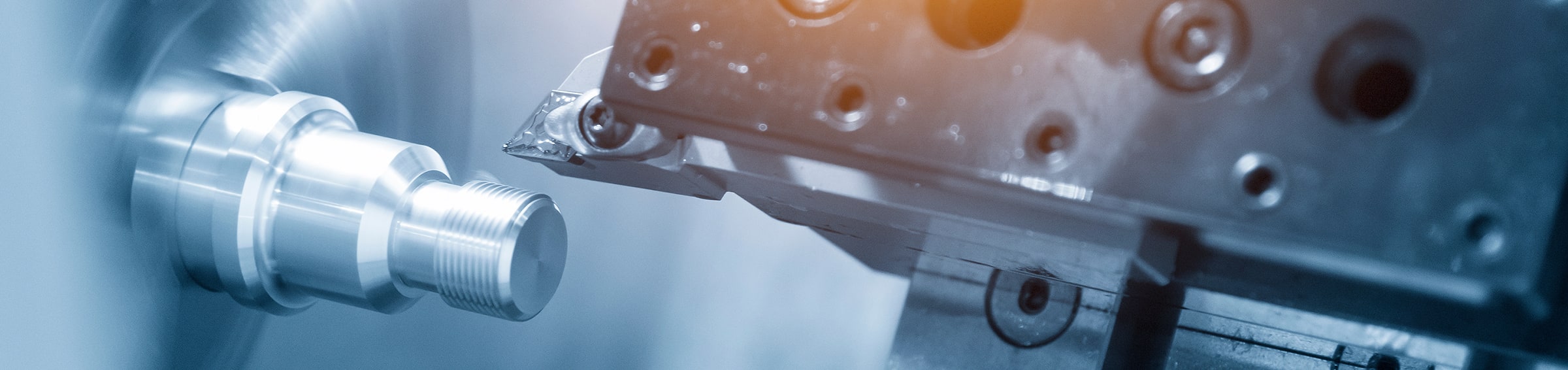
コラム column
穴あけ加工の王道!SKDフライス加工で求められる精度とは?
SKDフライス加工は、現代の製造業界で欠かせない技術の一つです。穴あけ加工においても、その精度は非常に重要です。しかし、その精度を求められる理由や具体的な要件は理解しにくいかもしれません。この記事では、SKDフライス加工における穴あけ加工の王道について掘り下げ、求められる精度やその重要性について解説します。加工技術に興味のある方や穴あけ加工の精度を向上させたい方は、是非ご覧ください。
Introduction
SKDフライス加工は穴あけ加工の中でも高精度が求められる分野です。特に、精度の要求される工業製品が多い日本では、SKDフライス加工の需要は高く、その理由にはいくつかのポイントがあります。まず、絶対的な精度の確保は、部品の互換性を保つ上で非常に重要であり、これによって組立ての際の手間が省け、生産効率が向上します。具体例としては、自動車や航空機の部品に見られるように、一貫した品質と正確な寸法が求められる場面では、SKDフライス加工が重宝されます。さらに、耐久性にも大きく寄与し、完成した製品の信頼性を高める要因となっています。したがって、精度を極めた穴あけ加工が求められるなかで、SKDフライス加工はその王道を行く技術と言えるでしょう。
1. SKD 穴あけ フライス加工の基本
SKDフライス加工は、機械部品製造において不可欠な技術であり、その精度は極めて高いレベルが求められます。フライス加工における穴あけ作業は、寸法精度や表面粗さといった品質が製品の性能に直結するため、その精度管理は製造現場において重要なポイントとなっています。具体的な例としては、自動車部品や精密機械のギアなど、微細ながらも高い耐久性を要する部品でSKDフライス加工が活用されています。こうした部品では、数マイクロメートル単位での誤差も許されないため、SKDフライスでの穴あけ加工は厳密な品質基準に従って行われます。結論として、SKDフライス加工で要求される精度は極めて高く、製品の信頼性を保証するためには、この高い水準を維持することが必須です。
2. マシニング加工とフライス加工の違い
SKDフライス加工は、穴あけ加工の分野で高い精度が要求される理由として、その信頼性と効率性が挙げられます。SKDとは特殊鋼の一種であり、耐摩耗性や強度が高いため、工具に用いられることが多いです。このSKDを使ってフライス加工を行う場合、精度が重要視されるのは、製品の品質や機能性を決定づけるためです。例えば、自動車業界では部品の寸法精度が極めて重要であり、わずかな誤差も許されません。SKDフライス加工によって、こうした高い要求を満たすことができるのです。また、耐久性の向上によりメンテナンスの頻度を低減し、コスト削減にも寄与します。したがって、SKDフライス加工で必要とされる精度は、産業全体の生産効率と品質向上に直結していると言えるでしょう。
3. 精度要求の見直しとコストダウン
SKDフライス加工は、その高精度さから穴あけ加工の最適解として広く認識されています。SKD加工において重要なのは、製品の品質を決定づける精度の高さです。特に、金型や機械部品などの製造において、ミクロン単位の公差で要求されることが一般的です。例えば、自動車産業におけるエンジン部品の加工などは、非常に厳しい寸法精度が求められる場合が多く、SKDフライス加工がその精度要求を満たす上で選ばれる理由となっています。しかしながら、この高精度を保ちつつコストを抑えることは、製造業者にとって大きな挑戦です。最新のCNC技術を使い、より効率的かつ経済的な方法で精度を守りながら加工を行うことが求められています。結論として、SKDフライス加工は精度が求められる穴あけ加工の分野において、その精度とコストのバランスに注意しつつ選択されるべき方法です。
4. 旋盤加工とSKD フライス加工の違い
SKDフライス加工が穴あけ加工で重宝されるのには明確な理由があります。この加工方法は、素材へのダメージを最小限に抑えつつ、高精度の穴を開けることが可能です。具体的には、SKDフライス加工で作成する穴は、その滑らかな表面と均一な寸法が求められます。例えば、精密機械の部品製作において、わずかな誤差も許されない状況下では、この高精度な加工技術が不可欠です。さらに、複雑な形状や狭いスペースの加工にも対応できる柔軟性を持っており、様々な産業でのニーズに応えることが可能です。結論として、SKDフライス加工が求められる精度は、極めて高いレベルであり、多岐にわたる用途において、精密かつ効率的な加工を実現するための王道技術であると言えるでしょう。
5. アルミニウム合金のSKD 穴あけ加工と切削剤の関係
穴あけ加工の中でも特に品質が求められるのがSKDフライス加工です。加工面の精度は製品の品質を大きく左右し、特に精密機械部品や自動車部品などの製造において重要視されます。SKDフライス加工で期待される精度は、公差±0.01mm程度と非常に高いレベルです。これは、紙の厚みがおよそ0.1mmであることを考えると、紙の十分の一の厚さの範囲で加工する必要があることを意味します。実際の製品例を見ても、自動車のエンジン部品や航空機の部品など、高い耐久性と信頼性が求められる分野で幅広く採用されています。これらの部品は、微細な寸法誤差が大きな問題を引き起こす可能性があるため、SKDフライス加工による高い精度が不可欠なのです。結論として、SKDフライス加工はその高い精度により、多くの産業分野で必須の技術とされており、精密な穴あけ加工を実現するためには、極めて緻密な工程管理が求められます。
6. 高硬度鋼のSKD 切削加工のコツ
穴あけ加工の分野で求められる精度の高さはSKDフライス加工においても重要です。SKD加工とは、工具鋼の一種であるSKD11やSKD61といった高硬度の鋼を用いた加工のことで、耐摩耗性や耐熱性が求められる部品作りに不可欠です。これらの材質を使い、一定の厚みを持つ板に複数の穴を空ける際には、穴のサイズや位置の精度が極めて重要になります。例えば、自動車や航空機の部品などでは、穴の位置が微妙にズレるだけで組み立てが不可能になったり、安全性に影響を及ぼす可能性があるため、高い精度が要求されます。そのため、SKDフライス加工では、加工機の精度はもちろん、刃物の選定、冷却剤の使用といった加工条件が徹底され、精度の高い加工が実現されています。穴あけ加工においてSKDフライス加工が王道たる所以は、このような高精度な成果を出すための細部にわたる注意とテクニックから成るのです。
7. SKD 穴あけ フライス加工の応用事例
SKDフライス加工において求められる精度は非常に高い。これは、工業製品の部品としての機能や耐久性を確保するためには、厳密な寸法と形状が求められるからである。例えば、自動車のエンジン部品や航空機のタービンブレードなど、要求される精度が非常に厳しい製品にはSKDフライス加工が不可欠であり、これにより、製品の寿命を延ばすと同時に安全性を高めることができる。穴あけ加工の一環として、SKDフライス加工は、その精密さから多くの製造業界で重宝されており、特に高精度が要求される機械の部品製造においては欠かせない技術の一つである。結論として、SKDフライス加工は製品品質の向上に直結し、産業全体の信頼性維持に寄与していると言える。
8. SKD 穴あけ フライス加工の将来展望
SKDフライス加工は、その高い精度が求められる加工方法の一つです。この加工技術は、特に要求される寸法精度や形状精度が非常に高く、工業製品の品質向上に不可欠です。例えば、自動車のエンジン部品や航空機の部品に用いられることが多く、ミクロン単位の精度が要求される場合があります。これらの部品が正確でなければ、製品全体の性能に影響を及ぼす可能性があるため、SKD加工には高い精度が求められるのです。また、耐摩耗性や熱処理による硬度の向上など、材料への要求も厳しいため、高品質なフライス加工を実現するためには、優れた技術と適切な工具選択が不可欠です。これにより、SKDフライス加工は精密な穴あけ加工の王道としての地位を確立し、今後も多くの分野での需要が見込まれます。
まとめ
SKDフライス加工は、穴あけ加工の王道として広く利用されています。この加工方法では、高い精度が求められます。穴あけの位置や深さ、直径など、厳密な仕様に応えるためには、適切な工具選びや工程管理が欠かせません。また、加工対象の素材によっても異なるため、それぞれの特性を理解し、適した操作を行うことが重要です。
【工業加工】SKDでの穴あけ・フライス加工のコツと注意点
加工業界でSKDでの穴あけやフライス加工を行う際、初心者から上級者まで必要とされるコツや注意点についてご紹介します。SKD加工は精密さが求められるため、正しい技術と知識が重要です。何をすべきか、どのように進めるべきか、この記事では初心者の方々にも分かりやすく解説します。加工技術を向上させ、より効果的で正確な作業を行いたい方は、ぜひお読みください。
1. SKD 穴あけ加工の基本
SKDでの穴あけ加工を行う際には、正確さと品質が求められます。SKDは工具鋼として広く利用されており、その耐摩耗性と硬度の高さから穴あけには特有の工夫が必要です。まず、適切なドリルの選択が重要であり、SKDの硬さに対応した超硬ドリルやコーティングドリルの使用が望ましいです。次に、適切な切削速度と送り速度の設定が成功のカギを握ります。速度が遅すぎると作業効率が落ち、速すぎると工具の磨耗や破断につながります。また、冷却剤の使用は、摩擦熱による影響を最小限に抑え、加工精度の向上に役立ちます。フライス加工では、カッターの選定にも注意が必要で、SKDの硬さに合わせた刃先の形状や材質を選ぶことが大切です。最後に、こまめな工具点検と交換を行い、常に良好な加工状態を保つことが求められます。これらのポイントを押さえることで、SKDにおける穴あけ・フライス加工の品質と効率を高めることができます。
