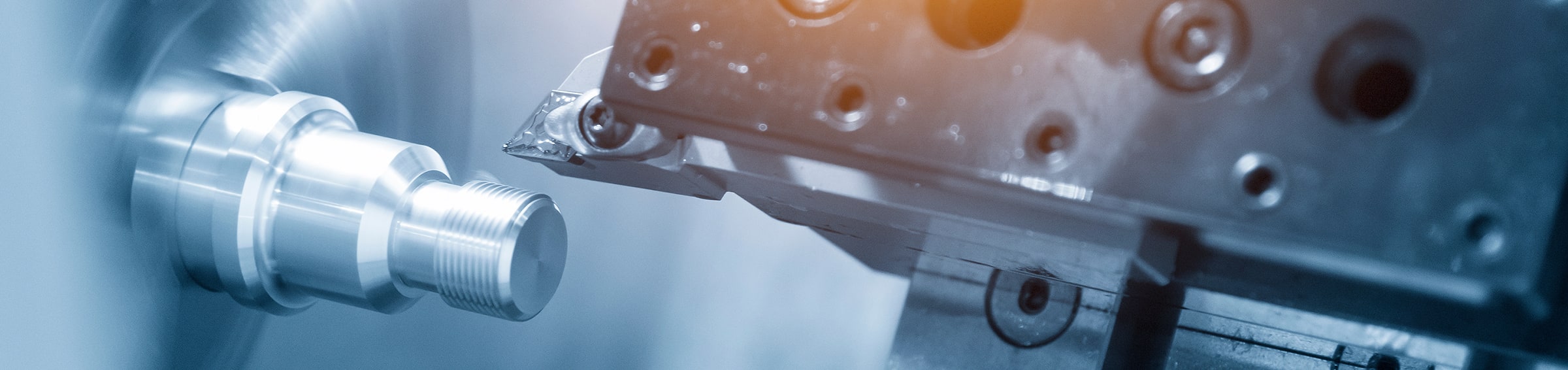
加工技術 column
SKD材加工をマスターする!フライス&タップ技術の全て
SKD材加工をマスターするためには、フライス加工とタップ加工の技術を習得する必要があります。これらの技術を使うことで、高品質な製品を生産することが可能となります。本記事では、SKD材加工におけるフライス加工とタップ加工の全てについて詳しく解説していきます。SKD材加工に興味がある方やこれらの技術を習得したい方にとって、必読の記事となるでしょう。
1. SKD タップ加工 フライス加工 の基礎
SKD材加工をマスターするためには、タップ加工とフライス加工の技術が不可欠です。SKD材は耐摩耗性や熱処理後の寸法安定性に優れ、多くの工業製品に使用されています。そのため、精密な加工技術が求められるのです。例えば、自動車や機械部品の製造において、フライス加工によって複雑な形状を持つ部品を作り出すことができ、タップ加工によって部品同士を組み合わせる際のねじ部分を作成します。これらのプロセスは、部品の品質と機能を確実にするために極めて重要です。結論として、SKD材の正確なタップ加工とフライス加工を習得することは、効率的で高品質な製品を製造する上で欠かせないスキルといえるでしょう。
2. SKD11材加工の基本知識
SKD材を使った加工技術は、高品質な製品を作る上で不可欠です。SKD材は硬度が高く耐摩耗性に優れているため、フライス加工やタップ加工に適しています。フライス加工では、精密な部品の造形が可能で、複雑な形状も高い精度で削り出せます。タップ加工においては、SKD材の硬さを考慮し、適切な切削速度と潤滑を選ぶことが重要です。例えば、自動車部品や金型など、耐久性が求められる製品にSKD材はよく用いられます。これらの技術をマスターすることで、製造業界での競争力を高めることができるでしょう。まとめると、SKD材のフライス加工とタップ加工は、その特性を生かした正しい方法で行うことで、製品の品質向上に寄与し、技術者のスキルセットを拡大する重要な工程と言えます。
3. マシニングセンタでのSKD タップ加工のテクニック
SKD材加工を習得することは、製造現場において極めて価値のあるスキルです。特にフライス加工とタップ加工の技術は、精密な部品製造に不可欠です。フライス加工では、SKD材からのバリ取りや形状創出が可能で、タップ加工によってはネジ穴の作成が行えます。例えば、自動車や飛行機の部品には、これらの技術を駆使したSKD材が多用されています。これらの部品は、極めて高い精度が求められ、それらを実現するためには、優れた加工技術が必要不可欠です。そのため、マシニングセンタでのSKD材加工技術をマスターすると、製造業界での競争力を大きく向上させることができるのです。最終的に、これらの技術は製品の品質向上に直結し、顧客からの信頼を勝ち取ることにつながります。
4. タップとダイス:SKD材における重要な選択
SKD材加工には特有の技術が求められます。特にフライス加工とタップ加工はその代表例で、これらをマスターすることは高品質の製品を生産する上で不可欠です。フライス加工では、SKD材の硬さや熱処理状態を考慮し、適切なカッターや速度選定が重要です。例えば、硬質のSKD材を加工する際には、耐摩耗性に優れたカッターを使用することで、精度の高い加工が可能になります。一方、タップ加工においては、ねじ山の精度を保つためには、適切なタップの選択と加工スピードが鍵となります。SKD材のような硬い材料では、ねじ山が簡単に損傷するため、慎重な操作が求められるのです。正確な加工技術を身につけることで、SKD材のフライス加工・タップ加工を成功させることができ、これが高品質な製品製造への道となります。
5. 高速工具鋼SKD:最新動向と応用
高速工具鋼SKDの加工技術を習得することは、精密部品製造において不可欠なスキルです。SKD材はその耐摩耗性と硬度から、多くの工業分野で高い評価を受けています。特にフライス加工とタップ加工は、SKD材の加工において重要な技術です。フライス加工によって、SKD材を複雑な形状に正確に切り出すことができます。タップ加工では、精密なねじの切削が可能となり、製品の組み立てに直結する部分での使用が可能です。例えば、自動車産業の部品製造や工作機械のコンポーネントなど、高精度が求められる領域での活用が見られます。これらの技術をマスターすることで、加工精度の向上、生産効率の増進、そして製品の信頼性の確保に繋がります。したがって、SKD材加工技術をマスタすることは、品質を重視する製造業において、競争力を維持する上で極めて重要です。
6. コストダウンのための精度要求の見直し戦略
SKD材の加工は、フライスとタップ加工のテクニックをマスターすることで、より効率的かつ精密な製品造りに繋がります。SKD材は硬質で耐久性に優れているため、金型製作などに広く利用されています。しかしながら、その堅牢さから加工は困難とされがちです。フライス加工では、工具の選定や切削条件を最適化することで、精度良く素早く材料を削り出すことが可能になります。また、タップ加工においては、正確なねじ切りが求められるため、機械や刃具、作業方法の精緻化が不可欠です。具体例としては、フライス加工におけるマルチアキシスマシニングの活用や、タップ加工における同期ねじ切り機能が装備されたマシニングセンターの使用などがあります。これらの技術を駆使することで、コストパフォーマンスの高いSKD材加工が実現します。結論として、フライス加工とタップ加工の技術をしっかりと学び、適切な機器を用いることで、SKD材の加工はより効果的かつ効率的になるのです。
まとめ
SKD材を使用した加工において、フライス加工とタップ加工の技術を習得することは非常に重要です。SKD材の特性を理解し、それに適した加工方法を選択することが必要です。フライス加工では正確な切削条件や適切な刃先形状を選ぶことがポイントです。タップ加工では適切な刃先形状や刃先処理、適切な切削油の使用が重要です。
最適な工具選びから学ぶSKD材のフライス加工
SKD材のフライス加工において、最適な工具選びは非常に重要です。特に、タップ加工に関しては、正しい工具の選択が作業効率や品質に直結します。この記事では、SKD材のフライス加工における最適な工具選びから学ぶことができます。
1. SKD タップ加工 フライス加工 の基礎
SKD材のフライス加工において最適な工具の選択は、加工精度や効率を大きく左右します。SKDとは金型の材料として多用される合金工具鋼の一種で、その硬度と耐摩耗性に優れています。このような特性を持つSKD材を加工する際には、材質に適した切削工具とパラメーターの選定が重要です。例えば、高硬度のSKD材には硬度が高く切れ味の良い超硬合金やコーティングされたエンドミルなどが適しています。加えて、正確なタップ加工を実現するためには、ねじ切り工具の選定も重要で、SKD材に合わせたタップと工具持ち手の剛性を考慮する必要があります。適切な工具を選ぶことで、加工時間の短縮や長寿命化を実現し、結果としてコスト削減にも繋がります。最適な工具選びは、SKD材フライス加工の品質を決定づけるため、その選択には慎重な検討が求められるのです。
2. 工具選びの重要性と基本原則
SKD材のフライス加工において最適な工具選びは非常に重要です。なぜなら、適切な工具を選ぶことで加工精度が向上し、製品の品質を確保できるからです。たとえば、SKD材を用いたタップ加工を行う際、硬度や耐摩耗性に優れた工具を使用すれば、長期にわたって安定した加工が実現できます。また、フライス加工においても適切な切削条件で工具を選ぶことが大切です。例えば、SKD材のような硬質材料を加工する際には、切れ味が良く長持ちする超硬材料の工具が推奨されます。これにより、加工時間の短縮やコスト削減も可能になります。結論として、SKD材の加工に際しては、その特性に合った工具を選ぶことが、加工効率と製品品質の向上につながるため、工具選びには十分な注意を払うべきです。
3. SKD タップ加工 フライス加工 における材料の選び方
SKD材のフライス加工において最適な工具選びは、加工の品質を決定づける重要なポイントです。加工に適した工具を選ぶことで、切削抵抗を減らし、精度の高い加工が可能になります。例えば、SKD材は硬度が高いため、高速度鋼(HSS)よりも硬質の超硬合金やコーティングが施された工具が適しています。タップ加工においても、SKD材特有の摩擦や熱に強い工具を選ぶ必要があります。また、工具の適性は加工するSKD材の種類によって異なり、実際に試作を行いながら最適なものを見つけるべきです。このように適切な工具を選ぶことで、フライス加工の効率が向上し、結果として生産性の向上にも繋がります。最適な工具選びにより、SKD材のフライス加工は更にその精度と効率を高めることができるのです。
4. 合金工具鋼SKDの被削性について
SKD材のフライス加工に適した工具の選び方は、精度の高い加工を実現する上で極めて重要です。SKD材自体、硬度が高く耐摩耗性に優れるため、工具にとっては厳しい材料となります。そのため、SKD材を加工する際には、耐久性と切削効率が高い工具を選択する必要があります。たとえば、コーティング技術を施した超硬工具や、高い硬度を保ちつつも靭性に富んだ工具は、SKD材のフライス加工において良好な結果をもたらします。さらに、タップ加工においても、材質や刃形状を選定することで、破損リスクを減少させると共に長寿命化を実現します。これらの選定基準により、SKD材の加工の品質向上とコスト削減が期待できるため、適切な工具の選択は加工効率の向上に直結すると結論付けられます。
5. SKD11のフライス加工における注意点
SKD材のフライス加工において、最適な工具の選び方は非常に重要です。SKD材は一般的に硬度が高く、耐摩耗性に優れた材質であるため、適切な工具を選ばなければ、加工精度が落ちるだけでなく、工具の損耗も早まります。例えば、SKD11などの高硬度材を加工する場合、超硬合金やコーティングされた工具が推奨されます。これらは耐熱性と耐摩耗性に優れており、精密なフライス加工を可能にします。さらに、低速での加工や、切削液を用いることも、工具の寿命を延ばし、加工精度を高めるために役立ちます。最適な工具を選び、適切な加工条件を用いることで、SKD材のフライス加工においても高い品質を保つことができるのです。
6. エンドミルの選定方法とSKD材加工への応用
エンドミルの適切な選択はSKD材のフライス加工において非常に重要です。SKD材はその硬度と耐熱性により、加工ツールには高い耐久性と切削性能が求められます。例えば、SKD材のタップ加工には、切れ味が良く、かつ加工熱に強いコーティングが施されたエンドミルが推奨されます。このようなエンドミルを使用することで、加工時の摩耗を抑え、精度の高い加工が可能となります。さらに、フライス加工には、材料の硬度や加工を行う条件に応じた多種多様なエンドミルが必要となります。結論として、SKD材を加工する際には、目的や加工条件に合った最適なエンドミルを選定することが、加工精度を高め、工具寿命を延ばす鍵となります。
