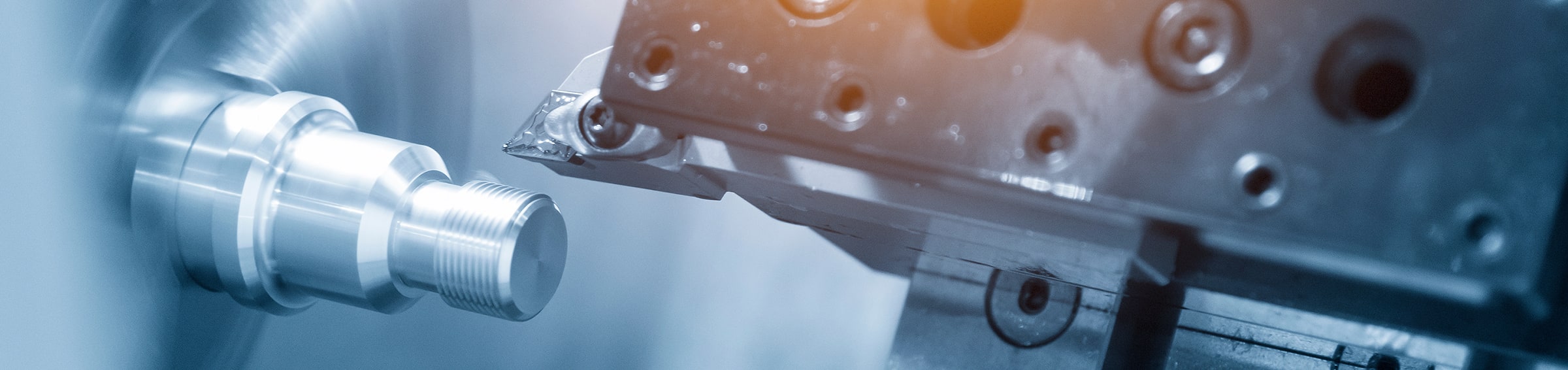
加工技術 column
工業高速加工の秘訣!SKD材フライスでの量産技術を徹底解説
『工業高速加工の秘訣!SKD材フライスでの量産技術を徹底解説』。皆さんは工業製品の生産において、高速加工と量産技術に関する課題を抱えていませんか?そこで、この記事では、SKD材を使用したフライス加工における量産技術の秘訣を詳しく解説します。高速加工と量産におけるコツやポイントについて知りたい方にとって、この記事は必読です。
1. SKD フライス加工量産の基礎知識
工業分野での高速かつ効率的な量産はSKD材を使用したフライス加工によって実現可能です。SKD材は硬度が高く、耐摩耗性に優れるため、量産において一貫した品質を保つことができます。例えば、自動車部品の製造では、SKD材のフライス加工によって精密な部品を大量に生産することが求められています。このようにSKD材を使った加工技術は、工業製品の量産において重要な役割を果たしており、その効率良い生産性によって、コスト削減にも寄与しています。結果として、品質と生産性の高い工業製品が市場に供給され、競争力が向上するのです。
2. SKD11とSKD61の材質比較
SKD材を用いたフライス加工は、量産においてその効率と品質で多くの製造業者にとって不可欠な技術です。SKD11とSKD61は、工業加工分野における主要な材料であり、それぞれ特有の特性を持っています。例えば、SKD11は耐摩耗性に優れ、精密な金型加工に適しています。一方、SKD61は高温強度と靱性に優れ、アルミニウムのダイカスト型などに利用されます。これらの材質を比較することで、使用する場面に最適な材料選びが可能となり、無駄なコストを削減しつつ生産効率を高めることができます。結論として、SKD材の選択は加工品質を左右するだけでなく、量産技術の効率化にも大きく寄与するため、各材質の特徴を理解することが重要です。
3. SKD フライス加工量産における材料選定のポイント
SKD材を用いたフライス加工は、量産においてその効率性から注目されています。SKD材は耐摩耗性に優れ、安定した加工が可能であるため、多くの工業分野での利用が進んでいます。具体的には、自動車部品や金型などの製造に適しており、硬度と加工性のバランスが求められる箇所での使用が一般的です。これらの部品の量産には、精度と速さが求められるため、SKD材はその要求を満たす最適な選択肢として重宝されているのです。加えて、フライス加工の際には、SKD材の種類や特性を踏まえたカッターや加工条件の選定が重要となります。これによって、高速かつ高品質な量産が可能になり、生産性の向上に貢献しています。結論として、SKD材を用いたフライス加工は、量産技術の効率化と品質の向上を実現するためのキーとなっています。
4. SKD フライス加工量産のための工具と技術
SKD材を使用したフライス加工は、量産においてその効率性と精度で高く評価されています。SKD材は硬さと耐熱性に優れており、工業高速加工に適しているためです。具体的な例としては、自動車のエンジン部品や金型などの耐久性が求められる製品に多く用いられています。これらの加工には、切削工具の材質選定や刃の形状、切削条件の最適化が重要となります。例えば、SKD材の加工に適した超硬カッターや、熱処理後の硬い材料を効率よく切削するためにコーティングされたカッターが選ばれます。また、適切な切削速度と送り速度の設定は、工具の寿命を延ばし、一貫した品質を保つために欠かせません。このように、適切な工具選択と加工技術の組み合わせによって、SKD材フライス加工の量産は成功を収めるのです。
5. SKD フライス加工量産に必要な機械設備
SKD材を用いたフライス加工が量産において重要な理由は、その効率の良さと加工精度の高さにあります。SKD材は、耐摩耗性や強度が高く、一度に多くの製品を高速で加工できるため、工業高速加工の現場では欠かせない材料です。具体的には、自動車産業や航空機部品の製造において、SKD材のフライス加工が活躍しています。これらの部品は、常に一定の品質と精度が求められるため、SKD材はその要求を満たす最適な選択となります。また、適切な機械設備を用いることで、SKD材のフライス加工はさらにそのポテンシャルを発揮し、量産体制の確立に寄与します。結論として、効率的で精度の高い量産を実現するためには、SKD材とそれを加工するための機械設備の整備が不可欠です。
6. SKD11とSKD61の加工事例と応用
SKD材を用いたフライス加工は、その耐摩耗性と硬度の高さから量産技術において非常に重要な役割を果たしています。特に、SKD11とSKD61は工業高速加工において広く利用されており、適切な加工技術を用いることで、高品質な製品を効率的に生産することが可能です。例えば、SKD11はダイスや金型などの精密部品に、SKD61はホットワーク用途にその特性が生かされています。これらの材料は、優れた熱処理と加工方法によって、耐久性が高く、長期にわたって安定した性能を保つことができるのです。従って、SKD材を使用することで、量産過程におけるコスト削減と生産効率の向上を実現できるため、製造業にとっての秘訣となっています。
7. SKD フライス加工量産のための表面処理技術
SKD材によるフライス加工量産は、熟練技術と先進の表面処理技術を組み合わせることで、効率良く高品質な部品を生産することが可能です。この製法のポイントは、耐摩耗性と精度の高さにあります。具体例を挙げると、自動車部品や航空機の部品など耐久性が求められる製品において、SKD材の硬さと耐熱性を活かすための特殊なコーティング技術や熱処理が施されます。これにより、材料の強度を保ちながら高速での加工を可能にし、量産におけるコスト削減と品質維持を実現しています。まとめると、SKD材のフライス加工量産は、先進技術を駆使してその最適性を追求することで、産業界における大量かつ高品質な部品供給に不可欠な要素となっています。
8. SKD フライス加工量産の品質管理と検査方法
SKD材を使用したフライス加工の量産は、その高い精度と効率の良さから多くの工業分野で重宝されています。その秘訣は、厳密な品質管理と検査方法にあります。まず、加工前には材料の均一性を確保し、設計された寸法に最適な切削条件を選定することが肝心です。例えば、自動車産業では、エンジン部品やトランスミッションのコンポーネントなど、SKD材を用いたフライス加工部品が量産され、その精度が直接製品の性能に影響を及ぼします。加工中には、定期的な工具の点検と交換を行い、切削速度や給送速度といった切削条件を適切に管理することが重要です。そして、量産後の検査では、三次元測定機を使用して製品の寸法精度を測定することで、一貫した品質を保証します。これらの厳格なプロセスを経て、高品質なSKDフライス加工品が量産されるのです。
9. SKD フライス加工量産のコスト削減と効率化戦略
SKD材のフライス加工は、現代の工業生産における量産技術の効率化とコスト削減に大きく寄与しています。SKD材料は硬度が高く耐摩耗性に優れているため、工具の寿命を延ばし、結果的に生産コストを削減することができます。具体的には、金型製造や自動車部品などの加工において、SKDフライスを使用すると、加工精度が高く、仕上がりの品質を均一に保つことが可能です。これは、細かい加工が必要な部品の量産において、大きな利点となります。さらに、適切な工具選定と切削条件の最適化により、加工時間を短縮し、生産効率を向上させることも実現できます。これらの戦略を駆使することで、SKD材を用いたフライス加工は、量産におけるコスト削減と効率化の鍵となるのです。
10. SKD フライス加工量産のトラブルシューティングガイド
SKD材を用いたフライス加工は、量産の現場でその効率の良さから注目されています。SKD材は工具鋼の一種であり、耐摩耗性に優れた特性を持っているため、多量の製品製造に適しています。特に量産においては、一貫した品質を保つことが求められますが、SKD材を用いたフライス加工はその点において高い信頼性を提供します。また、フライス加工機の進歩により、切削速度の向上や精密な加工が可能になっており、これによって量産時の生産性を大幅に向上させることができます。例として、自動車産業では部品の精密な大量生産が求められ、SKD材のフライス加工技術が重宝されています。このようにSKD材を用いることで、量産における品質と生産性のバランスを保ちつつ、製造コストの削減にも繋がるのです。最後に、これらの理由からSKD材のフライス加工は、量産技術の中でも特に重要な位置を占める技術であると結論づけることができます。
11. SKD フライス加工量産の国内外メーカーと供給チェーン
SKD材フライス加工での量産技術は、国内外のメーカーにとって革新的な製造方法となっています。この加工技術のメリットとしては、精度が高く再現性に優れている点が挙げられます。例えば、自動車産業や電子機器の部品製造において、SKD材を用いた部品はその耐久性と精度の高さから多くのメーカーに採用されています。また、SKD材は硬度が高く、長期間の使用に耐えうるため、工具の摩耗を減らし、コスト削減にも繋がります。さらに、熟練した技術者による操作によって、より高い生産効率を達成することができるのです。そうした技術的な利点により、供給チェーン内でのSKD材フライス加工の量産は、品質の均一化を実現しつつ、生産性の向上を図ることが可能になっているのです。
