いは、鉄加工の精度と効率を大きく左右します。アップカット加工は、刃が回転する方向と材料を送る方向が同じで、切りくずが上向きに排出される特徴があります。これに対し、ダウンカット加工では、刃の回転方向とは反対に材料を送るため、切りくずが下向きに押し込まれ、表面がきれいに仕上がるという利点があります。
具体的な例として、鉄フライス加工での粗加工には、アップカットが適しています。加工速度が速く、大量の切りくずを効率良く排出できるため、時間とコストを節約できます。一方、仕上げ加工や精密な加工が必要な場合、ダウンカット加工が選ばれます。この方法では、切りくずが材料の中に押し込まれるため、切削面が非常に滑らかに仕上がります。
結論として、鉄フライス加工におけるアップカットとダウンカットの選択は、加工の目的と材料に大きく依存します。粗加工や大量加工にはアップカットが、精密加工や美しい仕上げが求められる場合にはダウンカットが適していることを理解することが重要です。どちらの方法も、加工品質と効率を最大限に引き出すためには、適切な切削条件の選択が不可欠です。
6. 切削条件の最適化とトラブルシューティング
6-1. アップカット加工時の一般的な問題点
CNCフライス加工において、アップカットとダウンカットは切削条件の選択において非常に重要です。これらの方法は、加工の品質や効率に大きく影響します。具体的には、アップカット加工は、刃が材料の下から上に向かって材料を削る方法で、ダウンカット加工は、その逆で上から下へと切削する方法です。この違いが、鉄を含むさまざまな材料のフライス加工においてどのような影響をもたらすかを探りましょう。
アップカット加工は、特に材料の排出が良いという利点がありますが、材料の表面が荒れやすくなる傾向があります。これは、切削中に材料が持ち上げられるためです。一方、ダウンカット加工は、表面の仕上がりが非常に滑らかになる利点がありますが、材料の排出が悪くなるというデメリットがあります。
例えば、精密な仕上がりを求める場合、アップカットではなくダウンカット加工の方が適しています。これは、鉄などの硬い材料の加工において、ダウンカット加工が生成する滑らかな表面が、製品の品質向上に寄与するためです。しかし、加工中の材料の排出を優先する場合は、アップカット加工が選択されます。
結論として、アップカットとダウンカットのどちらの加工方法を選択するかは、加工される材料の種類や求められる製品の品質に大きく依存します。鉄のフライス加工においては、加工の目的に応じて、これらの方法の違いを理解し適切に選択することが重要です。
6-2. ダウンカット加工時の一般的な問題点
CNCフライスにおいて、アップカットとダウンカットは切削条件の違いが重要です。アップカット加工は、刃が材料の下から上に向かって材料を削り取る方法です。これに対し、ダウンカット加工は、刃が上から下へと材料を切削する方法を指します。この二つの方法は、鉄をはじめとするフライス加工において、仕上がりや加工速度に大きな違いをもたらします。
例えば、アップカット加工では、切削時に材料が持ち上がりやすく、特に薄い材料の加工においては仕上がりに影響が出ることがあります。しかし、切削抵抗が少なく、速い加工が可能という利点もあります。一方、ダウンカット加工は、材料が持ち上がりにくく、仕上がりが非常に滑らかになることが多いですが、切削抵抗が大きくなるため、加工速度が遅くなる可能性があります。
特に鉄のフライス加工においては、これらの違いを理解し、加工する材料の特性や仕上がりの要求に応じて最適な方法を選択することが重要です。結論として、アップカットとダウンカットの選択は、加工品質と効率のバランスを考慮した上で行うべきであり、両者の特性を理解することが加工の成功につながります。
6-3. 切削条件の最適化のためのヒント
CNCフライス加工でのアップカットとダウンカットは、鉄加工において重要な役割を果たします。結論から言うと、これらの技術は加工の品質と効率を大きく左右し、それぞれの特徴を理解し適切に使い分けることが重要です。アップカット加工では、工具が回転する方向と逆に材料を送り込むため、切れ味が良く、仕上がりが綺麗になります。これは、木材加工でよく使われる方法です。一方、ダウンカット加工は、工具の回転方向と同じ方向に材料を送り込む方法で、材料の押し付けが強く、加工中の材料のズレが少なくなります。これは、金属加工やプラスチック加工でよく見られる手法です。例えば、鉄を加工する際には、ダウンカットの方が加工面のバリが少なく、加工精度が高くなる傾向があります。しかし、どちらの方法も材料の種類や加工する内容に応じて適切に選択する必要があり、その選択が加工品質を大きく左右します。最後に、アップカットとダウンカットの違いを理解し、加工する材料や目的に応じて最適な切削条件を選ぶことが、高品質な製品を効率的に生産するための鍵となります。
7. 実践的なフライス加工のコツ
7-1. 材料ごとの切削条件の違い
CNCフライス加工において、アップカットとダウンカットは大きな違いを持つ切削方法です。これらの違いを理解し適切に選択することが、加工品質や効率の向上につながります。アップカット加工では、カッターが回転する方向と同じ方向に仕事物を送ります。これにより、仕事物の表面から削りカスが効率よく排出され、表面品質が向上します。一方、ダウンカット加工では、カッターの回転方向と反対に仕事物を送り、カッターが仕事物の上面を圧下しながら切削します。この方法では、仕事物の押さえつけにより、より滑らかな表面仕上げが可能となります。
特に鉄のような材料をフライス加工する場合、これらの違いが重要です。例えば、鉄をアップカットで加工すると、削りカスの排出がスムーズに行われ、加工時の熱が分散しやすくなります。しかし、細かい仕上げが必要な場合は、ダウンカット加工が適しています。その圧下作用により、材料表面が平滑に保たれ、微細な仕上げが可能です。
結論として、CNCフライス加工におけるアップカットとダウンカットは、それぞれに適した材料や加工の目的に応じて選択することが重要です。鉄などの材料加工では、切削条件の選択が品質や効率に直結するため、各方法の特徴を理解し、目的に合わせた適切な加工条件を選ぶことが求められます。
7-2. 長寿命なツールを選ぶためのポイント
CNCフライス加工において、鉄などの材料を加工する際は、アップカットとダウンカットという二つの切削方法の違いを理解することが重要です。この二つの方法は、切削条件において大きな違いを持ち、それぞれが持つ特徴によって加工品質や効率が大きく左右されます。
まず、アップカット加工は、工具が回転する方向と反対に材料を送り込む方法です。この方法の最大の特徴は、切削が始まる際に工具の刃先が材料に食い込む力が強く、これにより切りくずが上方に排出されやすくなる点です。鉄などの硬い材料を精密加工する際には、このアップカット加工が適しています。特に、切りくずの排出がスムーズに行われるため、加工面の仕上がりが良くなるというメリットがあります。
一方、ダウンカット加工は、工具の回転方向と同じ方向に材料を送り込む方法です。この加工方法の利点は、切削時に工具が材料を押し下げるため、加工面が非常に滑らかに仕上がることにあります。しかし、この方法では切りくずの排出が難しくなるため、特に深い切り込みをする際には注意が必要です。
最終的に、どちらの加工方法を選択するかは、加工する材料の種類や加工品質の要求、さらには加工効率など、目的に応じて決定する必要があります。アップカットは切りくずの排出が良いため精密加工に向いており、ダウンカットは加工面の滑らかさを重視する場合に適しています。そのため、CNCフライス加工を行う際には、これらの切削条件の違いを正しく理解し、最適な方法を選択することが、効率的で高品質な加工を実現する鍵となります。
7-3. 効率的な工程計画とは
CNCフライス加工におけるアップカットとダウンカットの切削条件の違いは、加工の効率性と仕上がり品質に大きな影響を与えます。アップカット加工では、カッターが回転する際に被削材から材料を持ち上げるように削り取ります。これに対し、ダウンカット加工では、被削材に対してカッターが押し付けながら材料を削り取るため、仕上がりが滑らかになりやすいです。
特に、鉄を含む硬質材料のフライス加工において、これらの方法の選択は重要です。たとえば、アップカット加工は切りくずの排出が良好であり、深い溝の加工に適していますが、切削時に材料が持ち上がりやすいため、仕上がりの精度に影響を与える場合があります。一方で、ダウンカット加工は材料の持ち上がりが少なく、表面仕上げが良いため、外観が重要な部品や、細かい仕上げが求められる加工に適しています。
例えば、装飾品や精密部品の加工には、ダウンカット加工の方が適している場合が多いです。これらの部品では、表面の滑らかさが製品の品質を左右するため、ダウンカットでの加工が好まれます。
結論として、CNCフライス加工におけるアップカットとダウンカットの切削方法の選択は、加工する材料の種類や求められる仕上がり品質によって異なります。加工前に両方の方法の特性を理解し、目的に合わせて適切な方法を選択することが、効率的で高品質な加工を実現する鍵となります。
まとめ
CNCフライスで重要なアップカットとダウンカットの切削条件の違いについて理解することが重要です。アップカットは切削エッジが上方向に向いており、材料を持ち上げます。一方、ダウンカットは切削エッジが下方向に向いており、材料を押さえつけます。これらの違いを理解することで、鉄などの材料のフライス加工において適切な切削条件を選択できます。
「フライス加工と旋盤加工を理解する!鉄を加工する2大技術を解説」
鉄を加工する2大技術であるフライス加工と旋盤加工。これらの技術を理解することは、製造業や工業分野における重要な基礎知識となります。では、これらの技術の違いや特徴、それぞれの仕組みについてどのように理解すればよいのでしょうか?本記事では、初心者から経験者まで幅広い層の方々に向けて、フライス加工と旋盤加工の基本から解説していきます。鉄を加工する際に必要な知識や技術、その違いについて詳しく知りたい方は、ぜひ最後までご覧ください。
1. 切削加工の基礎知識
1-1. 切削加工とは
鉄を加工する際に欠かせない2大技術、フライス加工と旋盤加工について解説します。これらの技術は、製品の形状や精度を高めるために不可欠です。フライス加工は多様な形状を削り出すことができ、旋盤加工は円形の物を加工するのに適しています。たとえば、フライス加工では平面や溝、複雑な形状を作り出すことが可能です。一方、旋盤加工はネジや円筒形の部品など、回転体の加工に特化しています。このように、これら2つの技術は、製品の要求に応じて使い分けられます。特に日本では、高度な技術力を要する精密部品の製造において、これらの加工技術が重要な役割を果たしています。結論として、フライス加工と旋盤加工は、それぞれ異なる特性を持ち、製品製造の現場で欠かせない技術です。これらの技術を理解し、適切に活用することで、より高品質な製品を生み出すことが可能になります。
1-2. 切削加工の歴史と発展
フライス加工と旋盤加工は、鉄などの金属を加工するための重要な技術です。これらの技術を理解することで、金属加工の世界がより身近に感じられるようになります。フライス加工とは、刃が回転することにより金属を削り取る加工方法です。一方、旋盤加工は、金属材料を回転させながら刃で削り取る方法で、形状を整えたり、細かな部品を作成したりするのに適しています。
例えば、フライス加工は平面や溝、歯車などの加工に用いられます。一方で、旋盤加工はネジや軸など、円筒形の部品の加工に適していると言えます。これらの違いから、フライス加工と旋盤加工はそれぞれ特有の強みを持ち、多様な製品の製造に寄与しています。
総じて、フライス加工と旋盤加工は金属加工技術の中核をなすものであり、それぞれに適した用途があります。これらの技術を適切に理解し、用いることで、より高品質で精度の高い製品の製造が可能となります。
1-3. 鉄とその特性について
鉄を加工する技術には、フライス加工と旋盤加工の2つがあります。これらは鉄を含む多くの材料を形成し、加工するために広く使用されています。フライス加工は、回転する刃を使用して材料から不要な部分を削り取る技術です。一方、旋盤加工は、材料自体を回転させながら固定された切削工具で材料を削ることにより、円形の形状を作り出す技術です。
たとえば、フライス加工はギアやエンジン部品のような複雑な形状を作るのに適しています。一方、旋盤加工は軸やローラーのような円形の部品を製造するのに最適です。日本では、これらの技術は自動車産業や電子機器の製造において特に重要です。技術の進歩により、より精密で複雑な部品を効率的に製造できるようになりました。
結論として、フライス加工と旋盤加工は鉄を始めとする多くの材料を加工する上で欠かせない技術です。それぞれに適した用途があり、日本の製造業において重要な役割を果たしています。これらの技術を理解し、適切に使用することが、高品質な製品を効率的に製造する鍵となります。
1-4. 切削加工における鉄の利点
鉄はその耐久性と加工しやすさから、切削加工において非常に重要な材料です。フライス加工と旋盤加工は、鉄を加工する上で最も一般的に使われる二つの技術であり、それぞれ特徴があります。フライス加工では、回転する工具を使って鉄の表面を削り取ります。これは平面や溝、歯車などの加工に適しています。例えば、自動車のエンジン部品や機械のフレームなど、複雑な形状の加工が可能です。一方、旋盤加工は、材料を回転させながら切削する方法で、主に円筒形の物体の加工に用いられます。シャフトやボルトなど、回転体の加工に最適です。
これらの加工技術により、鉄は幅広い用途に対応できるようになります。フライス加工と旋盤加工の選択は、加工したい鉄製品の形状や用途によって決定されます。これらの技術の理解と適切な活用により、効率的かつ精密な鉄製品の製造が可能となります。最終的に、フライス加工と旋盤加工は、鉄を加工する上で欠かせない二大技術であり、それぞれに特化した様々な製品の製造に寄与しています。
2. 切削加工の種類とその特徴
2-1. 切削加工の一般的な種類
フライス加工と旋盤加工は、鉄などの金属を加工する上で欠かせない2つの技術です。これらの技術により、精密な部品や機械を製造することが可能になっています。フライス加工は、回転する工具を用いて材料の表面を削り取る技術で、平面や溝、歯車など、複雑な形状を作り出すことが得意です。一方、旋盤加工は、材料を回転させながら工具で削ることで、円形や円筒形の形状を作る技術です。例えば、日本の自動車産業では、エンジン部品や車軸など、多くの部品がこれらの技術を用いて製造されています。このように、フライス加工と旋盤加工は、我々の日常生活に欠かせない様々な製品の生産に不可欠な技術であることが分かります。最終的に、これらの技術を理解し、適切に利用することが、高品質な製品を効率良く生産する鍵となるのです。
2-2. 各加工法の特徴と用途
フライス加工と旋盤加工は、鉄などの金属を加工するための2大技術です。これらの技術は、工業製品の製造において不可欠であり、それぞれに独特の特徴と用途があります。フライス加工は、回転する刃を用いて材料の表面を削り取る加工法で、平面や溝、歯車などの加工に適しています。一方、旋盤加工は、固定された切削工具で回転する材料を削る加工法で、円筒形の加工品や複雑な形状を持つ製品の製造に利用されます。
例えば、自動車のエンジン部品や、機械のギアなど、私たちの日常生活に欠かせない多くの製品が、これらの加工技術によって作られています。フライス加工によって、精密な平面や溝が加工され、旋盤加工によって、円滑に動作する円筒形の部品が製造されるのです。
最終的に、これらの加工技術は、製品の品質向上と製造効率の向上に寄与しています。フライス加工と旋盤加工の理解は、製造業における技術の進歩と、日常生活に欠かせない製品の生産に欠かせない知識と言えるでしょう。
2-3. 鉄を加工する際の注意点
鉄を加工する際には、フライス加工と旋盤加工という2つの主要な技術があります。これらは、鉄製品を製造する上で不可欠な方法です。フライス加工では、回転する工具を使用して鉄を削り、形状を作ります。一方、旋盤加工では、固定された切削工具を使用して、回転する鉄の材料を削り取ります。これにより、円筒形の形状が作られます。
例として、フライス加工は複雑な形状や平面を必要とする部品に適しています。自動車のエンジン部品や機械のフレームなどがこれに該当します。一方、旋盤加工は、ネジや軸受けのような円形の部品に使用されます。
この2つの加工方法は、それぞれ特有の利点があり、製品の要求に応じて選択されます。フライス加工は複雑なデザインに柔軟に対応できる一方で、旋盤加工は円形の精密な部品を効率的に製造できます。したがって、鉄を加工する際には、目的に応じた適切な技術を選択することが大切です。これにより、高品質かつ効率的な製品製造が可能となります。
3. 金属材料の選び方
3-1. 材料選定の基準
フライス加工と旋盤加工は、鉄などの金属を精密に加工するために欠かせない2つの技術です。これらは、製造業において非常に重要な役割を果たしています。フライス加工は、回転する刃を用いて材料の表面を削り取る方法で、複雑な形状や平面を作り出すのに適しています。一方、旋盤加工は、材料を回転させながら切削工具を用いて形を整える技術で、円形や筒形の部品製造に特に有効です。
例えば、自動車のエンジン部品や航空機の部品製造において、これらの加工技術は欠かせません。フライス加工と旋盤加工の適切な利用により、高精度かつ複雑な形状の部品を効率良く製造することが可能になります。また、日本はこれらの技術において高い技術力を有しており、世界中の製造業から高い評価を受けています。
このように、フライス加工と旋盤加工は鉄をはじめとする金属の精密加工において不可欠であり、日本の製造業の競争力を支える基盤技術と言えるでしょう。これらの技術を理解し、適切に活用することは、製品の品質向上と製造効率の向上につながります。
3-2. 鉄の種類と選び方
