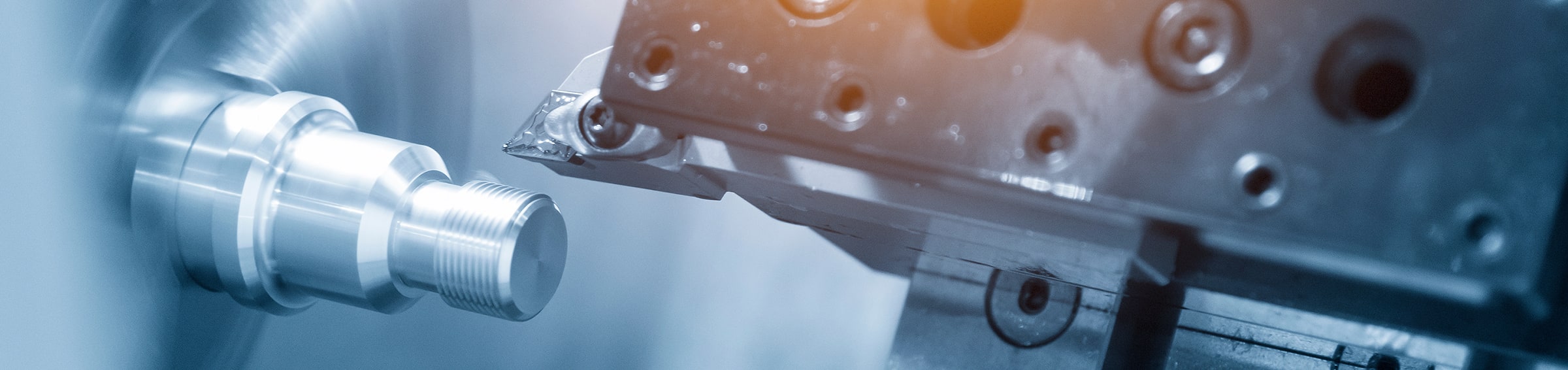
加工技術 column
量産に最適!SKDフライス加工の効果的な工程計画方法
量産において効果的な工程計画を立てることは重要です。特にSKDフライス加工においては、効率的な生産を実現するための工程計画の方法が求められます。本記事では、SKDフライス加工の効果的な工程計画方法について詳しく解説します。量産における効率的な生産を実現するためには、工程計画の適切な立て方が欠かせません。SKDフライス加工に特化した工程計画を考えることで、より効果的な生産が可能となります。
1. SKD フライス加工 量産の基礎知識
SKDフライス加工は量産に最適な方法として多くの製造業で採用されています。その理由は、SKD(Semi Knocked Down)方式を取り入れることで、効率よく部品を組み立てられるからです。具体的には、部分的に組み立てられた状態で製品を供給し、最終的な組立を行う事で、高効率かつ時間短縮を実現します。たとえば、自動車産業でのエンジン部品の加工や組立において、SKD方式を採用することで、労働力の削減やコストの低減を実現しています。結論として、SKDフライス加工による効果的な工程計画は、大量生産を行う上でのコスト削減と効率化に寄与する重要な手法であり、今後もさらなる改善と効率化が期待されます。
2. 金属加工とSKDの加工性比較
SKDフライス加工において効果的な工程計画は、量産におけるコスト削減と品質向上に不可欠です。理由として、SKDはその硬度と耐摩耗性に優れ、金属加工において高精度な製品を生産するのに適しているため、工程計画を最適化すれば、効率良く高品質な部品を大量に生産できます。具体的な例としては、適切な切削条件の選定、刃具の適切な選択、そして機械の運転時間の計画などが挙げられます。これらは全て、工具の摩耗を抑えつつ連続生産を可能にし、コストパフォーマンスを高めるために重要です。結論として、SKDフライス加工の工程を適切に計画することは、量産時のコスト削済みに加えて、安定した高品質な製品を確実に提供するために、極めて重要なプロセスといえるでしょう。
3. WC 含有 Ti(C,N)基サーメットの特性とSKD量産への影響
WC含有Ti(C,N)基サーメットは、SKDフライス加工において量産を最適化するための工程計画において重要な役割を果たします。この材料は、高い硬度と耐摩耗性を持ち合わせているため、工具の耐久性を向上させ、高速加工が可能になり、生産効率の向上に寄与します。特に、連続的な生産ラインで見られるように、切削工具の長寿命化は、停止時間の短縮とメンテナンスコストの削減につながり、大量生産の現場では重要な要素となります。たとえば、自動車部品の量産において、SKDフライス加工を用いたTi(C,N)基サーメット工具を使用することで、生産ラインの効率を大幅に向上させることができます。これは、製品の市場投入までの時間短縮とコスト削減に直結し、競争力の強化に寄与します。WC含有Ti(C,N)基サーメットを活用した工程計画は、SKDフライス加工の量産において、その効果的な応用により大きな利益をもたらすと結論付けることができます。
4. SKD フライス加工 量産のための生産性向上戦略
SKDフライス加工は、量産において高い生産性を実現する重要なプロセスです。そのためには効果的な工程計画が不可欠です。この計画では、加工時間の最適化、工具の選定、そして適切な切削条件の設定がポイントとなります。たとえば、工具の寿命を延ばすためには、適切な切削速度の選択が必要ですし、不要な工程の削減によって、加工時間を短縮し、コストを削減します。具体例として、SKDフライス加工においては、事前にシミュレーションを行い、衝突や過負荷を防ぐことで、工具の破損リスクを減少させることができます。これらの戦略を適切に組み合わせることで、量産時の生産性を大幅に向上させることが可能です。結論として、効果的な工程計画により、SKDフライス加工は量産に最適な加工方法となり得ます。
5. 増速スピンドルとSKD フライス加工の最適切削条件
SKDフライス加工は量産において重要な工程の一つであり、効果的な工程計画は生産効率の向上に不可欠です。この工程を最適化することで、加工時間の短縮とコスト削減が可能となります。具体例として、SKD(Semi Knock Down)部品は、予めある程度まで加工された状態で製造され、それを組み立てることで製品が完成します。これにより、部品の精度を均一に保つことができ、組み立て時の誤差を最小限に抑えることが可能となります。効果的な工程計画には、適切な切削条件の選定や増速スピンドルの利用が欠かせません。適切な切削速度や送り速度の設定によって、加工品の品質を保ちつつ、生産性を高めることが可能です。最終的に、これらの工程の最適化は、量産における品質と効率の両方を実現させる鍵となります。
6. SKD フライス加工による除去加工技術
SKDフライス加工は量産において非常に効果的な工程計画を持つ技術です。その理由は、SKDフライス加工が高い精度と速い生産速度を兼ね備えているため、多数の部品を迅速かつ均一に製造することができるからです。たとえば、自動車産業におけるエンジン部品や機械製造におけるギアなど、複雑な形状を持つ部品の量産にSKDフライス加工は頻繁に用いられています。この加工法では、精密な切削が可能なため、製品の品質を一定に保ちつつ、生産性を高めることが可能です。また、適切な刃具の選定やカット条件の最適化により、切削時間の短縮と工具寿命の延長を実現することができます。このようにSKDフライス加工の工程計画を最適化することで、経済的な量産が可能となり、製造業の競争力を高めることに貢献しています。
まとめ
SKDフライス加工は量産に最適な加工方法です。効果的な工程計画を行うことで生産性を向上させることができます。適切な工具選定や切削条件の最適化、工程の効率化などを行うことで、コスト削減や品質向上につながります。SKDフライス加工を導入する際は、熟練者の技術だけでなく、適切な計画と管理が重要となります。
高品質な試作品制作のためのSKDフライス加工テクニック
製造業界において、高品質な試作品を作るためのSKDフライス加工テクニックは欠かせません。この記事では、SKDフライス加工の基本から試作品制作に役立つテクニックまでを詳しく解説します。SKDフライス加工や試作品制作に興味がある方にとって、必読の内容となっています。
1. SKDフライス加工 試作の概要と重要性
高品質な試作品を制作するため、SKDフライス加工は欠かせない技術です。まず、試作品は最終製品と同等、またはそれ以上の品質を有している必要があり、そのためには精密な加工が求められます。SKDフライス加工は、硬質材料に対しても高精度な加工を実現し、複雑な形状や細部の仕上げにも対応可能です。例えば、自動車産業における部品試作では、厳しい耐久性や精度が要求され、SKDフライス加工によってこれらの条件を満たすことができます。また、エレクトロニクス分野では、微細な回路パターンを制作する際にもSKDフライス加工が利用されます。これにより、試作段階で高品質な製品が得られ、製品開発の成功率を高めることに寄与します。最終的には、SKDフライス加工は試作品の品質を確保する上で重要な役割を果たし、製品の市場導入をスムーズに進めるための鍵となります。
2. 金属加工業者の選定方法
高品質な試作品を作るためには、適切な金属加工業者の選定が非常に重要です。SKDフライス加工はその一例で、試作品の精度や耐久性を左右する重要な工程です。選定の際は、業者の過去の実績や技術力、納期遵守の実績に注目しましょう。例えば、SKDフライス加工を得意とする業者なら、複雑な形状や特殊な素材の加工にも対応でき、品質の高い試作品を提供してくれる可能性が高まります。さらに、緻密な技術力が要求される試作には、通常の加工業者ではなく、専門的なスキルを持った業者を選ぶことが不可欠です。最良のSKDフライス加工業者を選び、高品質な試作品制作に繋げていくことが成功への鍵となるでしょう。
3. SKDフライス加工 試作の部品加工サービス比較
SKDフライス加工は試作品制作において重要な技術です。この加工法は、精密な試作品を制作するために必要不可欠であり、その高い加工精度は高品質の試作品を約束します。具体的な例としては、複雑な形状を持つ部品や、極めて狭い公差を要求される部品など、細かなディテールが求められる状況においてSKDフライス加工の真価が発揮されます。また、この技術を用いることで、材料の無駄を最小限に抑えることが可能であり、コスト効率の良い試作が可能になります。結論として、SKDフライス加工は試作品を精密に、かつ効率良く制作する上で欠かせない技術であり、品質の高い試作品制作にはこの加工技術を用いることが推奨されます。
4. SKDフライス加工 試作のための旋盤とフライス加工の専門企業
高品質な試作品を作成するためには、SKDフライス加工が欠かせません。SKDフライス加工とは、金属加工技術の一つであり、試作の精度と品質を向上させるための重要な手法です。なぜなら、この加工法により複雑な形状や緻密なパターンの部品を高精度で製造することができ、試作品のレベルをぐっと高めることが可能になるからです。日本では、精密な技術が求められる自動車や電子機器などの産業分野で特に重宝されています。具体例としては、自動車のエンジン部品やスマートフォンの内部構造など、高度な技術が必要とされる部品の製作に利用されることが多いです。このような高品質な試作品を実現するためには、専門の技術と経験を持つ企業に依頼するのが最良の選択でしょう。そうすることで、企画段階から製品の完成に至るまで、一貫した品質管理の下で作業を進めることができます。結局のところ、SKDフライス加工は試作品の高品質化を実現するために不可欠な技術であり、それを駆使することがプロジェクト成功へのカギとなるのです。
5. 精密部品加工の技術とプロセス
SKDフライス加工は、高品質な試作品制作に不可欠な技術です。なぜなら、この技術は複雑な形状や多様な素材に対応可能で、精密な部品を製造する際の要求を満たすからです。具体的には、SKDフライス加工を利用することで、硬度が高い材料でも精細な加工が可能となり、試作品の品質と機能の向上が図れます。例えば、自動車産業や航空宇宙産業では、図面通りの精度が要求される部品が多く、SKDフライス加工によってその精密さが実現できます。また、少量生産の試作品においても、コスト効率を保ちつつ多様な形状を試作することができるのです。結果として、SKDフライス加工は試作品制作の過程でその高い技術力を発揮し、製品開発の成功率を高める重要な役割を担っています。
6. 金型製作業者の信頼性と実績
高品質な試作品を作成するためには、SKDフライス加工が重要な役割を担っています。SKDフライス加工は、耐久性に優れた金型を作成する際に不可欠な技術であり、その精度が試作品の品質を大きく左右します。例えば、緻密な寸法精度や表面粗さを実現するためには、適切な切削条件の選定や、専用の切削工具が必要不可欠です。実際に、精密部品の製造においてSKDフライス加工を採用することで、高い寸法精度と表面品質を持つ部品が得られ、試作品としての信頼性が向上します。このような技術の適用は、特に要求性能が高い航空宇宙産業や自動車産業の試作品作りにおいて、非常に重要です。したがって、SKDフライス加工テクニックは高品質な試作品制作において、その性能を最大限に引き出すためのキーとなるのです。
7. SKDフライス加工 試作を成功に導くコツ
試作品の制作において、SKDフライス加工はその高品質な結果により注目されています。試作の段階でSKD加工を選ぶことは、製品の精度向上とコスト削減の両面において利点をもたらします。SKDフライス加工は、耐磨耗性に優れた刃具を使用し、精密な加工が可能です。例えば、複雑な形状の部品や微細なディテールを必要とする製品において、この技術は特に効果を発揮します。しかも、試作品を実際の材料で正確に製作することで、将来的な量産に向けたデータ収集と検証が行えるのです。結論として、SKDフライス加工は、試作品を高品質で効率よく製作するために欠かせない技術であり、その精度とコストのバランスから、製品開発の現場で重宝されているのです。
8. よくある質問と答え