12. SKD フライス加工量産の将来展望と技術革新
SKD材を用いたフライス加工は、その高い精度と効率性から量産分野での重要性が高まっています。特に、耐摩耗性や強度が求められる製品に不可欠な技術であり、その運用には独自のノウハウがあります。例えば、SKD材の性質を深く理解し、適切な工具選定や切削条件の最適化を行うことが、効率的な量産を実現するための鍵です。また、CNCマシニングセンタの利用による自動化や、IoT技術を駆使した生産管理システムの導入など、最新の技術を取り入れることで、さらなる生産性の向上が期待されます。これらの技術進歩は、SKD フライス加工の量産単位コストを下げ、結果として日本の製造業の競争力を支えています。将来的には、持続可能な生産システムへの適応が求められる中、SKD材のフライス加工技術はますます進化していくことでしょう。
まとめ
工業での高速加工において、SKD材を使用したフライス加工は、効率的な量産技術として重要です。適切な切削条件と切削工具の選定がポイントとなります。加工時の切削速度や切削深さ、切削量などを最適化することで、高品質かつ効率的な量産が可能となります。
【精密加工】SS穴あけフライス加工の基本と注意点
精密加工におけるSS材料の穴あけフライス加工は、高度な技術と緻密な計画が必要な作業です。本記事では、SS材料の穴あけフライス加工の基本的な手順や注意点について解説します。精密加工に携わる方や興味をお持ちの方にとって、これからの情報は貴重なものとなるでしょう。
1. SS穴あけフライス加工入門
SS穴あけフライス加工は、精密な部品製造に不可欠である。この技術は、金属等の硬い素材に微細な穴を正確に開ける際に使用される。その際、注意すべき点が複数存在する。まず、適切なフライス工具の選択が重要である。素材の硬度や加工する穴のサイズに応じて、刃の材質や形状が異なるツールを選択する必要がある。次に、フライス加工機の設定も精密さが求められる。加工速度や切削速度、進行方向の調整などが品質を左右する。例えば、速度が速すぎると素材が熱を持ちすぎたり、遅すぎると不要な負荷がかかることがある。また、冷却剤の使用は摩擦熱を減少させるために欠かせない。こうした点を十分に検討し、正確なフライス加工を行うことが肝心であり、その結果として品質の高い製品が生まれる。結論として、SS穴あけフライス加工は適切な工具選択と機械設定の精密な管理によって、製品の品質を保証する重要な工程である。
2. SS穴あけフライス加工の基本概念
SS穴あけフライス加工は、精密な加工を要求される場合に特に重要な技術です。SSとはステンレスの略であり、ステンレス素材に対して精密な穴を開ける加工のことを指します。この加工の基本的なポイントは、素材の熱処理状態や工具の選択、回転速度といった複数の要素を適切に組み合わせることです。例えば、加工時の発熱を抑えるためには冷却液の使用が欠かせませんし、穴の精度を上げるためには工具の微調整が必要になります。加えて、SS素材特有の硬さや粘りに対応するため、特殊なフライス工具を選択する必要があるでしょう。総じて、SS穴あけフライス加工は慎重な準備と正確な操作が求められる技術であり、それを実現するためには上記の基本概念を理解し、具体的な作業に移すことが重要です。
3. 大型機械でのSS穴あけフライス加工
SS穴あけフライス加工は、精密な工業製品を作り出す際に不可欠な技術です。この加工方法は、特に大型機械において、その性能を最大限に活かすことができる点が大きな利点です。しかし、加工の精度を保つためには、いくつかの注意点を理解し実践することが重要です。特に、SS材料の特性を考慮した適切な切削条件の選定、鋭利な刃物の使用、そして定期的なメンテナンスが必須となります。例えば、SS材料は硬度が高いため、摩擦熱による変形や刃物の摩耗が起こりやすいです。そのため、適切な冷却剤を使用したり、刃物の切れ味を常にチェックすることが、加工品質を維持する上で欠かせません。最終的には、これらを踏まえた上で加工を行えば、精密なSS穴あけフライス加工における成功が期待でき、製品の品質向上に寄与することになります。
4. 一般機械部品のSS穴あけフライス加工
SS穴あけフライス加工は、精密な加工が求められる工業分野において不可欠な技術です。この手法は、金属などの硬い素材に対して小さい穴を高精度で開けることに特化しており、その精密さから幅広い分野で利用されています。たとえば、自動車や航空機の部品製造においては、極限まで重量を減らすために、穴あけ加工の精度が求められるのです。しかし、注意点も多く、切削速度や工具の摩耗、材料の熱処理状態などが品質に影響を及ぼすため、適切な切削条件の選定が重要になります。特にSS材料では、硬度が高く加工が困難な場合があるため、専門的な知識と経験が必要です。加工精度を確保しながら、コストを抑える効率的な加工方法の開発も進んでおり、今後もSS穴あけフライス加工の重要性は高まると考えられます。
5. SS穴あけフライス加工の種類と特徴
SS穴あけフライス加工は、製造業において重要な技術であり、その種類と特徴を把握することは必須です。フライス加工による精密な穴あけは、高度な精度を要求される部品製造において特に重要で、複雑な形状や微細な加工が求められる場合にも対応可能です。例えば、航空機や自動車などの産業で使用される部品では、微小な誤差も許されないため、精密加工技術が不可欠となります。ただし、注意すべき点がいくつかあります。材料の種類によっては切削条件を変える必要があり、また、工具の摩耗にも注意を払う必要があります。最適な切削条件と工具の選定が、高品質な加工結果を得るための鍵となるでしょう。精密加工の世界では、日々技術が進歩しており、常に最新の情報を得ておくことも大切です。
6. プレス加工とSS穴あけフライス加工の比較
SS穴あけフライス加工は、高い精度と効率性を求める製造業界において重要な技術です。この加工法は、プレス加工と比較して設備投資が少なく済むことが大きな特徴であり、小ロット生産にも柔軟に対応可能です。例えば、SS穴あけフライス加工では、複数の工程を一度に実施することができ、細かな直径の調整も可能です。これにより、プレス加工では実現しづらい複雑な形状や微細な加工も行えるため、製品の多様化に対応する生産が可能となります。ただし、注意点としては、加工する材料や刃の選定、それに加えて適切なパラメータ設定が求められます。適正な条件で加工を行うことで、高品質な製品が得られ、SS穴あけフライス加工のメリットを最大限に活かすことができるのです。
7. 塑性加工とSS穴あけフライス加工の違い
SS穴あけフライス加工は、高い精度と効率を求められる場面で重宝される技術です。この加工法の最大の特徴は、SS(ステンレススチール)などの硬質材料に対して、精密な穴を開けることが可能であるという点にあります。加工精度を高めるためには、適正な切削速度の選定や冷却剤の使用が重要です。具体的に、速度が速すぎると材料が熱を持ちやすく、穴の精度が損なわれる可能性があるため注意が必要です。また、フライスの刃先が欠けやすいため、定期的な交換やメンテナンスが欠かせません。例として、時計の部品製造や医療器具の加工において、その精密性が要求され、SS穴あけフライス加工が選ばれることが多いです。最終的に、この技術は高精度加工が求められる多くの分野での利用が期待され、その重要性はますます高まっています。
8. SS穴あけフライス加工の最新技術動向
SS穴あけフライス加工は、製造業における精密な部品加工に不可欠な技術です。この加工方法の最大の利点は、高い精度で均一な穴を短時間で加工できる点にあります。しかし、その精度を確保するためには、特に注意すべきいくつかのポイントがあります。具体的には、工具の選定、速度や送りの調整、冷却液の使用といった要素が大切です。たとえば、刃の材質には耐摩耗性に優れたものを選び、加工する材質や厚みに応じた速度や送りで加工する必要があります。また、適切な冷却液を用いないと、加工精度が低下したり、工具の寿命に影響を与える恐れがあります。これらのポイントをしっかりと押さえることで、SS穴あけフライス加工はより効率的かつ高精度の結果をもたらすでしょう。
9. SS穴あけフライス加工におけるトラブルシューティング
SS穴あけフライス加工は、精密な部品製造に不可欠な技術です。しかし、適切な知識と注意を欠いていると、加工不良のリスクを招く可能性があります。たとえば、フライスの選択ミスは切削精度に大きく影響し、使用するSS材料の種類によっては、切削速度やフィードレートの調整が必要になります。また、工具の摩耗や破損にも注意が必要です。一度に深い穴をあけようとすると、工具の破損や加工面の仕上がりが悪くなることがあります。これを防ぐためには、工具の負荷を適切に管理しながら、段階的に穴を深くしていくステップ加工が有効です。正しい工具選択と加工条件の設定、そして、工具の状態を常にチェックすることで、SS穴あけフライス加工におけるトラブルを回避し、品質の高い部品を製造することが可能です。
