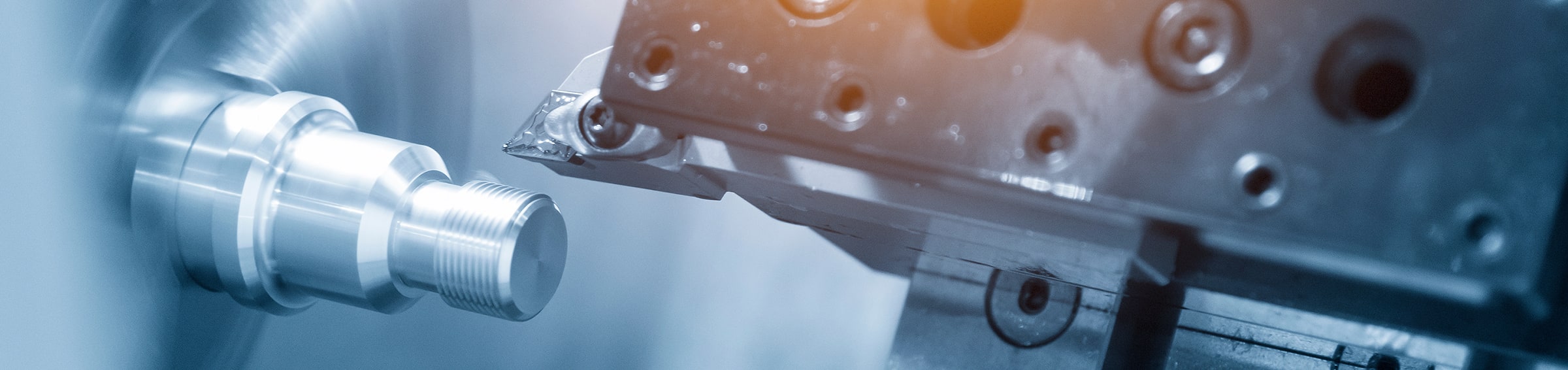
加工技術 column
【2023年最新】SS穴あけフライス加工の効率的な進め方とは?
2023年の最新技術として注目されているSS穴あけフライス加工。その効率的な進め方について知りたいと思っていませんか?この記事では、SS材料の穴あけフライス加工について、効率的な進め方を解説します。SS穴あけフライス加工の基本から、効率的な進め方まで、すべてを網羅しています。これを読めば、SS穴あけフライス加工の効率的な進め方がわかるはずです。
1. SS 穴あけ フライス加工入門
SS穴あけフライス加工は、製造業における重要な工程の一つです。この加工方法は、金属部品を高い精度で加工する際に不可欠とされています。効率的な穴あけフライス加工を行うためには、正確な設計図を基に、適切な工具選択と速度設定が鍵となります。例えば、SS材質の加工には特に硬度の高いドリルが必要であり、加工速度や送り速度も材質の特性に合わせて慎重に選定する必要があります。また、クーラントの利用は切削面の品質を保ちながら摩耗を減らし、工具寿命を延ばすことができます。これらの要素を総合的に考慮し適切に設定することで、穴あけフライス加工はより効率的かつ品質の高い結果をもたらします。結論として、適切な工具選択と速度設定、クーラントの使用はSS穴あけフライス加工の効率化に不可欠であり、これらを熟知していることが高品質な製品を生み出すためのカギです。
2. ステンレス穴あけ加工の基礎知識
ステンレス穴あけフライス加工は、その高い精密度と効率性から、2023年も製造業界で広く採用されています。この加工方法の効率的な進め方を理解することは、コスト削減と品質向上に直結します。まず、適切な工具の選定が重要です。耐久性と切削速度に優れたカッターを選ぶことで、加工時間を短縮し、製品の精度を保つことができます。さらに、適正な切削条件の設定は必須です。スピンドルの回転数や送り速度を材料の種類や厚みに応じて最適化することで、加工の負担を減らし、切削工具の寿命を延ばすことが可能です。具体例として、多層コーティングされたエンドミルはステンレス加工に適しており、長寿命かつ安定した加工が行えることが実証されています。最後に、加工後の冷却・潤滑剤の適切な使用も、仕上がりの質を左右します。結論として、適切な工具の選定、切削条件の最適化、冷却・潤滑剤の使用を徹底することにより、SS穴あけフライス加工の効率性と品質を向上させることができるのです。
3. SS 穴あけ フライス加工の効率化テクニック
SS穴あけフライス加工を効率化することは、工業生産性の向上に寄与します。このプロセスの最適化は、正確な計測と適切な工具選定から始まります。例えば、多様な工具径を用いることで、穴あけ加工時の振動を抑制し、高精度な加工を実現できるのです。また、新しいコーティング技術が施されたカッターの使用は、耐久性の向上とメンテナンスの頻度低減にも繋がるでしょう。加工パラメータの最適化、すなわち回転数や送り速度の調整も重要です。こうした具体的な改善策を施した結果、作業時間の短縮と品質の向上が見込まれます。結論として、機械設定や工具選定に注意を払い、継続的な改善に努めることがSS穴あけフライス加工の効率化への鍵であると言えます。
4. フライス加工のための切削性とは
SS穴あけフライス加工では、効率的な進め方が重要です。この加工法は、耐久性や精密さが求められるため、適切な工具選びと切削条件の設定が必須となります。例えば、SS材に適した高速度鋼や超硬合金のドリルを選び、適切な速度で穴あけを行うことがポイントです。さらに、切削油の使用による冷却や、スパイラルフルートの採用による切りくずの排出効率の向上が具体的な例です。これらを適切に行うことで、工具の摩耗を減らし、精度の高い加工を維持することができます。最適な方法で穴あけフライス加工を行うことで、作業効率の向上とコスト削減を実現できるのです。
5. SS 穴あけにおける旋盤加工のコツ
最新のSS穴あけフライス加工を効率的に進めるには、正しい工具選びと工程の最適化が必要です。まず、材質や加工する穴のサイズに適したフライスドリルを選ぶことが大切で、耐摩耗性や切削速度に優れたものを選ぶと作業効率が大幅に向上します。さらに、加工前の段取りをしっかりと行い、CNC(コンピュータ数値制御)プログラムの事前設定も精密にすることで、作業の正確性が保たれ、無駄が省けます。実際に、効率的な工程管理と適切な工具使いによって、加工時間を短縮した例は数多く報告されています。最終的に、効率的なフライス加工は、正確で迅速な穴あけを可能にし、生産性の向上に繋がるのです。これらのポイントを押さえておけば、2023年もSS穴あけフライス加工を成功させることができるでしょう。
6. レーザー加工の基礎とSS 穴あけ
SS穴あけフライス加工は、高精度で複雑な穴の加工が可能であり、2023年現在においても効率的な加工方法の一つです。この加工方法が注目される理由は、その精度とスピードにあります。特に、難削材であるステンレス(SS)に対しても優れた加工能力を発揮するため、多様な工業製品の製造に欠かせない技術となっています。具体例を挙げると、自動車や航空機の部品、医療器具など、耐食性や耐久性が求められる製品において、SS穴あけフライス加工は重要な役割を果たしています。この加工方法の効率化のためには、適切な工具選択、切削条件の最適化、そして定期的なメンテナンスが不可欠です。結論として、SS穴あけフライス加工の効率化は、これらの要素を適切に管理し、最新の加工技術を取り入れることでさらなる品質向上と生産性の向上が期待できます。
7. 穴あけ加工(ドリリング)の方法と選択
2023年におけるSS穴あけフライス加工を効率的に進める方法は、適切な工具の選定と加工条件の最適化にあることが結論として挙げられます。SS穴あけフライス加工は、ステンレス鋼などの硬質材料に対して高精度な穴を開ける工程で、工具の選択がその品質と効率に直結します。具体的には、耐熱性や耐摩耗性に優れたカーバイド製のドリルや、切れ味の良いコーティングが施されたフライスなどが推奨されます。また、適切な切削速度や送り速度といった加工条件を設定することで、摩耗を抑えつつスムーズな加工を実現できます。特にステンレス鋼は摩耗や熱影響による工具のダメージが生じやすい材料であり、こうした最適化が必須です。最終的に、適切な工具選定と加工条件の見直しを通じて、SS穴あけフライス加工の効率を大幅に向上させることが可能となります。
8. 切削加工における設計の配慮点
SS穴あけフライス加工を効率的に進めるには、適切な工程計画と最新の工具の選定が重要です。まず、加工対象のSS材が持つ特性を理解し、それに合わせた切削条件を設定することが、加工精度の向上と工具の耐久性を高めるポイントです。例えば、SS材特有の粘り強さに対応するため、高い切削速度と適切な送り速度を見極める必要があります。さらに、最新のコーティング技術を施したフライス工具を使用すると、耐摩耗性が向上し長寿命化を実現でき、コスト削減にもつながります。結論として、SS穴あけフライス加工は、素材の特性を踏まえた適切な切削条件の設定と先進工具の利用により、効率的かつ経済的に進めることが可能です。
9. SS 穴あけ フライス加工のトラブルシューティング
SS穴あけフライス加工は、金属加工の分野で高効率と精度を求められる作業です。適切な進め方を理解することで、作業の効率が大きく向上します。まず、適切な工具選定が重要です。具体的には、加工物の材質や厚みに応じたフライスカッターを選ぶ必要があります。例えば、ステンレス材の場合は、耐熱性や耐摩耗性に優れたカッターの使用が推奨されます。次に、適正な切削速度と送り速度の設定が加工精度に影響を及ぼします。低い速度では時間がかかりすぎ、速すぎるとカッターの損耗や加工物の損傷の原因となります。また、冷却液の使用は、加工中の熱を効果的に逃がし、工具と加工物の寿命を延ばすことに寄与します。結論として、適切な工具の選定、速度設定、冷却方法の理解により、SS穴あけフライス加工を効率的に行うことができます。
10. 最新機器によるSS 穴あけ フライス加工の未来
SS穴あけフライス加工が効率的に行われることは、精密部品製造の効率を大きく左右します。加工の精度とスピードは、生産の効率化に直結するため、2023年の最新の進め方を理解することが重要です。具体的には、最新のCNC技術を搭載した機器の導入が挙げられます。これにより、プログラムに従って自動で高精度な加工が行えるため、人的ミスが減少し、生産性が飛躍的に向上します。また、耐久性と加工速度を兼ね備えたカッターやドリルの選定も、効率化を促進します。実際には、マルチタスク加工機の使用や、チップの形状に工夫を凝らした新しい切削工具の開発など、多角的にアプローチすることで、加工時間の短縮とコスト削減が実現されています。最新技術の駆使は、高い品質の維持とコストパフォーマンスの良さを両立させる鍵です。
まとめ
SS穴あけフライス加工は、正しい工具と適切なスピード、フィードレートを使うことで高い精度と効率を得ることができます。適切な冷却剤を使用することで切削時の熱を逃がし、工具の寿命を延ばすことができます。工具選びや加工条件の最適化によって、作業効率を大幅に向上させることができます。
SSに穴あけ!フライス加工の基本から応用までを学ぶ
フライス加工において、SSに穴をあける方法を学びたいと思っていませんか? この記事では、初心者向けから応用まで、SSに穴をあけるためのフライス加工の基本について詳しく解説します。フライス加工における穴あけの重要性や技術、応用例について知りたい方にとって、この記事は必見です。さあ、フライス加工の世界へ一歩踏み出してみましょう!