SKDフライス加工は、試作品制作における高品質な製品を実現する上で重要です。この技術により、精密な部品加工が可能となり、特に金型や機械部品の試作に最適です。理由は、SKD材料が硬度と靭性のバランスが取れているため、耐久性と加工性の両方に優れているからです。例えば、自動車業界では、新しい部品の試作に際してSKDフライス加工が用いられることが多く、細かな形状やサイズの要求を満たすことができます。このようにSKDフライス加工は、品質が要求される試作品には不可欠であり、結果として製品開発の速度と効率を高めることに貢献します。
まとめ
SKDフライス加工は、試作品制作において高精度で複雑な形状の加工が可能なテクニックです。この加工方法を使用することで、試作品の品質向上と製造効率の向上が期待できます。素材や形状に合わせた適切な工具選びや切削条件の設定が重要です。また、加工経験豊富なスキルを持つ技術者が制御することで、高品質な試作品が実現します。
【試作必見】SKDフライス加工をマスターするための便利なティップス
SKDフライス加工をマスターするための便利なティップスをお探しの方には、この記事がぴったりです。試作を行う上で欠かせないSKDフライス加工について、基本的なことから始めて、実践に役立つヒントやテクニックまでを網羅しています。試作におけるSKDフライス加工の重要性を理解し、マスターするための貴重な情報を手に入れましょう。
1. SKD フライス加工 試作の基本
SKDフライス加工の試作は高精度な部品製造に不可欠です。試作を通じて、最終製品の品質や加工精度をなるべく高めることができます。具体的には、SKD材の特性を考慮した切削条件の決定や刃具の選定が重要となります。例えば、SKD材は硬度が高いため、耐摩耗性のある刃具を使用することが肝心です。また、加工中の熱影響を最小限に抑えるため、適切な冷却方法の選択も必要です。試作段階でこれらの要素を丁寧に調整することで、量産時のトラブルを減らし、コスト削減にも繋がります。結論として、SKDフライス加工の試作は工程を洗練させ、製品の質を向上させるための重要なステップであると言えます。
2. SKD11鋼とは?CNCフライス加工の適用性
SKDフライス加工は、試作品の製作を行う際に非常に重要なプロセスです。特に、耐摩耗性に優れたSKD11鋼は、金型や機械部品の製造に頻纍する素材であります。この素材を扱うには、適切な加工技術が必要とされています。たとえば、SKD11鋼を使用する際には、硬度が高いため、切削には特に注意が必要です。適切な切削工具の選定や、冷却液の使用、切削速度の調整が、精密な加工を実現するカギとなります。実際の製作例として、試作品製作においてSKD11鋼を用いて形状やサイズが特殊な部品を成功させる場合、これらのティップスを活用することが重要です。結論として、SKDフライス加工では、材料特有の性質を理解し、適切な加工方法を選択することで、高品質な試作品を製作することが可能となります。
3. SKD フライス加工 試作のための材料選定
試作品を作る際にSKDフライス加工を用いることは、その高い精度と耐久性から、多くのメーカーにとって重要なステップとなります。特に、工具の材料として使われるSKDは、硬度が高く加工が難しいという特性を持っていますが、適切な材料選定によって、加工の効率が大きく変わることがあります。たとえば、試作段階での材料の硬さ、対応する切削工具の選択、切削条件の最適化など、具体的な条件を細かく検討する必要があります。正しい材料を選定することで、加工精度の向上はもちろんのこと、工具の寿命を延ばし、コスト削減にもつながります。最終的には、これらの選択が試作品の品質に直結するため、SKDフライス加工をマスターするためには、材料選定が非常に重要なポイントとなるのです。
4. SKD フライス加工 試作の難削材対応戦略
SKDフライス加工は試作段階での適切な戦略を立てることが成功の鍵です。この材料は硬く加工が難しいため、詳細な計画が必要とされます。具体的には、最適な工具選びや切削条件の慎重な設定が挙げられます。たとえば、SKD材を扱う際は刃先の耐久性が高く、正確な切り屑排出が可能な工具を選択することが重要です。さらに、加工時の熱管理に注意し、過度な温度上昇が材料の変質を引き起こさないようにする必要があります。適切な冷却剤の使用は、これを防ぐ上で効果的です。これらの対策により、SKDフライス加工における試作品の品質を高めることができます。最終的に、事前の綿密な計画と正しい工具選択を通じて、SKDフライス加工の試作はスムーズに、そして成功裏に進むでしょう。
5. SKD フライス加工 試作における最新技術
SKDフライス加工は、試作品の製作過程でその精度と効率が評価されています。日本において、特に金型などの精密な部品を作る際には、耐摩耗性や強度に優れたSKD素材がよく用いられます。この素材を用いたフライス加工では、ツールの選択や切削条件が重要となり、経験豊富な技術者の知識が不可欠です。たとえば、SKD11のような硬質材料の加工には、硬度の高いカッターや特殊なコーティングが施された工具の選定が試作の成功を左右します。また、切削速度や給進速度などの条件を最適化することで、加工後の仕上がり精度を高め、耐久性を保つことができるのです。このように、試作段階でのSKDフライス加工を適切に行うことで、品質の高い製品を効果的に生産する基盤を築くことができます。
6. フライス盤の基礎とSKD フライス加工 試作への応用
SKDフライス加工は精密な部品制作に不可欠であり、その試作は多くの工業分野で重要なプロセスです。試作を成功させるためには、適切な技術と知識が必要です。たとえば、SKDの硬度や熱処理状態を理解し、適切な切削条件(切削速度、送り速度、切り込み深さ等)を選択することが重要です。また、使用する刃物の材質や形状も結果に大きく影響します。具体例として、SKD11などの合金鋼では、高い硬度を持つため、耐摩耗性に優れたコーティングカッターの使用が推奨されます。このように、試作には材料の特性を理解し、最適な刃物を選び、正確な加工条件を設定することが求められるのです。これらのポイントを押さえることで、SKDフライス加工の試作をマスターすることができます。
7. SKD フライス加工 試作におけるポリフェノール材料の特性
SKDフライス加工の試作には、いくつかの重要なポイントがあります。まず、SKD素材は硬度が高く耐摩耗性に優れているため、正確な加工が可能です。そのため、試作段階での精密な設計が求められます。具体例として、刃具の選定はSKD加工において重要な要素です。耐久性の高い刃具を選ぶことで、長期に渡って安定した加工が行え、コストパフォーマンスも向上します。また、冷却液の適切な使用は、加工時の発熱を抑え、素材の変質を防ぐために不可欠です。これにより、試作品の品質を保ちながら、効率的な生産を実現することができます。最終的にはこれらの注意点を踏まえたうえで、試作段階から正確な加工を心がけることが、SKDフライス加工をマスターするための重要なステップとなるでしょう。
8. メラノイジンを用いたSKD フライス加工 試作のポテンシャル
SKDフライス加工の試作は、製造業での品質向上とコストダウンに必須です。SKDとは特に硬度が高く加工が難しい工具鋼の一種であり、その試作を成功させるためには、適切なティップスを身につけることが重要です。例えば、適切な刃の選択、加工パラメータの細かな調整、クーラントの使用などが良い試作を行うための具体的なポイントとなります。特にSKDフライス加工では、切削速度や送り速度を慎重に決定することが、加工品質を左右します。また、冶具の固定方法や切削液の種類も、加工精度に大きな影響を与えるため、試作段階での十分な検証が求められます。試作を通じてこれらを最適化することで、量産時のトラブルを未然に防ぎ、効率的な生産ラインを実現することができます。
9. 日本におけるSKD フライス加工 試作機械の輸入動向
SKDフライス加工の試作は、精度が高く耐久性に優れた部品制作に不可欠なプロセスです。試作段階では、最適な加工方法の確立が重要となります。日本においてSKD材を用いた試作への需要は高く、これに伴い、効率的なティップスを知ることは技術者にとって非常に価値があります。例えば、適切な工具選択や切削条件の最適化、そしてCAD/CAMソフトウェアの活用などが挙げられます。また、小さなバリも製品の品質に大きく影響を与えるため、精密な仕上げが求められます。このようなティップスを活用することで、SKDフライス加工の試作においても、より速く、正確な部品作りを実現できるでしょう。結論として、試作は成功のための重要なステップであり、有効なティップスを掌握することはその成功への近道となります。
10. SKD フライス加工 試作の未来展望
SKDフライス加工の試作は、その精度と効率性から日本の製造業において重要な位置を占めています。試作段階では、様々な工夫が必要とされる中、いくつかのティップスを身につけることで、加工精度を高め、コストを削減することができます。例えば、適切な工具選択や切削条件の最適化、さらにはCAD/CAMソフトウェアを利用した事前シミュレーションにより、試作品の品質向上が期待できます。また、チップの交換頻度を抑えるためのクーラントの使用なども、長期的なコスト削減に寄与します。これらのティップスを活用することで、試作段階での問題を未然に防ぎ、最終製品への影響を最小限に抑えることが可能です。結論として、SKDフライス加工における試作は、適切な知識と工夫を組み合わせることで、その品質と効率性を大きく向上させることができるのです。
まとめ
SKDフライス加工をマスターするためには、正しい工具や適切な加工条件を選定することが重要です。試作品を作成する際には、加工精度や表面仕上げに注意することで、高品質な部品を製造することが可能です。また、素材の特性や適切な切削速度、切削深さなどのパラメータを把握することが成功のポイントです。マスターするためには実践を重ねることが重要であり、継続的なトレーニングが不可欠です。
試作を成功させる!SKDフライス加工の注意点と設計のポイント
試作品の開発において、SKDフライス加工は重要な役割を果たします。しかし、その成功には注意点や設計上のポイントが存在します。SKDフライス加工における試作の成功を目指す方々に向け、この記事ではその注意点と設計のポイントについて詳しく説明します。SKDフライス加工の専門知識を持ちながらも、試作の成功に悩む方々にぜひお読みいただきたい内容です。
1. SKD フライス加工 試作の基本
SKDフライス加工における試作成功の鍵は、正確な設計と加工プロセスの理解にあります。まず、材質の特性を十分に考慮することが肝心であり、SKD材は硬度が高く加工が難しいため、適切な工具選びと切削条件の設定が必要です。例えば、鋭角なカッターの使用や低速での切削は、加工時の負荷軽減と精度向上に寄与します。また、クーラントの適切な使用は、切削熱による変形を防ぐためにも重要です。試作段階では、小ロットでの反復試験を行い、仕上がりの品質を確認しながら設計を微調整していくことが望ましいです。結論として、材質理解、適正な工具選定、適切な条件設定、そして反復試験による確認は、SKDフライス加工における試作を成功させるための重要なポイントです。
2. SKD11とSKD61の違いとそれぞれの特性
SKDフライス加工の試作に成功するためには、その特性を理解し、適切な設計を心がける必要があります。SKD11とSKD61は、耐摩耗性や耐熱性に優れ、金型や工具材料として広く利用されていますが、これらの材質には異なる特性があります。たとえば、SKD11は高い耐摩耗性を持ち、精密な金型加工に適しています。一方でSKD61は、高温でも硬度が維持されるため、ダイカストなどの耐熱性が求められる用途に適しています。試作段階では、これらの材質特性を踏まえ、加工条件や設計の細部に注意を払うことが重要です。例えば、SKD11を用いる際には、細かい表面処理が必要になることもありますし、SKD61の場合は高温での加工に対応した機械設定が求められます。最終的には、これらの材料の特性を活かした設計と試作の反復を通じて、最適な加工方法を見つけることが成功への鍵となります。
3. 高品質なSKD フライス加工サービスの選び方