7. 切削加工のトラブルシューティングと対策
フライス加工において、適切な工具選びは大成功の鍵を握ります。特にSKD材の加工時には、その硬質で耐摩耗性に優れた特性が工具選択の重要性を高めます。SKD材を加工する際には、タップ加工やフライス加工に適した工具を選ぶことが不可欠です。例えば、高硬度のSKD材には、耐熱性と耐摩耗性に優れたコーティングが施されたカッターやエンドミルが推奨されます。これらはSKD材の硬さに対応しつつ、精密な加工を可能にするため、正確な仕上がりを期待できます。実際に、適切な工具を用いたSKD材のフライス加工は、寸法精度や表面仕上げの質を大きく向上させることが実証されています。加工トラブルを未然に防ぎ、効率的な生産を実現するために、SKD材に最適な工具選びを心がけましょう。
8. SKD タップ加工 フライス加工 の最新技術動向
SKD材のフライス加工における最適な工具選びは、加工の効率と品質の向上に不可欠です。SKD材は硬度が高く、耐摩耗性に優れているため、工具の選定には注意が必要です。適切な工具を選ぶことで、加工時間の短縮や精度の高い仕上がりを期待できます。例えば、マイクログレインカーバイド製のエンドミルはSKD材のタップ加工において優れた切削性能を発揮します。また、コーティング技術の進歩により、長寿命で耐久性のある工具が開発されており、これらはSKD材のフライス加工においてもその効果を発揮します。結論として、SKD材の加工に最適な工具の選定は、高品質な製品を効率的に生産するために必要不可欠であり、材料の特性を考慮した上での選択が推奨されます。
まとめ
SKD材のフライス加工においては、適切な工具選びが重要です。適切な工具を選ぶことで加工効率が向上し、加工精度も向上します。タップ加工やフライス加工においては、適切な切削条件や刃先形状、材質に応じた工具を選ぶことが必要です。また、適切な冷却・潤滑も加工品質に影響します。適切な工具選びと加工条件設定を行うことで、効率的かつ高品質なSKD材のフライス加工が可能となります。
フライス加工のプロが教える!SKD材の加工テクニック
フライス加工のプロが教える!SKD材の加工テクニックを知りたいと思ったことはありませんか?タップ加工やフライス加工に関心がある方には、SKD材の加工方法を知ることは重要です。この記事では、プロが教えるSKD材の加工テクニックについて紹介しています。さまざまな応用例や実践的なヒントを通じて、フライス加工におけるSKD材の加工方法を理解し、自分のスキルアップに役立てることができるでしょう。
1. SKD タップ加工 フライス加工 とは
SKD材を用いたタップ加工やフライス加工は、精密な工業製品を製造するにあたり欠かせない技術です。その理由は、SKD材の優れた耐摩耗性と硬度にあります。具体的な例を挙げると、金型の製作においてSKD材は頻繁に使用され、精度高く複雑な形状を持つ製品を可能にします。このような加工を行う際には、適切な切削速度の選定や冷却液の使用が重要となり、材料の特性に合わせた工具の選択も必要です。プロの技術によってこれらの条件が整えられれば、SKD材は非常に精度の高い加工が可能となります。その為、フライス加工を行う際には、これらの技術的なアプローチを適切に理解し、活用することが重要です。最終的に、これらの技術は高品質な製品を作り出すための基盤となります。
2. 金属加工における材料選定のポイント
フライス加工でSKD材を使用する際には、特有の加工テクニックが求められます。SKD材は硬度が高く耐摩耗性に優れている一方で、加工時には工具の摩耗や破損のリスクが高まるため、適切な技術が不可欠です。例えば、タップ加工においては、切削速度を落とし、切削油を適切に使用することで、摩耗を抑え、寿命を延ばすことができます。また、フライス加工では、精密な加工が求められるため、工具の選定や送り速度の調整が重要となります。これらの技術を駆使することで、SKD材は高い精度で加工が可能となり、品質の高い製品作りに貢献します。したがって、フライス加工のプロによる適切な加工テクニックの知識と技術の習得は、SKD材を用いた製造業において重要な要素と言えます。
3. フライス加工の基本
フライス加工においてSKD材を加工する際には、特有のテクニックが求められます。SKD材は硬度が高く耐摩耗性に優れているため、精密な加工が可能ですが、その反面、工具の摩耗も早まります。この点に注意し、適切な工具選びと切削条件の最適化が重要です。例えば、タップ加工の際には、刃先の強度が高く長寿命のタップを選ぶことがカギとなります。さらに、フライス加工では切りくずの排出効率を高めるために、適切な刃数と切削速度の選択が必要です。こうした細部にわたる配慮により、SKD材の加工精度を保ちつつ、工具の寿命も延ばすことができます。総じて、SKD材のフライス加工は適切な知識とテクニックがあれば、効率的かつ長期的な加工が可能になるのです。
4. SKD タップ加工 フライス加工 のプロセス
SKD材のフライス加工におけるタップ加工は、精度が非常に求められる作業です。この加工を成功させるためには、特有の技術と知識が必要となります。SKD材は硬度が高く加工が難しいため、適切な工具選びと加工条件の設定が重要です。例えば、工具はSKD材に対応した高硬度タップを使用し、切削速度や送り速度も材質の特性を考慮して慎重に選定する必要があります。さらに、冷却液の使用も、摩耗を抑え、タップの寿命を延ばすために欠かせません。適切な技術と工具を用いることで、SKD材のタップ加工は高い精度で実現可能となり、製品の品質を大きく左右する工程の一つとなります。このため、フライス加工のプロフェッショナルが、そのノウハウを教えることは非常に価値があると言えるでしょう。
5. 特殊鋼材 SKD の特性と加工のコツ
SKD材の加工においては、専門的な知識と技術が要求されます。その理由は、SKD材が特殊鋼として高硬度かつ耐摩耗性に優れているため、一般的な加工材料に比べて加工が困難であるためです。フライス加工における具体的な例としては、タップ加工が挙げられます。タップ加工では切削条件の選定が重要であり、適切な工具選びと冷却方法を用いることで、加工精度を高めることができます。また、SKD材を効率良く加工するためには、工具の摩耗を抑えるための工夫も必要です。例えば、工具の進行速度を適切に調節することで、工具寿命を延ばし、コストパフォーマンスの向上が見込めます。結論として、SKD材の加工には特別な注意が必要ですが、正しい技術と知識を持ち合わせることで、品質を損なうことなく効率的な加工が可能となります。
6. 精密部品の加工依頼先の選び方
フライス加工の現場で求められるのは精密さと効率です。特にSKD材のタップ加工は、その硬度と強度の高さから加工が難しいとされています。しかし、適切なテクニックを用いることで、この困難を乗り越えることができます。例えば、加工速度やフィードレートを材質に合わせて最適化する、専用の切削油を使用する、適切な工具選びをするといった工夫が重要です。また、切削工具の角度や冷却方法にも注意を払い、SKD材特有の加工課題に対処する必要があります。これらのテクニックをマスターすることで、フライス加工の品質を向上させ、作業効率を高めることができるのです。結論として、専門的な知識と経験を持つプロの技がSKD材のフライス加工には不可欠であり、それによって高品質な製品を効率良く生産することが可能になります。
7. 金属加工業者の選定と比較の重要性
フライス加工は、SKD材の加工において非常に重要であり、適切なテクニックを用いることで精度の高い製品を生み出すことができます。SKD材は硬度が高く、耐摩耗性に優れているため、タップ加工には特に注意が必要です。具体的なテクニックとしては、適切な切削油の選定、切削速度の調整、そして正確な工具の選択が挙げられます。例えば、SKD材を加工する際には、切削油を多めに使用し、工具の摩耗を防ぎながら精度よく加工することが大切です。切削速度を遅めに設定することで、材料への負担を減らし、均等な仕上がりを実現することが可能です。これらのテクニックを駆使することによって、フライス加工はSKD材の可能性を最大限に引き出し、高品質な製品を製造できるのです。締めくくりとして、フライス加工のプロはこれらのテクニックに精通しており、SKD材の加工の精度を飛躍的に向上させることができます。
8. SKD タップ加工 フライス加工 のトラブルシューティング
SKD材を使用したタップ加工においては、適切な加工テクニックを駆使することが重要です。SKD材は硬度が高いため、一般的なフライス加工よりも慎重な取り扱いが求められます。そのため、効率的かつ精密な加工を実現するためには、専門の知識と技術が必要不可欠となります。例えば、加工時には適切な切削速度の選定や冷却液の利用が重要です。切削速度を適切に設定することで、工具の摩耗を抑えながら加工精度を保つことができます。また、冷却液を使用することで、発熱を抑制し、工具の寿命を延ばすことができるのです。これらのテクニックを駆使することで、SKD材のフライス加工はより効率的で精度の高いものになります。このように、SKDタップ加工における専門技術を理解し、適切に実践することが、高品質な加工成果を得るための鍵となるのです。
9. 実例から学ぶ!SKD材の加工テクニック
SKD材は、耐摩耗性や硬度が高いため、フライス加工やタップ加工において一定の技術が要求されます。正しい技術を用いることで加工精度を高め、製品の品質を向上させることができます。例えば、SKD材のタップ加工では、切削速度の適正化や冷却剤の使用が重要です。低速で丁寧に加工を行い、切削熱を効果的に逃がすことで、ねじ山が崩れることなく加工できます。また、フライス加工では、専用の刃物を選定し、こまめに刃先のチェックを行うことで、SKD材特有の硬さによる刃物の摩耗を軽減することが可能です。これらの具体的なテクニックを駆使することで、SKD材も安定して高品質な加工を実現できます。結論として、正しい技術と適切な加工方法を理解し、実践することがSKD材の加工における成功の鍵となります。
10. 最新のSKD タップ加工 フライス加工 テクノロジー
フライス加工の専門家であるならば、SKD材のタップ加工はその技術と精度の高さから重要視されるべきポイントであることを理解しているだろう。具体的には、SKD材は硬度が高く、耐摩耗性にも優れているため、精密な加工を要求される場面においてよく用いられる。このような材質の加工には、特別なテクニックが必要であり、その中でもタップ加工は特に繊細な作業である。