フライス加工と旋盤加工は、鉄の加工における2大技術です。これらの技術は、それぞれ異なる特徴を持ち、用途に応じて使い分けられます。フライス加工は、主に複雑な形状を持つ製品の加工に利用され、旋盤加工は、円筒形の製品を作るのに適しています。例えば、フライス加工は自動車のエンジン部品や航空機の部品製造に、旋盤加工はネジや軸など、一定の形状を持つ部品の製造に使用されます。これらの技術を適切に使い分けることにより、製品はより精密に、効率良く製造されます。最終的に、フライス加工と旋盤加工を理解し、その違いを知ることは、鉄を加工する際に重要です。それぞれの技術が持つ特徴を理解し、目的に合わせて最適な加工方法を選ぶことが、高品質な製品を生み出す鍵となります。
3-3. 加工方法に適した鉄の選定
フライス加工と旋盤加工は、鉄を加工する際に頻繁に使用される2つの主要な技術です。これらの技術の理解は、機械加工分野において非常に重要です。まず、フライス加工は、回転する工具を使用して鉄などの材料から部品を削り取る加工方法です。この技術は特に、平面や曲面、溝など、複雑な形状の加工に適しています。一方、旋盤加工は、材料を回転させながら切削工具を材料に接触させて形状を作り出す方法であり、主に円筒形の作品に用いられます。
例として、フライス加工は自動車のエンジン部品や航空機の部品製造に、旋盤加工はボルトやナット、パイプなどの製造にそれぞれ活用されています。これらの加工技術によって、精度高く複雑な形状の部品を効率的に製造することが可能になります。
結論として、フライス加工と旋盤加工はそれぞれ異なる特性を持ち、適切に使い分けることで鉄を始めとする多様な材料の加工に役立っています。これらの技術の理解と適用は、製品の品質向上と生産効率の向上に直結するため、機械加工の分野では非常に重要です。
4. 旋盤加工の概要
4-1. 旋盤加工とは
旋盤加工とは、主に金属などの材料を回転させながら、切削工具を用いて材料の表面を削り取る加工技術です。この技術は、円筒形や円錐形など、対称形状の部品を製造するのに特に適しています。例えば、自動車のエンジン部品や、機械の軸など、精密な部品の製造に広く用いられています。旋盤加工の優れた点は、高い精度で複雑な形状の部品を製造できることにあります。これにより、様々な産業で必要とされる特殊な部品を効率的に生産することが可能になります。日本では、特に高品質な製品が求められるため、旋盤加工技術は重要な役割を担っています。この技術により、精密機械や自動車などの産業の発展が支えられているのです。
4-2. 旋盤加工のプロセスと技術
フライス加工と旋盤加工は、鉄をはじめとする金属の加工に不可欠な2つの技術です。これらの技術はそれぞれ異なる特徴を持ち、製品の形状や用途に応じて使い分けられます。フライス加工は、回転する刃で材料を削って形を作る技術であり、複雑な形状も精密に加工できるため、自動車の部品や機械の部品製造に広く利用されています。一方、旋盤加工は、材料を高速で回転させながら固定した刃で削り取る加工法で、円筒形の部品製造に最適です。例えば、ネジや軸受けなどがこれに該当します。
これらの技術が日本の製造業において重要な役割を果たしている理由は、高精度な部品が求められる製品を多く製造しているからです。日本製の自動車や電化製品は、その精密さで世界中に知られており、その製造過程でフライス加工や旋盤加工が欠かせないのです。
まとめると、フライス加工と旋盤加工は、それぞれ異なる特性を持ち、日本の製造業において不可欠な技術です。複雑な形状の加工が必要な場合にはフライス加工が、円筒形の部品を製造する際には旋盤加工が適しています。これらの技術を適切に使用することで、高品質な製品を効率良く生産することが可能になります。
4-3. 旋盤加工に適した鉄の種類
鉄を加工するには、フライス加工と旋盤加工という2つの主要な技術があります。旋盤加工に適した鉄の種類を理解することは、高品質な製品を生産する上で欠かせません。旋盤加工は、主に円形の物体を作り出すために用いられる技術です。この方法では、鉄を旋盤の中心に固定し、切削工具で形を削り出していきます。特に、柔らかめの鉄や、加工しやすい鉄が旋盤加工には適しています。たとえば、SS材(構造用炭素鋼)やS45C(炭素鋼)などが挙げられます。これらの材料は、加工しやすく、かつ強度が必要な部品に最適です。
最終的に、旋盤加工に適した鉄の選定は、製品の用途や必要な耐久性に大きく依存します。SS材やS45Cなどの鉄は、加工しやすさと強度のバランスが取れているため、多くの旋盤加工プロジェクトで好んで使用されます。このように、正しい種類の鉄を選ぶことで、効率的かつ質の高い加工が可能となります。
5. フライス加工の概要
5-1. フライス加工とは
フライス加工と旋盤加工は、鉄をはじめとする金属加工に不可欠な2大技術です。これらの技術の理解は、製品製造の効率と品質の向上に直結します。フライス加工では、回転する刃を用いて材料の表面を削り取り、必要な形状に加工します。この方法は、平面や曲面、溝など、複雑な形状の加工に適しています。例えば、自動車のエンジン部品や航空機の構造部材など、精密な仕上がりが求められる部品の製造に利用されます。一方、旋盤加工は、材料を回転させながら切削工具で削ることで、円形や筒形の形状を生み出します。この技術は、ボルトやナット、軸受などの部品製造に広く用いられています。フライス加工と旋盤加工は、それぞれ異なる特性と適用範囲を持ち、製品の設計において重要な役割を果たします。したがって、これらの技術を正確に理解し、適切に活用することが、高品質な製品製造の鍵となります。
5-2. フライス加工のプロセスと技術
フライス加工と旋盤加工は、鉄などの金属を加工する上で欠かせない2大技術です。これらの技術を理解することは、製品の品質向上や生産効率の向上に直結します。まず、フライス加工は、回転する刃を用いて材料の表面を削り取る加工方法です。具体的には、自動車のエンジン部品や飛行機の構造部材など、複雑な形状を持つ部品の製造に多く利用されています。一方、旋盤加工は、材料を回転させながら刃で削ることで、円形の部品を製造する技術です。例えば、ボルトやナット、軸受けなどがこの加工法で作られます。
これら2つの加工技術の大きな違いは、加工する部品の形状と加工方法にあります。フライス加工は平面や曲面を加工するのに適しており、旋盤加工は主に円形や円筒形の部品を製造するのに用いられます。日本でも、これらの技術は幅広い産業で活用されており、高度な精密加工技術として国内外から高い評価を受けています。
最後に、フライス加工と旋盤加工は、鉄をはじめとする金属加工の基本であり、それぞれに適した用途があります。これらの技術を理解し、適切に活用することで、製品の品質向上や生産効率を高めることが可能です。
5-3. フライス加工に適した鉄の種類
フライス加工と旋盤加工は、鉄をはじめとする金属を加工する上で非常に重要な技術です。これら二つの技術は、それぞれ異なる特徴を持ち、用途に応じて選択されます。フライス加工は、切削工具が回転することによって金属を削り取る方法であり、平面や曲面、溝など複雑な形状の加工に適しています。一方、旋盤加工は、金属を回転させながら切削工具で削り取る技術で、円形や円筒形の加工に最適です。
例えば、フライス加工は自動車のエンジン部品や機械のフレームなど、精密な平面や多角形の加工が必要な場合に用いられます。旋盤加工は、ボルトやネジ、軸受けなどの円筒形の部品製造に特に役立ちます。
このように、フライス加工と旋盤加工は鉄を含む多様な材料の形状や用途に応じて、それぞれ異なる場面で活躍する技術です。適切な加工方法を選択することで、より高品質な製品を効率的に生産することが可能になります。そのため、これらの加工技術の理解は、製造業における重要な知識となります。
6. 旋盤加工とフライス加工の違い
6-1. 加工方法の基本的な違い
フライス加工と旋盤加工は、鉄などの金属加工において最も基本的かつ重要な技術であり、これらの違いを理解することが工業製品の製造において必須です。フライス加工は、多様な形状を持つ切削工具を使って、固定された材料の表面を削り取る加工方法です。この技術は、平面や曲面、溝など複雑な形状を作ることが可能であり、例えばギアの製造などに応用されます。一方で、旋盤加工は、材料を高速で回転させながら、固定した切削工具で材料の表面を削り取る方法です。これは主に円筒形の材料を加工する際に用いられ、例としてはネジや軸などが挙げられます。
フライス加工と旋盤加工の主な違いは、加工する材料の動きと加工できる形状の種類にあります。フライス加工では複雑な形状を効率的に作ることができますが、旋盤加工はよりシンプルな形状の精密加工に適しています。これら二つの技術を組み合わせることで、幅広い工業製品の製造が可能となります。したがって、フライス加工と旋盤加工を理解し、適切に適用することは、日本の製造業における品質と生産効率の向上につながります。
6-2. 適用範囲と加工可能な形状
フライス加工と旋盤加工は、鉄などの金属を加工する際に欠かせない2つの主要な技術です。これらの技術の理解は、様々な製品の製造において重要となります。フライス加工は、主に平面や曲面を削るために用いられ、旋盤加工は、円筒形の物体を加工するのに適しています。例えば、自動車のエンジン部品や家電製品のコンポーネントなど、私たちの日常生活で使われている多くの製品が、これらの技術によって加工されています。
フライス加工では、回転する工具を用いて材料を削り取ります。この方法では、非常に複雑な形状や平面を精密に加工することが可能です。一方、旋盤加工は、材料を回転させながら固定された切削工具で材料を削り取る方法で、主に円形や円筒形の加工に用いられます。
これらの技術の違いを理解することで、製品設計や加工方法の選択において、より効率的かつ効果的なアプローチを取ることができるようになります。結論として、フライス加工と旋盤加工は、製造業における鉄やその他の金属を加工する上で不可欠な技術であり、それぞれが異なる特性と用途を持っていることを理解することが重要です。
6-3. 旋盤加工とフライス加工の選択基準
フライス加工と旋盤加工は、鉄をはじめとする金属加工において不可欠な2つの技術である。これらの加工技術を理解し、適切に選択することは、多くの製造プロセスにおいて重要である。フライス加工は、回転する工具を使用して被加工物から材料を削り取る加工法であり、複雑な形状や平面を加工するのに適している。一方、旋盤加工は、被加工物を回転させながら切削工具で材料を削り取る方法で、円形や筒形の部品を製造するのに最適である。例えば、自動車のエンジン部品やギアなどは、これらの加工技術を駆使して製造される。フライス加工と旋盤加工の選択は、製品の設計や要求される精度、製造コストなどによって決まり、適切な加工方法を選ぶことが品質の向上と効率的な生産に繋がる。したがって、これらの加工技術の違いを理解し、プロジェクトごとに最適な方法を選択することが、製造業における成功の鍵である。
7. 実践的な加工技術のポイント
7-1. 加工精度を高めるためのコツ
フライス加工と旋盤加工は、鉄を加工する際に重要な2つの技術です。これらはそれぞれ異なる方法で材料を加工し、製品の形状や精度に大きな影響を与えます。フライス加工は、主に平面や曲面を削るために用いられます。例を挙げると、機械部品の溝や歯車などの加工に適しています。一方、旋盤加工は円筒形の材料を回転させながら、切削工具で削り取ることによって形状を作り出します。この方法は、ボルトやシャフトなどの円形の部品を作るのに最適です。
両者の主な違いは、加工する物の形状と加工方法にあります。フライス加工は複雑な形状や細かい部品加工に対応できる反面、旋盤加工は比較的シンプルな形状の加工に適していますが、高い精度で円周を加工できるという利点があります。
日本では、これらの加工技術が高度に発展しており、特に精密な部品製造や工業製品の生産において中心的な役割を担っています。例えば、自動車や電子機器の部品製造において、これらの技術によって高品質で信頼性の高い製品が生み出されています。
結論として、フライス加工と旋盤加工は、鉄をはじめとする多くの材料を加工する上で欠かせない技術です。それぞれの方法が持つ特性を理解し、適切に選択することで、高い品質と効率の良い製品製造が可能になります。
7-2. 効率的な加工工程の計画
フライス加工と旋盤加工は、鉄をはじめとする金属加工において不可欠な2大技術です。これらの加工方法は、製品の形状や用途に応じて選ばれ、各々が特徴を持ちます。フライス加工は、回転する刃を用いて材料の表面を削り取ることで形状を作り出す技術です。一方、旋盤加工は、材料自体を回転させながら固定された刃で削ることにより、円筒形などの形状を生成します。
例えば、フライス加工は複雑な形状や平面を加工するのに適している一方で、旋盤加工は軸や円筒形の部品を作る際に特に有効です。日本では、自動車や電子機器の部品製造にこれらの技術が広く利用されています。自動車のエンジン部品やギアなど、精密さが求められる部品の製造には、これらの加工技術の精度が欠かせません。
このように、フライス加工と旋盤加工は、それぞれ異なる特徴を持ち、用途に応じて選択されます。製造業においてこれらの技術の理解と適切な使用は、効率的で高品質な製品を生み出すために必要不可欠です。
7-3. 安全な加工環境の確保方法
フライス加工と旋盤加工は、鉄をはじめとする金属を加工するための2大技術です。これらの技術の理解は、機械製造や工業デザインにおいて非常に重要です。フライス加工は、回転する刃を用いて材料の表面を削り取る方法です。これにより、平面や曲面、溝など、さまざまな形状を作り出すことができます。一方、旋盤加工は、材料自体を回転させながら刃で削ることで、円形や円筒形の形状を加工する技術です。
日本では、これらの技術が高度に発展しています。例えば、自動車や航空機の部品製造において、フライス加工と旋盤加工は不可欠な技術として活用されています。これらの加工方法により、高精度かつ複雑な形状の部品を効率良く生産することが可能となっています。
このように、フライス加工と旋盤加工は、鉄をはじめとする金属製品の製造において、それぞれ異なる役割を持っています。これらの技術の理解と適用により、より精密で高品質な製品の開発が進められています。
8. まとめと応用
8-1. 切削加工の基本を生かした応用例
鉄を加工する方法として、フライス加工と旋盤加工は非常に重要な技術です。これらの技術は、鉄などの金属を加工する際の基本であり、多くの製品の製造に欠かせません。フライス加工とは、回転する工具を使用して、金属表面から削り取る加工方法です。一方、旋盤加工は、金属材料を回転させながら、固定した切削工具で材料の一部を削り取る方法です。
たとえば、フライス加工は、自動車のエンジンブロックや機械部品など、複雑な形状の金属部品の製造に用いられます。旋盤加工は、ネジや軸など、円形や筒形の部品の加工に特に適しています。これらの加工技術は、精度が高く、さまざまな形状に対応できるため、製造業で広く利用されています。
結論として、フライス加工と旋盤加工は、鉄をはじめとする金属加工の基本であり、製品の精度や効率的な製造に不可欠な技術です。これらの加工方法を理解することで、製品設計や製造の幅が大きく広がります。
8-2. フライス加工と旋盤加工の組み合わせによる複雑な加工
フライス加工と旋盤加工は、鉄などの金属を加工する上で不可欠な二つの技術です。これらの技法を理解することは、精密な部品製作において極めて重要です。フライス加工は、回転する刃を用いて材料の表面を削り取る加工方法です。この方法により、平面や溝、歯車など、様々な形状を作り出すことが可能です。一方、旋盤加工は、材料を高速で回転させながら、固定された刃で削り取って形を整える方法です。これは主に円筒形の部品を作成するのに適しています。
特に日本では、これらの加工技術が高度に発展しており、自動車や家電製品など、多岐にわたる産業で活用されています。例えば、自動車のエンジン部品やギアなど、精密な加工が求められる製品の製造には、これらの技術が不可欠です。また、フライス加工と旋盤加工を組み合わせることで、より複雑な形状や高度な精度を持つ部品の生産が可能になります。
このように、フライス加工と旋盤加工は、製造分野において非常に重要な技術であり、それぞれが持つ特性を理解し、適切に使い分けることが、製品の品質向上につながります。
8-3. 今後の加工技術の展望
フライス加工と旋盤加工は、鉄を始めとする金属材料を加工する上で欠かせない2大技術です。これらの技術には明確な違いがあり、それぞれが特有の利点を持っています。フライス加工は、主に複雑な形状や平面を削り出すのに適しています。例えば、歯車や溝など、精密な部品製造に不可欠です。一方、旋盤加工は円筒形の物体を加工するのに特化しており、例えばネジや軸などの製作に用いられます。日本においても、これらの技術は多くの製造業で基本とされており、高度な技術力を要求されます。
フライス加工と旋盤加工の違いを理解することは、適切な加工方法を選択し、製品の品質を向上させるために非常に重要です。特に、精密な加工が求められる場合や、生産効率を考慮する必要がある場合に、それぞれの技術の適用可能性を見極めることがカギとなります。今後も、これらの加工技術は製造業の発展に欠かせないものであり、技術の進化とともにさらなる可能性が広がっていくことでしょう。
まとめ
鉄を加工するための主要な2つの技術であるフライス加工と旋盤加工について解説します。これらの技術を理解することで、鉄を効率的に加工し形作ることができます。それぞれの特徴や違い、利点と欠点について詳しく説明します。また、どちらの技術を使用するべきかを判断するための基準も解説します。
「鉄加工の基本を学ぶ!フライスと旋盤の方法論としての違いと活用術」
「鉄加工の基本を学ぶ!フライスと旋盤の方法論としての違いと活用術」へようこそ!鉄という耐久性に優れた素材を加工するための技術は、製造業や工業分野において極めて重要です。本記事では、フライス加工と旋盤加工の違いやそれぞれの活用術について解説していきます。鉄を扱う加工技術を学びたい方、どのようにして鉄を効率的に加工するか知りたい方にとって、貴重な情報を提供します。さあ、鉄加工の世界への扉を開けましょう!
