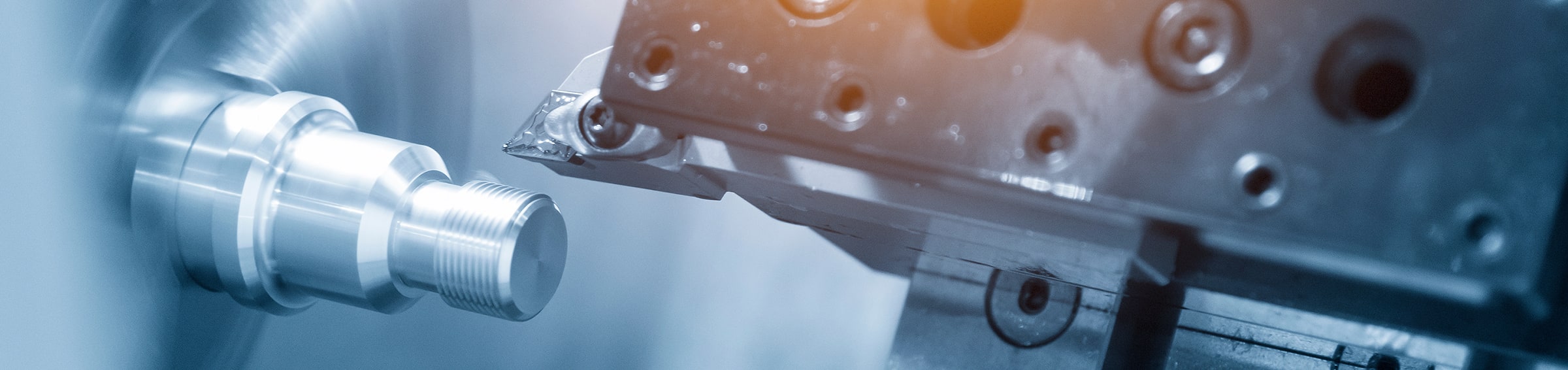
加工技術 column
【加工精度を上げる】SS材のタップ加工・フライスの効率的な方法
SS材のタップ加工やフライス加工において、加工精度を上げたいとお悩みの方へ。本記事では、効率的な方法について詳しく解説します。SS材の特性や加工時のポイント、最適なツールの選び方など、加工精度向上に役立つ情報をご紹介します。さらに、タップ加工やフライス加工における注意点やよくある問題についても取り上げます。加工作業の効率を上げ、品質の向上を目指す皆様にぜひお役立ていただければと思います。
1. SS タップ加工・フライス加工の基本
SS材のタップ加工やフライス加工の精度を向上させるには、特定の効率的な方法があります。まず、しっかりとした下準備が必須です。これには、使用する機械の正確なセットアップや、切削油の選択が含まれます。例えば、SS材に適した切削油を使用することで、摩擦を減少させ、切削性能を向上させることができます。また、刃具の選択は非常に重要であり、材質や刃の形状が加工精度に直接影響を与えるため、用途に応じた適切なものを選定する必要があります。さらに、加工条件の最適化、つまり切削速度や送り速度の適切な調整を行うことで、バリが少なく、仕上がりが滑らかな加工が可能になります。これらの方法を総合することで、SS材の加工精度は大幅に向上し、製造業における品質と効率が向上します。
2. SS400材料とは?その特性と加工の利点
SS400材料は、一般的な構造用鋼材の一つであり、その高い機械的性質と優れた加工性から、多くの産業で使用されています。タップ加工やフライス加工の精度を上げることは、製品の品質向上に直結し、結果として生産効率の向上にもつながります。具体的には、SS400材の加工に際しては、適切な切削油の使用や、加工速度の調整が有効です。例えば、タップ加工では、摩擦を減らすための切削油の選定が重要であり、フライス加工においては、工具の刃の数や角度を材料の硬さに合わせて調整することで、加工精度を高めることができます。これらの方法により、加工時のバリの発生を減らし、滑らかな仕上がりを実現することが可能です。こうした工夫をすることで、SS400材の加工精度を上げ、生産性を高めることができます。
3. タップ加工におけるSS400の選定基準
SS材におけるタップ加工・フライス加工の効率を上げるためには、適切な材料選定が重要です。特にSS400は加工性が高く、精度の要求される作業に適しています。SS400は炭素含有量が少なく、切削加工時のバリが少ないため、加工精度が向上します。例えば、SS400を使用したタップ加工では、タップの切れ味を長持ちさせ、目詰まりを防ぐ事ができます。フライス加工では、滑らかな表面仕上げが可能です。これらの特性により、SS400は多くの工場で高い評価を受けており、加工効率と品質の向上に貢献しています。よって、高い加工精度を追求するならば、SS400のような適切な材料を選定することが肝心です。
4. SS タップ加工の手順とテクニック
SS材のタップ加工やフライス加工の精度を上げることは、製造業での品質向上に直結します。これを達成するためには、適切な工具選びと加工条件の設定が不可欠です。例えば、SS材向けに設計されたタップやフライスカッターを使用すると、工具の耐久性が向上し、加工面の仕上りが良くなります。また、適正な切削速度や送り速度を見極めることで、加工時のバリの発生を抑え、精度の高い加工が可能になります。具体的には、試作を重ねながら最適な条件を探ることや、経験豊富なオペレーターの技術を活かすことも重要です。これらの方法を踏まえ、SS材の加工精度を高めることで、製品の信頼性を高め、顧客満足度を向上させることができるのです。
5. フライス加工におけるSS材の加工精度向上のポイント