SKDフライス加工における試作の成功は、製品の品質を左右する要因となります。そのため、設計段階から細心の注意を払い、試作の成功を目指す必要があります。まずは、加工する材料の特性をしっかり理解することが重要です。SKD材は硬度が高いため、加工時の熱対策や適切な切削条件の選定が欠かせません。さらに、精密な加工を要するため、刃具の選択や工具経路の設計も慎重に行う必要があります。例えば、複雑な形状の部品を加工する場合は、切削負担を均等に分散させる工具経路を設計することがポイントとなります。最後に、加工条件や工具の選定といった試作段階で得られたデータを基に、本番の製造に移る前に反映させることが、高品質な製品を生産するために不可欠です。このように、SKDフライス加工の試作では、材料の特性を理解し、適切な加工方法を選択し、詳細な設計を行うことが成功への鍵となります。
4. SKD フライス加工試作における加工性比較試験
SKDフライス加工の試作を成功させるためには、加工の特性を理解して設計段階で注意が必要です。SKD材は硬度が高く耐摩耗性に優れているため、金型制作に適していますが、その硬さが加工を難しくもしています。特に、試作段階では量産加工と異なる要素が多く、具体的には、切削条件の最適化や工具選定に細心の注意を払う必要があります。たとえば、工具はSKD材の硬さに耐えられるものを選び、切削速度や送り速度の設定は慎重に行うべきです。また、試作では小ロットのため、経済的な材料利用と時間短縮のバランスを取ることが重要になります。このように適切な設計と加工条件の選定により、SKDフライス加工の試作成功率を高めることができます。成功への鍵は、硬度と加工性のバランスを見極め、慎重かつ効率的なアプローチにあります。
5. 焼き入れ不要の高硬度鋼材NAK材とSKD フライス加工
SKDフライス加工が持つ重要性は試作段階での成功にあります。なぜならば、試作を通じて製品の設計に対するフィードバックが得られ、量産への道筋をつけるからです。SKD材の特性を考慮した加工設計は、耐摩耗性や耐熱性が求められる部品の実現に不可欠です。例えば、精密な金型部品を作る際には、SKD材の均一な硬度分布が品質の均一性を保つ上で重要です。そのためには、カッターパスの最適化や適切な切削条件の選定が必須となります。また、コーナーRの設計や排屑性の良い設計など、細部にわたる注意が必要です。結論として、SKDフライス加工の成功は、材料特性を理解し、それに応じた加工技術と設計の工夫によって左右されると言えます。これにより、試作品の品質向上と量産への移行がスムーズに進みます。
6. Mazak INTEGREX j-200 500Uを活用したSKD フライス加工技術
SKDフライス加工での試作成功は、効率よく高品質な製品を市場に供給するために不可欠です。そこで注目されるのが、適切な加工技術と設計のポイントの理解です。例えば、硬度が高いSKD材を使用する際には、切削工具の選定や切削条件の最適化が重要となります。具体的には、工具の耐摩耗性を考慮した材質選びや、切削スピード、フィード率の調整が挙げられます。また、フライス加工において均一な仕上がりを実現するためには、機械の剛性や精度も重要な要素です。Mazak INTEGREX j-200 500Uを用いることで、これらの要件を満たすことが可能であり、試作の精度を高めることができます。結論として、適切な工具と機械の選定、そして正確な設計が試作を成功させるカギとなり、SKDフライス加工のポテンシャルを最大限に引き出すことができます。
7. SKD フライス加工試作のための設計のポイント
SKDフライス加工における試作は品質の担保とコスト削減に直結するため、成功させることが非常に重要です。そのためには、加工性の良い材料選びや適切な切削条件の設定が必須となります。例えば、SKD材は硬度が高く加工しにくい特性を持っているため、加工時には低速での切削や冷却液の充分な使用が重要です。また、工具の選定にも注意が必要で、SKD材に適したコーティングや形状の工具を使うことで、耐久性を高めつつ精度の高い加工が可能になります。さらに、加工前の丁寧な設計は、試作品の精度向上に寄与します。設計段階でのシミュレーションを行い、加工工程や工具の動きを事前に検討することで、実際の加工で発生する問題を未然に防ぎます。これらの点に注意し、適切な設計と加工を行うことが、SKDフライス加工試作の成功に繋がります。
8. まとめ
SKDフライス加工における試作が成功するためには、いくつかの重要なポイントがあります。この加工法は、硬質材料の精密な成形に適しているため、特に金型製作などで使用されます。成功の鍵は、適切な設計と丁寧な加工工程の管理にあります。たとえば、材質の選定では、加工性と耐久性を考慮したSKDの種類を選ぶ必要があります。また、カッターの選択や切削条件の設定は、材料の特性に応じて慎重に行うべきです。具体的には、過度な切削抵抗を避けるためにも、適切な切削速度と送り速度のバランスを見極めることが重要です。最終的な製品の品質を確保するためには、試作段階での細かな調整が不可欠であり、これにより設計の精度を高め、製造コストの削減にもつながります。結論として、SKDフライス加工における試作成功は、材料選定から加工設定、細部にわたる検証まで、全工程に渡る注意深い検討が必須であると言えるでしょう。
まとめ
SKDフライス加工において試作を成功させるには、設計段階から適切な注意点を押さえることが重要です。材料選定や切削条件の検討、加工精度の確保などがポイントです。さらに、試作品の改善点を分析し、設計の段階から反映させることで効率的な試作が可能となります。
SKDフライス加工で試作品を作る際の完全ガイド【2023年版】
新しい製品を開発する際、SKDフライス加工を使って試作品を作ることは重要なステップです。本記事では、SKDフライス加工の基本から試作品を作るための具体的な手順まで、2023年版の完全ガイドを提供します。製品開発における重要な工程であるSKDフライス加工と試作作業について理解を深め、効率的な試作品作りに役立つ情報をご紹介します。製品開発における成功の鍵を手に入れるための一歩として、ぜひご一読ください。
1. SKDフライス加工試作の基礎知識
1-1. SKDフライス加工とは
SKDフライス加工とは、試作品や小ロット生産に適した高い加工精度と耐摩耗性を備えた工法です。この加工法は、試作品作りにおいて、その経済性とスピード感から注目されています。例えば、複雑な形状や特殊な材料を用いた部品には、SKDフライス加工が適しており、精密な仕上がりを要求される場合にも優れた選択肢となります。具体的には、新しい製品の開発段階で、機能やデザインの検証を行う際に、実際の製品と同様の材質で試作品を作成することが可能です。このため、SKDフライス加工は、製品開発のフィードバックを迅速に得るための重要な手段として、多くの製造業者に利用されています。総じて、SKDフライス加工は試作品製造の精度と効率を大きく向上させる技術であると言えるでしょう。
1-2. 試作品製作のプロセス
SKDフライス加工を用いた試作品製作は、その精度の高さから多くの企業にとって重要なプロセスです。この加工方法は、試作品が将来の量産に向けての品質や機能を満たすことができるかを確認するためのものであり、具体的な製品開発の初期段階で非常に役立ちます。たとえば、複雑な形状や独自の素材を用いた製品において、SKDフライス加工はその精密さを発揮し、実際の使用環境下での製品の振る舞いを予測するのに最適です。この技術により、設計段階での誤算を減らし、製品改善へとスムーズに繋げることが可能となります。最終的に、SKDフライス加工による試作品は製品の品質向上に必要不可欠なステップであり、成功への確かな道を築くための重要な基盤となるのです。
1-3. SKDフライス加工の利点と課題
SKDフライス加工は、試作品を製作する際に欠かせない工程です。この加工技術の最大の利点は、高精度かつ複雑な形状の部品を短時間で製作できる点です。例えば、自動車産業や航空産業においては、精密な部品が必要不可欠であり、SKDフライス加工によってデザインの検証から機能のテストまでスムーズに行うことができます。しかしながら、課題も存在します。特に、加工前には材質の選定や工具の選択が重要であり、経験豊富な技術者が不可欠です。さらに、試作品の複雑性が増すにつれて、加工時間やコストが増加する傾向にあります。結論として、SKDフライス加工は試作品を高品質に仕上げるためには最適な手法であるものの、それには適切な知識と技術が必要です。したがって、2023年版の完全ガイドを参照することで、これらの課題を克服し、試作品製造の効率化を図ることができます。
2. SKDフライス加工試作の企業ランキング
2-1. トップ試作部品加工サービス企業
SKDフライス加工による試作品作成は、製品開発の重要なステップです。この加工技術の精度と柔軟性により、高品質な試作品を迅速に作成することができます。SKDフライス加工では、硬質の材料を精密に削り出すことが可能であり、複雑な形状や微細な部品も製作することができるため、多くの産業での利用が見られます。例えば、自動車業界では、新たな部品の試作や改良にSKDフライス加工が頻繁に用いられています。さらに、この技術を用いることで、仮組みの段階でのフィッティングの問題や機能面での不具合を早期に発見し、開発サイクルの短縮とコストの削減に貢献することができます。以上の理由から、試作品の作成にはSKDフライス加工が極めて有効であると結論付けられます。
2-2. 選定基準と企業の強み
SKDフライス加工による試作品製作は、精度の高い部品を迅速に作る必要がある際に非常に有効な手段です。この技術がもたらすメリットは、高精度で複雑な形状を持つ試作品を短期間で製造できることにあります。例えば、自動車産業や航空産業における部品開発では、SKDフライス加工が活用され、緻密な設計が求められる部品を正確に再現しています。また、加工速度の向上もSKDフライス加工が選ばれる理由の一つです。試作段階では、設計変更が頻繁に発生するため、迅速な加工が可能なSKDフライス加工は大きなアドバンテージとなります。最後に、SKDフライス加工は小ロットにも対応可能で、コスト面でも利点があります。試作品製作においては、ひとつひとつの部品のコストが重要な要素となるため、こうした柔軟性が求められるのです。以上の理由から、SKDフライス加工は試作品を作る際の優れた方法として、2023年現在も高い評価を受けています。
2-3. 企業比較と選び方
SKDフライス加工は、試作品製作において高精度かつ高速な生産を可能にします。これは、試作品が設計の検証や市場での受け入れを確かめる重要なステップであるため、製造プロセスにおいて極めて重要です。たとえば、新しい自動車部品の試作を想像してください。SKDフライス加工によって、複雑な形状を持つ部品も短期間に正確に製作することができ、実際の運用状況を模擬したテストが可能になります。この精度とスピードは、市場投入までの時間を短縮し、競争力を保つために不可欠です。選択する企業では、最新技術を導入し、優れた技術力を持つ専門家による対応が期待できることを確認することが重要です。そうすることで、試作品の品質を保ちつつ、市場のニーズに迅速に応えられるのです。
3. 鍛造とSKDフライス加工試作の関連性
3-1. 鍛造技術の基本
SKDフライス加工を用いて試作品を作る場合、精度の高い製品が得られることが最大の利点です。SKDフライス加工は、金属やプラスチックなどの素材に溝や穴を加工する方法で、試作品作りには不可欠です。その理由は、SKDフライス加工により、複雑な形状や緻密なデザインが実現可能となるためです。たとえば、自動車の部品や医療機器のコンポーネントなど、精密な加工が求められる案件においては、SKDフライス加工が大きな力を発揮します。また、最新のSKDフライス加工機は、プログラミングによって操作を行い、非常に高い再現性と速度で加工を実施できるため、効率的な試作が可能となります。このように、SKDフライス加工を使用することで、試作品の品質向上と生産時間の短縮を実現することができ、それは製品開発の加速に寄与することになります。
3-2. SKDフライス加工と鍛造の組み合わせ
