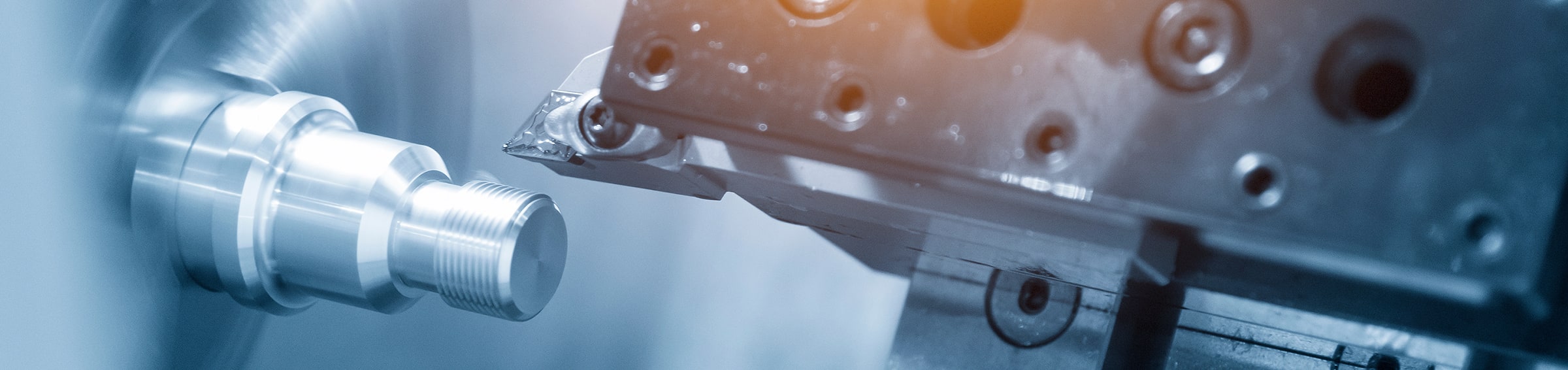
コラム column
【穴あけ加工必見】SKDフライス加工で押さえるべき3つのポイント!
SKDフライス加工は工作機械において重要な技術の一つです。穴あけ加工においては特に注意すべきポイントが3つあります。この記事では、SKDフライス加工の基本から応用まで、穴あけ加工における重要なポイントを分かりやすく解説しています。ぜひ参考にして、スキルアップに役立ててください。
1. SKD 穴あけ加工とフライス加工の基本
SKD穴あけ加工を行う際は品質を確保するために押さえるべき三つのポイントがあります。まず、適切な工具の選択が重要です。SKDの硬度や熱処理の状態に合わせたドリルやエンドミルの選定が、加工精度を大きく左右します。次に、正確な加工条件の設定が重要です。カット速度や送り速度、冷却剤の使用など適切な加工条件を見極めることで、穴の仕上がりや工具の寿命を最適化できます。最後に、工具のメンテナンスも欠かせません。加工後のチップの摩耗や損傷の確認、定期的な交換や研磨が必要です。これらのポイントを押さえることでSKD穴あけ加工の品質を保つことができるのです。
2. 旋盤加工とSKD フライス加工の違い
SKDフライス加工は、精密な穴あけ加工において非常に重要なプロセスです。適切な加工を行うためには、以下の3つのポイントを押さえることが肝心です。まず、SKDフライス加工では、材質の特性を十分に理解する必要があります。SKD材は硬度が高く加工には適切な工具選定が必要です。次に、冷却剤の使用は、加工中の発熱を抑え、工具の摩耗を防ぐために重要です。適切な冷却剤の選択と使用量の調整が必要です。最後に、正確な位置決めが重要です。穴あけの際には、工具やワークの位置ズレが極限まで小さくなるように、細心の注意を払う必要があります。これらのポイントをしっかり押さえれば、SKDフライス加工は精度が高く、効率の良い加工が可能となります。
3. マシニング加工とSKD フライス加工の違い
SKDフライス加工において最も重要な3つのポイントは、正確さ、耐久性、そして工具の選択です。SKD材を用いた穴あけ加工には高い精度が求められ、そのためには適切なマシニングセンタを利用することが不可欠です。また、SKDフライス加工を行う際には、材料の硬度に応じた耐久性の高い工具を選択する必要があります。例えば、硬い材料を加工する時はチップの切れ味が長持ちするコーティングされた工具が推奨されます。さらに、適切な冷却液の使用は、工具の摩耗を減らし長寿命化にも貢献します。最後に、加工条件の最適化も重要で、切削速度や送り速度、切削深さを材料や工具に応じて調節することで高品質な加工が可能になります。正確性と耐久性を確保し、適切な工具選択と加工条件の最適化を行うことが、SKDフライス加工で成功するための鍵となります。
4. SKD11鋼のCNCフライス加工の概要
SKDフライス加工において、穴あけ作業は繊細かつ精密な作業が求められます。この加工を成功させるためには、以下の3つのポイントを押さえる必要があります。まず、適切な工具の選定です。SKD材は耐摩耗性に優れているため、工具は高速度鋼や超硬合金など、硬質材料で作られたものを選ぶべきです。次に、冷却剤の使用が挙げられます。加工時の熱は精度に影響を与えるため、適切な冷却剤を使用して熱をコントロールすることが重要です。最後に、マシンの回転数と送り速度の設定があります。これらを適正に設定することで、工具の摩耗を防ぎ、加工精度を保つことができます。結論として、これらのポイントをしっかりと押さえ、事前の準備を怠らなければ、SKDフライス加工における穴あけ作業も成功に導くことができるでしょう。
5. 高硬度鋼SKDの切削加工における重要ポイント
SKDのフライス加工においては、工具の選定、切削条件、冷却方法の3つが重要なポイントとなります。まず、SKDは高硬度であるため、工具は硬質コーティングされたものを選ぶことが肝心です。これにより耐摩耗性が増し、工具の寿命を延ばすことができます。次に、切削条件は慎重に設定する必要があり、特に切削速度や送り速度を適正に保つことで、加工面の仕上がりや加工効率を良くすることができます。最後に冷却方法として、SKDの加工時は摩擦熱が高くなりやすいため、適切な冷却液を使用することが重要です。これによって切削熱を効果的に除去し、工具の損耗やワークの熱影響を最小限に抑えられます。これらのポイントを抑えることで、SKDの穴あけフライス加工の品質と効率を大きく向上させることが可能です。
6. 工具鋼の種類とSKD 穴あけフライス加工における考慮事項
SKDフライス加工における穴あけ作業は、精度と効率を追求する上で重要です。そのため、注視すべき3つのポイントを理解することが不可欠です。まず、適切な工具選びが基本で、SKD材の硬度や加工形状に応じたドリルやエンドミルの選定が必要です。次に、正確な切削条件の設定がポイントです。回転数や送り速度、切削深さなどを材質に応じて最適化することで、工具の寿命を延ばし、加工品質を保つことができます。最後に、加工時の冷却は欠かせません。適切な冷却方法を適用することで、刃先の温度上昇を抑え、加工精度の向上と工具の破損リスクを減少させることが可能です。これらを踏まえて、SKD穴あけフライス加工には綿密な準備と正確な操作が求められることを再確認し、品質と効率の向上を図りましょう。
まとめ
SKDフライス加工では、適切な切削条件の設定が重要です。また、適切な切削液の使用と工具の取り扱いに注意することも大切です。さらに、穴あけ位置の正確さを保つために、適切な工具の選択と専用の治具の使用が不可欠です。これらのポイントを押さえることで、効率的かつ精密な穴あけ加工が可能となります。
SK材利用者必見!穴あけとフライス加工の効率を上げる方法
SK材を利用する際、穴あけやフライス加工の効率を上げる方法について知りたくないですか?本記事では、SK材の加工において効率的な穴あけやフライス加工の方法を詳しく解説しています。SK材を使用する際には、効率的な加工方法を知っておくことが重要です。穴あけやフライス加工にお悩みの方は、ぜひご覧ください。
1. SK材とは?—切削加工における基本知識
SK材を使用した穴あけやフライス加工の効率を上げるには、適切な工具選びと処理方法の見直しが必要です。SK材は炭素鋼であり、一般に硬度が高く耐摩耗性に優れていますが、その分加工が困難になることも。では、どうすれば効率よく加工できるのでしょうか。まず、適切な切削工具を選ぶことが大切です。硬い材料には、耐摩耗性に優れたコーティングが施されたドリルやエンドミルを用いると良いでしょう。また、工具の送り速度や回転数を材料の硬度に応じて適切に設定することも重要です。具体例としては、SK材の場合、低速でじっくりと加工することがポイントです。また、切削液を使い、工具の冷却と潤滑をしっかりと行うことで、加工精度を高めるとともに、工具の寿命を延ばすことができます。最後に、再度結論ですが、SK材の穴あけやフライス加工の効率を上げるには、適した工具選びと処理方法の最適化が鍵となります。
2. SK 穴あけ加工—鉄や高硬度鋼におけるテクニック
SK材を使用した穴あけやフライス加工の効率を上げる方法は、工具選びから始まります。まず、鉄や高硬度鋼といったSK材の加工に適した高品質なドリルやエンドミルを選ぶことが重要です。特にコーティングされた工具は耐久性が高く、精度の高い加工を実現します。次に、適切な切削速度や送り速度を設定することで、切削抵抗を最適化し、加工品質と効率を向上させることが可能です。また、冷却液の流れを調整して、過熱を防ぎ、工具の寿命を延ばすこともポイントです。実際の現場では、これらの方法を組み合わせることで、SK材の穴あけやフライス加工の効率と精度を高めることができます。最後に、加工の各ステップでの継続的な改善を心がけることで、作業効率は更に向上し、最終的に高品質な製品を安定して生産することができるようになります。
3. SK フライス加工の基本—切削の種類と特徴
SK材を使用した穴あけやフライス加工の効率を上げるためには、正しい工具の選定と加工パラメータの最適化が重要です。SK材は耐摩耗性に優れ、加工精度が要求される場合に適していますが、硬い材質ゆえに適切な工具選びが不可欠です。例えば、超硬合金やコーティングされたドリルは硬い材質への穴あけ作業に適しており、加工寿命を延ばします。またフライス加工では、切削抵抗を下げるために、高い切削スピードと適切なフィードレートを見つけることがポイントです。特に、多様な加工形状に対応できるマルチエッジタイプのカッターを用いた場合、効率良く作業を進めることができます。最終的には、これらの方法によってSK材の穴あけとフライス加工の品質と効率を同時に高めることが可能になります。
4. 穴あけ機械の選定—SK材加工に最適なツール選び
SK材の穴あけやフライス加工の効率を高める方法は、適切な工具選びにかかっています。穴あけでは、SK材の硬さに対応した高速度鋼(HSS)ドリルや超硬ドリルを使用することで、加工性が向上します。フライス加工においても、SK材の特性に合ったカッターやエンドミルの選定が重要となります。特に、コーティングされたエンドミルは耐摩耗性が高く、長期にわたって安定した加工が可能です。また、加工時の冷却効果を高めるために適切な切削液の選択も効率化に寄与します。このように、最適な工具と条件を選ぶことで、加工時間の短縮と工具の寿命を延ばすことが可能になり、結果として生産性の向上が期待できます。
5. 穴あけ機械おすすめランキング—SK材加工向け
SK材を使用する際、穴あけとフライス加工の効率を上げることは、作業のスピードアップとコスト削減に繋がります。適切な工具選びと加工条件の設定が重要です。例えば、SK材の硬度に合わせたドリル選びや、冷却液の適切な使用は、穴あけ時の摩耗を減少させ、精度を保つ上で効果的です。フライス加工においては、カッターの歯数や切削速度の調整が、仕上がりの精度を高め、加工時間を短縮します。また、専用の工具を使うことで、より専門化された加工が可能となり、作業効率が向上します。結局のところ、適切な準備と工具選定が、SK材加工の効率を大きく左右するのです。