1. SS 穴あけ フライス加工の概要と基本
SS穴あけフライス加工は、工業分野での金属加工における基本技術の一つであり、多くの分野で応用されています。この加工方法では、特殊なカッターを使用してステンレス鋼(SS)に正確な穴を開けることができます。その理由としては、フライス加工が高い精度と良好な仕上がりを提供するからです。例えば、航空機の部品や医療機器など、高い耐久性と精密さが求められる製品製造において、SSフライス加工は重要な役割を果たします。最終的には、SSフライス加工を理解し、その技術を習得することで、品質の高い製品を効率良く生産することが可能となります。これが、フライス加工の基本から応用までを学ぶことの価値を示しています。
2. 異なる金属材料の特性とSS 穴あけ フライス加工への影響
ステンレス(SS)の穴あけにおいてフライス加工は、精度と効率を求められる作業です。SSは硬度が高く耐食性に優れているため、加工する際には適切な技術と知識が不可欠です。たとえば、SSの硬質性により切削には強い力が必要となりますが、力の加減一つで加工精度に大きな差が出てしまいます。フライス加工の際には、切削速度、送り速度、刃の選択が特に重要で、これらを適切にコントロールすることで、高品質な穴あけ加工が可能となります。例えば、スローフィードかつ高速回転で加工することで、SSのような硬質材料でも滑らかな表面仕上げを実現できます。結論として、SSにおける穴あけフライス加工は、材料の特性を理解し、適切な加工条件を選択することが成功の鍵となります。
3. SS 穴あけ フライス加工の技術と方法
SS(ステンレススチール)に穴をあけるフライス加工は、精密な作業が求められる工程です。この技術の学習は、基本から応用まで段階を踏むことで、幅広い加工が可能になります。まず、フライス加工には適切な切削工具の選定が重要であり、SSの硬さや加工する穴のサイズに応じたドリルビットを選ぶ必要があります。例えば、小径の穴加工には高速度鋼(HSS)のドリルが適していますが、大きな穴を加工する場合には、カーバイドドリルやコーティングドリルを選択することが一般的です。また、クーラントの使用は、切削熱を抑制し、工具の寿命を延ばす上で効果的です。応用的な技术としては、ステップドリルやカウンターシンクを使って、穴の形状を工夫することもできます。これらの工具を使いこなすことで、SSのフライス加工技術をより深く理解し、多様なニーズに応えることが可能になります。最終的に、確実な技術を身につけることで、SS材料の加工の幅が広がり、製品の品質を向上させることができるのです。
4. SS 穴あけ フライス加工における短納期の戦略
フライス加工は、SS(ステンレス鋼)などの金属材料に穴をあける際に不可欠な技術です。精密かつ効率的な穴あけを可能にするためには、基本から応用までの知識が求められます。例えば、SSの穴あけ加工では、材料の硬さに適した工具選びや、適切な速度で工具を回転させることが重要です。これにより、効率よく且つ精度高く穴を開けることができ、製品の品質を保つことができます。また、熱処理や冷却剤の利用は、工具の摩耗を防ぎ、長期にわたる使用に耐える仕上がりを実現します。効率的なフライス加工をマスターすることで、短納期での対応が可能になり、競争力のある製造業へとつながるのです。最終的には、これらの技術を駆使することで、時間とコストの削減に繋がり、顧客満足度を高めることができるのです。
5. オーダーメイドSS 穴あけ フライス加工サービスの選び方
SS(ステンレス)に穴をあけるフライス加工は、精密性が要求される技術です。この技術は、耐食性や強度に優れるSSの加工を可能にし、様々な産業で必要とされています。例えば、自動車や医療機器などの部品に穴を開ける場合に使用されます。ここで大切なのは、正確な加工が可能な機械を選ぶこと、そして経験豊富な技術者による操作が欠かせません。さらに、穴のサイズや形状、SSの種類に応じて最適な切削条件を選定することで、高品質な加工が実現します。オーダーメイドのフライス加工サービスを選ぶ際には、これらの点をしっかりと確認し、信頼できるサービス提供者を見極めることが重要です。結論として、SSの穴あけには専門的な知識と技術が必要であり、適切なサービス選びが品質を左右すると言えるでしょう。
6. SS 穴あけ フライス加工の深さの限界と機械選定
ステンレス(SS)の穴あけにフライス加工は欠かせない工程ですが、この工法には深さの限界と適した機械選定が重要です。フライス加工は材料の表面に複雑な形状を付けることが可能で、精密な穴あけが求められるため、限界の理解と正確な機械選びが不可欠です。例えば、フライス加工機の種類には横型と縦型があり、穴の深さや形状により最適な機械が異なります。また、切削速度やチップの材質も深さに影響を与えるため、事前の計画が大切です。設備に適したパラメータの設定により、SS材に正確でクリーンな穴をあけることが可能になります。結論として、フライス加工における穴あけの深さの限界を把握し、目的に応じた機械選定を行うことで、品質と効率の良い加工が実現できるのです。
まとめ
SSに穴をあける際には、硬さに注意しながら適切な工具と適切な切削条件を選択することが重要です。また、フライス加工では切削速度や切り込み深さを適切に設定し、クーリング効果を高めるために切削液を使用することも大切です。基本的な技術を習得したら、応用技術として穴の形状や位置によって変える必要があります。
【工業加工】SS素材の穴あけフライス加工の基礎知識と技術
工業加工の分野でSS素材を扱う際、穴あけフライス加工は重要な技術の一つです。本記事では、SS素材の穴あけフライス加工の基礎知識と技術について解説していきます。SS素材の特性や穴あけフライス加工の手法、適切な工具の選び方など、初心者から上級者まで幅広く役立つ情報を提供しています。工業加工における基本的なスキルや知識を身に付けたい方々にとって、この記事は貴重な参考になることでしょう。
1. SS 穴あけ フライス加工の概要
SS素材の穴あけフライス加工は、精密な工業生産において重要な技術です。この加工法は、耐食性や強度を持つステンレス鋼(SS)に正確な穴を開けることができます。理由として、SS素材は硬質で加工が難しいため、専用の工具や技術が必要となります。たとえば、工具の選定では、耐熱性や耐摩耗性に優れたものが適しており、加工時の速度や冷却方法にも注意が必要です。具体例として、航空機や医療機器の部品製造には不可欠な技術であり、その精度と品質は安全性に直結します。最終的に、SS素材の穴あけフライス加工は、特殊な素材を使用することで高い精度と品質を実現し、多岐にわたる産業での需要が高まっています。
2. 穴あけ加工の基礎知識
SS素材への穴あけフライス加工は、正確かつ効率的な工業加工技術の一つとして重要です。この加工は、強度の高いステンレス鋼(SS)に特化しており、精密な機械部品を始め、多岐にわたる製品に組み込まれています。なぜSS素材が選ばれるのかというと、その耐食性と強度にあります。例えば、医療機器や食品加工機械では、衛生的な材質が必須で、SSはそれを満たす材料の一つです。穴あけ加工自体は、専用のカッターやドリルを使用してSS素材に所定の位置、所定のサイズの穴を開ける作業です。しかし、この作業には技術が要求され、加工時に生じる熱や切り屑の除去、工具の摩耗に注意を払う必要があります。これらの課題を解決するため、適切な切削液の選定や工具の冷却が不可欠です。結論として、SS素材の穴あけフライス加工は、選ばれる材料の特性を理解し、適切な工具と技術を用いることで、産業界における精密加工の要となり得るのです。
3. SS 穴あけ工具の種類と特徴
SS素材の穴あけフライス加工は、精密な製造が要求される工業分野で重要な技術です。結論から述べると、この加工技術は高い耐久性と強度を持つSS素材の特性を活かし、様々な製品の品質と性能を向上させるために不可欠です。その理由は、SS素材が耐食性や耐熱性に優れ、医療機器や自動車部品など幅広いアプリケーションで利用されているからです。例えば、医療分野では、患者の安全を確保するための器具には耐食性が求められ、フライス加工により精密な穴あけが不可欠となります。自動車産業では、耐久性が要求される部品にSS素材が使用され、精確な穴あけが品質の保証に直結しています。最終的に、これらの具体例を通じて、SS素材に対する穴あけフライス加工技術は現代の製造業において必要不可欠であるという結論に至ります。
4. 高速・高精度SS 穴あけ フライス加工技術
SS素材の穴あけフライス加工は製造業において不可欠な技術です。SS素材はその耐食性や強度の高さから多くの工業製品に利用されていますが、加工が難しいという特性を持っています。穴あけフライス加工の技術は、製品の精度を左右するだけでなく、生産効率にも大きな影響を与えるため、技術の習得は業界において重要です。例えば、自動車の部品や医療機器など、精密な加工が必要なアプリケーションでは、高速かつ高精度なフライス加工技術が求められます。適切な工具選択、適用される速度やフィード、冷却液の使用方法など細部にわたる知識が不可欠であり、これらは全て加工品質に直結します。熟練した技術者による適切な加工技術は、耐久性や精度を高め、最終製品の信頼性を保証するのです。