1. 切削加工とは:基礎知識と概要
1-1. 切削加工の定義とその重要性
鉄加工において、フライス加工と旋盤加工は基本中の基本です。これら二つの方法論の違いを理解することは、鉄加工を行う上で非常に重要です。フライス加工は、主に平面や溝、複雑な形状を削り出すのに用いられます。一方、旋盤加工は円形の材料を加工するのに適しており、円筒形の部品作成に使用されます。例えば、フライス加工ではギアやフレームの加工が可能であり、旋盤加工ではボルトや軸などの円形部品の加工が行えます。
日本においても、これらの技術は製造業の基盤となっており、正確な部品を効率良く生産するためには欠かせません。特に、精密機械や自動車産業など、高度な技術を要求される分野での活用は目覚ましいものがあります。フライスと旋盤の違いを理解し、それぞれの加工法の特徴を活かすことは、高品質な製品を製造する上での鍵となります。
結論として、フライス加工と旋盤加工はそれぞれ異なる特性を持ち、製品の精度や効率を左右する重要な技術です。日本の製造業では、これらの加工技術がもたらす精密さと効率性を生かし、世界に誇る高品質な製品を生み出しています。
1-2. 切削加工の主な種類と特徴
鉄加工では、フライス加工と旋盤加工は最も基本的な技術の二つです。これらの加工方法はそれぞれ特徴があり、適した用途が異なります。フライス加工とは、刃が回転する工具を使用して鉄などの材料から不要な部分を削り取る技術です。一方、旋盤加工は材料を回転させ、切削工具を用いて形状を整える方法です。
フライス加工の特徴は、平面や曲面、溝など複雑な形状を加工できる点にあります。たとえば、機械部品の歯車やフレームなど、精密な加工が求められる場合に多く用いられます。対して、旋盤加工の長所は円形や円筒形の物を効率良く加工できることです。軸やボルトなど、回転する部品の製造に適しています。
日本においても、これらの加工技術は産業のさまざまな場面で活用されています。例えば、自動車産業ではエンジン部品の精密加工にフライス加工が、車軸などの製造には旋盤加工がそれぞれ用いられるなど、その用途は広く及んでいます。
結論として、フライス加工と旋盤加工は、それぞれ異なる特長を持ち、鉄加工の現場では不可欠な技術です。これらの方法論の違いを理解することで、より適切な加工技術を選択し、効率的な製造プロセスを実現できます。
1-3. 金属加工における切削加工の役割
鉄加工において、フライス加工と旋盤加工は、金属の形状を作る上で欠かせない技術です。これらの違いを理解することは、より効果的に金属を加工するために重要です。フライス加工は、工具が回転し、その刃が金属に触れることで金属を削り取る方法です。これに対し、旋盤加工は、金属自体を回転させながら工具で削ることで形を作ります。例えば、フライス加工は平面や曲面を加工するのに適しており、自動車のエンジン部品などの製造に利用されます。一方、旋盤加工は円筒形の加工に強く、釘やボルトといった製品の製造に多く用いられます。これらの加工方法を適切に選択することで、製造効率を高め、より精密な製品を生産することが可能です。結論として、フライス加工と旋盤加工の違いを理解し、それぞれの利点を活かすことが、鉄加工の基本を学ぶ上で重要であると言えます。
2. 鉄のフライス加工とその基礎
2-1. フライス加工の基本概念
鉄加工において、フライス加工と旋盤加工は基本的な加工方法として広く知られています。これらの手法は鉄をはじめとする金属を加工する際に欠かせない技術であり、それぞれに特有の利点と活用方法があります。フライス加工と旋盤加工の違いを理解することは、効率的で質の高い製品を製造する上で重要です。
フライス加工は、回転する刃を用いて材料の表面を削ることで形状を作り出します。この方法では、複雑な形状や平面、溝といった加工が可能であり、多様な製品の製造に適しています。例えば、自動車のエンジン部品や航空機の構造部材など、精密な加工が求められる場合に用いられます。
一方、旋盤加工は、固定された材料を高速で回転させ、切削工具を用いて材料の外形を削る加工方法です。主に円筒形や円錐形の部品を製造するのに適しており、一般的にはボルトやナット、軸受けなどの製造に多く用いられます。
フライス加工と旋盤加工の違いを理解し、それぞれの特性を活かすことで、より効率的かつ高品質な製品製造が可能になります。例えば、精密な平面が必要な場合はフライス加工を、円形の部品を多く製造する場合は旋盤加工が適しています。適切な加工方法を選択することで、生産コストの削減や製品の品質向上に繋がります。
このように、フライス加工と旋盤加工は鉄加工の基本であり、それぞれが持つ特性を理解し、適切に活用することが重要です。これらの技術をマスターすることで、より良い製品を効率的に製造することができるのです。
2-2. フライス盤の種類と特徴
鉄加工において、フライス加工と旋盤加工は基本的な技術です。これらの方法論の違いを理解することは、工作機械の適切な活用に不可欠です。フライス加工とは、回転する工具を使って材料の表面から削り取る加工方法です。その一方で、旋盤加工は材料自体を回転させながら、固定された切削工具で材料を削る技術です。
例えば、フライス加工は複雑な形状や平面を作成するのに適しています。具体的には、溝や側面の加工等に用いられます。旋盤加工は円筒形の材料に適しており、ボルトのねじ切りや円形の部品を作成する場合に活用されます。
これらの違いを踏まえると、鉄加工の際には目的に応じて適切な加工法を選択することが重要です。フライス加工であれば複雑な形状の加工に、旋盤加工であれば円筒形の部品作成に適しているということが結論として導き出せます。鉄加工の基本を学ぶうえで、フライスと旋盤の方法論の違いを理解し、それぞれの技術を適切に活用することが、効率的で高品質な製品を作るための鍵となります。
2-3. フライス加工の主要な技術と活用術
フライス加工と旋盤加工は、鉄加工において基本的でありながら、その方法論として大きな違いがあります。この二つの技術は、加工する部品の形状や必要とされる精度によって、柔軟に選択されるべきです。まず、フライス加工は、主に平面や曲面などの加工に適しており、複雑な形状の部品製造に不可欠です。一方、旋盤加工は、円筒形の物体を加工するのに適しており、特に長さ方向の精度が求められる場合に効果を発揮します。
具体的な例として、フライス加工は航空機の部品や自動車のエンジン部品の製造に使用されています。これらの部品は、複雑な形状や高い精度が必要とされ、フライス加工によってその要求を満たすことができます。旋盤加工は、ボルトやシャフトなど、長さ方向の精度が重要な部品の製造に欠かせません。これらの部品は、機械の動作において基本的な役割を果たし、旋盤加工によって高い品質が保証されます。
結論として、フライス加工と旋盤加工はそれぞれに適した用途があり、鉄加工におけるその活用は多岐にわたります。適切な加工方法を選択することで、高品質な製品の製造が可能となり、製造業の発展に貢献しています。
3. 鉄の旋盤加工とその基礎
3-1. 旋盤加工の基本概念
「鉄加工の基本を学ぼう!フライスと旋盤の方法論としての違いと活用術」では、鉄を扱う加工技術として、フライス加工と旋盤加工の重要性を探ります。鉄加工は日本の製造業において不可欠であり、これら二つの手法はそれぞれ特有の役割と利点を持ちます。
旋盤加工は、主に円形の材料を加工するのに適しており、精密な円筒形の部品製造に多用されます。一方、フライス加工は、より複雑な形状、例えば平面や溝を持つ部品の加工に適しています。この違いは、旋盤が材料を回転させることで加工を行い、フライス加工では刃が回転しながら材料に対して移動することで形状を変える点にあります。
日本では、自動車産業や電子機器に用いられる部品の多くが、この二つの加工技術によって製造されています。例えば、自動車のエンジン部分や、スマートフォンの内部メカニズムに用いられる精密な部品は、旋盤加工によって製造されることが多いです。また、ロボットの関節部分や機械のフレームには、フライス加工で作られた部品が使われています。
結論として、フライス加工と旋盤加工は、それぞれ特定の加工が得意な点が異なり、日本の製造業において不可欠な技術です。適切な技術を活用することで、高品質な製品を効率的に製造することが可能となります。
3-2. 旋盤の種類と特徴
鉄加工には多種多様な技術が存在しますが、特にフライス加工と旋盤加工は基本中の基本とされ、その違いを理解することが重要です。これら二つの加工法は、使用される機械の違いから、加工される鉄製品の形状や用途に大きな影響を与えます。
フライス加工は、主に平面や曲面を削る作業に用いられ、切削工具が回転することで材料を削り取ります。この方法は、複雑な形状や大量生産に適しており、例えばギアやフレームなどの部品作成に活用されます。一方、旋盤加工は、材料自身を回転させながら切削工具で削ることで、円筒形の物体を作るのに適しています。この加工法は、ボルトやシャフトなど、精密な円形の部品を製造する際に用いられます。
これらの違いを踏まえると、加工する製品の形状に応じて最適な加工法を選択することができます。フライス加工は複雑な形状の加工に、旋盤加工は円形の部品製造に有効であるという点が理解できるでしょう。日本では、これらの技術が長年にわたって研究され、高度な鉄加工技術が発展してきました。それぞれの方法論を学ぶことで、日本の鉄加工技術の深さと幅広さを改めて認識できるはずです。
3-3. 旋盤加工の主要な技術と活用術
鉄加工において、旋盤加工はその基本的な技術の一つです。この方法は、主に円形の物体を加工する際に利用され、その精密さと効率性から多くの工業分野で重宝されています。旋盤加工の特徴は、加工する材料を高速で回転させながら、カッターなどの工具を用いて形状を削り出す点にあります。これにより、非常に滑らかな表面を持つ製品を作り出すことが可能となります。
例として、自動車産業ではエンジンの部品や車輪のハブなど、精度が要求される部品の製造に旋盤加工が欠かせません。また、時計業界でも、精密な部品を作るためにこの技術が用いられています。これらの具体例からも、旋盤加工がいかに幅広い用途に活用されているかがわかります。
旋盤加工の技術は、その使いやすさと汎用性から、今後も様々な産業での利用が期待されています。特に、新しい材料や加工方法の開発が進む中で、更なる精度向上や効率化が求められているため、技術の進化が続くことでしょう。結論として、旋盤加工は鉄加工の分野における基本であり、その技術と活用法を理解することは、多くの工業製品を作る上で欠かせない要素です。
4. フライスと旋盤の違いと適用
4-1. フライス加工と旋盤加工の比較
フライス加工と旋盤加工は、鉄加工の分野でよく用いられる二つの基本的な技術です。これらの方法論の違いを理解することは、工業製品の製造における効率と品質の向上に不可欠です。フライス加工は、回転する工具を用いて材料から不要な部分を削り取る加工法です。これに対し、旋盤加工は、材料自体を回転させながら切削工具で形を整える加工法です。
例えば、複雑な形状や平面を加工する際は、フライス加工の方が適しています。フライス加工機は多様な形状の切削が可能であり、平面や溝、歯車などの加工に対応できます。一方、円筒形や円錐形の部品の製造には旋盤加工が適しています。これは旋盤が材料を回転させながら均一の形状を削り出すため、非常に精密な仕上がりが得られるからです。
このように、フライス加工と旋盤加工はそれぞれ異なる利点を持ち、製品の設計や要求される精度、加工する材料の種類によって選択が異なります。日本では、精密なモノづくりが求められる様々な産業でこれらの加工技術が活用されており、その技術力は世界でも高く評価されています。最終的に、フライス加工と旋盤加工を適切に使い分けることが、高品質な製品製造への鍵となります。
4-2. 各加工方法の適用範囲と選択ポイント
鉄加工におけるフライス加工と旋盤加工は、製造業において重要な役割を果たしています。その違いを理解することは、効率的な加工方法の選択に不可欠です。フライス加工は、主に平面や曲面を削り出すために使用され、その多様性から多くの形状の加工が可能です。一方、旋盤加工は円筒形の物体を加工するのに適しており、主に直径や内部の穴を精密に加工するのに用いられます。
例えば、自動車のエンジン部品や航空機の部品製造において、これらの加工方法の選択が重要となります。フライス加工で複雑な形状を持つ部品の外形を加工し、旋盤加工で部品の軸や穴の精密加工を行うことで、高度な組み立て精度が要求される製品の製造が可能になります。
このように、フライス加工と旋盤加工はそれぞれ異なる特性を持ち、適用範囲が異なります。正確な適用範囲の理解と選択ポイントの把握により、製造工程の効率化や品質向上に大きく寄与します。日本の製造業においても、これらの加工方法の適切な活用が求められています。
4-3. 加工方法に応じた材料の選択
鉄加工におけるフライス加工と旋盤加工の方法論の違いを理解することは、材料を適切に選択し活用するために非常に重要です。フライス加工は、主に平面や曲面を削るために使用され、高い精度と複雑な形状の加工が可能です。一方、旋盤加工は円筒形の材料を回転させながら、ドリルやバイトで削る方法で、主に円形や筒形の加工に適しています。例えば、自動車のエンジン部品や機械の軸といった部品は旋盤加工によって製造されることが多いですし、ギアや平板などはフライス加工で精密に加工されます。これらの加工方法の違いを理解し、適切な方法で材料を加工することで、耐久性が高く、精度の高い製品を製造することが可能になります。結論として、フライス加工と旋盤加工の違いを把握し、それぞれの長所を活かして材料を選択することが、鉄加工の基本であり、高品質な製品製造の秘訣です。
5. 金属加工における工作機械の基本
5-1. 工作機械とは:旋盤、フライス盤、研削盤
鉄加工には様々な方法がありますが、特に基本とされるのがフライス加工と旋盤加工です。これらは鉄を加工する際に使用される代表的な工作機械であり、それぞれ異なる方法論を持っています。フライス加工とは、回転する刃を用いて鉄に溝や平面を作る加工方法です。一方、旋盤加工は、鉄の材料を回転させながら、固定された刃で削り取ることで形を整える方法です。
例えば、フライス加工は複雑な形状を持つ部品の製造に適しています。自動車のエンジン部品や航空機の部品など、精密な加工が必要な場合に多く用いられます。一方で、旋盤加工は円筒形の部品や、内側や外側を滑らかに仕上げる必要がある場合に特に有効です。たとえば、ボルトやナット、パイプなどがこれに該当します。
これらの違いを理解することは、鉄加工の基本を学ぶ上で非常に重要です。適切な加工方法を選択することで、効率よく高品質な製品を製造することが可能になります。フライス加工と旋盤加工を適切に活用し、日本のものづくりの伝統と革新を支えましょう。
5-2. 工作機械の選択基準と加工適性
鉄加工の世界では、フライス加工と旋盤加工が基本的な技術として広く用いられています。これら二つの方法論はそれぞれ特有の違いがあり、適切に活用することで高い効率と品質を実現できます。フライス加工は、主に平面や曲面を削り出すのに適しており、複雑な形状の部品に対応可能です。一方、旋盤加工は円筒形の物体を加工するのに特化しており、精密な直径の加工が可能です。
例えば、自動車のエンジン部品や機械のギアなど、複雑な形状を持つ部品の加工には、フライス加工が適しています。フライス加工機を用いれば、多様なカットを一つの設定で行うことができ、効率良く精度の高い部品を製造することが可能です。一方で、軸受けやピストンロッドのように、高い円滑性が求められる円筒形の部品には、旋盤加工が最適です。旋盤を使用することで、非常に滑らかな表面を持つ部品を精密に製造することができます。
結論として、鉄加工においてフライス加工と旋盤加工は、それぞれ異なる特性を持ち、部品の形状や加工に求められる精度に応じて適切に選択し活用する必要があります。これらの方法を理解し、適切に用いることで、より高品質かつ効率の良い製品製造が可能となります。
5-3. 工作機械の保守と安全性
鉄加工では、フライス加工と旋盤加工は欠かせない技術です。これら二つの方法論の違いを理解することが、効率的で正確な加工には不可欠です。フライス加工は、主に平面や溝、歯車などの加工に用いられ、刃物が回転することにより材料を削り取ります。一方、旋盤加工は、円形や筒形の物を作る際に用いられ、材料が回転しながら刃物で削り取る方法です。
例えば、フライス加工では、複雑な形状の部品や精密な平面を作ることが可能です。自動車のエンジン部品や機械のフレームなど、精度が求められる部分の加工に役立ちます。対して、旋盤加工は、ボルトやナット、軸など円形の部品を効率よく製造できます。このように、加工方法の選択は製作する部品の形状や用途に深く関わっています。
結論として、フライス加工と旋盤加工は鉄加工の基本中の基本であり、それぞれ独自の特徴と適用範囲があります。この二つの違いを理解し、適切に活用することで、幅広い製品の加工が可能となり、より効率的で高品質な製造が実現します。鉄加工を学ぶ上で、これらの方法論の違いと活用術を掴むことは非常に重要です。
6. 実践!鉄加工でのフライスと旋盤の活用術
6-1. 初心者向けフライス加工のステップバイステップ
フライス加工と旋盤加工は、鉄をはじめとする金属加工において基本的な方法であり、それぞれに違いと独特の活用術があります。これらの違いを理解することは、加工技術を学ぶ上で非常に重要です。
フライス加工は、主に平面や曲面を削り出すために用いられます。この方法では、回転する刃を使って材料を削り取るため、非常に高い精度で複雑な形状を作ることが可能です。例えば、ギアや溝などの加工に適しています。
一方、旋盤加工は、主に円形の材料を加工する際に使用されます。この方法では、材料自体が回転し、刃がその表面を削り取ることで形を形成します。この技術は、ボルトやネジ、シャフトなど、対称的な形状の加工に最適です。
つまり、フライス加工と旋盤加工の主な違いは、加工する材料の回転と刃の動き方にあります。どちらの技術も、製品の品質や生産効率を高めるためには欠かせない技術であり、それぞれの特性を理解し、適切に活用することが重要です。
まとめると、フライス加工と旋盤加工は、加工方法としての違いを持ちつつ、金属加工においてそれぞれ独自の価値を提供します。これらの技術を理解し、適切に活用することで、より高品質な製品の製造が可能になります。
6-2. 初心者向け旋盤加工のステップバイステップ
鉄加工の世界には、フライス加工と旋盤加工という二つの重要な方法があります。これらは金属加工の基本であり、それぞれ独自の利点があります。フライス加工は、主に平面や曲面を削るのに適しており、旋盤加工は円筒形の加工品を作るのに最適です。この違いを理解することが、鉄加工の効率を高める鍵となります。
例えば、自転車のフレームを作成する際、その直線的な部分はフライス加工で、曲がっている部分や軸は旋盤加工で加工されることが多いです。フライス加工では、工作機械の回転するカッターが鉄を削り取り、旋盤加工では、工作物が回転しながら切削ツールで削られます。このような具体的な例を通して、それぞれの加工方法がどのような時に最適かが分かりやすくなります。
結論として、鉄加工を行う際は、加工したい物の形状や特性に最適な方法を選択することが重要です。フライス加工と旋盤加工を適切に活用することで、より高品質で効率的な製品作りが可能となります。
6-3. 加工精度を高めるためのコツとテクニック
鉄加工では、フライス加工と旋盤加工は基本的な技術であり、それぞれに適した使用法があります。これらの違いを理解し、適切に活用することが、加工精度を高めるための重要なポイントです。フライス加工は、主に平面や溝、そして複雑な形状を加工するのに適しています。一方、旋盤加工は円筒形や球形の加工に優れ、特に軸やスリーブなどの部品製作に用いられます。例えば、複雑な平面を持つ部品はフライス加工で、円滑な曲面を持つ部品は旋盤加工で加工すると、効率良く高精度な製品が得られます。このように、フライス加工と旋盤加工をその特性に応じて適切に選択し、活用することが、鉄加工の品質を向上させる鍵となります。再度強調しますが、加工方法の選択と活用によって、鉄加工の精度と効率は大きく変わってきます。
7. 切削加工の安全対策とトラブルシューティング
7-1. 切削加工時の安全管理
鉄加工においてフライス加工と旋盤加工は基本中の基本ですが、その方法論と活用術には大きな違いがあります。フライス加工は主に平面や曲面を削るのに適しており、その多様性から多くの部品製造に欠かせない技術です。一方、旋盤加工は円筒形の材料を加工するのに最適で、精密な円形部品の製造に不可欠です。
例えば、自動車のエンジン部品やギアなどはフライス加工によって平面や複雑な形状が加工され、シャフトやボルトのような円筒形部品は旋盤加工で製造されます。このように、製品の要求する形状や精度に応じて適切な加工方法が選ばれます。
また、最近では、これらの加工技術を組み合わせた複合加工機も登場し、より複雑な形状や高度な精度が求められる部品の生産に対応しています。日本では、精密加工技術の高さが国際的にも評価されており、鉄加工技術の進化は止まることを知りません。
結論として、フライス加工と旋盤加工はそれぞれに特化した役割を持ちながらも、製品製造における互いの補完関係は非常に大きいです。正しい理解と適切な技術の選択が、高品質な製品を生み出す鍵となります。
7-2. よくある問題とその解決策
鉄加工におけるフライス加工と旋盤加工は、それぞれ異なる方法論を持つ重要な技術です。これらの技術を学ぶことは、製品の精度や仕上がりに大きな影響を及ぼします。フライス加工は、主に平面や溝などの加工に使われ、回転する刃を持つ工具で鉄を削り取る方式です。一方、旋盤加工は円形や円筒形の加工に適しており、作業ピースを回転させながら固定した刃で削ることで形状を作り出します。
日本では、これらの加工技術が数多くの製造業で活用されています。例えば、自動車産業ではエンジン部品やシャフトなど、精密な加工が求められる部品製造に旋盤加工が用いられます。フライス加工は、電子機器の基板に穴を開けるなど、細かい作業に重宝されています。
これらの技術の違いを理解し、目的に応じた適切な加工方法を選択することが、高品質な製品を効率良く生産する鍵となります。結論として、フライス加工と旋盤加工は、それぞれ異なる特性を持ち、製造工程において互いに補完しあう存在です。これらの技術をマスターすることで、鉄加工の基本をしっかりと把握し、幅広い製品製造に応用することが可能になります。
7-3. 保守とメンテナンスの重要性
鉄加工の世界では、フライス加工と旋盤加工の違いを理解することが重要です。これら二つの方法論は、鉄の加工技術の基本をなしており、それぞれが異なる利点を持っています。フライス加工は主に平面や曲線、溝などの加工に用いられ、旋盤加工は円筒形の物体の外面や内孔を削る作業に特化しています。
たとえば、フライス加工は、歯車や金型などの複雑な形状を必要とする部品に用いられます。これに対して、旋盤加工は、軸やボルトなどの円形部品の製造に欠かせない技術です。日本の伝統的な技術と緻密な工作機械の発展により、これらの加工技術はさらに洗練されています。
結論として、フライス加工と旋盤加工は鉄加工の不可欠な技術であり、それぞれが独自の役割を持っています。適切な技術の選択は、加工する物の形状や必要な精度に依存します。鉄加工を学ぶ上でこれらの違いを理解し、それぞれの技術を効果的に活用することが、高品質な製品を生み出す鍵となります。
まとめ
鉄加工の基本を学ぶ!フライスと旋盤の方法論としての違いと活用術について、鉄やその他の金属を加工する際には、フライス加工と旋盤加工が用いられます。これらの違いを理解し、それぞれの活用術を習得することが重要です。これにより、効果的な鉄加工が可能となります。
鉄材フライス加工で理解するべきアップカット・ダウンカットの特徴
鉄材のフライス加工を行う際、アップカットとダウンカットの特徴を理解していますか?これらの違いは、作業にどのような影響を与えるのでしょうか?