フライス加工におけるSKD材のタップ加工の成功の秘訣は、適切な工具の選択と正確な切削条件の設定にある。例えば、SKD材の加工には、特に硬質のタッピング工具を使用することや、回転数や送り速度を材質の特性に合わせて慎重に調整することが挙げられる。適切な準備と知識があれば、SKD材でも美しいねじれ加工の実現は十分可能である。そのため、フライス加工のプロフェッショナルがこうしたテクニックを身に付けることは、その技術力の証とも言えるだろう。
まとめ
SKD材のフライス加工では、適切な切削条件や工具の選定が重要です。硬度の高いSKD材を効率的に加工するためには、適切な切削速度や切削深さ、刃先形状などを工夫する必要があります。また、冷却および潤滑にも配慮して加工を行うことで、切削時の摩擦や熱の影響を軽減し、加工精度を向上させることができます。SKD材の特性を考慮した上で、適切な加工テクニックを取り入れることが重要です。
【工業用ノウハウ】SKタップとフライス加工で押さえておきたい重要ポイント10選
工業用ノウハウにおけるSKタップとフライス加工の重要ポイントを10選、こちらの記事では詳しくご紹介いたします。もしも、あなたが工業加工に関わる方であり、スキルを向上させたいと考えているのであれば、この記事を読むことできっと役立つ情報を得ることができるでしょう。
1. SKタップ加工 フライス加工の基礎知識
SKタップ加工およびフライス加工は、精密な工業製品を製造する上で欠かせない技術です。これらの工法を用いることで、製品の品質と生産効率が大きく向上するため、押さえておくべき重要ポイントを理解することが重要です。たとえば、SKタップ加工では、タップの選択が切削効率に大きく影響し、フライス加工では刃の角度や素材によって仕上がりの品質が変わります。実際の例として、硬い材料を加工する際には、耐久性の高いタップを選ぶことで寿命を延ばすことが可能ですし、フライス加工においては、切削速度の調整が重要です。また、機械の定期的なメンテナンスを怠らないことで、加工精度の維持ができます。このような点を踏まえ、SKタップ加工とフライス加工の正しい知識と適切な使用法を身につけることが、高品質な製品を安定して生産するための鍵となります。
2. コストダウンを実現するSKタップ加工のテクニック
SKタップ加工は、工業用の製品作成においてコストパフォーマンスを高める重要なプロセスです。この加工法には、材料の無駄を減らし、製造工程を効率化するための幾つかのテクニックがあります。例えば、適切なタップサイズとピッチの選択は、材料の割れや損傷を避けるうえで重要です。また、最適な切削油の使用は、摩擦を減らし、工具の寿命を延ばすことにもつながります。精密な加工が求められる場合には、マシンの振動を抑制するための専門的な設備の導入が効果的です。これにより、高品質な製品を一貫して生産することが可能になり、結果としてコストパフォーマンスが向上します。以上のように、SKタップ加工における細かな注意点を押さえることは、製品の品質向上とコスト削減の両方を実現するために不可欠です。
3. ローコスト調達とSKタップ加工の関係
工業用ノウハウとしてSKタップ加工は、製造業でのローコスト調達と深く関連しています。コスト削減のためには、耐久性と加工速度が重要です。SKタップはその両方を兼ね備え、特に金属加工において優れた性能を発揮します。例えば、金属の穴あけ作業において、SKタップは他のタップに比べて摩耗しにくく、長期にわたって安定した加工が可能です。この耐久性は交換頻度の低下を意味し、長期的に見るとコスト削減につながります。また、フライス加工においてもSKタップはその精度と効率で知られ、精密な加工が求められる部品製造での利用が増加しています。結論として、SKタップ加工は、コスト削減と製品品質の両立を図る上で、製造現場では欠かせない選択肢となっています。
4. 機械加工業界のトレンドとSKタップ加工
現代の機械加工業界において、SKタップ加工はその精度と効率により非常に重要な役割を果たしています。この加工法は、部品の締結や組み立てに不可避なねじ加工において、高い信頼性と生産性を実現させます。具体例として、自動車産業や航空機の製造など、緻密なねじの品質が求められる分野でSKタップ加工が重宝されています。また、フライス加工もまた、複雑な形状の部品を一貫して高精度に加工するために不可欠であり、合理的な生産フローを実現する上で有効です。これらの加工技術は、製品の信頼性を左右するだけでなく、コスト削減や工程短縮にも寄与しています。まとめると、SKタップ加工とフライス加工は、現代の製造業において欠かせない技術であり、その使いこなしには特別な注意と知識が必要です。これらの技術を理解し、適切に応用することが、製造業における持続可能な競争力を維持する鍵となります。
5. SKタップ選定の基準と最適な方法
工業分野において、正しいSKタップの選択とフライス加工の技術は製品品質を左右する重要な要素です。SKタップ選定の基準として最も大切なのは、加工する材料の種類と硬度に合わせた適切な製品を選ぶことです。たとえば、アルミニウムや非鉄金属の場合は切れ味が良く、磨耗に強いタップが求められます。一方、硬質のステンレスや炭素鋼の加工には、高い耐久性と精度を備えたタップが必要とされます。フライス加工においては、切削速度や送り速度、さらにはフライスの種類にも注意し、材料や形状にベストマッチしたものを選ぶ必要があります。このように適切なSKタップとフライスを選ぶことで、加工精度の向上はもちろんのこと、工具の寿命を延ばし、コスト削減にも繋がるのです。緻密な選定が、高品質な製品を実現するカギとなるのです。
6. 大学や研究機関におけるSKタップ加工の公費支払いガイド
工業用ノウハウとしてのSKタップ加工やフライス加工は、精密な製品を生産するうえで欠かせない技術です。これらの加工技術は工業製品の品質向上に直結し、日本の製造業の競争力を支える要素となっています。例えば、SKタップ加工では、ねじ切りの精度が求められるため、材質の選定やタップの種類、切削液の使用が重要です。一方、フライス加工では、被削材の硬さや切削速度、刃の選択が製品の仕上がりに大きく影響します。こうした加工技術のポイントを理解し、正確に適用することで、高品質な製品が生産されるのです。日本のものづくり産業においても、SKタップ加工、フライス加工の精度はますます重要性を増しているため、これらのポイントを押さえておくことは、技術者にとって必須の知識といえるでしょう。
7. 工作機械の種類とSKタップ加工の適用
工作機械には多種多様なものがあり、SKタップ加工を適切に行うためには、機械の選定が重要です。SKタップとは、ねじ切りタップの一種であり、高精度なねじ加工が求められる産業でよく利用されます。例えば、自動車や航空産業においては、部品の微細なねじ部分にSKタップ加工が用いられることが多いです。これらの産業においては、耐久性や精度が極めて重要であり、正確なねじの形成が不可欠です。そのためには、フライス加工機やCNC旋盤など、精密加工が可能な工作機械を選ぶ必要があります。特にフライス加工では、回転する刃が材料の表面を削ることによって形状を作り出すため、SKタップでのねじ切りに先立って行う場合、その精度がねじ加工の質を大きく左右します。最終的に、適切な機械選びと正確な加工技術によって、高品質な製品が生み出されるのです。
8. 機械金属加工におけるSKタップとフライス加工の組み合わせ
産業機械の製造に欠かせないSKタップとフライス加工には、押さえておくべき重要ポイントがあります。これらの加工方法は、精密さと効率性を両立させるために、特有の技術と知識が求められます。例えばSKタップ加工では、タップの切れ味や材質選びが、ネジ山の品質に直結します。また、フライス加工は、切削速度や送り速度、そして切削深さの適切な設定が、仕上がりの精度を左右します。具体的には、硬い材料を加工する際には切れ味の良いタップを選ぶこと、複雑な形状を加工する場合はフライスの形状を工夫することが挙げられます。これらのポイントを理解し適切に適用することで、製品の加工精度を高め、生産効率を向上させることが可能です。最終的には、適切な工程設計とツール選択により、優れた製品を効率的に生産することが業界の競争力を支えています。
9. SKタップ加工 フライス加工のトラブルシューティング
SKタップ加工とフライス加工は、精密な加工が求められる工業分野で重要な技術です。そのため、加工時にはいくつかのポイントをしっかり押さえておくことが大切です。たとえば、SKタップ加工では、タップの先端角度や刃の数など、使用する工具の特性を理解し適切なものを選択することが肝心です。フライス加工では、加工物の固定方法やフライスの速度・送り速度を正確に設定することが重要になります。特に困難な形状や、高い精度が求められる加工の場合、これらの設定ミスは加工不良の原因となり得ます。たとえば、不適切なタップ選定によるねじ切りの失敗や、不正確なフライス速度設定による加工物の破壊などが挙げられます。以上のようなトラブルを避けるためには、正しい知識と経験が必須です。結論として、SKタップ加工とフライス加工においては、適切な工具の選定や加工条件の設定が加工品質を左右する重要ポイントです。
10. 将来のSKタップ加工 フライス加工技術の展望
日本の工業分野でSKタップ加工やフライス加工は、精密な製品製造に不可欠な技術です。これらの加工技術には、品質向上や効率化を図るために把握しておくべき重要なポイントがあります。例えば、正しい工具の選択は、加工精度に直接影響を及ぼしますし、工具の摩耗を定期的にチェックし交換することで、常に最良の状態で加工を継続することができます。また、適切な切削条件を選定することは、加工時間の短縮と工具寿命の延長の両方に寄与し、コスト削減にも繋がります。具体的な例としては、SKタップ加工では、タップの種類に応じた速度と進行方向の制御が重要です。フライス加工では、刃の数や形状、回転速度によって仕上がりの精度が変わってくるため、これらを適切に選択する必要があります。こうした知識を身につけることで、加工技術はさらに発展し、より高品質な製品の製造が可能となります。結論として、SKタップ加工やフライス加工の精度と効率化を追求することで、日本の製造業は競争力を維持し、さらなる成長を遂げることができるでしょう。
まとめ
SKタップとフライス加工の重要ポイント10選
1. 適切な切削条件を選定する
2. 適切な工具選びをする
3. 適切な刃先形状を選ぶ
4. 適切な刃先加工を行う
5. 適切な刃先コーティングを施す
6. 適切な刃数を選択する
7. 適切な切削速度を設定する
8. 適切な送り速度を設定する
9. 適切な切り込み深さを設定する
10. 適切な切削液を選ぶ
SKD用タップ加工完全ガイド:精度を高める技術とは?
