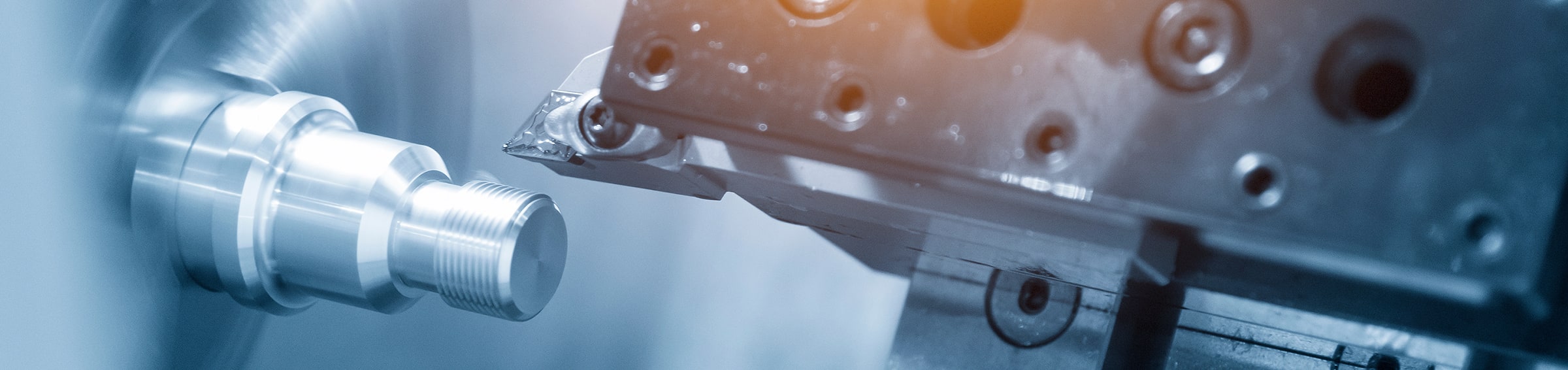
加工技術 column
【試作必見】SS材でフライス加工する際のポイントとは?
フライス加工を行う際、SS材は特に注意が必要です。SS材でのフライス加工は、試作品の製造において欠かせないポイントとなります。試作品を作成する際に、SS材を使用することが多いため、その加工方法について知っておくことは重要です。この記事では、SS材でのフライス加工のポイントについて紹介します。試作品を作る際に知っておくべきことを解説し、SS材でのフライス加工がどのように行われるか、その手順や注意点について詳しく説明します。
1. SS フライス加工 試作の基本
SS材でのフライス加工は試作段階で重要なポイントを押さえるべきです。SS材は耐食性や耐熱性に優れ、精密な部品作りに不可欠ですが、加工が難しい特性も持っています。まず、適切な切削工具の選択が必須です。SS材には硬質のカーバイド製工具が適しており、切削速度や送り速度の調整も重要です。例えば、通常の鋼材に対する加工速度よりも遅く設定することで、工具の摩耗を抑え、精度の高い加工が可能になります。さらに、冷却液の使用は切削温度を抑え、切りくずの排出を助けるために効果的です。これらのポイントを理解し、適用することで、試作段階での問題を未然に防ぎ、最終的な製品品質を高めることができます。
2. SS材とS45Cの特性比較
SS材でのフライス加工は、試作段階でのポイントを押さえることが成功への鍵となります。SS材は耐蝕性に優れたステンレスの一種であり、硬度が高く加工が難しい特性を持っています。このため、適切な工具選びと加工条件の設定が非常に重要です。例えば、切削速度や送り速度、そして冷却剤の使用は、加工中の熱影響を最小限に抑え、精度の高い加工を実現するための必須条件です。さらに、工具の摩耗を防ぐためには、適切な切削油の選択も重要であり、長期にわたる安定した加工を可能にします。以上のように、SS材でのフライス加工においては、材質の理解と細かな加工条件の調整が、高品質な試作品を作り出すために必須です。これらのポイントを押さえることで、効率的かつ成功率の高い試作加工が期待できるでしょう。
3. 試作品製作のためのフライス加工テクニック
SS材でのフライス加工は試作品製作において重要なポイントがいくつかあります。フライス加工は精密な形状を作り出すことができ、試作品においてもその再現性が求められるため、特に注意が必要です。まず、SS材はステンレスの一種であり、硬度が高く加工が難しい特性を持っています。このため、適切な工具の選択や冷却液の使用は、加工中の材料の温度上昇を抑え、工具の摩耗を防ぐために欠かせません。また、フライス加工時には、切削速度や送り速度の最適化が重要で、これによって精度良く、かつ効率的な加工が可能になります。例えば、切削速度が遅すぎると加工に時間がかかりすぎますし、速すぎると工具の摩耗や材料の損傷の原因になりかねません。最適な条件で加工することで、試作品の品質を保ちつつ、コストを抑えることができるのです。したがって、SS材でフライス加工を行う際には、これらのポイントを押さえ、試作品の成功に繋げることが大切です。
4. マシニング加工とSS フライス加工の事例紹介
SS材でのフライス加工は試作フェーズにおいて重要なポイントがいくつかあります。まず、SS材は耐食性や高強度などの特性を持つため、フライス加工には適切な機械設定が必要です。例えば、SS材の硬さに適したカッターやスピードの選択が、加工精度に大きく影響を与えます。また、適切なクーラントの使用は、加工時の摩耗や変色のリスクを減らし、仕上がりの品質を高めるためにも不可欠です。SS材の熱伝導率は低いため、加工中の熱管理も重要なポイントです。具体的な事例としては、航空機や自動車の部品製造においてSS材を使用した高精度のフライス加工が求められる場合があります。これらのポイントを抑えることで、SS材におけるフライス加工の試作段階はスムーズに進行し、製品の品質向上に繋がるでしょう。
5. SS400をはじめとする材料の特徴
SS材でのフライス加工は試作段階でのポイント把握が非常に重要です。SS材は強度が高く加工がしやすい一方で、適切な工具選定や加工条件の設定を怠ると工具の摩耗や加工精度の低下を招きます。例えば、SS400のような一般的な材料では、切削速度や送り速度、切り込み深さを適切に設定することで、効率良く加工することが可能です。また、試作では小ロットでの加工も多いため、効率的な工程設計が求められます。具体的な例としては、工具の刃先形状を最適化したり、冷却剤の使用を適切に行うことで、材料の特性を活かした加工が実現できます。結論として、SS材でのフライス加工においては、材料の特性を理解し、適切な加工条件を設定することが、高精度の試作品を作り出すカギであると言えます。
6. 加工時の安全性と注意点
SS材をフライス加工する際には、特有の加工難易度を理解することが肝心です。SS材は硬度が高く、耐熱性に優れているため、一般的な金属材料に比べて工具への負担が大きくなります。これを考慮し、フライス工具の選定を慎重に行ったり、切削条件を適切に設定することが必要です。例えば、工具の材質には耐摩耗性に優れたものを選び、送り速度や回転数はSS材の特性に合わせて調整します。また、冷却剤の使用は加工時の摩擦熱を抑制し、切削精度の向上や工具寿命の延長に寄与します。結論として、SS材のフライス加工を成功させるためには、材料の特性に応じた工具選定と切削条件の最適化が不可欠であり、これにより試作段階での効率と品質の両立が可能となります。
7. 機械加工後の材料試験と品質管理
フライス加工は精密な工程であり、特にSS材を使用する際には注意を要します。その理由は、SS材が持つ優れた耐食性や強度により、加工時の負荷が大きくなりがちだからです。実際に、正確な寸法を出すためには切削条件を丁寧に管理する必要があります。例えば、切削速度や送り速度、刃の種類を適切に選定することが重要です。また、試作段階では小ロットで加工を行い、寸法の精度や表面の仕上がりを確認することで、量産前の問題点を洗い出すことができます。結果として、試作を丁寧に行うことで、SS材のフライス加工における品質を確保し、最終製品の信頼性を高めることができるのです。
まとめ
SS材を使用したフライス加工においては、適切な切削条件を選定することが重要です。適切な切削速度や送り速度を設定し、切削時の過熱を防ぐために冷却液を使用することがポイントです。また、SS材は切削しやすい材料ではありませんが、適切な刃物を選択し、適切な刃先形状を用いることで効率的な加工が可能となります。試作品の製作にあたっては、これらのポイントを押さえることで高品質な加工が実現できます。
小ロットでも大丈夫!SSフライス加工で試作品を作る方法
スモールスケールの製品開発を行う際、SSフライス加工は非常に有用な方法です。この記事では、SSフライス加工とは何か、そして小ロットでの試作品作成に適した理由について詳しく解説します。SSフライス加工の基本から始め、試作品を作るための具体的な手順まで、一連のプロセスを詳細に説明します。SSフライス加工を利用して、小ロットでも高品質な試作品を効率的に作成するためのヒントを得られるでしょう。
1. 小ロットSSフライス加工試作の基本
小ロットでも試作品の制作は可能です。SSフライス加工は少量の材料で高精度な試作品を作るのに適しています。この加工方法の特長は、複雑な形状や繊細なデザインの実現が可能な点にあります。例えば、新しい機械部品の試作や特殊な工具の開発に利用されることが多く、小ロットながらもその性能やデザインを実際に確かめることができます。SSフライス加工を利用することで、コストを抑えつつも実物に近い試作品を手にすることが可能となり、開発のスピードアップにも繋がります。このため、製品開発初期段階において、多くの企業がSSフライス加工を採用しています。小規模でも高品質な試作品を手軽に作り出すことは、技術革新を推進する上で非常に重要なポイントです。
2. SSとS45Cの材質比較と特性理解