6. SK材のフライス加工—機械加工の理解を深める
SK材を使用した穴あけやフライス加工の効率を上げる方法は、正しい工具選択と処理条件の最適化にあります。SK材は硬度が高く加工しにくい特性を持つため、専用の工具や切削油の利用が効果的です。例えば、コバルト高速度鋼(HSS-Co)やチタンコーティングされたドリルは、耐摩耗性に優れ穴あけ作業をスムーズに行うことができます。また、フライス加工においては、工具の回転数や送り速度を材質に合わせて調整し、適切な切削条件を見つけることが重要です。これにより、工具の寿命を延ばし、精度の高い加工を実現することができます。最適な工具と条件選びにより、SK材の加工効率は格段に向上します。
7. 工具鋼SK材の特性と加工ポイント
工具鋼SK材は硬度が高く耐摩耗性に優れた材料であるため、穴あけやフライス加工の際には効率を上げる工夫が必要です。その方法とは、適切な工具選びと加工パラメータの設定です。特に、コーティングされたドリルやカーバイド製のエンドミルの使用は耐久性と切削速度の向上に寄与します。また、回転数や送り速度を材質に応じて最適化することで、焼き付きを防ぎつつ効率的に加工できます。例えば、SK材の場合、低い回転数で安定した送りを行うことが重要とされています。このように適切な工具の選択とパラメータ設定により、SK材の加工効率を大幅に向上させることが可能です。結論として、SK材を使用した穴あけやフライス加工では、材料の特性を理解し適切な工具と加工条件を選ぶことが非常に重要です。
8. SK 穴あけ・フライス加工のトラブルシューティング
SK材を使った穴あけやフライス加工の効率を高める方法は非常に重要です。なぜなら、SK材は硬度が高く加工が難しいからです。この材料に適した工具選びや切削条件の設定が必要です。例えば、コーティングされた超硬工具を使用することで、耐摩耗性が向上し、一貫した作業が可能になります。また、適切な切削速度と給送速度を見つけることで、切り屑の排出をスムーズにし、工具の熱負荷を減少させることができます。ちょうど良い量の冷却液を使用することも、切削効率を上げるためには欠かせません。これらの方法を採用することで、SK材の穴あけやフライス加工の精度と効率が大幅に向上し、生産性の向上に貢献することができます。
9. 穴あけ・フライス加工の効率化—専門家のコツ
SK材を使った穴あけやフライス加工の効率を上げるためには、適切な工具選びと加工条件の設定が重要です。まずは、SK材に合った材質と形状を持つドリルやエンドミルの選定が肝心。特に、硬いSK材には耐摩耗性に優れるコーティングが施された工具がお勧めです。また、加工条件としては、切削速度や送り速度、切削液の使用がポイントになります。例えば、切削速度を適切に保つことで、工具の摩耗を抑えつつ、加工面の仕上がりを良くすることが可能です。フライス加工では、適切な送り速度を保ちながら、一定の切削液を供給することで、切りくずの排出をスムーズにし、加工精度を向上させることができます。このように工具選びと加工条件の最適化により、SK材を用いた穴あけやフライス加工の効率は大幅に向上します。
10. 次世代SK材加工技術の展望
SK材を使用した穴あけとフライス加工の効率化は、製造現場において非常に重要です。主な理由は、加工時間の短縮と精度の向上に他なりません。具体的には、ツーリングの選定やカット条件の最適化が挙げられます。例えば、硬質なSK材に適した高速度鋼や超硬合金のドリルを使用することで、穴あけ作業のスピードと寿命が格段に向上します。フライス加工に関しても、切削抵抗を低減させるコーティングの適用や、振動を抑える工具の使用が効果的です。結論として、適切なツールと加工方法を選ぶことで、SK材の穴あけとフライス加工の効率は確実に上がり、生産性の向上に貢献します。
まとめ
SK材を使用した穴あけとフライス加工の効率を上げるためには、適切な切削条件や工具選びが重要です。適切な刃先や切削油を選択することで、加工時間を短縮し、作業効率を向上させることが可能です。また、加工前に素材の状態や目標とする加工精度を考慮し、適切な加工方法を選択することも大切です。
金属加工の新スタンダード!SK材での穴あけ・フライス加工ガイド
金属加工の分野において、SK材は新たなスタンダードとして注目されています。SK材を使用した穴あけやフライス加工は、従来の方法と比べてどのように進化しているのでしょうか?本ガイドでは、SK材を用いた金属加工の最新情報や技術について詳しく解説していきます。穴あけやフライス加工に関心のある方々にとって、このガイドは新たな知識とアイデアを提供することでしょう。
1. SK 穴あけ フライス加工とは?
SK材を用いた穴あけ・フライス加工は、金属加工の新たなスタンダードとして注目されています。この技術により、耐久性が求められる部品製造において、より高い精度と長寿命を実現できるからです。具体的な例としては、自動車産業や航空機部品の加工において、SK材による加工法が好まれています。これは、SK材が高硬度でありながら加工しやすい特性を持っているため、精密な部品を効率よく生産することができるからです。また、SK材を用いることにより、工具の摩耗を抑え、長期間にわたって高品質な加工が可能となる利点もあります。最終的には、この加工技術が製造コストの削減にも繋がり、産業全体の競争力向上に貢献しています。
2. 金属加工の基本:SK材を知る
金属加工の世界では、耐久性と加工性を兼ね備えたSK材が新たなスタンダードとして注目を集めています。この素材は、硬度が高く、精密な穴あけやフライス加工が求められる場面で優れた性能を発揮します。例えば、金型の製作や自動車部品の加工において、SK材はその強度と耐摩耗性で高い信頼を得ています。特に、微細な部品を正確に加工する必要がある電子機器の分野では、SK材の精度が重要な役割を担っています。また、長時間にわたる加工でも材料の劣化が少ないため、コスト効率も高くなります。このように、SK材はその特性を活かして多くの工業製品に不可欠な要素となっており、今後の金属加工技術の進展においても中心的な材料としての地位を確立していくでしょう。
3. SK 穴あけ加工の基礎
金属加工において、SK材はその優れた特性から新しいスタンダードとして注目を集めています。まず、SK材は耐摩耗性と硬度が高いため、穴あけやフライス加工において精度の高い仕上がりを実現することができます。特に、精密な部品を求められる航空宇宙産業や自動車産業では、SK材での加工が不可欠な場面が増えています。例えば、エンジン部品やタービンブレードなど、高い耐久性と強度が求められる部品の加工において、SK材の使用はその効果を発揮します。このようにSK材を使用することで、長持ちする製品をコスト効率よく生産することが可能となり、日本における製造業の競争力向上に貢献しています。総じて、SK材での穴あけ・フライス加工は、高品質な製品を生産する上での新たな基準となっているのです。
4. SK フライス加工の技術
SK材を使った金属加工は、その卓越した性能のために新しいスタンダードとなりつつあります。穴あけやフライス加工の際、SK材は耐久性と切削効率の高さを提供し、これがその理由です。例えば、自動車産業や航空宇宙産業では、精密な部品が求められ、SK材はその要求を満たすために頻繁に使用されています。SK材は硬質で粘り強く、長時間の加工にも耐えうる性質を持ち、工具の摩耗を大きく減少させるため、コストの削減にも繋がります。また、安定した加工が可能なため生産性の向上にも寄与しています。結論として、SK材を活用した金属加工は、その高い耐久性とコスト効率の良さにより、多くの産業で新しい標準として受け入れられており、今後もその需要は高まると考えられます。
5. 材料選定の重要性:SK材の利点と特性
SK材を用いた金属加工は、現代の製造業で新たなスタンダードとなりつつあります。この理由は、SK材の優れた耐久性と加工のしやすさにあります。たとえば、穴あけ作業において、SK材は硬い材料でありながら精密な加工が可能になっています。フライス加工においても、その均一な質感と硬度により、滑らかできれいな仕上がりを実現することができます。さらに、耐熱性・耐摩耗性に優れているため、工具の耐用年数を伸ばすことができ、結果的に経済的な選択となり得ます。これらの特性から、SK材は多くの現場で選ばれる理由がよくわかります。最終的に、SK材での穴あけ・フライス加工は、費用対効果と品質のバランスが優れているため、新しい工業標準としての地位を確立しつつあります。
6. SK材の加工に適した工具と機械
金属加工の分野で、SK材はその耐久性と加工性の良さから、新しいスタンダードとして注目されています。SK材に適した穴あけやフライス加工は、精密な作業が要求されるため、ここに適した工具や機械の選定が不可欠です。たとえば、SK材の穴あけには、高速で精密な切削が可能なカーバイドドリルが適しており、フライス加工には、切削抵抗が少なく高い耐久性を誇るエンドミルが推奨されます。また、加工機械には安定した切削速度を維持できるCNC工作機械が適しているとされています。これらの工具と機械を使いこなすことによって、SK材はさらにそのポテンシャルを発揮し、製品の品質向上に貢献します。このような工具や機械の進化は、金属加工技術の発展を支え、業界の新たなスタンダードを築いています。
7. 穴あけ・フライス加工の応用例
穴あけやフライス加工の技術は金属加工業界において、精度と効率化の追求から新たなスタンダードとなっています。特にSK材を用いた加工は、その優れた耐摩耗性と耐久性から多くの産業で重宝されているのです。例えば、自動車産業においては、エンジン部品やトランスミッションの精密な穴あけ加工にSK材が用いられており、これにより部品の寿命と性能が飛躍的に向上しています。また航空宇宙産業では、航空機のタービンブレードなどの高強度な部品をフライス加工する際にSK材が欠かせない材料となっています。これらの具体例からも、SK材による穴あけ・フライス加工がいかに製造現場で不可欠かがわかります。さらに、SK材は加工の精度を高めるだけでなく、生産性の向上にも寄与しており、これが新スタンダードとして広まっている主な理由の一つです。