10. SS穴あけフライス加工プロジェクトの成功事例
SS穴あけフライス加工は、精度の高い加工を要する分野です。この方法は、特に金属加工において重宝されており、正確な穴加工が可能であるため、多くの工業製品の製造に欠かせません。しかし、正しい知識と技術がなければ、加工品の品質に影響を及ぼし、結果的に生産効率の低下を招くことになります。例えば、SS穴あけフライス加工を行う際には、加工する材料の種類や硬度を考慮し、適切な切削条件を選定する必要があります。具体的には、刃の速度や進行速度を適切に設定することで、熱による影響を最小限に抑え、精度の高い加工が可能となります。また、刃の摩耗を防ぐためには、定期的なメンテナンスも必要です。総じて、SS穴あけフライス加工は、適切な知識と技術をもって丁寧に行うことで、優れた精度と品質を実現できる加工方法であると言えます。
まとめ
SS穴あけフライス加工は、素材の性質や寸法精度に合わせて適切な工具や切削条件を選定することが重要です。特に硬度の高いSS材料の加工では、適切な刃先形状や刃先材質を選ぶことがポイントとなります。切削時の冷却や潤滑も適切に行い、加工精度を求める場合は適切な工具や機械の選定が必要です。
コストカット実現!SKDフライス加工で量産を効率化する方法
製造業におけるコスト削減や生産効率化は常に重要な課題です。特に、SKDフライス加工を活用することで、量産を効率化する方法は大きな関心事となっています。この記事では、SKDフライス加工を用いた効率的な量産方法について解説します。新たな生産手法に興味がある方やコスト削減を目指す製造業者にとって、必見の内容となっています。
1. SKDフライス加工量産の基礎知識
SKDフライス加工は量産においてコストカットを実現します。具体的には、SKD(半完成品)として部品を仕入れ、必要な加工を行うことで、生産効率が大幅に向上します。この方法は、高い精度が必要な部品の製造に多く採用されています。たとえば、自動車産業ではエンジン部品やトランスミッションのギアなど、複雑な形状の部品をSKDフライス加工で効率よく生産しています。その結果、製造コストを削減し、より競争力のある製品価格を実現できるのです。また、加工時間短縮により、市場への迅速な製品供給も可能となります。結論として、SKDフライス加工は量産の効率化とコスト削減に寄与する重要な手法であり、製造業の競争力向上に欠かせない戦略の一つです。
2. SKDフライス加工量産のコスト削減戦略
SKDフライス加工を用いた量産は、コストカットを実現し、生産効率を大きく向上させることができます。この加工方法がコスト削済に有効な理由は、半完成品を組み立てる際に、加工時間が短縮されるためです。具体的な例として、既成の部品を細かい部分まで加工する必要がなくなるため、時間とコストを削減できます。さらに、組み立てラインでの作業効率も高まります。SKD方式の採用は、特に大量生産を行う場合にその効果を発揮します。結果として、SKDフライス加工は、生産コストの削減と効率化の両面でメリットをもたらし、企業の競争力を高める要素となり得るのです。
3. マシニングセンタの利点とSKDフライス加工量産
SKDフライス加工による量産は、コストカットと効率化を実現し企業の利益向上に直結します。なぜなら、SKD(半ノックダウン)方式では、部品を一部組み立てた状態で輸入し、残りの加工を国内で行うため、輸送コストを大幅に削減できるからです。具体的な例として、自動車産業ではSKDフライス加工が多用され、部品の輸入時に発生する高額な輸送コストを抑えることができています。また、国内での最終加工により、細かな品質調整が可能となり、高品質な製品を市場に提供することができます。これにより、量産を行う際の生産効率が高まり、コストパフォーマンスが向上します。結論として、SKDフライス加工は、輸送コストの削減と国内での品質管理の徹底により、量産におけるコストカットと効率化を実現する有効な方法です。
4. マシニングセンタの課題とSKDフライス加工量産
SKDフライス加工を利用した量産はコストカットに繋がる重要な手法です。この加工法は特定の製造分野での材料費の削減と生産効率の向上に貢献します。たとえば、自動車産業における部品製造では、SKDフライス加工によって、同一形状の部品を大量に、かつ迅速に製造することが可能です。精密なカットが求められる部品においても、SKDフライス加工は高い再現性を実現し、廃材の削減にもつながります。さらに、工具の摩耗を抑えることで長期的なコスト削減が期待できるため、経済的な量産が実施可能となります。結果として、SKDフライス加工は、低コストで高品質な製品の量産を実現する方法として、多くの製造現場で採用されているのです。
5. 海外調達によるSKDフライス加工量産部品のコスト削減
SKDフライス加工を用いた量産は、コスト削減の鍵となります。この方法は、部品の大量生産において効率的なプロセスを提供し、特に国内でのコスト高に対する課題を解決するために有効です。例えば、日本では労働コストが高く、これが製造業全般において大きな負担となっています。しかし、SKD(Semi Knocked Down)方式を採用し、一部の加工を海外で行うことで、組立て工程を国内に残しつつ全体のコストを下げることが可能です。このアプローチにより、人件費が安い国で部品を部分的に加工し、最終的な品質管理と組立てを日本で行うことで、品質を損なわずに生産コストの削減を実現できます。結論として、SKDフライス加工は、高品質な製品を維持しつつ生産コストを抑える効果的な手段であり、量産効率化において重要な役割を果たしています。
6. 高品質なSKDフライス加工サービスの選択基準
SKDフライス加工によるコストカットは量産効率の向上に直結します。SKDは経済的で高品質な成形が可能であるため、製造業でのコスト削減に有効です。なぜなら、SKDフライス加工に適した材料は、耐久性や加工性が高く、複雑な形状の部品にも対応できるからです。実際の例として、自動車業界では、エンジン部品やシャーシ部品の製造にSKDフライス加工が用いられています。これらは大量生産が求められる部分であり、SKDフライス加工を採用することで、製造コストを大幅に削減しつつ、必要な品質を保持することが可能になります。したがって、適切なSKDフライス加工サービスを選ぶことは、コスト削減と品質維持の両立を実現し、市場競争力を高めるために不可欠と言えるでしょう。
7. 複合加工技術とSKDフライス加工量産のシナジー
SKDフライス加工の導入は、量産におけるコスト削減を実現する効果的な方法です。SKDとは減速機能を持つ組み立て式の駆動部品であり、フライス加工ではこれを効率的に利用することが可能です。特に大量生産が求められる場合、SKDフライス加工による部品の組み立てと調整が、生産性を大幅に向上させます。例えば、自動車産業や電子機器の製造ラインでは、SKDフライス加工により生産の高速化と品質の均一化が実現されています。これらのラインでは、複雑な形状や精度が要求される部品を短時間で大量に生産する必要があり、SKDフライス加工がその要求に応える重要な要素となっています。結論として、SKDフライス加工は量産工程の効率化とコスト削減に寄与し、様々な産業でその価値を発揮する技術といえるでしょう。
8. 実例から学ぶSKDフライス加工量産の成功事例
SKDフライス加工を導入することで、コスト削減を図ることができ、量産をより効率化することが可能です。この加工技術がコストカットにつながる理由は、その精度の高さと生産速度の速さにあります。例えば、ある自動車部品製造会社がSKDフライス加工を採用した場合、統制された品質で一貫した部品を高速で生産することが可能となり、従来の方法に比べて生産コストを大幅に削減できました。さらに、加工にかかる時間が短縮されることで、納期の短縮にも寄与し、顧客満足度の向上にもつながっています。このようにSKDフライス加工は、低コストで高品質な製品を迅速に市場に提供する一助となり、製造業の量産効率化に大きく貢献しているのです。
9. まとめを含めない最終セクション
SKDフライス加工は量産においてコスト削減を実現します。その根拠は、SKDフライス加工による部品の組み立てが容易になり、生産効率が向上するからです。具体例として、SKD方式では部品を分解して出荷し、現地で最終的な組み立てを行うことができます。これにより、輸送コストの削減や輸送時のリスク軽減が可能になります。また、現地での調整が容易になるため、製品の品質保持にも寄与します。結論として、日本におけるSKDフライス加工は、効率的な量産体制の構築を支援し、コスト削減に大きく寄与する方法として高く評価されています。
まとめ
SKDフライス加工を活用することで、製造業における量産のコストを削減し効率化することが可能です。SKDフライス加工は精密加工が求められる部品の製造に適しており、高い精度と品質の製品を短期間で生産することができます。適切な工程管理と最適な工具選定を行い、生産ラインにおける無駄を徹底的に削減することで、コストカットを実現することができます。
【工業用途】SKDフライス加工の量産向けテクニックとは?