SS材のタップ加工やフライス加工の精度を上げることは、製品の品質向上に直結します。そのためには、適切な工具選びと加工パラメータの最適化が重要です。例えば、SS材には硬度が高いため、特に耐磨耗性に優れた工具を選ぶことが求められます。また、フライス加工では、適切な切削速度や送り速度の選定が、バリの発生を抑え、より滑らかな表面を実現するために不可欠です。具体的には、マシニングセンターで使用するエンドミルの材質を選ぶ際には、SS材の特性に合ったコーティングが施されたものを選ぶことが効果的です。これにより、加工精度が向上し、製品の信頼性も高まります。最終的には、これらの工夫によって、SS材の加工における品質と効率の両立が実現されることでしょう。
6. タップ加工での高品質な仕上がりを実現するコツ
SS材のタップ加工やフライス加工の品質を向上させるには、適切な工具選びと加工条件の最適化が欠かせません。タップ加工では、硬さや粘り強さに優れたSS材に対応できる高硬度のタップを選び、適切な送り速度や回転数を厳密に管理することで、精度よくねじ山を形成できます。例えば、高粘度の潤滑剤を使用することで、切削抵抗を減らし、摩擦熱を低減させることが可能です。フライス加工では、カッターの選択が重要で、SS材の特性に合わせたコーティングが施されたカッターを使用すると、耐久性が向上し、長期間にわたる安定した加工が行えます。適正な切削速度と送りを保つことで、微細な仕上がりが実現します。結論として、SS材を用いた高精度なタップ加工・フライス加工を実現するためには、素材に最適化された工具と条件の選定が成功の鍵となります。
7. SS タップ加工における特殊な加工対応と追加工事
SS材のタップ加工・フライス加工の精度を向上させることは、製品の品質向上と生産効率の観点から重要です。そのためには、適切な工具選択と加工条件の最適化が欠かせません。具体例として、タップ加工においては、SS材専用のタップを使用し、材質に合わせた切削速度と送り速度を設定することが効果的です。また、フライス加工では、刃先のコーティングや形状を選ぶことで、耐久性を高め、切削抵抗を低減させることができます。これにより加工精度を維持しつつ、工具の寿命を延ばし、結果としてコスト削減にもつながります。最適な工具と加工条件を選択することで、SS材のタップ加工・フライス加工の効率と精度は大きく改善するでしょう。
8. タップ加工で使用する機器と工具の選定と使用方法
SS材のタップ加工やフライス加工の精度を向上させることは、工業製品の品質向上に直結します。特に、加工精度が要求される分野での生産性を高めるためには、効率的な方法を取り入れることが重要です。例えば、SS材の切削には、硬度が高く摩耗に強いコーティングが施された工具を使用することで、工具の寿命が長くなり精度の高い加工が可能になります。また、タップ加工の際には、適切な潤滑剤を使用し、切削抵抗を低減させることが、糸切りの精度を保つ上で効果的です。フライス加工においても、切削速度や送り速度の最適化を図ることで、仕上がりの均一性を向上させることができます。これらの方法を適宜採用することで、生産効率と加工精度の両方を高めることが期待されます。最終的に、これらの効率的な方法が一般化することで、日本の工業製品が一層の品質向上を実現し、国際競争力を高めることに貢献するでしょう。
9. SS タップ加工・フライス加工に関するよくある質問
SS材のタップ加工やフライス加工の精度を向上させるためには、正確な方法を適用することが不可欠です。加工精度を上げることは、製品品質の向上に直結します。そのため、工具の選定から加工条件の設定まで、細部にわたる注意が求められます。具体的な例として、タップ加工では、適切な切削油の使用が挙げられます。これにより、切削抵抗を減少させ、ねじ部の仕上がりを良くすることができます。フライス加工においては、切削速度や送り速度の最適化が重要とされ、これにより不要な振動を抑制し、加工面の仕上げ精度が向上します。最終的に、これらの方法を組み合わせることで、SS材の加工精度は格段に向上するでしょう。