2. 高硬度材料SKDにおける穴あけのテクニック
高硬度の金属材料であるSKDの加工においては、正確で丁寧な穴あけ・フライス加工が不可欠です。加工における最大のポイントは、適切な工具の選択と加工パラメータの調整にあります。SKD加工専用の工具を使用することで、材料の硬さに対応した切削が可能になり、摩耗や工具の破損リスクも軽減されます。特に、穴あけ加工では、スピンドルスピードやフィードレートを材質に合わせて慎重に設定する必要があります。例えば、小径のドリルビットを使用する際は高速回転を避け、切削油を適切に供給することで、熱の発生を抑え、仕上がりの精度を高めることができます。フライス加工では、切削抵抗を考慮した刃の数や形状を選定し、不規則な負荷がかからないようにすることも必要です。最終的には、これらのコツと注意点を踏まえた加工技術によって、SKDの穴あけ・フライス加工の質を高めることができるのです。
3. SKD11の穴あけ加工条件の選定
SKDの穴あけやフライス加工には特有のコツと注意点があります。SKDを使用した加工の際、耐摩耗性や硬度が高いため、工具への負担が非常に大きいです。したがって、切削工具の材質選びや刃の状態を常にチェックし、専用の硬質コーティングを施した工具の使用が推奨されます。さらに、SKD加工においては低切削速度と高トルクが必要であり、熱管理も重要です。適切な冷却液を使用し、加工中の熱を適切に逃がすことで、切削精度を保ちながら工具の寿命を延ばすことができます。例として、フライス加工の際には一貫した送り速度を保ちつつ、過度の加圧を避けることが重要です。最終的には、これらのコツと注意点を踏まえた上で、実際の加工条件を細かく調整することにより、SKDでの高品質な穴あけ・フライス加工が実現します。
4. 異なる種類のSKD 穴あけ加工手法
工業加工においてSKDでの穴あけやフライス加工は精密さと効率が求められる技術です。穴あけ加工では、事前に材質の硬さや切削速度を考慮することが重要であり、フライス加工では刃の選定や進行方向に注意が必要です。例えば、SKD材は硬いため通常の鋼材を加工する時よりも低い速度で加工する必要があり、また、耐熱性の高い刃を選ぶことが切削精度を保つコツです。加工時には、刃の摩耗を常にチェックし、必要に応じて交換することで、品質の高い加工を継続することが可能です。フライス加工では、刃の進行方向が反時計回りか時計周りかによっても仕上がりに差が出るため、目的に応じて適切な方法を選択することが大切です。最終的に、これらのコツと注意点を守ることで、SKDにおける穴あけ・フライス加工の品質を向上させることができます。
5. 熱処理済みSKD材の穴あけ加工
SKD材の穴あけ加工は、正確で美しい仕上がりを求められる工業加工の一環です。この作業のポイントは、熱処理によって硬度が増したSKD材を使用する際の適切な切削条件の選定にあります。まず、工具はSKD材の硬さに対応できるよう、超硬合金やコバルトハイスなどの耐久性の高いものを選ぶべきです。また、切削速度は適度に抑え、冷却液を適切に使用することが重要です。特に、熱処理後の材料はその硬さから、加工時の熱の影響を受けやすいため、冷却液を使用して熱を逃がしながら加工することが、品質を保つ秘訣と言えます。実際の事例として、冷却液を充分に使用しなかったことで工具の摩耗が早まり、加工精度が落ちたという報告は数多くあります。ですから、穴あけ加工においては冷却管理を徹底し、定期的な工具の点検を行うことが大切です。これらを守ることで、SKD材の穴あけ加工は効率よく、かつ高品質な結果を出すことが可能になります。
6. SKD 細穴加工の特別な考慮事項
SKDにおける穴あけ及びフライス加工は、耐摩耗性や強度などの特性を持つ材料を使用しているため、適切な加工方法と注意が必要です。処理を行う際は、適切な切削工具を選び、切削速度や送り速度を材料の硬さに応じて調整することが重要です。例えば、硬度が高い材料では低い切削速度を用いると工具の摩耗を減らすことができます。また、冷却液を適切に使用することで、切削面の仕上がりを良くし、加工時の熱ダメージを防ぐことができます。特にSKD材では、加工時に発生する熱により硬化する特性があるため、冷却には十分注意を払わなければなりません。最適な加工条件の下で加工を行うことにより、製品の品質を維持しながら効率的に作業を進めることができるのです。
7. SKD 穴あけ加工のトラブルシューティング
SKDでの穴あけやフライス加工は高精度な工業製品を生産する際に不可欠です。これらの加工の成功の鍵は、適切な工具選びと加工条件の調整にあります。特にSKD材は硬度が高いため、工具の摩耗が激しくなる傾向があります。効率的な加工のためには、耐摩耗性に優れたコーティングつきのドリルやエンドミルを使用すると良いでしょう。また、SKD材の加工には、低速での切削や、冷却液を適量使用するなど、熱による影響を抑える工夫も必要です。こういった専門的な加工を行う際には、加工前に材料の特性を理解し、ツールパスの設計を丁寧に行うことが重要です。最終的には、これらのポイントに注意しながら慎重に加工を進めることが、SKD加工の品質を決めると言えます。
8. SKD フライス加工の基礎と応用
SKDでの穴あけ・フライス加工は、金属加工における基本中の基本です。適切な加工がなされた場合、製品の精度や強度を大きく向上させることができます。そのためには、適切な工具選びと加工条件が重要です。具体的には、SKD材での作業には高速度鋼や超硬合金のドリルやエンドミルが適しており、切削速度や送り速度、切り込み量を材質や形状に応じて適切に設定する必要があります。また、切削油の使用は、摩擦熱を軽減し、工具の寿命を延ばす上でも重要です。例えば、硬い材質であるSKD11では、フライス加工する際には特に冷却効果の高い切削油を使用すると良いでしょう。最終的には、これらのポイントを押さえることで、SKDでの穴あけ・フライス加工の精度を高めることが可能です。
まとめ
SKDを使用した穴あけやフライス加工においては、適切な工具選びや切削条件の設定が重要です。適切な切削油を使用し、適正な切削速度や切削深さを設定することで、加工精度を向上させることができます。また、穴あけにおいては適切な冷却を行うことで工具の寿命を延ばすことができます。加工時の振動や刃先の摩耗にも注意が必要です。
【工業加工】SKDでの穴あけ・フライス加工のコツと注意点
工業加工における穴あけやフライス加工は高度な技術や知識が必要ですが、SKDを活用することでより効率的かつ正確な加工が可能となります。本記事では、SKDを用いた穴あけやフライス加工のコツや注意点について解説します。加工技術の向上を目指す方々にとって、ぜひ参考にしていただければと思います。
1. SKD穴あけ加工の概要
SKDでの穴あけ加工は、金属加工の現場でよく適用される技術です。穴あけの正確性が製品品質に直結するため、コツと注意点を押さえることが重要です。まず、鋼材の硬度に適したドリル選びが基本で、ドリルの刃先角度やスピードも材質に応じて調整する必要があります。具体例としては、SKD材を加工する際には、高い硬度と耐摩耗性を持つコーティングドリルの使用が推奨されます。加工時には冷却液を適切に使用し、熱によるドリルの損傷や変形を防ぐことも大切です。最後に、加工後のバリ取りを怠らないことで、製品の精度をさらに高めることができます。結論として、SKDでの穴あけ加工は適切な工具選びと加工条件の調整、アフターケアが品質に大きく影響するため、これらのポイントをしっかりと押さえておく必要があります。
2. SKD穴あけ加工の方法と技術
SKDにおける穴あけやフライス加工には特有のコツと注意点があります。まず、SKDは耐摩耗性や硬度が高い材質であるため、穴あけやフライス加工を行う際には高い精度が要求されます。具体的には、適切な工具の選定が重要になります。鋭い刃を持つ高速度鋼や超硬材質のドリルやエンドミルを使用し、また、適切な切削速度と送り速度を見極めることが肝心です。例えば、不適切な速度で加工を行うと、工具が摩耗しやすくなり、加工精度が低下するだけでなく、製品の寿命にも影響を及ぼします。更に、冷却液の適切な使用は、加工時の熱を効果的に逃がし、工具の寿命を延ばす上で不可欠です。このように、SKD材を加工するには正しい知識と技術が必要とされますが、それらを把握することで高品質な製品を効率よく製造することが可能になります。
3. SKD高硬度材料の穴あけ加工の最適条件
SKDとは、一般的な工具鋼の一種であり、高硬度と耐摩耗性を持つため、穴あけやフライス加工において特有の加工コツが求められます。まず、SKD材料の高硬度に応じて適切なドリルやエンドミルを選択することが重要です。硬い材料には、高速度鋼(HSS)よりも超硬合金の切削工具が適しています。次に、切削速度や送り速度などの加工条件を正確に設定することが肝心です。具体的には、切削速度を低めに設定し、工具の摩耗を防ぐために冷却液を適量使用することが推奨されます。また、フライス加工では、切りくずの除去が円滑に行われるように工具の形状に注意し、工具の刃数を増やすことで切削抵抗を分散させることも有効です。SKD材料加工のコツを抑え、適切な注意点を守ることで、精度の高い加工が可能になります。
4. SKD11の穴あけ加工条件について