SSフライス加工は少量生産でも効率的に試作品を作成する方法として注目されています。従来の大量生産に比べて、SSフライス加工はその柔軟性で個別のニーズに応えることが可能です。例えば、新しい製品開発の初期段階では、デザインや機能の試行錯誤が必要ですが、SSフライス加工ならば必要な数だけを短期間で製作でき、大量生産前のリスクを低減することができます。具体的には、小ロットでもオーダーメイドでの生産が可能となり、細かな設計変更にも柔軟に対応できるため、試作品の品質向上にも寄与します。このような特性により、SSフライス加工を利用した試作品作りは、コストと時間の節約に繋がり、製品開発の効率化を実現します。最終的には、この加工方法によって、より競争力のある製品を市場に送り出すことが可能になります。
3. SSフライス加工試作の製作プロセス
小ロットでも試作品を作る際には、SSフライス加工が適しています。この加工方法は少ない数量からでも高精度な加工が可能で、コストも抑えられます。例えば、新しい製品の開発段階で、多くを生産する前にデザインや機能の確認が求められる場合、SSフライス加工は理想的です。また、特定の部品に小さな変更を加えたい時や、カスタマイズ性が高い製品を少量ずつ作りたい場合にも有効です。最終的に、小ロットでの試作が成功すれば、大量生産へとスムーズに移行できます。小ロット試作のニーズに応えるSSフライス加工は、柔軟性と経済性を兼ね備えた製作プロセスとして、ますます重要性を増しています。
4. SSフライス加工試作に必要な機械設備
SSフライス加工は、小ロットでも柔軟に試作品を作る方法として注目されています。具体的には、この加工法により、複雑な形状や精密な部品の製造が可能となり、短期間での製品開発に貢献しています。まず、SSフライス加工ではコンピュータ制御により、非常に正確な切削が行えるため、多様なデザインの製品を高い精度で仕上げることができます。たとえば、特殊な歯車やプロトタイプのカスタムパーツなど、従来の大量生産では困難だったアイテムも、この技術を用いれば少量から作成することが可能です。さらに、小ロット生産に適しているため、大量生産に比べて初期コストを抑えられるという経済的な利点もあります。最終的に、SSフライス加工は試作品の製造において、柔軟性とコスト効率の両面で優れた選択肢となり得るのです。
5. SSフライス加工の加工実績と事例紹介
SSフライス加工は試作品作りにおいて小ロット生産も問題なく対応可能な手法です。この加工方法の利点は、オーダーメイド生産が行えるため、デザインの変更や改良が頻繁にある試作段階でも柔軟に対応できる点です。例えば、新しい製品の開発において、初期コンセプトから何度も改良を重ねる必要がある場合、SSフライス加工ならば小規模な変更でも迅速に反映させることができます。また、必要な部品が少ない場合にも、余分な材料やコストをかけずに製造することが可能であり、コストパフォーマンスにも優れています。このように、SSフライス加工は少量でも高品質な試作品を迅速かつ効率的に生産するための適切な解決策となるでしょう。
6. フライス加工と旋盤加工の適切な使用用途
小ロットの試作品もSSフライス加工で簡単に作成できます。SSフライス加工は、少量の試作品を作る際に特に適しており、柔軟性が高いため、多様なデザインに対応可能です。たとえば、新しい機械部品のデザインを考案した場合、まずはSSフライス加工を用いて試作品を作成することで、デザインの検証や機能の確認が可能となります。この加工方法は、緻密な作業が要求される小規模な製品にも対応できるため、ミスを最小限に抑えつつ、効率良く試作品を制作できるのです。結局のところ、SSフライス加工は、コストと時間の節約につながり、製品開発プロセスを加速することに寄与します。小ロットでの試作が必要な際には、SSフライス加工が理想的な解決策となるでしょう。
7. 引張試験の方法とSSフライス加工試作への応用
小ロットの試作品製造において、SSフライス加工は非常に有効な手法です。SSフライス加工により、必要な部品を少量からでも迅速に製造することが可能で、開発の初期段階でのコスト削減に貢献します。たとえば、新しい製品のプロトタイプを作る際やカスタマイズされた部品が必要な際に、SSフライス加工は理想的です。極めて短いリードタイムで細部にわたる精度の高い部品が必要な場合でも、SSフライス加工は対応可能です。具体的には、医療機器のプロトタイピングや自動車部品のカスタマイズにおいて、この技術が活用されています。結論として、SSフライス加工は小ロットでの試作品製造において、柔軟性、速度、精度を備えた、非常に魅力的な選択肢であることがわかります。
まとめ
小ロットの試作品を作る際には、SSフライス加工が有効です。この方法では、コストを抑えながらも高精度な加工が可能です。また、CADデータがあれば容易に製作ができるため、迅速な試作品の製作が期待できます。SSフライス加工は小ロット生産に最適な方法と言えます。
【技術者向け】SS材を使用したフライス加工試作の進め方
技術者の皆さん、SS材を使用したフライス加工試作の進め方について興味はありませんか?この記事では、SS材を使用したフライス加工試作の具体的な進め方やポイントについて解説します。フライス加工におけるSS材の利用法や試作における注意点など、実践的な情報を幅広く提供しています。技術者としてのスキルを向上させたい方や新しいチャレンジを考えている方にとって、参考になる内容が満載です。
1. SS フライス加工試作の基本
SS材を用いたフライス加工試作は、精密な部品製作に不可欠です。この工程の適切な進め方が、製品の品質を左右するため、技術者は注意深く計画を立てる必要があります。まず、使用するSS材の種類を選定し、加工に適した工具を選ぶことが重要です。例えば、耐食性や強度が特に求められる場合、316Lなどの特定のSS材を選びます。次に加工条件、つまり切削速度や送り速度、切削液の使用などを決定します。実際の試作においては、小ロットから始めて段階的に条件を調整し、目標とする寸法精度や表面粗さを達成します。試作を通じてデータを蓄積し、本番加工前の最適な条件を見極めることが、効率的かつ高品質な製品生産への道です。結局、入念な準備と連続したテストが、SS材を使用したフライス加工で成功する鍵となります。
2. SS400材料の特性とフライス加工時の注意点
SS400は一般構造用圧延鋼材として広く利用されていますが、フライス加工を行う際にはいくつかの注意点があります。まず、SS400はその成分構造上、粘りが強いため加工時に切りくずが巻き付くことが多く、これを防ぐためには適切な切削条件の選定が重要です。具体例としては、高速度鋼や超硬合金の刃物を使用し、切削速度を適切に設定すること、冷却液を適量使用することが挙げられます。次に、SS400の熱処理状態は加工性に大きく影響を及ぼすため、材料の供給状態を確認し、必要に応じて予備加工を行うことも重要です。加工精度を高めるためには、機械の状態も常に最適なものにする必要があります。これらの注意点をふまえ、適切なフライス加工方法を選定することで、試作時の加工効率を高め、質の高い製品を製作することが可能となります。
3. 6面フライス加工と4面フライス加工の違い
6面フライス加工と4面フライス加工では、加工される面の数に違いがあります。6面フライス加工は、素材の6つの面全てに加工を施す方法で、箱形の部品製作などに適しています。一方4面フライス加工は、素材の4つの面だけを加工し、上下の面は加工しません。これはフレームの加工など、特定の面の精度が要求される場合に適しています。例えば、ある機械のフレームを作る際、接続部分に精度が求められるため、それらの面を特に4面フライス加工で仕上げることがあります。何面フライス加工を選ぶかは、製品の用途や必要な精度によって決まりますが、加工時間やコストも重要な判断基準になります。結論として、加工する面の数が多いほど、より高い精度や複雑な形状が要求される場合に適しており、少ない面数ではコストと時間を節約できる場合が多いです。
4. フライス加工の種類と選択基準