鉄材フライス加工は、産業界で広く利用されている重要なプロセスの一つです。このプロセスにおいて、アップカットとダウンカットは重要な概念となります。アップカットは素材を削る際に上方向に押し上げるようなカッターの動きを指し、一方でダウンカットは下方向に素材を削り出す動きを表します。
この記事では、鉄材フライス加工において重要なアップカットとダウンカットの特徴に焦点を当て、それぞれが加工品質や効率に与える影響について探求します。さらに、どちらの方法が特定の状況で適しているのか、なぜそれが重要なのかについても詳しく解説します。鉄材のフライス加工におけるアップカットとダウンカットについての理解を深め、効果的な加工技術の習得に役立てていきましょう。
1. フライス加工の基本
1-1. フライス加工とは
フライス加工におけるアップカットとダウンカットの特徴を理解することは、加工品質や効率を大きく左右します。この二つのカット方法は、鉄材加工においてそれぞれ異なる効果を発揮します。アップカット加工では、カッターが材料を持ち上げるように切削するため、切りくずが上方向に排出され、仕上げ面には滑らかさが得られます。これは、比較的薄い材料や、精密な加工が求められる場合に適しています。一方、ダウンカット加工は、カッターが材料を押し込むように切削するため、切りくずが材料に押し込まれることで、加工中の材料の安定性が高まります。これは、厚手の材料や、加工時の材料のずれを防ぎたい場合に有効です。例えば、大きな鉄製の部品を加工する際にダウンカット加工を使用することで、加工精度の向上が期待できます。結論として、アップカットとダウンカットの選択は、加工する材料の特性や加工内容によって最適な方法を選ぶことが重要です。これにより、加工効率と品質の向上が図れるのです。
1-2. 鉄材フライス加工の一般的な用途
鉄材フライス加工において、アップカットとダウンカットの理解は重要です。この二つの方法は加工品質と効率に大きく影響を及ぼします。アップカット加工では、切削工具が回転する際に鉄材を持ち上げるように切削を行うため、切りくずが排出しやすくなります。これにより、比較的クリーンな加工面を得ることができ、特に薄い材料や軽量の部品加工に適しています。一方、ダウンカット加工は、切削工具が鉄材を押し込む形で切削を行うため、材料の固定がしっかりしている必要があります。しかし、この方法は加工面の仕上がりが非常に良く、高い精度を要求される部品の加工に適しています。例えば、高精度を要求される機械部品や工具類の製造において、ダウンカット加工は重要な役割を果たします。結論として、アップカットとダウンカットはそれぞれ特有の利点があり、加工する鉄材の種類や求められる精度、仕上がりに応じて適切に選択することが重要です。
1-3. フライス加工におけるエンドミルの役割
フライス加工では、精密な金属加工技術が求められますが、その中でもエンドミルの選択は絶大な影響を及ぼします。エンドミルにはアップカットとダウンカットの二種類があり、それぞれ特徴を理解することが鉄材加工の効率性と品質向上につながります。アップカットは、工具が回転する際に切削屑を上方に排出するため、切削部の清掃が容易で加工品質が向上します。一方、ダウンカットは切削屑を材料に押し込むため、表面の仕上がりが非常に滑らかになります。たとえば、細かい仕上がりが求められる精密部品には、ダウンカットのエンドミルが適しています。しかし、切削屑の排出性が悪いため、加工時には注意が必要です。結論として、鉄材フライス加工においては、加工品の仕上がりや加工効率を高めるために、それぞれの特徴を理解した上でアップカット・ダウンカットの選択を行うことが重要です。
2. アップカットとダウンカットの理解
2-1. アップカット加工のメカニズム
アップカット加工とダウンカット加工は、鉄材フライス加工において理解するべき重要な概念です。これらの加工法は、加工時の切りくずの排出方向や加工面の仕上がりに大きく影響を及ぼします。
アップカット加工では、カッターが材料を持ち上げるように切り込み、切りくずを上へ排出します。この方法の最大の利点は、切りくずが加工面から離れやすいため、加工面が非常に滑らかになることです。例えば、薄い鉄板を加工する際、アップカット加工を用いることで、鉄板の歪みが少なく、精度の高い加工が可能です。
一方、ダウンカット加工では、カッターが材料を押し下げるように切り込み、切りくずを下へ排出します。これにより、材料が固定されやすく、特に厚い鉄材の加工に適しています。また、ダウンカット加工は、切りくずが加工部分に留まりやすいため、深い切り込みが必要な場合に有効です。
結論として、アップカット加工とダウンカット加工は、それぞれ特有の利点があり、加工する材料の種類や加工の目的によって適切な方法を選択することが重要です。薄い材料や滑らかな加工面を求める場合はアップカット、厚い材料や深い加工を必要とする場合はダウンカット加工が適しています。これらの加工法をうまく選択することで、効率的かつ高品質な鉄材フライス加工を実現できます。
2-2. ダウンカット加工のメカニズム
鉄材のフライス加工におけるアップカットとダウンカットは、それぞれ特有の特徴を持ち、加工の目的や材質に応じて使い分けることが重要です。アップカット加工は、工具が材料を持ち上げながら切削するため、表面がきれいに仕上がりやすいという特徴があります。これは、特に精密な仕上がりが求められる場合や薄い材料の加工に適しています。一方、ダウンカット加工は、工具が材料を押し付けながら切削するため、材料の押し出しが少なく、加工中の材料の安定性が高まります。これは、厚い材質や硬い材質を加工する際に適しており、加工時の振動が少ないため、精度の高い加工が可能です。
例えば、鉄材を用いた精密部品の製造では、ダウンカット加工により、振動を抑えつつ高い精度での加工が求められます。これにより、部品の精度を確保しつつ、生産効率も向上させることができます。また、薄板の加工や複雑な形状の部品製造には、アップカット加工が用いられ、仕上がりの美しさと加工の正確さが求められます。
結論として、鉄材フライス加工におけるアップカットとダウンカットの使い分けは、加工する材料の特性と目指す加工品質によって左右されます。正しい加工方法の選択によって、高品質かつ効率的な製造が可能になり、製品の品質向上に繋がります。それぞれの特徴を理解し、適切に活用することが鍵となります。
2-3. アップカットとダウンカットの違い
鉄材フライス加工において、アップカットとダウンカットの理解は極めて重要です。これらの違いを把握することにより、加工品質を向上させることが可能です。アップカット加工では、カッターの回転方向が材料の送り方向と同じであり、切りくずが上方に排出されます。これは、切削抵抗が少なく、比較的クリーンな切断面を得やすい方法です。一方、ダウンカット加工では、カッターの回転方向が材料の送り方向と反対であり、切りくずが材料に押し込まれる形になります。これにより、加工面が安定し、特に薄い材料や精密な加工が求められる場合に適しています。
例えば、アップカット加工は、大量の切りくずを効率的に排出する必要がある粗加工に適しています。対してダウンカット加工は、表面仕上げが重視される細かい作業や、切りくずの排出方向に配慮が必要な場合に優れた結果を示します。
結論として、加工方法を選択する際には、加工する材料の特性や加工後の品質要求に応じて、アップカットとダウンカットの特徴を理解し適切に適用することが重要です。その理解と適用により、効率と品質の双方で高い成果を達成することができるでしょう。
3. エンドミルの使い分け方
3-1. アップカットエンドミルの特徴と適用
鉄材フライス加工で、アップカットとダウンカットの選択は非常に重要です。それぞれには特有の特徴があり、適切に使い分けることで、加工の効率と品質を大きく改善できます。
アップカット加工では、刃が材料を持ち上げるように削り取るため、切りくずが上方向に排出されます。これにより、加工面が非常にクリーンに仕上がるという利点があります。特に、深い溝やポケット加工をする際に、切りくずが詰まりにくく、加工精度を高めることができます。
一方、ダウンカット加工は、刃が材料を押し付けながら削るため、切りくずが材料の間に留まりやすくなります。しかし、この方法は切断面を滑らかに保つことができるため、外観が重視される部品の加工に適しています。例えば、見える面にキズやバリが許されない装飾品や外装部品の加工に使用されます。
結論として、アップカットは切りくずの排出性と加工精度が重視される場合に適しており、ダウンカットは加工面の仕上がりが重要な場合に最適です。加工物の要求仕様に応じて、これらの特性を理解し、適切に選択することが、高品質な製品を効率的に生産する鍵となります。
3-2. ダウンカットエンドミルの特徴と適用
フライス加工において、アップカットとダウンカットはそれぞれ独特の機能を持ち、加工品質や効率を左右します。特に、ダウンカットエンドミルは、その特徴を理解し適切に適用することで、加工の精度を高めることができます。ダウンカットエンドミルは、切削時に加工面へ向かって力を加えるため、材料の押し潰しを防ぎながら、きれいで滑らかな表面仕上げを実現します。この特性は、特に鉄材のような硬い材料を加工する際に有効です。例えば、精密な外観が求められる部品や、薄い材料の加工において、ダウンカットエンドミルは優れた結果をもたらします。しかし、ダウンカットエンドミルを使用する際は、材料の種類や加工条件に注意し、適切な切削速度と送り速度を選定することが重要です。適用を誤ると、加工品質に影響を与える可能性があります。結論として、ダウンカットエンドミルの特色を十分に理解し、適切に適用することで、鉄材のフライス加工においても高い加工精度と優れた表面仕上げを達成することができます。
3-3. 材料と加工方法に応じたエンドミルの選択
鉄材のフライス加工において、正しいエンドミルの選択は非常に重要です。特に、アップカットとダウンカットは加工品質に大きく影響を与えるため、その特徴を理解することが必要です。アップカット加工では、カッターが材料を持ち上げながら切削するため、切削抵抗が少なく、仕上がりがきれいになります。この方法は、特に薄い材料や精密な加工が求められる場合に適しています。一方で、ダウンカット加工では、カッターが材料を押し付けながら切削するため、加工面に対する押し付け力が大きくなり、材料が安定して加工できます。これは、厚い材料や荒加工に適している方法です。つまり、加工する材料の種類や加工の目的に応じて、アップカットとダウンカットのどちらを選択するかが重要です。例えば、精密な仕上がりが求められる場合はアップカット、材料の安定した加工が必要な場合はダウンカットを選ぶと良いでしょう。結論として、鉄材のフライス加工では、加工品質を高めるためには、アップカットとダウンカットの特徴を理解し、目的に応じて適切な加工方法を選択することが大切です。
4. 溝フライス加工の方法
4-1. 溝フライス加工の基本手順
鉄材のフライス加工において、アップカットとダウンカットの理解は非常に重要です。フライス加工とは、切削工具を回転させて材料から削り取る加工方法のことで、アップカットとダウンカットはその切削方法の違いによる特徴です。
アップカット加工では、切削工具が材料を持ち上げるように削り取ります。これは、切りくずの排出が良好であるため、加工精度が高くなりやすいという利点があります。一方、ダウンカット加工では、切削工具が材料を押し付けながら削り取るため、材料の固定が固く、表面仕上げが良好になる傾向があります。
例えば、鉄材の薄い板を加工する場合、アップカット加工を用いると切りくずの排出がスムーズに行われ、繊細な加工が可能です。しかし、より精密な表面仕上げが求められる場合は、ダウンカット加工が適しています。
結論として、鉄材のフライス加工におけるアップカットとダウンカットは、それぞれに独特の特徴があり、加工する材料の種類や求められる加工精度に応じて適切な方法を選択することが重要です。理解と適切な適用により、より良い加工結果を得ることができるでしょう。
4-2. アップカットとダウンカットを利用した溝加工の違い
アップカットとダウンカットの選択は、鉄材フライス加工の品質と効率に大きく影響します。アップカット加工は、工具が材料を持ち上げながら切削する方法で、切削時の材料の引っ張りを生じさせます。これにより、切削面が滑らかに仕上がり、特に精密な加工が必要な場合に適しています。一方、ダウンカット加工は、工具が材料を押し込みながら切削するため、材料を固定する力が強く、加工中の材料の動きが少なくなります。これは、大きな切削力が必要な作業や、材料の変形を最小限に抑えたい場合に適しています。
例えば、薄い金属板の加工ではアップカットを使うと、材料が引っ張られることで板が歪む可能性があります。しかし、ダウンカットを使用すれば、押し込む力によって材料が安定し、歪みが少なくなります。反対に、精密な表面加工が求められる場合は、アップカットがスムーズな仕上がりを提供します。
結論として、鉄材フライス加工においては、加工する材料の特性や、求められる仕上がりに応じてアップカットとダウンカットを適切に選択することが重要です。それぞれの方法の特徴を理解し、具体的な加工例を参考にすることで、より高品質かつ効率的な加工が可能になります。
4-3. 溝加工における注意点とコツ
鉄材フライス加工では、アップカットとダウンカットの選択は非常に重要です。それぞれが持つ特徴を理解することで、加工精度や仕上がりの質を高めることができます。アップカット加工は、フライスの回転方向が工件の送り方向と同じで、切りくずを上方に排出するため、切りくずの処理が容易というメリットがあります。例えば、溝加工時には、アップカットを使用することで、切りくずが加工部分に詰まることなく、スムーズな加工が可能です。一方、ダウンカット加工は、フライスの回転と工件の送り方向が逆で、表面が非常に滑らかに仕上がるという特徴があります。これは、アップカット加工で起こりやすい表面の毛羽立ちを抑える効果があるため、見た目が重要な部品の加工に適しています。
結論として、アップカット加工は切りくずの処理が容易で、内部の精密な加工に適しています。一方で、ダウンカット加工は表面の仕上がりを重視する場合に優れた選択です。鉄材フライス加工においては、これらの特徴を理解し、適切な方法を選択することが、高品質な製品製造の鍵となります。
5. フライス加工の適切な会社選び
5-1. 加工品質を左右する会社選びのポイント
フライス加工において、鉄材の加工品質を大きく左右する要素のひとつが、アップカットとダウンカットの使用方法です。適切な方法を選択することで、加工精度や仕上がりの美しさが大きく向上します。アップカットとは、カッターが材料を持ち上げるように切削する方法で、特に薄い材料や軽量の材料に適しています。一方、ダウンカットはカッターが材料を押し付けながら切削する方法で、より厚い材料や重量のある材料に適しているとされます。
例えば、鉄材のフライス加工で薄い板材を加工する際にアップカットを用いれば、材料の振動を抑えつつスムーズに切削でき、加工面の仕上がりが良くなります。一方で、厚い鉄板を加工する場合にはダウンカットを選択することで、加工中の材料の安定性が向上し、より精度の高い加工が可能になります。
結論として、鉄材フライス加工においては、アップカットとダウンカットの特徴を理解し、加工する材料の種類や形状に応じて最適な方法を選択することが重要です。これにより、加工品質の向上だけでなく、加工効率の向上にも寄与することができます。選択を誤ると加工品質が低下する可能性があるため、フライス加工を行う際は、これらの点を十分に考慮する必要があります。
5-2. 実績と評判を考慮した会社選び
鉄材のフライス加工において、アップカットとダウンカットの理解は重要です。アップカット加工では、カッターが材料を持ち上げながら切削するため、仕上がりがきれいになりやすく、特に薄い材料や不安定な固定状態の材料の加工に適しています。一方、ダウンカット加工は、カッターが材料を押し下げながら切削するため、材料が固定台に強く押し付けられ、材料のズレが少なくなります。これは、厚い鉄材や硬い材料の加工に有利です。例えば、アップカット加工は精密な電子部品の基板加工に、ダウンカット加工は建築用の厚手の鉄板加工によく使用されます。結論として、鉄材のフライス加工を行う際は、加工する材料の特性と加工目的に応じて、アップカットかダウンカットのどちらを使用するかを選択することが重要です。
5-3. アフターサービスとサポートの重要性
鉄材フライス加工では、アップカットとダウンカットの理解が不可欠です。フライス加工とは、切削工具が回転しながら鉄材などの被削材を削る加工方法です。この加工方法において、アップカットとダウンカットは、それぞれ特徴があり、適切に使い分けることが重要です。
アップカット加工では、工具の回転方向と送り方向が同じであり、切削屑を上方に排出します。この方法の利点は、切削屑が作業領域から効率良く除去されるため、切削部の清潔さを保ちやすく、加工精度の向上に寄与する点です。特に、深い溝の加工や複雑な形状の加工に適しています。
一方、ダウンカット加工では、工具の回転方向と送り方向が反対であり、切削屑が加工面に押し込まれます。これにより、加工面の仕上がりが非常に滑らかになり、特に外観が重要視される部品の加工に適しています。しかし、切削屑の処理が難しくなるため、加工環境の管理が重要となります。
結論として、鉄材フライス加工において、アップカットとダウンカットはそれぞれにメリットとデメリットがあります。加工する部品の要求仕様や加工環境を考慮し、どちらの加工方法を選択するかを判断することが、高品質な製品製造に繋がります。適切な加工方法の選択によって、加工効率の向上や製品の品質向上を実現することができます。
まとめ
鉄材のフライス加工では、アップカットとダウンカットの特徴を理解することが重要です。アップカットは切削刃が材料に対して上方向に向かって進む切削方法であり、切りくずを上方に排出します。一方、ダウンカットは切削刃が材料に対して下方向に進む切削方法であり、切りくずを下方に排出します。これらの特徴を理解することで、適切な切削方法を選択し、効率的な加工を行うことができます。
「鉄加工入門:フライス加工と旋盤加工の特徴と選び方」
鉄加工という分野は、多くの人にとって専門的かつ興味深い領域です。金属を切削し形作るフライス加工と旋盤加工は、鉄加工の基本的な方法として広く知られています。この記事では、初心者の方でも理解しやすいように、フライス加工と旋盤加工の特徴や選び方について解説していきます。鉄加工におけるこれらの違いを理解することで、自分に最適な加工方法を選ぶ手助けとなるでしょう。さあ、鉄加工の世界への扉を開いてみましょう。
1. 鉄加工入門とは
1-1. 鉄加工の基本
鉄加工の世界では、フライス加工と旋盤加工は基本中の基本とされています。これらの加工方法は、鉄を含む多くの金属の形状を変えるために用いられますが、それぞれ特徴があり、選び方が重要です。フライス加工は、主に平面や溝、複雑な形状を削り出すのに適しています。具体的な例としては、ギアやフレーム加工などが挙げられます。一方、旋盤加工は円形や円筒形の部品を作るのに最適で、ネジや軸などがこれに該当します。
選び方のポイントは、加工したい部品の形状や必要な精度、量産性を考慮することです。例えば、複雑な形状を少量生産する場合はフライス加工が向いていますが、円形の部品を高精度で大量に生産する必要がある場合は、旋盤加工が適しています。このように、フライス加工と旋盤加工はそれぞれに特化した用途があり、適切に選択することが重要です。
結論として、鉄加工におけるフライス加工と旋盤加工は、それぞれ独特の特徴を持ち、加工する部品の形状や生産性に応じて選択することが肝心です。正しい選択をすることで、効率的かつ高品質な部品製造が可能となります。
1-2. 切削加工の役割と重要性
フライス加工と旋盤加工は、鉄加工の世界において非常に重要な技術です。どちらも金属を削り、形を整えるために用いられますが、それぞれに特徴があり、適した用途が異なります。結論から言うと、フライス加工は平面や複雑な形状の加工に適しており、旋盤加工は円筒形の物を加工するのに最適です。
理由としては、フライス加工は刃が回転し、その刃によって材料の表面を削り取る方法です。これにより、非常に精密な平面加工や、複雑な形状の加工が可能になります。例えば、歯車の加工などがフライス加工の代表的な用途の一つです。一方、旋盤加工は材料自体を回転させ、固定された切削工具で材料の表面を削り取る方法です。これにより、非常に滑らかな表面を持つ円筒形の物を効率良く加工できます。例えば、針金やボルトの加工が旋盤加工でよく行われます。
結論として、フライス加工と旋盤加工はそれぞれ異なる特徴を持ち、加工したい物の形状や求められる精度に応じて選ばれるべきです。どちらも鉄加工の基本であり、それぞれの技術を理解し適切に選択することが、高品質な製品を作り出す鍵となります。