5. 超硬鉄工用ドリルとSS 穴あけ加工の関係
SS素材における穴あけフライス加工は、精密で緻密な工程が求められるため、基礎知識と技術が不可欠です。この加工には、正確な穴の位置決めと寸法を守ることが重要であり、使用されるドリルの選択にも技術が必要です。例えば、超硬鉄工用ドリルは硬度が高く耐久性に優れ、SS素材のように硬い材料を加工する際に効果的です。その鋭い切削面は、滑らかな穴あけを実現し、製品の品質を向上させることができます。さらに、フライス加工においてはクーラントの使用も重要で、加工中の発熱を抑えることで、工具の摩耗を減らし、精度を保つことができます。結論として、SS素材の穴あけフライス加工においては、適切な工具の選択と加工技術が、最終製品の品質を決定づける要素であると言えます。
6. 一般構造用圧延鋼材(SS材)の特性
SS素材の穴あけフライス加工は、精密な工業製品を作る上で不可欠な技術です。この理由は、SS素材がその耐久性と強度から多くの工業製品で用いられるためです。例えば、自動車や建築物の部品など、日常的に接する多くの製品がSS素材で作られています。穴あけフライス加工によって、これらの製品は必要な箇所に正確な穴を開けることが可能になり、組み立てや機能の向上に寄与しています。この技術がなければ、現代の製造業は大きな制約を受けるでしょう。したがって、SS素材の穴あけフライス加工に関する基礎知識と技術を理解し、習得することは極めて重要であり、工業製品の品質を決定づける要素とも言えます。
7. SS 穴あけ フライス加工の応用例
フライス加工は、SS(ステンレススチール)素材の加工において重要な技術であり、特に精密な穴あけ加工が必要とされる場面でその真価を発揮します。この加工技術が注目される理由は、SS素材の優れた耐食性と強度にあります。これにより、医療機器や食品機械といった厳しい環境要求を満たす製品に使用されることが多いです。具体例を挙げると、フライスを用いた高精度な穴加工は、ピッチや深さが正確に制御されることで、部品の組み合わせ精度を向上させ、製品の信頼性を高める効果があります。これには、工具の選定や切削条件の最適化が不可欠です。結論として、SS素材の穴あけフライス加工は、高品質な製品の製造において不可欠な技術であり、その基礎知識と技術の習得は非常に重要であると言えます。
8. SS 穴あけ フライス加工のトラブルシューティング
SS素材の穴あけフライス加工は精密な工程を要する作業です。なぜなら、SS(ステンレススチール)は硬度が高く、耐食性に優れているため加工が難しいからです。具体的な例として、フライス加工時には適切な切削速度の選定や、冷却剤の使用が重要になります。これらはSS素材の加工時に発生しやすい、切削熱による変色や工具の摩耗を防ぐためです。さらに、加工面の滑らかさを保つためにも、細かい注意を払う必要があります。結論として、SS素材の穴あけフライス加工を成功させるには、適切な工具選定や加工条件の管理が極めて重要であり、これらの技術がトラブルシューティングの鍵となるでしょう。
まとめ
SS素材の穴あけフライス加工においては、適切な工具の選択が重要です。適切な刃先形状や切れ刃数、切れ刃の材質などを考慮することで、高品質な穴あけ加工が可能となります。また、適切な切削速度と送り速度の設定も重要です。これらの基礎知識と技術を習得することで、SS素材の穴あけフライス加工において高い精度と効率性を実現することができます。
フライスで穴を開ける!SS素材加工のための詳細ガイドとヒント
フライスで穴を開けるための効果的な方法とヒントを知りたいですか?この記事では、SS素材の加工に焦点を当て、フライス加工を使って穴を開ける方法について詳しく解説します。SS素材加工のための詳細ガイドとヒントをまとめたので、ぜひ参考にしてください。
1. フライス加工の基礎
フライス加工は、SS素材に穴をあける際に選ばれる重要な方法です。なぜなら、フライス加工は精密かつ効率的であり、多様な形状の穴開けが可能だからです。例えば、円形、長穴、あるいは複雑な内部形状を持つ穴など、フライス加工を用いることで細かな調整が行えます。特に、SS素材のような硬質な材料を扱う場合、フライスはその切削能力と汎用性で抜群の性能を発揮します。ただし、フライスでの穴あけ作業には適切な刃の選定や冷却方法の理解が不可欠です。具体例を挙げると、SS素材加工専用の刃を選び、適切な速度で加工を行うことで、材料を傷めることなく滑らかな表面を得ることができます。このように、フライスを使用する際は、材料の特性を理解した上での適切な準備が重要という結論に至ります。
2. SS 穴あけ フライス加工の手順とテクニック
SS素材のフライス加工は精密な作業が求められ、特に穴あけ工程においては細部に注意を払うことが重要です。フライスで穴を開ける際、適切なスピンドルスピードとフィードレートの選定は不可欠であり、これには素材の硬度や切削工具の特性を考慮しなければなりません。具体例として、SS素材に対しては、HSS(高速度鋼)やカーバイド(超硬質)のドリルビットが推奨されます。また、冷却液を使用することで、熱の発生を抑え、工具の摩耗や材料の損傷を防ぎます。このように適切な準備と正しい手順を踏むことで、SS素材に対しても精度の高い穴あけ加工が可能になります。最終的に、品質の高い製品を製造するためには、準備段階から加工完了まで細心の注意が必要です。
3. 素材別フライス加工のポイント
SS素材に穴あけを行う際のフライス加工は、精度と効率を考慮する必要があります。SS素材はステンレスのことで、耐食性や耐熱性に富む一方で、硬度が高いため加工が難しい特性を持っています。適切なフライスを選ぶことで、これらの課題を克服し、正確な穴あけが可能となります。例えば、フライス選びでは、SS素材の硬さを考慮した刃先の材質やコーティングがポイントとなります。また、切削速度や送り速度の設定も重要で、これらを適切に調整することで加工時のバリの発生を抑え、滑らかな表面仕上げを実現できます。さらに、冷却液を適切に使用することで、切削熱の影響を軽減し、工具の寿命を延ばすこともできます。総じて、フライスでSS素材に穴をあけるには、工具の選定、運転条件の最適化、冷却管理の徹底が成功の鍵を握っています。
3-1. SS400でのフライス加工のコツ
SS400素材におけるフライス加工で穴を開ける際は、特有の工夫が求められます。この素材は一般的な構造用鋼材であり、その加工性は良好ですが、適切な工具選定と加工条件の設定が重要です。具体例として、切削速度や送り速度の適正化、またはフライスカッターの歯数や形状の選定が挙げられます。これらを適切に調整することで、穴あけ時のバリの発生を抑制し、精度の高い加工を実現することが可能です。最終的には、SS400素材でも、フライス加工による穴あけは、適切な知識と技術で高精度な結果をもたらすことができるのです。
3-2. S45C素材のフライス加工
S45C素材にフライス加工で穴をあける際、正確な作業を行うことが非常に重要です。S45Cは一般的な炭素鋼で、硬度と加工性のバランスが取れているため、機械部品の製造に広く利用されています。しかし、フライス加工には適切な工具選びと条件設定が不可欠です。例えば、切削速度や送り速度、刃の数などを材質に合わせて調整することで、精密な穴あけが可能になります。さらに、工具の摩耗を防ぐために、適切な冷却液を使用することも重要です。フライス加工は繊細な作業であるため、詳細なプランニングと正確な施工が要求されるのです。これらのポイントをしっかり押さえておけば、S45C素材の加工はより効果的かつ効率的に行えるでしょう。最終的には、正しい知識と技術を駆使することで、高品質な製品が生産されるのです。
4. SS 穴あけ フライス加工における旋盤との違い
SS素材に穴を開ける際にフライス加工を選ぶ理由は、精密さと効率性にあります。フライス加工では、多様な形状の穴を一度に加工することが可能です。例えば、正方形や不規則な形状など、旋盤での加工が難しい形状でもフライスなら簡単にこなすことができます。さらに、フライスは旋盤と違い、固定された材料に対してカッターが動くため、より複雑な加工が可能となり、加工時間の短縮にもつながります。そのため、効率的で柔軟な穴あけ加工を行いたい場合には、フライス加工が適しています。結論として、SS素材の加工においては、フライス加工の方が旋盤加工よりも優れた選択であると言えるでしょう。
5. SS 穴あけ フライス加工と複合加工の統合
SS素材の加工には特有の注意点が必要であり、フライスを使用して穴を開ける際には、正確さと効率性が求められます。フライス加工では、SS素材の硬さや粘りに対応するため、適切な切削速度や冷却液の使用が重要です。例えば、硬い素材には低い切削速度を選び、刃の摩耗を防ぐために冷却液を多用するといった工夫が必要です。また、穴あけ加工においては、フライスの種類に応じた正確な位置決めが、仕上がりの品質を左右します。このように適切な設定と正確な操作により、SS素材に穴を開けるフライス加工は成功に導かれます。最終的に、技術の向上と共に加工精度も高まり、満足のいく加工が可能になるのです。