SKD用タップ加工完全ガイドでは、精度を高める技術について解説します。SKDやタップ加工、フライス加工に慣れている方も初心者の方も、このガイドで新たな知識を得ることができます。精密な加工技術は、製品の品質向上に欠かせない要素です。このガイドを通じて、より高い精度を実現するためのテクニックやノウハウを学んでみましょう。
1. SKD タップ加工入門:基本となる選定基準
SKD用タップ加工は、精密なねじ加工が求められる分野での重要な技術です。この工程の成功は、適切なタップと加工条件の選定に依存します。具体的には、SKD材に応じた適切なタップを選び、切削速度や送り速度などのパラメータを最適化することが必要です。たとえば、フライス加工で使用するタップは、硬度や耐熱性を考慮して選ばれることが一般的です。これにより、SKD材の硬さや切削時の高温に耐えうるタップが選定されるため、正確で長寿命のねじ加工が可能となります。この選定基準を踏まえることで、SKDタップ加工の精度は大幅に向上し、高品質な製品製造に寄与します。結論として、タップ選定と加工条件の最適化は、SKD加工技術を精度高く遂行する上で不可欠です。
2. 超硬タップの選び方:SKD タップ加工での決定要因
SKDタップ加工において、製品の精度を高め、効率的な作業を実現するには適切な超硬タップの選択が欠かせません。SKDとは、工具鋼の一種であり、耐摩耗性や耐熱性に優れています。この特性に適したタップを選ぶことで、精密なねじ切り加工が可能になります。具体的には、フライス加工に適した形状や刃の設計を持つタップを選定する必要があります。例えば、高硬度のSKDに対応した特殊なコーティングが施されたタップは、耐久性を高めると同時に、加工中の熱の影響を抑える効果があります。また、切り屑の排出性能が高いタップを選ぶことによって、スムーズな加工が行え、加工後の清掃時間も短縮されます。このように、適切なタップを選ぶことで加工の精度が向上し生産性が高まるため、SKDタップ加工における最適なタップ選びは非常に重要なポイントとなります。
3. 精度を決める!SKD タップ加工の精度向上テクニック
SKDタップ加工で精度を高めることは、高品質な製品を生産する上で不可欠です。この工程は、製品の組み立てや機能性に直接的な影響を及ぼすため、重要な工程とされています。例えば、フライス加工を伴うタップ加工では、工具の刃先角度や加工速度が精度を左右します。切削条件を適切に管理することで、ねじ山の精度が向上し、結果として耐久性や信頼性の高い製品が得られます。また、切削油の選定や冷却方法の最適化も、精度向上に寄与する要素です。適切な設備投資と運用を行い、これらの技術を磨くことで、SKDタップ加工の精度は大きく向上します。したがって、精度を高める技術が製品品質を決定づけるといえるでしょう。
4. SKD タップ加工におけるフライス加工の役割
SKD用タップ加工において、フライス加工技術の精度向上は、極めて重要です。フライス加工により、タップ加工に必要な前穴を精密に加工することで、タップ切りの精度が向上します。例えば、自動車のエンジン部品や構造体に使われるSKD材へのタップ加工では、ネジの締結強度が要求されるため、フライス加工での前穴の位置精度や寸法精度が極めて重要になります。これにより、タップ加工後のネジの嵌合精度が保証され、耐久性や信頼性の向上に寄与します。フライス加工の技術向上は、製品品質の向上と直結しており、SKD材を用いた高性能部品製造において不可欠です。そのため、まずは精密なフライス加工技術の確立が求められ、それがSKDタップ加工の精度を高める技術と言えるでしょう。
5. 高硬度鋼対応!SKD用超硬ハンドタップの使い方
SKD用タップ加工において、加工精度の向上は重要なテーマです。SKD素材は高硬度であり、その性質から通常のタップ加工では摩耗や破損のリスクが高まります。しかし、適切な技術を用いることでこの問題は克服可能です。たとえば、超硬合金を用いたハンドタップは、SKDのような高硬度鋼に対応しており、耐久性に優れています。実際に、フライス加工と合わせて使用することで、タップの先端が正確に位置づけられ、ねじの精度が飛躍的に向上します。最終的には、SKD用タップ加工で優れた精度を実現するには、超硬ハンドタップの正確な使い方を理解し、適用することが不可欠です。この技術的な進歩が、製造業の効率化と品質向上を支えます。
6. SKD タップ加工に最適な金型材料の選び方
SKDタップ加工における精度向上は、製品の品質を左右する重要な要素です。そのため、最適な金型材料の選定が必須となります。SKDは炭素鋼等の合金素材であり、優れた耐摩耗性と加工性を持っています。これにより、フライス加工時の精密なタップ形成が可能になるため、多くの専門家が推奨する素材です。実際の例として、精密部品を製造している工場ではSKD素材を利用した金型で加工を行い、高い評価を受けています。このように、SKDを使用することは、タップ加工における精度の高さを実現し、最終製品の信頼性を保つ上で欠かせないのです。結論として、SKD素材はタップ加工において最適な選択であり、その優れた特性を利用することで、加工精度を飛躍的に向上させることができます。
7. SKD タップ加工のトラブルシューティング:よくある問題と解決策
SKDタップ加工における精度を高めるためには、特有の技術が求められます。SKDという素材の特性上、正確な加工をするためには、適切な工具選びと加工方法が不可欠です。たとえば、フライス加工に適した高硬度のタップを選ぶことで、ねじ山の精度が向上し、製品の品質が安定します。また、適切な切削油を用いることで、タップの摩耗を防ぎながら滑らかなねじ加工を実現することができます。これらの方法を用いることで、SKDタップ加工の精度は飛躍的に向上し、長期にわたる安定した生産活動に寄与します。最終的には、これらの技術を駆使することで、高品質な製品を提供できるという結論に至ります。
8. SKD タップ加工の未来:進化する技術と市場の動向
SKD用タップ加工は、精密な工作物の製造において不可欠な技術です。この加工方法は、複雑な形状を持つ金属材料へのねじ切りに特化しており、その使用は日本の製造業において広く普及しています。SKD材の特性上、高い精度を要求される場面が多く、適切な技術の選択が品質向上に直結します。例えば、フライス加工を用いることで、均一なねじ溝を精密に加工することが可能となり、これが高品質なSKDタップ加工の要となります。加えて、加工精度を高めるためには、適切な切削液の選択や、切削速度の最適化が重要です。これらの技術の進化と共に、産業界におけるSKDタップ加工の需要は今後も拡大していくと考えられます。最終的に、高度な技術により、精度の高い加工が求められる場面でSKD用タップ加工の価値は一層高まることでしょう。
まとめ
SKD用タップ加工では、適切な刃先や刃先形状の選択が非常に重要です。また、適切な刃先冷却や切削油の利用も精度向上につながります。さらに、フライス加工の際には適切な刃先形状や刃先材質の選択が重要です。技術的な理解と適切な装置の選択が精度向上につながります。
SKD材加工の新常識!フライス&タップで品質アップの方法
SKD材加工における新しい常識を紹介します。この記事では、フライス加工とタップ加工を駆使して品質を向上させる方法について解説します。SKD材を使用した加工にお悩みの方、品質改善を目指す方にとって、この記事は貴重な情報源となるでしょう。
1. SKD材加工の入門ガイド
SKD材の加工において、フライス加工とタップ加工が品質向上の新常識として注目されています。SKD材はその硬度から加工が難しく、精密な部品製造において品質維持が重要なポイントです。特にフライス加工は、複雑な形状や平滑な表面を得ることができ、同時にタップ加工は、ネジ穴を正確に加工する際に必要不可欠です。具体的な事例として、自動車や航空機の部品製造では、この二つの技術が組み合わさることで、高い耐久性と精度を要求される部品の品質向上が見込まれます。このようにフライスとタップ加工を適切に組み合わせることで、SKD材のポテンシャルを最大限引き出し、優れた製品を生み出すことが可能になるため、加工業界において新たな標準となりつつあります。
2. SKD タップ加工の基本
SKD材を使用したタップ加工は、高品質な製品づくりに欠かせない重要な工程です。この加工においては、硬質であるSKD材の性質を理解し適切なフライス加工を施すことが、品質向上の鍵となります。例えば、SKD材のタップ加工には、摩耗に強い工具を選び、適切な切削速度や送り率を設定することが重要です。これにより、タップの精度を高め、ねじ山の形成を均一にすることができます。また、フライス加工では、SKD材の硬さに対応するために、高い切削能力と耐久性を持つ工具選びが重要であり、こうした選択により加工時の負担軽減と、仕上がりの品質向上が期待できます。結論として、SKD材の加工には正しい工具選びと加工条件の最適化が不可欠であり、これにより製品の品質が飛躍的に向上することでしょう。
3. マシニングセンタを活用したSKD タップ加工
3-1. マシニングセンタでのタップ加工の方法
マシニングセンタでのタップ加工は、SKD材の精度を向上させる新常識となりつつあります。従来の工法と比べて、フライス加工と組み合わせることで、より高精度な加工が可能になるということがその理由です。具体的には、フライス加工で予め穴を開け、その後にタップ加工を施すことで、ねじの精度が向上します。なぜなら、フライス加工によって穴の位置が正確に決まり、タップ加工の際のねじれやズレが格段に減少するからです。この方法により、SKD材を使用した部品や製品の品質は一段と高まり、耐久性や信頼性が要求される分野での利用が拡大しています。結論として、フライスとタップの組み合わせは、加工精度と効率の両面で利点が大きく、SKD材加工の新たなスタンダードとして注目されています。
4. SKD焼入れ鋼とリジッドタップ加工
4-1. 焼入れ鋼へのリジッドタップ加工の実行可能性
焼入れ鋼(SKD材)へのリジッドタップ加工は高い品質と生産性を実現するための新常識となっています。これは、フライス加工で先に穴あけを行い、その後タップ加工を施すことで、精度の高いねじ加工が可能になるからです。具体的には、フライス加工では、高剛性の工具を使用して精密な穴を開けることが求められます。これによって、タップ加工では、ねじの山を正確に形成することができるのです。さらに、リジッドタップ加工は、一般的なタップ加工と比べて振動が少なく、工具の寿命も延びるという利点もあります。その結果、焼入れ鋼への加工は、より効率的でコストパフォーマンスに優れ、一貫した品質を保つことが可能となりました。このため、SKD材を使用する製造業においては、フライスとタップを組み合わせることが、品質向上のための新たなスタンダードとして注目されているのです。