SKD素材における穴あけやフライス加工には特有のコツと注意が必要です。SKDは耐摩耗性に優れた工具鋼であり、特にSKD11は硬度が高く加工が困難です。そのため、適切な工具の選定、切削スピード、送り速度の管理が重要となります。例えば、超硬ドリルやコーティングドリルの使用が推奨され、フライス加工には、切削油を適切に使用し冷却しながら行うことがキーポイントです。また、加工時には工具の摩耗にも注意を払い、定期的な交換を行うことで精度の高い加工を維持できます。最終的には、SKDでの穴あけ・フライス加工は、材料の特性を理解し、適正な条件で慎重に行うことが成功への近道です。
5. 異なる穴あけ加工の種類
SKDでの穴あけやフライス加工には特有のコツと注意点があります。これらの工程は、工具の選定や工程の精度が製品の品質に大きく影響します。例えば、穴あけ加工の際にはドリルの刃の摩耗に注意し、適切な冷却液の使用は刃の寿命を延ばし、精度の高い加工を保証するのに役立ちます。フライス加工においても、切削速度と送り速度のバランスを適切に保つことが重要です。これにより、加工面の仕上がりが良く、工具の摩耗を抑えることができます。とりわけSKDでは、硬度が高い材料を扱うため、工具の選定や加工条件の設定には特に慎重な検討が必要です。穴あけ・フライス加工の知識と経験を活かすことで、製品の品質を向上させつつ、効率的な生産を行えるでしょう。
6. SKD穴あけ加工におけるねじ加工のコツ
SKDでの穴あけやフライス加工は、正確さと丁寧さが非常に重要です。SKD素材は硬度が高いため、加工時には工具の摩耗や被加工面の品質に気をつける必要があります。例えば、穴あけ加工では、ドリルの切削速度や送り速度を適切に設定することが重要です。これにより、過度な加工熱を避け、工具寿命を延ばすことができます。フライス加工においても、カッターの選定や冷却剤の使用がキーポイントです。特に、複雑な形状の加工や精度を要する場合は、細心の注意を払って作業を行うべきです。また、加工後のバリ取り作業にも丁寧に取り組むことで、高品質な仕上がりを実現することができます。最終的には、これらのコツと注意点を実践することで、SKD素材の加工を成功に導くことが可能です。
7. SKD材料におけるパイプ穴あけの技術
SKD材を使用した穴あけ・フライス加工は、工業加工分野において重要な技術であり、その品質が製品の精度に直結します。まず、SKD材に適した工具選びが重要です。合金鋼のため、高い硬度を持ち、通常の工具では摩耗しやすい特徴があります。そのため、超硬合金やコーティング加工された工具の使用を推奨します。次に、適切な切削条件を見極めることが大切です。切りくずの排出を効率的に行いつつ、熱の発生を抑えるためには、回転速度や送り速度を調整する必要があります。具体例として、穴あけの際には低速で安定した加工を心がける、フライス加工では高い切削速度で一定の深さを保つといった方法が挙げられます。最後に、加工に際しては冷却液の適切な使用も欠かせません。これにより、工具の摩耗を防ぎ、加工面の仕上がりを良くすることができます。結論として、SKD材料における穴あけ・フライス加工を成功させるには、適切な工具の選定、切削条件の最適化、冷却液の効果的な利用が重要です。
8. 熱処理材の穴あけ加工
SKDは一般的な熱処理材であり、工業加工において穴あけやフライス加工が頻纍する分野です。熱処理によって硬度が上がったSKDを加工する際は、適切な工具選びが成功の鍵となります。具体的には、超硬合金やコーティングされたドリルやエンドミルを使用し、切削速度と送り速度を適切に設定することが重要です。また、冷却液の使用は、切削時の熱を抑え、工具の耐久性を保つためにも欠かせません。実例として、一部の製造現場では、SKDの硬さに合わせてドリルの先端角を調整し、フライス加工では刃数が多い工具を選ぶことで、加工精度を高めています。最適な工具と加工条件を見極めることが、高品質な穴あけ・フライス加工を実現させるためには必須で、再度結論を述べれば、SKD加工の成功は適切な工具選びから始まるのです。
9. 細穴の穴あけ加工技術とSKD材料への応用
SKDでの穴あけ・フライス加工は、精密性と耐久性が要求される工業加工の一環です。この加工には、正確な知識と技術が必要とされます。まず、SKD材料は硬度が高く、耐摩耗性に優れているため、加工工具には高い負担がかかります。従って、適切な工具の選定が重要であり、超硬合金やコーティングされた工具の使用が有効です。例えば、フライス加工では、カッターの刃先の角度や切削速度を適切に設定することで、耐久性に優れた切断が可能になります。また、冷却剤の利用も、加工精度の向上と工具寿命の延長に寄与します。しかし、冷却剤はSKD材料に適したものを選ぶ必要があり、間違った選択は逆に加工品を損傷させる可能性があります。結論として、SKDでの穴あけ・フライス加工を成功させるには、適切な工具と冷却剤の選定、さらに細かな加工条件の最適化が不可欠です。これにより、工業製品の品質は飛躍的に向上するでしょう。
10. SKD穴あけ・フライス加工のトラブルシューティング
SKDでの穴あけ・フライス加工には、いくつかのポイントがあります。まず、適切な工具選択が重要です。SKD材は硬さと強度が特徴であるため、耐摩耗性に優れた超硬合金製の工具を選ぶことが必須です。次に、切削条件の管理もポイントです。切削速度、送り速度、カッターの径と刃数など、条件を適切に設定することで、加工精度や工具寿命の向上が期待できます。また、SKD材の加工時には、適切な冷却方法が不可欠です。工具と材料の発熱を抑え、バリの発生や工具の摩耗を防ぐためには、冷却剤を適切に使う必要があります。これらのポイントに注意し、事前にテストカットなどで加工条件を確認することで、トラブルを回避し、効率的なSKD加工を実現することが可能です。
11. SKD穴あけ・フライス加工の安全対策
SKDでの穴あけやフライス加工は、工業加工の現場で非常に一般的な作業ですが、正しい技術と注意点を知ることが重要です。まず、SKDにおける穴あけ・フライス加工の成功のコツは、適切な加工条件の選定にあります。材質に合わせたドリルやカッターの選定、正確な速度と送り速度の設定が必須です。例えば、硬度の高いSKD材を加工する際には、耐久性に優れたドリルを使用し、過度な負荷がかからないように注意する必要があります。また、冷却液の使用は、摩擦熱による材料の損傷を防ぐためにも欠かせません。このプロセスを怠ると、工具の磨耗が早まり、製品の精度が低下する原因にもなります。最後に、加工後のチェックは必ず行い、寸法の精度や表面の仕上がりを確認することで、高品質な製品が生産されることを保証します。穴あけ・フライス加工におけるこうした基本的な流れとチェックポイントを把握することが、より良い工業製品を生み出すための鍵となるでしょう。
12. 最新技術と将来の展望
SKDにおける穴あけやフライス加工は、精密な工業加工に不可欠である。その成功のカギは、正しい工具の選択と加工条件の厳密な管理にある。例えば、SKDの硬度や特性に適合したドリルやエンドミルの選定は、製品の品質を大きく左右する。また、回転速度や送り速度などの加工条件を適切に設定することが重要で、こうしたパラメーターは材質や加工形状に応じて微調整されるべきである。不適切な条件下での加工は、工具の破損や加工面の粗さを引き起こす可能性があるため注意が必要だ。まとめると、SKDでの穴あけ・フライス加工を成功させるには、適切な工具選びと正確な加工条件の設定が不可欠である。この2点に注意を払うことで、高品質な製品製造が可能となる。
まとめ
SKDでの穴あけやフライス加工において、適切な工具や切削条件の選定が重要です。材料に合わせた適切な切削速度や刃先の設定、冷却液の使用などがコツとなります。また、適切な固定具や治具を使用することで、加工精度を高めることができます。一方で注意が必要な点としては、過剰な加工負荷や刃先の摩耗による加工精度の低下が挙げられます。適切なメンテナンスと工具の取り扱いにも注意が必要です。
SKD穴あけ加工を完璧に!効率的なフライス選定ガイド
『SKD穴あけ加工を完璧に!効率的なフライス選定ガイド』をご覧の皆様、SKD穴あけ加工において効率的なフライス選定が重要であることはご存知でしょうか。本記事では、スキルアップを目指す方々のために、SKD穴あけ加工におけるフライス選定のポイントや効率的な方法について紹介しています。穴あけ作業におけるフライス加工のテクニックや注意点、そして適切なフライス選定のための具体的なガイドをご提供することで、作業効率と品質向上に繋がる有益な情報をお届けします。
1. SKD穴あけフライス加工の基礎
SKD穴あけ加工では、適切なフライス選定が非常に重要です。精度の高い加工を実現するためには、材質や形状に最適なフライスを選ぶ必要があります。例えば、SKD材には硬さと耐熱性に優れた工具が求められます。具体的には、超硬フライスやコーティングフライスが推奨されることが多いです。これらはSKD材の硬度に対応できるだけでなく、長時間の使用においても優れた耐久性を示します。また、切れ味が鈍ることなく安定した加工が可能で、精度の高い穴あけ加工を支える重要な要素となります。適切なフライスを選ぶことで、効率的かつ経済的な加工が実現し、最終的には製品の品質向上にも寄与します。
2. 切削加工の基礎知識とSKD対応の重要性