SS材を使用したフライス加工の試作は、その優れた強度と耐久性から多くの技術者に注目されています。結論から言えば、適切な工具とパラメータの選定が重要です。具体的には、SS材の硬質な特性を考慮し、摩擦熱に強いコーティングを施した刃物や、加工速度、送り速度などのパラメータが重要となります。例を挙げると、柔軟性が求められる試作の段階では、小ロットにも対応可能なCNCフライスを用い、材料の種類に応じた専用の切削油を使用することが一つの方法です。また、加工途中での冷却液の適切な配合と管理も、品質保持に不可欠です。再度強調しますが、SS材を用いたフライス加工においては、材料の特性を理解し、それに適した加工方法の選択が試作成功の鍵を握ります。
5. SS材の面仕上げにおける曇りの原因と対策
SS材を使用したフライス加工における曇りの発生は、加工精度に影響を及ぼす重要な問題です。この曇りは、工具の摩耗やカッティングオイルの不適切な使用といった、様々な要因によって生じます。例えば、切削工具のエッジが摩耗していると、材料表面が不均一になり曇りが発生することがあります。また、適切でない切削油を使用すると冷却と潤滑が不十分となり、同様に曇りを引き起こします。これらの問題を解決するためには、定期的な工具の点検と交換、適切なカッティングオイルの選定と管理が必要です。適切な工具とオイルを使いこなすことで、フライス加工の品質は大きく向上し、SS材の面仕上げにおける曇りを効果的に防ぐことができるのです。
6. NCフライス加工とSS400プレートの加工技術
SS材を利用したフライス加工の試作には、適切な進め方が求められます。まず、材料の特性を理解し、加工に適した工具や条件を選定することが重要です。SS材は耐食性に優れた材質でありながら加工がしにくいという特徴を持っています。このため、切削速度や送り速度、切り込み量といった加工条件の最適化が欠かせません。特に、試作段階では、小ロットかつ高精度が要求されることが多いですから、精度を維持しつつ効率も考慮した条件設定が求められます。具体的な例としては、切削油の選定ではSS材の高い熱伝導性に対応したものを選び、工具の摩耗を抑えることができます。また、工具の選定では硬質コーティングされたエンドミルなどが有効です。こうした選定を通じて、フライス加工のトラブルを避け、スムーズな試作過程を実現することが可能になります。最後に、試作を重ねて得たデータをもとに加工条件を見直すことで、より良い製品を効率良く生産できる体制を整えることができるのです。
7. 半導体部品におけるSS材フライス加工の応用
半導体部品の製造においてSS材を用いたフライス加工試作は、精密な部品を効率的に生産する上で欠かせないプロセスとなっています。SS材は耐食性や強度が高いため、半導体部品に適しているのですが、加工には特別な配慮が必要です。具体的な進め方としては、まず加工条件の検討から始めます。適切な切削速度や送り速度を見極めることが品質を左右します。次に、適切な工具選定が重要です。SS材の硬さに対応するカッターやエンドミルの選択が、加工精度に大きく影響します。さらに、加工する際は冷却液の使用が効率的なチップの除去と品質の維持につながります。加工後は、精密測定機器を用いて部品の寸法精度を確認し、必要に応じて微調整を行います。これらの一連のプロセスが、半導体部品製造の精度と効率を大きく向上させるのです。結論として、SS材を使用したフライス加工試作は適切な方法と注意深いプロセス管理によって、半導体部品の品質向上に不可欠であり、その重要性は今後もますます高まっていくでしょう。
まとめ
SS材を使用したフライス加工試作の進め方について、材料特性や加工方法、工程管理などを学ぶことが重要です。SS材は耐熱性や耐食性に優れており、それに合わせた適切な切削条件を設定することがポイントです。また、試作品の寸法精度や表面仕上げにも注意が必要です。技術者はこれらの点を把握し、緻密な計画と適切な工程管理を行うことで効率的なフライス加工試作を進めることができます。
SS材フライス加工の基礎知識と試作のためのコツ【入門編】
もしSS材でのフライス加工に興味があるけれども、何から始めればいいのかわからないと感じているなら、この記事はきっと役立つはずです。ここではSS材フライス加工の基礎知識や、試作の際に役立つコツについて解説します。フライス加工の世界に入り込んでみたいけれど、手探り状態で不安を感じている方にとって、この入門編は必読です。
1. SS フライス加工 試作におけるSS材の選定基準
SSフライス加工を行う際には、適切なSS材の選定が重要です。なぜなら、材料の特性が加工精度や仕上がりに大きく影響するからです。例えば、試作品の作成には、加工しやすく、かつコストパフォーマンスに優れたSS材を選ぶことが一般的です。具体的にはSUS304やSUS316といったオーステナイト系ステンレス鋼が選ばれることが多いです。これらは耐食性と加工性のバランスが取れているため、初めてフライス加工を行う方にも扱いやすい材質です。試作段階では、これらのSS材を活用し、加工条件を最適化することで、コストを抑えつつ高品質な製品を創出することができます。最終的にはSS材の選定によって、製品の品質だけでなく、製造コストにも影響するため、慎重な選定が求められます。
2. SS400材の特性とフライス加工時のアプローチ
SS400材は機械構造用の普通鋼であり、フライス加工においてその特性を理解することが重要です。加工性が良く、比較的安価であるため、試作に適しています。しかし、その硬度や強度には限界があるため、加工パラメータの選定には細心の注意が必要です。例えば、切削速度を適切に選ぶことで、工具の摩耗を防ぎつつ、加工精度を保つことができます。また、SS400材は溶接性も良好なので、加工後の組み立て作業が容易になります。フライス加工の際には、SS400材の物性値を参考にしながら、切削条件を最適化し、高い生産性と精度が求められる試作を成功させることが肝心です。最終的に、これらのポイントを抑えることで、効率的なフライス加工が実現されるのです。
3. 試作品製作のプロセスとSS フライス加工 試作のポイント
SS材フライス加工は精密かつ効率的な金属加工技術として重宝されています。この技術により、製作される試作品は高い精度を要求される製品開発において、不可欠な役割を果たします。加工の正確さは製品の品質に直結するため、SS材のフライス加工では詳細な設計図の作成から始めることが肝要です。特に、試作段階では設計変更が頻繁に行われるため、柔軟性を持って迅速に対応できる工夫も必要です。一般的な例として、加工前にデジタルシミュレーションを利用することにより、加工パスの最適化、時間の短縮、材料の節約が可能になります。また、切削条件の選定は材料の特性に適したものを選ぶことが重要で、経験豊富な技術者による知識が求められます。このような工程を経て製作される試作品は、最終製品の品質向上に直結し、開発の効率化を実現します。
4. マシニングとフライス加工の違いとそれぞれの利点
フライス加工は多様な形状を加工できるため、SS材を使用した試作において不可欠です。この加工法が選ばれる主な理由は、精度の高さと加工の柔軟性にあります。例えば、複雑な曲面や溝を必要とする部品も、フライス加工を使用すれば容易に作成可能です。加えて、SS材を使う場合は、刃の選択や冷却剤の使用など、材質の特性に合わせた加工技術が求められるため、試作段階での注意が必要になります。適切な工具と技術の選択により、高品質な試作品を効率良く生産することができるのです。最終的に、SS材フライス加工は緻密な作業を要しますが、その柔軟性と高い精度により、多くの試作プロジェクトで頼りにされているのです。
5. SS フライス加工 試作における施工事例の分析
SS材フライス加工は精度が要求される作業であり、試作には特に注意が必要です。始めに、フライス加工の基本として材料選びが大切です。SS材は耐食性や強度など特有の特性を持つため、適切な材料を選ぶことが成功への第一歩となります。加工では、正確な工具の選定や切削条件の調整が重要です。例えば、SS材に合わせた切削速度や送り速度の設定は、加工精度に大きく影響します。また、試作段階では小ロットでの生産が一般的であり、コスト管理にも留意する必要があります。加工事例を分析することで、どの工程で問題が生じやすいかやどのような対策が有効かが見えてきます。最終的に、これらの情報をフィードバックして初めて、次の試作に活かせるのです。フライス加工の技術を磨き、試作の精度を高めることで、より良い製品製造へと繋がるでしょう。
6. 材料試験片を用いたSS フライス加工の品質管理