8. SK材加工の品質管理と検証
SK材を利用した穴あけやフライス加工が金属加工の新たな基準となっています。これは、SK材の特性が加工の精度や効率を飛躍的に向上させるためです。たとえば、SK材は優れた耐摩耗性を持つため、加工中の工具の摩耗を抑え、より長い期間高精度な加工を維持することができます。さらに、SK材の均一な組織と硬度により、安定した加工が可能となり、製品の品質ばらつきを最小限に抑えることが可能です。実際、多くの製造現場でSK材を取り入れることにより、穴あけやフライス加工の工程での生産性の向上やコスト削減が実現しています。これらの利点により、SK材は今後も金属加工の分野で重要な役割を果たすことが予想されます。結論として、SK材は金属加工における品質と効率の向上を可能にする新スタンダードであると言えるでしょう。
9. 金属加工サービス選びのポイント
金属加工の分野では、SK材を用いた穴あけやフライス加工が新たなスタンダードとして注目されています。SK材は優れた耐摩耗性と適度な硬さを兼ね備え、精密な加工が可能なことから、多くの業界で採用が進んでいます。たとえば、自動車産業においては、エンジン部品や駆動系のコンポーネントにSK材が使用され、その耐久性と精度が要求される性能を実現しています。また、航空宇宙産業では、飛行機のタービンブレードなど重要な安全部品の加工にも利用され、その信頼性が証明されています。このように、SK材を用いた穴あけやフライス加工は、高品質な製品製造に不可欠な技術として、今後もさらに普及していくでしょう。金属加工の新しいスタンダードとして、SK材の重要性はますます高まることが予想されます。
10. SK 穴あけ・フライス加工に関するよくある質問
SK材を使用した穴あけ・フライス加工が、金属加工の新たなスタンダードとして注目されています。SK材は独自の特性を持ち、耐摩耗性や切削性が高いことから、多様な加工ニーズに応えることが可能です。たとえば、精密な穴あけ加工が求められる自動車産業や、複雑な形状のフライス加工を必要とする航空機部品製造において、SK材は優れた性能を発揮します。これらの業界で実際に使用されている事例を参考にすると、SK材による加工がいかに効率化と高品質をもたらすかがわかります。結果として、金属加工業界におけるSK材の地位は不動のものとなりつつあり、今後もその利用範囲は広がっていくことでしょう。
まとめ
SK材は金属加工において高い精度と耐久性を持っています。SK材を使用した穴あけやフライス加工は、高速加工が可能であり、処理時間を短縮することができます。また、高耐熱性があるため、長時間の加工作業にも適しています。SK材を使用することで、金属加工の精度と効率を向上させることができます。
SK材加工のプロ直伝!穴あけからフライスまでの完全マニュアル
SK材加工のプロ直伝!穴あけからフライスまでの完全マニュアルへようこそ。本記事では、SK材加工における穴あけからフライスまでの手法やテクニックを解説します。SK材加工に興味があるけれど、どこから始めればいいかわからないとお困りの方にこそぜひおすすめしたい内容です。穴あけやフライス加工に関する基本から応用まで、この記事を読めばSK材加工についての理解が深まることでしょう。さあ、スキルアップの第一歩を踏み出してみませんか?
1. SK材加工入門:基本的な知識と技術
SK材加工は精密な作業が要求される分野であり、正確な穴あけやフライス加工が不可欠です。この加工技術は、工業製品の品質向上に大きく寄与しています。たとえば、自動車や電子機器に使われる部品の加工には、このSK材加工技術が用いられ、その高い精度が要求されるのです。穴あけ作業においては、適切なドリル選びや回転数の設定が重要であり、フライス加工においては、刃の種類や送り速度、切削深さの選定が成功の鍵を握ります。さらに具体的な例を挙げると、自動車のエンジン部品などは、微細な公差内で加工される必要があるため、SK材加工技術が必須とされます。このようにして、SK材加工は製品の信頼性を保証し、幅広い産業における技術進歩を支えているのです。
2. SK 穴あけ加工の基礎
SK材加工における穴あけ作業は、精密な製造を要する一連のプロセスであり、その品質が最終製品の性能に直結します。穴あけの基本としては、適切なドリルの選定が必須です。SK材の硬度や加工する穴の大きさに合わせたドリルを使用することで、きれいな穴を効率よくあけることが可能になります。たとえば、小径の穴加工にはツイストドリルを、大径の穴加工にはコアドリルが適しています。さらに、フライス加工では、カッターの選定が重要となります。SK材の特性を理解した上で最も適したカッターを選び、適切な切削条件を設定することが、高精度なフライス加工を実現する鍵です。具体的には、切削速度や送り速度を材質や形状に応じて調整する必要があります。以上の基礎を押さえることで、SK材の穴あけからフライス加工まで、一貫した高品質な加工が可能となります。
3. SK フライス加工の基本
SK材加工は精密な技術を要する作業であり、穴あけからフライス加工に至るまで、専門的な知識と技術が求められます。穴あけ作業では、材質や厚みに応じたドリル選びが肝心です。例えば、SK材には高速度鋼や超硬合金が用いられることが多く、適切なドリル速度や冷却方法の理解が必要です。一方、フライス加工では、カッターの種類や切削条件が重要で、これらを適正に設定することで、SK材の持つポテンシャルを最大限に引き出すことができます。誤った工具選びや設定は、加工誤差や材料の損傷につながるため注意が必要です。最後に、専門家による正確な知識の伝達と実践は、SK材加工技術の向上に不可欠です。
4. 異なる材料へのSK 穴あけ・フライス加工方法
SK材加工における穴あけやフライス加工は精密作業であり、そのノウハウは産業界で高く評価されています。まず、均一な穴開けは製品の品質を左右するため、適切な工具選びと正確な位置決めが極めて重要です。たとえば、硬度が高いSK材への穴加工には、耐久性と切削力のあるドリルが必要となります。同様にフライス加工においては、材料を傷つけず滑らかな仕上がりを得るために、精密な速度調整と適切なカッター選びが求められます。さらに、加工する材料の特性を考え、切削液の使用も非常に効果的です。これらのプロセスを適切に行うことで、効率的かつ高品質なSK材加工が実現されます。結論として、穴あけからフライス加工に至るまで、適切な道具と技術があれば、優れた加工品質を保証することが可能です。
5. 高硬度鋼SK材の切削加工テクニック
SK材の加工は、精密で繊細な技術が要求されます。とりわけ穴あけやフライス加工は、その技術の粋を集めた工程であり、適切な工具選びと加工条件が成功のカギを握ります。例えば、穴あけではドリルの材質や形状、冷却方法を選ぶことが重要です。フライス加工では、カッターの種類や刃の数、切削速度や送り速度の調整が品質を左右します。これらの工程をマスターすれば、SK材加工での一貫した高品質な製品づくりが可能となります。それゆえに専門知識の習得と実践は不可欠です。こうした細かなテクニックを積み重ねることで、高硬度鋼SK材の加工を極めることができるのです。
6. 工具鋼SK材の種類とその特性
工具鋼SK材は、その硬度と耐摩耗性により、穴あけやフライス加工において広く利用されています。SK材の正しい扱い方を理解することで、作業の精度を高め、効率的な加工が可能となります。たとえば、穴あけ作業においては、材料の硬さに応じた適切なドリルの選択が重要です。硬い材料の場合、高速度鋼や超硬合金製ドリルを用いることで、きれいな穴をあけることができます。また、フライス加工では、切削速度や送り速度を適切に設定することが肝心で、SK材の特性を考慮した加工法を採用する必要があります。最適な加工条件のもとでなければ、工具の摩耗が早まり、製品の品質にも影響を及ぼすことになります。結論として、SK材加工の専門知識を有することで、製品の精度を高めるだけでなく、加工コストの削減にも繋がるのです。
7. SK材の旋盤加工について
SK材加工は精密な技術が求められる作業で、特に穴あけやフライス加工の段階には細心の注意が必要です。まず、穴あけ作業の際には、SK材の硬さに合わせたドリル選びが重要で、正確な穴径と位置精度を実現するためには高品質なドリルと正しい速度設定が要となります。一例として、小径の穴を精密に開ける際には、高速回転が可能な超硬ドリルの使用が推奨されます。また、フライス加工では、刃の選定に加えて、材料の送り速度や切削深さを適切に管理することで、美しい仕上がりを得ることができます。SK材加工の成功は、こうした適切な道具選びと作業条件設定によって大きく左右されます。そのためにも、ノウハウを身につけ、常に精度を求めた作業を心掛けることが不可欠です。
8. SK 穴あけ機械の選び方と人気ランキング
SK材加工における穴あけからフライス加工までの工程は、品質の良い製品を作り出すために欠かせない工程です。適切な機械を選ぶことで、この複雑な作業を簡単かつ効率的に行うことが可能になります。一例として、高精度な穴あけにはドリルプレスが推奨され、フライス加工ではデジタル制御のフライス機が優れた仕上がりを提供します。また、加工時の材料の固定方法や機械のメンテナンスも重要なポイントとなります。これらを総合的に考慮し、SK材の加工に適した機械を選定し、その使い方を学ぶことが、高品質な製品を効率良く生産する鍵となります。
9. マシニング加工とSK材切削の理解
SK材の加工についての理解と技術は、高精度な製品を作り出すうえで欠かせません。加工の基本である穴あけは、材料の特性を理解して適切なドリル選びから始まります。たとえば、SK材は硬度が高いため、高速度鋼や超硬合金のドリルが適しています。さらにフライス加工では、刃の数や形状を考慮することが重要です。正しい工具と加工パラメータを選ぶことで、精度の高い加工が可能になるのです。特に、切削抵抗が大きいSK材を扱う際は、冷却液の使用や工具の切れ味を常にチェックすることで、工具の寿命を延ばし品質を保つことができます。最終的には、これらのプロセスを経て、精密な部品や工具が作られ、機械の性能を最大限に引き出すことが可能になるのです。