6. 切削加工のための素材選び
切削加工では、素材選びが重要なポイントです。中でも、SS(ステンレススチール)素材は、その耐食性や強度の高さから、幅広い産業で利用されています。しかし、SS素材をフライスで加工する際には注意が必要です。この素材は硬いため、切削工具や条件を適切に選定しないと、工具の摩耗が早まったり、加工精度が低下する恐れがあります。例えば、穴を開ける場合には、多刃のエンドミルを使用し、切削速度や送り速度、冷却液の使用に気をつけることが重要です。特にSS素材の穴あけでは、工具の刃先角度やコーティングなど、細部にわたる工具の特性を考慮する必要があります。適切な加工条件でフライスを用いれば、SS素材の穴あけでも高い精度と効率を実現できます。このように、SS素材をフライスで加工する際には、素材の特性を理解し、適切な工具と条件の選定が成功の鍵となります。
7. 全国対応のフライス加工サービスの選び方
SS素材にフライス加工で穴を開けることは、精密さと技術が要求される作業です。この作業が重要なのは、正確な穴径と仕上がりが必要な機械部品などに使用されるからです。フライスは回転する刃を使い、素材を削りながら穴を開ける工具で、SS素材のような硬い材料にも適用可能です。例えば、自動車やバイクの各部品には、フライス加工により正確な穴が開けられています。穴の精度を左右する重要なポイントは、フライスの刃の選定、切削条件の設定、そして機械の精度です。これらの要素が適切に管理されていれば、高品質な加工が保証されます。最適なフライス加工サービスを選ぶ際には、加工機の性能、担当者の技術力、過去の実績をしっかりと確認しましょう。そうすることで、求める品質のSS素材加工が実現されるのです。
まとめ
SS素材をフライス加工で穴あけする際には、適切な工具選びや切削条件の設定が重要です。SS素材は加工が難しい素材の一つであり、高硬度や高強度を持っているため、適切な工具と切削条件を設定することが必要です。適切な冷却剤を使用することで加工効率を向上させることができます。また、穴あけ加工においては適切な切削速度や切りくず排出方法も重要です。
フライス加工初心者向け!SS素材への穴あけの正しい進め方
フライス加工を初めて行う方にとって、SS素材への穴あけは正しい進め方を知ることが重要です。この記事では、フライス加工初心者向けにSS素材への穴あけの手順やポイントを分かりやすく解説します。SS素材の特性やフライス加工の基本、穴あけの方法について詳しく説明します。フライス加工の世界への第一歩を踏み出したい方におすすめの内容となっています。
1. SS 穴あけフライス加工入門
フライス加工におけるSS素材への穴あけは、初心者にとって難しい作業の一つですが、正しい進め方を理解すれば容易なものになります。まず、SS素材はステンレスの略で、その硬さから正確な穴位置と滑らかな仕上がりを実現するには適切な工具選びが必須です。例えば、鋭い刃先を持つコーティングドリルは、SS素材に対して効率的な穴あけを提供します。また、切削速度や送り速度の設定も重要で、適正な設定により加工にかかる時間を短縮し、素材への負担を最小限に抑えることができます。具体的には、SS素材の場合、一般的な鋼材よりも低めの速度で加工することが推奨されます。初心者でもこれらの基本に注意すれば、SS素材への穴あけに成功しやすくなり、フライス加工の技術を一層磨くことができるでしょう。
2. 金属加工におけるSS素材の選定ポイント
フライス加工でSS素材へ穴あけを行う際は、正しい手順を理解し、適切な方法で進めることが重要です。まず、SS素材を選定するにあたっては硬度や耐食性を考慮することが大切です。SS素材は耐久性に優れているため、適切な工具と技術を使いこなさなければ加工は困難です。具体的には、適切な切削油を使用して切削抵抗を減らし、摩擦熱を最小限に抑えることがポイントです。また、工具の選定では、SS素材に適したドリルの角度や素材を選び、回転速度や送り速度も慎重に設定する必要があります。例として、多くの場合、高速度鋼(HSS)や超硬合金が用いられることが一般的です。結論として、フライス加工におけるSS素材への穴あけは、適切な選定と加工条件の設定が成功への鍵となります。これらのポイントを押さえることで、初心者でも安全かつ効率的に作業を進めることができるでしょう。
3. 金属加工の難しさとSS 穴あけフライス加工の理解
フライス加工は精密な技術を要する作業であり、特にSS(ステンレス)素材への穴あけはより高度な注意と正確な手順が必要です。理由として、SS素材はその硬さと粘り気のため、加工時のダメージが大きくなりやすいのです。適切な進め方としては、まず適正な切削速度の選定が重要です。速度が速すぎると、素材を過度に熱してしまい、加工面にダメージを与えやすくなります。また、フライスの刃先は常に冷却液で冷やしながら使用することで、発熱を防ぎ素材への負担を軽減します。具体的な例としては、小径のドリルビットを使用して徐々に大きさを上げていくステップドリリングが挙げられます。これにより、素材への負担を段階的に分散させながら加工を進めることができます。結論として、SS素材への穴あけでは、適正な切削速度の選定、冷却液による冷却、そして段階的な加工が鍵となります。これらを守ることで、フライス加工の初心者でもSS素材への穴あけを成功させることが可能です。
4. 切削加工の種類とSS 穴あけフライス加工の特徴
フライス加工は精密な穴あけに不可欠であり、特にSS(ステンレス鋼)素材においては、その正しい手順を守ることが重要です。SS素材はその硬さと耐食性から、多くの産業分野で利用されていますが、加工時には特有の注意点があります。先ず、適切な工具選びが重要であり、SS専用のドリルやフライスを選ぶことで、切削抵抗や発熱を抑えることができます。また、切削速度や送り速度の調整も重要で、SS素材の硬さに適合した設定にすることが肝心です。具体的な例として、穴あけ加工では低速回転に設定し、冷却液を適切に使用することで、切りくずの排出を助け、工具の摩耗を防ぎます。このように正しい方法でフライス加工を行うことで、SS素材への穴あけは精度良く、効率的に行えるのです。結論として、SS素材への穴あけには適切な工具の選択、速度設定、冷却方法が不可欠であり、これらを遵守することで初心者でも成功に導くことができます。
5. SS 穴あけフライス加工方法の基本
フライス加工の初心者の方にとって、SS(ステンレス鋼)素材への穴あけは一つの挑戦です。この作業を正しく進めることで、工具の寿命を延ばし、加工の精度も高めることが可能になります。まず、正しいドリル選びから始めましょう。SS素材は硬いため、硬質のドリルを選ぶことが重要です。例えば、コバルト高速度鋼や超硬合金が適しています。次に、ドリルの速度と送りの設定です。SS素材への穴あけには低速で安定した送り速度を心掛けることが肝心です。具体的な値は材質や厚みによって異なりますが、一般的には毎分30〜50メートルの切削速度が目安とされています。冷却液の使用も忘れずに、刃先の過熱を防ぎながら切削性能を維持しましょう。こうした正しい手順で穴あけを行なうことで、フライス加工のスキルを着実に向上させることができます。
6. 金属加工依頼先の選び方とSS 穴あけフライス加工の重要性
SS素材への穴あけフライス加工は、正しい技術を用いれば初心者でも上手に行えます。フライス加工では、素材の種類が重要な要素となりますが、特にSS(ステンレススチール)素材は硬度が高く扱いにくいとされています。そのため、穴あけ加工には適切な工具選びが不可欠です。例えば、ドリルの選定では、SS素材向けのものを使用し、低速で丁寧に加工を行います。さらに、切削油を適切に使用することで、摩擦熱を軽減し、切れ味を保つことができます。このように適切な工具と方法を選択することで、SS素材への穴あけも初心者にとって簡単な作業となり、加工精度を高めることが可能です。つまり、正しい進め方さえ押さえれば、SS素材への穴あけフライス加工は初心者でも成功に導けるのです。
まとめ
フライス加工において、SS素材への穴あけは正しい工具と追加冷却剤の使用が重要です。鋼材と異なり、SS素材は熱がたまりやすく、切削時に高温になりがちです。このため、十分な冷却が必要です。また、適切な切削速度と刃先の精度も注意が必要です。初心者がフライス加工を正しく進めるためには、これらのポイントに注意することが大切です。
SS穴あけフライス加工をマスターする!選ぶべき工具と操作方法
「SS穴あけフライス加工をマスターする!」というテーマに興味はありませんか?SS素材の穴あけフライス加工は、正しい工具と操作方法を選ぶことが成功の鍵です。この記事では、SS素材に特化した穴あけフライス加工のマスター方法について詳しく解説します。それでは、さっそく始めてみましょう!