5. SKD11メーカーの選び方
5-1. SKD11メーカーの比較情報
SKD材加工における新たな手法が注目されています。特にフライス加工とタップ加工の組み合わせによる品質向上がその理由です。フライス加工によって、SKD材の表面をなめらかに整えることができる一方で、タップ加工は精密なねじ切りを可能にし、製品の精度を格段に高めます。たとえば、金型製作における一貫した加工精度は、製品寿命を伸ばし、メンテナンスコストの低減にも繋がります。このようにフライスとタップを駆使することで、耐久性と信頼性が増すSKD材の加工技術は、製造業界において新常識となりつつあります。最終的に、この加工技術はコスト効率の良い生産を実現し、業界全体の品質向上に寄与すると考えられます。
6. 特殊鋼フライス加工のテクニック
6-1. 特殊鋼フリープレートの利用方法
特殊鋼フリープレートの加工においてフライス加工とタップ加工は品質向上に不可欠です。これらの加工法は、SKD材の固さと耐熱性を考慮した選定が肝要であり、適切な工具と加工条件の見極めが重要です。例えば、フライス加工では刃の材質を選ぶことが精度を高めるポイントであり、タップ加工においては、先端の角度や溝の形状がねじ切りの品質を左右します。特にSKD材は硬度が高く加工が困難とされてきましたが、これらの加工方法を駆使することで、精度良く、効率的に加工することが可能になります。このようにフライスとタップの適切な加工法の採用は、SKD材の加工品質を飛躍的に向上させ、ワークピースの寿命を延ばし、最終製品の信頼性を高める効果があります。だからこそ、加工技術の進化とともに、これらの方法が新しく、また常識として認識されているのです。
まとめ
SKD材加工では、フライス加工とタップ加工を組み合わせることで効率的かつ高品質な加工が可能です。フライス加工によって精度の高い形状加工を行い、タップ加工によって内部へのねじ加工を行うことで、品質アップが期待できます。新しい方法を取り入れて、より効率的にSKD材の加工を行いましょう。
【業界の常識を変える】SKタップを使用した革新的なフライス加工法
革新的なフライス加工法で業界の常識を変える、SKタップを使用した新たな加工方法についてご紹介します。SKタップを使用することで、従来のフライス加工と比べてどのような利点があるのか、そしてどのようにして効果的に活用するのか、詳しく解説します。従来の常識にとらわれず、新しい技術を取り入れることでどのようなメリットが得られるのか、ぜひご覧ください。
1. SK タップ加工とは何か:切削加工の基礎
革新的なフライス加工法として、SKタップを使用した加工法が業界の常識を変えつつあります。伝統的なフライス加工に比べて、SKタップを用いた方法は、より高速かつ精密な加工を実現します。具体例として、従来の加工法では到達できなかった微細なねじれ形状の加工が可能になるなど、その優位性は明らかです。この方式では、工具の耐久性も向上し、長期にわたって安定した加工品質を保つことができるため、コスト削減にも大きく寄与します。結論として、SKタップを使用したフライス加工法は、時間とコストの節約だけでなく、加工品質の向上にも寄与するため、今後も注目されると考えられます。
2. 切削加工業界における最近の課題
切削加工業界では、生産性の向上とコスト削減が最近の大きな課題となっています。この二つの課題に応えるため、SKタップを使用した新しいフライス加工法が注目されています。SKタップ加工は、従来のタップに比べて、寿命が長く、加工スピードが速いという利点があります。具体例として、自動車産業での利用が挙げられます。自動車部品の製造では多くの穴あけ加工が必要であり、SKタップを用いることで作業時間の大幅な短縮が図れるため、大量生産において大きなアドバンテージとなります。さらに、SKタップは切削精度も高いため、高品質な製品をより効率的に生産することができるのです。このようなSKタップを使った加工法の普及は、今後業界の常識を変え、より良い製品を迅速に提供することに貢献すると考えられます。
3. 1-1. フライス加工の基本
フライス加工の分野では、SKタップを使用した加工法が業界の常識を変える可能性を秘めています。従来のフライス加工では、工具の限界があり、加工の効率と精度の向上には限界がありました。しかし、SKタップを採用することにより、これらの課題が大きく改善されると期待されています。たとえば、SKタップは特に硬い素材を加工する際にその優れた切削能力を発揮し、一度により多くの材料を取り除くことが可能です。これは、加工時間の短縮とコスト削減に寄与し、製造業にとって大きなメリットです。また、耐久性にも優れており、工具の交換頻度の低減も実現できます。SKタップを使ったフライス加工は、より効率的でコストパフォーマンスに優れた製造プロセスを実現するための鍵となるでしょう。
4. 1-2. SK タップ加工のフライス加工への応用
SKタップを使用したフライス加工法は、業界の常識を変える可能性を秘めています。従来のフライス加工方法では、加工時間や工具の寿命に課題がありました。しかし、SKタップを応用することで、これらの課題が大幅に改善されることが期待されます。たとえば、SKタップを用いた加工法は、切削速度を上げることができ、より短時間での加工を実現します。また、工具の摩耗を減らし、長寿命化を促進することにも寄与します。これは、加工現場でのコスト削減や生産効率の向上に直結します。結果として、SKタップを採用した新しいフライス加工法は、経済的な利益をもたらすだけでなく、業界全体のプロセス改革を促進するキーテクノロジーとなることでしょう。
5. プラスチック下肢装具におけるSKタップ加工の利点
プラスチック下肢装具の製造においてSKタップを用いたフライス加工法が注目されています。これは、従来の製法に比べて加工時間の短縮と精度の向上が図れるためです。例えば、装具の調整に必要な細かなスレッド加工が、SKタップによって高い精度で迅速に施されます。これは、リハビリテーションの分野で患者さんに提供する装具のカスタマイズを、より効果的かつ効率的に行うことを可能にします。結果として、患者さんの快適性と装具の機能性が大幅に向上します。また、材料の無駄を削減することにも寄与し、持続可能な生産活動への貢献が期待できます。このSKタップ加工の革新的な利用法は、今後、プラスチック下肢装具産業のスタンダードになる可能性が高いと言えるでしょう。
6. 2-1. 設計の観点から見た下肢装具とフライス加工
SKタップを用いたフライス加工法は、業界の常識を変えるほどの革新的な技術です。従来のフライス加工では、多くの工程と時間を要し、効率性に課題がありました。しかし、SKタップを使用することで、これらの課題が大幅に改善されます。例えば、SKタップは一度の工程で複数の穴加工を同時に行う能力を持っており、これにより加工時間の短縮が可能になるのです。また、SKタップはその精度の高さから、加工後の仕上げにかかる時間も削減できるため、全体の生産効率が向上します。特に、精密な加工が求められる電子部品や自動車部品の生産において、この技術は大きなメリットをもたらすことでしょう。結論として、SKタップを使用したフライス加工法は、その効率性と精度の高さから、製造業の生産性向上に貢献することが期待されます。
7. 2-2. 機能性を高めるSKタップ加工技術
SKタップを使用した革新的なフライス加工法が、業界の常識を覆す可能性を秘めています。これまでのフライス加工は、一定の限界に直面していましたが、SKタップを用いることで、加工精度の大幅な向上が実現されています。例えば、難削材の加工や複雑な形状の加工において、SKタップは優れた性能を発揮し、これまでの方法では達成が難しかった仕上げ面の質を向上させることができました。この技術は、精密部品を要求される航空宇宙産業や自動車産業など、多岐にわたる分野での応用が考えられ、加工工程の効率化だけでなく、製品品質の向上にも寄与します。さらなる技術開発と普及により、SKタップを使用したフライス加工は、製造現場の新しいスタンダードとなることでしょう。
8. 5軸加工技術とSKタップの融合
SKタップを使用した新しいフライス加工法は、業界の常識を変える可能性を秘めています。従来のフライス加工では、精密なねじ加工を実現するために多くの時間とコストが必要でした。しかし、SKタップを取り入れることで、これらの問題が大幅に改善されます。例えば、SKタップは、切削抵抗が低く、長寿命であるため、加工時間を短縮し、工具コストを削減することができます。また、SKタップによる加工は、非常に高い精度と仕上がりの良さを実現し、これまで困難だった複雑な形状のねじ加工も可能にします。このようにSKタップを用いたフライス加工は、加工品質の向上、コスト削減、そして生産効率の向上という点で、従来の加工方法を凌駕するものです。今後、この技術が広く普及すれば、製造業界における生産性の大きな革新となるでしょう。
9. 3-1. 5軸加工による難削材の取り組み
産業界においてSKタップを用いたフライス加工法は、その優れた加工効率と精度で常識を変えつつあります。この革新的な加工法は、硬い材質でも精密なねじ加工が可能となり、多くの製造業者にとっての救世主となっています。例えば、航空機や自動車の部品製造において、SKタップは困難な加工を可能にし、生産性の向上に寄与しています。品質と生産のスピードは、製造業において最も重視される要素であり、この新しい方法が広く採用される理由です。また、専門的な設備も必要なく、既存のフライス加工機をそのまま使用できるため、導入の敷居も低いのが魅力です。これにより、生産ラインの更新を行わずとも、効率化とコスト削減に大きく貢献してくれるでしょう。最終的に、SKタップを使用したフライス加工法は、日本の製造業界において新たな標準となる可能性を秘めています。
10. 3-2. SKタップ加工を活用した難削材の加工法
SKタップを用いたフライス加工法は業界の常識を覆す革新的な技術として注目されています。この加工法は、特に難削材の加工において、従来の方法に比べて効率的かつ精度が高い結果をもたらします。例えば、航空機部品や医療機器などの製造に必要な難削材を用いた際に、SKタップ加工は素材の硬度を生かしつつ、きれいで正確なねじれの形成を実現します。これは、タップ加工において重要なことであり、製品の品質と生産性の向上に直結します。また、切削工具の寿命も延ばすことができるため、コスト削減にも寄与し、エンドユーザーにとっても大きなメリットがあります。このように、SKタップを使用した加工法は、高い効率性と経済性を実現し、加工業界における新たなスタンダードとなる可能性を秘めています。
11. ナフサ接触分解プロセスにおける革新的触媒の役割