SKD素材の穴あけ加工においては、フライス選定が非常に重要です。この選定が、加工効率と製品品質の両面に大きく影響を及ぼします。適切なフライスを使用することで、SKDのような硬質材料でも効率良く穴をあけることができるため、生産性の向上につながります。例えば、耐熱性や耐摩耗性を持つコーティングが施されたフライスは、SKD加工時の熱問題を軽減し、工具寿命を延ばすことができます。また、切れ刃の形状が最適化されたフライスは、切削抵抗を減らし、よりスムーズな加工を実現します。これらを慎重に選定することで、加工の精度を保ちつつ、スピードも保つことができるのです。結論として、SKD穴あけ加工の成功はフライス選定にかかっており、適切な工具の選定が品質と効率を向上させる鍵となります。
3. マシニング加工におけるクーラントの役割と選定
SKD穴あけ加工では、適切なフライスを選定することが極めて重要です。フライス選定が加工の効率と品質を左右し、間違った選択はコスト増加や加工時間の延長につながるためです。具体例として、SKDのような硬質材料の加工には、耐久性と精密性を兼ね備えたフライスが必要です。高速で精密な穴あけを可能にする超硬フライスや、長寿命を実現するコーティングフライスなどが選ばれます。これらは硬い材料を効率良く加工し、優れた表面仕上げを提供します。最適なフライスの選定によって、SKD穴あけ加工はより完璧に、かつ効率的になります。適切な工具を選ぶことで、最高品質の加工を実現し、生産性の向上を図ることができるのです。
4. SKD穴あけに最適なエンドミルの選定方法
SKD穴あけ加工を行う際には、適切なフライス選定が非常に重要です。なぜなら、SKDといった硬質材料を加工するには、耐摩耗性や切削性能に優れた工具が不可欠だからです。例えば、超硬質のエンドミルはSKDのような硬い材料に対して、精度の高い穴あけが可能であり、長寿命を約束します。また、コーティングの種類にも注目して選ぶことが大切です。特に、アルミチタンナイト(AlTiN)コーティングされたエンドミルは耐熱性に優れ、高速加工時の摩耗を減らすことができます。このように、適切なフライスを選定することで、SKD穴あけ加工の効率が大幅に向上し、コスト削減にも寄与するのです。最終的に、理想的な加工結果を得るためには、材料の性質を理解し、それに合わせた最適な工具を選ぶことが不可欠です。
5. マシニング加工とフライス加工の違いと応用
SKD穴あけ加工を成功させるためには、適切なフライスの選定が非常に重要です。SKD材は硬質であるため、フライス加工には特に注意が必要となります。適したフライスを使用することで、加工の精度を高めると同時に、工具の寿命を延ばすことが可能となります。例えば、超硬合金製のフライスやコーティングの施されたフライスは、SKDのような硬質材料に対して高い耐久性と優れた加工性を発揮します。これにより、製品の品質向上はもちろん、効率的な加工が期待できるため、コスト削減にも繋がります。最適なフライス選定によって、SKD穴あけ加工の精度を確保し、製造現場の生産性向上に寄与することは間違いありません。
6. コストダウンとVA/VEにつながるSKD穴あけフライス加工の工夫
SKD穴あけ加工において最適なフライス選定は、コスト削減やVA/VEへの貢献が期待できるため重要です。SKD材は硬いため加工が難しく、適切なフライスを用いないと工具の摩耗が激しくなる一方で、製品の精度にも影響します。例えば、超硬合金製のフライスは高硬度材料の加工に優れた耐久性を持ち、長寿命化に貢献するため適しています。また、切削条件を最適化することで、工具寿命を延ばし加工効率を高めることも可能です。結果として、フライスの選定によっては、SKD穴あけ加工におけるコストパフォーマンスを大幅に向上させることができるのです。総括すると、適切な工具と加工条件の見直しにより、SKD穴あけ加工はより効率的かつ経済的に進められることが明らかです。
まとめ
SKD穴あけ加工では、適切なフライスを選定することが成功の鍵です。フライスの種類や刃先数、刃先形状などを工具メーカーのデータや専門書を参考に選定しましょう。また、適切な切削速度や切り込み量、冷却方法なども重要です。これらを十分に考慮した上でフライス加工を行うことで、高品質な穴あけ加工が実現できます。
SKD穴あけ加工を完璧に!効率的なフライス選定ガイド
あなたの製造プロセスをより効率的にするために、SKD穴あけ加工の完璧なガイドを提供します。製造業界での競争が激しくなる中、フライス加工の効率化は非常に重要です。この記事では、SKD穴あけ加工における効果的な手法やツールの選定方法について解説します。製造業に従事している方やこれからこの分野に進もうと考えている方々にとって、貴重な情報が満載です。
1. SKD穴あけ加工の基礎
SKD穴あけ加工を行う際に効率的なフライス選定は、仕上がりの品質を左右する重要な要素です。SKDとは耐摩耗性に優れた特殊工具鋼の一種であり、その硬度の高さが加工においての最大の課題となります。適切なフライスを選ぶことで、加工時間の短縮と精度の向上が期待できます。具体的には、SKD加工用に設計された超硬フライスやコーティングフライスが有効です。これらはSKDの高い硬度に耐え、長寿命を実現します。また、切削速度や送り速度の適正な設定が重要であり、これにより一層の効率化が図れます。結論として、正しいフライス選定と運用によってSKD穴あけ加工は効率的かつ高品質に実行可能となるのです。
2. マシニング加工とフライス加工の違い
SKD穴あけ加工において、適切なフライスの選定は非常に重要です。フライス加工は、素材や加工条件に最適化された工具を選ぶことで、効率と精度を高めることができます。例えば、SKD材料は硬度が高いため、硬質合金やコーティングされたフライスが推奨されます。特に、穴あけ加工においては、被削材の硬さや加工速度、冷却の有無に合わせた選定が必要です。早い段階で適切なフライスを選ぶことで、工具の摩耗を抑え、長寿命化を実現し、コスト削減にもつながります。結論として、SKD穴あけ加工におけるフライスの効率的な選定は、加工品質の向上とコストパフォーマンスのバランスを最適化するために欠かせない要素です。
3. SKD穴あけフライス加工におけるクーラントの役割
SKD穴あけ加工においては、適切なフライス選定が重要です。理由は、フライスの種類によって加工の効率や品質が大きく変わるからです。例えば、適切なフライスを使用すれば、切削抵抗を低減し、摩耗を抑えることができます。これによって、工具の寿命を延ばすことが可能であり、結果としてコスト削減にもつながります。また、精度の高い穴あけ加工にはSKD特有の硬さや熱処理に適したフライスの選定が不可欠です。さらに、フライスの形状や刃数、材質にも注目し、SKD加工に最適なものを選ぶことが成功の鍵を握ります。正しいフライス選定によって、SKD穴あけ加工はより効率的かつ精度高く行えるのです。
4. エンドミル選定のための基礎知識
SKD穴あけ加工を行う際には、適切なフライス選定が重要です。SKDは加工硬度が高く、耐摩耗性に優れた工具を選ぶことで、効率良く穴あけが可能となります。具体例として、超硬合金やコーティングされたエンドミルはSKDの穴あけに適しています。これらのエンドミルは、硬い素材に対する切削性能が高く、長寿命を保ちつつ精度の高い穴あけ加工を実現します。また、エンドミルの形状や刃数を加工物の形状に合わせて選ぶことも、効率的な加工のためには不可欠です。最適なフライスを選定することで、SKD穴あけ加工の品質も向上し、コスト削減にも繋がります。結論として、穴あけ加工の効率と品質を高めるためには、適切なフライスの選定が欠かせません。
5. アルミ加工の基本とSKD穴あけフライス加工への応用
SKD穴あけ加工を行う際、適切なフライスの選定は非常に重要です。これは、フライスの特性が加工の精度や効率に直結するからです。具体例として、SKD(工具鋼)は硬度が高く加工が困難な材料であり、こういった材料を扱う際は耐摩耗性や切削性に優れたフライスを選ぶ必要があります。適切なフライス選びにより、寿命が長く、精度の高い加工が可能になります。また、作業の効率化にも繋がります。結論として、SKD穴あけ加工には材料の特性に適したフライスの選定が不可欠であり、これにより加工の品質と効率を両立させることができるのです。
6. SKD穴あけフライス加工のトラブルシューティング
SKD穴あけ加工を行う際、適切なフライスの選定は非常に重要です。その理由は、フライスが加工品質に大きく影響を与えるからです。例えば、硬度の高いSKDには、硬度に耐えうる刃物が必要とされます。適切なフライスを選ぶことで、切削速度の向上、加工精度の向上、そして工具の寿命の延長が期待できます。一方で、不適切なフライスを選択すると、切削不良や工具の破損など、加工において様々な問題が発生する可能性があります。したがって、材料の特性を理解し、それに合ったフライスを選ぶことが、SKD穴あけ加工を成功させる鍵となります。このように適切なフライスの選定によって、効率的かつ正確なSKD穴あけ加工が可能となるのです。
まとめ
SKD穴あけ加工において、効率的なフライス選定が成功のカギとなります。適切なフライスの選定によって、穴あけ加工の品質と効率を向上させることができます。素材や加工条件に応じて最適なフライスを選ぶことが重要です。加工精度や寿命、コストなどを考慮して、穴あけ加工を効率的に行いましょう。
次世代の穴あけ!SKDフライス加工による高効率技術を徹底解説
穴あけ作業やフライス加工において、SKDフライス加工という次世代の技術が注目されています。この技術は従来の方法よりも高い効率で作業を行うことができるため、多くの業界で注目を集めています。本記事では、SKDフライス加工の基本から応用までを徹底解説します。穴あけやフライス加工における最新の技術に興味がある方にとって、貴重な情報が満載です。どのような作業を行いたいのか、どのような業界で活躍したいのかに関わらず、SKDフライス加工について知識を深めたい方におすすめの一読です。