1. SS穴あけフライス加工の基本概念
SS穴あけフライス加工が注目されているのは、精度高く複雑な穴形状を実現できるからです。この技術は、自動車や航空機の部品など、高精度が求められる分野で特に重宝されています。選ぶべき工具としては、刃径の精度やコーティングの種類、材質などが加工物に適したものを選択することが大切です。例えば、ステンレス鋼の加工には硬度が高く耐摩耗性に優れたカーバイドフライスが推奨されます。操作方法においては、フライスの回転速度や送り速度、切り込み深さの設定が重要です。正しい操作でなければ、工具の損耗や加工物の破損につながりかねません。このため、操作者はそれぞれの工具特性と加工物材質を理解し、適切な加工条件を見極める必要があります。要するに、SS穴あけフライス加工をマスターするには、適切な工具選びと正確な操作方法が鍵となるのです。
2. 切削加工の種類とSS穴あけフライス加工の位置づけ
SS穴あけフライス加工は高精度な穴を開けるために重要な工法です。この加工法は、耐久性や精度が高く、とりわけ金属加工において重宝されています。適切な工具の選択と操作方法の習得は、その成功の鍵を握っています。例えば、SS穴あけフライス加工には特別なフライスカッターが必要となり、選定時には材質や加工する穴のサイズ、形状が考慮されるべきです。また、運転手は速度や送りの設定を適切に管理し、ワークピースの冷却が適切に行われることを確認しなければなりません。これらの要素を正しく組み合わせることで、SS穴あけフライス加工はその真価を発揮し、加工精度が大幅に向上します。したがって、工具の選択と操作方法の習得はSS穴あけフライス加工をマスターするための基本となります。
3. SS穴あけフライス加工における穴あけの条件と種類
SS穴あけフライス加工は、精度の高い加工が可能で、工業製品の製造に不可欠です。選ぶべき工具は、材料の硬度や加工する穴のサイズによって異なりますが、一般的には高速度鋼(HSS)や超硬材料が推奨されます。操作方法にも注意が必要で、フライス盤の速度や送り速度を材料に適した数値に設定することが重要です。たとえば、ステンレス鋼の場合は硬度が高いため、低速で丁寧に加工を行う必要があります。また、冷却液を適切に使用することで、工具の摩耗を防ぎながら清潔な仕上がりを実現できます。これらのポイントを抑えることで、SS穴あけフライス加工をマスターし、高品質な製品を作り出すことが期待されます。
4. SS穴あけフライス加工で使用する工具の種類と特徴
SS穴あけフライス加工を理解し、適切な工具選びと操作方法の知識を身につけることは、工作の精度を高める上で欠かせません。穴あけフライス加工では、素材の硬さや加工する穴の大きさに適した刃物を選ぶことが重要です。たとえば、ステンレス(SS)材には強度の高いカッターやコバルトハイスドリルなどが好適で、長い寿命と精度の高い加工を実現できます。また、フライス盤のスピードや送り速度の正確な設定も、仕上がりの品質に直結します。具体的な操作では、適切なクーラントの選定や、チップの交換頻度の見極めが重要であり、これらをマスターすることで長期にわたり高品質な加工が可能となります。結論として、SS穴あけフライス加工の成功は、適切な工具の選定とその正しい操作方法の習得にあると言えるでしょう。
5. CNC加工技術とSS穴あけフライス加工
SS穴あけフライス加工をマスターするためには、適切な工具の選択と正確な操作が不可欠です。この技術は、精密な機械加工を要する場面で重要とされており、特に金属加工分野での利用が顕著です。適切なフライス工具を選択することで、材料の無駄が少なくなり、コスト削減にもつながります。また、操作方法をしっかりと学ぶことで、工具の寿命を延ばし、より精度の高い加工が可能になります。例えば、SS素材に細かい穴をあける際には、切削速度や送り速度を適切に設定することが重要です。これにより、加工面の仕上がりが良くなり、再加工の必要性を減少させることができるのです。最終的に、これらの知識と技術を身に付けることで、作業効率の向上と高品質な製品製造に寄与することが期待されます。
6. タップ選定の基準とSS穴あけフライス加工での応用
SS穴あけフライス加工は精密な作業が求められるため、適切な工具選びと操作方法が極めて重要です。この工程で最も大切なのは、材質に合ったタップの選定です。例えば、ステンレス材には硬度や耐食性に優れたタップを使用することが肝要となります。具体的には、コーティング技術が施されたタップが有効です。これにより、切削抵抗が下がり、寿命が延びるため、コストパフォーマンスも向上します。また、操作方法においては、適切な切削速度と冷却剤の利用が欠かせません。これにより、タップの摩耗を防ぎながら、精度の高い穴あけが可能になります。最終的に、正しい工具選びと正確な操作によって、SS穴あけフライス加工はその真価を発揮します。この技術をマスターするには、理論だけでなく実践を通じた経験が不可欠です。
まとめ
SS穴あけフライス加工をマスターするためには、適切な工具と操作方法を選ぶことが重要です。加工に適したフライス盤や切削油を使用し、適切な切削速度や刃先形状を選ぶことで穴あけ作業を効率的に行うことができます。また、加工する素材によって最適な工具や操作方法が異なるため、素材に合わせた選択肢を検討することが必要です。
量産に最適!SKDフライス加工の効果的な工程計画方法
もしもあなたが、SKDフライス加工の効果的な工程計画方法について知りたいと思っているのであれば、この記事はぴったりです。何をすればいいのか分からない、という方のために、SKDフライス加工についての完全ガイドを作成しました。この記事では、SKDフライス加工の基本、効果的な工程計画の方法、そして量産に最適な手法について詳しく紹介しています。
1. SKDフライス加工量産の序論
1-1. SKDフライス加工とは
SKDフライス加工は量産に最適な手法です。これは、一定の品質を維持しながら、高速で部品を製造できるからです。特に、SKD(Semi Knock Down)方式により、あらかじめ部分的に組み立てられた状態で部品を供給することで、組み立て工程の効率化が図れます。たとえば自動車産業においては、エンジンやトランスミッションといった複雑な部品をSKD方式で供給し、最終組み立てラインにて迅速に組み立てることで、生産時間の短縮とコスト削減が可能になります。この方法により、一貫生産では対応が難しい大量かつ多様な製品の需要に柔軟に応えることができるのです。従って、SKDフライス加工は、量産の必要性が高まる市場において、効果的な工程計画の方法の一つとして重要な役割を果たすことが結論付けられます。
1-2. 量産のメリットとチャレンジ
SKD(Semi Knocked Down)フライス加工は、部品の量産に非常に適しています。量産を行う上で効率的な工程計画は、コスト削減と生産性向上の鍵となります。特に、SKDフライス加工では、部品を半完成品の状態で製造し、最終組立を行うことで工程を細分化し、労力や時間の削減を図ることが可能です。例えば、一つの部品を完成させるのではなく、複数の工程に分けてそれぞれの工程に特化した設備や技術を用いることで、専門性を高め、効率的な量産を促進します。更に、SKDフライス加工においては、標準化されたパーツを利用することにより、予備部品の在庫管理が容易になり、総合的なコストの削減に寄与します。つまり、適切に工程計画を行うことで、SKDフライス加工は、量産におけるコスト効率と生産効率を同時に向上させることができるのです。
2. 金属加工とSKDフライス加工量産の比較
2-1. 加工性の要因と比較