SS材フライス加工は、精密部品の製造において重要なプロセスです。その品質を確保するためには、適切な加工技術と試作が不可欠です。なぜなら、試作を行うことで、材料の特性や加工条件を理解し、最終製品の品質を向上させるからです。例えば、SS材を用いた加工試作では、切削速度や送り速度、切削液の種類などが品質に大きな影響を及ぼします。これらのパラメータを適切に調整することで、精度の高い加工が可能になるため、事前の試作による検証は非常に重要です。試作を繰り返すことで、より良い加工方法が見つかり、コスト削減や生産性の向上にも寄与します。したがって、SS材フライス加工の品質を管理する上で、材料試験片を用いた試作は欠かせないステップであると結論付けることができます。
7. 機械加工技術の進歩とSS フライス加工 試作の未来
SS材フライス加工は高精度な試作に不可欠であると結論付けることができます。その理由としては、SS材料の優れた機械的特性が挙げられます。具体的には、耐久性と加工性が高く、精密な部品製造に適しているため、試作段階での高い信頼性を求められる製品に適しているのです。例えば、航空宇宙産業における部品や自動車産業におけるプロトタイピングにおいて、SS材のフライス加工は重要な役割を果たしています。試作を成功に導くコツとしては、適切な切削条件の選定や冷却剤の使用が挙げられます。これにより、材料特有の問題を避けつつ、所望の形状と精度を達成することが可能です。結論として、SS材フライス加工の知識と適切な加工技術は、高品質な試作品を製造する上で欠かせない要素と言えます。
まとめ
SS材のフライス加工では、適切な切削条件や工具選定が重要です。適切な切削速度や切削深さを設定することで、高品質な加工を実現できます。また、試作品を作成する際には、素材特性や設計図をしっかりと把握し、適切な加工工程を選択することが重要です。正確な計測と検査を行いながら試作を進めることで、品質の高い製品を生産することが可能です。
【2023年最新】SKDとSK、フライス加工における徹底比較と適用事例
フライス加工の世界では、様々な材料に対応するために、SKDとSKの比較が重要な要素となります。これらの略号について理解し、適切な材料と使用方法を知ることは、効率的な加工プロセスを確立する上で不可欠です。本記事では2023年最新の情報を元に、SKDとSKの徹底比較とそれに伴う適用事例について解説します。フライス加工に携わる方々にとって、貴重な知識となることでしょう。
1. SKD SK 比較 フライス加工の基礎
フライス加工において、SKDとSKの刃物鋼はそれぞれ異なる特性を持ち、用途に応じて適切な選択が必要です。本文では、SKDとSKの違いと、それぞれの具体的な使用例について述べます。SKDは耐摩耗性に優れ、高硬度の材料加工に適しています。そのため、型や金型のような耐久性が求められる分野での使用が一般的です。一方、SKは靱性に富み、断続的な切削や衝撃を受けやすい加工に適しており、自動車の部品製造などに利用されます。例えば、SKDを使用したフライス刃は精密な型の仕上げ加工に有効であり、SKを使用したフライス刃は大量生産される部品の加工に最適です。これらの特性を踏まえた上で選択することで、効率的で品質の高い加工が可能となります。結論として、SKDとSKはそれぞれ特定の加工条件において最適な素材であり、使い分けが加工の品質を左右する重要な要素となります。
2. SKD11とSKD61の特性と違い
SKD11とSKD61はどちらもフライス加工において頻繁に使用される工具鋼ですが、用途に応じて適切な選択が求められます。SKD11は炭素とクロムを多く含む材質で、耐摩耗性に優れています。そのため、精密な金型が必要な加工に利用されることが多いです。一方、SKD61はより高温での強度が求められる場合に適しており、アルミニウム合金の加工などに使われます。例えば、自動車産業では、精度を要する部品をSKD11で加工し、耐熱性が必要なエンジン部品の加工にはSKD61が選ばれることがあります。このように、SKD11とSKD61はそれぞれの特徴を活かした分野で使用され、フライス加工の精度と効率を高めています。最適な材料を選択することで、製品の品質向上に繋がります。
3. SKD11の切削加工の要点
SKD11とSK材料、それぞれの特性を理解し、フライス加工において適切な選択を行うことが重要です。結論から言うと、SKDは耐摩耗性に優れ、困難な加工に適していますが、SKは加工性が良好で一般的な用途に適用しやすいという特徴があります。例えば、SKDは金型の製作などによく使用され、精密な耐久性が求められる部品加工において、その高硬度が生きてきます。一方、SK材料は構造用鋼材や一般機械部品の加工において、その加工のしやすさから選ばれることが多いです。同じフライス加工でも、加工する材料の特性を考慮することが、製品の品質を決める上で非常に大切であり、結果的に最適な材料選びがコスト削減にも繋がるのです。
4. SKS3からSKD11への材料選定とコスト削減
フライス加工におけるSKDとSKの材料は、それぞれの特徴を理解し適切に選定することが重要です。一般にSKDは耐摩耗性に優れ、高い硬度を保ちながら加工精度も維持できるため、難削材の加工に適しています。例えば、金型の製造においてSKD11がよく用いられるのは、優れた耐摩耗性と精度を長時間保つことができるからです。一方、SK材は加工性が良く、比較的柔らかい材料でコストも抑えやすい特性を持っています。これは、量産品の加工や一般的な機械部品に適していることを意味します。しかし、最終的には、加工する製品の用途や必要とされる特性、コストパフォーマンスを総合的に考慮し、SKDとSKのどちらの材料を選択するか決定されるべきです。まとめると、目的に応じた材質選定は製品の品質を保ちつつコスト削減につながる重要なポイントであると言えます。
5. 高硬度鋼切削加工のための技術ポイント
フライス加工におけるSKDとSK材料の適用性は、加工精度やコスト面で明確な違いを示します。SKDは硬度が高く耐摩耗性に優れており、金型などの耐久性が求められる精密部品加工に適しています。一方、SKは柔らかく加工しやすい特徴があり、一般的な機械部品や構造部材の加工に用いられます。たとえば、自動車のエンジン部品やギアなど、繰り返しの負荷がかかる部品はSKDを用いることで、長期にわたる信頼性を確保できます。しかし、コストを重視し大量生産を行う際には、SKが選ばれるケースが多いです。最終的に、用途に合わせた材料選定が、加工の効率と製品の品質を決定づけることになります。このようにSKDとSKを比較することで、フライス加工における適材適所の理解が深まり、より効率的な生産が実現可能です。
6. SKD SK 比較: 旋盤加工とフライス加工の相違点
2023年におけるSKDとSKのフライス加工に関する比較を通じて、両者の特性と適用事例を検討します。SKDは耐摩耗性に富んだ合金工具鋼であり、一方のSKは炭素工具鋼です。SKDはその硬度と耐熱性から、高負荷かつ高温条件下での加工に適しているため、自動車や航空機の部品製造に多く用いられます。SKは硬度はそれほど高くないものの加工容易性が高いため、一般的な金型や工具製作に適しています。例として、SKD製のドリルは堅牢な金属板を穿孔する際に、SK製のノミは木材や軟金属の彫刻に適しています。最終的には、使用目的に応じて適切な材質の選択が重要であり、各材質の持ち味を生かした加工が求められます。
まとめ
SKDとSKはどちらもフライス加工に使用される工具鋼ですが、それぞれ特徴や適用事例が異なります。SKDは熱処理性に優れ、高速鋼や超硬合金よりも高温での硬度保持が可能です。一方、SKは耐摩耗性に優れており、研削加工や切削加工に適しています。フライス加工においては、加工材料や加工条件に応じて適切な工具鋼を選定することが重要です。
S45Cのフライス加工!表面粗さを改善する方法とは?
フライス加工でS45Cの表面粗さを改善する方法について知りたいですか?S45Cは一般的な鋼材であり、その表面仕上げは加工品の品質に直結します。本記事では、S45Cのフライス加工において表面粗さを改善する方法について詳しく解説します。S45Cの特性やフライス加工のポイントについて知りたい方は、ぜひ読んでみてください。