工業界において、効率的な生産を実現するために、SKDフライス加工の量産向けテクニックが注目されています。生産性の向上や品質の確保を目指す企業にとって、このテクニックは重要な要素となっています。本記事では、SKDフライス加工の量産向けテクニックについて詳しく解説していきます。どのようなテクニックが使用されているのか、その効果や利点、さらには導入する際のポイントなど、網羅的に紹介します。工業用途における生産性向上のために欠かせない情報を取り揃えていますので、ぜひご覧ください。
1. SKDフライス加工とは?
SKDフライス加工は工業生産において高い精度と効率を誇る技術です。特に量産を前提とした場合、安定した品質と生産性の確保が欠かせません。そのためには、専用の治具を使用し加工精度を向上させることや、切削条件の最適化が重要です。具体例として、高速度鋼(SKD)を用いたフライス加工では、耐摩耗性に優れたコーティングの選定が必要とされます。また、精密な寸法管理を行うためには、カッターの交換時期の見極めや、加工中の温度管理がポイントになります。これらのテクニックを駆使することで、SKDフライス加工は量産においても均一な品質を維持し、コスト効率の良い生産を実現させることができるのです。
2. SKDフライス加工の量産向け材料選定
SKDフライス加工の量産向けに適した材料選定は、生産効率とコスト削減に大きく貢献します。SKD材は工具鋼としてその硬度と耐久性で選ばれることが多いですが、量産においてはこれらの特性と加工性のバランスが重要です。例えば、ある程度の硬度を持ちつつも加工しやすいSKD11は、量産用途では適している材料の一つです。加えて、耐熱性に優れるSKD61も部品の量産においては、形状の安定性を保ちつつ高速加工を可能にします。これらのSKD材を選定することで、機械の負荷を軽減し、工具の寿命を延ばし、結果的に生産コストを抑えることができるのです。要するに、適切なSKD材の選定は量産フライス加工における成功の鍵であり、投資対効果を最大化するための重要な要素となります。
3. SKDフライス加工量産技術の進化
SKDフライス加工が量産分野で注目されている理由は、その高い耐摩耗性と精密度にあります。特に、工業用途においては、大量生産を行う上でこれらの特性が不可欠です。量産に適したSKDフライス加工の技術は、工具寿命の延長や加工精度の向上といった点で進化しており、具体的には、高品質なカッター材料の選定、適切な切削条件の設定、そして先進的なCNC(Computer Numerical Control)機械の使用が挙げられます。これらの技術により、同一の品質を保ちつつ、より効率的に製品を生産することが可能となります。例えば、CNC機械を用いることで、人の手による誤差を減らし、複雑な形状の加工も容易に行えます。結果として、SKDフライス加工は量産において、コスト削減と効率化を実現する重要な役割を果たしています。
4. SKDフライス加工で使うエンドミルの特性
SKDフライス加工の量産向けには、適切なエンドミルの選択が極めて重要です。SKD素材は硬度が高く加工が難しいため、エンドミルは耐久性に優れたものを選ぶ必要があります。例えば、コバルトハイスやカーバイド製のエンドミルは、硬い材料を加工する際の耐摩耗性に優れており、精度の高い加工が可能です。また、量産を見据えた場合、工具寿命も考慮することで、連続生産におけるコスト削減に繋がります。さらに、切削条件の最適化を行うことで、加工時間の短縮と工具の摩耗を抑えることができます。結論として、適切なエンドミルを選び、切削条件を最適化することが、SKDフライス加工の量産における品質と効率を高めるテクニックです。
5. CNC加工の基本とSKDフライス量産のメリット
SKDフライス加工は、工業分野での量産において非常に効率的な加工技術です。結論から言うと、この技術は短い製造リードタイムと高い精度を要求される製品の量産に最適化されています。その理由は、SKD(すぱいらるかったーでんど)フライス加工が、硬質材料であっても精密なカットを可能にし、反復精度が高く、作業効率を大幅に向上させるからです。例えば、自動車産業や航空機産業では、部品の互換性が求められ、SKDフライス加工によって同一の高品質な部品を大量に生産できるため、広く用いられています。このように、SKDフライス加工は量産に適した技術であり、その利便性から今後も多くの工業分野で重宝されることでしょう。最後に再び述べますが、SKDフライス加工は量産における高効率と高精度の確保に欠かせない技術です。
6. SKDフライス加工量産のための機械選定
SKDフライス加工が量産において重要な役割を果たしていることは明らかです。量産に適した機械選定は、能率的かつ経済的な加工を実現するための鍵となります。たとえば、高速運転が可能な機械を使うことで、加工時間の短縮と生産性の向上が望めます。また、耐久性のある機械を選択することで、長期的な稼働にも耐え、メンテナンスコストの削減にも繋がります。実際、特定の量産向けモデルはこれらの要件を満たし、多くの工業現場で採用されています。総じて、賢明な機械選定は、SKDフライス加工を量産する上で不可欠であり、生産効率の向上とコスト削減を実現します。
7. 量産におけるSKDフライス加工の精度向上方法
SKDフライス加工は量産において重要な工程であり、その精度を向上させることは極めて重要です。その理由は、SKDフライス加工によって生産される工業製品の品質が直接的に影響を受けるからです。例えば自動車産業において、エンジン部品やシャシー部分などの精密な加工が必要とされる場合、SKDフライス加工の精度は直接的に製品の信頼性に関わってきます。このような部品の量産においては、ツールの選定や切削条件の最適化、そして定期的なメンテナンスが不可欠です。また、加工機の精度や温度変化による影響を最小限に抑えるための工夫も求められます。これらの技術を駆使することで、SKDフライス加工の量産時の精度は大きく向上し、結果として高品質な製品の安定した供給が可能になります。
8. SKDフライス加工量産のための工程最適化
SKDフライス加工の量産においては、工程の最適化が鍵となります。この最適化を実現するためには、適切な機械設定、工具の選定、そして効率的な作業フローが不可欠です。たとえば、SKDフライス加工で使用する製品の材質や大量生産の必要性に基づいて、耐久性と精密性を兼ね備えたカッターやエンドミルを選ぶことが重要です。また、工具の摩耗を常に監視し、予防保全に努めることで、停止時間を減らし、連続生産を可能にします。さらに、CAD/CAMなどのソフトウェアを利用して、事前に加工プロセスをシミュレートし、問題点を事前に洗い出すことも量産の効率化に寄与します。このような戦略的アプローチにより、SKDフライス加工における量産はより効果的かつ経済的に実行可能となり、最終的には業界における競争力の向上につながるでしょう。
9. SKDフライス加工を活用した企業の製品ランキング
SKDフライス加工は、精密な部品を大量に製造する際に不可欠な技術です。SKD(Superior Knife and Die steel)とは、特殊工具鋼の一種であり、工業用途においてその硬度と耐摩耗性が高く評価されています。そのため、量産を視野に入れた工業製品生産において、SKDフライス加工は重要な役割を担っています。具体例としては、自動車産業におけるエンジンパーツや、電子機器の精密部品などが挙げられます。これらの部品は、耐久性と精度が求められるため、SKDを用いたフライス加工が適しているのです。さらに、最新のCNC(Computer Numerical Control)技術を組み合わせることで、一貫した品質の部品を効率よく生産することが可能になります。結論として、SKDフライス加工は、量産における品質と効率を両立させるためのテクニックであり、工業製品の品質向上に寄与していると言えます。
10. 部品加工業界のSKDフライス加工量産サービス
SKDフライス加工は、量産において非常に重要な役割を果たしています。その理由は、SKDフライス加工が高硬度で耐摩耗性に優れた金属部品の製造を可能にするからです。特に自動車業界や工作機械部品の製造では、この技術を用いることで、精密な部品を大量に生産することが可能になります。例えば、エンジンの部品やギアなど、複雑な形状をした部品の加工には、SKDフライス加工が不可欠です。さらに、量産で求められる高い品質と低コストを両立させるためには、最適化された工具選定や、加工パラメータの細かな調整が必要です。このような量産向けのテクニックによって、製造業はより効率的となり、市場での競争力をさらに高めることができます。
11. SKDフライス加工量産のトラブルシューティング
SKDフライス加工が量産において重要なテクニックであることは間違いありません。その理由は、精密な加工が可能であると同時に、硬質材料への適用が可能なため、工業用途における幅広い需要に応えることができるからです。例えば、自動車や航空機の部品製造において、SKDフライス加工はその高精度と耐久性から選ばれています。具体的には、SKDフライスを用いた量産ラインでは、刃の交換周期の最適化、冷却液の効率的な使用、正確な工具経路の設計といった細部に至るまでの工夫が求められます。これらのテクニックによって、量産時のコスト削減と生産効率の向上が可能となり、結果として競争力のある製品作りに寄与しているのです。このようなSKDフライス加工の効率化は、産業界において引き続き重要であり、その技術開発と応用は今後も進化し続けるでしょう。
12. SKDフライス加工量産の将来展望
SKDフライス加工が量産において重要なテクニックであることは明らかです。その理由として、SKD材を用いた加工は耐久性や精度が求められる工業製品に不可欠であり、これらの特性を持続させるためには適切な加工技術が必要不可欠です。例えば、自動車産業や航空機部品の製造では、SKDフライス加工が正確な寸法と強固な耐久性を実現し、量産に至るまでのコストを大幅に削減することに寄与しています。このように、SKDフライス加工は特定の工業用途において効率的な生産を可能にするために重要な役割を果たしているのです。したがって、量産を目指す企業にとって、SKDフライス加工のテクニックを習得し、その効率を最大化することは業績向上に直結するのです。
まとめ
SKDフライス加工の量産向けテクニックとして、適切なカッターや刃先形状の選定が重要です。また、高速切削や高能率化のために、最適な切削条件や工具磨きの技術も必要です。さらに、自動化や機械化を取り入れることで効率的な量産が可能となります。
短納期・大量生産!SKDフライス加工で重視すべき要素とは?