SKDフライス加工は、試作品製作において重要な役割を果たします。この加工方法は、複雑な形状や精密な部品を効率的に造形することができるため、試作品の開発には欠かせません。特に、SKD(工具鋼)は耐摩耗性や硬度が高い特性を持っており、フライス加工に適しています。例えば、自動車の部品や家電製品のプロトタイプを作る際、SKDフライス加工を用いることで、実際の製品に近い強度や耐久性を持った試作品を得ることが可能です。さらに、SKDフライス加工と鍛造を組み合わせることで、より一層の強度を持ちながらも、コストを抑えた試作が実現します。これらの理由から、試作品を製作する際にはSKDフライス加工を活用することが推奨されています。その結果、開発プロセスが効率化され、製品の市場投入までの時間を短縮することに貢献するのです。
3-3. 技能向上のためのリソース
SKDフライス加工は、試作品を作成するうえで非常に有効な手法です。試作品を作ることは、新しい製品開発において最終製品の品質を予見し、設計の誤りを修正するために不可欠です。SKDフライス加工はその精密さから試作品作成に適しており、よりリアルなモデルを提供します。例えば、複雑な形状や微細な部品でも、この加工方法により高い精度で再現することが可能です。また、材料の無駄を減らし、コストを削減することもできます。確かな試作品によるフィードバックは、製品の市場投入前の改善に直結し、失敗リスクを減らします。このようにSKDフライス加工は、試作品を通じた製品開発の質の向上に大きく寄与するため、積極的な活用が推奨されます。
4. SKDフライス加工試作における用語解説
4-1. 機械加工関連の重要用語
SKDフライス加工で試作品を作る際、その正確な実施は製品開発の成功に不可欠です。この加工方法は、精密な部品を素早く生産することが可能であるため、試作段階での利用に適しています。例えば、複雑な形状の金属部品や耐久性が求められるプラスチックの部品の製作には、SKDフライス加工がよく採用されます。この技術を使用することで、設計図通りの正確な寸法と形状を持つ試作品を短期間で製作することが可能になります。さらに、適切な工具選択や条件設定を行うことで、高品質な試作品が得られ、後の量産化に向けてのリスクを最小限に抑えることができます。したがって、精密な試作品製作にはSKDフライス加工が不可欠と言えるでしょう。
4-2. 試作と製品化の間の用語
SKDフライス加工は、試作品作りにおいて精度が高く、効率的なため注目を集めています。試作段階では、デザインの検証や機能のテストが不可欠です。SKDフライス加工を利用することで、これらの工程を正確かつ迅速に行うことができます。具体的な事例として、複雑な形状を有する部品の試作では、SKDフライス加工により微細な加工が可能となり、従来の方法に比べ大幅な時間短縮を実現しています。また、改良を重ねる工程においても、加工の再現性が高いため、安定した品質の試作品を繰り返し作成することが可能です。このように、SKDフライス加工は試作から製品化への橋渡しとして、その精度と効率性により、高い評価を受けています。
4-3. 技術文書における専門用語
SKDフライス加工は試作品を作る際に非常に効率的な方法であることが結論として挙げられます。この加工法は精密な作業が可能であり、複雑な形状や細部の再現も高い精度で行えるため、試作開発段階での利用が推奨されます。たとえば、新しい自動車部品の開発や医療機器のプロトタイピングにおいて、SKDフライス加工を利用することで、デザインの検証や機能テストを迅速に進めることができます。また、修正や変更が必要な場合も、加工の柔軟性が高いため短時間で対応することが可能です。このように、SKDフライス加工は試作品作りにおいて、その速度と精度の高さから選ばれる技術であり、2023年現在もその需要は高まる一方です。最終的に、この加工方法を選ぶことで、時間とコストの削減につながることが結論です。
5. SKDフライス加工試作での静的引張試験と脆性
5-1. 静的引張試験の概要
SKDフライス加工による試作品作成は、その高精度と迅速性から、2023年においても多くの企業にとって不可欠なプロセスです。特に、新製品開発の初期段階において、デザインや機能の検証を行うための試作品を作る際、SKDフライス加工は理想的な解決策となります。この技術は、複雑な形状の部品でも、短時間で精密な加工が可能であるため、試作品作りにおいて優れたスピードと品質を提供します。例えば、自動車産業や航空機産業では部品の試作に際し、SKDフライス加工を用いて実際の運用環境を模倣した試作品を迅速に製作し、性能評価を行っています。これにより、市場投入前の製品調整や改善が容易になり、研究開発のサイクルを加速する効果があります。結論として、SKDフライス加工は試作品を作成する際の完璧なガイドであり、製品開発をより早く、効率的に進めるための鍵となるでしょう。
5-2. SKDフライス加工試作品の脆性評価
SKDフライス加工を用いた試作品作成は、その優れた精度と迅速性で注目を集めています。加工における詳細なデザインの再現性に優れ、複雑な形状の試作にも適しているため、多くの産業分野で利用されているのです。例えば、自動車産業では、新型部品の試作にSKDフライス加工が用いられることが一般的です。これにより、試作段階でのデザイン修正が容易になり、時間とコストの削減に貢献しています。さらに、SKDフライス加工では、仕上がりの表面品質が高く、これが最終製品の品質向上に直結しています。総じて、SKDフライス加工は試作品作成における信頼性の高い技術であり、精密な試作が求められる現代の製造業にとって不可欠な加工方法であると言えるでしょう。
5-3. 脆性に関するよくある質問と回答
SKDフライス加工は、試作品を作成する際の最適な選択肢の一つです。まず、SKDフライス加工を利用することで、試作品の精度が高く、複雑な形状でも正確に加工することが可能になります。特に、独自の設計や特殊な部品の加工を要する場合には、この技術の精度と柔軟性が最大の強みとなります。具体例として、自動車産業や航空宇宙産業で用いられる部品では、極めて高い精度が求められ、SKDフライス加工はその要望を満たすことができます。また、試作品を迅速に製作することもSKDフライス加工の利点です。短期間でデザインから製品へと移行できるため、市場への導入が速やかになり、競争上の優位性を確保することが可能です。総じて、SKDフライス加工は、高い精度、迅速な製造、複雑なデザインへの対応という点で試作品の製作には欠かせない手法であり、その利用はこれからも一層広がっていくことでしょう。
まとめ
SKDフライス加工を利用した試作品の製作には、最新の技術と知識が必要です。2023年版の完全ガイドでは、最新の機械とソフトウェアを活用することで、効率的かつ高品質な試作品を作ることができます。さらに、適切な材料の選択や加工条件の最適化によって、製品の品質向上とコスト削減が実現できます。試作品の成功には正確な設計と機械加工の専門知識が不可欠です。
【専門家推薦】SKDフライス加工での試作プロセス徹底解説
製造業における試作プロセスの重要性は計り知れません。特に、SKDフライス加工を行う際の試作プロセスには専門的な知識や技術が必要です。そこで、今回は専門家によるSKDフライス加工での試作プロセスについての徹底解説をご紹介します。SKDフライス加工とは何か、試作プロセスのポイント、成功するためのコツなど、これからSKDフライス加工を行う方々に役立つ情報が満載です。ぜひご覧ください。
1. SKDフライス加工試作入門
1-1. SKDフライス加工とは
SKDフライス加工は、精密な試作品を作成する際に推奨される加工方法です。この技術は、特別な工具を用いて材料を削り出すことにより、高い精度と複雑な形状の部品を製造することが可能です。例としては、自動車や航空機の部品製造において、その利点が特に顕著です。試作段階では、しばしば細かな修正や機能の検証が必要になるため、SKDフライス加工を用いることで、迅速に高品質な試作品を得ることができます。加えて、少量生産にも適しており、コストと時間の節約に繋がるため、専門家からも推奨される技術なのです。最終的に、SKDフライス加工は試作プロセスを効率化し、製品開発の成功率を高める重要な役割を果たします。
1-2. 試作の基本概念
SKDフライス加工における試作は、高精度な部品製造に不可欠な工程です。試作を行う主な理由は、設計段階での図面通りの部品が製造可能かどうかを確認し、必要に応じて改善を加えるために他なりません。特に、SKD(スチール鋼の一種)を用いたフライス加工では、材料の硬度や切削条件が製品の品質に大きく影響するため、試作を通じてこれらの要因を事前に検証することが重要です。例えば、自動車部品の製造においては、極めて狭い公差での加工が求められることが多く、試作によってこれらの公差を確実に実現できるかをテストします。また、試作段階では、材料の選定から加工パラメータ、工具の選択に至るまで、最適な条件を見極めることが可能です。このようにして、試作は最終製品の品質向上に寄与し、結果的に生産効率の向上にも繋がるのです。
2. 技能検定とSKDフライス加工試作
2-1. 技能検定の概要
SKDフライス加工の試作は製品開発の上で欠かせない工程であり、専門家による徹底解説が推奨されます。この過程において試作の重要性は大きく、適切な方法で行われた場合、最終的な製品の品質向上に大いに寄与します。SKDフライス加工における試作では、材料の特性を理解し、加工条件を最適化することが重要です。例えば、専用の工具選びや切削条件の調整など、細かい配慮が求められる作業が多数存在します。これらの過程を経て、より精度の高い製品を作る土台を築くことができます。そのため、専門家の推奨する試作プロセスに従うことは、製品の品質を左右するだけでなく、コストの削減や製造時間の短縮にも繋がります。最終的には、この試作プロセスが良質な製品生産の鍵となるため、SKDフライス加工における試作の重要性は非常に高いと言えるでしょう。
2-2. SKDフライス加工試作の検定基準
SKDフライス加工での試作は、精密な部品製造において不可欠な工程です。このプロセスによって、設計の実用性や製品の機能性を事前に検証することが可能となります。試作を行う際には、加工精度や材質の選定、表面処理の質などに特に注意を払う必要があります。具体的には、SKD鋼を使用した加工では硬度や耐摩耗性が求められるため、こうした特性が試作品にもしっかりと反映されるようにします。加えて、試作を通じて製造コストの見積もりや工程の最適化も行われ、量産への移行をスムーズに行うための基盤を作ります。そのため、SKDフライス加工試作の段階では、細部にわたる検証が不可欠であり、最終製品の品質向上を実現するための重要なステップとなるのです。
3. SKDフライス加工試作の企画段階
3-1. 設計思想の理解
SKDフライス加工を用いた試作は、精密な製品制作には欠かせないプロセスです。この方法は、製品の設計思想を理解する上で、非常に効果的な手段であると専門家は推薦しています。試作を行うことで、仮想環境だけでは見えてこない物理的な問題点を発見し、設計に反映させることが可能です。例えば、SKDフライス加工を使った試作を通じて、材料の耐久性や加工時の挙動などの実際のデータを得ることで、より実用的な製品設計へと繋がります。そして、試作を繰り返すことで、最終的な製品の品質を高め、市場への導入リスクを低減させることができます。したがって、SKDフライス加工による試作は製品開発において、重要なプロセスと結論づけることができるのです。
3-2. 材料選定の重要性
SKDフライス加工における試作は、製品開発の初期段階で不可欠なプロセスです。なぜなら、試作を行うことで材料の性質や加工の精度を事前に検証できるからです。特に、SKDフライス加工では、耐摩耗性や強度など、材料に求められる特性が高いため、適切な材料選定が成功の鍵を握ります。例えば、耐久性に優れるSKD11や加工性が良好なSKD61など、用途に合わせた素材選びが重要です。試作を行うことで、設計通りの性能を発揮するか、またコストパフォーマンスは適切かなど、多くのデータが得られます。これらの情報は量産に移る前の改善点の発見や、製品の信頼性を高めるために不可欠です。したがって、SKDフライス加工における試作の段階で、正確な材料選定を行うことが非常に重要です。
4. カット治具企業の選び方
4-1. 治具企業の評価基準