1. S45C フライス加工とは?
S45Cのフライス加工において表面粗さを改善することは、加工品質を高める上で重要です。結論から言うと、正確な切削条件の選定、適切な工具の選択、冷却剤の利用が表面粗さを改善する鍵となります。例えば、切削速度や送り速度、切り込み深さを適切に設定し、S45C特有の硬さに適合した切削工具を使用することが必要です。また、冷却剤を適切に使用することで、切削熱による影響を抑え、滑らかな表面を得ることができます。実際の加工現場では、粗削りと仕上げ削りを区別し、それぞれに最適な条件を適用することが一般的です。最終的に、これらの対策を総合することによって、S45Cのフライス加工における表面粗さを大幅に改善することが可能となります。
2. S45C フライス加工における表面粗さの基準
S45Cのフライス加工における表面粗さを改善することは、高品質な製品を製造する上で欠かせない要素です。この改善には、適切な切削条件の選定が重要となります。たとえば、使用する工具の選定、刃の数、回転速度、送り速度など、加工条件を見直すことで表面粗さを向上させることが可能です。具体的には、新しく鋭い刃を使用することで切削抵抗を減らし、より滑らかな表面を得ることができます。また、適切な冷却剤の使用は、工具と加工物の温度上昇を抑え、表面粗さを改善する効果があります。これらの方法を試すことで、S45Cのフライス加工における表面粗さを効果的に改善し、品質の高い製品を製造することが期待できます。最終的に、こうした工夫により、製品の信頼性を高め、顧客満足度を向上させることに繋がります。
3. S45C フライス加工で表面粗さを改善する技術
S45Cのフライス加工において表面粗さを改善するためには、いくつかの重要な方法が存在します。まず、適切な切削条件の選定が重要であることを理解する必要があります。具体的には、切削速度、送り速度、およびカッターの選択が表面粗さに大きく影響を及ぼします。例えば、切削速度が速すぎると表面に微細な傷がつきやすくなりますし、遅すぎると加工時間が長くなり非効率です。また、フライスカッターの刃数が多いほど切削は滑らかになり、表面粗さは向上します。さらに、工具の摩耗も表面粗さに影響するため、定期的な工具交換やメンテナンスが必要です。そして、加工機の振動を抑制することも重要で、適切な機械保守と運用が求められます。これらの要因を適切に管理することで、S45Cのフライス加工における表面粗さの改善が可能となるのです。
4. プラスチック板の精密加工と表面粗さ
S45Cのフライス加工を行う際、表面粗さを改善することは重要です。この理由は、フライス加工後の表面の滑らかさが製品の品質に直結するからです。具体的な改善方法としては、適切な切削油の使用、カッターの選定、切削スピードの最適化が挙げられます。切削油を使用することで、摩擦熱を減少させ、切削面の仕上がりを良くします。また、カッターは刃の数や形状によって異なりますが、材質に合ったものを選ぶことで、精密な加工が可能になります。さらに切削スピードを材質や形状に合わせて調整することで、理想的な表面粗さを得ることができます。結論として、これらの方法を適切に組み合わせることで、S45Cのフライス加工における表面粗さの改善が期待できるのです。
5. 表面粗さの測定方法
S45C材のフライス加工における表面粗さを改善する方法は、加工精度を高めることに他なりません。S45Cは一般的な機械構造用炭素鋼であり、その表面粗さは製品の品質に直結します。具体的には、切削工具の選択、切削条件の最適化、そして潤滑の適切な使用が重要です。例えば、刃物の新しさや切れ味を保つことは表面の滑らかさを改善させますし、スピンドルの回転数や送り速度などの切削条件を材質に応じて調整することにより、荒れた表面を未然に防ぐことができます。また、クーラントの使用は熱を適切に排出し、切削物の微細な欠けや溶着を防ぎます。最終的に、これらの工程を適切に管理することで、S45Cのフライス加工した表面の粗さを効果的に改善することが可能です。
6. 表面粗さパラメータとその活用
S45Cのフライス加工において、表面粗さを改善することは製品の品質向上に直結します。理由として、フライス加工の仕上げ面が機械部品としての機能や寿命を左右するからです。具体的な改善方法としては、適切な切削速度の選定、使用する刃物の材質や形状の最適化が挙げられます。例えば、切削抵抗を低減するためにコーティングされた刃物を用いたり、切削液の使用を工夫することで、焼き付きを防ぎながら表面の微細な凹凸を減らすことが可能です。最適な条件下でフライス加工を行うことで、S45Cの表面粗さは確実に改善され、結果として製品の品質が向上するのです。
まとめ
S45Cは一般構造用炭素鋼であり、機械構造部品に適しています。S45Cのフライス加工において表面粗さを改善するには、適切な切削条件や工具の選定が重要です。切削速度や切り込み深さ、刃先形状などを適切に選定することで、より綺麗な仕上がりの表面を得ることが可能です。
【プロが教える】S45CとSS、フライス加工での性能差と選定ポイント
フライス加工においてS45CとSSを比較する際、どのような性能差があり、どのような選定ポイントがあるのでしょうか?この記事では、プロが教えるS45CとSSの違い、性能、そして選定ポイントについて徹底的に解説します。もし、あなたがフライス加工に興味をお持ちであれば、この記事を読んで、S45CとSSの選定に役立つ情報を手に入れましょう。
1. S45CとSSの基本的理解
フライス加工において素材選びは非常に重要です。S45CとSSは代表的な材料であり、それぞれの性能差を理解することが重要です。S45Cは炭素鋼であり、強度があり加工性が高いため、一般的には耐久部品や機械部品の製造に広く使われています。一方、SS材はステンレス鋼を指し、耐食性や耐熱性に優れており、食品機械や化学プラントなどの特殊な環境での使用に適しています。例を挙げると、S45Cは自動車のエンジン部品や駆動系コンポーネントに、SSはキッチン用品や医療器具に選ばれます。適切な材料選びは、製品の性能や耐用年数を大きく左右するため、加工前にはその特性をしっかりと把握し選定することが肝心です。
2. フライス加工概要
S45CとSS材は、フライス加工でよく使用される材料ですが、性能差により適用が異なります。S45Cは炭素鋼であり、強度と硬度が必要な部品に使用されるのが一般的です。一方、SS材はステンレス鋼で、防錆性が求められる場所での使用が適しています。たとえば、S45Cはギアやフレームの加工に適しており、SSは食品機械や化学プラントの部品に適しています。選定ポイントとしては、加工する部品の用途を考慮し、必要な機械的特性に基づいて材料を選ぶことが重要です。結論として、フライス加工においては、S45CとSSの性能差を理解し、目的に応じて適切な材料を選定することが、製品の品質と経済性を保証する鍵となります。
3. S45C SS 比較:フライス加工機の選び方
フライス加工において、素材選びは非常に重要です。特に、一般的な機械構造用炭素鋼であるS45Cとステンレス鋼のSSでは、性能差が明確に存在します。S45Cは加工性が良く、コストも比較的低いため、多くの機械部品に使われています。対してSSは、耐食性に優れるものの、加工性が低く価格も高めです。具体例を挙げると、耐久性が求められる環境下ではSSが選ばれがちですが、コストや加工性を重視する場合はS45Cが選定されます。さらに、フライス加工においては、刃具の摩耗も考慮する必要があり、それらのバランスを取りながら適切な素材を選ぶことが重要です。最終的には、使用環境や加工の精度、コストなどの複数の要因を考慮し、S45CとSSのどちらを選ぶべきかが決まります。
4. フライス盤作業の基本的な手順
フライス加工での材料選定は非常に重要であり、S45CとSS材それぞれの性能差を理解することが成功の鍵となります。S45Cは炭素鋼であり、機械構造用鋼として高い強度と硬さを有しているため、耐久性が要求される部品加工に適しています。一方、SS材はステンレス鋼を指し、耐食性や耐熱性に優れており、化学的に厳しい環境や清潔を保つ必要がある用途で重宝されます。例えば、S45Cは自動車のエンジン部品や産業機械のギアなどに、SS材は食品機械や医療器具に利用されることが多いです。選定する際には、加工する部品の使用環境や要求特性を慎重に考慮し、両材料の性能を最大限活かすことが肝心です。最終的には、加工品の用途や性能要件に応じて、最適な材料を選ぶことが求められます。
5. S45C SS 比較:複合加工機の検定と最新技術
S45CとSSの材料は、フライス加工で異なる性能を示します。S45Cは炭素鋼であり、その強度と加工性のバランスが良いため、一般的な機械部品製造に広く利用されています。対照的に、SS(ステンレススチール)は耐食性に優れており、特に化学的な耐性が求められる環境でよく使われます。フライス加工では、SSはS45Cに比べて加工が難しく、工具の摩耗も早いですが、最終製品の品質保持には有利です。例えば、食品機械や医療器具にSSが選ばれるのはこのためです。従って、フライス加工で使用する材料を選定する際には、製品の用途や必要な特性に合わせ、適切な材料選びが重要です。耐久性と加工性のバランスを求めるならS45C、耐食性を最優先するならSSが推奨されます。最終的には、製品の性能を最大限に引き出せる材料選定に努めるべきでしょう。
6. 品質管理基準とS45C SSの規格値
フライス加工において、適材適所は重要です。S45CとSS材は、いずれも広く使用される鋼材でありつつ、それぞれ特徴があります。S45Cは炭素鋼で、高い強度と硬さを持ち、耐摩耗性に優れ、一方、SS材はステンレス鋼で、耐食性に優れています。よって、フライス加工においては、加工物の用途に応じて選定する必要があります。例えば、S45Cは歯車や軸受けなどの部品に使用され、SSは化学設備や食品機械部品に利用されます。適切な材料の選定は、コストの削減だけでなく、製品の寿命を延ばすという点においても極めて重要です。最終的には、製品の用途や必要とされる性能に最適な材料を選ぶことが、品質管理の上での最良のアプローチと言えるでしょう。
7. 5軸プログラム作成の方法