新しいフライス加工法が業界の常識を変えようとしています。その中心にあるのがSKタップ加工です。これまでのフライス加工では、加工速度や精度に限界がありましたが、SKタップを使った方法はそれらの課題を大幅に改善しています。例えば、耐久性が高く加工速度が速いSKタップを使用することで、材料の切削時に生じる時間とコストを削減できます。さらに、SKタップは微細な調整も可能で、精度の高い加工を求める用途にも最適です。この技術の導入により、製造業はより高品質な製品を効率的に生産できるようになるでしょう。全体として、SKタップによるフライス加工は製造の現場でのコスト削減と生産性の向上に寄与し、産業の新たな潮流を作り出しています。
12. 4-1. 触媒を用いたプロセス基盤技術の概要
新たなフライス加工法としてSKタップの使用が注目を集めています。従来の加工方法に比べ、この方法は加工効率を大幅に向上させ、工業界に革命をもたらす可能性を秘めています。SKタップを用いたフライス加工は、特に硬い材料や複雑な形状の加工において、その優位性を発揮します。例えば、高硬度の金属を加工する際に、SKタップは切削抵抗を低減し、工具の摩耗を減少させることで、長寿命化を実現しています。これにより、工具交換の頻度が減り、生産性の向上に直結します。また、精密なスレッド加工が可能となるため、より複雑なデザインの製品製造に貢献しています。このようにSKタップは、フライス加工の効率と品質を向上させることで、業界の常識を覆す存在となりつつあります。
13. 4-2. SKタップ加工が可能にする革新的プロセス技術
新たなフライス加工法の導入により、SKタップを活用した加工技術が業界の常識を塗り替えています。これまでの加工法は限界がありましたが、SKタップ加工では、その限界を超える精度と効率を実現しています。具体的な例として、従来のフライス加工では到達できなかった微細な加工や複雑な形状の加工が可能になりました。この技術を駆使し、製造業がより高品質な製品をより速く、そしてコスト効率よく生産することができるようになっています。SKタップ加工は、その高い柔軟性と精度により、各分野での活用が期待されており、これからの製造業において中心的な役割を果たすことは間違いありません。この新しい加工法は、今後の各業界における生産性の大幅な向上を約束する、まさにゲームチェンジャーと言えるでしょう。
まとめ
SKタップを使用した革新的なフライス加工法は、従来のフライス加工方法と比べて高速かつ高精度な加工が可能です。SKタップは切りくずを効果的に取り除き、高剛性で高速回転が可能なため、効率的な加工が期待できます。この革新的なフライス加工法は、加工効率の向上に大きく貢献するだけでなく、加工精度の向上ももたらします。
SKタップの選び方とフライス加工で実現する高品質な仕上がりの秘密
SKタップの選び方とフライス加工で実現する高品質な仕上がりの秘密について、興味を持っている方は多いのではないでしょうか?本記事ではSKタップの選び方からフライス加工での高品質な仕上がりの具体的な方法まで、徹底的に解説します。もしあなたが精密な加工を行う際に高品質な出来栄えを求めているのであれば、ぜひこの記事を読んでみてください。
1. SK タップ加工とは?金属加工の基礎
SKタップ加工は、金属製品に内部ねじを切る工程の一つで、正確なねじ加工が求められるフライス加工の仕上がりの品質に大きく影響します。適切なSKタップを選ぶことは、耐久性のある高品質な製品を作り出すための鍵です。例えば、硬い材質を加工する際は、耐摩耗性に優れたコーティングが施されたタップが適しています。また、精細なねじを必要とする精密機器には、高精度なねじ加工が可能な高品質のSKタップが不可欠です。最終製品の用途や加工材に合わせた最適なタップ選びが、フライス加工での高い品質の実現に繋がります。結論として、SKタップの選択はフライス加工での精度と製品の品質を左右する重要なステップであり、適材適所の原理を適用することで、高品質な仕上がりを実現できるのです。
2. フライス加工の原理とSK タップの役割
フライス加工での高品質な仕上がりを実現するためには、適切なSKタップの選択が不可欠です。SKタップは、フライス加工時に内部ねじを切るために使用される工具であり、材質や形状が加工品質に大きく影響します。たとえば、硬い材料を加工する場合は、耐久性と硬度が高い高速度鋼(HSS)製のタップが推奨されます。また、精密なねじ加工を要する場合には、微細なピッチや特殊な形状のSKタップを選ぶことが、仕上がりの精度を左右することになります。さらに、適切な潤滑油の使用は、タップの摩耗を防ぎ、長寿命化を促進します。以上のポイントを考慮したSKタップの選択は、フライス加工において高品質な成果物を生み出すために、極めて重要です。
3. SK タップ加工の利点と金属加工における重要性
SKタップを選ぶことで、フライス加工における高品質な仕上がりが実現します。このタップ加工は、金属加工業界での精度と効率を重視したい場合に特に重要です。SKタップには、耐摩耗性に優れ、長寿命であるという特徴があり、その緻密なねじ山が正確なねじ加工を可能にします。例えば、自動車産業や航空機部品の製造では、このSKタップによる正確なねじ加工が品質の安定に不可欠です。また、多様な材料に対応する多種多様なタップが存在するため、用途に合わせたタップ選びが可能です。最適なSKタップを選ぶことで、工具の寿命を延ばし、生産性の向上にもつながります。総じて、SKタップの選び方を理解し適切に適用することで、金属加工の品質が向上し、経済的、効率的な生産が可能になるのです。
4. フライス加工機の選び方とSK タップの適用
フライス加工で使用するSKタップ選びは、製品の品質に大きく影響します。適切なSKタップを選ぶことで、加工面の精度を高め、高品質な製品を実現することができます。この選定において重要なのは、使用するフライス加工機の仕様と加工する素材の種類を考慮することです。例えば、硬い材料を加工する際には、より高硬度のタップを選ぶ必要があり、精密なねじ切りが求められる場合には、微細なピッチのタップを選定することが重要です。具体的な例として、航空宇宙産業で使用されるチタン合金の加工では、耐熱性や耐摩耗性に優れたSKタップが必要となります。このように選び方一つで、フライス加工における出来栄えが大きく変わるため、適切なSKタップを選定することは、高品質な製品を生み出す秘訣と言えるでしょう。
5. 超硬ピンゲージとリーマを活用した精密加工
SKタップの選び方には、フライス加工での高品質な仕上がりを実現するためのポイントがいくつかあります。結論から言うと、適切なSKタップを選ぶことで、加工物の精度を飛躍的に向上させることが可能です。理由としては、SKタップが持つ独特の刃形状や硬度が、材質を選ばずに均一なねじの加工を可能にするからです。具体例を挙げると、硬い材質の加工においてもタップの切れ味が長持ちし、ねじ山の形成が安定します。これは、作業の効率化だけでなく、切削精度の維持にも寄与し、再加工の必要性を低減します。最終的には、適切なSKタップの選択が、製品の品質を決定づけるとも言えるのです。
6. SK コレットキットとFMBバーの特性と選定基準
正確なフライス加工を行うためには、適切なSKタップを選ぶことが重要です。SKタップは、その精度と耐久性からフライス加工において優れた性能を発揮します。特に、硬い材料を加工する際には、精密なねじ切り加工が可能なSKタップが推奨されます。たとえば、高い硬度を持つ鋼材の加工においては、SKタップにより滑らかなねじ面が得られ、品質の向上が期待できます。また、繰り返しの使用においても磨耗しにくいため、長期にわたり安定した加工が可能です。結論として、フライス加工における高品質な仕上がりを実現するためには、用途に応じたSKタップの選択が不可欠です。耐久性と精度を考慮したSKタップは、繊細な加工を要求される場面でその真価を発揮します。
7. アルミ切削加工とプレート加工の技術動向
SKタップ選びは、フライス加工における高品質な仕上がりを実現する上で非常に重要です。適切なSKタップを選ぶことで、加工物の精度が飛躍的に向上し、長期間の使用に耐えうる耐久性を確保できます。例えば、切削速度に応じたタップの選定や、適切な摩擦係数を持つタップの使用は、材料の負担を減らし精度の高い加工を可能にします。実際、日本における精密加工分野では、こうした高機能なタップの選択が一般的であり、これによって得られる滑らかな表面仕上げと正確なねじ山は、製品の品質を大きく左右します。再度強調しますが、最適なSKタップの選定は、フライス加工における成功のカギとなり、より良い製品を市場に送り出すために不可欠です。
8. SK タップ加工におけるトラブルシューティングと対策
高品質なフライス加工を実現するためには、適切なSKタップの選び方が重要です。SKタップ加工においては、材質や被削材の硬度、加工速度などの条件を考えながら、適したタップを選定することがトラブルを避けるカギとなります。例えば、アルミニウム合金や銅などの非鉄金属を加工する際は、切削抵抗が低くなるように設計されたSKタップを選ぶことで、切りくずの排出がスムーズになり、加工面の仕上がりが良くなります。また、硬い材料を加工する場合には、耐久性に優れた高硬度のタップを選ぶことで、精度良く長期間の使用が可能となります。これらの選定を正しく行うことで、フライス加工における高品質な仕上がりを実現し、製品の信頼性を高めることができます。
9. フライス加工プロジェクトの成功事例とSK タップの効果
フライス加工では、SKタップの選び方が仕上がりの品質を左右します。SK タップを正しく選べば、高精度で滑らかなねじ山を実現できるのです。この選択が、加工精度と効率を高め、長期的に見てコスト削減にも繋がります。例えば、硬い素材を加工する際には耐久性の高いSKタップを使用することで、摩耗を減らし長持ちさせることができます。また、独自の刃先形状を持つタップは、切りくずの排出を改善し加工時間を短縮します。加工材料や切削条件に応じた適切なSKタップを選定することで、加工物は一貫した品質を保ちつつ、作業の効率もアップします。その結果、フライス加工プロジェクトは成功し、高品質な製品が安定して生産されるのです。
10. 将来のSK タップ加工とフライス加工技術の展望
SKタップの選択とフライス加工を用いた高品質な仕上がりは、金属加工業界において非常に重要です。正しいSKタップを選ぶことで、ネジ切りの精度が向上し、製品の信頼性が高まります。具体的な例として、小型の精密機器の組み立てにおけるSKタップの選択は、その機器の性能を大きく左右します。高品質なフライス加工も同様で、適切な刃物と条件を選ぶことで、表面の滑らかさや寸法の正確さが保証されます。フライス加工では、例えば航空宇宙部品の製造において、高い精度が求められるため、厳格な基準の下で行われます。SKタップ選びとフライス加工技術は相乗効果を生み出し、優れた品質を生むために不可欠です。したがって、これらの工具や技術を正しく選択し、適用することで、製品の高品質な仕上がりを実現することができるのです。