SKDフライス加工での試作は高品質な製品開発に必須であると専門家は推奨しています。試作プロセスにおいてSKDフライス加工を選択する理由は、その精密さと効率性にあります。具体例として、加工精度が要求される自動車部品や医療機器の試作には、この技術が特に有効です。SKDフライス加工は、複雑な形状や細かいディテールが必要なパーツでも、精度高く仕上げることが可能です。試作における正確性は、量産時のコスト削減や時間の短縮、品質の向上に直結するため、この工程を軽視するわけにはいかないのです。結論として、SKDフライス加工は試作段階での品質保証と効率化を実現し、成功に導くために推奨される選択肢の一つです。
4-2. 実績と信頼性
SKDフライス加工は精密加工が可能であり、試作プロセスにおいて、専門家から推薦される理由がいくつかあります。まず、フライス加工は幅広い材料に対応し、複雑な形状も実現可能です。そのなかでも、SKD鋼は硬度が高く耐摩耗性に優れているため、精度を要する試作に適しています。たとえば、自動車部品や金型の試作でSKDフライス加工が選ばれることが多いです。これらの部品は、耐久性と精度が非常に重要とされており、SKDフライス加工はそれを満たすからです。結果として、試作段階でのコスト削減と時間短縮を実現し、製品開発の効率化に貢献します。以上の理由から、SKDフライス加工は試作プロセスにおいて不可欠な技術と言えます。
5. SKDフライス加工試作の加工工程
5-1. 加工設備の選定
SKDフライス加工における試作は、製品開発の初期段階において極めて重要です。この過程においては、加工設備の選定が成功の鍵を握ります。まず、高い精度と複雑な形状の加工が可能な機械を選ぶことが求められます。例えば、多軸制御が可能なフライス盤は、複雑な曲面加工が要求される試作品に非常に適しています。また、加工時間の短縮が可能な機械を選ぶことはコスト削減にも繋がります。さらに、試作段階では材料の無駄を極力抑えたいため、材料の利用効率が高い機械の選択も重要です。実際に、正確な試作品を迅速に作り出すことで、製品開発をスムーズに進行させることができ、最終的な製品の品質向上に寄与します。したがって、SKDフライス加工での試作における加工設備の選定は、製品開発の成功に不可欠な要素です。
5-2. 加工プロセスの最適化
SKDフライス加工を用いた試作は、高精度かつ効率的な生産を可能にします。試作プロセスにおいて最適化は非常に重要であり、これによってコスト削減と時間短縮を実現できます。例えば、SKDフライス加工では最新のCAD/CAM技術を組み合わせることで、精密な部品を短時間で製作可能です。また、試作段階で発生する可能性のある問題を早期に発見し修正することで、最終製品の品質向上につながリます。これは、金型の制作や複雑な形状の加工において、特に威力を発揮します。最適化されたSKDフライス加工プロセスを取り入れることで、試作品の精度を高めると同時に、市場への導入速度も向上します。結論として、SKDフライス加工は試作プロセスの質と効率を飛躍的に向上させるための鍵となる技術であると言えます。
6. 技能検定の受験案内
6-1. 受験資格と申請方法
SKDフライス加工において試作は極めて重要なプロセスです。その理由は、試作によって設計の有効性を確認し、量産前に問題を発見し解決することができるからです。例えば、SKDフライス加工で作成した部品の寸法精度や表面処理に問題がないか、試作を通じて検証します。この段階での調整が、後の生産効率を高め、コストを削減することにもつながります。また、試作はクライアントとのコミュニケーションを密にし、最終製品の質を向上させるためにも不可欠です。したがって、SKDフライス加工の試作段階には、十分な時間とリソースを割くことが推奨されます。
6-2. 試験内容と対策
SKDフライス加工は、試作品を製作する上での精度と効率を高める重要なプロセスであり、専門家もその利用を推奨しています。試作段階での品質が最終製品のクオリティに直結するため、このプロセスは特に重要です。具体的には、SKDフライス加工では、硬質材料を使用することで、耐久性や精度の高い試作品を製作できるのです。日本におけるSKDフライス加工による試作は、自動車や電子機器の部品製造など、多岐にわたる産業で活用されています。精密な部品が求められるこれらの産業で、SKDフライス加工はその精度の高さから、高く評価されています。最終的に、SKDフライス加工による試作プロセスは、品質の向上、コストの削減、効率的な生産スケジュールの遵守に寄与するため、製品開発の初期段階において不可欠な工程であると結論付けられます。
7. 最新情報とトレンド
7-1. SKDフライス加工試作の新技術
SKDフライス加工における試作段階は、製品開発の成功に不可欠な工程です。この工程で、デザインの妥当性が検証され、実用化に向けた改善点が見つかるからです。例えば、自動車部品の試作にSKDフライス加工を使用する場合、材質の特性を活かしつつ、精密な部品を効率よく削り出すことが可能です。実際に、SKDフライス加工を利用することで、耐摩耗性や強度といった必要条件を満たした部品の試作がスムーズに進むことが多くの企業によって報告されています。また、試作を重ねることで、製品の高度化にもつながります。結論として、SKDフライス加工は試作プロセスにおいて制度と効率の両面で優れており、革新的な製品開発に貢献する技術と言えるでしょう。
7-2. 業界ニュースと更新情報
SKDフライス加工は精密な試作を必要とする産業において、その高い対応力と効率から専門家に推薦されています。フライス加工による試作は、製品開発段階でのデザインや機能の検証に不可欠であり、SKDのような硬い材料を使用した加工は、耐久性や耐摩耗性に優れた部品を生み出すために特に重要です。例えば、自動車や航空機の部品製造では、厳しい環境下での使用に耐える強靭な材料が必要とされ、SKDフライス加工での試作品はその基準を満たす部品開発を可能にしています。このプロセスを理解し適用することで、効率的かつ効果的な試作が行え、結果として製品の市場への導入速度を高めることができます。そのため、SKDフライス加工は試作分野において推薦される技術となるのです。
まとめ
SKDフライス加工は試作品を作るための理想的な方法です。専門家によると、適切な材料と工具を使用することで、高品質な試作品を効率的に製作することが可能です。また、適切なプロセスを選択することで、製品の完成までの時間を短縮し、コストを削減できます。SKDフライス加工を使用することで、試作品の品質と効率を両立させることが可能です。
試作工程をスムーズに!SKDフライス加工の最適な条件とは
試作工程をスムーズに進めるためには、SKDフライス加工の最適な条件を知ることが重要です。試作品を効率的に製造するためには、材料や工具、加工条件などを適切に選定する必要があります。本記事では、SKDフライス加工の基本から試作に最適な条件までを詳しく解説します。試作工程を円滑に進めたいと考えている方におすすめの情報です。
1. SKDフライス加工試作の基本理解
SKDフライス加工は、試作工程をスムーズに進めるために最適な条件選びが欠かせません。試作段階では、材料の性質や加工の精度を確かめることが重要であり、特にSKD材は硬度が高いため適切な工具選びと条件設定が必要です。例えば、カット速度や送り速度、工具の種類や冷却剤の使用がその条件に当たります。適切な条件下で加工を行うことで、SKD材の持つ特性を活かしながら、精度の高い部品作りが可能となります。また、無駄なトライアルを避け、コストや時間の削減にもつながります。最適なフライス加工条件を見極めることは、試作の効率化だけでなく、製品開発の成功にも直結するため、非常に重要なプロセスと言えるでしょう。
2. SKDフライス加工試作の条件設定
SKDフライス加工における試作工程は、効率的な製品製造に不可欠です。この段階で最適な条件を見極めることが、コスト削減と品質向上に直結します。特にSKD材は硬度が高く加工が難しいため、適切な工具選定と切削条件が求められます。例えば、フライスの刃の材質には耐久性のある超硬タイプを選ぶこと、また切削速度や送り速度を材質の特性に合わせて調整することが効果的です。さらに、ラフィングとフィニッシングの工程を明確に分け、それぞれに最適化された条件を適用することも重要です。結論として、試作工程での細かな条件設定は、最終製品の品質を左右すると同時に、大量生産に移行する際のスムーズな過渡を実現するために不可欠なステップとなります。
3. SKD11旋盤加工の精度向上戦略
試作段階でのSKDフライス加工をスムーズに進めるためには、最適な加工条件の見極めが重要です。SKD材は硬度が高く加工が難しいため、正確な工具選定と速度設定が求められます。例えば、耐摩耗性に優れた超硬工具を使い、切削速度を抑えることが一つの方法です。さらに、試作では、小ロット生産に対応可能な柔軟性も必要とされます。そこで、高速で精度の高い加工が可能なマシンを選択し、細かい部品形状にも対応できるような工夫を施すことが肝心です。これにより、試作段階でのコストと時間の削減につながります。結論として、SKDフライス加工では、適切な工具と加工速度の選定、柔軟性を持った機械設備の利用が、スムーズな試作工程への鍵となります。
4. 試作・テスト加工部品の種類と選定
試作工程の成功は、製品開発の鍵を握る要素の一つです。SKDフライス加工において最適な条件を見極めることで、効率的な試作が実現可能になります。たとえば、SKDの硬度や熱処理状態に合わせた切削速度の調整が重要であり、材料に応じた刃の選定や冷却液の使用も加工品質を左右します。実際の加工例では、精密な部品製造において、適切な工具選択とパラメータ設定が試作の精度を向上させました。最終的には、これらの要因を組み合わせたテストにより、製品の信頼性が高まり、市場導入までの時間も短縮されます。試作工程の最適化は、時間とコストの節約に直結し、競争力のある製品開発を実現するために不可欠です。
5. 超硬合金のSKDフライス加工試作のテクニック
SKDフライス加工における試作工程は、効率よく高品質な製品を生み出すために最適な条件が求められます。SKDとは、耐熱性や耐摩耗性に優れた特殊な鋼のことで、加工が困難な材料です。そのため、試作段階で正しい条件を見極めることが極めて重要です。具体的には、カッターの選定や切削速度、送り速度、冷却方法など、多くの要素が最終品質に影響します。例えば、SKDの硬度に合わせた超硬質のカッターを使用し、相応の切削速度と送り速度を組み合わせることが重要です。また、適切な冷却剤を使用することで、切削時の熱ダメージを防ぎ、工具の寿命を延ばすことができます。加工条件を適切に管理することで、試作工程は効率的に進み、コスト削減にも繋がるため、製品の品質向上と併せて生産性も向上するでしょう。
6. 機械加工技能検定試験への道
試作工程をスムーズに行うためには、SKDフライス加工の最適条件の理解が不可欠です。結論から言うと、適切な工具選択、切削速度、送り速度、クーラントの使用が重要です。SKDは耐摩耗性が高い鋼材であり、適切な加工条件により工具の摩耗を抑えることができ、長期にわたる精密な試作が可能になります。たとえば、硬い材料には切れ味の良い工具を選び、適切な切削速度を保つことで、精度の高い加工を実現できます。また、送り速度を適切に制御し、クーラントを適切に使用することで、加工中の熱ダメージを防ぎ、品質の安定を図ることができます。最後に再度強調しますが、SKDフライス加工におけるこれらの条件は、試作品の品質を左右するだけでなく、コスト削減や生産効率の向上にも直結します。
まとめ
SKDフライス加工において試作工程をスムーズに進めるためには、適切な加工条件の設定が重要です。適切な切削速度や送り速度、切削深さなどを適用することで、材料の特性に合った最適な加工状態を実現できます。また、工具の選定も重要であり、試作品に最適な工具を選ぶことで加工精度や効率を向上させることが可能です。試作工程でのスムーズな加工を目指す際には、これらの条件を適切に設定し、適切な工具を選定することが重要です。
【試作向け】SKD材を使ったフライス加工で知っておくべきポイント
SKD材を使ったフライス加工は、製造業界で重要な役割を果たしています。では、試作向けのフライス加工では、何を知っておくべきでしょうか?本記事では、SKD材の特性やフライス加工のポイントについて解説します。試作における効率的な加工方法や注意すべき点についても徹底的に紹介します。試作向けのフライス加工に関心がある方は、ぜひ本記事をご覧ください。