1. SKD 穴あけ フライス加工とは?
SKD穴あけフライス加工は、次世代の高効率な技術として業界内で注目を浴びています。従来の穴あけ加工方法に比べ、SKDフライス加工は素材を素早くかつ正確に加工することが可能であり、生産性を飛躍的に向上させます。その秘密は、特殊なカッターと精密な制御にあります。例えば、航空機の部品製造などでは、複雑な形状でも短時間で高精度の穴を開ける必要があり、SKDフライス加工はその要求を満たす重要な役割を果たしています。この技術は、加工時間の短縮はもちろん、工具の摩耗を減らすことでコスト削減にも寄与し、多くの製造業界で利用される可能性が高まっています。結論として、SKD穴あけフライス加工は、その高い生産効率とコストパフォーマンスから、製造業における穴あけ加工の新たな標準となることが予想されるのです。
2. SKD 穴あけ フライス加工の技術的進化
SKD穴あけフライス加工は、現代の工業界において重要な位置を占めています。この技術は、高精度かつ高効率で穴を開けることが可能であり、そのため様々な産業での需要が高まっています。従来の穴あけ技術に比べ、SKDフライス加工は、工具の摩耗を抑えつつ、より早く多くの穴を開けることができるため、コスト削減にも繋がります。例えば、自動車製造業界では、エンジンの部品などに精密な穴をあける必要があり、SKDフライス加工がその要求を満たすことができます。また、耐久性や加工速度の点で優れた性能を発揮するため、生産効率の向上にも寄与しているのです。これらの理由から、SKDフライス加工の技術は次世代の穴あけにおいて、欠かせないものとなっています。
3. 高速度工具鋼(SKD)の特性と利点
高速度工具鋼(SKD)を用いたフライス加工は、次世代の穴あけ技術として高効率を誇ります。SKDは耐熱性や硬度が非常に高く、切削工具に使用される際、その精度と耐久性を向上させることができます。例えば、一般的なフライス加工に比べて、SKDフライス加工は長時間にわたる作業でも切削性能の低下が少なく、精密な穴あけが可能です。結果として、製品の品質を保ちつつ生産性を高めることができるのです。また、工具交換の頻度が減少するため、メンテナンスコストの削減にも寄与します。このようにSKDフライス加工は、その特性を活かして高い経済性と生産効率を実現する技術として、今後の製造業において重要な役割を担っていくことでしょう。
4. マシニング加工とフライス加工の比較
SKDフライス加工とは、穴あけ加工における革新的な技術であり、従来のマシニング加工よりも効率的です。理由は、SKD技術により加工時間が短縮されるからです。例えば、ある種の部品加工では、SKDフライス加工を用いた場合、加工に必要な時間が半分以下になることが報告されています。これにより、生産性が向上し、コスト削減にも寄与します。また、精度の高い加工が可能であるため、高品質な製品作りに不可欠です。さらに、SKDフライス加工は、硬い材料にも対応可能で、耐久性のある工具を使用するため、長期にわたる使用においても安定した加工品質を維持します。結論として、SKDフライス加工は、生産性と品質の向上を実現するための次世代技術と言えるでしょう。
5. マシニングセンタのメリットとデメリット
SKDフライス加工は、次世代の穴あけ技術として高い効率性を有しています。従来の穴あけ加工法と比べ、SKDフライス加工は、その精度とスピードにおいて優れているため、様々な産業で注目されています。たとえば、自動車や航空機の部品製造において、高精度が求められる小さな穴を数多く開ける必要がある場合にSKDフライス加工は力を発揮します。これは、特殊なカッターとプログラミングを用いることで、複雑な形状や硬度の高い材料にも対応可能で、かつ加工時間を大幅に短縮することが可能だからです。この技術により、生産効率の増加とコスト削減が期待できます。まとめると、SKDフライス加工はその高精度と効率性により、今後、製造業界でより一層の普及が見込まれる技術です。
6. 切削加工の基本概念
SKDフライス加工は、高精度で効率的な穴あけが可能な次世代技術です。その理由は、特殊なフライス盤を使用することで、従来のドリル加工に比べ、時間短縮とコスト削減が実現できるからです。例えば、自動車産業において、エンジンの部品などの複雑な形状の穴を開ける際に、SKDフライス加工は大きな利点を発揮します。高速で精密な加工が可能なため、生産性の向上に直結し、製造コストの削減にも寄与します。再度強調しますが、SKDフライス加工は製造業の効率化を可能にする技術であり、今後の工業生産の現場においてさらなる発展が期待されます。
7. SKD フライスカッタの構造と耐久性
SKDフライス加工は、高効率な穴あけ技術として注目されています。この技術の大きな利点は、耐久性と精度の高い加工が可能であることにあります。SKDとは、特殊鋼の一種で、工具や金型に使用される素材です。この素材を使ったフライスカッタは、硬度が高く、熱に強いため、長時間の使用に耐えることができます。例えば、自動車産業では、エンジン部品の精密な穴あけにSKDフライス加工が用いられており、その耐久性によって生産効率の向上に大いに貢献しています。このように、SKDフライス加工は、耐久性と高い加工精度を兼ね備え、多様な産業での利用が見込まれており、次世代の穴あけ技術としての地位を確立しつつあります。
8. SKD 穴あけ フライス加工の応用事例
SKDフライス加工は、高効率かつ高精度な穴あけ技術として、製造業界で注目を集めています。この技術は、特に金属加工において優れた能力を発揮し、従来の穴あけ方法に比べて作業時間の短縮とコスト削減に寄与します。例えば、自動車産業や航空機製造において、SKDフライス加工は一度に複数の穴を正確かつ迅速に開けることが可能です。また、モールドやダイなどの耐久性を要求される金型加工においても、これらを長持ちさせるための細かな穴あけにSKDフライス加工が利用されています。このように、多岐に亘る産業での応用事例がSKDフライス加工の効率性と信頼性を証明しており、さらなる技術の発展と普及が期待されます。この穴あけ技術の未来はまさに明るく、次世代の製造業を支えるキーテクノロジーと言えるでしょう。
9. 穴あけ フライス加工の将来展望
SKDフライス加工は、高精度かつ高効率な穴あけ技術の代表例として、今、注目を集めています。この技術は、従来の穴あけ方法に比べ、材料の硬度に左右されることなく、高速でかつ精密な加工が可能です。たとえば、硬質な金属材料でも、SKDフライス加工によれば、切削抵抗が少なく、工具の摩耗も少ないため、長時間の連続作業が実現可能です。また、複雑な形状や奥行きのある穴あけにおいても、均一な仕上がりを確保できるのです。この技術を使うことで、生産性の向上はもちろん、製造コストの削減にもつながり、企業の競争力を高めます。今後、より多くの産業での導入が進めば、製造業のさらなる革新が期待されるでしょう。SKDフライス加工は、次世代穴あけ技術の中核としての地位を確立しています。
まとめ
SKDフライス加工は次世代の高効率技術であり、従来の穴あけ方法よりも効率が良く、高精度な加工が可能です。従来の方法では難しかった複雑な形状の穴あけも容易に行うことができます。加工速度や精度を求める産業では、SKDフライス加工が重要な技術となっています。
【プロ技】SK材の穴あけ加工!長寿命を実現するフライスの選び方
フライス加工において、SK材の穴あけ加工は長寿命を実現するために欠かせない技術です。本記事では、SK材を使用した穴あけ加工のプロ技に焦点を当て、適切なフライスの選び方について解説します。SK材の穴あけ加工における重要性や効果について知りたい方、長寿命を実現する穴あけ加工のポイントを知りたい方にとって、必読の内容となっています。
1. SK 穴あけ フライス加工の基本