まとめ
SKタップを選ぶ際には、材質や切削条件に合ったものを選ぶことが重要です。また、フライス加工を行うことで高品質な仕上がりを実現することができます。適切な刃先形状や刃先材質を選ぶことで、加工精度や耐摩耗性を向上させることができます。
【2023年最新】フライス加工入門!SKタップで高精度を実現するコツ
2023年最新のフライス加工に興味はありますか?SKタップを使って高精度な加工を実現するコツを知りたいと思っていませんか?本記事では、フライス加工とSKタップ加工の基本から最新のテクニックまでを網羅した内容をお届けします。これからフライス加工を始めたい方や高精度な加工を目指す方にとって、役立つ情報が満載の記事となっています。
1. SK タップ加工 フライス加工 の最近の課題
フライス加工の分野で注目されるSKタップ加工は、高精度なねじ加工が可能となり、2023年もその需要は高まっています。SKタップとは、特に金属加工において内部ねじを切るために使用される工具で、精密な加工が求められる産業において重宝されています。加工精度を上げるコツとしては、適切な切削速度の選定や切削油の使用、そして工具の刃先の状態を常にチェックすることが挙げられます。例えば、航空機の部品などの精度が要求される製品を作る際、SKタップ加工により精密なねじの形成ができ、製品の品質を大きく左右します。したがって、正しい知識と技術があれば、SKタップ加工は高精度な加工結果をもたらし、製造産業における利益向上に直結するのです。
2. コストダウンのための機械部品加工見積り戦略
フライス加工において、SKタップ加工の使用は高精度な部品作成を可能にします。日本の製造業では、精度の維持が不可欠であり、SKタップはその核となる要素です。その理由は、SKタップが優れた切削性能と耐久性を持ち合わせているため、加工時の安定性が増すからです。例えば、金属部品の内部にねじを切る際、SKタップを使用することで、滑らかなねじ面が得られ、ねじ山が正確で丈夫な仕上がりとなります。これにより、部品の組み立てや取り付けが容易となり、製品の品質向上に直結するのです。結論として、フライス加工におけるSKタップの活用は、コストパフォーマンスと品質の両面においてメリットが大きく、今後の製造業における競争力を高めるためには、その適用を積極的に考慮するべきでしょう。
3. S45C材料を用いたSK タップ加工 フライス加工 のポイント
フライス加工における高精度な仕上がりを実現するためには、適切な工具の選択が必要不可欠です。特に、S45C材料の加工にはSKタップが適しています。SKタップは、その耐久性と精度の高さから、フライス加工の現場で高く評価されています。例えば、S45Cという炭素鋼は硬度が高く加工が難しい材料ですが、SKタップを使用することで、確実なねじ切りが可能となり、製品の品質向上に寄与します。正しい切削条件と組み合わせることで、加工面のバリの発生を抑え、滑らかな表面を実現することができるのです。結論として、SKタップを用いることで、S45C材料のフライス加工においても高い精度と仕上がりを求めることが可能になります。
4. 切削部品設計の基礎とeラーニングリソース
フライス加工は精密な加工技術であり、SKタップを使った加工法はその高精度性から注目されています。フライス加工におけるSKタップの使用は、ねじ山の精度向上に大きく寄与します。特に、耐久性や締結力が要求される部品において、その利点は顕著です。たとえば、自動車や航空機の部品製造では、SKタップによる加工が不可欠となっています。このタップは、一貫した品質と高い再現性を実現するための重要なツールです。まとめると、SKタップを用いることで、フライス加工の精度を大幅に向上させることができるため、高品質な製品を効率良く生産するためには欠かせない技術であるといえます。
5. 門形五面加工機の利点とSK タップ加工 フライス加工 への応用
門形五面加工機を用いたSKタップ加工はフライス加工の精度を大幅に向上させる手法です。この加工方法の利点は、一貫性のある精度と加工の効率性にあります。例えば、SKタップを使用することで、ねじの加工において均一なピッチと精度を保つことが可能になります。これは、複雑な形状や精密な部品の製造において重要な要素です。さらに、SKタップによる加工は摩耗の少ない工具寿命の延長という利点もあります。結論として、SKタップを用いたフライス加工は、製造業において高精度な部品作りと生産性の向上に寄与し、2023年においてもその重要性は増すばかりです。
6. 実践!SK タップ加工 フライス加工 の精度を向上させるテクニック
フライス加工の精度を向上させるには、SKタップ加工が鍵となります。フライス加工は金属やプラスチックを削るために用いられる一般的な手法であり、SKタップはその加工性能を飛躍的に高めることで知られています。特に、内部ねじ加工においては、SKタップを使用することで、高い寸法精度と優れた表面粗さを実現することが可能です。例えば、精密部品を製造する際、SKタップを使用することで、ねじのピッチや深さが一貫しており、後の組み立て工程での誤差を最小限に抑えられます。このように、SKタップによるフライス加工は精度が要求されるさまざまな製品製造において不可欠であり、2023年においてもこの技術は多くの工場で積極的に採用されています。締めることで、SKタップを使用したフライス加工が、高精度の製品作りに欠かせない理由が明らかになるでしょう。
7. SK タップ加工 フライス加工 を活用した工業製品の事例紹介
フライス加工は、工業製品の精密な部品作りに不可欠な技術です。最新のSKタップを用いることで、その精度を一層高めることができます。SKタップは、優れた切削性能と高い耐久性を兼ね備え、フライス加工の効率を格段に上げることができます。例えば、自動車のエンジン部品や航空宇宙産業の部品加工では、SKタップによる精密なねじ切り加工が必須とされています。これらの分野では、ミクロン単位での精度が要求されるため、SKタップを使用したフライス加工は適しているのです。さらに、SKタップは耐久性に優れているため、長期間にわたって安定した品質の維持が可能です。このように、SKタップを活用したフライス加工は、精密工業製品の生産に欠かせないテクニックです。
8. SK タップ加工 フライス加工 の将来性と業界動向
フライス加工の分野でSKタップを用いることは、高精度の加工を実現する上で不可欠です。まず、フライス加工における高精度を求める理由として、製造業における品質の競争力が挙げられます。具体的には、自動車や航空機の部品など、寸法精度が求められる製品でSKタップの利用が重要です。SKタップは、優れた切削性能と長寿命を併せ持つことから、正確で効率的な加工が可能となります。また、フライス加工におけるSKタップの適用事例には、金型の微細な加工や複雑な形状を持つ部品の加工などがあります。これらの例からも、SKタップは加工精度を高め、製品の品質を向上させるために必須の工具であることがわかります。今後、さらに加工技術が進化していく中で、SKタップによるフライス加工は業界の新たな標準となり、製造現場における効率と精度の向上が見込まれます。
まとめ
フライス加工では、高精度を実現するために正しい工具の選定と適切な加工方法が重要です。SKタップ加工は、正確な加工を実現するための重要な工程です。適切な刃先形状や切削速度、切り込み量などを工夫することで、高精度なフライス加工を実現することができます。
【2023年版】S45C材のタップ加工・フライス加工!最新の効率的な方法
2023年、S45C材のタップ加工・フライス加工について最新の効率的な方法をご紹介します。S45C材の加工方法は常に進化しており、最新のテクニックやツールを使うことでより効率的な加工が可能です。この記事ではS45C材の特性や最新の加工方法について詳しく解説し、タップ加工やフライス加工における効率的な手法を具体的に示します。S45C材を使用した加工に興味がある方や効率的な加工方法を学びたい方にとって、この記事は貴重な情報源となるでしょう。
1. S45C タップ加工・フライス加工の基本
1-1. S45Cとは?炭素鋼の特徴と用途
S45C材は、機械部品や金型など幅広い用途に用いられる炭素鋼であり、優れた機械的性質を有しています。そのため、タップ加工やフライス加工などの切削加工が頻繁に行われることがあります。加工の効率を上げる新しい方法として、2023年には高精度で耐久性の高い工具の使用が推奨されます。例えば、マルチコーティングが施された切削工具は、S45C材の加工時における耐摩耗性を向上させ、長寿命を実現します。また、高速加工可能なカーバイド工具も、切りくずの排出を促進し、加工速度の向上に寄与しています。さらに、適切な冷却剤の使用は、工具の摩耗を抑え、品質の一貫性を保つ上で効果的です。これらの進歩は、加工の効率と品質の両方を高めるために不可欠で、結果的に生産性の向上に貢献するでしょう。
1-2. タップ加工とフライス加工の違い
2023年、日本国内でのS45C材の加工において、タップ加工とフライス加工の方法がさらに進化し、効率的な生産を実現しています。まず、タップ加工の新しい手法では、高精度の加工を可能にする多機能CNC機械を使用することで、一貫した品質と加工速度の向上が図られています。例えば、回転速度と送り速度を最適化した同時複合加工は、従来の単機能機に比べて生産効率を飛躍的に向上させています。一方、フライス加工に関しても、切削抵抗を低減する新型の刃物が開発され、従来の工具よりも長い寿命と高い切削能力を実現。これにより、S45C材を始めとする多種多様な材料に対して、より短時間で精度の高い加工が可能となりました。このような最新の技術により、S45C材のタップ加工及びフライス加工は、より効率的で経済的な生産へと進化しているのです。
1-3. 金属材料としてのS45Cのメリット
S45C材は、耐摩耗性や機械的特性に優れた金属材料として利用され、そのタップ加工・フライス加工技術は2023年においても大きく進化しています。具体的には、多軸制御のCNC(コンピュータ数値制御)機械を利用した加工が主流となっており、これにより複雑な形状であっても高精度かつ効率的に加工が行えるようになりました。さらに、加工液の改良により、摩耗を抑えつつ速い切削速度を実現することが可能になり、製品の品質向上と生産効率の両方を実現しています。これにより、S45C材の加工技術は、経済性と環境への配慮を兼ね備えたものに進化し、製造業における競争力の強化に寄与しているのです。最新の加工技術を取り入れることは、今後の産業発展にも不可欠であり、S45C材を用いる企業にとって重要な戦略となっています。