大量生産の短納期を実現するために、SKDフライス加工が重要な要素となっています。本記事では、SKDフライス加工の重要性やその過程で重視すべき要素についてご紹介します。SKDフライス加工によって、効率的かつ高品質な大量生産を実現するためのポイントを探求します。
1. SKD フライス加工量産への序論
短納期での大量生産において、SKDフライス加工はその効率と精度から重要な役割を果たします。まず、短納期を実現するためには、加工工程の合理化が必要不可欠です。SKDフライス加工は、一度に多量の素材を高精度で加工できるため、この点で非常に有効です。例として、自動車業界では部品を迅速に生産する必要があり、SKDフライス加工は部品生産のスピードとコスト削減に大きく寄与しています。また、工具の耐久性や加工機のメンテナンススケジュールも、量産体制を維持する上で考慮すべき要素です。耐久性の高い工具を使用し、適切なメンテナンスを行うことで、連続稼働を可能にし生産性を高めることができます。最後に、品質管理の徹底も大量生産では欠かせません。最終的な製品品質を保証するため、SKDフライス加工の各ステップにおいて厳密な品質検査を行う必要があるのです。短納期と大量生産を実現するためには、これらの要素に注目し最適化を図ることが不可欠です。
2. 機械加工業者の選定方法とSKD フライス加工の重要性
短納期・大量生産を実現するSKDフライス加工では、選定する機械加工業者の資質が非常に重要です。何故なら、品質の安定した部品を迅速に供給するためには、高度な技術と確かな経験が必要とされるからです。例えば、自動車産業や家電業界では、一貫した品質の部品が大量に必要とされており、わずかな誤差も許されない場面が数多く存在します。このような状況下では、信頼性の高いSKDフライス加工を提供できる業者選びが極めて重要になります。その業者が持つ設備の精度や技術力、また納期に対する確実な対応力が重視されるべきです。結果として、適切な業者の選定は、高品質な製品を市場にタイムリーに提供するうえで、不可欠な要素と言えるでしょう。
3. SKD フライス加工と他の異なる加工方法の比較
短納期での大量生産を実現するSKDフライス加工は、効率性と品質のバランスを重視すべきです。短納期での生産が重要とされるのは、市場の変動が速いため需要に迅速に応えることが企業競争力の源となるからです。SKDフライス加工は、その特性を生かして量産に適している加工方法の一つです。例えば、自動車産業においては、部品の一貫性と精度が求められるため、SKDフライス加工は重宝されます。重要なのは、アルミやスチールなどの材料を加工する際に生じる熱や摩耗を考慮し、適切な冷却方法と工具の選定を行うことです。また、操作や設計の精度を高めることで、無駄な廃材を減らし、コスト効率も向上します。結論として、SKDフライス加工においては、短納期と大量生産を可能にする要素として、材料の選定、工具の管理、及び精度の高い設計を重視する必要があります。
4. 小ロット生産におけるSKD フライス加工の効率化戦略
SKDフライス加工は短納期と大量生産の需給バランスを成立させるうえで不可欠な技術です。重要なのは、高精度での加工能力と時間効率、さらにはコストパフォーマンスの三つをバランスよく達成することです。たとえば、自動車業界では、部品の大量生産が求められる場合が多く、SKDフライス加工で加工された部品が広く使用されています。特に、金型の製作において、SKDフライス加工は精密な成形が可能であり、また短時間での生産が可能なため、短納期での大量生産を可能にしています。さらにコスト削減も重要であり、素材費の削減や工程の改善を通じて、製造コストを抑えることが求められます。このようにSKDフライス加工は、高精度な部品製造を短時間で行いつつコスト効率も考慮する必要があるため、生産戦略において中心的な役割を担っています。
5. 金属製品製造におけるSKD フライス加工の役割
SKDフライス加工は短納期と大量生産に不可欠な要素です。この加工技術により、企業は製品の市場への迅速な投入を実現できます。その理由は、SKDフライス加工が高速で精密な加工を可能にするため、生産性を大幅に向上させることができるからです。例えば、自動車産業では、多様な部品を大量に生産する必要があり、SKDフライス加工はその要求を満たすために広く利用されています。その際、耐摩耗性や切削速度の適正化など、品質を保ちつつ効率を求める要素が重視されます。結局、SKDフライス加工での成功は、技術の適用を理解し、適切な加工条件を見極め、継続的な品質管理を行うことに尽きます。これらを実行することで、短納期と大量生産を実現し、ビジネスの競争力を高めることができるのです。
6. 加工設備の導入とSKD フライス加工の統合
SKDフライス加工は短納期と大量生産において重要な役割を果たす技術です。その鍵となる要素は、精密な加工能力とコストのバランスにあります。特に、自動車産業や家電製品などの分野で、部品の高品質かつ迅速な供給が求められる際、SKDフライス加工の利点が際立ちます。例えば、自動車のエンジン部品やフレーム部材の量産において、SKDフライス加工はその精密さによって高品質な部品を一貫して提供することができます。また、コスト面においても、耐久性と再研磨可能性を考え合わせたSKDの選択は、長期的なコスト削減に寄与します。総じて、SKDフライス加工は、品質とコストのバランスを重視することで、短納期・大量生産のニーズに応える強力なソリューションとなるのです。
7. SKD フライス加工 量産における品質管理と最適化
SKDフライス加工において短納期と大量生産を実現するためには、品質管理と最適化が重要です。日本の製造現場では、コストを削減しながら高品質を維持することが求められています。そのためには、まず材料の均一性を保つことが不可欠。SKDの特性を理解し、最適な切削条件を見極めることで、精度の高い加工が可能になります。さらに、加工機械の定期的なメンテナンスを行い、刃具の選定にも注意を払うことが品質維持には必要不可欠であると言えるでしょう。具体例として、ある自動車部品メーカーでは、これらの要素に注目し、連続した作業でのミスを削減し、生産性を50%向上させたケースがあります。最終的には、これらの要素に注意を払いながら、継続的な改善活動を行うことで、短納期・大量生産を達成し、競争力のある製造を実現できるのです。
8. 結論: 短納期・大量生産に向けて
短納期・大量生産を可能にするSKDフライス加工では、効率と精度が重視されるべきです。日本において、SKDフライス加工は量産を前提とした製造業で欠かせない技術ですが、短納期を実現するためには計画的な工程管理と高品質なカッターの選択が必要となります。例えば、自動車産業では部品の精度が製品品質に直結するため、加工機の正確なセットアップが求められ、それには熟練した技術者の存在が不可欠です。さらに、耐久性と高い切削能力を備えたカッターの使用は、連続稼働時の効率向上とコスト削減に寄与します。従って、短納期・大量生産を目指す際には、これらの要素をしっかりと管理し、最適化することが成功の鍵となるでしょう。
まとめ
SKDフライス加工では、生産効率と品質を重視する必要があります。短納期・大量生産を実現するためには、適切な加工設備の選定や切削条件の最適化が重要です。また、工具の選定や切削油の適切な使用など、細部にわたる工程管理も欠かせません。これらの要素を考慮することで、効率的かつ高品質なSKDフライス加工が実現できます。
SKDフライス加工で量産性を高める!実践的アドバイス集
SKDフライス加工を行う際、量産性を高めるための実践的なアドバイスをお探しですか?本記事では、SKDフライス加工の基本から応用まで、量産性を向上させるための具体的な方法を紹介しています。量産における効率的なスキルやテクニックを学びたい方には、この記事がお役立ちです。
1. SKDフライス加工の基本概念と量産への影響
SKDフライス加工は、量産において非常に効率的な手法として注目されています。この加工方法の利点は、精度の高い部品製造が可能である点に加え、一度に多くの部品を加工できるため、作業コストの削減と生産性の向上が期待できます。例えば、自動車産業におけるエンジン部品など、同じ形状の部品を大量に生産する際にSKDフライス加工は重宝されます。加工精度が非常に要求されるこの分野では、SKDフライス加工により一貫した品質の部品を迅速に供給することができ、結果的に市場への迅速な対応という競争力の向上に繋がっています。このようにSKDフライス加工は量産体制を確立する上で欠かせない技術と言えるでしょう。
2. 機械加工の基礎知識とSKDフライス加工の役割
SKDフライス加工は量産性を高める鍵となります。この加工法は、一貫した品質と高い生産効率を実現するために不可欠です。たとえば、自動車産業においては、複雑な形状や高精度が求められる部品の生産にSKDフライス加工が用いられています。この加工技術を適切に活用することで、大量生産が容易になり、コスト削減にも繋がります。例えば、専用の工具を使用してSKDフライス加工を行い、製造工程を簡略化することで、工程ごとの時間短縮を実現します。さらに、工具の耐久性を高めることで交換頻度の低減も可能です。結論として、あらゆる生産現場においてSKDフライス加工は、精度と効率を両立させた量産体制を構築する上で、非常に重要な役割を担っています。
3. SKDフライス加工で遭遇するエンドミルの課題と解決策
SKDフライス加工は量産性を高めるには非常に効果的な手法です。その理由は、SKD(特殊工具鋼)の優れた耐摩耗性と安定した加工性にあります。例えば、自動車部品の製造においてSKDフライス加工を用いることで、精度の高い部品を効率良く大量生産することが可能です。しかしながら、エンドミルの摩耗や破損は避けられない課題です。これに対処するため、耐摩耗性に優れたコーティングされたエンドミルの使用や、定期的な交換計画を立てることが重要です。また、適切な切削条件の選定も加工精度を保つうえで欠かせません。これらの対策を講じることで、SKDフライス加工の量産性はより向上し、生産効率の最大化が期待できます。
4. 工具鋼SKDの特性とフライス加工での利点
SKD工具鋼は硬度が高く耐摩擦性に優れているため、フライス加工に適しています。その結果、量産時の精度維持が容易になり、コスト削減にも繋がります。例えば、自動車部品の生産などでSKDを利用した場合、その耐久性の高さから長期間にわたって安定した品質の部品を提供することが可能です。また、フライス加工における工具の交換頻度が減ることで、ダウンタイムも削減され、生産効率が向上します。SKDフライス加工は、長期間にわたって一貫した品質を維持することで、結果として量産性の向上に寄与するのです。
5. プラスチック金型分野におけるSKDフライス加工の技術動向
プラスチック金型分野におけるSKDフライス加工は、量産性を高めるための重要な技術であることが結論として得られる。その理由は、SKDフライス加工が高硬度材料に対しても優れた切削能力を発揮し、精度の高い部品を効率良く生産できるからである。具体的には、SKDフライス加工を用いることで、金型の寿命が延び、メンテナンスの頻度が低減される。加えて、微細な加工も可能となり、より複雑な形状の金型製作に対応できるようになる。これらの特性が、量産におけるコスト削減や効率化に直結する。結論として、SKDフライス加工はプラスチック金型分野における生産性向上に寄与し、その実践は業界の競争力を高める一助となることは間違いない。
6. 建設機械用部品の耐摩耗性向上に寄与するSKDフライス加工技術
SKDフライス加工は量産性の向上に不可欠です。その理由は、SKD材は硬度が高く耐摩耗性に優れているため、部品の寿命を延ばし、製造コストを削減するからです。具体例として、建設機械用の刃物などが挙げられます。これらの刃物は常に高い耐久性が求められ、SKDフライス加工によってその要求を満たすことができます。また、精度の高い加工が可能なため、量産時のバラツキを減らし、品質の均一化を図ることができるという利点もあります。最終的に、SKDフライス加工は製造プロセスを合理化し、製品の品質向上とコスト削減に寄与します。これらの理由から、SKDフライス加工は量産を行う上で非常に重要な技術と言えるでしょう。
まとめ
SKDフライス加工は量産性を高めるための重要な工程です。良好な切削条件を設定し、適切な工具選択を行うことで加工効率を向上させることができます。また、工具の寿命を延ばすために冷却や潤滑の効果を最大限に活かすことも大切です。さらに、適切な加工方法と精密な作業を行うことで高品質な製品を効率よく生産することが可能です。
【最新技術】SKD材料のフライス加工で量産を成功させる方法
SKD材料のフライス加工において、量産を成功させるための最新技術について考えてみましょう。 最新の技術を駆使して、生産性を向上させる方法や、品質を保ちながら効率よく量産を行う方法について、この記事では詳しく解説します。SKD材料のフライス加工において量産を成功させたいと考えている方々にとって、貴重な情報が得られることでしょう。