1. SKD フライス加工 試作とは?
SKD材を用いたフライス加工は、試作品製作において重要なポイントがあります。まず、SKD材は硬度が高く耐摩耗性に優れているため、精密な加工が可能です。しかし、その硬度ゆえに工具の選定や加工条件の設定が重要となります。例えば、SKD材専用の超硬工具を使用したり、切削速度を適切に調整することが要求されます。また、試作段階では、加工に際して発生する熱による材料の変質や寸法の精度に影響を与えないよう、冷却方法にも注意を払う必要があります。結論として、SKD材を用いたフライス加工には特有の知識と技術が要求されるため、試作品の品質を確保するためには経験豊富な加工技術者と適切な加工条件が不可欠です。
2. SKD フライス加工 試作の基礎知識
試作におけるSKD材のフライス加工は、その特性を理解していなければ困難な作業となります。SKD材は耐摩耗性に優れており、射出成型の金型などによく使用されています。しかし、この硬さが加工の難易度を上げる原因にもなっています。具体的には、SKD材を加工する際は、カッターの選定に注意を払い、切削条件を適切に設定する必要があります。たとえば、切削速度を遅くし、冷却液を多めに使用することで、材料を効率的に削れる場合があります。また、刃先が丸みを帯びたエンドミルを使用することで、刃物の損傷リスクを抑えられます。試作段階では小ロットでの加工が多いため、加工パラメータの最適化は試行錯誤が不可欠です。結論として、SKD材のフライス加工は、材料の性質を熟知し、適切なツールと加工条件の選定を行うことで、成功に導くことができるでしょう。
3. SKD11材料の旋盤加工の概要
SKD材を使ったフライス加工は、試作品の製造において重要なポイントがいくつか存在します。SKD材料は硬度が高く耐摩耗性に優れているため、工具の選定や加工条件の設定に特に注意を要します。例えば、カッターの材質はSKD材の硬さに耐えうるものを選び、適切な切削速度や送り速度を見極めることが必要です。また、切削液の使用も重要で、発熱を抑えることで切削精度の向上にも繋がります。適切なフライス加工を行うことで、試作品の精度を保ちつつ、工具の寿命を延ばし、コスト削減にも繋がるため、これらのポイントを押さえることが非常に重要です。最終的に、より効率的かつ効果的な試作品の製造が可能となります。
4. SKD フライス加工 試作の加工性比較試験
SKD材を用いたフライス加工は試作において重要な工程の一つです。まず、SKD材は耐摩耗性が高く、工具の摩耗を抑えながら精密な加工が可能である点が利点です。そのため、試作段階での加工精度を高めるためには最適の材料であるといえます。具体例として、金型の試作においてSKD材を使用した場合、仕上がりの品質が良く、耐久性の面でも優れています。また、SKD材は硬度が高いため加工には専門の技術が求められますが、これをマスターすることで、より複雑な形状の加工にも対応可能となります。結論として、SKD材を使用したフライス加工は、試作において精度と品質の向上を実現するため、知っておくべき重要なポイントが多いため、適切な材料選定と加工技術の習得が必須です。
5. NC旋盤とNCフライスを用いたSKD フライス加工 試作
SKD材を使用したフライス加工は、精密な試作品製造において欠かせない工程です。SKD材は硬く耐摩耗性に優れているため、切削工具の選定には特に注意が必要です。例えば、加工する際には超硬質合金やコーティングされた工具を選択し、切削速度や送り速度も材質に合わせて適切に設定する必要があります。具体的には、SKD材には低い切削速度で加工を開始し、徐々に最適な条件を見極めることが推奨されます。さらに、冷却液の使用は切削熱を効果的に抑制し、材料の変質を防ぎつつ寸法精度を維持するのに役立ちます。このような点に留意してフライス加工を行うことで、試作品の品質と製造効率が大幅に向上します。総じて、SKD材のフライス加工は適切な工具選びと条件設定が成功の鍵となるのです。
6. SKD フライス加工 試作による組立工数の削減
試作向けのSKD材を使ったフライス加工は、組立工数の削減という大きな利点をもたらします。SKD材は耐摩耗性に優れ、精密な加工が可能です。このため、精度の高い試作部品を製造する際には、SKDを用いることで、組立てや調整にかかる手間を大幅に減少させることができます。例えば、金型製作においてSKDを選択することで、長期間の使用に耐えうる高い耐久性を保ちつつ、細部まで精緻な加工が行え、結果的に調整や修正の必要性が低減します。これは、短期間での試作品の提供が求められる開発スピードが重視される現代において、大きな経済的なメリットに繋がります。したがって、時間とコストの削減を実現するためにも、SKD材を使ったフライス加工は試作段階での選択肢として非常に有効であると結論づけられます。
7. マシニング加工とフライス加工の違い
SKD材を使ったフライス加工は試作品製作において重要な役割を果たします。この加工は、耐摩耗性や耐衝撃性に優れるSKD材の特性を活かし、精密な部品を製作する際に不可欠です。具体的には、金型の試作においてSKD材を加工することで、実際の量産前に多くのテストを経て品質の高い製品が生まれます。そのためには、高い切削抵抗を持つSKD材に適したフライス加工機の選定や、刃の摩耗を最小限に抑えるために適切な切削条件を見極めることが重要です。例えば、適切な切削速度、送り速度、切り込み量を見極めることにより、SKD材の特性を最大限に活かした高品質の製品が得られるのです。結論として、試作向けのフライス加工では、加工材の特性を理解し、それに適した機械や条件を選択することが最終製品の品質を左右すると言えます。
8. SKD フライス加工 試作における注意点
SKD材を使用したフライス加工は精度が要求される試作において、その特性を理解することが成功へのカギとなります。SKD材は耐摩耗性に優れている一方で加工が難しい特徴を有しています。特に、試作段階では寸法の精度が極めて重要になりますが、SKD材は硬度が高く、工具の選定や切削条件の設定に注意が必要です。具体例としては、刃先が摩耗しにくい超硬エンドミルの使用や、適切な切削速度の選択が挙げられます。また、熱処理前後での寸法変化にも注意を払い、加工計画を慎重に立てることが求められます。結論として、SKD材を用いたフライス加工では材料の特性を深く理解し、適切な工具選びと加工条件の慎重な設定を行うことで、高品質な試作品の作成が可能になります。
9. SKD フライス加工 試作の未来展望
SKD材を使用したフライス加工は試作品製作において重要な要素です。これは、SKD材が優れた硬度と耐摩耗性を持つため、精密な部品製造に適しているからです。例えば、金型の試作においてSKD材はその耐久性の高さから選ばれることが多いです。このような加工を行う際には、材料の特性を十分に理解し、適切な切削条件を選定することが重要です。適切な工具選びや冷却剤の使用も、品質を保つ上で欠かせません。最終的に、SKD材を使ったフライス加工により、優れた試作品を製造することができるので、製造業のニーズに応えることが可能になります。
10. 1-1. SKD フライス加工 試作のメリット
SKD材を使ったフライス加工は、試作品製作において重要な役割を果たします。その最大の理由は、SKD材が優れた加工性と高い耐摩耗性を兼ね備えている点にあります。例えば、複雑な形状の部品を試作する際、SKD材は均一な質感を保ちつつ精度高く加工することが可能です。また、耐久性が求められる部品にとって、SKD材は試作段階での強度試験にも耐えうる材料です。これらの特性から、SKD材は自動車や航空機の部品など、精密かつ強靭な製品の試作にしばしば用いられています。最終的には、SKD材のフライス加工を行うことにより、実用段階への移行前に高品質な試作品を得られるため、製造プロセス全体の効率化にも繋がります。
11. 1-2. SKD フライス加工 試作のデメリット
試作向けにSKD材を使ったフライス加工には、特有の注意点があります。SKD材は硬度が高く耐摩耗性に優れているため、刃物の選定や切削条件の設定が非常に重要です。例えば、硬い材料を加工する際は、切れ味が良く耐久性のある超硬合金製の工具を使用することが一般的です。また、加工時の送り速度やスピンドル速度も適切に管理し、過度な負荷がかからないように気をつける必要があります。これらの点を怠ると、工具の早期摩耗や破損、加工精度の低下を招くことになります。したがって、試作段階ではこれらの条件を十分にテストし、最適な加工条件を見極めることが重要です。SKD材の特性に合わせた適切な加工方法を選択することで、高品質な試作品を製造することが可能となります。
12. 2-1. SKD フライス加工 試作の材料選定
SKD材を使ったフライス加工は試作段階において重要な点がいくつかあります。SKD材は工具鋼として広く使用されており、耐摩耗性や硬度が高いことから試作に適しています。しかし、その硬さゆえに加工には特別な注意が必要です。具体的には、適切な切削速度の選定や冷却液の使用が挙げられます。これらを適切に管理することで、精度の高い加工が可能となり、試作品の品質を保証することができます。また、工具の摩耗を防ぐための工夫も必要です。試作に際しては、これらのポイントを踏まえた上で、SKD材を用いたフライス加工を行うことが推奨されます。最終的に、これらの注意点を守ることで、耐久性と品質を兼ね備えた試作品を作り出すことができるのです。
13. 2-2. SKD フライス加工 試作の工具選定
SKD材を使ったフライス加工は試作品製作において重要な要素です。この材料は硬度が高く、耐摩耗性に優れているため、精密な加工が求められる場合に適しています。しかし、その硬度のために適切な工具選定が必須となります。例えば、超硬合金やコーティングされた工具を使用することで、SKD材の加工性を高めることができます。また、切削条件の最適化も重要です。速度や送り、冷却剤の使用によっても加工の仕上がりが大きく変わります。試作段階では、これらの条件を小さなステップで調整し、最適な条件を見つけ出す作業が不可欠です。結論として、SKD材を使用したフライス加工では、適切な工具選定と切削条件の調整により、高品質な試作品を製作することが可能です。
14. 3-1. SKD11材料の特性
SKD材を使用したフライス加工は、試作に際して多くの優れた特性を提供します。特にSKD11材料は、優れた耐摩耗性と硬度を備えており、精密な加工が必要な部品製造に適しています。その理由は、SKD11は高炭素・高クロムの合金工具鋼であり、治療後に60HRC以上の硬度を達成できるためです。例えば、金型のコアやスライダーなどの部品にSKD11が用いられることが多いです。これらの部品は繰り返しの負荷に耐える必要があるため、SKD11のような材料の使用が求められます。試作段階でのSKD材の選択は、最終製品の品質を大きく左右するだけでなく、製造過程におけるコスト効率と耐久性の向上にも寄与します。最終的には、SKD材を使用することで、高品質かつ長寿命な部品の製造が可能となるのです。
15. 3-2. SKD11材料の旋盤加工技術
SKD材を用いたフライス加工は試作において重要な工程の一つです。SKD材は耐摩耗性や硬度が高いため、工具の選択や加工条件の設定が試作の成功を大きく左右します。例えば、SKD11は一般的な金属加工用の工具で加工する際には、刃先の耐久性を考慮した選択が必要です。また、加工速度や送り速度、切削液の使用など、細かな条件設定が求められる材料です。特に試作段階では、これらの条件を試行錯誤しながら最適化することが、コスト削減や効率的な時間管理に繋がります。結論として、SKD材を用いたフライス加工は高い技術と正確な条件設定を要求される作業ですが、適切に対応することで試作の質を高めることが可能です。
16. 4-1. 加工性比較試験の目的
SKD材を使用したフライス加工は、試作において非常に重要な役割を果たします。SKD材は特に硬質で耐摩耗性に優れているため、正確な試作品を製造する際に適しています。フライス加工の際には、SKD材の硬度を考慮した工具選択や、加工速度、送り速度といった条件の最適化が必要です。たとえば、硬質材を加工する際に用いられる超硬工具は、SKD材の加工にも効果的ですが、工具の消耗も早まるためコスト管理にも留意する必要があります。また、試作段階では多くの場合、少量多品種の加工が求められるため、工具の交換作業や機械のセットアップ変更が頻繁になることを想定し、効率の良い作業フローを構築することが重要です。結論として、SKD材のフライス加工は、試作品の品質を高める一方で、工具選択や作業フローに特別な注意が必要な加工方法であると言えるでしょう。