SKDフライス加工は量産において極めて効果的な工程計画が可能です。加工性が良く、一度に多くの部品を生産できるため、コスト削減に大きく寄与します。例えば、特定の切削工具を使用することで、複数の部品に同時に加工を施し、生産効率を向上させることができます。また、加工工程を細分化し、それぞれの工程で最適な切削条件を適用することにより、精度の高い部品を均一に生産することが可能になります。SKDフライス加工の工程計画を適切に行うことで、時間とコストの削減、そして品質向上が期待できるため、量産において最適な加工方法と言えます。
2-2. SKDフライス加工量産の特徴
SKDフライス加工は量産に適していると言われています。その理由は、一度に多くの部品を高精度で加工できるからです。例えば、自動車産業においてSKDフライス加工は重宝されており、エンジン部品やフレーム部分の精密な加工が要求される際には、この手法が選ばれることが多いです。さらに効果的な工程計画により、生産効率とコスト削減を実現することが可能です。このような特徴からSKDフライス加工は、量産を伴う産業において欠かせない技術となっています。最適な工程計画と高い加工能力によって、日本の製造業の競争力を支える一翼を担うことでしょう。
3. WC 含有 Ti(C,N)基サーメットの特性
3-1. 合金炭素量と結合金属相
SKDフライス加工は量産において最適な方法の一つです。その理由は、SKD(Semi Knocked Down)の工程を採用することで、効率的な組み立てとコスト削減が可能になるためです。具体例を挙げると、部品の多くを予め加工しておくことで、現地での組み立て時間が短縮され、生産性の向上が期待できます。さらに、輸送時には部品をコンパクトにすることが可能なため、物流コストの削減にもつながります。このようにSKDフライス加工を効果的に計画することで、コスト削減と生産性の向上、そして競争力の強化を実現することができるのです。
3-2. SKDフライス加工量産への応用
SKDフライス加工は、量産の場面で大きな利点を提供します。その理由は、SKD(Semi Knocked Down)方式により製造工程が細分化され、各工程において特化した効率化が図れるからです。具体的な例として、組立前の部品製造では、部品ごとに最適化されたフライス加工が可能となり、これにより製造コストの削減と生産性の向上が実現されます。また、部品の品質の均一性も高められるため、組立工程での問題発生のリスクも低減します。さらに、これらの工程を順に経ることによって、最終製品の品質向上にも寄与することができます。総じて、SKDフライス加工による工程計画は、コスト削減、生産性の向上、品質の均一化に効果を発揮するため、量産に最適な方法といえるでしょう。
4. 工場の生産性向上とSKDフライス加工量産
4-1. 生産性向上の戦略
SKDフライス加工を用いた量産では、効果的な工程計画のもと、生産性の向上が見込まれます。この計画において重要なのは、加工の精度と速度を損なうことなく、一貫性のある品質を保つことです。たとえば、治具の設計を工夫することで、部品のセットアップ時間を削減し、効率を高めることができます。また、フライス加工のパラメータ(切削速度や送り速度など)の最適化によって、一つ一つの工程の時間を短縮し、総生産時間の削減に寄与します。さらに、耐用性の高い工具を選択することで、工具交換の頻度を減らし、機械の稼動時間を最大化することが可能です。これらの工程計画を丁寧に行うことにより、高品質な製品を短時間で量産することが実現します。最終的には、これらの効果的な計画により、コストの削減と生産効率の向上を実現できるのです。
4-2. SKDフライス加工による効率改善
SKDフライス加工は量産において高い効率を発揮する工程計画方法です。その理由は、SKD(Semi Knocked Down)の手法を取り入れることで、部品の一部を予め組み立てることが可能となり、組立作業の削減に繋がるからです。具体的な例として、自動車の部品製造では、エンジンやトランスミッションなど、複数の部品を個別に加工後、ある程度組み立てた状態で出荷することが一般的です。この方法により、最終組立工場での作業時間が短縮され、全体の生産性が向上します。結論として、SKDフライス加工を適切に行うことで、生産効率の向上とコスト削減を実現できるため、量産体制を構築する際には、この工程計画が極めて重要であると言えます。
5. 増速スピンドルとSKDフライス加工量産の最適化
5-1. 切削条件の最適化
SKDフライス加工において、量産に適した効果的な工程計画は、生産性の向上とコスト削減に直結します。この適切な計画の根幹をなすのが、切削条件の最適化です。その理由は、最適な切削速度、送り速度、切り込み量の設定によって、加工時間を短縮し、工具の摩耗を抑制できるからです。例えば、適切な切削速度を見つけることで、無理な負荷をかけずに効率的に金属を削ることができます。また、送り速度や切り込み量を調整することで、加工中の振動を抑え、より高い精度の加工が可能になります。これにより、不良品の発生を減らし、再加工の手間や材料の無駄を削減することに繋がります。結論として、SKDフライス加工において量産向けの効果的な工程計画を行うためには、切削条件の最適化が不可欠であり、これが全体の生産性と品質の向上に寄与すると言えます。
5-2. 増速スピンドルの活用
増速スピンドルを活用することにより、SKDフライス加工の効率は劇的に向上します。これは、加工時間の短縮という明確な結果に繋がり、量産の現場では特に重宝されています。具体的な例として、高速での切削が可能な増速スピンドルは、従来のスピンドルと比較して作業時間を大幅に削減。また、切削速度が上がることで、より精密な仕上がりを期待できるというメリットもあります。最適な工程計画においては、生産性を最大限に引き出すためにも、この増速スピンドルの導入を前提とした設計が不可欠です。最終的には、この技術を取り入れることで、コスト削減と品質向上の両方を達成し、競争力のある製品を市場に提供することが可能となります。
6. SKDフライス加工における除去加工技術
6-1. 除去加工の基本
SKDフライス加工が量産に最適な理由は、その効果的な工程計画にあります。精度が要求される部品製造において、SKDフライス加工は繰り返し精度の高い作業が可能で、一貫した品質を保ちつつ高速生産を実現します。たとえば、自動車業界では、複雑な形状の部品を大量に生産する必要があり、SKDフライス加工は形状や寸法が一定であることを重視する場面で非常に有効です。このような加工においては、工具の摩耗管理や交換時期の見極め、さらに適切な切削条件の設定が重要となり、これらを事前に計画することで無駄な工程を省き、コスト削減にもつながります。最終的に、SKDフライス加工における効果的な工程計画は、量産時の安定性と効率性を実現する鍵であると言えるでしょう。
6-2. 技術の進歩と応用
SKDフライス加工は、その精度と効率性から量産に最適な加工方法とされています。なぜなら、SKDフライス加工は均一な品質を維持しつつ、大量の製品を短時間で生産することが可能だからです。特に、工程計画をしっかりと立てることで、その効果はより顕著となります。例えば、工具の選択に始まり、切削条件の最適化、治具の設計に至るまで、各段階を丁寧に設計することで、無駄な工程を省き、生産効率を大幅に向上させることができます。また、CAD/CAMシステムの活用により、加工プログラムを事前にシミュレートし、最小限の試作で最適な加工条件を見つけ出すことが可能です。このように、適切な工程計画によってSKDフライス加工は、量産の現場においてその真価を発揮するのです。
まとめ
SKDフライス加工は品質と生産効率の両面で優れた加工方法です。効果的な工程計画により、工程間の無駄な移動や待ち時間を減らし、生産性を向上させることが可能です。量産に適した工程計画を立てることで、素材の無駄を最小限に抑えつつ高精度かつ効率的な加工が実現できます。
【SKD量産】フライス加工で効率アップ!コスト削減のコツとは?