10. SK材加工のトラブルシューティングと対策
SK材の加工は精密さを要する作業であり、穴あけからフライス加工まできちんとした知識と技術が必要です。穴あけ作業においては、選定するドリルの種類や刃の角度が仕上がりの品質に直接影響を及ぼしますし、フライス加工では刃の速度や送り速度が重要です。例えば、SK材に小さい穴を開ける際には、高速回転のドリルを使用し、冷却液を適切に供給しながら加工を行なうことで、きれいな仕上がりを実現することができます。また、フライス加工では、適切な切削条件を設定することで、材料の焼けやバリを防ぐことができます。これらの技術をマスターすることで、SK材加工の品質を向上させ、トラブルを未然に防げます。結論として、SK材を加工する際は正しい工具の選択と、正確な加工条件が極めて重要であり、これにより高品質な製品を効率よく生産することが可能になります。
まとめ
SK材加工において、穴あけからフライス加工までの基本的な手順やポイントを網羅したマニュアルです。穴あけでは適切な刃先と回転数を選ぶことが重要です。また、フライス加工においては正しい切削条件や適切な刃物選びが成功のカギとなります。プロの技を学びながら、SK材加工のスキルを向上させましょう。
【2023年版】SK材穴あけからフライス加工までの一連の流れ
2023年もうすぐ到来しますが、SK材を使用した加工に関心がありますか?SK材を使用した加工の一連の流れ、穴あけからフライス加工までの工程について、この記事で詳しく解説します。SK材穴あけとフライス加工に関する新たな情報や最新の手法について学びたい方におすすめです。
1. SK材穴あけ加工とは
SK材穴あけ加工とは、製品や部品を作る際に必要な精密な穴を開ける工程を指します。2023年においても、この技術は製造業にとって不可欠です。たとえば、自動車部品や家電製品において、正確な位置に穴を開けなければ、製品の品質や機能に大きく影響します。SK材に穴をあける際には、特殊なドリルと正確な技術が必要とされ、それに続くフライス加工では、さらなる精度を要求されます。フライス加工では、穴の周辺を削り出して形状を整えることで、部品同士の組み合わせを可能にします。この一連の工程を適切に行うことで、高品質な製品へとつながるのです。したがって、SK材穴あけからフライス加工までの流れは、優れた製品を生み出すための重要なステップと言えます。
2. SK材フライス加工の基礎
SK材のフライス加工は精密な部品製造に欠かせない工程であり、穴あけ加工から始まります。この流れは、高い品質の部品を作り出すためには非常に重要です。まず、穴あけ加工によって、SK材に必要な直径の穴を開けます。次に、フライス加工を施し、穴の形状や表面を仕上げていきます。特に、工業製品の精度を左右する部分であるため、SK材の加工は多くのメーカーにとって不可欠です。例えば、自動車や電子機器の部品などに使われる精密部品は、この加工を経て、その性能が保証されます。最終的には、穴あけとフライス加工を通して、設計通りの正確な寸法と仕上がりを実現したSK材の部品が完成します。この一連の流れは、製品の品質を決定づけるため、2023年現在も変わらずに製造現場で重視されています。
3. 異なる材料の切削加工方法
SK材の穴あけからフライス加工までの流れは、工程の精度が最終製品の品質を左右するため、重要です。穴あけ加工では、SK材の種類に応じたドリル選びが必要となり、切削速度や送り速度の調整も精密な製品を作るためには不可欠です。例えば、穴あけ加工後のバリ取りは、次のフライス加工に影響を及ぼすため、丁寧に行わなければなりません。フライス加工においても、切削条件の設定や工具の選択が製品の精度に大きく関わってきます。このように、各工程は互いに関連しながら、製品の品質を形成していくのです。したがって、SK材の穴あけからフライス加工までの一連の流れは、精度の高い製品を生産する上で欠かせないプロセスであり、各段階での注意深い作業が求められます。
4. 高硬度鋼SK材の切削加工ポイント
SK材の穴あけからフライス加工までの流れは精密な作業が求められる。まず、高硬度を持つSK材の穴あけには、正確な位置決めと速度制御が必要不可欠であり、特にドリルの選定には注意を要する。例えば、超硬ドリルやコーティングドリルを使用し、冷却液を適切に使いながら加工を進めることで、材料の硬さに対応した穴あけが可能となる。次にフライス加工では、カッターの種類や刃の数、送り速度を調整し、高い精度での加工を目指す。具体的には、マルチフルートカッターや高送りカッターを用いて、加工負荷を分散しながら効率良く材料を削り取ることができる。この一連の流れは、SK材を使った精密部品製造において、品質の高さを保つために非常に重要である。
5. 穴あけ加工機械の選び方
穴あけ加工からフライス加工までの一連の工程は、製造業における基本的かつ重要なプロセスであり、2023年現在もその流れは進化を続けています。まず、適切な穴あけ加工機械を選択することが肝要です。これには、加工する材料の種類、必要な穴の大きさや精度、生産効率などが考慮されます。例えば、小さな穴を大量に、かつ高精度で加工する場合、高速かつ高精度なマシンニングセンタが好ましい選択となるでしょう。また、大型のワークを扱う場合は、それに適したサイズと機能を持つ機械を選ぶ必要があります。適切な機械を選ぶことで、製品の品質向上と生産効率の最適化が図れ、これが後のフライス加工の精度にも直接的な影響を及ぼします。結果として、適切な穴あけ加工機械の選定は製品の品質を決定づけ、コスト削減にも寄与する重要なステップであると言えます。
6. SK材穴あけ機械の人気ランキング
SK材の穴あけからフライス加工にいたるまでの流れは、精密な工程を要するため、専門知識と高度な技術が必要です。まず、材料であるSK材に対して設計図に基づき穴あけを行います。この段階で正確な位置決めが求められ、穴あけの精度がその後の工程に大きく影響します。続いてフライス加工により、穴あけで生じたバリを取り除いたり、寸法を調整したりします。ここでの精度も製品の品質に直結するため、高い技術力が必要となります。実際に2023年には、この一連の流れを効率良く、かつ高精度に行える新しい機械が市場に登場しており、それらは多くの製造現場で採用されています。これらの機械の活用によって、SK材の加工精度が向上し、より高品質な製品作りに貢献しているのです。
7. 旋削加工とフライス加工と穴あけ加工の違い
旋削加工、フライス加工、穴あけ加工はいずれも金属加工の基本的な方法ですが、適用される作業内容と用途に違いがあります。旋削加工は円筒形状の材料を加工する際に用いられ、工具が材料を削り取ることで形状をつくります。フライス加工は平面や曲面など複雑な形状に用いられる加工方法であり、複数の刃を持つ工具が材料に対して移動することで加工します。一方で穴あけ加工は、文字通り材料に穴を開けるための作業であり、ドリルやエンドミルなどの工具を使用します。例えば、自動車のエンジン部品や航空機の構造体にこれらの加工方法が用いられています。それぞれの加工方法が持つ特性を理解し適切に選択することで、高品質な製品の製造が可能になります。
8. 機械加工の基礎知識
SK材の穴あけからフライス加工までの工程は精密かつ効率的に行われるべきです。まず、穴あけとは、ドリルを使用して材料に円形の穴を開ける作業のことです。SK材においては、硬質で精密な加工が必要とされるため、特別なドリルビットや冷却油の使用が求められます。次にフライス加工とは、フライス盤を用いて材料の表面を削り取り、所望の形状や表面仕上げを実現する工程です。SK材の場合、一般の材料よりも切削条件を慎重に選定し、高い精度を維持することが重要です。例えば、航空宇宙部品などの精密なアイテムを作成する際には、これらの工程が適切に実施されることが不可欠です。最終的には、穴あけからフライス加工までの一連の流れを通じて、高品質な製品を生産することが、SK材加工の目標となります。
9. マシニング加工の詳細
2023年におけるSK材の穴あけからフライス加工までの一連の工程は、精密な製品製造に不可欠です。まずは穴あけ加工がスタートです。正確な寸法を測り、材料の特性に合わせたドリルを選定します。次に、フライス加工が行われます。ここでは、回転する刃物を用いて、余分な材料を削り取り、製品の形状を整えます。この工程では、工具の選定や速度設定が品質を左右します。具体的には、自動車部品や航空機のコンポーネントなど、精度が求められる分野で頻灹に行われます。最終的には、加工された部品が無駄なく、かつ高い精度で完成することが目指されます。この一連の加工フローが、効率的で高品質な製品作りを実現する鍵であると言えます。
まとめ
SK材を使用した穴あけやフライス加工は、高精度な加工が求められるため、専門的な知識や技術が必要です。穴あけでは適切な切削条件や工具の選定、冷却潤滑剤の使用が重要です。一方、フライス加工では適切な刃先形状や切削速度、切り込み量などを考慮する必要があります。2023年版の最新技術を取り入れた効率的な加工方法を学んで、高品質な製品を生産しましょう。
【工業用】SK材での穴あけ・フライス加工のコツと注意点
工業用の加工において、SK材を使った穴あけやフライス加工について興味はありませんか?これからSK材を利用した加工を行う方や、より効率的な方法を模索している方にとって、この記事は必見です。SK材での加工においてのコツや注意点について詳しく解説していきます。穴あけやフライス加工に関する基礎知識から、具体的な作業手順まで、本記事で分かりやすく解説します。さらに、成功するためのポイントや失敗を回避するための注意点も含めて、SK材を使った加工について幅広くカバーします。
1. SK 穴あけフライス加工の基本