17. 4-2. 加工性比較試験の方法
SKD材を使用したフライス加工は、その特性を理解しておくことで試作段階の効率を高めることができます。SKD材は硬質で耐摩耗性が高いため、加工には特別な注意が必要です。たとえば、切削速度の選定は材質の硬さに合わせて慎重に行う必要があり、適切な切削油の使用も加工精度を保つ上で重要です。さらに、刃の摩耗を防ぐために適した切削工具を選定することが不可欠です。日本における実例として、SKD材のフライス加工にはしばしば超硬合金が用いられ、これにより一貫した加工品質の維持が可能になっています。結論として、SKD材を用いたフライス加工では材料の特性に合わせた機械設定と工具選択が試作の成功への鍵となります。
18. 5-1. NC旋盤加工の基本
SKD材を使用したフライス加工は試作品づくりにおいて重要なポイントがあります。SKD材は硬度が高く加工が困難な材質であるにも関わらず、その耐摩耗性や強度から、精密な試作品を要求される分野でよく利用されます。フライス加工では、SKD材の特性に合わせた適切な工具選びが必要不可欠です。例えば、超硬材料やコーティングされた工具を使用することで、耐久性を保ちながら加工精度を高めることができます。また、工具の進行速度や回転数の調整も、SKD材加工の際には欠かせない要素です。適切な設定により、材料の熱変形を最小限に抑え、試作品の品質を保つことが可能になります。結論として、SKD材に適した工具選びと加工条件の最適化が、高品質な試作品を作り出す上での鍵となるのです。
19. 5-2. NCフライス加工の基本
SKD材を使用したフライス加工は、試作品の製造において重要なポイントがいくつかあります。まず、SKD材は硬度が高く耐摩耗性に優れているため、切削工具の選定には特に注意が必要です。適切な刃物と速度を選ぶことで、精度の高い加工が可能になります。例えば、超硬合金のエンドミルはSKD材の加工に適しており、長寿命を保つことができます。更に、加工時にはSKD材の高温硬化を避けるために冷却液の利用が必須です。これにより、加工精度を損ねることなく、スムーズな試作が行えるでしょう。最終的に、これらのポイントを踏まえた上でフライス加工を行うことで、試作品の品質を保ちながら効率的な製造が実現するのです。
20. 6-1. 削り出し加工によるコスト削減
SKD材を使用したフライス加工は試作フェーズにおいて、そのコストパフォーマンスと加工性から注目されています。SKD材とは、耐摩耗性や靭性に優れた合金工具鋼のことで、フライス加工での利点が多い材料です。具体例として、炭素鋼に比べてSKD材は硬度が高く、精密な試作品製造に適しており、長期間に渡って安定した寸法精度を保てるためです。また、SKD材は加工後のサーマル処理によってさらに強度を増すことができ、試作段階での品質確認や耐久テストにも適しているため、幅広い産業での利用が期待されます。このような理由から、試作品製造にSKD材を使用するフライス加工は、効率的かつ経済的な選択と言えるでしょう。
21. 6-2. 加工精度と組立工数の関係
SKD材を使用したフライス加工は、試作段階での精度とコストのバランスを考慮に入れた加工方法です。SKD材とは、耐摩耗性に優れた工具鋼を指し、試作においてはその加工性が非常に重要になります。まず、SKD材は硬度が高いため、切削工具への負荷が大きくなることが予想されます。これを踏まえ、刃先の選択や切削条件の設定が重要となるのです。例えば、超硬合金やコーティングされた工具の使用は、摩耗を減らし長寿命を実現するために効果的です。また、SKD材のフライス加工では冷却液の選択もポイントであり、適切な冷却液は材料の熱変形を防ぎ、加工精度を高める結果に繋がります。最後に、試作段階での高精度を実現するためには、これらの加工条件を綿密に検討し、工数とのバランスを取る必要があります。SKD材を使ったフライス加工におけるこれらのポイントを押さえることで、試作品の品質向上とコスト削減が期待できるでしょう。
22. 7-1. マシニング加工の特徴
SKD材を使用したフライス加工は試作品の作成において重要な役割を果たします。SKDは耐摩耗性に優れ、硬度も高いため、精密な部品製造に適しているのです。試作品では、しばしば一貫した品質と特定の要件を満たす必要がありますが、SKD材料はこれらの要求を満たすのに役立ちます。特に、金型や高負荷を受ける部品の試作には、SKD材の利用が推奨されます。これらの部品は高い強度と耐久性を必要とし、フライス加工中の精度も求められるためです。例として、自動車産業や航空宇宙産業で使われる部品が挙げられ、これらの分野ではSKD材の特性が最大限に活かされます。結論として、試作品のフライス加工においてはSKD材の選択が重要であり、その優れた特性が多くの業界での信頼性の高い製品造りに寄与しています。
23. 7-2. フライス加工の特徴
フライス加工は、試作品の製作において広く採用される加工方法であり、SKD材を使用する際にはいくつかの重要なポイントがあります。SKD材は硬度が高く耐摩耗性に優れているため、精度の高い加工が可能です。しかし、その硬さゆえに、正しい切削条件の選定が不可欠です。例えば、切削速度や送り速度、カッターの材質と形状を適切に選ぶことが挙げられます。また、SKD材は加工時に発生する熱により焼き入れが進行する可能性があるため、冷却方法にも注意を払う必要があります。このような点を考慮することで、SKD材を使用したフライス加工は試作品製作においても高い品質を保ちつつ効率良く行うことができます。
24. 8-1. SKD フライス加工 試作の品質管理
SKD材を使ったフライス加工は試作品の製造において重要なポイントがいくつかあります。SKD材料は硬度が高く、耐摩耗性に優れているため、精度の高い加工が可能ですが、その加工には特別な注意が必要です。まず、適切な工具選定が不可欠であり、SKD材の硬さに耐えうる高品質なカッターを使用することが重要です。次に、正確な冷却が試作品の品質を左右します。冷却不足は工具の過度の摩耗や加工物の変形を引き起こす可能性があります。また、切削条件の最適化も欠かせません。切削スピード、送り速度、切り込み量を材料の特性に合わせて調整することで、精度の高い加工を実現し、試作品の品質を向上させることができます。まとめると、SKD材を使ったフライス加工では、適切な工具の選定、冷却方法の最適化、切削条件の調整により、高品質な試作品作りが可能です。
25. 8-2. SKD フライス加工 試作のトラブルシューティング
SKD材を使ったフライス加工にはいくつかの重要なポイントがあります。SKD材は耐摩耗性に優れているものの、加工時にはその硬さや粘りがトラブルの元となることがあります。特に試作段階では、これらの特性に注意しながら慎重に加工を進めることが求められます。例えば、適切な切削条件、工具の選択、冷却方法などを事前にしっかりと検討することが重要です。具体的には、SKD材の硬さに合わせた切削速度の設定や、耐摩耗性の高い工具の使用が挙げられます。また、加工時の熱影響を最小限に抑えるための適切な冷却手段の採用も不可欠です。これらの対策により、試作時のトラブルを未然に防ぎ、スムーズな加工を実現することができます。最終的には、これらのポイントに留意することで、SKD材を用いたフライス加工試作の成功に繋がるでしょう。
26. 9-1. 技術革新とSKD フライス加工 試作
SKD材を使ったフライス加工は試作品製作において欠かせないポイントがいくつもあります。まず、SKDとは耐摩耗性や耐熱性に優れた工具鋼の一種であり、高精度な試作品作りには最適な材料です。そのため、正しい加工方法と適切な切削条件を理解することが重要です。例えば、SKD材の硬度に合わせて適切な切削速度を選ぶことや、冷却剤を適切に使用することで、加工中の材料の変質を防ぎながら精度の高い加工が可能になります。さらに、試作段階ではしばしばデザインや仕様が変更されるため、SKD材を使ったフライス加工はその修正を容易にし、時間とコストの削減にもつながります。したがって、SKD材を用いたフライス加工は試作品製作において非常に有効であると結論づけることができます。
27. 9-2. 環境持続可能性とSKD フライス加工 試作
SKD材を使ったフライス加工は試作品製作において非常に重要なポイントがいくつかあります。SKD材は炭素工具鋼であり、優れた耐摩耗性と硬度を持っています。このため、試作段階で使用することには大きな利点がありますが、正しい知識と技術が不可欠です。例えば、SKD材は加工が困難な素材であるため、切削条件を適切に管理する必要があります。特に、切削速度や送り速度、刃先の冷却などは精密な加工に影響を与える重要な要素です。また、工具の選定においてもSKD材の特性に合わせたものを選ぶ必要があります。これらの点に注意して適切なフライス加工を行うことで、試作品の品質を確保し、最終製品に向けた開発がスムーズに進むことでしょう。
まとめ
SKD材を使ったフライス加工では、適切な切削条件や工具の選定が重要です。特に試作向けの場合、材料の性質や切削の安定性を考慮し、適切な切削パラメータを設定することがポイントです。加工精度や表面仕上げにも注意し、試作品の要求仕様に適した加工を行うことが重要です。
試作開始前に知っておきたい!SKフライス加工のメリットとポイント
もしもあなたがSKフライス加工に興味があるなら、この記事はきっと役立つ情報が盛りだくさんです。試作開始前に知っておきたい、SKフライス加工のメリットやポイントについて解説します。SKフライス加工はどのようなメリットがあり、試作においてどのようなポイントが重要なのか、それについて詳しく説明しています。あなたが効果的なSKフライス加工を行い、試作プロセスをスムーズに進めるための貴重な情報が満載です。
1. SK フライス加工 試作の基本概要
SKフライス加工は、精密な部品を製作する際に不可欠な加工方法であり、試作段階でその利点を理解しておくことが重要です。この加工法は、その高い精度と仕上がりの良さにより、多くの産業で採用されています。例えば、複雑な形状や狭い溝を持つ部品の加工において、SKフライス加工は非常に有効です。その理由は、SKフライス加工が多軸の動きを利用するため、難易度の高い形状も正確に加工できるからです。さらに、試作品を製作する際には、その正確性が製品の品質に直結するため、SKフライス加工は初期段階での品質確認にも役立ちます。最終的に、この加工方法を利用することで、時間やコストの削減に繋がる可能性があり、賢明な選択と言えるでしょう。
2. SK フライス加工 試作がもたらすメリット
SKフライス加工の試作には、多岐にわたるメリットが存在します。この加工方法は、精密な加工が可能で、複雑な形状や困難な材料にも対応できるため、幅広い産業で活用されています。例えば、自動車産業においては、エンジン部品や駆動系のコンポーネントの試作に頻繁に用いられています。これらの部品は高精度が要求され、SKフライス加工によってその要求を満たすことができます。また、試作段階での精密かつ迅速な加工は、製品開発のスピードアップにも繋がります。さらに、この技術は材料の無駄を最小限に抑えることができるため、コスト削減にも効果的です。最後に、試作を経て、問題点の早期発見や改善が可能になるため、最終製品の品質向上にも寄与します。SKフライス加工を試作段階から活用することは、製品開発の成功への重要な一歩です。
3. 信頼できるSK フライス加工 試作サービスの選び方
試作品の製作には多くの加工方法が存在しますが、SKフライス加工はその中でも特に優れたメリットを持ちます。精密な加工が可能である点が最大の利点であり、複雑な形状や微細な加工を必要とする部品に適しています。例えば、医療機器や自動車部品などの高精度が要求される分野では、SKフライス加工の精度の高さが重宝されています。また、SKフライス加工は短納期で試作品を製造することができ、市場の変化に迅速に対応することが可能です。このように、SKフライス加工は試作において優れた精度とスピードを兼ね備えており、製品開発の初期段階においてそのメリットを最大限に活かすことができるのです。
4. 職場での技能向上:SK フライス加工 試作の役割