SK材の穴あけ加工には適切なフライス選びが重要です。なぜなら、適切なフライスを選ぶことで加工精度が向上し、工具の耐久性が大幅に伸びるからです。具体的には、SK材に合った切れ味の良いフライスを選ぶことで、摩耗を減少させ、長寿命化を図れます。たとえば、高速度鋼(HSS)や超硬合金のフライスはSK材加工に適しており、材質ごとの切削特性を理解することが重要です。また、適切な切削速度や送り速度の設定は、加工効率を向上させると同時に、フライスの長寿命化にも寄与します。結論として、フライスの選び方一つでSK材の穴あけ加工の品質と効率が大きく変わるため、材質や加工条件に応じた選択が必須であるといえます。
2. 切削加工の種類と特徴
SK材の穴あけ加工において、長寿命のフライスを選ぶことは極めて重要です。この選択が加工精度やコストパフォーマンスに大きく影響を及ぼします。特にSK材は硬度が高いため、耐摩耗性に優れたフライスの選定が求められます。例えば、超硬合金製のフライスは硬い材質を加工する際の耐久性が高く推奨されます。また、工具のコーティングや刃の形状も寿命を左右する要因ですので、加工する材質や形状に合わせた仕様のフライスを選ぶことが大事です。正しいフライスを選べば、工具交換の頻度を減らすことができ、結果として生産効率の向上とコスト削減につながります。したがって、SK材の穴あけ加工の際には、材料特性に適した高品質なフライスの選定が、長寿命化を実現するための鍵となるのです。
3. SK 穴あけ フライス加工のメリット
SK材の穴あけ加工において、適切なフライスを選ぶことは、加工物の品質向上と工具寿命の長期化を実現するために不可欠です。SK材は硬度が高く、耐摩耗性に優れた特性を持つため、一般的な材料を加工する際に用いるフライスでは、早期摩耗や切削性の低下を招きがちです。具体的な例として、超硬フライスやコーティングフライスはSK材の硬度に適応することで、摩耗を抑制し、精度の高い加工を可能にします。また、カッターの刃先形状を最適化することで、切りくずの排出を円滑にし、切削抵抗を減少させる効果も期待できます。結果として、これらの選択は加工効率の向上とコスト削減にも繋がり、SK材の穴あけ加工における長寿命と高品質を実現する上で重要な要素となります。
4. 高硬度鋼SK材の穴あけにおける注意点
高硬度のSK材を加工する際、適切なフライス選びが長寿命の穴あけ加工を実現します。SK材は硬さや耐摩耗性に優れているため、一般的なフライスだと摩耗が早くなりがちです。しかし、SK材専用のフライスを選ぶことで、材料の硬さに対応し、効率的な加工が可能になります。例えば、超微粒子超硬合金製のフライスは、SK材の穴あけ加工において高い耐久性を発揮します。その結果、切削抵抗が低減し、加工精度が向上し、工具の交換頻度が減るため、コスト削減にもつながります。適切なフライス選びによって、SK材の穴あけ加工は、より効率的かつ経済的になり、長寿命の加工を実現することができます。
5. フライス加工機の選び方
SK材の穴あけ加工を行う際、長寿命のフライスを選ぶことは極めて重要です。理由は、高品質なフライスを選ぶことで、加工精度を高めると同時に、工具の交換頻度を減らし、コスト削減にも繋がるからです。具体的な例として、耐久性に優れた超硬フライスは、SK材の硬さに対しても高い耐性を示し、長期間にわたって安定した穴あけが可能です。また、コーティング技術の進歩により、摩耗や熱に強いフライスも登場しています。こうしたフライスを選定することで、加工の効率化と長寿命化が実現し、結果的に生産性の向上に寄与します。最適なフライスを選ぶことは、SK材の穴あけ加工における長寿命と高品質な仕上がりの両立に不可欠です。
6. SK 穴あけ加工用フライスの種類
SK材の穴あけ加工時に適切なフライスを選択することは、加工物の品質向上と工具の長寿命化に不可欠です。SK材は硬度が高いため、通常の材料より緻密な加工技術を要求されます。適切なフライスの選択によって、精度の高い穴加工が可能となり、工具の摩耗を抑えることができます。例えば、コーティング技術を施したフライスは、非コーティングのものに比べて耐久性が向上し、長期にわたる使用が見込めます。さらに、SK材専用に設計されたフライスは、この材質に最適化された切削角度や刃の形状を備えており、加工精度の差は歴然です。結論として、SK材の穴あけ加工には材質に適した特化したフライスを選定することが、品質とコストのバランスを最適化し、最終製品の価値を高める上で決定的な要素となります。
7. 穴あけ機械の推薦モデル
SK材の穴あけ加工において、長寿命を実現するフライス選びは非常に重要です。その理由は、SK材は硬度が高く、加工が困難な材料であるため、適切なフライスを使用しないと工具の摩耗が早くなり、精度が低下することにあります。例えば、高硬度用のコーティングが施されたカーバイドフライスは、SK材の加工時に高い耐久性を発揮します。また、フライスの刃の形状や切れ刃数も加工の効率に大きく関わり、角度が鋭角であるほど、また切れ刃数が多いほどスムーズに加工を行えます。したがって、SK材の穴あけ加工で長寿命を達成するためには、硬度に適したコーティング、最適な刃の形状、適切な切れ刃数を持つフライスの選択が肝要です。これにより、精度の高い加工を維持しつつ、工具の交換頻度を減らし、コスト削減にも繋がるのです。
8. フライスや旋盤加工時の技術的ポイント
SK材の穴あけ加工時には、適切なフライス選びが長寿命化への近道です。SK材は加工が難しい素材であるため、フライスの選定には注意が必要です。具体的には、切れ味が良く耐久性のあるフライスを選ぶことが重要です。たとえば、コーティング技術が施されたフライスは、摩擦を低減させることで、摩耗を防ぎつつ作業効率を向上させます。また、切削負荷が均一になるようなデザインのフライスは、加工物への負担を減らし、精度の高い加工を実現することができます。これらの点を考慮したフライスの選択は、SK材の加工寿命を延ばし、コスト削減にも寄与します。結論として、SK材の加工においては、適切なフライス選びが非常に重要であり、より長い工具の寿命と効率的な作業を実現するための鍵となります。
9. SK 穴あけフライス加工のトラブルシューティング
SK材における穴あけの加工は精度と効率の両立が求められますが、適切なフライス選びにより長寿命の実現が可能です。SK材は硬く、耐摩耗性が高いため、通常のフライスではすぐに摩耗してしまうという問題があります。これに対し、高硬度で耐熱性に優れたカーバイドフライスを使用することで、穴あけ加工時の摩耗を抑え、長期にわたる使用が可能となります。たとえば、一般的な高速鋼(HSS)フライスと比べ、カーバイドフライスは硬度が高く、耐久性に優れているため、SK材加工において長寿命を実現します。結果として、継続的なツール交換のコスト削減及び加工の安定性向上に寄与し、最終的には生産性の向上に繋がります。
10. 穴あけ加工の効率化とコスト削減
SK材の穴あけ加工において、長寿命で効率的なフライス選びは、工程の効率化とコスト削減に直結します。適切なフライスを選ぶことで、切削抵抗を抑え、均一な穴を安定して加工することが可能となり、工具の摩耗も減少します。例えば、SK材専用に設計されたフライスでは、鋭い刃先と特殊コーティングにより、長時間の使用にも耐える耐久性を備えています。このように特化した工具を使用することで、加工速度の向上や交換頻度の低減を実現し、結果として生産性の向上とコストの削済が期待できます。したがって、SK材の穴あけ加工には、長寿命かつ効率的なフライス選びが鍵となるのです。
まとめ
SK材の穴あけ加工において、フライスの選び方が重要です。長寿命を実現するためには、適切な刃先形状やコーティングを選択することがポイントです。また、切削条件や冷却方法にも注意が必要です。プロの技を駆使して、高品質な穴あけ加工を実現しましょう。
SKD材の効率的な穴あけフライス加工術!プロが教えるコツとは?