まとめ
SS材のタップ加工やフライス加工においては、適切な切削条件を設定することが精度を上げるポイントです。適切な切削速度や切削深さ、刃先の選定が重要です。また、適切な冷却や潤滑を行うことで加工精度を高めることができます。加工前に材料や工具の状態を確認し、適切な加工条件を設定することが効率的な加工の鍵となります。
SS材加工を極める!プロが推奨するタップ・フライスの小ワザ
プロによるSS材加工の極意がここに!タップ加工とフライス加工の小ワザをご紹介します。SS材の加工には独自の工夫が必要ですが、この記事を読めば初心者でも理解しやすく、スキルアップできるでしょう。どうぞ最後までご覧ください。
1. SS タップ加工とは?
SS材のタップ加工は、精密なねじを切る技術であり、高い技術力が求められる作業です。この加工を極めるには、プロから推奨される特別なコツを知ることが重要です。たとえば、適切な潤滑剤の使用は、タップ刃の磨耗を防ぎ、ねじ山の品質を維持する上で欠かせません。また、フライス加工においては、切削速度と送り速度の適切な調整が、仕上がりの精度に直結します。特にSS材のような硬質材料を加工する場合、これらの小ワザが加工の精度と効率を大幅に向上させるのです。したがって、タップやフライスを使用する際は、専門的な知識と経験を積み重ねることで、より高品質な加工を実現することができるでしょう。
2. SS タップ加工の基本
SS材のタップ加工は精密な加工が可能で、その結果として製品の品質を高めることができます。この加工を効率よく行うには、正しい技術と適切な工具選びが重要です。例えば、小径のタップを使用する際は、前もって穴の位置決めや直径を正確に計測することが必須です。また、フライス加工では、切削速度と給送速度のバランスを見極めることがキーポイントとなります。これにより、加工面の粗さを抑え、精密さを保ちつつ、工具の摩耗を最小限に抑えることが可能になります。さらに、工具の振れをチェックすることで、加工精度を向上させることもできます。これらの小ワザを駆使することで、SS材加工の品質を格段に上げることができるのです。最終的には、これらの工夫を積み重ねることが、高品質な製品を生み出す秘訣となるのです。
3. SS400とは? – 鉄(SS400)レーザー加工の基礎
SS材の加工では、その品質や精度が求められるが、特にタップ加工とフライス加工の技術は非常に重要である。この加工技術を極めることで、材料の損失を減らしつつ、製品の品質向上に直結するためである。例えば、タップ加工では切削油の選定やタップの切れ味を常にチェックすることが細かなネジ山をきれいに仕上げるポイントとなる。一方、フライス加工では、工具の刃の角度や送り速度を吟味することで、仕上がりの精度を格段に向上させることができる。これらの小技が、SS材加工における大きな差となり、プロフェッショナルな仕上がりを実現する。よって、SS材加工を極めたいならば、これらの点に留意し、継続的なスキルアップを心がけることが推奨される。
4. SS400の6面フライス加工テクニック
SS400の6面フライス加工で求められるのは、精度の高い仕上がりと効率的な生産性です。これを実現するためプロから推奨される小ワザがいくつかあります。まず、タップ加工の際は、適切な切削油の使用が重要です。これにより、タップの寿命を延ばし、繰り返しの精度を保つことができます。さらに、フライス加工では、切削工具の選定に注意を払い、材質や形状に最適なものを選ぶことが重要です。具体的には、長刃のエンドミルを使用することで、一度に大きな面積を削ることができ、生産効率が大幅に向上します。そして、切削速度や送り速度の調整によって、加工面の滑らかさを最適化することもできます。これらの小ワザを駆使することで、SS400の6面フライス加工は、高品質かつ効率的なものとなるでしょう。