2. S45C タップ加工の基礎知識
2-1. タップ加工に必要な工具とその選び方
S45C材の加工には、適切な工具選びが欠かせません。特にタップ加工とフライス加工では、精密さと効率が要求されます。2023年現在、S45C材の加工方法には更なる進化が見られ、作業効率を大幅に向上させる新たな技術が導入されています。たとえば、タップ加工では、マルチリードタップの使用が増えており、複数のリードを持つことで一度の回転でより多くのねじ山を切ることができ、加工時間の短縮に貢献しています。また、フライス加工においては、高精度なカッターが開発され、耐摩耗性の向上によって長寿命を実現し、コストパフォーマンスの高い加工が可能になっています。これらの工具を選択することで、S45C材の加工精度を高め、生産効率の向上が期待できます。
2-2. S45Cのタップ加工における注意点
S45C材のタップ加工にはいくつか注意すべき点があり、それらを理解しておくことで効率的な加工が可能です。S45Cは一般的な機械構造用炭素鋼であり、優れた機械的性質を持つため多くの工業製品に利用されています。しかし、その硬度と強度のため加工性には特有の難しさが存在します。具体的には、タップ加工では正しい切削油の選定が重要であり、これによりスムーズな切りくずの排出とタップの寿命を延ばすことが可能になります。また、正確なピッチと直角度を確保するために、CNC加工機を用いることが現在の最善策とされています。フライス加工においても、適切な切削条件の選定が重要で、工具の摩耗を抑えつつ、高精度での加工を実現できます。これらの注意点を踏まえることで、S45C材の加工はより効率的かつ精度高く行うことができ、2023年における最新の方法と言えるでしょう。
2-3. タップ加工の工程と最適な条件
S45C材のタップ加工やフライス加工において、2023年ではさらに効率的かつ精度の高い方法が注目されています。S45Cは一般的な炭素鋼であり、機械構造用鋼として広く使用されているため、加工技術の向上は産業界において重要な意味を持ちます。特に、タップ加工における最新の工具の使用や、フライス加工における最適な速度と送りの設定が、生産効率とコスト削減に役立つとされています。具体的な例として、マルチアクシスマシニングセンターを活用した複雑な形状のフライス加工や、変数リードタップを使用することで、ねじ山の精度を格段に向上させることができるという報告があります。これらの新しい方法は、従来の加工法に比べて、加工時間の短縮および製品品質の向上を可能にしており、今後も更なる技術革新が期待されます。結論として、タップ加工、フライス加工ともに、適切な技術選択と工程管理によって、S45C材の加工効率を高めることができるのです。
3. S45C フライス加工の技術解説
3-1. フライス加工における切削工具の種類
2023年版のS45C材のタップ加工・フライス加工方法について、効率的かつ最新の技術を見ていくことは、製造業者にとって重要です。S45C材は硬度が高く加工しにくい特徴があるため、正確な加工方法を選ぶことが肝心です。たとえば、タップ加工では、最新のマルチコーティングされたタップを使用することで、耐摩耗性を高め、長寿命を実現できます。フライス加工においても、同様に最新のコーティング技術を施したエンドミルの使用により、精度の高い加工が可能となります。さらに、適切な切削速度や送り速度の選定は、効率化を図るうえで不可欠です。これらの最新の方法を取り入れることで、S45C材の加工における時間短縮とコスト削減を実現し、結果として品質の高い製品が生産できるのです。
3-2. S45Cフライス加工のパラメータ設定
S45C材を用いたタップ加工やフライス加工において、2023年は効率が一層重視されるようになりました。精度を保ちつつ、加工時間の短縮やコスト削減に繋がる新しい方法が求められています。具体例として、マルチアクシスマシニングを活用することで、従来の加工に比べて手戻りを減らし、一度のセットアップで多面加工が可能になり、加工効率を大幅に向上させることが出来ます。また、最新のCNCマシンの導入により、より複雑な形状でも高速かつ正確に加工することが可能となります。このような技術革新によりS45C材のタップ加工・フライス加工は、これまで以上に効率の良い生産が期待されるのです。
3-3. フライス加工時の切削油の役割
2023年におけるS45C材の効率的なタップ加工・フライス加工については、最新の技術と知見を用いることが重要です。とりわけ、S45C材はその強度と加工性のバランスから、様々な工業製品に利用されているため、効率化は生産性向上に直結します。例えば、フライス加工時には、切削油の正しい選択と使用が、工具の摩耗を抑え品質を維持するうえで不可欠です。特に、切削油は摩擦を減少させ、冷却効果をもたらし、切削速度の向上と工具寿命の延長を実現することが可能です。これにより、精密な加工が求められるS45C材において、より一層の効率化とコスト削減が期待できます。このような技術の進展は、業界全体の競争力強化に貢献することでしょう。
4. 他の金属材料との比較
4-1. S45CとS50Cの特性と用途の違い
S45C材のタップ加工やフライス加工は、機械部品製造において欠かせない工程です。最新の方法を取り入れることで、加工効率が格段に向上します。具体的には、高精度なCNC加工機を使用し、切削条件を最適化することが効率化の鍵です。例えば、適切な速度での切削を選択することで、S45C材の硬度と強度を維持しつつ、滑らかな仕上がりを実現できます。更に、冷却液を適正に使用することで、加熱による材料の変質を防ぎ、精度の高い加工が可能になります。結果として、タップ加工やフライス加工においても、このような最新の技術を活用することで、生産性の向上と製品品質の維持が実現可能です。
4-2. SUS303フリープレートの特徴とS45Cとの比較
S45C材を効率よくタップ加工・フライス加工する新しい方法は、2023年版として注目されています。S45C材は一般的な機械構造用炭素鋼として広く使用されており、その加工性が良いため、産業の現場で好まれています。しかし、従来の加工方法では、時間がかかる上に工具の摩耗も激しく、コストと効率の面で課題がありました。最新の方法では、切削条件の最適化や高性能加工液の使用により、これらの問題を大幅に解消。例えば、特殊コーティングが施されたタップでは、長寿命を実現し加工の精度も向上しています。加えて、高速で精密なフライス加工が可能なマシニングセンタの導入も、効率化に寄与しています。このように、S45C材の加工技術は日々進化しており、より良い製品製造に不可欠なプロセスとなっています。この新しい加工方法を取り入れることで、品質と生産性の向上が期待できるのです。
5. 加工の補助材料
5-1. 金属加工油の種類と特徴
S45C材のタップ加工・フライス加工に関して、2023年においても効率的な方法が注目されています。S45C材は、機械構造用炭素鋼として優れた加工性とバランスの取れた機械的性質を持ち、多くの工業製品に使用されています。最新の加工技術では、摩耗しにくい特殊なコーティングが施された工具の使用や、最適な切削速度の選定などにより、加工精度を高めつつ、工具の寿命を延ばすことが可能です。具体的な例として、小径のタップ加工では、予備穴の精度を高めることで、ねじ切りがスムーズになり、破断のリスクを減少させています。また、フライス加工においては、多刃エンドミルの利用により、高速での加工が実現し、生産性の向上に貢献しています。これらの方法を取り入れることにより、S45C材の加工効率は飛躍的に向上し、製造業のコスト削減と品質向上が期待されます。
5-2. 切削油の選定とその重要性
タップ加工やフライス加工は精密な作業であり、S45C材料の加工を行う上で切削油の選定は不可欠です。正しい切削油を使用することで、工具の摩耗を抑え、製品の品質を保障することができます。特にS45C材は硬度が高く加工が困難なため、切削油が加工効率と品質の向上に大きく寄与します。最新の切削油は、これまで以上に耐熱性や潤滑性が高く設計されており、長時間の作業においても安定した性能を維持します。例えば、特定の添加剤を含む切削油は、S45C材の長時間のタップ加工においても、摩擦熱を効果的に低減し、工具の寿命を延ばすことが報告されています。このように適切な切削油を選ぶことは、タップ加工・フライス加工における効率性と経済性を同時に高める鍵となります。
6. 切削加工に関する用語と知識
6-1. 機械加工で使われる基本用語
S45C材のタップ加工・フライス加工においては、最新の効率的な方法が求められています。この鋼材は機械構造用炭素鋼として広く利用され、耐久性と加工性のバランスが良いため、多くの製造現場で重宝されています。特に、S45C材は硬度が高く、精密な加工が可能であることから、タップ加工やフライス加工に適しています。そのため、切削工具の材質選定や加工条件の最適化が非常に重要となります。例として、最新のコーティング技術が施された切削工具を使用することで、耐摩耗性が向上し、長寿命化が期待できるだけでなく、切削速度を高めることができ、生産性の向上にも寄与します。このような技術革新は、加工精度の向上と製造コストの削減に結びつき、結論としてS45C材の加工効率を大幅に向上させることができます。
6-2. 旋盤加工の基礎とS45C加工への応用
旋盤加工は様々な材料に対応可能な汎用性を持ちつつ、S45C材においては特に精密で強靭な部品製造が求められます。2023年におけるS45C材のタップ加工やフライス加工は、更なる効率性と精度向上が図られています。例えば、新しいコーティング技術が開発され、工具の耐摩耗性が向上し、長寿命化が実現しています。また、CNC機械の精度が向上し、複雑な形状でも高精度での加工が可能となりました。これらの進化によって、小ロットでの多品種生産が現実のものとなり、柔軟かつ迅速な生産体制が可能となっています。結果として、S45C材の加工における生産性と品質が大幅に向上し、様々な産業でのニーズに応えられるようになりました。これらの技術革新により、今後もS45C材の加工技術は進化し続けるでしょう。
まとめ
S45C材のタップ加工およびフライス加工には、最新の切削工具と加工方法を使用することが重要です。適切な切削速度や切削量を設定することで、高い加工効率と品質を実現できます。特に、ハイスピードスチールや硬質合金を使用した切削工具を選定するとよいでしょう。最新の加工技術を取り入れることで、作業効率が向上し、コスト削減にもつながります。