SK材を利用した穴あけおよびフライス加工は、その高硬度と耐摩耗性から、工業用加工において広く用いられています。正確な加工を実現するためには、いくつかのコツと注意点を押さえておく必要があります。まず、適切な加工機を選ぶことが大切です。SK材の硬度に適した機械でなければ、ツールの損耗が早まったり、加工精度が落ちる原因となります。また、ツールの選定にも気を配るべきです。SK材用に設計されたドリルやエンドミルを使用し、切削速度や送り速度は材質の特性に合わせて慎重に設定する必要があります。具体的な例として、穴あけ加工時には切りくずの排出がスムーズに行われるよう工夫し、フライス加工では一度に削り取る材料の量(切込み量)を調節して、ツールへの負荷を最小限に抑えることがポイントです。これらのコツを踏まえ、正確かつ効率的なSK材の穴あけ・フライス加工を実現しましょう。
2. 工業用穴あけ工具の選択基準
工業用のSK材を使用した穴あけやフライス加工を成功させるためには、正しい工具の選択と加工方法の理解が不可欠です。SK材は硬度が高く耐摩耗性に優れるため、通常の材料より正確な加工が必要とされます。例として、穴あけ加工では、SK材の硬さに適合したドリル選びが重要です。高速度鋼や超硬合金製のドリルは、SK材の硬度に対して優れた切削能力を発揮します。また、フライス加工では、切削速度や送り速度を適切に設定することが肝要であり、これによって切削抵抗を適切に管理し、ツーリングやワークの損傷を避けることができます。最終的には、正確な加工を実現するためには、適切な工具選びと加工パラメータの調整が大切であり、これによって加工の品質と効率が向上すると結論付けられます。
3. SK材料の特性と穴あけ加工
工業用SK材を用いた穴あけ・フライス加工は、その特性を理解することが加工の成功に繋がります。SK材は硬質で耐摩耗性に優れ、精密な加工に適している一方で、加工ミスが起こりやすい材料でもあります。穴あけ加工の際は、適切なドリル選びが重要です。SK材に合った刃先角度と高速度鋼(HSS)や超硬ドリルの使用が、精度よく穴を開けるコツです。また、切りくずの排出を促進するための冷却液の利用も欠かせません。フライス加工では、カッターの選定に加え、切削速度と送り速度の適正な設定が品質を左右します。具体的な例として、刃の数が多ければ多いほど仕上がりは滑らかになりますが、切削抵抗が大きくなるため、その分送り速度を落とす必要があります。最後に、SK材の加工では、ツールの状態をこまめにチェックし、摩耗や損傷に気を付けることが品質を保つためには不可欠です。これらのコツと注意点を守れば、SK材の加工精度を高めることができるでしょう。
4. 電動ドリルと穴あけドリルの選び方
工業用SK材における穴あけ・フライス加工は精密で高品質な製品を作るために欠かせない工程です。SK材は炭素工具鋼として知られ、硬度が高く、耐摩耗性に優れていますが、その分加工が難しい特性も持っています。適した工具の選定が重要で、例えば穴あけには高速度鋼(HSS)ドリルや超硬ドリルが推奨され、フライス加工にはコーティング付きのエンドミルを使用すると良いでしょう。また、適切な切削速度や送り速度を見極めることも大切です。具体的には、SK材に合わせた低〜中速での加工が望ましく、加工時の冷却液の使用も、材料の焼け付きを防ぎ、工具の寿命を延ばす点で重要です。最後に、加工後のバリ取りも品質を左右するため、丁寧な仕上げ作業にも注意を払う必要があります。このように、SK材の加工にはいくつかのコツと注意点がありますが、これらを守ることで高品質な製品が作れることでしょう。
5. フライス加工技術の進展
SK材での穴あけやフライス加工は、工業用途では必須の技術ですが、その加工にはいくつかのコツと注意点があります。まず、SK材は硬質で耐磨耗性が高いため、高い精度と品質の穴あけ加工を実現するには、専用の工具選定と適切な切削条件の設定が重要です。例えば、ドリルの先端角や刃の形状をSK材向けに最適化する、または、フライス加工においては、切削速度や送り速度などを材質に応じて調整することが必要です。具体例としては、SK材の硬度に合わせた超硬質ドリルを用いることで、摩耗を抑えつつ、効率的な加工が可能となります。フライス加工では、粉塵の発生を抑えるための冷却液の使用や、切りくずの排出効率を考慮した工具パスの設計が重要となります。結論として、適切な工具の選択と切削条件の最適化がSK材の穴あけ・フライス加工の成功には不可欠です。これらのポイントを押さえることで、加工品質の向上や工具の寿命を延ばすことができます。
6. 穴あけ加工におけるウォータージェットの活用
工業用のSK材を使用した穴あけやフライス加工では、精度と効率を重視するためにいくつかのコツと注意点があります。まず、SK材は硬質で高い耐久性を持っているため、適切な工具選びが重要です。硬度に見合ったドリルやフライスカッターを使用し、切削速度と送り速度を適正に設定することが求められます。具体的には、高い切削速度での加工は避け、材料に合ったスピードで丁寧に加工を進める必要があります。また、加工の際には冷却液の使用を忘れずに。これにより、工具の熱ダメージを防ぎつつ、仕上がりの品質を高めることができます。冷却液が適切に使用されていないと、工具の摩耗が早まり、精度が低下する原因にもなります。このような点を注意してSK材の穴あけ・フライス加工を行うことが、製品品質の向上に直結します。
7. 穴あけ作業の効率化ツールとアクセサリー
SK材における穴あけやフライス加工は、精密な作業を要求されるため、適切なアプローチが重要です。SK材は硬質でありながらも加工性が良いため、工業用途に広く用いられています。しかし、その硬さが原因で加工ツールへの負担が大きくなりがちです。適正な切削条件の選定や、切削液の使用は、効率的な加工と工具の寿命を延ばす上で不可欠です。たとえば、ドリル加工においては、過度な送り速度や回転数は避け、SK材の硬度に適したドリルの選択が求められます。また、高精度を要するフライス加工では、クーラントの流量や種類に注意を払い、熱による変形や工具の摩耗を防ぐことが重要です。これらのコツと注意点を守ることで、SK材の加工はより効率的かつ高品質な結果をもたらします。
8. 穴あけ加工の安全管理と環境対策
工業用SK材の穴あけやフライス加工を行う際には、正確さと細心の注意が必要です。まず、適切な工具の選択が重要であり、SK材の硬度や加工する穴のサイズに応じて適切なドリルやエンドミルを選ぶことが基本です。例えば、小さい穴加工には微細加工用ドリルを、大きな穴には高トルクのマシニングセンターを用います。また、加工中に発生する熱を軽減するための冷却剤の選択も、品質を保持する上で不可欠です。具体的には、油性冷却剤がSK材の熱伝導を助け、工具の寿命を延ばし、仕上がりを向上させます。最終的には、これらの適切な工具と冷却剤の使用によって、精密な加工が可能となり、SK材を用いた部品の品質維持に寄与します。このように、工具と冷却剤の選択が、SK材加工の成功には不可欠であると言えるでしょう。
9. ケーススタディ: SK材を用いた穴あけフライス加工の実例
SK材での穴あけ・フライス加工には、適切な工具選びと加工方法の習得が重要です。SK材は特に硬度が高く、加工時には工具の摩耗が早まるため、硬質で耐熱性のある工具を選ぶ必要があります。例えば、タングステンカーバイド製のドリルやエンドミルが効果的です。また、切削速度や送り速度の調整は、SK材の性質に合わせ慎重に行う必要があります。具体的な例として、加工時には切削油を適量使用し、加熱による変質を防ぎながら、刃の冷却を行うことが挙げられます。最終的には、精度の高い加工を実現するためには、これらのコツと注意点を熟知し、適切に適用することが不可欠です。
10. 新技術の展望: SK 穴あけフライス加工の未来
工業用SK材を用いた穴あけやフライス加工は、精密かつ効率的な加工が求められる場面で欠かせない技術です。この技術のポイントは、適切な工具の選定と加工条件の最適化にあります。例えば、SK材は硬質であるため、工具の耐久性や切削速度を考慮した選定が必要です。具体的には、鋭利な刃を持つ超硬合金製のドリルやエンドミルが適しています。また、冷却液の使用は、摩擦熱による材料の損傷や工具の摩耗を防ぐ上で効果的です。しかし、冷却液の選択にも注意が必要で、SK材に適したタイプを使用する必要があります。最後に、適切な速度と送りで加工することで、仕上がりの精度を高め、工具寿命を延ばすことができます。これらのコツと注意点を押さえることで、SK材の穴あけ・フライス加工は、より効果的で長寿命な加工を実現します。
まとめ
SK材を使用した穴あけやフライス加工において、適切な切削条件や工具の選定が重要です。加工時には適切な冷却や潤滑を行うことで工具の寿命を延ばし、高品質な加工面を得ることができます。また、加工時の振動や切りくずの排出にも注意が必要です。機械の操作には細心の注意を払い、正確な加工を心がけましょう。
S45C加工のプロが教える!穴あけフライス加工の正しい進め方
S45C加工のプロが教える!穴あけフライス加工の正しい進め方、あなたの加工技術を向上させるためのガイド記事をお届けします。本記事では、S45Cとは何か、穴あけフライス加工とはどのようなものか、そして正しい進め方について詳細に解説します。S45C加工における穴あけフライス加工の基本から実践的なテクニックまで、あなたの技術向上の手助けとなる情報を提供します。S45C加工に携わる方々にとって、必読の内容となるでしょう。
1. S45Cの基本的理解:炭素鋼の用途と特徴
S45Cの材料を用いた穴あけフライス加工は、製造業における精密加工の一つとして重要です。まず、S45Cは日本工業規格で定められた炭素鋼であり、その特性から多様な産業で用いられる汎用材料であることを理解することが肝心です。S45Cは、優れた機械的特性と耐摩耗性を持ち合わせており、特に歯車や軸などの部品製造に適しています。穴あけフライス加工では、これらの特性を生かし、正確な穴の位置決めと寸法を保証するため、適切な工具選定と加工条件の設定が求められます。例えば、切削速度や送り速度、クーラントの使用は、加工の精度を左右する要素です。最終的には、S45C材料の特性を十分に理解し、適切な加工技術を用いることで、耐久性のある高品質な製品を創出することができます。この流れを守ることで、穴あけフライス加工の正確性と効率性を高め、製品の信頼性を向上させることが可能です。