もしフライス加工における効率アップやコスト削減のノウハウに興味をお持ちで、もっと効率的なSKD量産を実現したいとお考えなら、この記事はきっと役立つ情報が満載です。本記事では、フライス加工における効率アップやコスト削減のコツに焦点を当て、SKD量産の方法や具体的なヒントを詳しく解説していきます。フライス加工における効率アップやコスト削減について知りたい方はぜひご覧ください。
1. SKD フライス加工量産の基礎
フライス加工によるSKDの量産は、製造業の効率化とコスト削減に大きく寄与しています。その効率の秘訣は、精密な工程設計と最適化された切削条件にあります。例えば、専用の治具を用いて複数の工程を一度に処理することで、作業時間を大幅に削減することが可能です。また、SKD特有の材質に合わせた切削工具の選定や、適切な送り速度と回転数の設定は、工具の摩耗を減らし長寿命化を実現し、結果としてコストを抑えることにもつながります。こうした細部にわたる注意と工夫が、SKDフライス加工の量産における効率向上とコスト削減を実現しているのです。最後に、継続的な改善活動は、生産性の更なる向上を約束します。
2. SKD フライス加工で使われる部品とその応用例
フライス加工によるSKD製品の量産は、効率向上とコスト削減に大いに寄与します。結論から言えば、適切な工具選択と加工条件の最適化がコスト削済みの鍵となります。理由は、SKD材料は硬度が高く加工が困難なため、効率的な工具を使って加工時間を短縮し、材料の消耗を抑える必要があるからです。具体例を挙げると、フライスの刃先を工具の寿命を延ばすコーティングで選ぶこと、または、カッターの回転速度や送り速度を材料に適した設定にすることが挙げられます。最適化されたフライス加工は、耐久性のあるSKD製品を効率良く量産することが可能になり、結果としてコストパフォーマンスが向上します。
3. 加工性比較試験とSKD フライス加工量産の関係
フライス加工におけるSKDの量産は、コスト削減と効率化の大きな鍵となります。SKD材は硬さと耐摩耗性に優れた特性を持ち、フライス加工に最適です。効率化のためには、適切な工具選定が不可欠です。例えば、SKD専用の工具を使用することで、切れ味が長持ちし、工具の交換頻度を減らすことができます。さらに、正確な工具の位置決めや速度の調整を行うことで加工精度を高め、不良品の発生を低減させることが可能になります。これらの工夫により、長期的に見て材料費や工具コスト、メンテナンス費用の削減に繋がるのです。まとめると、フライス加工でSKD材を量産する際は、適切な工具の選択と加工条件の最適化がコスト削減へのコツであると言えます。
4. 金型材SKDの最新動向と市場の現状
フライス加工を活用してSKDの量産効率を高めることは、コスト削減に直結します。その理由は、フライス加工により、素材の無駄を最小限に抑えられるからです。特にSKDのような金型材では、精密な加工が求められるため、材料を細かく削り出すフライス加工はその要求を満たします。例えば、一般的なフライス加工機を用いることで、複雑な形状のSKDパーツでも、高い精度で迅速に製造することが可能になります。また、最新のCNC(コンピュータ数値制御)技術を取り入れることで、一貫した品質管理が行え、無駄のない生産ラインを実現できます。これにより、材料コストの削減だけでなく、製造工程の時間短縮にも寄与し、結果的に全体的なコストダウンを果たすことができます。その結果、フライス加工を適切に活用することで、SKD量産の効率を上げることができるのです。
5. SKD フライス加工量産におけるエンドミルの選定基準
SKD量産におけるフライス加工の効率化は、コスト削減に直結します。この過程での重要なポイントは、適切なエンドミルの選択にあると言えるでしょう。適正なエンドミルを選ぶことにより、工具の摩耗を減らし、製品の精度を保つことが可能となります。例えば、SKDのような硬度が高い材料を加工する際には、耐摩耗性に優れた超硬エンドミルが適しています。また、異なる切削条件に応じたフルート数やヘリックス角の考慮も必要です。正しいエンドミルを選べば、1つの工具で長時間の加工が可能となり、工具交換の頻度を下げることができ、結果として生産効率の向上とコスト削減に繋がるのです。従って、SKDフライス加工においても、最適なエンドミル選びがコスト削減の鍵となると結論付けられます。
6. SKD フライス加工量産と高速加工技術の融合
SKDフライス加工の量産において、効率化とコスト削済が重要です。その鍵となるのは、高速加工技術の導入にあります。この技術を活用することで、加工時間を大幅に短縮し、同時に消耗する工具のコストも削減可能となります。たとえば、SKDに適したカッターや、最適化されたカッティング条件を選定することで、材料を効率よく削りだし、耐久性のある工具を長く使い続けることができます。また、精度の高い加工が可能になるため、後工程での修正が減り、余計なコストを抑えることにも寄与します。結論として、フライス加工におけるSKDの量産は、高速かつ精密な加工技術によって効率が向上し、結果的にコスト削減につながるのです。
まとめ
SKDでのフライス加工においては、工程ごとの効率化やツールの最適化が重要です。量産においては、工程を見直し、自動化や省力化を図ることでコスト削減につなげることができます。また、素材選定や加工方法の工夫により、高品質かつ低コストな製品を生産することが可能です。
【プロ直伝】SS材の穴あけ・フライス加工テクニックとは?
もし、あなたがSS(ステンレス鋼)の穴あけやフライス加工に興味があり、しかし具体的なテクニックや方法が分からないという問題を抱えているのであれば、この記事はあなたのためです。メーカーやプロフェッショナルによる直伝のテクニックを紹介します。SS材における穴あけやフライス加工について、どのようなテクニックが必要で、それはどのようなものなのか、を分かりやすく解説していきます。
1. SS 穴あけ フライス加工の基礎
ステンレス材(SS材)の穴あけやフライス加工は、耐食性や硬度が高いため特別な技術が要求されます。このような加工を成功させるには、適切な工具選びと加工条件の設定が不可欠です。例えば、穴あけには先端が鈍らないよう硬質のドリルを選び、回転数や送り速度を材質に応じて慎重に調整する必要があります。フライス加工の場合も、カッターの選択に気を配り、冷却液を適切に使用して加工時の熱を抑えることが重要です。実際にこれらの技術を用いることで、SS材でもクリーンな穴開けや滑らかなフライス加工が可能になり、耐久性や精度の高い製品製造へと繋がります。この工程をマスターすることが、品質の高い金属加工を実現する鍵となります。
2. 切削加工の基本とSS 穴あけ フライス加工の原理
SS材の穴あけやフライス加工は、精密な工程を要するため、適切な技術の知識が非常に重要です。特にSS材は、その硬さと耐食性に優れているため、通常の材料より加工が困難とされています。このようなSS材の加工においては、専用の工具を使用し、適正なスピードと冷却液の利用が鍵となります。例えば、穴あけ加工では、ドリルの先端角や回転速度を材料の硬さに応じて調整する必要があり、フライス加工では、切削抵抗を考慮しながら工具の送り速度や刃の数を選定することが重要です。適切な調整を行うことで、加工時のバリ発生を防ぎ、美しい仕上がりを実現することができます。結論として、SS材の穴あけ・フライス加工には専門的な技術と正確な工程管理が不可欠であり、これらのテクニックをマスターすることで、製品の品質向上に寄与することができるのです。
3. SS材料の特性と加工上の注意点
SS材の穴あけやフライス加工は、正確な技術が要求される作業です。SS材はステンレスの一種で、その特有の硬さと強度のため、一般的な金属加工よりも注意を払う必要があります。例えば、穴あけの際には、適切な速度と冷却液の使用が不可欠です。速度が速すぎたり遅すぎたりすると、工具の摩耗や材料の損傷の原因になります。また、フライス加工に関しても、切削速度や送り速度を正確にコントロールし、過度な加工熱の発生を避けることが大切です。これには、経験豊富な技術者の知識が必要とされます。うまく加工を行うことで、SS材の持つ耐久性と美しさを最大限に活かすことができるため、専門の技術者による正確な加工技術の理解と実践が重要です。
4. SS400とS45Cの材料比較と用途
SS材の穴あけやフライス加工は、その精度と技術的な要求から専門的な知識が必要です。SS材とは、一般的に耐食性や強度が高く、産業機械や建築物に使用されるステンレス鋼のことを指します。この材質を加工する際には、適切な工具選びが重要であり、例えば、穴あけ加工ではハイスドリルやカーバイドドリルなどが使用されます。また、フライス加工では、工具の回転速度や進行速度の調整がキーとなります。具体的な例を挙げると、SS400という材料は、焼き入れが不要でありながら、加工容易性に優れているため、多くの産業で穴あけやフライス加工に使用されています。むしろ、精度の高い加工を実現するためには、材質の性質を理解し、適した工具と加工条件を見極めることが不可欠です。このような適切なテクニックを駆使することで、加工精度が向上し、製品の品質にも貢献できるのです。
5. 鉄の切削加工方法とその技術
ステンレス(SS)材の穴あけやフライス加工は、製造業においては避けては通れない技術です。SS材はその優れた耐食性や強度のため多くの産業で使用されていますが、加工の難しさもまたトピックとなります。具体的には、SS材は硬くて粘りがあるため、切削工具に高い耐摩耗性が求められるのです。このため、穴あけやフライス加工には特別な工夫が必要で、例えば、適切な切削速度の選定や冷却液の使用が挙げられます。また、使用するドリルやエンドミルの材質選定も重要で、コバルトハイスやカーバイド製が推奨されています。しかし、単に良い工具を選べば良いというわけではなく、穴あけ加工時には段階的に径を大きくしていくステップドリリングの技法や、フライス加工では正しい切削量を見極めることが重要です。これらのテクニックを駆使することで、SS材の加工精度を高め、工具の寿命を延ばし、コストを削減することが可能になります。