5. S45Cフライス加工のポイント
S45Cフライス加工では、適切なタップやフライスの使用が高精度な加工を実現する鍵となります。SS材の加工においては、特に材質の硬さを考慮した選択が求められ、プロからも推奨される小ワザが存在します。例えば、タップ加工では切りくずの排出性を高めるためにスパイラルタップを選ぶことが有効です。一方、フライス加工においては、刃の数や形状を選定することにより、加工面の仕上がりや加工スピードに大きく影響を及ぼします。特に、硬い材質では多刃のエンドミルを使用することで、均一な仕上がりを得ることができるでしょう。これらの小ワザを駆使することにより、効率的で精密な加工が可能となり、結果として製品品質の向上にも繋がります。SS材加工の極め方を理解し、適切なツールの選択と小ワザの活用には、ぜひ注目していただきたいと結論づけます。
6. タップ加工用の材料選定
SS材の加工を極めたいなら、タップ加工やフライス加工のテクニックの習得が不可欠です。これらの加工手法においては、材料選定が仕上がりの品質を大きく左右します。たとえば、耐食性や強度が求められるSS材では、加工時に発生する熱や摩擦に強い特殊タップや、切削抵抗が低いフライス工具を選ぶことが重要です。また、加工精度を高めるためには、切削油の選択も重要ポイントです。例えば、SS材専用の切削油を使用することで、摩擦を減少させ、タップやフライス工具の寿命を延ばすことができます。このように材料や工具、消耗品の選定に気を配ることで、高品質なSS材の加工が可能になります。プロが推奨する小ワザを取り入れることで、加工技術の精度を一層高めることができるでしょう。
7. 4F材と6F材の特徴と違い
SS材の加工において、効率と精度を追求するプロの間では、タップ加工とフライス加工の小ワザが重要とされています。特に、SS材はその硬度から加工が難しいため、適切な技術を駆使することが肝要です。タップ加工では、低速での加工と均一なチップの排出が重要ポイントとなります。これにより、ねじ山が綺麗に形成され、加工物の寿命が延びます。フライス加工においては、刃の角度や回転速度が重要で、これらを最適化することで、SS材特有の加工時の負担を減少させることができます。例えば、適切なクーラントの使用は、熱の影響を抑え、仕上がりの質を高めることに寄与します。結論として、これらの小ワザをマスターすることで、SS材加工の効率と品質を飛躍的に改善させることが可能です。
8. SS タップ加工の応用とコツ
SS材を加工する際、プロから推奨されるタップ加工やフライス加工の小ワザを身につけることは、精度と効率性を飛躍的に向上させます。例えば、SS材専用のタップを選ぶことは、ネジ山を正確に形成する上で不可欠です。タップの先端形状や溝の設計に特化したものを使用することで、加工時の抵抗を減らし、寿命を延ばすことができます。フライス加工では、カッターの選定が重要であり、SS材に適した刃先材質やコーティングをもつカッターを用いることで、摩耗を防ぎながら滑らかな表面仕上げを実現します。また、切削条件の最適化により、バリの発生を減少させることが可能になります。このような細かな工夫を凝らすことが、より高品質なSS材加工につながり、結果として生産性を高めることに繋がるのです。
9. プロが教えるSS タップ加工・フライス加工の小ワザ