1. SKD材料のフライス加工とは?
SKD材料のフライス加工は、工具や金型に使われる高硬度の特殊鋼を正確に加工する技術です。この加工方法が量産に成功すると、製品の品質や生産効率が飛躍的に向上します。そのため、正確な測定技術と高い加工精度が求められるのです。例えば、自動車の金型製造において、SKD材料を使用した部品は、耐久性や精密さが要求されるため、非常に重要視されています。フライス加工により一貫した厚みや形状を実現することで、大量生産が可能となり、コスト削減にも寄与するのです。最新技術を取り入れた加工機械の使用や、オペレータの技術向上がカギとなります。結論として、SKD材料の精密なフライス加工は量産に不可欠であり、技術革新と人材育成がその成功を左右する要因であるといえます。
2. SKD フライス加工 量産の基本
SKD材料を使ったフライス加工の量産は、その高い品質と効率性により注目されています。SKD材料は耐摩耗性に優れており、精密な部品を製造する際に多く利用されていますが、これを量産するには特定の工夫が必要です。例えば、適正なカッター選定とカッターの速度・送りの最適化は、高い精度と生産効率を実現するため不可欠です。また、冷却液の適用方法を工夫することで、加工時の熱影響を抑え、品質の安定化に貢献します。さらに、工具の摩耗を定期的にチェックし、適切なタイミングで交換することで、一貫した加工精度を維持することができます。これらの要点を押さえることで、SKD材料のフライス加工量産は成功へと繋がり、高品質な製品を効率良く提供することが可能になります。
3. SKD フライス加工に適した金属材料の選定
SKD材料を用いたフライス加工の量産成功の鍵は、適切な材料選定にある。SKD材料は硬くて耐磨耗性に優れているため、量産時の精度と効率が求められるが、正しい選定が行われれば量産は十分可能である。具体例として、耐熱性が必要な部品製造ではSKD61が好まれる。この材料は加工硬度が高く、熱処理後も安定した性質を保つため、連続した生産ラインでの使用に最適である。また、切削工具の製造用途では、SKD11が選ばれることが多い。このように、用途に応じてSKD材料を選ぶことで、フライス加工による量産を成功させることができる。したがって、目的に即したSKD材料を選定することが、量産成功への近道と言えるだろう。
4. SKD11とSKD61の材料特性と加工の違い
SKD11とSKD61という材料は、それぞれ耐摩耗性や耐熱性に優れており、フライス加工での量産においてもその特性が生かされます。これらのSKD材料を成功裏に量産に結びつけるには、材料特性を理解した上での適切な加工方法が重要です。たとえば、SKD11は炭素鋼で硬度が高く、精密な加工が可能ですが、その分、工具の摩耗が早まるため注意が必要です。一方、SKD61は高合金ホットワーク鋼で、高温でも強度が保持される特徴を持っていますが、硬度はSKD11ほどではありません。量産時には、これらの特性に合った工具選びや冷却方法、加工速度などを最適化することで、効率よく品質の高い製品を生産することができるでしょう。結論としては、SKD材料のフライス加工における量産を成功させるには、それぞれの材料特性に合わせた加工技術の選択が必須となります。
5. NCフライス加工の基礎とSKD材料への応用
量産におけるSKD材料のフライス加工は、効率的な生産を実現する鍵となります。なぜなら、SKD材料は優れた耐摩耗性を備えている一方で、硬質で加工が困難な特性を持っているからです。具体的な成功例として、適切な切削工具の選定、切削条件の最適化、および冷却剤の使用が挙げられます。特に、専用の超硬合金カッターやコーティングされた工具を使用することで、SKD材料の加工精度と効率が大幅に向上しました。また、切削スピードや送り速度を細かく調節することで、材料の熱負荷を抑制し、加工誤差を最小限に抑えることができます。さらに、適切な冷却剤を利用することで、工具の寿命を延ばし、継続的な量産が可能となります。結論として、これらの方法を組み合わせることで、SKD材料のフライス加工における量産を成功させることができるのです。
6. 精密なSKD フライス加工のための工具選定
SKD材料のフライス加工において量産を成功させるためには、適切な工具選定が不可欠です。この理由は、SKD材料の硬度や強度が高いため、通常の工具では摩耗が激しく、精度を維持することが難しいからです。例として、硬質合金やコーティングされたエンドミルはSKD加工において優れた耐摩耗性と長寿命を提供します。また、正確な切削が可能な高度なCNCマシンを使用することで、一貫した品質を保ちながら生産効率を向上させることができます。したがって、高品質な工具選定と先進の加工機を組み合わせることが、SKD材料のフライス加工での量産成功の鍵となります。
7. SKD フライス加工の最新技術動向
SKD材料のフライス加工における最新技術は、量産成功への鍵となる。SKD材料は工具鋼としての優れた硬度と耐摩耗性を持つが、その分加工が難しく、量産化には高度な技術が求められる。その解決策として、最新のCNC技術を駆使した高精度フライス加工が挙げられる。この技術を用いることで、複雑な形状でも均一な品質での大量生産が可能となる。特に、カッターの材質選定や切削条件の最適化、そして精密な測定機器を利用した品質管理が、量産において重要な要素である。具体例としては、自動車産業や航空宇宙産業で見られる部品の量産において、これらの技術が既に実践されていることが挙げられる。結論として、SKD材料の量産を成功させるためには、最新のフライス加工技術の採用が不可欠であり、それによって安定した品質の製品を効率的に生産することができる。
8. SKD フライス加工における量産の課題と解決策
SKD材料のフライス加工で量産を成功させるには、加工方法の見直しが必要です。SKD材料は硬度が高く、工具の摩耗が激しいため、従来の加工方法ではコストが増大し、量産に向かないという問題がありました。しかし最新技術の導入により、工具の寿命を延ばし、加工速度を上げることができ、コスト削減と効率向上を実現しています。例えば、コーティング技術の向上は工具の耐久性を高め、切削液の最適化は摩耗を抑制しています。また、CNCフライス盤の精度向上により、細部にわたる精密な加工が可能となり、製品の品質向上にも寄与しています。結果として、SKD材料を用いた製品の量産が可能となり、製造業の生産性向上に大きく貢献しているのです。
9. SKD フライス加工量産の成功事例紹介
SKD材料を用いたフライス加工での量産に成功するには、特有の工夫が必要です。SKD材料は硬質でありながら加工性が良好なため、耐摩耗性という強みがあります。そのため量産に適していると言えますが、正しい方法で加工しなければ品質のばらつきが生じやすくなります。具体的な成功例として、切削速度の最適化、適切な冷却液の使用、専用工具の選定といった工程の見直しが挙げられます。これらを総合して、加工精度の向上やコスト削減に繋がると共に、製品の品質を均一に保つことができます。したがって、SKD材料のフライス加工において、これらの点に注意し、適切な加工条件を見つけ出すことが量産成功の鍵となるでしょう。
10. 今後のSKD フライス加工技術の展望
SKD材料のフライス加工は、成功した量産には不可欠です。この加工技術は、耐摩耗性や耐熱性が要求される製品において重要な役割を果たします。特に、SKD材料は硬度が高いため、加工時の精度を維持することが挑戦となりますが、最新の技術を用いることでその課題を克服することができます。例えば、高精度のCNC(コンピュータ数値制御)機械を使用することにより、一貫した品質と寸法の精度を保ちながらの量産が可能になります。さらに、カッターの種類を選ぶ際にも、SKD材料を効率的にかつ精密に加工できるものを選定することが肝要です。このような最新の技術と適切な工具の選択により、SKD材料のフライス加工での量産は成功へと導かれるでしょう。
まとめ
SKD材料を使用したフライス加工では、適切な切削条件や工具選定が重要です。量産を成功させるためには、高硬度のSKD材料に適した切削工具を選ぶことがポイントです。また、切削速度や切り込み量などのパラメータを正確に設定することで効率的な加工が可能となります。最新の技術を取り入れたフライス加工で、高品質な製品を効率よく生産することができます。
【初心者向け】SKD材とフライス加工を用いた試作のステップバイステップ
初めて機械加工を行う初心者の方に向けた、SKD材とフライス加工を使った試作のステップバイステップガイドへようこそ。この記事では、機械加工における基礎から実践的な手順までを詳しく解説します。SKD材とフライス加工を使った試作の具体的な手法やポイントについて知りたい方は、ぜひお読みください。
1. SKD フライス加工 試作の基本概念
SKD材を用いたフライス加工で行う試作は、製造業における製品開発の初期段階において非常に重要です。試作品を作ることは、製品の設計が実際の物理的な形をとる第一歩であり、設計上の問題を発見し、改善する機会を提供します。具体的には、SKD材は優れた耐摩耗性を持ち、機械的強度が高いため、試作品の材料として選ばれます。フライス加工は、材料から余分な部分を削り取り、必要な形状を作り出す加工方法で、試作品作りにおいては、その精度と速さが求められます。例えば、自動車の部品や医療機器などの精密な製品は、初めにSKD材を使用してフライス加工による試作品を作成し、その機能や耐久性をテストします。この工程を経ることで、最終製品の品質向上に寄与し、コストの削減にも繋がります。したがって、初心者にとっても、SKD材とフライス加工を用いた試作のステップを学ぶことは、製造プロセスを理解し、技術を磨く上で不可欠なステップです。
2. 材料選定:SKD材の特性と選び方