6. SS 穴あけ フライス加工の実例紹介
ステンレス(SS)材の穴あけやフライス加工は、正確な技術を要します。SS材は硬度が高く、作業には特別な注意が必要です。例えば、穴あけの際には、適切な切削速度と冷却剤の使用が必須であり、フライス加工においては工具の刃の角度や切り屑の排出方法を工夫することが求められます。特に、SS材は熱を持ちやすく、加工時には熱による変形を避けるためにも、冷却しながら加工を行うことが一つのポイントとなります。また、専用の工具を用いて加工を行うことで、SS材特有の光沢を保ちながら、きれいな仕上がりを実現できます。これらの技術を身に付けることで、SS材の加工はより高品質で、効率的になり、結果として製品の信頼性を高めることにつながります。
7. 加工依頼先の選び方とチェックポイント
SS材の穴あけやフライス加工は、高い精度と専門技術を要求される作業です。そのため、適切な加工技術を知ることは、製品品質の向上に直結します。例えば、SS材にはその硬度や耐食性から特有の工具や加工速度が求められることが多く、これらを正確に把握することが重要です。特に、フライス加工では切削液の選定や送り速度の調整が精度を左右するため、経験豊かなプロフェッショナルに依頼することが望ましいでしょう。成功した事例として、適切な工具選定と送り速度の管理により、高品質な仕上がりを実現した例が多数報告されています。そして、再び結論として、SS材の穴あけ・フライス加工においては、特殊な材質に適した技術と経験が必要不可欠であり、正確な加工を実現するためには専門のプロフェッショナルに相談し、加工依頼を行うことが賢明な選択と言えるでしょう。
8. フライス加工と旋盤加工の違いと適用
SS材の穴あけやフライス加工は、精密な技術を要するため、適切な方法とテクニックの習得が重要です。まず、SS材はステンレス鋼のことで、耐食性や強度が高い反面、加工が難しい特徴を持っています。理由としては、硬い材質のため工具への負担が大きく、また熱もこもりやすいためです。具体的な例を挙げると、穴あけ加工では、切削速度を適切にコントロールし、頻繁に冷却液を用いることが重要です。また、フライス加工においては、適切な刃の選定と進行速度の調整が鍵を握ります。これらの技術をマスターすれば、SS材の加工精度を高めることができ、長期的に見て工具の寿命を延ばし、コスト削減にもつながります。したがって、SS材の加工における適切な穴あけ・フライス加工テクニックの習得は、品質の向上と効率的な生産の両面で極めて重要なのです。
9. SS 穴あけ フライス加工の依頼先リスト
SS材に穴をあけたりフライス加工を行うテクニックは、精度の高い加工を求められる分野で重要です。その理由は、SS材は強度が高く硬いため、加工には特別な注意が必要だからです。例えば、正確な穴あけには、適切なドリルビット選びや冷却液の使用が必須です。フライス加工においては、カッターの角度や送り速度を適切に調整することが品質を左右します。実際に業界では、専門の技術者がこれらの作業を精密に行い、機械部品や工業製品に適用しています。そのため、SS材の加工を依頼する際には、これらのテクニックを理解し、実績のある業者を選ぶことが肝要です。このような加工技術は、最終製品の品質を大きく左右するため、非常に重要と言えるでしょう。
10. 最終章:SS 穴あけ フライス加工に関するQ&A
SS材の穴あけやフライス加工は、正確な技術が必要不可欠であり、工業分野での製品精度を大きく左右する工程です。SS材とはステンレスの略で、その硬さと加工の難しさから特別なテクニックが求められています。例えば、穴あけではステンレスの硬質に対応したドリル選びや冷却液の適切な使用が必要です。フライス加工では、カッターの種類や刃のスピード調整が重要となります。加工時には、これらの条件を見極め、適切な工具と方法を選択することが成功の鍵です。結論として、SS材の穴あけ及びフライス加工には、材質特有の性質を理解し専門的な技術を駆使することが不可欠です。この分野での熟練は、製品の品質向上に直結し、生産効率の向上にも寄与します。
まとめ
SS材は硬度が高く、穴あけやフライス加工が困難な素材です。しかし、適切な切削条件や刃具を使用することで、効率的かつ正確な加工が可能となります。穴あけには適切な刃具選定と冷却剤の利用が重要です。また、フライス加工では適切な刃先形状と切削速度を選択することで、高品質な加工が実現できます。プロのテクニックを参考にして、効率的なSS材加工を行いましょう。
【経験者向け】SKDフライス加工量産のための上級ティップス
多くの経験者が直面する課題の1つに、SKDフライス加工の量産に関する上級ティップスを得ることがあります。そのために私たちは、『SKDフライス加工量産のための上級ティップス』を作成しました。この記事は、SKDフライス加工や量産に詳しい方を対象としており、基本的な知識から実践的なテクニックまで、カバーしています。SKDフライス加工において量産を行いたいと考えている方々にとって、重要な情報が満載です。
1. SKDフライス加工量産の効率化戦略
SKDフライス加工の量産を成功させるためには、効率性の追求が欠かせません。その理由は、生産性の向上がコスト削減に直結し、競争力のある製品を市場に提供するための基盤となるからです。具体的な例を挙げると、ツールの選定においては、耐摩耗性に優れた超硬材料を用いることで工具の寿命を延ばし、交換頻度の低減に努めることが挙げられます。また、最適な切削条件の確立を図り、非効率な加工時間を削減することも重要です。さらには、CAMソフトウェアを活用した加工プログラムの最適化により、一貫した加工の質を保ちつつ作業効率を高めることができます。これらの高度なティップスを実践することで、SKDフライス加工の量産は、より効率的で、経済的なものとなるのです。
2. 異なる材料のSKDフライス加工性能比較
SKDフライス加工において、量産を目指す上での加工性能は非常に重要です。SKD材料は、硬度や耐摩耗性に優れる一方で、その加工は困難を伴うため、詳細な加工ティップスの把握が必要とされます。たとえば、切削速度や送り速度、カッターの材質選定など、適切な条件設定が量産効率を大幅に向上させます。実際に、適したコーティングを施したカッターを用いることで、耐久性が向上し、長時間安定した加工が可能になり、その結果、量産ラインにおける停止時間の短縮に貢献します。このように、細かなテクニックの積み重ねが量産におけるSKDフライス加工の成功を左右するのです。最終的に、これらのティップスを活用することで、製造コストの低減と生産性の向上が実現可能となります。
3. SKDフライス加工量産におけるタップの選定
SKDフライス加工量産を成功させるには適切なタップの選定が不可欠です。この加工法で求められるのは一貫性と精度の高さ、そして経済性です。適切なタップを選ぶことで、加工時間の短縮と耐久性の向上を実現でき、結果として生産性が向上します。特に、硬度が高く耐摩耗性に優れたSKD材を使用する場合、材料特有の加工困難さを考慮した専用のタップを選択することが重要です。例えば、コーティングされたタップはSKD材の硬い表面を効率よく切削でき、長い工具寿命を保証します。さらに、適切な潤滑剤の使用はタップの摩耗を抑制し、スムーズな切削を促進することにも繋がります。したがって、材料の特性に合わせたタップの選定は、SKDフライス加工量産の質と効率を大きく左右するため、高度な知識が求められるという結論に至ります。
4. SKDフライス加工と環境:リサイクルシステムの導入
SKDフライス加工における量産を成功させるためには、リサイクルシステムの導入が効果的です。量産において最も重要なのは、コスト削減と効率の向上です。SKDフライス加工では、切削屑が大量に発生するため、これを有効活用することが不可欠です。例えば、リサイクルシステムを用いることで切削屑を再処理し、新たな原料として再利用する流れを作ることが可能です。これにより、材料コストの削減及び環境への負荷軽減が図られます。また、工程間の無駄を省くことで、時間的な効率も飛躍的に向上します。経験者にとっても、常に改善されるべきポイントであり、SKDフライス加工の量産においてリサイクルシステムは欠かせない要素と言えます。結論として、リサイクルシステムの導入は、SKDフライス加工における量産においてコスト削減と効率化を実現するための重要なステップであると言えるでしょう。
5. 長野県におけるSKDフライス加工量産の特色技術
長野県におけるSKDフライス加工量産のためには、特化した技術とノウハウが必要とされます。この地域は、緻密な技術力が求められる精密機械産業が盛んであり、SKDフライス加工の量産においてもその特色が生かされています。具体的には、工具の選定や切削条件の最適化、そして高い熱処理技術が必要となります。例えば、SKD材を用いた加工品は耐摩耗性が求められることから、工具選びには特に注意を要し、適切なコーティングが施された刃物を選定することが重要です。また、量産を考慮した場合、効率良く加工するためには切削条件を細かく調整し、一貫した品質を保つための管理体制も整える必要があります。加えて、長野県は冷涼な気候が熱処理に適しており、材料の歪みを最小限に抑えることができるという利点もあります。これらの技術と環境を活かし、SKDフライス加工の量産が成功しているのです。
まとめ
SKDフライス加工量産を成功させるためには、効率的な生産ラインの設計が重要です。加工工程の最適化と自動化を行うことで、生産性を向上させることができます。また、適切な切削条件とツール選定によって、加工品質を向上させることができます。経験者向けのテクニックを駆使して、SKDフライス加工量産を効果的に行いましょう。