SS材のタップ加工とフライス加工は、精密で高品質な製品を作り出すために欠かせない工程です。加工のプロフェッショナルは、これらの工程における小ワザを駆使して、効率と精度を向上させています。例えば、タップ加工においては、切削油の選択が重要です。高品質な切削油を使用することで、タップが材料にスムーズに切り込んでいき、精度の高いねじ加工を実現できます。さらに、フライス加工では、カッターの歯の数を増やすことで、1回転当たりの切削量を均等にし、振動を減少させることができます。これらの小ワザは、耐久性のある製品を効率良く生産するためには不可欠です。最終的に、これらの技術を駆使することで、SS材加工の品質向上とコスト削減を同時に実現することが可能です。
10. SS タップ加工・フライス加工のトラブルシューティング
SS材加工におけるタップ加工・フライス加工は、精密で高品質な製品を作り出すために必要不可欠です。この加工技術を極めることで、製造業の生産性と品質が飛躍的に向上します。例えば、タップ加工では刃先の角度や切削油の種類を選定することが重要で、適切に選ぶことでねじ山の精度を大幅に高めることができます。また、フライス加工では、切削速度や送り速度の調整により、加工面の仕上がりと工具の耐久性の両方を向上させることが可能です。これらの小ワザを駆使することで、SS材を加工する際のトラブルを効果的に減少させ、結果として高品質な製品を安定して生産することができるのです。
11. 安全なSS タップ加工・フライス加工のための環境整備
SS材加工は、高い精度と品質が要求される分野であり、タップ加工やフライス加工の技術は非常に重要です。これらの加工を極めるためには、専門の小ワザを身につけることが推奨されます。例えば、タップ加工においては、適切な潤滑油の選択が切削性能を大きく向上させます。また、フライス加工では、刃の角度や回転速度を材質に応じて調整することが、仕上がりの質を高めるポイントです。これらの工程で使用する工具のメンテナンスにも注意を払い、常に最適な状態を保つことが、精密な加工を実現する上で欠かせません。専門のテクニックを駆使することで、SS材の加工精度を高め、製品の品質向上につながるため、プロが推奨する小ワザを習得することが、加工技術を極める上での鍵となるのです。
まとめ
SS材の加工において、タップ加工やフライス加工は重要な技術です。タップ加工では、適切な切削油を使用することで加工精度を高めることができます。また、刃先に工夫を凝らした特殊タップを使用することで加工効率を向上させることができます。フライス加工では、適切な刃先形状を選択することで削りだしの処理をスムーズに行うことができます。プロの小ワザを活用して、SS材加工をより効率的に行いましょう。
SKD穴あけ加工を完璧に!効率的なフライス選定ガイド
あなたはSKD穴あけ加工で完璧な仕上がりを求めていますか?それなら、効率的なフライス選定ガイドがお役に立つかもしれません。このガイドでは、SKD穴あけ加工やフライス加工についての基本から始め、効率的な方法やポイントについて詳しく解説しています。SKD穴あけ加工について知りたい、穴あけのコツを知りたいという方にオススメの内容です。
1. SKD穴あけ加工の基礎知識
SKD穴あけ加工は、精密な製品作りに欠かせない工程であり、その完璧な仕上がりは適切なフライス選定から始まります。SKDとは金属を加工する際の難削材の一つであり、その硬度と耐摩耗性のために特別な注意を払う必要があります。効率的なフライス選定においては、まずSKDの材質特性を理解することが重要です。例えば、硬質であるがゆえに通常のフライスでは摩耗しやすく、その結果として加工精度が低下する場合があります。したがって、SKD用に特化した超硬フライスやコーティングされたフライスなどが推奨されます。具体例としては、チタンアルミニウムナイトライド(TiAlN)コーティングフライスが挙げられ、これは耐熱性や耐摩耗性に優れ、SKD加工において長寿命を保つことができます。最適なフライス選定を行うことで、加工時間の短縮やコスト削減につながり、最終的な製品品質の向上に寄与します。結論として、SKD穴あけ加工におけるフライスの選定は、製品の品質を左右するだけでなく、製造効率とコストにも大きな影響を与えるため、慎重に選ぶ必要があると言えます。