フライス加工における材料選定は、加工品の品質に大きく影響します。特にS45CとSSの比較は、その差が顕著です。S45Cは炭素鋼であり、強度が高く耐摩耗性にも優れているため、一般的な機械部品の製作に適しています。一方、SSはステンレス鋼の略で、耐食性が特徴ですが、S45Cに比べて硬さや強度は劣ります。フライス加工においては、S45Cは硬いため切削条件を適切に選定しないと工具の摩耗が激しくなりますが、加工精度が高い部品を製作可能です。逆にSSは柔らかさのため加工しやすく、特に衛生的に問題がある食品機械や化学機械への使用に適しています。具体例としては、S45Cは自動車のエンジン部品や産業機械の歯車などに、SSはキッチン用品や医療器具に用いられることが挙げられます。結論として、フライス加工においては、加工する部品の用途によって材料を選定すべきであり、それぞれの材料が持つ特性を考慮に入れることが重要です。
8. 技能レベル向上に向けたトレーニング
S45CとSS材のフライス加工においては、それぞれ異なる性能を持っているため、適切な選定が求められます。S45Cは一般的な炭素鋼であり、優れた機械的性質を有しており、耐久性や強度が高い部品加工に適しています。一方、SS材はさびにくいステンレス鋼で、耐食性が求められる使用環境に適しています。例えば、フライス加工でギヤやシャフトを製作する場合、S45Cが選ばれることが多いです。これは、その耐久性が高いためで、長期にわたって安定した性能を維持することができるからです。しかし、食品機械や化学プラントなどの耐腐食性が必要な場所では、SS材が選ばれる傾向にあります。したがって、使用される環境と加工する部品の性能要件に応じて、S45CまたはSS材を選定することが大切です。適切な材料選びをすることで、製品の品質と寿命を保ち、コストパフォーマンスも向上させることが可能になります。
まとめ
S45CとSSはどちらも一般構造鋼であり、硬度や耐熱性には大きな差がありませんが、切削性においてはS45Cの方が優れています。フライス加工では、切りくずの排出性や刃先の摩耗に影響を及ぼすため、適切な材質を選定することが重要です。刃先の摩耗が少なく、高い切削性を求める場合はS45Cを選ぶことをおすすめします。
機械加工のプロが教える!S45CとS50C材料のフライス加工比較術
機械加工の世界では、材料選択が非常に重要です。特にS45CとS50Cの材料はフライス加工において重要な役割を果たします。この記事では、機械加工のプロがS45CとS50Cの材料のフライス加工比較術を紹介します。S45CとS50Cの違い、それぞれの特性、フライス加工方法など、機械加工に関心のある方々に役立つ情報を提供します。
1. S45CとS50Cの基本的な特性とその比較
S45CとS50Cの材料を用いたフライス加工は、精密な機械部品製造において欠かせない工程です。これらの材料は特性が異なるため、加工時のアプローチも変わってきます。S45Cは機械構造用炭素鋼で、優れた機械的特性と加工性を持ちながら、低コストでありながらも一定の強度を持っています。それに対し、S50CはS45Cよりも炭素含有量がやや高く、硬度と強度が増すことで耐摩耗性に優れる一方で加工がやや困難になります。例えば、フライス加工においては、S50Cの方が切削速度を遅くするなど、慎重な設定が必要です。この違いを理解し、それぞれの材料の特性に応じた加工条件の見極めがプロの技術です。結論として、S45CとS50Cの適切なフライス加工を行うには、それぞれの材料特性を理解し、加工条件を最適化することが重要です。
2. S45CとS50Cのフライス加工特性
S45CとS50Cの材料は、フライス加工においてそれぞれ独自の特性を持っています。S45Cは一般的な機械構造用炭素鋼で、優れた機械的性質と加工性を持つため、広く利用されています。一方、S50CはS45Cよりも炭素含有量がわずかに高く、硬度が増す一方で加工性は若干劣るとされています。例えば、S45Cは比較的低い硬度のため、切削工具に対する抵抗が少なく、精密な加工が可能です。対照的に、S50Cは高硬度により耐久性が高まりますが、工具への負担も大きくなるため、適切な工具選定と加工条件の調整が必要です。最終的には、製品の用途や必要な特性に応じて、S45CとS50Cのどちらを選択するかが決まります。フライス加工においてこれらの材料を適切に利用することで、高品質の製品を効率良く生産することが可能です。
3. S45CとS50Cにおけるフライス加工の適用例
S45CとS50C材料のフライス加工比較術について知ることは、機械加工の精度を向上させる上で非常に重要です。これらの材料はそれぞれ異なる特性を持ち、適切な選択が品質に大きく影響を及ぼします。例えば、S45Cは炭素量が少なくて加工しやすく、一方でS50Cは炭素量がやや多く、硬度が高いため耐摩耗性に優れています。フライス加工においては、S45Cは一般的な部品の加工に適しており、その柔軟性から複雑な形状の加工が可能です。一方、S50Cは耐久性が要求される歯車や歯型などの部品加工に適しています。各材料の特性を理解し、使用目的に応じた適切な加工方法を選ぶことで、加工精度は飛躍的に向上します。結論として、S45CとS50Cの適切な比較と選択は、機械加工における品質と効率を左右するため、プロの技術者にとって必須の知識であることがわかります。
4. 加工効率を高めるS45CとS50Cのバリ・面取り技術
S45CとS50Cの材料を用いたフライス加工では、微妙な材質の違いが加工効率に大きな影響を及ぼします。S45Cは一般的な炭素鋼であり、良好な機械的性質と加工性を持ち、一方でS50CはS45Cよりもわずかに高い炭素含有量を持ち、硬度が高くなります。この硬度の違いがフライス加工時の加工効率に影響を与えるのです。例えば、S45Cの場合、比較的柔らかいため、刃先の摩耗が少なく、長時間の加工に適しています。それに対し、S50Cは硬度が高いため、刃の耐久性に優れる代わりに摩耗が起こりやすくなるため、切削条件の選定が重要となります。このように、材料に応じた加工技術を用いることで、フライス加工の効率を高めることができるのです。まとめると、S45CとS50Cでは硬度という物性が異なるため、フライス加工のアプローチもそれぞれ異なる必要があります。適切な知識と技術を用いることで、これらの材料の特性を最大限に引き出し、加工効率を高めることができるのです。
5. アスファルトスプレーヤにおけるS45CとS50C材料の利用
フライス加工においてS45CとS50C材料は明確な差があります。機械のプロフェッショナルとして、S45Cは一般的な機械構造用炭素鋼であり、S50Cはより炭素含有量が高いため硬度が増します。具体的には、S45Cは比較的柔らかく加工しやすいのに対し、S50Cは硬度が高い分、耐摩耗性に優れるが加工は困難です。例えば、同じ条件でフライス加工した場合、S45Cでは工具の摩耗は少なく、安定した加工が可能ですが、S50Cの加工にはより高いスキルと特別な工具が必要になります。結論として、材料を選ぶ際には製品の用途に合わせて、S45CとS50Cの特性を理解し、適切に選定することが重要です。
6. S45CとS50C軸受の公差と等級の比較
S45CとS50Cの材料は、フライス加工においてそれぞれ異なる特性を持っています。S45Cは一般的に強度と加工性のバランスが取れているため、多くの工業製品に利用されています。一方でS50Cは、より高い強度を持ち、耐摩耗性に優れるため、厳しい条件下での使用に適しています。たとえば、S45Cは基本的な機械部品や建設機械の部材に使われることが多いですが、S50Cは工具鋼として、または摩耗に強い部品が必要な場合に選ばれます。このように、S45CとS50Cはそれぞれの特性を生かし、適した用途で使用されることが多いです。最適な材料選びは、製品の性能を最大限に引き出すために欠かせない工程であるといえます。
7. CNC工作機械におけるS45CとS50Cの高速高精度加工
高速高精度なフライス加工には適材適所の原則が重要です。S45CとS50Cはともに炭素鋼でありながら、その機械加工性には差があります。具体的には、S45Cは耐摩耗性が高く、一般的な金型材料として広く使用されています。一方、S50Cはより高い強度と靱性を備えており、耐力が求められる部品に適しています。例えば、S45Cは曲げや衝撃に対する耐性が求められる構造部品に、S50Cは更に高い荷重がかかるギアやロッドに使用されることが多いです。このように、フライス加工で最適な結果を得るためには、使用する材料の特性を十分に理解し、その用途に応じた材料を選定することが肝要です。最終的に、S45CとS50Cを比較し選定することで、製品の性能や耐久性を最大化できるのです。
8. 炭素鋼S45CとS50Cのフライス加工におけるトラブルシューティング
炭素鋼のフライス加工では、材料の選択が重要です。ここで、よく使用されるS45CとS50Cの比較を通して適切な加工方法を解説します。S45Cは機械構造用炭素鋼で、一般的な機械部品に用いられる一方、S50Cはやや炭素含有量が高く硬度が上がることで知られます。例えば、S45Cは比較的柔らかいため加工しやすく、一方でS50Cは硬度が高いため耐摩耗性に優れていますが、加工時の工具の摩耗や熱影響を受けやすいという特徴があります。したがって、S50Cを加工する際は、切削速度を落とすか、冷却液を適切に使用して工具の寿命を延ばす必要があります。このような違いを理解しておくことで、フライス加工において材料ごとの適切な条件を選び、トラブルを避けることができます。
まとめ
S45CとS50Cはともに一般構造用炭素鋼であり、フライス加工に適した素材です。しかし、S50Cの方が硬度が高く、耐磨耗性に優れているため、加工難易度はS45Cよりも高いと言えます。フライス加工においては適切な切削条件を選択し、切削油を使用することで効率的な加工が可能です。
フライス加工での選択肢:S45CとS50Cのメリットとデメリット
フライス加工における材料選択は非常に重要です。特にS45CとS50Cは、その特性によって異なる利点や欠点があります。この記事では、フライス加工における材料選択の重要性とS45CとS50Cの比較を掘り下げて解説します。もし、フライス加工の際に適切な材料選択ができていないと感じている場合、この記事を参考にすることで、より的確な選択ができるようになるでしょう。
1. フライス加工とは:基礎から学ぶ
フライス加工において、使用する素材の選択は重要なポイントです。S45CとS50Cはその選択肢としてよく比較される素材で、それぞれが持つメリットとデメリットを理解することが重要です。S45Cは炭素含有量が少なく、加工性に優れているため、複雑な形状の加工に適しています。一方、S50Cは炭素含有量がやや高く、硬度・耐摩耗性に優れているため、耐久性が求められる部品作りに適しています。例えば、S45Cは自動車の内装パーツや家具の金具など細かいディテールが要求される製品に、S50Cはギアや歯車など負荷がかかる部位に使用されます。適切な素材選択により、加工効率と製品の品質を高めることができるため、S45CとS50Cの特性をしっかりと把握し選択することが、フライス加工において肝要なのです。