SKD材を効率的に穴あけするフライス加工術について知りたいと思っていませんか? この記事では、プロが教える穴あけフライス加工のコツや効率的な加工方法についてまとめています。SKD材の特性やフライス加工の基本、さらには穴あけにおける注意点など、どなたでも役立つ情報を提供しています。穴あけフライス加工に関心がある方は、ぜひこの記事をお読みいただき、スキルアップにつなげてみてください。
1. SKD穴あけフライス加工とは?
SKD穴あけフライス加工は、金属加工の一手法であり、特に硬質材料への穴あけにおいてその効率と精度が高く評価されています。この加工のポイントは適切な工具の選択と適正な加工条件の設定にあります。例えば、SKD材には高速度鋼や超硬合金のドリルを使用することで、耐久性と効率が向上。さらに、穴あけ時の回転数や送り速度を材質に合わせて調整することで、加工精度を高めることができます。具体的な例としては、加工前の適切な材料の予熱や、冷却液の使用が挙げられます。これらを適切に行うことで、SKD材の穴あけフライス加工の効率と精度は格段に向上します。最終的に、これらの手法を駆使することで、製品の品質を保ちつつ、生産効率を高めることが期待されます。
2. 高硬度鋼SKDの切削加工の基本
SKD材の穴あけフライス加工を効率的に行うには、適切な工具選択と加工条件の最適化が不可欠です。SKD材は硬度が高く加工が困難とされていますが、正しい方法を採用することによって、その困難を克服することができます。例えば、超硬合金製やコーティングされたドリルの使用は、耐久性と切削速度の向上に寄与します。さらに、正確なスピンドル速度の設定と切削油の適切な使用は、加工の精度を高めるだけでなく、工具の摩耗を減少させることにつながります。これらのポイントを念頭に置きながら加工を進めることで、SKD材の穴あけ作業は格段に効率的かつ精密に行うことができるでしょう。結論として、適切な工具の選定と加工条件の最適化により、困難とされるSKD材の穴あけフライス加工が、高効率かつ高精度に実現可能です。
3. マシニング加工とフライス加工の違い
SKD材を効率よく穴あけフライス加工するためには、適切な工具選びと加工条件の設定が重要です。SKD材は硬度が高く耐摩耗性に優れているため、一般的な材料に比べて加工が難しいとされています。しかし、専用の超硬ドリルやコーティング加工されたエンドミルなど、適切な工具を使用することで、精度と効率を高めることが可能です。例えば、SKD材のフライス加工には、切れ味が良く摩耗しにくい超硬質合金やセラミックスを使用した工具が推奨されます。さらに、切削速度や送り速度、切り込み深さなどの加工条件を材料の特性に合わせて最適化することで、工具の寿命を延ばし、加工時間を短縮できます。結論として、SKD材に適した工具選びと加工条件の調整により、穴あけフライス加工を効率的かつ高品質に行うことが可能になります。
4. 精密SKD穴あけフライス加工の秘訣
SKD材に効率的な穴あけフライス加工を施すことは、専門的な技術を要します。まずは、適切な工具選びが重要であり、SKD材の硬度に合わせた超硬合金やコーティングされたドリルを使用することが肝心です。また、適切な切削速度と送り速度の設定が必要不可欠で、これにより摩耗を抑えつつ、効率的に加工することが可能になります。実際の例としては、低速で高トルクの設定で加工を開始し、徐々に速度を上げていく方法があります。こうすることで、初期の摩耗を防ぎつつ、精度の高い穴あけが実現できます。最終的には、これらの工程を適切に管理することで、耐久性と精度を兼ね備えたSKD穴あけフライス加工が実現します。
5. 信頼できるフライス・旋盤加工業者の選び方
SKD材の穴あけフライス加工は、正確さと効率性が求められる作業です。その実現にはいくつかのポイントがあります。まず、SKD材に適した切削工具の選択が重要です。SKD材の硬さに対応した高品質のドリルやエンドミルを使用することで、摩耗を減らし、精度の高い加工が可能になります。また、適切な切削条件、すなわち回転数と送り速度の調整は、バリの発生を抑え、切削効率を最適化します。具体的な例としては、SKD材加工においては通常よりも低い回転数で開始し、徐々に最適な条件を見つけていくことが良いでしょう。また、冷却液の使用により、加工部の過熱を防ぎ、工具の寿命を延ばすことができます。これらのコツを押さえることで、SKD材の穴あけフライス加工の効率と品質を向上させることが可能です。結論として、適切な工具の選択、切削条件の最適化、そして冷却液の活用により、高効率かつ高品質なSKD材のフライス加工が実現します。
6. 工具鋼SKDと旋盤加工の要点
SKD材を用いた穴あけフライス加工は、精密な工業製品を作る際に不可欠です。そのためには、専門家が伝えるコツを把握することが重要です。まず、適切な工具選びが重要であり、SKD材には硬度が高く耐摩耗性の優れたドリルやエンドミルが推奨されます。具体的には、超硬合金製やコーティングされた工具を使用すると良いでしょう。また、適切な切削条件の設定が重要であり、回転速度や送り速度を材料の硬さに合わせて調整する必要があります。冷却液の使用も、材料の過熱を防ぐために重要です。こうしたことに加え、穴の位置決めの正確さも精度を左右するため、工具のセットアップには細心の注意を払うべきです。このように正しい工具の選択、適切な設定、丁寧なセットアップを行うことで、SKD材の穴あけフライス加工の効率と精度を大きく向上させることが可能です。
まとめ
SKD材の効率的な穴あけフライス加工には、適切な切削条件と工具の選定が重要です。適切な切削速度や切り込み量、切削液の使用によって高品質な穴あけ加工が可能となります。また、専用のフライス工具を使用することで、穴あけ作業を効率的に行うことができます。プロの技術を取り入れることで、高精度な穴あけ加工が実現できるでしょう。
SKDの穴あけ加工に革命!フライスの選び方と加工法の最新情報
SKDの穴あけ加工に革命をもたらす最新のフライス加工法と選び方についてご紹介します。SKDの穴あけ加工にお困りの方、フライス加工に興味がある方にとって、この記事は必見です。穴あけ加工の基本から最新の加工法まで、わかりやすく解説します。さらに、フライス加工を利用して効率的に作業を進める方法についても詳しく説明します。
1. SKD 穴あけ加工の基礎
SKDの穴あけ加工には独自の技術が必要であり、その中でもフライスの選び方と加工方法が革命的に進化しています。SKDとは、耐摩耗性に優れた工具鋼の一種であり、その硬度の高さから機械加工が困難とされてきました。しかし、最新の技術を用いることで、SKDの加工が以前よりも容易になっています。具体的には、切削工具の素材やコーティング、切削条件の最適化がその鍵を握ります。例えば、ダイヤモンドコーティングされたフライスはSKDの高硬度を突破するのに適しており、加工時の熱や摩耗にも強いという特性があります。このように適切な道具と方法を選ぶことで、SKDの穴あけ加工はより効率的かつ精密に行うことが可能です。この進展は、精密工業をはじめとする多くの分野での生産性の向上に寄与しています。
2. 旋盤加工とSKD フライス加工の違い
SKDの穴あけ加工においてフライス加工は、その精度と効率で大きな革命をもたらしました。従来の旋盤加工では困難だった複雑な形状や深い穴の加工も、適切なフライス選びと加工法によって、高い精度で実現可能になっています。例えば、特殊な形状の刃を持つフライスを使用することで、SKDの硬い材質でも滑らかな加工面を得られ、加工時間の短縮とコスト削減にも繋がります。そして、フライス加工機の進化により、従来の方法に比べて加工速度が飛躍的に向上し、細かい部分の調整も簡単になりました。結論として、適切なフライスの選び方と最新の加工法を理解することは、SKDの穴あけ加工における品質向上と生産性の向上に不可欠です。
3. 高硬度鋼SKDの切削加工ポイント
SKDの穴あけ加工では、適切なフライス選びと加工法が重要です。SKDは高硬度であるため、通常の鋼材に使われる切削ツールでは加工が困難です。それを解決するため、特に硬度に対応したフライスやコーティングが開発されています。例えば、超微粒子超硬合金のフライスはSKDのような材料に適しており、長寿命で精度の高い加工が可能になります。また、切削速度や送り速度の設定も重要で、これらを適切に調整することで加工の効率と品質を向上させることができます。結論として、SKDの穴あけ加工はフライス選びと正確な加工条件の設定により、加工の革命をもたらす可能性があるといえます。
4. 精密SKDフライス加工の魅力
SKDの穴あけ加工において、適切なフライスを選び、最新の加工法を取り入れることが大きな進歩をもたらしました。SKD材の硬度や耐摩耗性を考慮したフライス選びは、加工精度を大きく左右し、製品の品質向上に直結します。具体的には、超硬合金製やダイヤモンドコーティングされたフライスなど、SKD材の特性に最適化された工具の使用が推奨されます。これらのフライスを用いることで、従来よりも長い工具寿命と安定した加工を実現することが可能となり、生産効率の向上にも寄与しています。最新の加工法により、細かい穴あけ加工も高精度で行うことができ、複雑な形状のSKD加工にも対応可能です。このような進化を経て、SKDの穴あけ加工は新たな可能性を開拓しており、加工業界においてもその価値が高まっています。
5. SKDフランジ穴あけ加工におすすめのフライス選択ガイド
SKDの穴あけ加工に革命をもたらす適切なフライスの選び方と加工法についての情報が求められています。SKDとは金属加工でよく用いられる合金鋼の一種で、特に硬度が高く加工が難しい材料です。これを効率よく加工するためには、適切なフライスを選択することが重要です。たとえば、超硬質フライスやコーティングフライスは、SKDの高硬度による摩耗や熱に対して強い耐性を持っており、穴あけ加工において一般的な高速度鋼よりも優れた性能を発揮します。また、切削条件の最適化や冷却方法の改良も穴あけの精度と効率を高めるために不可欠です。このように適切な工具と加工法を選ぶことで、加工時間の短縮や工具の寿命を伸ばすなどのメリットが得られます。結論として、SKDの穴あけ加工に革命をもたらすためには、材質に適したフライス選びと精密な加工法の知識が必須となります。
まとめ
SKD(Special Knife Drill)を使用した穴あけ加工は従来の方法よりも高速で効率的に行うことができます。フライスの選び方や適切な加工法を把握することで、SKDを使用した穴あけ加工の品質と生産性を大幅に向上させることができます。最新の情報を常に把握し、穴あけ加工の革新的なアプローチを取ることが重要です。
フライス加工の基礎!SK材料で穴あけを成功させるポイント
フライス加工は工作機械を使用して工程を行う際に欠かせないステップの一つです。特にSK材料を使用した穴あけ作業は、正確かつ効率的な加工が求められます。本記事では、フライス加工におけるSK材料の穴あけ作業に焦点を当て、成功させるためのポイントをご紹介します。穴あけ作業の基礎から応用まで、幅広く解説しますので、ぜひご覧ください。