SKフライス加工の試作は、高い精度と複雑な形状の部品製作においてそのメリットが顕著です。この技術がもたらす利点として、まず試作により、設計段階での想定と実際の加工品がどの程度合致するのかを確認できることが挙げられます。理由は、実際の加工プロセスを経ることで理論上の数値だけでは把握しきれない材料の挙動や加工時の課題を明らかにできるからです。例えば、SKフライス加工では、複雑な形状や狭い部分の加工が可能であり、さらには試作を通じてこれらの加工条件を最適化できます。結論として、試作は製品の品質向上に直結し、無駄なコスト削減にも寄与するため、製造開始前にその重要性を理解し、実施することが推奨されます。
5. テフロンと精密加工:SK フライス加工 試作の応用
試作品の製作においてSKフライス加工はその正確さと効率性で多くの製造業者にとって重要なプロセスとなります。この加工方法は、硬い材料でも高精度な部品を制作することが可能で、結果として製品の品質が向上するというメリットがあります。特に、複雑な形状や狭い溝を持つ部品において、SKフライス加工はその優れた能力を発揮します。例えば、自動車のエンジン部品や航空機のタービンブレードなど、精密さが要求される部品の製作には欠かせません。また、試作段階でSKフライス加工を用いることで、設計の見直しが必要な場合でも迅速に対応することが可能になります。これは、最終的な製品の市場導入をよりスムーズにし、開発サイクルを短縮する効果を持ちます。したがって、製品開発におけるSKフライス加工の利用は、効率的な試作を実現し、製品の品質向上に寄与することで、競争力のある製品づくりに不可欠です。
6. 難しい加工部材へのアプローチ:SK フライス加工 試作によるシミュレーション技術
SKフライス加工は、試作段階から多くのメリットを提供します。この加工技術は、複雑な形状や精密な部品も高い精度で製造することが可能で、特に難易度の高い加工に適しています。たとえば、航空宇宙や自動車業界で用いられる複雑な部品は、SKフライス加工によって精密に作り出されます。この技術は、試作品の品質を向上させるだけでなく、製造プロセスの最適化にも寄与し、結果として生産効率を高め、コスト削減に繋がる可能性があります。さらに、試作を通じてデータを収集し、最終的な製品設計を更に洗練させることもできます。したがって、SKフライス加工を試作段階で採用することは、製品開発の成功にとって非常に重要な要素と言えるでしょう。
7. 口腔用ドライジェリー製剤のSK フライス加工 試作による評価方法
SKフライス加工の試作を開始する前に、そのメリットを理解しておくことが重要です。SKフライス加工は、精密さと効率性が求められる金属加工技術の一つであり、複雑な形状や高い精度が必要な部品を製造する場合に特に有効です。例えば、航空機の部品や医療器具など、寸法の正確さが極めて重要なアイテムの加工に多く用いられています。SKフライス加工は、素材の硬度に関わらず、高速で正確な切削が可能で、仕上がりの品質を高めることができます。さらに、従来の加工方法と比較して加工時間を短縮できるため、コスト削減にも寄与します。試作段階でこの技術を採用することは、製品開発の初期コストを抑えつつ品質を担保する上で、非常に効果的な選択肢と言えるでしょう。したがって、SKフライス加工は、高品質かつコストパフォーマンスに優れた試作品を求める際に、強力な手段となります。
まとめ
SKフライス加工は高精度な金属加工が可能であり、試作品の製作に適しています。加工精度が高く、形状の複雑な部品も精密に加工することができます。また、素材によっては高速加工が可能なため、短期間で試作品を製作することができます。SKフライス加工を活用することで、試作開始前に必要な情報やメリットを把握し、効率的な試作品の製作を目指しましょう。
【技術者必見】試作品製作の成功率を高めるSKフライス加工のコツ
技術者の皆様に捧ぐ。試作品の製作において成功率を高めるための、SKフライス加工のコツをご紹介します。SKフライス加工とは何か、どのように機能するのか、そして試作品製作にどのように役立つのか、本記事では詳しく解説します。試作品の製作に悩む技術者の方々に参考になる情報が満載です。
1. SK フライス加工 試作の基本概要
SKフライス加工は精密な試作品製作において必要不可欠です。試作の成功率を高めるには、SKフライス加工の技術を習得することが重要であり、これにはいくつかのコツがあります。まず、適切な刃物の選択が必要不可欠です。材料の種類によって適した刃物を選ぶことで、加工時の精度が大幅に向上します。次に、切削条件の最適化も重要です。回転速度や送り速度を材料や形状に合わせて調整することで、無駄なバリの発生を防ぎ、仕上がりの品質を高めることができます。さらに、最新のCAD/CAMソフトウェアを用いることで、加工プロセスを効率化し、正確な試作品を素早く作り出すことが可能です。これらのポイントを押さえることで、試作品製作の成功率は格段に向上し、技術者としての価値も高まるでしょう。
2. SK フライス加工における材料の選定
SKフライス加工での成功は、適切な材料選定に大きく依存します。加工精度や仕上がりの質を高めるには、用途に応じた材料選びが不可欠です。例えば、高硬度の材料は耐久性に優れている一方で加工には高い技術が要求されます。また、アルミニウム合金のような軽量かつ加工しやすい材料は、形状が複雑な試作品製作に適しています。さらに、材料の物性に適した切削条件を選ぶことも重要であり、これによりツールの摩耗を減らし、コスト効率も向上させることができます。最終的に、材料に見合った工具や設備を選び、試作品の品質を確実にすることが、SKフライス加工の成功へのカギと言えるでしょう。
3. SK フライス加工の主要な工程
SKフライス加工においては、試作品の成功率を上げるコツがあります。主に、加工精度の向上、加工時間の効率化、そして材料の無駄遣いをなくすことが、成功への鍵です。例えば、設計段階でのシミュレーションを徹底することで、加工前に問題点を発見しやすくなります。また、最適な工具選びや、切削条件の事前設定により、精密で効率的な加工が可能となり、結果的にコスト削減にも繋がるでしょう。さらに、材料を上手に利用して無駄を省くことで、試作品だけでなく量産品においてもコストパフォーマンスの向上が見込めます。結論として、上記のポイントを抑えることでSKフライス加工の成功率は飛躍的に高まることでしょう。
4. SK フライス加工の精度を決める要因
SKフライス加工での試作品製作は精度が命であり、成功率を高めるためにはいくつかのコツがあります。まず、工具の選定が重要です。試作品の用途や材質に合わせた適切な刃の種類やサイズを選ぶことで、加工時の精度を向上させることができます。次に、加工パラメータの最適化が挙げられます。切削速度、送り速度、切り込み量を材質ごとに調整することで、微細ながらも重要な差異を出し、高品質な試作品を作り出すことが可能です。さらに、工具の摩耗にも注意が必要です。定期的な工具の点検や交換を行うことで、常に最良の状態で加工を行うことができます。これらのコツを押さえることで、SKフライス加工における試作品の成功率は飛躍的に向上します。結論として、適切な工具選定、加工パラメータの最適化、そして工具の管理がSKフライス加工の成功の鍵となります。
5. SK フライス加工機の種類と特徴
SKフライス加工は試作品製作において、精度が高く作業効率も向上するため、技術者にとって重要な技術の一つです。成功率を高めるためには、まず適切な工具選びが肝心。SKフライスには様々なカッターやエンドミルがあり、材質や形状によって最適なものを選ぶ必要があります。たとえば、硬質材を加工する際は、耐久性のある高速度鋼や超硬合金製のカッターを選ぶことが望ましいです。また、精度を要する部品の加工には、微細な加工が可能な小径のエンドミルが適しています。さらに、切削条件の設定も重要で、回転数や送り速度を材質や刃の数に合わせて調整することで、加工面の仕上がりが大きく改善されます。このように、適切な工具選びと切削条件の調整によって、SKフライス加工の成功率を飛躍的に向上させることができます。
6. 金属と樹脂のSK フライス加工 試作の違い
金属と樹脂のSKフライス加工で試作品を作る際、成功率を高めるにはいくつかのポイントがあります。金属加工に比べて樹脂は加工しやすい一方で、精度を維持することが難しいです。ここで大切なのは、適切な工具選びと加工条件の設定です。具体例として、樹脂専用のカッターを使用し、切削速度や送り速度を金属加工時よりも低く設定することが挙げられます。また、樹脂特有の熱による変形を避けるために、冷却液を活用することも重要です。これらの工夫をすることで、試作品の精度を保つことができ、成功率を高めることができます。技術者の皆さんは、これらのコツを活かし、試作品製作のプロセスを改善しましょう。
7. SK フライス加工 試作のための設計のポイント
SKフライス加工は、試作品製作においてその精度と効率が求められる重要なプロセスです。成功率を高めるためには、幾つかのコツが存在します。まず、適切な工具選択が必須です。材料の種類に合わせた刃の材質や形状を選ぶことで、加工精度を向上させることができます。次に、切削条件の最適化が挙げられます。切削速度、送り速度、切り込み量を材料や工具に適した条件で行うことが、仕上がりや加工時間に大きく影響します。例えば、アルミニウム合金では高速かつ浅い切り込みで加工すると、良好な表面仕上げを得られます。さらに、加工前の適切な固定方法も重要です。不適切な固定は振動や変形の原因となり、試作品の品質を損なう恐れがあるからです。これらのコツを押さえ、常に機械の状態に注意を払うことで、試作品製作の成功率は大きく向上するでしょう。
8. SK フライス加工 試作の効率化技術
SKフライス加工は試作品製作においてその正確性と効率性から多くの技術者に重宝されています。成功率を高めるには、工具選びから始まり、適切な切削条件の設定が重要です。具体的には、使用するフライス工具の材質選びや刃の形状に注意し、被削材の材質や硬度に合わせたものを選ぶ必要があります。また、切削速度や送り速度、切削深さなどの条件を試作品の材質や形状に適したものに調整することで、加工精度を向上させることができ、不具合の発生を抑えることが可能です。実際に、適切なSKフライス加工によって試作品の仕上がりが良くなり、余分な修正作業が減少する例が多々報告されています。結論として、SKフライス加工のコツを押さえることで、効率的かつ高精度な試作品製作が可能になり、開発工程のスピードアップにも寄与します。
9. トラブルシューティング: SK フライス加工 試作でよくある問題
試作品の製作において、高い成功率を達成するためには、SKフライス加工の技術が重要です。SKフライス加工は、精度が高く、複雑な形状を持つ部品や金型の製作に欠かせない技術であるため、そのコツを押さえることが品質向上の鍵を握ります。例えば、工具の選定では、切削抵抗が低く長寿命のものを選ぶことが重要です。また、加工パラメータの調整には細心の注意が必要であり、適切な速度と送り速度のバランスを取ることで、粗さを最小限に抑えることができます。このような細かな点に注意を払いながら進めることで、トラブルを防ぎながら、効率的かつ高品質な試作品を製作することが可能です。結論として、SKフライス加工の成功は、適切な工具の選定と加工パラメータの最適化、そしてそれらに対する綿密な理解と経験によって大きく左右されるのです。
10. SK フライス加工試作成功のためのベストプラクティス
SKフライス加工は試作部品の製造において精密さと効率を要求される分野であり、これをマスターすることは技術者にとって非常に重要です。その成功率を高めるには、まず適切な工具選びが肝心です。専用の刃を選択し、材質に合わせた切削速度を守ることで、加工精度を向上させることができます。また、加工前のシミュレーションを行い、予期せぬ誤差を事前に検証することも重要です。実際に、3D CADデータを利用したシミュレーションは、試作品製作の初期段階において誤差を発見しやすくするため、効果的です。加工工程が始まる前にこれらのチェックを怠らなければ、トライアルでの失敗を減らし、最終的な製品の品質を向上させることが可能になります。SKフライス加工の技術を磨くことで、試作品の成功率を飛躍的に高めることができるのです。
まとめ
SKフライス加工は試作品の製作において成功率を高めるための重要な工程です。適切な切削条件や刃具の選定が重要です。加工精度を高めるためには刃具の適切な選定と適切な切削条件を設定することが必要です。また、素材の特性や形状に合わせた適切な工具選定が成功のカギとなります。技術者はこれらのポイントを押さえて試作品の製作を行うことで、成功率を向上させることができます。