フライス加工に適した材料として、SKD材は試作において理想的な選択肢です。SKD材は耐摩耗性や硬さが高く、精密な加工が求められる試作品作りに適しています。たとえば、金型などの試作に使用する際に、SKD材の硬さはその形状を正確に保持することを助け、耐久性を保証します。初心者でも比較的加工しやすく、フライス加工の練習にも最適です。SKD材を選ぶ時は、加工する試作品の用途や必要な特性をしっかりと理解し、それに適したグレードのSKD材を選定することが重要です。結論として、SKD材はフライス加工による試作において、その優れた特性を活かし、初心者でも取り扱いやすい材料として推奨されます。
3. フライス加工技術の基礎
フライス加工は、SKD材を含む多種多様な材料に対応できる加工技術であり、試作品作りにおいて初心者でもステップバイステップで学ぶことができます。まず、フライス加工のメリットとしては、高精度な形状を実現できる点が挙げられます。この技術を用いれば、複雑な形状や微細な加工も可能となり、試作段階でのアイデアを具現化しやすくなります。たとえば、SKD材を使った機械部品の試作において、フライス加工によって細かい溝や角度の調整が正確に行えるのです。こうした工程を一つ一つ確実に行うことで、初心者でも理解を深めながら技術を習得できます。最終的には、フライス加工が試作品作りに不可欠な技術であることが認識され、その重要性がより明確になるでしょう。
4. SKD フライス加工 試作のステップバイステップ解説
SKD材を使った試作品作りは、その精度と強度で知られ、特にフライス加工においては初心者でも取り組みやすい工程です。まず、フライス加工に適したSKD材を選ぶことが大切です。SKD材は硬度が高く加工しやすいため、初心者にも扱いやすいのです。次に、正しい工具と加工機を選び、基本的なフライス加工の手順に従いながら材料を削り出します。例えば、直線的な部分はエンドミルを使用し、曲線部分にはボールエンドミルが適しています。加工の際に生じる熱による変形を避けるために、適切な冷却剤の使用も重要です。最後に、細かい仕上げを行い、必要な寸法と形状に近づけていきます。このように、SKD材とフライス加工を活用すれば、精密な試作品を効率よく作り出すことが可能です。
5. SKD11の切削加工における注意点
SKD材を用いたフライス加工での試作は、工具の耐久性や加工の精度をテストするのに最適です。フライス加工は、切削工具を回転させながら材料を削ることで形を作りますが、SKD材のような硬質材料を加工する場合は特に注意が必要です。例えば、SKD11は耐摩耗性に優れた工具鋼であり、プレス金型やゲージなどに使用されることが多いですが、適切な切削条件の選定が重要です。切削速度や送り速度、刃の選定は材料の特性に応じて慎重に選ばれ、冷却剤の使用は切削熱を抑制し工具の寿命を延ばします。これらの点を考慮し、試作品は段階を追って慎重に加工されるべきです。最終的に、これにより製品の品質が向上し、フライス加工の技術が磨かれていくのです。
6. JIMTOF2012で注目されたフライス加工関連の新製品
フライス加工を初めて体験する方々にとって、SKD材を用いた試作品の製作は極めて学びが多いプロセスです。まず結論から言うと、SKD材を用いたフライス加工による試作は、技術を磨く上で非常に効果的な手段となります。その理由は、SKD材料が持つ加工しやすさと、実際の製品製作に近い経験が積める点にあります。たとえば、フライス加工では異なる種類の刃を使って材料を削る技術が必要ですが、SKD材は硬度が適度であるため、刃の扱いや切削条件の選定について基本的な理解を深めるのに最適です。また、試作過程では実際の製品を作る際の設計変更にも柔軟に対応できるため、プロセスの各段階での学びが盛りだくさんです。最終的には、SKD材とフライス加工を駆使し、完成度の高い試作品を作り上げることができれば、それは一人前の加工技術者へと近づく大きな一歩となるでしょう。
7. フライス加工の求人情報:業界で活躍するために
フライス加工を用いた試作は技術革新の舞台となっています。この分野での試作は、SKD材を活用することによって、製品開発を格段に前進させることが可能です。SKD材は耐摩耗性や耐衝撃性に優れており、フライス加工に最適な材料です。たとえば、自動車産業では、エンジン部品やギアなどの試作にSKD材とフライス加工が頻繁に用いられます。これらの部品は精密さと耐久性が要求されるため、SKD材の選択は非常に重要です。初心者でもこれらの材料を使いこなせるように、まずはSKD材の特性を理解し、次に基本的なフライス加工の技術から学ぶことが肝要です。適切な工具の選択や切削条件の設定など、基本を押さえておくことで、試作はより効果的に、そしてスムーズに進行します。要するに、SKD材とフライス加工を組み合わせた試作は、初心者でも技術を磨き次世代の製品開発に貢献できる重要なステップであると言えるでしょう。
まとめ
SKD材を使用した試作品を作成する際には、まず適切な材料の選定が重要です。次に、フライス加工を正確に行うことで、精密な仕上がりを実現することができます。試作品の製作においては、材料や加工方法についての正しい知識と技術が必要です。初心者の方でも、ステップバイステップで学びながら試作品を作成することが可能です。
【品質向上】SKD材料を使ったフライス加工で量産時のポイント
量産において品質の向上を目指すなら、SKD材料を使ったフライス加工が重要なポイントとなります。本記事では、SKD材料を使用したフライス加工の重要性や応用方法について詳しく解説します。また、量産における効果的なフライス加工のポイントについてもご紹介します。材料や加工方法に関心のある方にとって、この記事はきっと興味深い情報となるでしょう。
1. SKD フライス加工 量産とは
SKD材料を利用したフライス加工において品質向上が重要であると結論付けられます。その理由は、SKD材料の特性上、硬度が高く耐摩耗性に優れているため、量産時の安定した加工精度を維持することができます。例えば、自動車や工業用機械の部品製造において、SKD材料はその耐久性から多く採用されています。しかし、その硬度のために適切な工具選択や切削条件の管理が重要となります。さらに、加工機のメンテナンスを定期的に行うことで、品質のブレを防ぐことができるのです。したがって、品質を保ちながら量産するためには、SKD材料の特性を理解し、最適なフライス加工法を選択することが肝要です。最終的に、これらのポイントを押さえることで、製品の品質向上とコスト削減に繋がります。
2. SKD11とSKD61の違い
SKD材料を使用したフライス加工における量産時のポイントは品質向上に不可欠です。特に、SKD11とSKD61という高い硬度と耐摩耗性を持つ工具鋼は量産において重要な役割を果たします。SKD11は冷間作業用、SKD61は熱間作業用として使い分けられ、それぞれ加工物の特性に合わせた優れた性能を発揮します。例えば、SKD11はダイスやゲージ製作に、SKD61はアルミニウムや亜鉛のダイカスト型に使用されます。この材料の選定は、製品の精度保持と加工コストの削減に直結し、最終的な品質を左右するため、適切な材料選びが量産時の品質向上には必須です。このため、高品質な加工品を一貫して生産するためには、SKD材料を適切に選択し、その特性を理解し活用することがポイントとなります。
3. SKD11 フライス加工のキーポイント
SKD材料を用いたフライス加工は、精度と寿命の向上に不可欠であると同時に、大量生産におけるコスト効率を改善する重要なポイントを持っています。SKD材料は耐摩耗性に優れており、厳しい加工条件にも適応できるため、量産時の一貫性と品質の維持が可能です。たとえば、金型製作においてSKD材料を使用することで、長期にわたり安定した品質の部品を供給することが可能となります。また、SKD材料を適切にフライス加工するためには、適正な切削条件の選定や、適切な工具の使用が重要です。これにより、材料の特性を最大限に活かしつつ、摩耗や損傷を抑え、長寿命化を実現することができるのです。結論として、SKD材料に適したフライス加工技術を駆使することで、量産における高品質とコスト効率の良い生産体制の確立が期待できます。
4. 金型材の最新トレンドと市場状況
SKD材料を使用したフライス加工は、量産時に品質向上の重要ポイントである。SKD材料は炭素鋼や合金鋼と比較して耐摩耗性が高く、安定した加工精度を維持できるため、長期間にわたる大量生産においても品質が一定に保たれる。具体的には、自動車や機械部品の量産において、フライス加工を用いてSKD材料から精密部品を作り出す際、その耐摩耗性により刃具の摩耗が少なく、加工誤差を最小限に抑えることができる。さらに、SKD材料の一貫した特性は、加工後の部品の寸法精度や形状保持にも寄与する。結論として、SKD材料を使ったフライス加工は、量産時の品質維持に不可欠であり、製造業の競争力を高めるための鍵となる。
5. 高精度フライス加工の技術
SKD材料を使ったフライス加工は、製品の品質向上に不可欠であり、量産においても重要なポイントがいくつかあります。まず、SKD材料は硬度が高く耐摩耗性に優れているため、精密な加工が可能となり、品質の安定化を実現できます。有効な例としては、自動車や航空機の部品製造において、SKD材料を用いることで、摩擦や衝撃に強い部品が量産されています。さらに、耐久性が求められる工業製品にもこの材料が使用され、長期にわたる安定した性能を顧客に提供することができます。しかし、SKD材料の硬度が高い分、加工設備への負荷が大きくなるため、工具の選定や保守にも注意が必要です。結論として、SKD材料を使用したフライス加工は、量産時の品質向上に寄与し、より耐久性と精度の高い製品を製造する上で重要な役割を果たしています。
6. 金型材料と被削性