2. マシニング加工とフライス加工の違い
SKD穴あけ加工において最適なフライス選定は、効率的な加工を実現する鍵です。SKD材は硬質でありながら加工性が良い特性を持つため、適切なフライスを選ぶことで、精密な穴あけが可能となります。例えば、SKDでは一般的なドリルではなく、超硬質のフライスを使用することで、耐久性と速度のバランスを取ることができます。さらに、フライスの形状や刃の数、コーティングの種類によっても加工効果は異なりますので、加工するSKD材の種類や加工条件に合わせて選定することが重要です。正確なフライス選定により、製品の品質向上はもちろんのこと、工具の寿命を延ばし、コスト削減にも繋がるため、加工現場においては欠かせない知識であると言えるでしょう。
3. SKD穴あけフライス加工のためのエンドミル選定方法
SKD穴あけ加工を行う際には、適切なフライス選びが重要であるといえます。SKDとは耐摩耗性に優れた工具鋼であり、その硬度のために加工が難しい特徴を持っています。そのため、精度の高い穴を開けるためには、特に加工の負荷に耐えうるフライス選定が必須です。例えば、コバルトハイスや超硬合金製のフライスは、SKD加工に適し、長寿命で加工精度を維持するのに有効です。また、フライスの刃の形状やコーティングも加工結果に大きく影響するため、加工する材料の種類や状態に合わせた選定が求められます。適切なフライスを選ぶことで、SKD穴あけ加工の効率と精度を大幅に向上させることができます。
4. マシニング加工におけるクーラントの選定ポイント
SKD穴あけ加工を行う際には、適切なフライス選定が極めて重要です。適正な工具を用いることで、加工精度の向上と効率的な作業が可能となります。具体的には、SKD材の硬度や切削抵抗が大きい性質を考慮した、耐久性と切削能力に優れたフライスが求められます。例えば、コーティング技術が施された超硬フライスは、耐摩耗性が高く長寿命を実現できるため、SKD穴あけ加工には最適です。また、刃先形状を工夫することで、被削材の排出を助け、スムーズな加工を助けることもできます。適切なフライスを選定することによって、品質の高い穴あけ加工を行い、コスト削減にも繋がります。
5. コストダウンとVA/VEを実現する機械設計
SKD穴あけ加工を行う際には、最適なフライス選定が重要です。SKDとは、耐摩耗性や耐熱性に優れた高硬度の鋼材ですが、その特性上、加工が難しい材料でもあります。適切なフライスを選択することで、加工精度の向上はもちろん、工具の耐久性も向上し、結果的にコストダウンを図ることができます。たとえば、SKD材の穴あけには、高硬度材対応の超硬フライスやコーティングフライスが推奨されます。これらはSKDの硬さに耐えることができ、長期間にわたって安定した加工を実現します。また、フライスの形状や刃の数にも注意が必要で、適切に選んだフライスを使用することによって、加工時間の短縮や仕上がりの精度も格段に向上します。このように、効率的なフライスの選定は、SKD穴あけ加工を成功させるために不可欠であり、最終的な生産性の向上につながるのです。
まとめ
SKD穴あけ加工を行う際には、適切なフライス選定が重要です。硬い素材や特殊な形状の加工には適したフライスを選ぶことで、作業効率が向上します。また、適切な切削条件や冷却方法を選定することも重要です。適切なフライス選定と切削条件設定により、SKD穴あけ加工をより精密かつ効率的に行うことが可能となります。
【2023年版】SKD穴あけフライス加工のテクニックまとめ!