2. 工作機械の基礎:フライス盤のABC
S45C材を加工する際の穴あけフライス加工は、品質と効率を両立させる重要な工程です。この加工の正しい進め方は、高品質な製品を作るために不可欠です。まず、加工する際には適切な切削条件の選定が必要となり、これには切削速度や送り速度、さらには適切な冷却液の使用が含まれます。具体的な例としては、S45C材に適した刃物として、チップの形状や材質を見極めることが挙げられます。また、ワークに余計な負担をかけないためにも、切削のバランスを整えたり、フライス盤の精度を常にチェックしたりすることが必要です。最終的には、これらの条件を適切に管理することで、加工精度を高め、生産性を向上させながら、S45C材の穴あけフライス加工を成功に導くことができます。
3. S45CとSS材料:違いと特性比較
穴あけフライス加工において、S45C材料はその加工性の良さから多くの製造業界で利用されています。結論から言えば、S45Cにおける穴あけフライス加工は正しい手順を踏むことで、効率的かつ高精度に行うことが可能です。その理由は、S45Cが一定の硬度を持ちつつも、適度な靭性を備えているため、切削加工がしやすい特性を持っているからです。具体的な例としては、ドリルの選定では、材料の硬度に適した刃先角度を持つものを選ぶことや、フライス加工に際しては、切削速度や送り速度を材料の特性に合わせて適切に設定することが挙げられます。結論として、S45C加工においては、材料の特性をしっかりと理解し、それに合わせたツール選定と加工条件の設定が成功の鍵となります。
4. S45C穴あけフライス加工のステップバイステップガイド
S45C材料の加工では、穴あけフライス加工が一つの重要なプロセスです。正しい方法で進めることで高精度な加工が可能になります。まず、作業を始める前には適切なフライスを選択することが肝心です。S45Cは炭素鋼の一種で硬度が高いため、硬質のフライス工具を使用することが推奨されます。次に、フライスの回転数や送り速度を、材料の硬度や加工する穴のサイズに応じて最適化することが大事です。例として、小さな穴を加工する際には高い回転数を、大きな穴を加工する際には低い回転数を選ぶと良いでしょう。また、クーラントや潤滑油を適切に使うことで、切削抵抗を減らし、工具の寿命を延ばすことができます。最終的には、フライス加工後の仕上がりをチェックし、必要に応じて仕上げ工程を施すことで、高い水準の製品を生産することができます。この一連のプロセスを正確に実行することで、S45C材の穴あけフライス加工においても優れた結果を得ることができるのです。
5. 結晶粒の超微細化とS45C加工への影響
S45C材の加工において穴あけフライス加工は最適な手法とされています。その正しい進め方を理解することが、加工精度を向上させる鍵です。まず、S45C材は炭素鋼であり耐摩耗性に優れているため、工具への負担が大きくなります。そのため、適切な工具選定と切削条件の最適化が不可欠となります。例えば、高速度鋼や超硬合金製のドリルを使用し、低速かつ高トルクでの加工を行う等が挙げられます。さらには、工具の摩耗を適時にチェックし、冷却潤滑剤を適切に使用することも重要です。これにより、S45C材特有の硬さと引っ張り強度に対応した穴あけ加工が行え、精度の高い製品を生産できるのです。結論として、S45Cの穴あけフライス加工では、適切な工具選定と切削条件の最適化、工具管理が良品質を実現するために必須です。
6. ツーリングの選択とフライス盤操作のコツ
S45C材の穴あけフライス加工を正しく進めるためには、適切なツーリングの選択とフライス盤の操作が重要です。まず、結論からいうと、S45C材への穴あけには硬度にマッチしたドリルの選定が必須です。S45Cは炭素鋼であり、一定の硬度を有しているため、加工時には耐摩耗性や刃先の強度に優れたツーリングを選ぶ必要があります。具体例として、高速度鋼(HSS)製やコーティングが施されたドリルは、S45C加工において高いパフォーマンスを発揮します。さらに、フライス盤操作では、回転数の適正な設定がカギを握ります。過度な速度はドリルの消耗を早めるだけでなく、作業精度の低下を招く可能性があるため、材質やドリルの特性を理解した上での設定が求められます。最終的には、こうした適切なツーリングの選択と機械操作により、S45C材の穴あけ加工は正確かつ効率的に行えるのです。
7. S45C穴あけフライス加工でのトラブルシューティング
S45Cの穴あけフライス加工において、正しい進め方を理解することは、加工トラブルを未然に防ぎ、製品品質を保つ上で極めて重要です。まず、S45Cのような炭素鋼は硬度が高く、適切な工具選択が必要不可欠であるという点が挙げられます。例えば、高速度鋼(HSS)や超硬質合金のフライスカッターなどが適した工具の一例です。さらに、切削速度や送り速度、冷却液の使用も、加工精度に直結するため、各パラメータは慎重に設定する必要があります。実際の加工現場では、低い回転速度での加工開始や、段階的に負荷をかけていくことで、熱影響を最小限に抑え、工具の磨耗や材料の変形を防ぐことができます。正しい進め方を把握し、具体的な操作を行うことで、S45Cの穴あけフライス加工における品質と効率は大幅に向上します。
8. よくある質問:S45C穴あけフライス加工についてのQ&A
S45C加工での穴あけフライス加工は工業分野で広く利用される技術です。正しい進め方を理解することで、加工精度の向上と作業効率を高めることができます。具体的には、適切な工具選定や切削条件の設定が重要です。例えば、フライス加工にはS45C材料に適したドリルやエンドミルの使用が推奨され、低速での回転と冷却液の適切な使用が必要です。また、段階的な加工を行い、直径が大きい穴を開ける場合にはピロットホールを先に開けるといった工夫が求められます。これらの適切なプロセスを踏むことで、S45C素材の特性を活かした精密な穴あけが可能となります。最終的には、正しい知識と技術の適用により、耐久性と品質が保証された製品を製造することができるのです。
まとめ
S45Cのフライス加工において、正しい穴あけの進め方は重要です。まず、適切な切削条件と工具を選択することが重要です。適切な切削速度や切削量を確保することで、高精度な穴あけ加工が可能となります。また、適切な冷却や潤滑も加工品質に影響します。熱や振動による歪みや刃先の摩耗を防ぐためにも、適切な冷却・潤滑を行いましょう。
フライス加工の新常識!SK材穴あけの精度を高めるテクニック
「フライス加工の新常識!SK材穴あけの精度を高めるテクニック」をご覧いただき、ありがとうございます。フライス加工における穴あけ作業は、製品の精度や品質に大きな影響を与えます。そこで本記事では、SK材を対象とした穴あけの精度向上のためのテクニックについて解説いたします。これからSK材の加工を行う際には、ぜひこの新たな常識を取り入れて、高い精度と品質を実現してください。
1. SK 穴あけ フライス加工の概要
フライス加工におけるSK材の穴あけ作業は、その精度の高さで知られています。この作業の成功は材質の均一性や工具の正確性といった多くの要因に左右されますが、特定のテクニックを用いることでさらなる精度向上を図ることができます。たとえば、適切な切削条件の選定、先端技術を駆使したフライス工具の利用、そして工具経路の最適化などが挙げられます。これらはSK材を使用した穴あけにおいて、均一で精密な結果を出すために極めて重要です。実際にこれらのテクニックを用いた多くの現場では、製品の品質向上につながっています。結論として、SK材の穴あけにおいて、これらのテクニックを習得し適用することは、加工精度を高め、製品品質を向上させるために不可欠です。
2. 切削加工の基本
フライス加工におけるSK材の穴あけは、精密な作業が求められるため、新しい工夫が常に求められています。SK材の穴あけにおいては、具体的なテクニックを用いることで加工の精度を大幅に向上させることが可能です。例えば、適切な切削速度の選定、穴あけ時の振動を抑制するための工具の選択、冷却液の適切な使用などが挙げられます。これらのテクニックを用いることで、SK材の穴あけ作業における微妙なズレやバリの発生を抑え、より高い精度での加工が実現します。よって、これらの工夫を積極的に取り入れることで、品質の高い製品を効率良く生産することができるようになるのです。
3. 異なる材料とSK 穴あけ フライス加工性の比較
フライス加工においてSK材の穴あけは、その精度の高さから新しい常識となりつつあります。従来の加工に比べてSK材を使用することで、摩擦が少なく、耐熱性に優れているため穴あけ時の精密性が向上します。具体的な例として、SK材を用いた加工では、冷却液の使用量を減らすことが可能であり、工具の摩耗を抑えつつ繊細な穴加工が可能になります。また、高硬度の材質ながらも優れた機械的特性を持つため、長時間の加工にも耐えることができ、コストパフォーマンスにも寄与します。これらの理由から、SK材は穴あけフライス加工における精度向上のための鍵となる材料です。結果として、精密な加工が求められる現代製造業でSK材の使用はますます一般的になることが予想されます。
4. SK 穴あけ フライス加工の先進技術
フライス加工におけるSK材穴あけの精度を高めることは、製造業にとって重要な課題です。SK材は硬く耐摩耗性に優れているため、一般的な加工材料より加工が難しくなります。しかし、適切な技術を用いることでこれらの課題を克服し、高精度な穴あけが可能になります。具体的には、適切な工具選択、切削条件の最適化、そして高精度なマシン設定が重要です。例えば、SK材専用のドリルを使用することで、材料特有の硬さに対応し、摩耗を最小限に抑えつつ精度良く穴あけすることができます。また、切削速度や送り速度を材料特性に合わせて調整することで、加工面の仕上がりを改善し、寸法精度を向上させることができます。これらのテクニックを駆使することで、SK材穴あけにおける精度は飛躍的に向上し、製造業の品質向上とコスト削減に貢献することになるでしょう。