1. SK 穴あけ フライス加工とは?
フライス加工においてSK材料を用いた穴あけは、精度の高い加工を要求される場面で重要な役割を果たしています。その成功の鍵は、SK材の特徴を理解し正確な工具選びと適切な加工条件を選定することにあります。SK材料は硬度と耐摩耗性に優れ、そのため加工時の抵抗が通常の材料よりも大きくなることが一般的です。例えば、適切な切削速度と送り速度の組み合わせは、SK材料の硬度を乗り越えるために欠かせません。また、刃先の材質やコーティングもSK材料の硬度に適したものを選ぶ必要があります。丁寧な工程設計と適切な工具選択によって、SK材料での穴あけは精度良く、効率的に行うことが可能です。このプロセスの理解と適用は、SK材料を使用したフライス加工の品質を大きく左右します。
2. SK 穴あけ フライス加工の基本原理
SK材料での穴あけ加工は、正確さと耐久性が求められる作業です。フライス加工における穴あけの成功は、ツールの選択、加工条件の設定、そして材料特性の理解に大きく依存しています。SK材料は硬度が高く耐摩耗性に優れているため、適切なカッターやドリルの使用が不可欠です。具体的には、材料の硬度に合わせて、高速度鋼(HSS)や超硬合金を用いることが一般的です。また、冷却液を使用し切削熱を抑えることで、材料の変質を防ぐこともポイントです。最適なスピードと送り速度で加工することで、SK材料を使用した穴あけにおいても滑らかな仕上がりと長い工具寿命を実現することができます。結論として、正しい工具選択と加工条件の見極めがSK材料での穴あけを成功させるためには不可欠です。
3. SK 穴あけ フライス加工における材料の選び方
フライス加工において穴あけを行う際、SK材料を選択することは成功への重要な鍵です。まず、結論から申し上げると、適切なSK材料を使用することで、加工精度が向上し、工具の寿命が延び、コストパフォーマンスが高まります。その理由は、SK材料が優れた耐摩耗性と適度な硬さを持ち、フライス加工時の熱や圧力に強いからです。例えば、SKD11やSKH51といったSK材料は一般的に硬い材料加工において高い実績があり、穴あけにおいてもその精度と耐久性が求められる場面で選ばれています。穴あけ加工の際には、これらのSK材料を選ぶことで、仕上がりの美しさと精度を確保し、結果として生産効率を高めることに繋がります。最後に再度結論を強調しますが、SK材料の選択はフライス加工における穴あけ作業の品質とコスト効率を大きく左右するため、選材には細心の注意を払うべきです。
4. SK 穴あけ フライス加工の機械と装置
フライス加工において、SK材料を使用した穴あけ作業の成功にはいくつかの要点があります。SK材料は硬度が高く耐久性に優れているため、精密な加工が求められる場合によく使用されます。まず、適切な工具の選定が重要です。SK材料に適したドリル選びは、穴あけの精度と寿命を左右します。次に、切削速度や送り速度の設定が重要です。これらのパラメータを適切に管理することで、加工時の摩耗を抑え、高い加工品質を維持することができます。実際の例として、SK材料を用いた場合、一般的な材料に比べて切削速度をやや低めに設定することが一般的です。これにより、材料の硬度に対応し、バリの発生を抑制しつつ、穴あけ加工を行うことが可能です。結論として、SK材料での穴あけを成功させるためには、適切な工具の選択、切削速度、送り速度の適切な設定が重要であり、これらを適切に管理することで、高品質な穴あけ加工を実現できます。
5. SK 穴あけ フライス加工の工程と手順
フライス加工でのSK材料を使った穴あけは、高い精度と仕上がりが求められます。これを成功させるためには、いくつかのポイントを押さえておくことが重要です。まず、SK材料は硬度が高く、耐摩耗性に優れているため、適切な工具選択と刃の角度が不可欠です。例えば、硬質のSK材料には、切れ味の良いカーバイド製のドリルビットが適しています。また、穴あけの際は、スピンドルスピードとフィードレートを適切に設定することで、材料の熱損傷を防ぎ、均一な穴を確実にあけることができます。具体的には、低速での加工を心掛け、冷却液を使用することで、材料の過熱を防ぎながら、精密な穴あけが行えます。最終的に、工具のメンテナンスにも気を付けることで、一貫した品質の穴あけ加工を継続的に行うことができるでしょう。このように、SK材料を使用したフライス加工での穴あけを成功させるためには、適切な工具の選択、適正な加工条件の設定、そして工具のメンテナンスが重要です。
6. SK 穴あけ フライス加工における切削条件の設定
フライス加工における成功のカギは適切な切削条件の設定にあります。特に、SK材料を用いた穴あけ加工では、材質の特性を理解し正確な条件を選ぶことが重要です。SK材料は硬度が高いため、耐摩耗性に優れていますが、切削条件が適切でなければ工具の損傷や加工精度の低下を招く可能性があります。例えば、速度や送り速度、冷却液の使用は、SK材料の穴あけ加工における品質を左右する重要な要素です。適切な速度で切削することで、摩擦熱を適度に保ち、材料の硬化を避けることができますし、冷却液の適切な使用は、加工面の仕上がりを良好に保つのに役立ちます。要するに、材料の性質を踏まえた切削条件の設定は、SK材料を用いた穴あけフライス加工を成功に導く鍵となるのです。
7. SK 穴あけ フライス加工のトラブルシューティング
SK材料を用いた穴あけのフライス加工では、成功の鍵はいくつかの要点を押さえることにあります。まず、材料の選定が重要です。SK材料は硬度が高く耐摩耗性に優れているため、正しい工具と条件で加工することで精度の高い穴あけが可能となります。次に、適切な工具の選択が大切です。SK材料を加工する際には、硬度に合わせた刃の材質や形状を選ぶ必要があります。例えば、超硬合金製のドリルはSK材料の加工に適しています。さらに、切削速度や送り速度などの加工条件を最適化することが重要です。具体的には、低速・高トルクで加工を行い、加工時の熱を抑えるための冷却液の使用も考慮すべきです。最後に、こうしたポイントを踏まえた上で、定期的な刃物の点検や交換を行い、常に最高の状態で加工を続けることができるようにすることが、SK材料の穴あけフライス加工でのトラブルを避け成功に導くポイントです。
8. SK 穴あけ フライス加工の依頼先選びと注意点
フライス加工においてSK材を用いた穴あけは、その成功にいくつかのポイントがあります。まず、フライス加工では正確な穴位置と形状の維持が重要です。このため、SK材の特性を考慮した適切な切削工具と条件の選定が不可欠です。例えば、高硬度を活かした加工を望む場合、SK材の熱処理状態に合わせたドリル選びや、切削速度の調整が重要になります。また、切りくずの排出方法にも注意が必要です。切りくずが適切に排出されないと、穴が不完全になったり、工具が破損する原因にもなりかねません。取り扱う業者選びでは、これらの技術的な要求を満たせるかどうかが選定基準の一つです。結論として、SK材を用いた穴あけフライス加工を成功させるためには、材料の特性に応じた適切な工具と加工条件の選択、そして経験豊富な業者の選定が鍵となります。
9. SK 穴あけ フライス加工に関するよくある質問
フライス加工において、SK材料を用いた穴あけ作業の成功は、工作物の品質向上に直結します。理由は、SK材料が硬く耐久性に優れているため、正確で精度の高い加工が求められるからです。具体例として、穴あけの際には、ドリルの選定に注意し、材料の硬さに適したものを選ぶことが重要です。さらに、適切な速度と送りで加工を行うことで、材料の損耗を抑え、長寿命な穴あけが可能になります。また、冷却剤を適切に使用することで、加工中の過熱を防ぎ、材料の変質を避けることができます。結論として、SK材料で穴あけを成功させるには、適切なドリル選び、加工速度・送りの調整、冷却剤の使用がポイントとなります。これにより、精度高く耐久性のある加工が実現し、製品品質を高めることに繋がるのです。
10. SK 穴あけ フライス加工の未来と発展
フライス加工において、SK材料を使用した穴あけ作業は精度が要求されるため、成功させるにはいくつかのポイントがあります。まず、SK材料の特性を理解することが重要です。この材料は硬さが高く、耐摩耗性に優れていますが、その分、加工時には切削条件を慎重に選ぶ必要があります。具体的には、適切な切削速度とフィードレートの選定、そして鋭利な刃物の使用が挙げられます。例えば、SK材料の穴あけでは、低速での加工と高いフィードレートを組み合わせることで、材料の熱影響を抑えつつ、切削屑の排出をスムーズに行うことができます。また、工具の摩耗を防ぐためには、刃物の冷却が不可欠です。これらのポイントを念頭に置き、適切な工具選びと加工条件の設定を行うことで、SK材料の穴あけを成功させることができるのです。最後に、この流れを守ることで、フライス加工の精度を高く保ち、製品の品質向上にも繋がります。
まとめ
フライス加工において、SK材料での穴あけを成功させるためのポイントはいくつかあります。まず、適切な工具選びが重要です。硬度や耐摩耗性に優れた適切なフライス工具を選ぶことが必要です。また、切削速度や切削深さ、切削量などのパラメータを正確に設定することも重要です。加工対象の材料特性を考慮し、適切な加工条件を設定することが成功のポイントとなります。