2023年版のSKD穴あけフライス加工のテクニックについて、最新の情報をまとめました!この記事では、SKD穴あけフライス加工に興味がある方や実践したい方に役立つテクニックを紹介します。穴あけやフライス加工に関する基本から応用まで、幅広く解説していきます。SKD技術を活用して効率的かつ高品質な加工を実現するために、ぜひこの記事を参考にしてください!
1. SKD穴あけフライス加工の基礎
SKD穴あけフライス加工とは、製品の品質向上と生産性の向上に不可欠な技術です。この加工技術によって、精密な穴径と形状が実現されます。特に工具の材質においてSKD(特殊鋼)を使用することで、耐摩耗性が高く、長寿命な穴あけ加工が可能となります。たとえば、金型の製造においてSKDを使用した穴あけフライス加工は、金型の精度を大きく左右します。これは、金型の穴が部品の合わせ面となるため、寸法精度が非常に重要になるからです。この技術を習得すれば、工業製品の多くで求められる高い加工精度を達成できるため、製造現場における競争力を高めることができます。結論として、SKD穴あけフライス加工のテクニックは、優れた製品を効率よく生産するために、極めて重要なものであり、技術の習得が推奨されます。
2. 穴あけ加工の種類と適用
SKD穴あけフライス加工は、精密な製造が必要な工業分野で注目されています。この技術の鍵は、材料の損傷を最小限に抑えながら穴あけ加工を行うことです。例えば、自動車産業や航空宇宙産業では、部品の耐久性と軽量化が求められ、SKD穴あけフライス加工がそのニーズに応える解決策として選ばれています。この技術は、異なる種類の材料にも適用され、材料の特性に合わせた加工方法が開発されています。最終的には、SKD穴あけフライス加工は、耐久性と高精度が要求される部品製造において、その効率性と精度の高さで再び選ばれる技術です。
3. ソリッドエンドミルの選び方
ソリッドエンドミル選びにおいて、SKD穴あけフライス加工の精度と効率は大きく左右されます。この工具の適切な選択が、加工の成功へのカギと言えるでしょう。特に、SKD材の硬度や加工する穴のサイズに応じたエンドミルの選定が重要です。たとえば、小径の穴加工にはシャープなエッジを持つエンドミルの使用が適しており、逆に大きな穴を加工する際には、より強靭な刃先を持つエンドミルが推奨されます。また、SKDの硬度が高い場合は、摩耗に強いコーティング処理が施されたエンドミルが有効です。これらの選択を適切に行うことで、加工精度の向上だけでなく、工具寿命の延長にも寄与し、結果的にコスト削減にも繋がります。従って、SKD穴あけフライス加工に適したソリッドエンドミルの選び方を理解し、適用することが非常に重要です。
4. SKD穴あけツールの特徴と選定基準
SKD穴あけフライス加工技術は、精密な加工が求められる様々な製造業において、その精度と効率性から注目を集めています。SKDとは、耐摩耗性や耐熱性に優れた特殊工具鋼のことを指し、この材質を使用した穴あけフライスは、高硬度の被削材にも対応することが可能です。特に、複雑な形状や狭いスペースでの加工においては、選定したSKDツールの性能が重要になります。例として、微細な加工が必要な電子部品などでは、SKD穴あけフライス加工が威力を発揮します。選定する際には、加工する材料の硬度や形状に応じて、適切なツール形状や刃径を考慮することが肝心です。また、切削条件の最適化も仕上がりのクオリティを左右します。結局のところ、適切なSKDツールの選定と運用は、精度の高い加工を実現し、製造効率を飛躍的に向上させる鍵となるのです。