5. 高硬度鋼SK材の切削加工のコツ
フライス加工でSK材に穴をあける際の精度を高めるには、適切な加工技術の選択が重要です。SK材は硬度が高いため、通常の加工方法では精度を確保することが難しいです。そこで、専用の刃物を選び、適切な切削速度と給送速度を設定することが肝心です。例えば、超硬合金やコーティング加工された刃物を使用することで、切れ味を保ちながらSK材を効率良く加工することが可能になります。また、加工時の振動を抑えることで、加工面の粗さを低減し、精度を向上させることができます。このように、適した工具と加工条件の選定を行うことで、SK材穴あけの精度は著しく向上することでしょう。最適なツールと加工条件を選ぶことで、SK材穴あけの精度向上が期待できます。
6. 旋盤加工の基礎とSK 穴あけ フライス加工への応用
穴あけフライス加工において、SK材の使用は精密な作業に不可欠です。SK材とは、工具鋼の一種であり、高い硬度と耐摩耗性を持つことから、穴あけ加工において優れた性能を発揮します。具体的には、SK材の刃先が鋭いため、加工物に対して精度良く穴を開けることが可能になります。例として、時計のギア加工など、微細な部品に要求される高精度な穴あけにSK材が用いられています。また、SK材を使用することで切削条件を最適化し、長寿命で安定した加工を実現することができるため、コスト削減にも寄与します。このように、SK材を活用した穴あけフライス加工は、精度と効率の両面で新たな常識となっています。
7. マシニングセンターを使ったSK 穴あけ フライス加工
SK材の穴あけにおけるフライス加工技術は、精度の向上が求められる新常識といえます。SK材は硬質で加工が難しい特性を持っているため、従来の方法では精度の高い穴あけが困難です。そのため、マシニングセンターを利用した専門のテクニックが開発されました。例えば、適切な切削速度の選定や、冷却液をうまく使った加工方法などがあります。これにより、従来よりも綺麗で精度の高い穴を実現することができます。このような新しいテクニックを取り入れることで、SK材の加工効率を上げるとともに、製品の品質を向上させることが期待されます。結論として、SK材の高精度な穴あけを実現するためには、マシニングセンターを用いた先進的なフライス加工技術が不可欠となっています。
8. SK 穴あけ フライス加工のトラブルシューティング
フライス加工におけるSK材の穴あけ作業は、製造業においてその精度が非常に重要視されています。SK材を利用した穴あけ加工の精度を向上させることは、製品の品質向上へ直結するためです。具体的なテクニックとしては、適切な刃先の角度の選択、冷却剤の使用、そして加工速度の調整が挙げられます。特に刃の角度は、材料の硬さに応じて最適化することが重要で、SK材のような硬質材の穿孔には尖った角度よりも鈍角が好まれます。加えて、適切な冷却剤の利用は摩擦熱を抑え、切削精度を高めるだけでなく刃の消耗も抑える効果があります。さらに、加工速度を材質や厚みに合わせて調整することで、バリの発生を抑え、穴の仕上がりを向上させることができます。これらのテクニックを組み合わせることで、SK材の穴あけにおける精度は飛躍的に向上し、最終的な製品品質に大きな差をもたらすのです。
9. SK 穴あけ フライス加工の将来性と発展
フライス加工におけるSK材の穴あけ作業は、その精度が製品品質に直結するため非常に重要です。ここで紹介するテクニックは、SK材の穴あけ精度を向上させるために役立ちます。まず、適切な工具選択が肝心です。SK材の硬さに対応した硬質のドリルを使用することで、材料へのダメージを減らし、仕上がりの精度を高めることができます。また、冷却液の使用は切削温度の上昇を防ぎ、SK材の変形を最小限に抑えることにも繋がります。加えて、穴あけ加工時の送り速度や回転数の正確な管理も、精度向上には不可欠です。これらのテクニックを駆使することで、SK材の穴あけ作業の精度は格段に向上し、高品質な製品を安定して提供することが可能になります。このような穴あけの精度向上は、製造現場での生産性の向上にも直結し、フライス加工の新たな常識となっていくでしょう。
まとめ
フライス加工におけるSK材の穴あけでは、適切な切削条件と工具の選定が重要です。適切な切削条件を選定することで、穴あけ時の精度を向上させることができます。また、切削油や冷却水の使用も効果的です。穴あけの工程において、加工精度を高めるためには、工具の適切な選定と切削条件の最適化が必要です。
【精密加工】SK材とフライスを使った穴あけ手法の全知識
大量生産に対応するため、精密加工の需要が増加しています。今回は、SK材とフライスを使用した穴あけ手法について詳しく解説します。穴あけ工程で使用されるSK材の特性やフライス加工の基本、さらには効率的な手法まで、全ての知識を網羅しています。精密加工に興味がある方や新しい手法を探している方にとって、役立つ情報が満載です。
1. SK 穴あけ フライス加工の基本概念
SK材を使った穴あけ加工にフライスを活用する技術は、精密な加工が求められる場面での重要な役割を果たしています。この手法は、SK材の高硬度とフライスの精密な動きを組み合わせることにより、必要とされる寸法や形状の穴を正確に加工することができます。例えば、自動車の部品製造や医療機器のコンポーネントなど、極めて高い精度が求められる分野でこの手法が用いられています。フライスによる加工方法は、刃の形状や回転速度などを細かく設定できるため、微妙な調整が可能であり、多様な加工ニーズに応えることが可能です。このように、SK材とフライスを用いた穴あけ加工は、精度と効率を高めることに貢献しており、その技術の進展は今後も多くの産業での応用が期待されています。
2. 金属加工における材料選定の重要性
精密加工において材料選定は製品の品質を左右する重要な要素です。SK材は特に硬度が高く耐摩耗性に優れた工具鋼として知られ、穴あけ加工において優れた成績を示します。これにフライス加工を組み合わせることで、精度の高い穴を効率良く加工することが可能になります。例えば、工業部品や精密機械に必要な微細なピンホールを作る場合、SK材を利用したフライス加工はその精密さから選ばれます。最終的な製品の品質を保つためにも、正確な材料選定と加工方法の選択が不可欠であり、SK材とフライスを使った加工法はその一つの有効な手段なのです。
3. SKシリーズ鋼材の特性と選定
SK材を使用した精密加工においては、その特性を理解し選定することが重要です。SK材は炭素工具鋼の一種であり、硬度が高く耐摩耗性に優れているため、フライス加工においても優れた性能を発揮します。この材質は穴あけ加工時の精度を保ちやすく、工具の摩耗に強いため、長期にわたって安定した加工が可能です。例えば、小さなピンホールから大きな径の開口部まで、SK材はさまざまなサイズの穴あけに対応できます。フライスを用いた場合、複雑な形状や微細な仕上がりも期待でき、高精度な製品作りには欠かせない技術です。最終的に、SK材の正しい選定とフライスを使用した穴あけ技術は、精密加工において品質の向上と生産性の向上に直結し、工業製品の高度化に貢献しています。
4. フライス加工の基礎知識
精密加工においてSK材を使用し、フライスを活用する穴あけ手法は、その高い加工精度により注目されています。SK材は硬度が高く耐摩耗性に優れ、フライスによる穴あけ加工では複雑な形状や細部まで正確に仕上げることが可能です。例えば、精密機械の部品製造においては、微細な公差を要する部分に対して、この手法が適しています。これにより、フライスを用いたSK材の穴あけは、自動車産業や航空機産業など、さまざまな分野で重宝されています。最終的に、この技術によって製品の信頼性が高まり、産業全体の競争力強化に寄与しているのです。
5. SK 穴あけ フライス加工の技術的詳細
SK材を使った穴あけとは、硬質で耐摩耗性に優れたフライス加工技術の一種です。この方法は、精密な加工が求められる製品に適しており、例えば自動車や航空機の部品製造に不可欠です。SK材は高い硬度を持つため、工具への負担が大きい作業にも耐えうることが特徴です。また、フライス加工により、穴の径や深さを正確に制御することができます。具体的には、高速回転するフライスカッターが材料の表面を削りながら進むことで、円滑で均一な穴を形成します。この技術は、小さな穴から大きな穴まで、様々なサイズの加工が可能で、その精度は数ミクロン単位で管理されています。このように、SK材とフライス加工を組み合わせた穴あけ手法は、高い精度と耐久性を実現し、多くの産業で重宝されているのです。
6. フライス加工における切削条件の最適化
フライス加工における切削条件の最適化は、精密な穴あけ加工において非常に重要です。SK材(工具鋼)を使った穴あけでは、正確な穴の径や表面粗さを実現するため、切削速度や送り速度、カッターの種類などの条件を適切に設定することが求められます。例えば、SK材は硬度が高く耐磨耗性に優れているため、高速での切削が可能ですが、適切な冷却がなければカッターの摩耗を早め、加工精度に影響を及ぼすことがあります。また、選択するフライスカッターによっても、仕上がりの品質が左右されます。最適化された切削条件によって、効率よく高精度な穴あけを実現することができます。結果として、工具の寿命を延ばし、製造コストを削減することにもつながるため、切削条件の見直しは、穴あけ加工の品質向上に不可欠です。
7. 炭素工具鋼(SK)の加工事例
精密加工において、炭素工具鋼(SK)材とフライスを使った穴あけ手法は、高い精度と効率を求める製造業界で非常に重要です。SK材は硬度が高く、耐摩耗性に優れているため、精密な加工が可能になります。フライス加工では、回転するカッターが材料の表面を削り取ることで穴をあけるため、非常に滑らかな内壁を実現できます。例えば、自動車のエンジン部品や時計のギアなど、精密さが求められる部品の製造には、この方法が頻繁に使用されます。穴のサイズや形状に合わせてフライスカッターを選ぶことで、さまざまな要件に対応できるため、応用範囲が広がります。したがって、SK材とフライス加工を駆使した穴あけ技術は、精度と効率の追求において、製造現場で不可欠な存在であると結論づけられます。