2. S45CとS50Cの特性:フライス加工における比較
フライス加工において、S45CとS50Cはよく使用される素材であり、それぞれの特性を理解することが重要です。S45Cは耐性が強く加工性に優れる一方で、S50Cはより高い硬度を持ち、耐磨耗性に優れています。たとえば、S45Cは一般的な機械部品や金型に使用されることが多いですが、S50Cはより高い強度を要求される部品に適しています。しかし、S50Cは硬度が高い分、加工する際に工具への負担が大きくなる点がデメリットです。総じて、S45Cは加工しやすさを重視する場合に適しており、S50Cは耐久性を重視する場合に向いています。両素材の選択にあたっては、製品の用途や加工の条件をしっかり考え選ぶことがポイントです。
3. S45Cフライス加工の利点と課題
フライス加工における材料選択は、製品の品質に直接関わる重要な要素です。特に、S45CとS50Cは多くの選択肢の中でも人気のある炭素鋼で、それぞれにメリットとデメリットがあります。S45Cは比較的安価で入手しやすく、強度と加工性のバランスが取れているため、多様な用途で使用されています。たとえば、一般的な機械構造用部品や、焼き入れを施して表面硬度を上げる必要がある製品に適しています。しかし、S45CはS50Cに比べて炭素含有量が低いため、強度が若干劣るという欠点があります。一方のS50Cは、S45Cよりも高い炭素含有量を持ち、高硬度を必要とする部品に理想的です。ただし、その分、加工が困難になることがあり、コストも高くなりがちです。従って、使用目的に応じて適切な材料を選ぶことが、フライス加工での成功には不可欠です。総じて、S45Cは汎用性とコストパフォーマンスに優れ、S50Cは特定の高い性能が求められる場合に適していると言えるでしょう。
4. S50Cフライス加工の利点と課題
S45CとS50Cはフライス加工における一般的な材料選択肢ですが、それぞれにメリットとデメリットがあります。S45Cは、比較的安価で入手が容易なことが大きな利点です。また、優れた機械的性質を持ち、一定の強度と靱性を備えています。これにより、汎用的な部品製造に適しています。反面、S50CはS45Cよりも炭素含有量が高く、硬度と強度が増します。そのため、より耐久性が求められる部品に適していますが、加工性は若干劣り、費用も高くなりがちです。例えば、精密な金型が必要な場合、S50Cが選ばれることがあります。しかし、その分加工には特別な配慮が必要となります。結論として、フライス加工における材料選択は、製品の用途やコストなどの要素を考慮し、バランス良く選択することが重要です。
5. 加工能率を向上させるフライス加工のテクニック
フライス加工において、多くの材料が使用されますが、特にS45CとS50Cはその選択肢として頻繁に比較されます。S45Cは加工性が優れており、一般的には硬度がやや低いため、比較的加工が容易です。これは、形状が複雑な部品や大量生産を必要とする場合に特に有利です。一方、S50CはS45Cよりも炭素含有量が高く、硬度が高いため耐摩耗性に優れていますが、加工が難しく、工具の摩耗も早い可能性があります。たとえば、金型などの耐久性が求められる部品にはS50Cが選ばれることが多いです。しかし、どちらも熱処理を施すことで性質を向上させることが可能です。結論として、S45Cは加工しやすさを、S50Cは耐久性を重視する場合に適していると言えます。適切な材料選びは、加工効率と製品の品質を左右するため、目的に応じて適切な選択が求められます。
6. ねじ切りフライスの選定とその利点
フライス加工で使われるS45CとS50Cは、それぞれにメリットとデメリットがあります。S45Cの利点は、その加工性の良さとコストパフォーマンスの高さにあります。中炭素鋼であるため、硬度も十分にありながら加工しやすく、多くの工業製品に適しています。反面、S50Cは高炭素鋼で硬度がより高いため、耐摩耗性に優れていますが、加工が困難であるというデメリットがあります。例えば、金型の基板などには、耐久性が求められるためS50Cが選ばれることが多く、逆に一般的な部品加工には加工性を重視してS45Cが選ばれます。最終的な選択は、加工する部品の用途や必要とされる特性に依存します。総じて、両材料ともにその特徴を理解し適材適所で利用することが重要です。
7. 機械加工でのS45CとS50Cの応用
フライス加工では、材料選びが重要です。特に、S45CとS50Cはその選択肢としてよく比較されます。S45Cは、優れた加工性と中程度の強度があり、一般的な部品製作に適しています。一方、S50CはS45Cよりも炭素含有量が高く、硬度と強度が増しますが、加工性は若干劣ることがあります。たとえば、S45Cは歯車やフランジなどの機械部品に用いられることが多く、S50Cはより高い強度を必要とする金型などに選ばれる傾向にあります。しかし、S50Cは加工により発生する熱によって硬度が高まるため、慎重な温度管理が必要になります。最終的には、製品の用途や必要な特性に応じて、S45CとS50Cのどちらを選ぶかを決定することが肝心です。適正な材料選定により、フライス加工の精度と効率を高めることができます。
8. 新しいフライス加工ヘッドの開発動向
フライス加工において、適切な材料の選択は品質とコストのバランスを大きく左右します。一般的に、S45CとS50Cはそれぞれ異なる特性を有し、選択にはメリットとデメリットが存在します。S45Cは焼入れ性が良く、加工性に優れている点がメリットであり、多くの工業製品の基本素材として使われています。しかし、強度や耐摩耗性を最大化させたい場合、S45Cは適していない場合があります。反対にS50Cは、より高い炭素含有量による強度があり、耐摩耗性が要求される部品に適していますが、S45Cに比べて加工性が劣るというデメリットがあります。例えば、プラスチック成型用金型では、耐久性が重視されるためS50Cが選ばれることが多いです。結論として、フライス加工においては、製品の用途に応じて、S45CやS50Cを適切に選択することが求められます。
9. S45C S50Cの被削性に関する研究
フライス加工において、S45CとS50Cはよく使用される材料ですが、選択にあたってはそれぞれの特性を理解することが重要です。S45Cは炭素含有量がやや低く、加工性が良好であり、比較的低コストで入手可能です。多くの機械部品や治具に利用され、その汎用性から多様な産業で採用されています。一方、S50Cは炭素含有量が高く、硬度や強度がS45Cよりも若干高いため耐久性に優れていますが、それに伴い加工が困難になる可能性もあります。特に精密な寸法を要求される部品製造には適しています。しかしながら、S50Cは硬度が高い分、加工ツールに与える負担も大きくなるため、工具の摩耗が激しくなる可能性があります。結論として、フライス加工での材料選択は、製品の用途と必要な特性を考慮し、コストとのバランスを見極めることが肝心です。S45Cは加工性とコストのバランスが取れた選択肢と言えるでしょう。一方で、耐久性を優先するならS50Cの選択が望ましいでしょう。
10. 熱可塑性エラストマーとフライス加工の相性
フライス加工において、しばしば選択される材質がS45CとS50Cです。これらの材質は、それぞれ一長一短をもちます。S45Cは汎用性が高く、中炭素鋼であるため、硬度と加工性のバランスが取れています。これにより、一般的な機械部品や金型などに適しており、幅広い用途で利用されます。一方、S50CはS45Cよりも炭素含有量がやや高く、より高い硬度を持っていますが、それにより加工性は若干落ちるというデメリットもあります。しかし、その分耐摩耗性に優れているため、摩耗に強い部品の加工に適しています。例としては、プレス金型や高負荷がかかる機械部品などが挙げられます。最終的には、製作する製品の使用条件や必要な特性を考慮して、S45CとS50Cのどちらを選択するか決定することが重要です。
11. フライス加工における材料選択の重要性
フライス加工において材料選択は重要であり、特にS45CとS50Cは多く用いられる素材ですが、それぞれメリットとデメリットが存在します。S45Cはより加工しやすく、一般的な機械部品に広く採用されています。それに対して、S50Cは硬度が高く耐摩耗性に優れているため、金型材料として選ばれることが多いです。例えば、S45Cは低い炭素含有量により靭性があり、溶接性も良好ですが、一方で強度はS50Cに劣ります。S50Cは高い炭素含有量で硬度と強度が増すため、耐久性が必要な部品に適していますが、加工が難しいというデメリットがあります。結論として、フライス加工においては、製作する部品の用途に応じて、S45CとS50Cのどちらを選ぶかを検討することが重要です。
12. S45C S50C比較:フライス加工ケーススタディ
フライス加工におけるS45CとS50Cの選択は、それぞれの材質が持つメリットとデメリットを理解することが重要です。S45Cは、優れた機械的性質と加工性を持ち、多くの機械部品に適しています。特に炭素含有量がやや低いため、硬度は必要十分でありながら加工しやすいのが特長です。一方、S50CはS45Cより炭素含有量が高く、より高い硬度を持つため耐摩耗性に優れていますが、その分加工が難しくなります。例として、S45Cは軸や歯車などの一般的な機械部品に多用され、S50Cは型や刃物などの耐摩耗性が求められる部品に用いられる傾向があります。しかし、硬度が高い材料は加工工具にも負担をかけるため、コストが上昇することも考慮する必要があります。結論として、フライス加工における材料選択は、製作する部品の用途に応じてS45CとS50Cの特性を踏まえた上で慎重に行うべきです。
まとめ
フライス加工において、S45CとS50Cはそれぞれ異なる特性を持っています。S45Cは加工性が良く、切削加工が容易ですが、耐摩耗性には劣ります。一方、S50Cは硬度が高く耐摩耗性がありますが、切削加工が難しい特性があります。加工する材料や求める特性に応じて適切な素材を選択することが重要です。
フライス加工での材料選び!S45C VS S50C徹底比較
フライス加工における材料選びは非常に重要です。特にS45CとS50Cは、フライス加工において最も一般的な材料です。本記事では、これらの材料を徹底比較し、それぞれの特性や利点、欠点について解説します。フライス加工における材料選びに迷っている方や、S45CとS50Cの違いについて知りたい方にとって、この記事は役立つ情報を提供することでしょう。
1. フライス加工とは?