1-3. 切削加工に適した鉄の特性
鉄はその優れた加工性と多様な用途から、機械部品の製造において広く用いられています。特に、フライス加工と旋盤加工は鉄の加工に適した代表的な方法です。フライス加工は複雑な形状や平面を加工するのに適しており、旋盤加工は円筒形の部品を効率良く加工できます。
例えば、フライス加工はギアやフレームの製造に適している一方で、旋盤加工はシャフトやボルトなどの製造に最適です。これらの加工方法を選ぶ際は、製造したい部品の形状と加工精度を考慮する必要があります。
結論として、フライス加工と旋盤加工はそれぞれに独特の特徴を持ち、製造したい部品の要件に応じて適切に選択することが重要です。鉄の加工を行う際には、これらの加工方法の特徴を理解し、目的に合った加工技術を選ぶことで、効率的かつ高品質な製品製造が可能になります。
2. 旋盤加工の基礎
2-1. 旋盤加工とは
旋盤加工は、鉄を含む様々な材料を加工するための一般的な方法です。この加工技術の特徴は、回転する材料に対して切削工具を進めることで、円筒形の部品を製造することにあります。旋盤加工は、非常に精密な作業が可能で、特に円形や筒形の部品製造に適しています。たとえば、自動車や機械の部品など、日常生活でよく使用される製品の加工に用いられることが多いです。しかし、複雑な形状や多面体の加工には向いておらず、こうした場合にはフライス加工が選ばれることがあります。フライス加工では、回転する工具を用いて材料を削り取るため、旋盤加工よりも多様な形状を作り出すことが可能です。選択する加工方法は、製造したい部品の形状や精度、製造コストなど、様々な要素を考慮して決定されます。結論として、旋盤加工は円筒形の部品製造に適しており、フライス加工はより複雑な形状の加工に向いています。正しい加工方法の選択は、高品質な製品製造の鍵となります。
2-2. 旋盤加工の主な用途
旋盤加工は、円形の金属部品を作成するのに特に適しています。この加工方法の利点は、精密な円形部品を効率的に製造できる点にあります。例えば、自動車のエンジン部品や電子機器のコネクターといった、精度が求められる部品の加工によく使用されます。旋盤加工を選ぶ主な理由は、その高い精度と加工の柔軟性にあります。具体的な例として、円筒形や円錐形の部品を作る場合、旋盤加工を活用することで、均一で滑らかな表面を持つ部品を効率的に生産できます。このように、旋盤加工は特定の形状を持つ部品の製造において、その適性と有効性を発揮します。結論として、旋盤加工は精密な円形部品を必要とする様々な産業で重要な役割を果たしており、選択する際には、加工したい部品の形状や精度を考慮することが重要です。
2-3. 旋盤加工の特徴とメリット
フライス加工と旋盤加工は、鉄加工の重要な方法であり、それぞれが特有の特徴と利点を持っています。旋盤加工は、主に円形の材料を加工する際に使用される技術で、精密な円筒形の部品製作に適しています。この加工方法の最大のメリットは、その高い精密度と仕上がりの良さにあります。例えば、自動車のエンジン部品や時計の部品など、細かい仕上がりが求められる製品の製作において、旋盤加工は不可欠です。
一方、フライス加工は、平面や曲面などの加工を可能にする多様性が特徴です。この方法では、カッターを回転させながら材料を動かすことで、様々な形状を創出することができます。フライス加工は、複雑な形状や大きな部品の加工に特に適しており、例としては航空機の部品や機械のフレームなどが挙げられます。
結論として、旋盤加工は精密な円筒形部品の製作に、フライス加工は複雑または大きな部品の加工に適しています。どちらの加工方法を選ぶかは、製作したい部品の形状や要求される精度によって異なります。したがって、加工したい部品の特性を正確に理解し、目的に合った加工方法を選択することが重要です。
3. フライス加工の基礎
3-1. フライス加工とは
フライス加工と旋盤加工は、鉄加工における最も基本的な技術の二つです。これらの加工方法を理解することは、適切な加工方法を選ぶ上で非常に重要です。まず結論から述べると、フライス加工は複雑な形状や平面を作るのに適しており、旋盤加工は円筒形の加工に最適です。フライス加工は、回転するカッターを用いて材料を削り取る加工方法で、直線や曲線など様々な形状を作り出すことができます。例として、歯車や溝の加工が挙げられます。一方、旋盤加工は回転する材料に対して、固定された切削工具を用いて形状を作る方法で、主に円筒形の加工に使用されます。例えば、軸やピンの製作に適しています。このように、加工する製品の形状や必要とする精度に応じて、フライス加工と旋盤加工のどちらを選ぶかが決まります。最終的には、これらの特徴を理解し、具体的な加工ニーズに合わせて最適な方法を選択することが、効率的で品質の高い鉄加工を実現する鍵です。
3-2. フライス加工の主な用途
フライス加工と旋盤加工は、鉄をはじめとする金属加工に欠かせない技術です。これらの加工方法を選ぶ際には、それぞれの特徴を理解することが重要です。フライス加工は、主に平面や曲面、溝などを削り出すのに適しています。具体的な例としては、機械の部品や歯車などの加工に用いられます。一方、旋盤加工は、主に円筒形の物体を削るのに適しており、針や軸など、回転対称の形状を持つ部品の製造に最適です。
選び方の基準としては、加工したい物の形状が最も大きなポイントになります。平面や複雑な形状を加工したい場合はフライス加工を、円筒形や回転体を加工したい場合は旋盤加工を選ぶと良いでしょう。日本では、高精度な加工が求められる場合が多く、これらの加工技術を駆使して世界に誇る製品が数多く生み出されています。
まとめると、フライス加工と旋盤加工は、それぞれ異なる特徴を持ち、加工する物の形状によって適した選択をすることが重要です。日本の高度な技術力によって、これらの加工方法はさまざまな分野で活用されています。
3-3. フライス加工の特徴とメリット
フライス加工と旋盤加工は、鉄や他の金属の加工に不可欠な技術です。これら方法の選択は、作業の特性によって異なります。フライス加工は、主に平面や溝、複雑な形状を削るのに適しています。これは、回転する工具が材料を削り取ることで行われます。旋盤加工は、円筒形の作業物を加工する際に選ばれ、材料を回転させながら工具で削る方式です。例えば、フライス加工は機械部品のキーウェイやギヤなどを作るのに用いられ、旋盤加工はシャフトやボルトの製造に最適です。
選択肢について、フライス加工はその多様性により、複数の面を一度に加工できる点で高い柔軟性を持ちます。一方で、旋盤加工は円筒形の物体を効率的に加工でき、特に長さのある部品加工に適しています。したがって、加工したい部品の形状や必要な精度、生産量を考慮して適切な加工方法を選ぶことが重要です。
結論として、フライス加工と旋盤加工はそれぞれ異なる特徴を持ち、選択は加工したい物の形状や性質に依存します。各加工法の理解と適切な選択は、効率的で質の高い製品を作るために不可欠です。
4. 旋盤加工とフライス加工の違い
4-1. 加工方法の違い
フライス加工と旋盤加工は、鉄加工において基本となる二つの方法で、それぞれが持つ特徴を理解することが重要です。フライス加工は、主に平面や曲面を削るのに適しており、複雑な形状でも加工が可能です。一方、旋盤加工は、円筒形の材料を高速で回転させながら削ることで、主に円形や筒形の部品製造に用いられます。
たとえば、フライス加工を用いれば、ギアやカムのような複雑な部品も精密に作成できます。一方で、旋盤加工は、ボルトやシャフトなど、直線や円形のシンプルな形状の加工に適しています。このように、加工したい部品の形状や精度によって、フライス加工と旋盤加工のどちらを選ぶかが決まります。
結論として、フライス加工は複雑な形状の加工に、旋盤加工は円形や直線形状の部品製造に適しています。それぞれの特徴を理解し、目的に応じて適切な加工方法を選ぶことが、効率的かつ高品質な鉄加工の鍵となります。
4-2. 用いられる工作機械の違い
フライス加工と旋盤加工は、鉄加工の分野において重要な技術です。その選び方を理解することは、効率的かつ効果的な製品作りに欠かせません。フライス加工は、主に平面や曲面などの複雑な形状を削り出すのに適しています。一方、旋盤加工は、円筒形の物体を加工する際に主に用いられます。
たとえば、フライス加工は、自動車のエンジン部品や航空機の部品製造に使われることが多く、高い精度が要求される複雑な形状の加工が可能です。これに対して、旋盤加工は、ボルトやナットなどの比較的シンプルな形状の製品を効率良く加工するのに適しており、製品の量産に役立ちます。
したがって、製品の形状や用途に応じて、フライス加工と旋盤加工のどちらを選ぶかを決定することが重要です。複雑な形状を持つ製品を製造する場合はフライス加工が、円筒形の部品を大量に生産する場合は旋盤加工が適しています。適切な加工方法を選ぶことで、製品の品質を保ちながら、生産効率を高めることができるのです。
4-3. 適用される製品の違い
フライス加工と旋盤加工は、鉄加工の世界でよく使われる二つの基本技法です。どちらも金属加工に欠かせない方法ですが、適用される製品や加工方法には大きな違いがあります。フライス加工は平面や曲面を削るのに適しており、旋盤加工は円形や円筒形の加工に適しています。たとえば、自動車のエンジン部品や工業用ギアなど、精密な平面が必要な製品はフライス加工で、ネジやボルトのような円筒形の部品は旋盤加工で作られることが多いです。
これらの技術を選ぶ際は、加工したい製品の形状をよく考えることが重要です。複雑な形状や特殊な加工が必要な場合は、フライス加工が適しているかもしれません。一方で、長さがあり、回転体の加工が必要な製品は、旋盤加工が得意とする領域です。また、コストや加工時間も考慮に入れる必要があります。フライス加工は複雑な加工が可能ですが、設備投資や時間がかかる場合があります。旋盤加工は比較的シンプルな加工なので、効率よく製品を作ることができます。
結論として、フライス加工と旋盤加工はそれぞれ特有の特徴があり、適用される製品によって選ばれるべき技術です。加工したい製品の形状や必要な加工の種類、コストなどを考え合わせ、最適な加工方法を選択することが重要です。
5. 切削加工における材料の選び方
5-1. 鉄とステンレスの切削性
フライス加工と旋盤加工は、鉄加工の世界で非常に基本的かつ重要な技術です。適切な加工方法を選択することは、製品の品質や生産効率に直結します。フライス加工は、主に平面や曲面を加工するのに使用され、その多様性により複雑な形状も実現可能となります。一方、旋盤加工は、円筒形状の材料を加工する際に適しており、高い精度で滑らかな表面を実現します。
たとえば、フライス加工では、自動車のエンジンブロックや航空機の部品など、精密な平面や溝が必要な場合に使用されます。対照的に、旋盤加工は、ボルトやシャフトなど、円形の部品作成に適しています。
最終的に、フライス加工と旋盤加工のどちらを選択するかは、加工したい製品の形状や必要な精度、生産量によって異なります。フライス加工は複雑な形状や大量生産に適している一方で、旋盤加工は円形部品の高精度な加工に優れています。適切な加工方法を選択することで、高品質の製品を効率良く生産することが可能となります。
5-2. 材料による加工の違い
フライス加工と旋盤加工は、鉄加工の中でも特に重要な技術であり、それぞれに独特の特徴と適用範囲があります。この二つの加工方法の選択は、製作する製品の形状や精度、そして生産性に大きく影響します。
まず、フライス加工は主に平面や曲面、溝などの加工に適しており、非常に高い精度で複雑な形状を作り出すことが可能です。たとえば、自動車のエンジン部品や航空機の部品製造に多く使われます。一方、旋盤加工は軸や円筒形の部品を製造するのに適しており、比較的単純な形状でも高速で大量生産が可能です。この方法では、ボトルのような形状やネジのような細長い部品が効率良く作られます。
したがって、製品の要求される形状や精度、生産量を考慮した上で、これら二つの加工方法のいずれか、または両方を適切に選択することが重要です。例えば、複雑な形状で精度が求められる場合はフライス加工が、単純な形状で大量生産を目指す場合は旋盤加工が適しています。
最終的に、フライス加工と旋盤加工はそれぞれに異なる特徴を持ち、製品の仕様に応じて最適な方法を選ぶ必要があります。適切な加工方法を選択することで、製品の品質向上と生産効率の最大化が実現可能となります。
5-3. 最適な材料の選び方
鉄加工で重要なのは、適切な加工方法を選ぶことです。フライス加工と旋盤加工は、それぞれ特徴があります。フライス加工は、複雑な形状や平面を加工するのに適しており、旋盤加工は円形や筒形の加工に優れています。例えば、フライス加工は歯車やキー溝の加工に用いられ、旋盤加工は軸やリングのような部品の加工に適しています。選び方のポイントは、加工したい部品の形状や精度、量産性を考慮することです。結論として、フライス加工は複雑な形状の加工に、旋盤加工は円形や筒形の部品加工に適しており、加工内容に応じて最適な方法を選ぶことが重要です。
6. 工作機械の種類とその特徴
6-1. 旋盤の種類と特徴
フライス加工と旋盤加工は、鉄加工の世界において基本かつ不可欠な技術です。それぞれが持つ特徴を理解し、適切に選び取ることが重要です。まず結論から言いますと、フライス加工は複雑な形状の加工に優れており、旋盤加工は円形や筒形の加工に特化しています。
フライス加工では、回転する刃を用いて材料を削り取ります。これにより、平面や曲面、溝など、様々な形状を作り出すことが可能です。例えば、ギアやカムなどの精密部品の製造に適しています。
一方、旋盤加工は、材料を回転させながら固定された刃で削り取る方法です。この技術は、シャフトやボルトといった円形や筒形の部品を加工するのに最適です。特に、精度が要求される部品の製造には欠かせません。
結論として、フライス加工と旋盤加工は、それぞれ特有の長所を持ち、使用する目的に応じて選択することが大切です。自分のプロジェクトや製造したい製品の要件をよく理解し、それぞれの加工技術の特徴を活かすことが、効率的かつ高品質な製品を生み出す鍵となります。
6-2. フライス盤の種類と特徴
フライス加工と旋盤加工は、鉄をはじめとする金属加工において欠かせない技術です。これらの加工方法を適切に選択することで、製作物の精度と効率が大きく向上します。フライス加工は主に平面や曲面を削るのに用いられ、旋盤加工は円筒形の加工に適しています。例えば、フライス加工は航空機の部品や自動車のエンジンの部品製造に、旋盤加工はボルトやナット、軸などの製造に多く用いられます。このように、加工する物の形状や必要な精度、生産量に応じてフライス加工と旋盤加工を選択することが重要です。結論として、フライス加工と旋盤加工はそれぞれ特徴があり、製品の要求に応じて適切な加工方法を選ぶことが、高品質な製品を効率的に生産する鍵となります。
6-3. その他の工作機械と比較
フライス加工と旋盤加工は、鉄加工の中でも特に重要な技術です。これらの加工方法を理解し、適切に選択することが、製品の品質向上に直結します。フライス加工は、主に平面や溝を削るのに適しており、旋盤加工は円形や筒形の加工に適しています。例えば、フライス加工はギアや平面の加工に、旋盤加工はシャフトやボルトの加工に用いられます。
フライス加工は、刃が回転することで材料を削り取る加工法です。これに対し、旋盤加工では材料が回転し、固定された切削工具で材料を削り取ります。そのため、フライス加工は複雑な形状や平面を加工しやすく、旋盤加工は円筒形の物を加工するのに適しています。
適切な加工方法を選択するには、加工したい製品の形状や要求される精度を考慮する必要があります。たとえば、複雑な形状の部品を製作する場合はフライス加工が向いているかもしれませんし、円形の部品には旋盤加工が適しているでしょう。
結論として、フライス加工と旋盤加工はそれぞれ異なる特徴を持ち、製品の要求に応じて選択することが重要です。適切な加工方法を選ぶことで、製品の品質向上につながります。どちらの加工技術も日本において長年にわたり培われてきた技術であり、多くの製品の製造に欠かせない存在です。
7. 金属切削加工の方法と応用
7-1. 旋盤加工の具体的な方法
フライス加工と旋盤加工は、鉄加工の中でも特に重要な技術であると言えます。これら二つの加工方法はそれぞれ独自の特徴を持ち、適用すべき場面が異なります。まず、旋盤加工は主に円形の物体を加工する際に用いられます。これに対して、フライス加工はより複雑な形状や平面を削り出すのに適しています。
たとえば、ボルトやナットなどの円筒形の部品を製造するときには旋盤加工が選ばれます。一方、歯車や機械部品のように、平面や複雑な形状を必要とする物にはフライス加工が用いられます。
選択の際には、加工したい物の形状や精度、そして生産量も考慮する必要があります。旋盤加工は比較的単純な形状でも高精度を実現でき、少量生産にも向いています。一方、フライス加工は複雑な形状も可能であり、大量生産にも対応できる柔軟性を持ちます。
結論として、鉄加工を行ううえでフライス加工と旋盤加工は欠かせない技術です。その選択は、加工したい物の特性をよく理解し、その用途に最適な方法を選ぶことが重要です。適切な加工方法の選択によって、効率よく、高品質な製品を生産することができます。
7-2. フライス加工の具体的な方法
鉄加工において、フライス加工と旋盤加工はそれぞれ独自の特徴を持ちます。適切な加工方法を選ぶことで、効率良く高品質な製品を作り出すことが可能です。フライス加工は、主に平らな面や溝、複雑な形状を加工するのに適しています。この加工方法は、回転する工具を用いて材料から削り取ることで形状を作り出します。例えば、自動車のエンジンブロックや電子機器の基盤など、精密な部品製造に広く用いられています。
一方、旋盤加工は円形や筒形の物体を加工するのに特化しています。材料を回転させながら、固定された切削工具で削ることで形状を整えます。この方法は、ボルトやネジ、ピストンなどの部品作りに適しています。
それぞれの加工方法は特定の用途に最適化されており、製品の要求に応じて選択することが重要です。フライス加工は複雑な形状や平面加工に、旋盤加工は円形の部品加工に最適です。正しい加工方法を選ぶことで、高品質な製品を効率良く生産することが可能になります。
7-3. 金属切削加工の応用例
鉄加工の世界には様々な技術がありますが、特にフライス加工と旋盤加工はその基本とされています。これら二つの加工方法の選び方を理解することが、効率的かつ質の高い製品製造への鍵となります。
フライス加工は、主に平面や曲面を削る作業に適しています。多様な形状のカッターを使用できるため、複雑な形状の加工が可能です。例えば、歯車の製造などに使われます。一方、旋盤加工は、回転する材料に刃物を当てて形状を削り出す方法で、円筒形やテーパー形の加工に適しています。バットのような形状やネジ山の加工に用いられることが多いです。
どちらの加工方法を選ぶかは、製品の要求される形状や精度、製造コストなどに依存します。フライス加工は複雑な形状でも対応可能ですが、設備や技術が高価であることが多いです。旋盤加工は比較的シンプルな形状の加工に向いており、コストが低い傾向にあります。
結論として、フライス加工と旋盤加工はそれぞれに特徴があり、製品の要求に応じて適切な方法を選ぶことが肝心です。どちらも重要な加工技術であり、日本の鉄加工業界ではこれらを駆使して高品質な製品が生産されています。適切な技術選択により、効率的かつ経済的な製造が可能となるのです。
8. 切削加工のための工具選び
8-1. 旋盤加工用工具の種類
フライス加工と旋盤加工は、鉄加工の基本的な方法であり、どちらを選択するかは加工したい物の形状や精度によって異なります。フライス加工は平面や曲面の加工に適しており、複雑な形状も作り出せる特徴があります。一方、旋盤加工は円筒形の加工品を作るのに適しており、特に精度の高い円形部品の加工には欠かせません。たとえば、フライス加工は自動車のエンジンブロックやギアなど、旋盤加工はボルトやシャフトなど、それぞれが得意とする分野があります。選択する際には、加工したい物の形状や必要な精度を考慮し、それぞれの加工方法の特徴を理解することが大切です。フライス加工と旋盤加工を正しく選択し適用することで、求める品質と効率の良い鉄加工が可能となります。
8-2. フライス加工用工具の種類
鉄加工の世界では、フライス加工と旋盤加工が基本的な加工方法として広く利用されています。これら二つの加工方法は、鉄を形成する際の特徴と選び方を知ることで、より効率的で質の高い製品を作り出すことが可能です。
まず、フライス加工の特徴は、主に平面や曲面を加工するのに適している点です。この方法では、回転する刃を使用して鉄を削り取るため、非常に高い精度で複雑な形状を作り出すことができます。例えば、機械部品の溝や階段状の形状など、細かいディテールが求められる場合に適しています。