最適な金型製品を量産する際には、SKD材料を使用したフライス加工が欠かせません。SKD材料は硬度が高く、耐摩耗性に優れているため、製品の品質を一貫して保持することが可能です。フライス加工においては、SKD材料の硬さを考慮した刃物選びが重要となります。例えば、超硬合金製の刃物はSKD材料の高硬度に対応し、精度の高い加工を実現します。また、加工時には材料の熱処理状態を考慮し、適切な冷却方法を選択することも品質向上に繋がります。さらに、フライス加工機の精度も量産品質を左右するため、定期的なメンテナンスが必須です。これらのポイントに注意を払いながら量産を行うことで、SKD材料を使った製品の品質を向上させることができるのです。
まとめ
SKD材料を使用したフライス加工において、量産時には加工条件の安定化が重要です。適切な切削速度や刃先形状、潤滑材の選定などを工夫することで加工精度の向上と工程効率の改善が期待できます。また、適切なクーリングシステムを導入することで加工時の熱処理を行い、材料の耐久性を高めることができます。量産におけるフライス加工には、これらのポイントを抑えることが重要です。
試作の成功へ導く!SKフライス加工の基本と応用テクニック
製造業における試作品の作成は、新しい製品や部品を開発する上で不可欠なプロセスです。その中でも、SKフライス加工は高い精度と効率性で評価されています。本記事では、SKフライス加工の基本から応用テクニックまでを詳しく解説します。製品開発の重要なステップである試作を成功に導くための情報をお届けします。
1. SK フライス加工 試作入門
SKフライス加工は試作品作成において不可欠な工程であり、その基本を理解し応用技術を駆使することは成功の鍵となります。この加工法は、精密かつ複雑な形状を実現可能にするため、多くの工業分野で用いられています。例えば、自動車の部品や航空機の構造物に至るまで、幅広い製品の試作にSKフライス加工が活かされています。この技術を使いこなすには、刃の選定から送り速度、回転数の調整に至るまで、細部にわたる注意が必要です。また、材料の種類によっては加工条件を微調整することで、より高品質な試作品を得ることができます。このように、SKフライス加工の基本をマスターし、状況に応じた応用技術を用いることで、試作品の成功率は大きく向上します。
2. SK フライス加工の基本テクニック
SKフライス加工は高精度な試作品を作り出すために必要不可欠な技術です。試作の成功はこの技術の理解と適切な応用に大きく依存しています。基本的なテクニックを押さえ、材料や形状に応じた適切な工具選択と速度設定が成功の鍵となります。たとえば、アルミニウムや銅などの非鉄金属加工では、切削抵抗が小さい工具を用い、高速での加工が可能です。一方、硬度が高い鋼を加工する際には、強靭な工具を使用し、適切に加工速度を下げることが重要です。これらの基本に忠実に加工を行うことで、ほぼ無欠陥の高品質な試作品を製造することができます。試作の成功はSKフライス加工の正しい理解と技術の応用によって、より確実なものになります。
3. SK フライス加工の応用テクニック
SKフライス加工の試作は、精密で高品質な製品を生み出すためには不可欠です。試作の成功には、基本的な技術の習得と応用が鍵を握ります。まず、正しい工具選択と加工パラメータの設定が基礎として挙げられます。例えば、異なる材質や形状には特有の切削条件があり、それを見極めることが重要です。また、導入する最新のフライス機器を用いて、微細な加工も可能になります。このようにして、試作段階で多くのバリエーションを試しつつ、最適な条件を見つけ出すことができます。さらに、加工の精度を上げるためには、工具の摩耗を常にチェックし、適時に交換する必要があります。この循環的なプロセスを通じて、SKフライス加工の技術は向上し、高品質な試作品を創出することが可能になるのです。
4. SK フライス加工 試作のための材料選定
SKフライス加工による試作品の成功は、適切な材料選定から始まります。試作においては、目的や使用条件に応じた材料が求められ、材料の特性が加工品質に直結するため重要です。例えば、耐熱性や耐摩耗性を必要とする部品では、それに適した特殊な合金が選ばれることが一般的です。また、試作段階ではコストも考慮し、無駄な投資を避けるためにも実際の使用環境を想定した材料選びが必須となります。成功の鍵を握るのは、これらの条件を満たす材料を見極めることであり、そのためには豊富な知識と経験が要求されます。結論として、SKフライス加工における試作段階での材料選定は、製品の品質を左右するだけでなく、コストパフォーマンスを考慮した上で、最終的な成功に直結する重要なプロセスであると言えます。
5. SK フライス加工と旋削加工の比較
SKフライス加工は成功の試作に不可欠であることは、その精度と効率において明らかです。この技術は、特に複雑な形状や精緻な部品が求められる場面において、その真価を発揮します。例えば、航空宇宙産業や精密機器の部品製造では、高い精度と複雑な形状が要求されるため、SKフライス加工は理想的な解決策となります。また、小ロットでの柔軟な対応が可能であり、試作段階での様々な調整に迅速に対応できる点も、SKフライス加工の大きなメリットです。試作品の成功は結果に直結するため、SKフライス加工の基本を押さえ、応用テクニックを習得することで、製品開発の効率化と市場への速やかな導入が可能となります。このように、SKフライス加工は試作から製品化に至るまでの過程をスムーズにすることで、成功へと導く重要なプロセスといえるでしょう。
6. SK フライス加工 試作に最適なツールの選び方
試作品の品質向上と効率化を目指すSKフライス加工では、適切なツール選びが重要です。その理由は、試作段階で求められる精度と加工速度に適切なツールが不可欠だからです。たとえば、複雑な形状を持つ部品の加工には、細かいディテールに対応できる高精度のエンドミルが求められます。一方で、大量の材料を速やかに除去する必要がある場合は、大きな切れ刃を持つカッターが適しています。加えて、SKフライス加工における材料の特性に応じて、刃の材質やコーティングの種類も選び方の重要な要素になります。このようにして、最適なツールを選ぶことで、試作はより精度が高く、時間とコストを省くことが可能になります。最終的に試作の成功は、品質、スピード、コストのバランスが取れたツール選びから始まるのです。
7. SK フライス加工の試運転マニュアル
SKフライス加工は、精密な部品製造に不可欠な工程です。試作の成功は、製品開発の効率を大きく左右するため、基本と応用テクニックの理解が重要です。まず、加工する材料やフライス盤の特性を把握し、適切な切削条件を選定することが基本です。たとえば、アルミニウム合金なら高速切削が可能ですが、硬質材料では低速で慎重に進める必要があります。また、刃の交換時期の見極めや冷却液の適切な使用も、精度を保つ上で欠かせません。具体的な応用テクニックとして、工具の振動を抑えるための工夫や、複雑な形状の加工に対する工夫があります。試作段階でこれらのテクニックを駆使することで、製品の精度向上とコスト削減につながります。結論として、基本をしっかり押さえ、目的に応じた応用テクニックを採用することが、SKフライス加工における試作の成功を導く鍵となるのです。
8. SK フライス加工 試作プロジェクトの事例紹介
SKフライス加工は、試作品作成においてその精度と効率から多くの企業に採用されています。この技術は、複雑な形状や精密なパーツ製造に特に優れた能力を発揮し、産業全体にイノベーションをもたらす潜在性を持っています。例えば、自動車産業や航空産業では、極めて高い寸法精度が要求される部品をSKフライス加工で試作し、製品開発のスピードを大幅に向上させています。また、プロトタイピングの段階で生じる材料の無駄を削減し、コスト効率を高める効果もあります。このようにSKフライス加工は、幅広いアプリケーションに適した柔軟性と高い精度を兼ね備えており、成功への道を切り開く確かな技術であると結論づけられます。
9. SK フライス加工 試作のトラブルシューティング
SKフライス加工は試作品の製作において欠かせない工程であります。試作の成功は、製品開発のスピードと品質に直接影響を与え、そのためには基本的なテクニックの理解が必要です。SKフライス加工では、材料の種類や形状、加工条件などに応じて切削速度や送り速度を適切に設定することが肝心です。例えば、アルミニウムなどの軟らかい材料では速い切削速度で加工が可能ですが、硬度の高い鋼では速度を落とし、切削液を適切に使用することが重要です。また、複雑な形状の試作品を作成する場合には、多軸制御のフライス盤を用いて精密な加工を行うテクニックが求められます。これらの基本と応用を組み合わせることで、高品質な試作品の作成に繋がり、製品開発の成功へと導かれます。
10. SK フライス加工 試作の将来展望
SKフライス加工は試作品製作において重要なプロセスの一つです。この技術は高い精度と複雑な形状の加工が可能で、試作の成功へと大きく寄与します。理由として、SKフライス加工は、切削工具の微妙な調整が可能であり、材料の無駄を最小限に抑えつつ、品質の高い加工を行えるからです。具体的な例として、航空宇宙産業における部品製作や自動車産業におけるモックアップの製作などが挙げられます。これらの分野では、極めて高い精度が求められるため、SKフライス加工の精密な技術が不可欠です。結論として、SKフライス加工は試作の品質を大きく左右する技術であり、その応用範囲の拡大が今後の製造業での成功をより確実なものにするでしょう。
まとめ
SKフライス加工は試作品を作成する際に重要な加工技術です。正確な寸法や形状を得るためには、基本的な加工技術だけでなく、応用テクニックも理解することが重要です。特に、複雑な形状を持つ部品の加工には高度なテクニックが要求されます。適切な工具選びや加工条件の設定、適切な冷却・潤滑などを行うことで、高品質な試作品を製作することが可能です。