フライス加工において最適な材料選びは非常に重要です。ここでは、よく使用されるS45CとS50Cの材料を比較します。S45Cは一般的な機械構造用炭素鋼で、加工性が良く、強度も適度に高いため幅広い用途で利用されます。対してS50Cは、S45Cよりもわずかに炭素含有量が高く、硬度が高いことが特徴です。例えば、プレス型やプラスチック成型型など、耐摩耗性を要求される部品に使われることが多いです。両材料ともフライス加工に適していますが、仕上がりの品質や用途によって選ぶべき材質は異なります。耐久性と強度を優先するならS50C、加工性とコストを重視する場合はS45Cが適していると言えるでしょう。最終的には、製品の用途と加工条件を考慮し、それぞれの特性を生かした材料選びが求められます。
2. S45CとS50Cの材質基本知識
フライス加工における材料選びは、加工品の品質を左右する重要なポイントです。特に、S45CとS50Cは、その選択に頭を悩ませる方も多いでしょう。S45Cは、優れた機械的性質を持ちながら加工性にも優れているため、一般的な機械部品や金型などに幅広く使用されています。一方のS50Cは、S45Cに比べて炭素含有量がわずかに高く、硬度と強度が若干向上していますが、その分、加工性は若干劣るという特徴があります。例えば、高い耐久性が求められる部品ではS50Cが選ばれることがありますが、加工が複雑である場合や大量生産を見込む場合には、加工しやすいS45Cが選ばれる傾向にあります。結論として、フライス加工において適切な材料を選択することは、目的と加工のしやすさを天秤にかけ、バランスを見つける作業であると言えます。
3. S45C S50C 比較:機械的特性の違い
フライス加工において、適切な材料の選択は非常に重要です。日本でよく利用されるS45CとS50Cは、それぞれ異なる特性を持っています。S45Cは硬度がやや低く、加工しやすいという利点がありますが、S50Cは硬度が高く、耐摩耗性に優れているため、より高い強度を必要とする部品に適しています。例えば、S45Cは一般的なギアやフィクスチャーの製作に使用されることが多く、S50Cはより高負荷がかかる歯車や高強度を求められる機械部品に選ばれます。したがって、加工する部品の用途を正しく理解し、それに最適な材質を選ぶことが、フライス加工の成功には不可欠です。
4. S45C S50C 比較:フライス加工性能
フライス加工において適切な材料を選ぶことは、製品の品質を決める上で非常に重要です。特に、S45CとS50Cという二つの炭素鋼材は、その違いを理解し選択することが求められます。S45Cは、優れた機械的性質と加工性を持ち、一般的な機械部品や金型の材料として広く利用されています。一方、S50Cは、S45Cよりもわずかに炭素含有量が高く、硬度が上がりますが、その分加工が難しくなる傾向にあります。例えば、細かい形状のフライス加工を行う場合や、表面処理が必要な時には、S45Cの方が適していることが多いです。対照的に、高い強度が要求される部品では、S50Cが選ばれるケースがあります。したがって、フライス加工における使用目的と加工条件を考慮して、最適な材料選択が求められるのです。
5. 旋盤・フライス加工におけるステンレスの切削性
フライス加工において材料の選定は非常に重要です。ここでは、よく使われる2つの材料、S45CとS50Cを比較します。結論から言うと、一般的な用途ではS45Cが推奨されますが、より高い強度が求められる場合はS50Cが適しています。S45Cは機械構造用炭素鋼であり、加工性が良く、比較的低コストで入手可能です。一方、S50Cも同じく炭素鋼の一種ですが、S45Cに比べて炭素含有量がわずかに高いため、硬度が増し強度が高まります。たとえば、プレス金型やギャーなどの耐久性が要求される部品にはS50Cが使われることが多いです。しかしながら、S50CはS45Cと比較して加工がやや難しくなるため、加工コストが上がる可能性があります。したがって、必要な特性を検討した上で材料を選ぶべきです。最終的に、用途に合わせて適切な材料選びが求められるのです。
6. 樹脂の切削加工と最適な素材の選び方
フライス加工において材料選びは非常に重要です。特に、機械部品の製造に多く用いられるS45CとS50Cは、その特性を理解することが肝心です。S45Cは炭素含有量が約0.45%で、強度と加工性のバランスが取れた材料として知られています。対して、S50Cは炭素含有量が約0.50%で、耐摩耗性に優れ、より高硬度の製品に適しています。例えば、S45Cは一般的な機械部品や、冷却が難しい加工に適しており、S50Cは型や金型などの耐磨耗性を要求される部品に使用される傾向があります。結論として、用途に応じてこれらの材料を選ぶことが成功の鍵となります。S45C、S50Cそれぞれの特性を理解し、最適な材料選びを行いましょう。
7. 螺紋フライスの定義と選び方
フライス加工における材料の選択は、製品の品質に大きく影響します。特に、S45CとS50Cはよく比較される材料であり、その特性を理解することが重要です。S45Cは強度と加工性のバランスが良く、一般的な機械部品や金型に適しています。一方、S50CはS45Cよりも炭素含有量が高く、硬度が増すため、耐摩耗性に優れる点が特徴です。たとえば、プレス金型や摩耗に強い部品には、S50Cが選ばれることが多いです。しかし、硬度が高くなるほど加工が難しくなるため、加工条件には注意が必要です。最終的には、加工する製品の用途や要求される特性に合わせて、適切な材料を選ぶことが肝要です。結論として、S45CとS50Cはそれぞれの特性を持ち、用途に応じて適切な選択が必要です。
8. CNC加工プロジェクトに適切な材料の選択
CNCフライス加工では材料選びが重要です。S45CとS50Cはどちらも一般的に利用される炭素鋼の一種で、機械部品などの製造に適しています。しかし、両者には微妙な違いがあります。S45Cは強度と加工性のバランスが良く、多くの工業製品で標準的に使用されています。一方、S50Cは炭素含有量がわずかに高く、硬度が増すため、より耐久性が求められる部品に適しています。例えば、精密な金型や耐摩耗性が必要な機器の部品製造にはS50Cが好まれます。選択に際しては、製造する部品の用途や必要な特性を考慮することが重要です。最終的には、加工性、強度、耐久性などの要因を総合的に考慮し、最適な材料を選ぶことが求められます。この徹底比較が、材料選びにおいて有用な参考になるでしょう。
9. 金属材料の種類と選び方
フライス加工において、最適な材料選びは仕上がりの品質を左右します。S45CとS50Cは、一見似た特性を持つ金属材料ですが、微妙な違いがあります。S45Cは炭素含有量が0.45%で、耐摩耗性や機械的性質が良好であり、一般的に多くの工業製品に使用されています。一方、S50Cは炭素含有量がやや高い0.50%で、S45Cよりも硬さが増すため、耐久性が要求される部品に適しています。たとえば、S45Cはフライス加工でのギアやフレームなどに使われることが多く、S50Cはハイエンドな金型や工具などに選ばれることがあります。結論として選択は用途に依存するため、加工物の特性を考慮し、適切な材料を選定することが重要です。
10. 結論:S45CとS50C、どちらが適材か
フライス加工で適切な材料を選ぶことは、製品の品質とコストに大きく影響します。特に、S45CとS50Cは一見似た特性を持ちながらも、その適用には差があります。S45Cは低炭素量で加工性が良く、あらゆる機械部品の製造に幅広く使用されています。一方、S50Cは炭素量がやや高く、硬度が若干高めで耐摩耗性に優れるため、より高い強度を要求される部品に選ばれることが多いです。例えば、精密機械や高負荷がかかる部品ではS50Cの使用が適しています。しかし、汎用性とコストを考慮するとS45Cが適材といえる場合もあります。結論として、フライス加工におけるS45CとS50Cの選択は、製造する部品の要求特性とコスト効率を慎重に考慮することが重要です。
まとめ
フライス加工では、S45CとS50Cの違いを理解することが重要です。S45Cは炭素含有量が少なく、機械加工性に優れています。一方、S50Cは耐摩耗性に優れており、硬度が高い特徴があります。加工する材料の用途や条件に合わせて適切な材料を選択することが、高品質な製品を生産するための重要な要素です。