一方、旋盤加工は円筒形の物体を加工するのに特化しています。この加工では、材料を回転させながら刃を当てることで、材料を削り取っていきます。そのため、ボルトやナットなどの円形の部品や、筒形の部品の加工に最適です。
結論として、フライス加工と旋盤加工はそれぞれ異なる特性を持ち、使用するシチュエーションによって適した方法を選ぶ必要があります。加工したい物の形状や細部の要求に合わせて、これらの加工方法を適切に選択することが、製品の品質向上に繋がります。
8-3. 工具選びのポイント
フライス加工と旋盤加工は、鉄をはじめとする金属加工において非常に重要な技術です。これら二つの加工方法の理解と選択は、製品の品質や効率を大きく左右します。まず、フライス加工は、回転する多刃のカッターを使い、被加工物に対して主に平面や溝を削り出す工程です。これに対して旋盤加工は、被加工物を回転させ、切削工具で材料を削り取り形状を整えていく工程です。
例えば、円筒形の部品や複雑な曲面が必要な場合は旋盤加工が適しています。一方で、平面や角のある部品、溝が必要な場合にはフライス加工が効果的です。
正しい加工方法の選択は、加工品の精度を高めるだけでなく、製造コストの削減にもつながります。例えば、旋盤で加工すべき部品をフライス加工で無理に加工しようとすると、時間がかかったり品質が落ちたりすることがあります。
結論として、フライス加工と旋盤加工はそれぞれに特徴があり、使い分けることが非常に重要です。加工する部品の形状や必要な精度を考慮し、適切な加工方法を選択することで、効率的で高品質な製品製造が可能になります。
9. 加工精度を左右する要因
9-1. 機械の精度とその影響
フライス加工と旋盤加工は、鉄加工の分野でよく利用される二つの主要な方法です。これらの加工方法を適切に選ぶことが、製品の品質に大きく影響します。フライス加工は、主に複雑な形状を持つ部品や、平面、溝、ギアなどの加工に適しています。一方で、旋盤加工は、円筒形や円錐形など、回転対称の部品を加工するのに特に適しております。
たとえば、自動車のホイールやギアの製造には、フライス加工がよく用いられます。これらの部品は、複雑な形状と高い精度が求められるためです。一方、釣り竿のハンドルや木工品の脚など、細長い部品の加工には旋盤加工が選ばれることが多いです。これらの例からも分かるように、加工する部品の形状や要求される精度によって、フライス加工と旋盤加工のどちらを選ぶかが決まります。
結論として、フライス加工と旋盤加工はそれぞれ異なる特徴を持ち、用途によって選択する必要があります。部品の形状や必要な精度を考慮して、最適な加工方法を選ぶことが、高品質な製品を製造する鍵となるのです。
9-2. 切削条件の設定
フライス加工と旋盤加工は、鉄加工の基本中の基本と言えます。これらを選ぶ際は、それぞれの特徴を理解することが重要です。フライス加工は、平面や曲面を削るのに適しており、複雑な形状や溝の加工に優れています。一方、旋盤加工は、円筒形の物を加工する際に特に有効で、直径や長さの精密な調整が可能です。
たとえば、フライス加工は、自動車のエンジン部品など、精密な平面が必要な部品に使われます。旋盤加工は、ボルトやナットのような円筒形の部品の加工に広く用いられています。
選択する際のポイントは、加工したい部品の形状と必要な精度です。複雑な形や精密な溝が必要な場合はフライス加工、円筒形の部品には旋盤加工が適しています。最終的に、それぞれの加工方法を理解し、適切な選択をすることで、効率的かつ高品質な鉄加工が可能になります。
9-3. 作業者の技術と知識
鉄加工の世界では、フライス加工と旋盤加工が基本的な技術として知られています。これらの選び方を理解することは、効率的かつ高品質な製品を作り出すために重要です。フライス加工は主に平面や曲面などの加工に適しており、複雑な形状も実現できます。一方、旋盤加工は円筒形の物を加工するのに適しており、主に円形の部品作りに用いられます。
フライス加工の一例として、ギアやカムなどの精密部品があります。これらの部品は、複雑な形状を持ち、高い精度が求められるため、フライス加工の適用事例として良い例です。また、旋盤加工の典型的な例は、軸やローラーなど、円形の部品の製造です。これらは旋盤を使用して一定の形状に仕上げることができます。
適切な加工方法の選択は、製品の品質や生産効率に直結します。フライス加工は柔軟性が高く複雑な形状に対応できる一方で、旋盤加工は円形の部品に特化しており、それぞれに適した役割があります。したがって、製造する部品の形状や用途を正確に理解し、それに合った加工方法を選ぶことが重要です。
最終的に、鉄加工においてフライス加工と旋盤加工の特徴を理解し、適切な方法を選ぶことが、高品質な製品を効率的に生産する鍵となります。それぞれの技術が持つ特性を活かし、製品の要求に応じた最適な加工方法を選択することが求められます。
10. 切削加工のトラブルシューティング
10-1. よくある加工トラブルとその原因
フライス加工と旋盤加工は、鉄加工業界において最も基本的でありながら、それぞれ独特の特徴を持つ加工方法です。どちらを選ぶかは、製作する部品の形状や精度要求、加工時間などにより決定されます。フライス加工は平面や曲面など、複雑な形状の加工に適しており、旋盤加工は円筒形の部品や、内外の円形加工が必要な場合に優れた選択となります。
例えば、フライス加工はギアや金型の製作、複雑な3D形状の部品製作に利用されることが多く、旋盤加工はボルトやシャフトなどの円筒形の部品に使用されます。これらの違いを理解することは、加工品の品質と効率を最大化するために非常に重要です。
結論として、フライス加工と旋盤加工はそれぞれ独特の利点があり、選択は製作する部品の要件に基づいて行うべきです。特定の形状や加工の必要性を正確に評価することで、最適な加工方法を選定し、効率的かつ高品質な製品製作が可能となります。
10-2. トラブル時の対処法
鉄加工において、フライス加工と旋盤加工はそれぞれ異なる特徴を持ち、選び方を理解することが重要です。フライス加工は、主に平面や溝などを削るのに適しており、複雑な形状も加工できるのが特徴です。一方、旋盤加工は円形や円筒形の物を削るのに最適で、主に軸や円柱の加工に使われます。たとえば、自動車の部品や工具など、日常生活でよく見る物にもこれらの加工技術が活用されています。
選び方においては、加工する物の形状や精度、量産性を考慮する必要があります。例えば、複雑な形状や特定の溝を持つ部品を加工する場合はフライス加工が向いているでしょう。一方で、円形の部品や長い棒材を加工する際には、旋盤加工の方が適しています。
結論として、フライス加工と旋盤加工はそれぞれ独自の強みがあり、加工したい物の特性に応じて適切な加工方法を選ぶことが大切です。そのため、具体的な加工内容を考慮しながら、どちらの加工技術を用いるべきか判断することが、鉄加工の入門段階で非常に重要となります。
10-3. トラブルを避けるための予防策
鉄加工の世界では、フライス加工と旋盤加工が基本的な技術として知られています。これら二つの加工方法は、製品の形状や用途に応じて選ばれ、それぞれ特有の特徴を持っています。フライス加工は、主に平面や曲面を削り出すのに適しており、複雑な形状も実現可能です。例えば、歯車やカムシャフトなどの精密部品の製造に使われます。一方、旋盤加工は、円筒形の物を加工するのに特化しており、主軸と呼ばれる部分が回転しながら、工具が材料を削ることで形を整えます。これはボルトやネジ、筒状の部品など、回転対称の形状を持つ製品に最適です。
選択に際しては、製品の要求される形状や精度、量産の有無を考慮する必要があります。フライス加工は複雑な形状でも対応可能ですが、設備投資が比較的大きくなりがちです。旋盤加工は、比較的シンプルな形状の大量生産に適しており、コストパフォーマンスに優れています。
結論として、フライス加工と旋盤加工は、それぞれに独自の特徴があり、加工する製品の形状や精度、生産量によって適切な方法を選択することが重要です。日本では、これらの技術を駆使して高品質な製品が多数生産されており、選び方一つで製品の品質と生産効率が大きく変わることを理解することが鉄加工入門の第一歩です。
11. フライス加工と旋盤加工の選び方
11-1. 加工品質を決定する要素
鉄加工の世界では、フライス加工と旋盤加工が中心的な技術です。どちらも鉄をはじめとする金属の形状を加工するために不可欠ですが、その特徴と適用範囲には明確な違いがあります。適切な加工方法を選ぶことが、求められる加工品質を実現する上で極めて重要です。
フライス加工は、回転する刃を使って材料の表面を削り取る加工方法です。これにより、平面や溝、歯車などの複雑な形状を精密に削り出すことができます。例えば、自動車のエンジン部品や機械のフレームなど、精度が求められる部品の製造に多用されています。
一方、旋盤加工は、材料を高速回転させながら、切削工具で削り取る方法で、円筒形や円錐形の部品を製造するのに適しています。この方法では、ボールペンの芯やボトルのキャップなど、日常生活でよく見る製品も加工されています。
どちらの加工方法もその特性を理解し、加工したい部品の形状や精度、製造コストなどを考慮して選ぶ必要があります。フライス加工は複雑な形状や大量生産に適しており、旋盤加工は円形の部品や単品生産に向いています。
最終的に、フライス加工と旋盤加工の選択は、加工する物の特性と目的に合わせて行うべきです。どちらの技術も鉄加工において重要な役割を果たしており、それぞれの特徴を生かした加工が求められる品質を実現します。
11-2. コストと生産性のバランス
鉄加工におけるフライス加工と旋盤加工は、それぞれ独自の特徴を持ち、選択することで製品の品質や生産性に大きな違いが生じます。適切な加工方法を選ぶことが、コストと生産性のバランスを最適化する鍵です。フライス加工は、複雑な形状や平面を加工するのに適しており、多くの場合、高精度な仕上がりが求められる部品製造に用いられます。一方、旋盤加工は円筒形の材料を高速回転させながら行う加工方法で、主に円形や筒形の部品を製造する際に選ばれます。
たとえば、複雑な三次元形状を持つ自動車の部品や精密機器の部品などは、フライス加工によって高い精度で製造されます。これに対し、ネジや軸などの回転体は、旋盤加工によって効率良く、かつ高精度に製造することが可能です。
このように、フライス加工と旋盤加工は、それぞれ特有のメリットがあり、製品の要件に応じて適切な加工方法を選択することが重要です。適切な加工方法を選ぶことによって、生産効率を向上させ、コストを抑えることが可能になります。したがって、鉄加工の入門としては、これらの加工方法の特徴を理解し、製品の要件に最も合った加工手法を選ぶことが肝心です。これにより、鉄加工の分野におけるコストと生産性のバランスを最適に保つことができます。
11-3. 適切な加工方法の選択基準
フライス加工と旋盤加工は、鉄をはじめとする金属加工において非常に一般的な方法です。これら二つの加工方法は目的に応じて選ぶことが重要です。フライス加工は主に平面や溝、複雑な形状を加工するのに適しています。例えば、機械の部品や金型などの製造に多く用いられます。一方、旋盤加工は円形の物体を加工するのに適しており、軸やネジ、筒状の部品などを作るのに用いられます。両者の最大の違いは、フライス加工が物を動かしながらカッターが静止しているのに対し、旋盤加工では物が回転し、工具が物に接近して加工を行う点にあります。
したがって、加工したい物の形状や用途を考慮しながら、適切な加工方法を選択することが大切です。例えば、複雑な平面を加工したい場合はフライス加工を、円形の物を加工したい場合は旋盤加工を選ぶべきです。正しい選択をすることで、効率的かつ高品質な加工が可能になります。フライス加工と旋盤加工の理解と適切な選択は、金属加工の基礎として非常に重要です。
まとめ
鉄加工にはフライス加工と旋盤加工という2つの主要な方法があります。フライス加工は主に平面や溝を切削する際に使用され、一方旋盤加工は円筒形の対象物を加工するために用いられます。フライス加工では回転しないカッターを使用し、対象物が動きますが、旋盤加工では逆に対象物が回転し、切削工具が進む方向に動きます。これらの違いを理解することで、どちらの加工方法を選ぶべきかを判断する手助けになるでしょう。
メカニック必見!鉄のフライス加工アップカット・ダウンカット完全ガイド.
メカニックの皆さん、鉄のフライス加工においてアップカットとダウンカットとは一体何でしょうか?どのように行われるのか、そしてそれぞれがどのような特性を持つのか、気になりませんか?
この完全ガイドでは、鉄のフライス加工におけるアップカットとダウンカットの違いや使い方について詳しく解説します。メカニックの方々が理解しやすいように、わかりやすくイラストを交えて紹介します。
鉄を扱う際に必須となるこのテクニックをマスターし、より効率的かつ精度の高い作業を実現しましょう。さあ、鉄のフライス加工におけるアップカットとダウンカットの知識を深めて、作業の幅を広げていきましょう。
1. フライス加工の基本
1-1. 切削加工とは
鉄のフライス加工において、アップカットとダウンカットは重要な技術です。主に、これらの加工方法は、切削の質と効率を大きく左右します。その理由は、アップカット加工とダウンカット加工が材料に与える力の方向と、切削時のチップの排出方法が異なるためです。例えば、アップカット加工では、カッターが材料を持ち上げるように切削するため、切削面が滑らかになりやすく、特に溝加工や深い切削に適しています。一方、ダウンカット加工では、カッターが材料を押し下げながら切削するため、材料が固定されやすく、表面の仕上がりが良くなる傾向にあります。特に、薄い材料や仕上げ加工に適しています。このように、アップカットとダウンカットはそれぞれ特性が異なるため、加工する材料や求められる精度、仕上がりに応じて適切な方法を選択することが重要です。結論として、鉄のフライス加工におけるアップカット・ダウンカットの選択は、加工品質を左右する重要な要素であり、それぞれの特性を理解し適切に用いることで、高品質な製品を効率的に生産することが可能です。
1-2. 切削加工の種類とその特徴
フライス加工において鉄などの金属を加工する際、アップカットとダウンカットは重要な技法です。アップカット加工は、カッターが回転する方向と同じ方向に材料を送る方法で、主に粗加工に適しています。これは、大量の材料を一度に取り除くことができ、作業効率が良いためです。一方、ダウンカット加工は、カッターの回転方向と反対に材料を送る方法で、仕上げ加工に最適です。この方法では、より滑らかな表面が得られ、加工後の仕上がりが美しくなります。
たとえば、鉄の部品を製造する際、初期段階ではアップカットを用いて大まかな形状を作り、最終的な仕上げにはダウンカットを適用して滑らかな表面を実現することが一般的です。このように、アップカットとダウンカットを適切に使い分けることで、効率的かつ高品質な加工が可能になります。
結論として、フライス加工においては、アップカットとダウンカットの使い分けが極めて重要です。これらの技法を理解し、適切に活用することで、鉄などの金属加工の効率性と品質を大幅に向上させることができます。
1-3. 鉄のフライス加工とは
鉄のフライス加工において、アップカットとダウンカットは重要な手法です。フライス加工は、鉄などの素材を切削して形を整える工程であり、アップカットとダウンカットはその切削方向の違いによって名付けられています。アップカット加工では、カッターが材料を持ち上げながら切削し、ダウンカット加工では、カッターが材料を押し下げながら切削します。この二つの方法は、仕上がりの質や加工時の挙動に大きく影響します。
例えば、アップカット加工は、切りくずの排出が良好であり、深い溝の加工に適していますが、材料が持ち上がりやすいため、加工中の固定が重要になります。一方、ダウンカット加工は、加工表面が非常に滑らかになるため、外観が重要な部品に適していますが、切りくずの排出が悪いため、浅い加工に限られます。
このように、アップカットとダウンカットはそれぞれ異なる特性を持ち、加工する鉄の部品や目的に応じて適切に選択する必要があります。最終的には、これらの加工方法を理解し、適切に応用することが、鉄のフライス加工の質を向上させる鍵となります。
1-4. フライス加工の基本用語
フライス加工は、鉄などの金属材料を削る工程で鍵となる技術です。特に、アップカットとダウンカットは、仕上がりの質を大きく左右します。この二つの方法の選択によって、加工される部品の精度や表面の仕上がりが変わるため、正しい知識を持つことが非常に重要です。
アップカット加工では、刃が回転する方向と同じ方向に材料を送ります。これにより、切りくずが上方向に排出されやすくなるため、切削がスムーズに進みます。特に、長い切りくずが出る材料の加工に適しています。一方、ダウンカット加工は、刃の回転方向と反対に材料を送る方法で、切りくずが加工面に押し込まれる形になります。これにより、仕上がりが非常に滑らかになるため、表面品質を重視する加工に適しています。
たとえば、鉄でのフライス加工において、アップカットを用いれば、切削抵抗が少なくなり加工スピードを上げることができますが、ダウンカットを選べば、加工した面の滑らかさを最大限に高めることが可能です。
このように、アップカットとダウンカットはそれぞれ異なる利点があり、加工する材料や目的に応じて最適な方法を選択することが、高品質な製品を作り出す鍵です。フライス加工の基礎を理解し、正しい加工方法を選ぶことで、加工精度や効率を大きく向上させることができるでしょう。
2. アップカットとダウンカットの理解
2-1. アップカット加工の概要
フライス加工において、鉄の加工方法は大きく分けてアップカットとダウンカットの二つに分類されます。アップカット加工は、カッターが回転する方向と逆の方向に材料を送る方法です。この方法の最大の利点は、切削時に生じる切り屑が上向きに排出されるため、加工面が非常にきれいに仕上がる点です。例えば、精密な部品製作や複雑な形状の加工において、このアップカット加工は特に重宝されます。その一方で、材料を固定するための力が大きく必要になることや、工具の摩耗が早いというデメリットもあります。しかし、これらの問題も適切な工具選択と加工条件の調整によって、大きく改善することが可能です。アップカット加工は、その清潔な加工面と精度の高さから、鉄のフライス加工においては欠かせない技術の一つと言えるでしょう。
2-2. ダウンカット加工の概要
ダウンカット加工は、切削工具が回転する向きと進行方向が同じであるため、仕上がりが非常に滑らかになるという特徴があります。これは、切削工具が素材の表面を押し込むように削るため、素材の押し出しや引っ掛かりが少なく、細かい仕上げ加工に適しています。たとえば、金属の精密な部品製造や複雑な形状の加工において、ダウンカット加工はその利点を発揮します。日本のメカニックの中には、この加工法を用いて、高品質の製品を製造している例もあります。ダウンカット加工による滑らかな仕上がりは、製品の美観だけでなく、機能性の向上にも寄与するため、高い評価を得ています。まとめると、ダウンカット加工はその特性から、精密加工が求められる場面で非常に有効な手法であり、日本の技術者にとっても重要な技術の一つと言えるでしょう。
2-3. 鉄におけるアップカット・ダウンカットの適用
アップカットとダウンカットの加工法は、鉄のフライス加工において重要な技術です。これらの技術の適用により、加工の品質や効率が大幅に向上します。アップカット加工では、カッターが回転する方向と同じ方向に仕事を進めるため、切り屑が効率良く排出されます。これにより、清潔な加工面を得ることが可能となり、特に溝加工などの細かい作業に適しています。一方、ダウンカット加工では、カッターの回転方向とは逆に仕事を進めるため、加工面に強い押し込み力をかけることができます。この方法は、表面の仕上がりをより滑らかにするために利用されることが多く、外観が重視される部品の加工に適しています。
例えば、自動車のエンジン部品や建築用の金属部品など、精度と美しさが求められる鉄製品の加工には、これらの方法が活用されています。アップカット加工で粗削りを行い、その後ダウンカット加工で仕上げを行うという工程は、業界では一般的な流れとなっています。
結論として、鉄のフライス加工におけるアップカットとダウンカットの正しい理解と適用は、製品の品質向上と生産効率の向上の両面で極めて重要です。機械加工の技術者やオペレーターは、これらの技術を適切に使い分けることが求められています。
3. 金属部品の試作とフライス加工
3-1. 試作部品とフライス加工の関係