8. フライス加工機の種類と選定
フライス加工におけるSK材を用いた穴あけ手法は、高精度な加工を可能にする重要な技術です。SK材とは、工具鋼の一種であり、優れた耐摩耗性と硬度を持つことから、切削工具に適しています。穴あけ加工においては、SK材製のドリルなどが用いられ、フライス加工機と組み合わせて使用されます。この組み合わせにより、金属などの硬い素材に対しても正確かつ効率的に穴を開けることができます。たとえば、精密機械の部品製造において、フライス加工機は不可欠であり、SK材のドリルを使用することで、要求される公差内での穴径と位置精度を実現することが可能です。最後に、SK材とフライス加工機の選択は、加工する素材や仕上がりの質に大きく影響を与えるため、その選定には注意が必要です。この技術は高い生産性と品質を保証し、日本の製造業においてもその価値が高いと結論付けられます。
9. SK 穴あけ フライス加工の応用と革新
精密加工の分野で、SK材を使用した穴あけにはフライス加工が欠かせません。SK材料は硬く、耐摩耗性に優れた特性を持っているため、精密な加工を実現します。フライス加工では、多様なカッターが使用され、複雑な形状や非常に小さな穴の加工も可能になります。例えば、時計の部品製造などの精密機械には、微細な穴が均一かつ正確に開けられる必要があり、SK材とフライス加工の組み合わせが重宝されています。この技術のおかげで、高い精度が求められる医療器具や自動車部品などの産業分野でもSK材の穴あけ加工が広く用いられています。そのため、フライス加工はSK材を利用した精密加工分野で不可欠な技術と言えるでしょう。
10. 精密部品加工におけるSK材の役割
精密加工の世界では、SK材を用いたフライス加工による穴あけが不可欠です。SK材は炭素工具鋼とも呼ばれ、硬度と耐摩耗性に優れています。これにより、長時間の使用においても精度の高い加工が可能となり、工業製品の品質向上に寄与しています。例えば、自動車や航空機の部品など、高度な精度が要求される分野でSK材のフライス穴あけは活躍しています。この手法により、極めて小さな公差で穴を開けることが可能であり、精密部品の組み立てにおいても高い信頼性を確保できます。結論として、SK材とフライス加工による穴あけは、精密部品加工における重要なプロセスであり、その精度と効率は産業全体に大きな影響を与えています。
11. メンテナンスとトラブルシューティング
精密加工の世界では、SK材を使用したフライス加工による穴あけ手法が重要な位置を占めています。SK材は工具鋼の一種であり、耐久性と硬度が非常に高く、精密な加工が可能です。フライス加工を用いることで、様々な大きさや形状の穴を精密に開けることができます。具体的な例として、機械部品の微細な通気孔や複雑な形状のギア内への穴などが挙げられます。これらは手作業では困難であるため、SK材とフライス加工の組み合わせは、精密性が要求される工業製品には不可欠な技術と言えるでしょう。最終的には、これらの加工手法により製品の品質と機能性が向上し、結果として産業全体の発展に貢献しています。
12. 今後のSK 穴あけ フライス加工技術の展望
SK材を用いた穴あけやフライス加工は、その高精度と効率性から、今後も製造業における不可欠な技術であると言えます。SK材は硬く、耐摩耗性に富んでいるため、正確な穴あけ加工が可能です。具体的には、フライスを使用することで、複雑な形状や非常に狭い部分への穴あけも実現でき、これがSK材を用いる理由の一つです。加えて、フライス加工の進化により、より複雑なデザインの実現が可能になり、例えば、航空宇宙産業や自動車産業での要求される部品製作においては、この技術が中心的な役割を果たしています。最終的には、SK材とフライス加工技術の併用は、品質の向上、生産性の向上に直結し、製造業の発展を支える重要な柱となるでしょう。
まとめ
SK材を使用してフライス加工を行う際には、適切な切削条件や工具の選定が重要です。適切な切削条件を設定することで、正確な穴あけ加工が可能となります。また、工具の選定によって加工精度や作業効率が大きく変わるため、十分な検討が必要です。SK材の特性やフライス加工の基本知識を理解した上で作業に取り組むことが重要です。
「SK 穴あけ加工」徹底解説!プロが推奨する正確な技術とは?
「SK 穴あけ加工」に興味はありますか?プロが推奨する正確な技術とは?この記事では、SK 穴あけ加工の徹底解説を行います。穴あけやフライス加工に関する正確な技術やプロのノウハウを知りたい方にぴったりの内容です。SK 穴あけ加工について知りたい、技術を磨きたいと考える方々へ、ぜひお役立てください。
1. SK 穴あけ フライス加工とは?
SK穴あけフライス加工は、精密かつ効率的な加工技術として現場のプロに推奨されています。これは、金属等の素材に対して特定のサイズの穴を開けるために使用される技術です。理由としては、穴あけ加工後の仕上がりがきれいであり、また加工精度が非常に高い点が挙げられます。例えば、機械部品や電子部品などの製造において、極めて正確な穴の位置とサイズが求められる際に、SK穴あけフライス加工は大きな強みを発揮します。それに加え、工具の摩耗が少なく、長期間にわたり安定した加工が可能であるため、コストパフォーマンスにも優れています。以上の点から、SK穴あけフライス加工は、高精度が要求される工業製品の生産において非常に重要な技術と言えるのです。
2. 難削材へのSK 穴あけ加工の基礎
SK穴あけ加工は、難削材への加工においてその精度と効率が高く評価されています。この技術は特にフライス加工において重要で、高硬度材料に対しても確実に穴を開けることが可能です。具体的な例を挙げると、金型の製造や自動車部品の加工において、SK穴あけ加工はその正確性が求められます。これは、微細な公差を必要とするパーツにおいて、どれだけ正確に穴を開けることができるかが重要な指標となるからです。このような精密な作業では、SK穴あけ加工がその強みを発揮し、製品の品質向上に直結します。結論として、SK穴あけ加工はプロが推奨する技術であり、精度と効率を兼ね備えた加工方法として、多くの産業で非常に重宝されているのです。
3. プラスチック素材のSK 穴あけ加工テクニック
SK穴あけ加工は、精密な部品製造において欠かせない技術です。この加工技術は、特にフライス加工を用いた方法であり、工具としてのSK (スピードカッター) が用いられます。その正確さから、多くのプロが推奨する技術となっています。例えば、電子部品や自動車部品などの微細な穴加工において、SK穴あけ加工はその精度と効率性で高い評価を受けています。この技術の特徴は、素材に与える熱影響が少なく、精密な穴を安定して開けることができる点にあります。その結果、加工品の品質を一定に保ちながら、生産効率を高めることが可能です。細かな穴の加工が求められる現代の製造業において、SK穴あけ加工はますますその重要性を増していくことでしょう。
4. ドリルガイドSKの選び方と通販情報
穴あけ加工において、正確性を求められる工程であることは間違いありません。その中でも、「SK 穴あけフライス加工」は特に精度が重視される作業です。この技術が推奨される理由として挙げられるのが、その高い位置決め精度と均一な穴径です。例えば、高精度が必要とされる自動車のエンジン部品や航空機の構造部材においては、微細な誤差も許されないため、SK 穴あけフライス加工が求められます。加工時に使用されるドリルガイドSKは、その精密さが重要視され、適切なものを選ぶことが極めて重要です。通販情報を得る際には、製品の品質を保証する信頼性の高いメーカーから購入することをお勧めします。こうした厳格な基準を満たすSK 穴あけフライス加工は、正確な穴あけを実現するために不可欠な技術として、多くのプロフェッショナルから推奨されています。
5. ケガキ工具の種類とSK 穴あけ加工での利用方法
「SK穴あけ加工」とは、正確無比な穴開けを可能にする技術です。この技術は、特に精密な加工が必要とされる分野で強みを発揮します。利用する工具の選定こそが、SK穴あけ加工のカギとなり、フライス加工において重要な役割を担います。たとえば工業製品の部品など、微細な寸法の誤差も許されない製品を作る際には、SK穴あけ加工による精度の高い穴開けが不可欠です。そのためには、正確なケガキ工具の選択が求められます。工具の種類は多岐にわたりますが、それぞれの加工物に適したものを選ぶことで、理想的な成果をもたらすことができるのです。最終的に、適切な工具と技術を組み合わせることで、SK穴あけ加工はその真価を発揮し、高い精度の穴加工を実現します。
6. 穴開け工具のおすすめとSK 穴あけ フライス加工の人気ランキング
「SK穴あけフライス加工」は精密な穴開け作業に不可欠な技術であり、プロからも高い推奨を受けています。この加工法の大きな利点は、その正確性にあります。特に金属やプラスチックなどの硬質材料において、正確な穴径と滑らかな内壁が要求される場合には、SKフライスを使った加工が適しています。例えば、機械の部品での精密な組み合わせや、エレクトロニクス業界での小さいながらも高精度な穴あけなどが挙げられます。加えて、SKフライス加工では切削速度が高速でありながらも、材料への負荷が少ないため、効率よく作業を進めることが可能です。結論として、SK穴あけフライス加工は、精度と効率を兼ね備えた方法であるため、多くの専門家によって推奨されているのです。
まとめ
SK穴あけ加工は、精密な加工が求められる工程であり、正確な技術と装置が必要です。フライス加工を利用することで、高い精度と品質を実現することができます。プロが推奨する正確な技術を学び、適切な装置を使用することで、効率的かつ高品質な加工を行うことが可能です。