フライス加工は、試作部品製造において非常に重要な役割を果たしています。特に、鉄を使ったアップカットとダウンカットの選択は、部品の品質に大きな影響を与えます。アップカット加工では、カッターが回転する方向と同じ方向に材料を送るため、切りくずが上向きに排出されます。これにより、切断面がきれいに仕上がりますが、材料を押し上げる力が働くため、薄い材料での加工には不向きです。一方、ダウンカット加工では、カッターの回転方向と反対に材料を送るため、切りくずは下向きに排出されます。この方式は、材料を下に押さえつける効果があるため、精度が要求される加工や薄い材料に適しています。
日本で鉄のフライス加工に携わるメカニックたちは、これらの加工方法の特性を理解し、試作部品の要求に応じて最適な方法を選択することが重要です。例えば、精密な部品を製造する場合はダウンカット加工が適している一方で、大量に素早く製造する必要がある場合はアップカット加工が選ばれることが多いです。
結論として、鉄のフライス加工においてアップカットとダウンカットの適切な選択は、試作部品の品質と製造効率に直結します。メカニックは、それぞれの加工方法の特性を理解し、プロジェクトの要件に合わせて最適な選択をすることが求められます。
3-2. 鉄部品の試作における注意点
鉄のフライス加工において、アップカットとダウンカットは非常に重要な工程です。これらの工程を理解し適切に選択することで、加工品の品質を大きく向上させることができます。アップカット加工は、カッターが回転する向きと同方向に材料を送る方法で、特に溝や深い切削に適しています。この方法では、切りくずが上方に排出されるため、加工面がきれいに仕上がるという特長があります。一方、ダウンカット加工は、カッターの回転方向と反対に材料を送る方法で、表面仕上げを重視する場合に適しています。この工程により、材料が押し締められるため、より滑らかな表面が得られます。
例えば、鉄の精密部品を作る場合、ダウンカット加工を利用することで、表面の微細な傷を減らし、高品質な製品を生産することが可能です。また、特定の形状を加工する際にアップカットを選択することで、効率的に材料を削り取り、形状の精度を向上させることができます。
結論として、鉄のフライス加工においては、アップカットとダウンカットそれぞれの特性を理解し、加工する部品の要求に応じて最適な方法を選択することが重要です。これにより、品質、効率、そして経済性のすべてを高めることができます。
3-3. 試作過程での加工精度の確保
試作過程での加工精度を確保することは、製品の品質向上に直結するため非常に重要です。特に、鉄のフライス加工においては、アップカットとダウンカットの使い分けが精度確保の鍵を握ります。アップカット加工は、カッターが材料を持ち上げるように切削する方法で、切削精度が高く、表面が滑らかに仕上がります。これは、細かい加工や精密な部品製作に適しています。一方で、ダウンカット加工は、カッターが材料を押し付けながら切削する方法で、切削抵抗が少なく、加工速度を上げることができます。これは、大量生産や荒削りに適している加工方法です。例えば、自動車のエンジン部品や機械のフレームなど、精度と効率のバランスが求められる場合に有効です。したがって、試作過程では、製品の用途や加工条件を考慮して、適切な加工方法を選択することが重要です。これにより、加工精度の確保と生産効率の向上が実現します。
4. マシニング加工とフライス加工の違い
4-1. マシニング加工の基本
フライス加工におけるアップカットとダウンカットは、鉄を加工する際の重要な技術です。この二つの手法の理解と適切な使用は、加工の品質を大きく左右します。アップカット加工は、カッターが材料に対して上向きに削り取る方式で、特に断層がクリアである必要がある場合に適しています。一方、ダウンカット加工は、カッターが材料を下向きに押し付けながら削る方式で、表面の仕上がりを滑らかにしたい場合に最適です。
例えば、装飾的な部品や精密な部品を作る際にはダウンカット加工が好まれます。これは、ダウンカット加工の方が表面の仕上がりが良く、加工後の微細な調整が少なくて済むためです。一方で、内部構造が複雑で、クリアな断面が必要な部品加工にはアップカット加工が用いられることが多いです。アップカット加工は、材料の切りくずを効率良く排出できるため、加工の精度を高めることが可能です。
結論として、アップカットとダウンカットはそれぞれに適した用途があり、これらを適切に選択することが高品質なフライス加工の鍵となります。具体的な加工要件に応じて最適な方法を選ぶことで、品質、効率、コストのバランスを最適化できるのです。
4-2. フライス加工との比較
鉄のフライス加工におけるアップカットとダウンカットは、効率と精度を大きく左右します。この二つの加工方法の選択は、仕上がりの品質を決定づける要素と言えるでしょう。アップカットは、工具が回転する方向に対して材料を押し上げるように削り取る方法です。これにより、比較的クリーンな切断面を得ることが可能になります。例えば、精細な仕上げが求められる部品の加工に適しています。一方、ダウンカットは、材料を押し下げながら削る方法で、材料の押し出しによる欠けや割れが少なくなるため、加工の安定性が向上します。特に、表面の仕上がりを重視する場合に有効です。
結論として、鉄のフライス加工においては、加工する物の特性や要求される仕上がりに応じて、アップカットとダウンカットのどちらを選択するかが重要です。精細な表面仕上げを求める場合はアップカット、加工の安定性と表面の仕上がりを両立させたい場合はダウンカットが適していると言えます。それぞれの特徴を理解し、適切に選択することで、高品質なフライス加工が可能となります。
4-3. 各加工方法の選択基準
鉄のフライス加工において、アップカットとダウンカットはどちらも重要な役割を持っています。結論から言うと、材料の種類や加工する表面の仕上がりによって、適切な加工方法を選択することが不可欠です。例えば、アップカットは切削時に材料を持ち上げる力が働くため、切りくずの排出が良好であり、主に溝加工や深い切込み加工に適しています。一方、ダウンカットは材料を押し付ける力が働き、表面の仕上がりが滑らかになるため、外観が重要視される部品に適しています。
具体的な例として、鉄で作成されるギアやフレームなどの機械部品では、精度と強度が要求されるため、ダウンカット方式が好まれます。一方で、高速で大量の切削を必要とする場合や、切りくずの排出性が重要視される場合は、アップカット方式を選択することが多いです。
結局のところ、アップカットとダウンカットの選択は、加工する鉄部品の用途や要求される品質に応じて柔軟に判断することが重要です。適切な加工方法を選ぶことで、効率的かつ高品質な製品製造が可能になります。
5. 6面フライスと4面フライスの違い
5-1. 6面フライス加工の特徴
フライス加工において、特に鉄を対象としたアップカットとダウンカットは、精度と仕上がりの面で大きな違いを生む重要な技術です。アップカット加工とは、カッターが材料を持ち上げるように切削する方法で、これにより切りくずが上方向に排出されます。一方、ダウンカット加工では、カッターが材料を押し下げるように切削し、切りくずを材料に押し込む形で排出します。この両者の選択は、加工する材料や求められる仕上がりによって異なります。
例えば、アップカット加工は、切りくずの排出が良いため、切削部分の熱が材料に籠もりにくく、精密な加工が可能です。しかし、材料が持ち上げられやすいため、固定が不十分だと加工精度に影響が出ることがあります。一方、ダウンカット加工は、カッターが材料を押し固めるため、表面仕上げが非常に滑らかになりますが、切りくずの排出が悪いため、加工中の熱が問題となることがあります。
日本における鉄のフライス加工では、これらの特性を理解し、加工する製品の要件に応じて適切な方法を選ぶことが重要です。例えば、高精度が求められる部品ではアップカットが、より滑らかな表面が必要な場合はダウンカットが選ばれます。このように適切な加工方法を選ぶことで、求められる品質を実現することができます。
まとめると、鉄のフライス加工におけるアップカットとダウンカットは、それぞれ特有の利点があり、製品の要求仕様に応じて最適な方法を選択する必要があります。適切な加工方法を理解し選択することで、高品質な製品製造が可能になります。
5-2. 4面フライス加工の特徴
鉄のフライス加工では、アップカットとダウンカットの技術が重要です。これらの方法は、加工品の品質や仕上がりに大きく影響します。アップカット加工では、切削刃が回転する向きと同じ方向に材料を送ります。これにより、きれいな切削面を得ることができ、特に溝加工や側面加工に適しています。例えば、精密な部品や装飾的な要素が必要な場合、アップカット加工が選ばれることが多いです。一方、ダウンカット加工では、切削刃の回転方向とは逆に材料を送ります。これは、材料の押し出しを防ぎ、特に断面が薄い材料や表面処理が必要な場合に有効です。
両方法の選択は、加工する鉄材の種類や目的により異なります。たとえば、アップカットは鉄材の速い除去が必要な場合や、大きな力を加える必要がある時に適しています。ダウンカットは、精度を重視する細かな作業や、表面を滑らかに仕上げたい時に選ばれます。
結論として、鉄のフライス加工においてアップカットとダウンカットは、それぞれ異なる状況や要件に応じて選択すべき重要な手法です。加工品の品質を最大限に高めるためには、これらの加工方法の特徴を十分に理解し、適切に使い分けることが必須です。
5-3. 加工手順と工程の違い
フライス加工で重要なのは、アップカットとダウンカットの理解です。これらの加工方法によって、鉄の加工精度や仕上がりが大きく変わります。アップカットは、カッターが材料を持ち上げながら削る方法で、特に溝切りや深い切削に適しています。これに対し、ダウンカットは、カッターが材料を押し付けながら切削する方法で、表面の仕上がりを綺麗にするのに有効です。
例えば、鉄の平面加工を考えた場合、ダウンカット加工は表面の滑らかさを重視する場合に選ばれます。一方で、アップカット加工は切削時の材料の排出が良いため、深い溝を切る作業などでは有利です。実際に、日本の精密機械加工では、これらの特性を生かし、製品の用途に応じて適切な加工方法を選択しています。
結論として、フライス加工のアップカットとダウンカットは、それぞれ異なる特性を持ち、鉄の加工においてその特性を活かした選択が求められます。優れた加工品を作るためには、これらの違いを理解し、目的に応じて適切な方法を選択することが重要です。
6. 切削加工における形状の重要性
6-1. 形状を決定する要因
フライス加工で鉄を削る際、アップカットとダウンカットはその仕上がりに大きく影響します。この二つの方法は、切削した金属の形状を決定する上で非常に重要です。アップカット加工は、刃が回転する方向と同じ方向に材料を送る方法で、これにより材料から切り屑が上方に排出されます。これは、比較的きれいな切断面を実現するのに適しています。一方、ダウンカット加工は、刃の回転方向と反対方向に材料を送る方法であり、切り屑が材料に押し込まれるため、より滑らかな表面が得られます。
例えば、細かい仕上がりを必要とする部品や装飾品を加工する場合、ダウンカットが選ばれることがあります。アップカットは、切り屑の排出が良いため、深い溝を切る作業などに向いています。このように、アップカットとダウンカットはそれぞれ特徴があり、加工する鉄の形状や求められる仕上がりによって適切な方法を選ぶことが重要です。
結論として、フライス加工におけるアップカットとダウンカットは、鉄の加工品質を左右する要素として重要です。適切な加工方法の選択により理想的な仕上がりを実現できるため、メカニックはこれらの技術を習得し、加工条件に応じて適切に選択することが求められます。
6-2. 形状による加工性の違い
フライス加工において、アップカットとダウンカットは鉄の加工性に大きく影響を及ぼします。この二つの方法は、それぞれ異なる利点と適用場面を持っており、理解することがメカニックにとって必須です。
まず、アップカット加工では、カッターが回転する方向と同じ方向に材料を送ります。この方法の最大の利点は、切削力が材料をテーブルに押し付けるため、加工中の材料の安定性が向上することです。例えば、薄い材料や形状が複雑な部品の加工に適しています。
一方、ダウンカット加工では、カッターの回転方向とは反対に材料を送ります。この方法の特徴は、切削表面が非常に滑らかに仕上がることであり、外観が重要な部品の加工に最適です。しかし、材料が押し上げられやすいため、加工中の材料の固定には十分な注意が必要です。
結論として、アップカットとダウンカットのどちらを選択するかは、加工する部品の材質、形状、および求められる仕上がりによって異なります。鉄のフライス加工を行う際にこれらの方法を適切に選択し、使い分けることで、より高品質な製品を効率的に生産することが可能となります。
6-3. 複雑な形状のフライス加工技術
鉄のフライス加工において、アップカットとダウンカットは、それぞれ独自の利点を持ちます。アップカット加工は、材料から切り屑を効率よく排出することができるため、清潔な加工面を得ることができます。これは、細かな作業が必要な部品製造に適しています。一方、ダウンカット加工は、材料に対して刃が押し付ける形で切削するため、加工面がなめらかに仕上がります。これは、見た目が重要な製品や、精密な加工が求められる場合に有効です。
日本においては、特に精密機械や電子機器の製造において、これらの加工方法が重宝されます。例えば、自動車の部品や電子機器の基板など、耐久性と美観が要求される製品には、ダウンカット加工が好んで用いられます。一方で、より高速で効率的な加工を求める工業製品では、アップカット加工が選ばれることが多いです。
結論として、アップカットとダウンカットの選択は、製品の用途や求められる品質によって異なります。鉄のフライス加工を行う際には、これらの特性を理解し、適切な加工方法を選択することが、高品質な製品を生産する上での鍵となります。
まとめ
鉄のフライス加工において、アップカットとダウンカットは重要な要素です。アップカットは切削時に切屑が上方へ排出されるため、切り粉の排出がスムーズであり、切れ味も向上します。一方、ダウンカットは切屑が下方へ排出されるため、刃先によるすり減りが少なく、表面仕上げに適しています。メカニックの皆様にとって、これらの違いを理解することは重要です。
「加工選びの秘訣を伝授!鉄用フライスと旋盤、どう使い分ける?」
鉄を加工する際に、フライス加工と旋盤加工の使い分けがわからないことはありませんか?『加工選びの秘訣』をお伝えします。この記事では、鉄を加工する際に重要となるフライス加工と旋盤加工の違いについて詳しく解説します。鉄の特性や使用する機械の特徴を理解することで、仕事の効率や品質向上につながることでしょう。さあ、加工選びのポイントを探りながら、鉄をより効果的に加工するためのヒントを見つけてみましょう。
1. 鉄の切削加工入門
1-1. 鉄の特性と加工の基本
鉄を加工する際には、フライス加工と旋盤加工の使い分けが重要です。この違いを理解することで、より良い製品を作り出すことができます。フライス加工は、切削工具が回転することで鉄の表面を削り取る方法です。この方法は、平面や溝、複雑な形状の加工に適しています。一方、旋盤加工は、鉄を回転させながら固定された切削工具で削る方法で、円筒形の加工や穴あけに最適です。
例えば、フライス加工は自動車のエンジン部品やフレームの加工に用いられ、旋盤加工はボルトやナット、軸などの円形部品を作るのに適しています。これらの加工法を使い分けることで、精度高く効率的に鉄製品を製造できます。
結論として、鉄の加工においてフライス加工と旋盤加工はそれぞれ独自の利点があり、製品の要件に応じて適切に選択することが重要です。加工方法を理解し、具体的な例に基づいて使い分けることで、高品質な製品製造に繋がります。
1-2. 炭素鋼とその切削性の理解
鉄用フライス加工と旋盤加工の使い分けは、加工の細かな違いを理解することから始まります。フライス加工は、回転する刃で材料を削り取る加工方法で、旋盤加工は、材料を回転させながら刃で削る方法です。フライス加工は平面や曲面などの複雑な形状を加工するのに適しており、一方、旋盤加工は円筒形や円錐形など、回転対称の形状を持つ部品の加工に特化しています。
例えば、エンジン部品や歯車などの精密な加工が必要な場合は、フライス加工が選ばれることが多いです。これらの部品は、複数の平面や角度を持つ複雑な形状であるため、フライス加工によって高い精度を実現できます。一方で、軸やボルトなどの部品は、旋盤加工によって、その円筒形状を効率良く高精度に加工することができます。
このように、鉄用フライス加工と旋盤加工は、それぞれ特有の特徴を持ち、加工する部品の形状や必要とされる精度に応じて使い分けられるべきです。加工選びの秘訣は、これらの加工方法の特性を理解し、加工する部品の要件に最も適した方法を選択することにあります。
1-3. ステンレス鋼の切削性の特徴
鉄用のフライス加工と旋盤加工、それぞれの利点を知っていると、加工選択において非常に役立ちます。フライス加工は複雑な形状や平面を削るのに適しており、旋盤加工は円形や筒形の加工に最適です。たとえば、フライス加工はギアや溝の加工に用いられ、旋盤加工は軸やボルトなどの円筒形の部品の製造に適しています。このように、目的に応じた加工方法を選ぶことが重要です。
日本では、高い技術力を持つ加工業者が多いため、特に精密な部品が求められる場合には、これらの加工技術の理解が不可欠です。例えば、自動車産業や精密機械産業などでは、この二つの加工方法を組み合わせて、より高度な部品を製造しています。
結論として、鉄用のフライス加工と旋盤加工を使い分けることで、加工の精度を上げるとともに、効率的な生産が可能になります。各加工方法の特徴を理解し、適切な選択を行うことが、質の高い製品を生産するための秘訣です。
2. フライス加工と旋盤加工の基礎知識
2-1. フライス加工の概要と鉄への適用
フライス加工と旋盤加工は、鉄などの金属加工において、その適用と機能が異なります。フライス加工は、主に平面や曲面、溝などの加工に適しています。これは、回転するカッターを使用して材料から金属を削り取る方法です。例えば、機械部品のキーウェイやギアの製造によく使用されます。一方、旋盤加工は、円筒形や円錐形の外面加工、内径の穴あけ加工に最適です。これは、固定された切削工具で回転する材料を削ることによって行われます。自動車の車軸やボールペンの芯などがこれに該当します。
このように、フライス加工と旋盤加工は使用する目的や加工する形状によって使い分けられます。適切な加工方法を選ぶことで、効率的かつ高品質な製品を製造することが可能です。したがって、加工選びにおいては、加工したい部品の形状や必要とする仕上がりを考慮して、それぞれの特性を理解し選択することが重要です。
2-2. 旋盤加工の原理と鉄の加工法
鉄用フライス加工と旋盤加工は、それぞれ異なる特性を持ち、用途に応じて使い分けることが重要です。フライス加工は、主に平面や溝などの加工に用いられ、高速で大量の金属を削り取る能力があります。これに対し、旋盤加工は円筒形の材料を加工するのに適しており、非常に高い精度での仕上がりを期待できます。
例えば、複雑な形状のギアや歯車を作る場合、フライス加工の能力を活かして効率よく材料を削り出します。一方、シャフトやボルトなどの円筒形の部品を作成する際には、旋盤加工の精度の高さが求められます。
このように、鉄用フライス加工と旋盤加工はそれぞれ得意とする分野があり、適切に使い分けることで、効率的かつ高品質な加工が可能になります。生産の効率化や品質の向上を図るためにも、これら加工方法の特性を理解し、目的に応じた適切な選択が求められます。
2-3. 加工方法の違いとそれぞれの特徴
加工選びのポイントは、目的に合った機械を選ぶことです。特に、鉄加工におけるフライス加工と旋盤加工には明確な違いがあります。フライス加工は、主に平面や曲面の造形に適しており、精密な部品や複雑な形状の加工が得意です。例えば、ギアやカムのような部品が挙げられます。一方、旋盤加工は、軸に関する部品や円筒形の加工に適しています。車輪の軸やボールペンの芯など、円を描く形の加工に優れているのです。
適切な加工方法を選ぶことで、加工の精度を高め、コストを削減することが可能です。加工選びの際は、これらの特徴を理解し、製作したい部品の形状や用途に最適な機械を選定することが重要です。結論として、鉄用フライスと旋盤の使い分けは、加工する部品の形状と目的に基づいて行うべきです。それぞれの特性を理解し、適切な加工方法を選択することが、効率的で高品質な製品を生み出す秘訣と言えるでしょう。
3. 加工選びの秘訣
3-1. 炭素鋼の切削性と最適な加工法の選定
加工選びをする際、鉄用フライス加工と旋盤加工の適切な使い分けが重要です。これらの加工方法は、それぞれ特有の利点があり、加工する物の形状や必要な精度によって選ばれます。具体的に言うと、フライス加工は平面や曲面を加工するのに適しており、複雑な形状や大きな物も加工できます。一方、旋盤加工は円形や筒形の物を高精度で加工するのに最適で、特に円周の平滑性が要求される場合には旋盤が選ばれます。
日本においても、これらの加工技術は広く利用されており、例えば自動車業界や機械部品製造において、フライス加工は複雑な部品の製作に、旋盤加工はシャフトやベアリングのような円形部品の加工に使用されています。このように、適切な加工方法を選択することで、高品質な製品を効率良く生産することが可能になります。
結論として、鉄用フライス加工と旋盤加工は、それぞれ異なる特性を持ち、用途に応じて適切に使い分けることが重要です。加工する物の形状や求められる精度を考慮し、それぞれの加工方法の利点を最大限に活用することが、高品質な製品を生産する鍵となります。
3-2. 依頼先を選ぶ際のポイント
鉄用フライス加工と旋盤加工の違いを理解することは、加工の品質を高め、効率を良くするために非常に重要です。フライス加工は、主に平面や曲面などを加工するのに適しており、複雑な形状も精密に作り出すことができます。一方、旋盤加工は円筒形の加工に適しており、内外の円形加工や穴あけなど、回転する物体の加工に強みを持っています。
たとえば、鉄製のギアを作る場合、その複雑な形状を正確に加工するにはフライス加工が適しています。一方で、シャフトのような円筒形の部品を作る際には、旋盤加工が適しています。このように、加工する部品の形状に合わせて適切な加工方法を選ぶことが、高品質な製品を効率よく生産する鍵となります。
結論として、鉄用フライス加工と旋盤加工はそれぞれ異なる特性を持ち、適した用途があります。加工する部品の形状や要求される精度を考慮して、最適な加工方法を選択することが重要です。これにより、加工の品質を高め、生産効率を向上させることが可能になります。
3-3. フライス加工と旋盤加工の使い分け方
フライス加工と旋盤加工は、鉄を含む様々な材料を加工する際に欠かせない手法ですが、その使い分けは非常に重要です。フライス加工は平面や曲面を削り出すのに適しており、複雑な形状や精密な部品製作に役立ちます。一方、旋盤加工は円形や筒形の材料を回転させながら加工する手法で、主に円筒形の部品の加工に適しています。
たとえば、エンジンのブロックや歯車などの製造時にはフライス加工が用いられます。これらの部品は複雑な形状や細かい溝が必要であり、フライス加工の方が適しているからです。一方で、ボルトやシャフトなどの円筒形の部品は、旋盤加工によって高い精度で製造されます。これは部品の形状が単純で、旋盤の回転により一貫した仕上がりが得られるためです。
つまり、フライス加工と旋盤加工の使い分けは、製作する部品の形状と精度要求に依存します。フライス加工は形状の複雑さや精密さが求められる場合に、旋盤加工は円筒形部品の精密加工に、それぞれ最適な加工方法として選択されるべきです。この適切な使い分けにより、効率的かつ高品質な製品製造が可能になります。
4. 切削条件の重要性
4-1. 切削加工時の基本的な切削条件
加工選びの秘訣を伝授します。鉄用フライスと旋盤加工の違いを理解することは、工作機械を使用する上で非常に重要です。フライス加工は、主に平面や曲面を削る際に用いられ、旋盤加工は円形や筒形の物を削るのに適しています。たとえば、フライス加工では、ギアや複雑な形状を持つ部品の加工が可能です。一方、旋盤加工では、ボルトやシャフトなどの円形部品の加工に優れています。
この違いを把握することで、加工品の品質向上や作業効率の向上が期待できます。例えば、フライスで適切に加工されたギアは、スムーズな動作や耐久性を持ち合わせることになります。また、旋盤で正確に加工されたシャフトは、機械全体の性能を最大限に引き出すことができます。したがって、加工方法を適切に選択することは、最終製品の品質に直結し、製造業において極めて重要な意味を持ちます。
結論として、鉄用フライスと旋盤加工の正しい使い分けを理解し、適切に適用することが、製品の品質向上と生産性の向上に繋がります。この知識を持つことで、より効率的で高品質な製造が可能になるでしょう。
4-2. フライス加工における切削条件の設定
フライス加工と旋盤加工は、鉄などの金属を加工する際に欠かせない方法ですが、その使い分けにはいくつかポイントがあります。まず、フライス加工は平面や曲面、溝などの加工に適しており、複雑な形状も実現できます。一方、旋盤加工は円筒形の物を加工するのに最適で、特に直径の精密な調整が必要な場合に優れています。
例えば、エンジン部品やギアなどの精密な円筒形部品を作る際は、旋盤加工の精度と能力が必要になります。一方で、機械のフレームや、複雑な形状の金型を作る時はフライス加工の方が適しています。
結論として、鉄をはじめとする金属加工において、フライス加工と旋盤加工はそれぞれ得意とする分野が異なります。加工する部品の形状や必要な精度に応じて、最適な加工方法を選択することが大切です。そのため、両者の特性を理解し、適切に使い分けることが、高品質な製品を効率良く生産する秘訣と言えるでしょう。
4-3. 旋盤加工における切削条件の設定
鉄用フライスと旋盤加工は、それぞれに適した用途があります。これを理解することが、加工選びの秘訣です。フライス加工は、主に平面や溝、複雑な形状を削り出す際に適しています。一方、旋盤加工は円形や円筒形の加工に特化しており、精密な直径の加工や内径の加工に優れています。
例えば、機械の部品である歯車を作る場合、その複雑な形状を削り出すにはフライス加工が利用されます。一方で、軸やボルトなどの円筒形の部品は、旋盤加工によってその精度高く仕上げられます。
したがって、加工選びの秘訣は、加工したい物の形状や必要な精度を考慮し、フライス加工と旋盤加工の特性を最大限に活かすことにあります。この理解を深め、適切な加工方法を選択することで、効率的かつ高品質な加工が可能になるのです。
5. 実践!鉄用フライスと旋盤の使い分け方
5-1. プロジェクトに応じた適切な加工方法の選択
フライス加工と旋盤加工は、鉄の加工において異なる特徴と用途を持っています。ここでは、それぞれの加工方法を適切に使い分ける秘訣を紹介します。
まず、フライス加工は、主に平面や溝、複雑な形状を加工するのに適しています。これは、フライス加工機が回転する刃を用いて、多様な形状を精密に削り出せるからです。例えば、ギアやエンジン部品の加工には、このフライス加工がよく用いられます。
一方、旋盤加工は、円筒形の物体を加工するのに特化しています。旋盤では、回転する材料に対して固定された切削工具を接触させることで、材料を削り取ります。シャフトやボルトなど、円形や棒状の部品の加工に適しているのが特徴です。
結論として、フライス加工と旋盤加工は、加工する部品の形状や必要な精度によって使い分けることが重要です。平面や複雑な形状の加工にはフライス加工を、円筒形の物体には旋盤加工を選択することで、効率的かつ高品質な加工が可能になります。
5-2. 鉄フライス加工の具体的なアプローチ
鉄用フライス加工と旋盤加工の使い分けは、加工の目的と特性を理解することから始まります。フライス加工は、主に平面や曲面などの形状を削り出すのに適しています。これは、回転するカッターが材料の表面を削り取ることで形状を作り出すためです。たとえば、複雑な形状の金型や部品の製造によく用いられます。一方、旋盤加工は、円形の材料を加工する際に適しており、材料を回転させながら固定された切削工具で材料を削り取っていきます。これは、主にシャフトやボルトなどの円筒形の部品の製造に用いられる方法です。
このように、フライス加工と旋盤加工はそれぞれ特定の用途に適した特性を持っています。加工する部品の形状や必要な精度に応じて、これらの加工方法を使い分けることが重要です。例えば、複雑な立体形状を必要とする部品はフライス加工が適しており、円筒形で精度の高い部品は旋盤加工が適しています。
結論として、鉄用フライス加工と旋盤加工の使い分けは、加工したい部品の形状と精度の要件を理解し、それぞれの加工方法の特性に合わせて選択することが秘訣です。この知識を持つことで、より効率的で高品質な加工が可能となります。
5-3. 鉄旋盤加工の実践的な応用
鉄用フライス加工と旋盤加工は、それぞれが持つ特性を理解し適切に使い分けることで、加工の効率と品質を飛躍的に向上させることが可能です。フライス加工は平面や曲面を削り出すのに適しており、複雑な形状や精密な部品の製作に優れています。例えば、鉄を使ったギアや機械の部品など、細かい凹凸や特殊な形状を持つ製品の加工にはフライス加工が選ばれます。一方、旋盤加工は円筒形の材料を回転させながら削ることで、高い精度を要する軸や棒状の部品を製作するのに最適です。具体的には、スクリューやローラー、軸受けなどがこれに該当します。
これらの加工方法を適切に使い分けることで、製作したい部品や製品の特性に合わせた加工が可能となり、最終的な製品の品質を高めることができます。フライス加工と旋盤加工の違いを理解し、それぞれの長所を活かすことが鉄加工の秘訣です。
6. 切削加工の品質を左右する要因
6-1. 材料の特性と加工品質
鉄用フライス加工と旋盤加工は、製造現場では欠かせない技術です。これらの違いを理解することは、材料の特性を生かし、高品質な製品を作り出すために重要です。フライス加工は主に平面や溝、複雑な形状の加工に適しています。この方法では、回転する工具が材料に接触し、所望の形状を削り出します。例えば、機械部品のキー溝や歯車などがこの方法で加工されます。一方、旋盤加工は、円筒形の材料を回転させながら、工具を材料に接触させて形状を整える技術です。シャフトやボルトなどの円形の部品が、旋盤加工で作られます。
これらの技術を適切に使い分けることで、材料の特性を最大限に活かし、加工品質を向上させることができます。例として、複雑な形状を必要とする部品はフライス加工が向いており、円形の部品は旋盤加工が適しています。このように、加工方法を選ぶ際には、製品の形状や用途、そして材料の特性を考慮する必要があります。適切な加工方法を選ぶことで、効率的に、かつ高品質な製品製造が可能になります。
6-2. 切削工具の選定と保守
鉄用フライス加工と旋盤加工は金属加工の基本であり、その使い分けは加工品質を左右します。フライス加工は、特に平面や溝などの複雑な形状を加工するのに適しています。これに対し、旋盤加工は円形や円筒形の部品の加工に優れています。たとえば、フライス加工ではギアやフレームのような部品が効率的に加工でき、旋盤加工ではシャフトやボルトなどの円形部品の加工が得意です。
フライス加工と旋盤加工のこれらの特性を理解することは、適切な加工方法の選定に不可欠です。適切な加工方法を選択することで、製品の精度を高め、生産効率を向上させることが可能になります。
このように、鉄を加工する際には、加工する部品の形状や要求される精度に応じて、フライス加工と旋盤加工を適切に使い分けることが重要です。その結果、製品の品質を向上させ、コスト削減にも繋がることから、鉄用フライス加工と旋盤加工の違いを理解し、それぞれの特性を活かした加工方法を選択することが、製造現場における成功の鍵となります。
6-3. 加工精度を高めるためのコツ
適切な加工方法の選択は、鉄加工の精度を大きく左右します。特に、フライス加工と旋盤加工は、それぞれ特有の利点があり、使い分けが重要です。フライス加工は、平面や曲面を削るのに適しており、複雑な形状の加工に優れています。一方、旋盤加工は、円筒形の加工に適しており、円周の精度を高める作業に最適です。例えば、鉄でできたギアを作る際には、フライス加工で粗く形を整えた後、旋盤加工で細かい部分を調整するという使い分けが効果的です。このように、加工する物の形状や求められる精度に応じて適切な加工方法を選ぶことで、高品質な成果物を生み出すことができます。結論として、フライス加工と旋盤加工は、それぞれ異なる状況に適した加工方法であり、これらを上手く使い分けることが鉄加工の秘訣と言えるでしょう。
7. トラブルシューティングと最適化
7-1. よくある切削加工の問題と対策
加工作業において鉄を扱う際、フライス加工と旋盤加工はそれぞれ異なる特性を持ち、使い分けが重要です。フライス加工は平面や溝、複雑な形状を加工するのに適しています。一方、旋盤加工は円形や筒形の加工に優れています。
例えば、フライス加工は、部品の平らな面を削ったり、特定の形の溝を作ったりするのに適しています。これに対し、旋盤加工は、ネジのような円周上に連続したパターンを作るなど、円形の物体に最適です。日本の製造業では、これらの加工方法を組み合わせることで、精度の高い部品製造を実現しています。
さらに、フライス加工機は加工面に対して複数の刃を用いることができるため、大量生産に向いています。一方で、旋盤加工は細かい加工が得意で、特に一点物の製品や試作品の作成に有効です。
結論として、鉄の加工においてフライスと旋盤の使い分けは、加工する物の形状や生産量に依存します。フライス加工は平面や複雑な形状、大量生産に、旋盤加工は円形や筒形、細かい作業や一点物の制作に向いています。これらの特性を理解し、適切に使い分けることが、効率的で高品質な加工を実現する秘訣です。
7-2. 加工プロセスの最適化と効率化
鉄の加工において、フライス加工と旋盤加工の使い分けは非常に重要です。それぞれ加工方法の違いが、製品の品質や生産効率に大きく影響を及ぼします。フライス加工は、主に平面や溝などの形状を加工するのに適しています。特に、複雑な形状や精密な加工が必要な場合に優れた性能を発揮します。例えば、機械部品のキーウェイやギアの加工にはフライスを使用します。一方、旋盤加工は円筒形の物体を加工するのに適しており、主軸に材料を固定して回転させながら切削することで、外径や内径の加工、面取りなどが行えます。例えば、ボルトやシャフトなどの加工に適しています。結局、加工する製品の形状や必要な精度によって、フライス加工と旋盤加工を適切に選択することが、効率的かつ高品質な製品製造の鍵となります。
7-3. 継続的な品質向上のためのヒント
鉄用フライス加工と旋盤加工は、それぞれ異なる機能を持ち、使い分けることで作業の効率化や品質向上が見込めます。フライス加工は主に平面や曲面を削り出すのに適しています。一方、旋盤加工は円筒形の加工や内孔の加工に適しており、細かい仕上げが可能です。
例えば、フライス加工は鉄製のギアやフレームなど、複雑な形状を持つ部品の製造に適しています。一方で、旋盤加工はシャフトやボルトなど、円筒形をした部品や、精密な内径加工が必要な部品の加工に最適です。
このように、フライス加工と旋盤加工を適切に使い分けることで、製作する部品の品質を高めることができます。それぞれの加工方法に適した部品を選び、高精度な加工を実現しましょう。加工選びの秘訣を理解し、最適な方法を選択することが、品質向上のカギとなります。
8. 最新技術と加工の未来展望
8-1. 切削加工技術の進化と新材料
鉄用フライス加工と旋盤加工は、製造現場での重要な技術です。これらは目的に応じて使い分けることが重要で、それぞれの特徴を理解することが加工選びの秘訣となります。フライス加工は主に平面や溝、複雑な形状を加工するのに適しています。これは、刃が回転し、ワークピースが移動することにより加工が行われるためです。一方、旋盤加工は円柱形のワークピースに適しており、主に外周や内径、端面加工に使用されます。この際、ワークピースが回転し、工具が移動することで加工が行われます。
例として、鉄製の歯車を作る場合、フライス加工で精密な溝を作ることができます。また、軸やピンなどの円柱形部品は、旋盤加工によって外周や端面を滑らかに仕上げることが可能です。
結論として、加工する部品の形状や必要とする精度に応じて、鉄用フライス加工と旋盤加工を適切に使い分けることが、製品品質の向上に繋がります。適切な加工方法の選択が製造効率の向上とコスト削減にも寄与するため、これらの特徴をしっかりと把握し、使い分けることが重要です。
8-2. 自動化とデジタル化の影響
鉄用フライス加工と旋盤加工は、金属加工の世界で欠かせない技術ですが、それぞれに適した用途があります。フライス加工は平面や曲面など、様々な形状の加工が可能であり、旋盤加工は円筒形の物体の加工に適しています。例えば、フライス加工は歯車や金型などの複雑な形状の加工に用いられ、旋盤加工はネジやシャフトなどの円筒形の部品を製作するのに使われます。日本では精密な技術が求められるため、これらの加工技術の選択が製品の品質を大きく左右します。したがって、加工する物の形状を理解し、それに最適な加工方法を選ぶことが重要です。このように、鉄用フライス加工と旋盤加工はそれぞれ異なる特性を持ち、適切に使い分けることで、高品質な製品製作が可能となります。
8-3. 持続可能な加工方法と環境への配慮
加工選びにおいて、鉄用フライス加工と旋盤加工の使い分けは、非常に重要です。これらの加工方法は、それぞれが持つ特性により、適した用途が異なります。フライス加工は、特に複雑な形状や平面を加工するのに適しています。例えば、ギアやカムなどの精密部品の製造に利用されます。一方、旋盤加工は、円筒形の材料を加工する際に最適で、ボルトやシャフトなどの製造に用いられます。具体的には、フライス加工機で複数の刃を用いて材料を削り取ることで形状を作り出し、旋盤加工では材料を回転させながら刃で削ることで製品を作ります。これらの違いを理解し、プロジェクトに応じて最適な加工方法を選択することが、効率的で高品質な製品を作るための秘訣です。結論として、鉄用フライス加工と旋盤加工は、それぞれ異なる特性を持ち、適した用途が異なるため、プロジェクトの要件に応じて適切に使い分けることが重要です。
9. 結論:加工選びの秘訣と賢い使い分け
9-1. 加工方法の決定における総合的な考慮
鉄用フライス加工と旋盤加工は、それぞれに適した用途があります。フライス加工は複雑な形状や平面を削り出すのに適しています。一方、旋盤加工は円筒形の加工に特化しており、精密な直径の調整が可能です。例えば、ギアや歯車などの精密な部品製造には、フライス加工が選ばれます。これに対して、シャフトやボルトのような円形の部品には、旋盤加工が使われることが多いです。このように、加工する部品の形状や必要な精度に応じて、フライス加工と旋盤加工を適切に選択することが、効率的かつ高品質な製品製造の秘訣です。どちらの加工方法も鉄材料に対応しており、日本の製造業で広く利用されています。最適な加工方法を選ぶことで、コスト削減や生産性向上に繋がります。
9-2. 長期的な視点に立ったパートナー選び
鉄を加工する際のフライス加工と旋盤加工の使い分けは、製品の精度と効率を大きく左右します。フライス加工は、複雑な形状や平面を削り出すのに適しています。一方、旋盤加工は、円形や円筒形の加工に優れているため、目的に応じて選ぶことが重要です。
例えば、鉄でギアやフレームなどの複雑な形状を作る場合は、フライス加工が向いています。その精密な動きで、細かい部分まで正確に加工することができます。反対に、シャフトやボルトなどの円筒形の部品を作る際は、旋盤加工が効果的です。旋盤の回転により、一定の形状を均一に削り出すことが可能になります。
これらの違いを理解し、適切な加工方法を選ぶことで、効率よく高品質な製品を作り出すことができます。鉄の加工において、フライスと旋盤の適切な使い分けは、製品の品質を決める重要な要素です。
9-3. 今後の学びと技術の継続的なアップデート
鉄用フライス加工と旋盤加工の違いを理解し、適切に使い分けることは、加工品質を高める秘訣です。フライス加工は、主に平面や曲面を削る際に用いられる技術で、複雑な形状の部品も高精度で加工できます。一方、旋盤加工は、主に円筒形の部品を加工するのに適しており、内外の円形加工や穴あけなどに用いられます。
例を挙げると、自動車のブレーキディスクやギアなどの精密な部品はフライス加工で作られることが多いです。これらは、平面や斜面の加工精度が求められる部品で、フライス加工により高い精度を実現できます。一方で、シャフトやボルトなどの円筒形部品は、旋盤加工で効率良く高品質に仕上げることができます。
このように、鉄用フライス加工と旋盤加工は、それぞれ得意とする加工範囲が異なります。適切な加工方法を選択することで、加工効率を上げると共に、高品質な製品を製造することが可能になります。加工技術の選択は、製品の品質を左右する重要な要素であり、その秘訣を理解することが、製造業における成功への鍵となります。
まとめ
鉄を加工する際には、フライス加工と旋盤加工の違いを理解することが重要です。フライス加工は切削工具を回転させながら材料を加工する方法であり、複雑な形状の加工に適しています。一方、旋盤加工は材料を回転させながら切削工具を進める方法であり、円筒状の形状を加工するのに適しています。どちらの方法を選ぶかは加工する材料や形状によって異なります。これらの違いを理解して、加工選びの秘訣を探ってみましょう。