5. フライス加工技術の進歩とSKD材料
SKD穴あけフライス加工は、日本の製造業で不可欠な技術の一つです。この技術は高硬度で耐摩耗性に優れたSKD材料に対しても、正確で効率的な穴あけを可能にします。主な理由は、SKD材料の特質に適した特殊な切削工具の使用と、最適な工程パラメータの選定にあります。例えば、SKD材料を用いた加工においては、工具の先端角や刃径が重要なポイントとなり、これに適した工具を選ぶことで加工精度が大幅に改善されます。また、切削速度や送り速度などのパラメータを適切に設定することにより、工具の消耗を抑えつつ、高効率な作業を行うことができます。このように、適切な工具選びとパラメータ設定により、SKD穴あけフライス加工は、より精度高く、効率的なものになっています。2023年版としてのこれらのテクニックは、製造現場での生産性向上に大いに貢献することでしょう。
6. 機械加工の精度向上テクニック
SKD穴あけフライス加工は、その精度の高さから多くの製造業界で重要視されています。その理由は、製品の品質を左右する重要なプロセスであり、また、精度が高いほど長期にわたって製品の耐久性も保たれるからです。例えば、自動車産業ではエンジン部品などの加工にこの技術が用いられ、微細な誤差でも性能への影響が大きいため、SKD穴あけフライス加工の技術力が直接製品の信頼性に結びついています。このような背景から、毎年その技術は進化しており、2023年現在も新しいテクニックが次々と開発されているのです。結論として、SKD穴あけフライス加工のテクニックは、製品の品質向上に不可欠であり、これを習得することは製造現場での競争力を高める鍵となります。
7. SKD穴あけフライス加工の応用例
SKD穴あけフライス加工は、精密な金属加工において重要な技術です。この技術は、特に硬度が高く加工が困難なSKD鋼において、その優れた切削能力を発揮します。例として、自動車産業におけるエンジン部品やギアの加工には、耐久性と精度が求められ、SKD穴あけフライス加工が選ばれることが多いです。同じく航空宇宙産業では、タービンブレードの製造においても、その精密性が利用されています。このように、SKD穴あけフライス加工は幅広い分野での需要があり、高い技術力を持つ日本のメーカーにとって、競争力の源泉となっています。技術の進歩に伴い、今後もこの加工方法の重要性は増すでしょう。
8. テクニカルガイダンスと技術資料の活用
SKD穴あけフライス加工は、その精度と効率性から製造業において不可欠な技術の一つです。特に、硬質材料を精密に加工する際には、SKD穴あけフライス加工が重宝されています。この技術が注目される理由は、耐摩耗性に優れた工具の使用にあり、これにより長時間の稼働が可能となり、加工精度の向上にも繋がるためです。例えば、金型製作においては、SKD工具を利用して複雑な形状の穴を精密に加工することができます。また、自動車業界では、エンジン部品などの高硬度材への穴あけ加工にSKDフライスが用いられることが多いです。これらの具体例からも、SKD穴あけフライス加工がいかに業界にとって重要であるかがわかります。まとめると、SKD穴あけフライス加工は、その高い耐久性と精密性により、多岐にわたる産業分野で重要な役割を果たしているのです。
9. 加工内容と機械設備の最新トレンド
SKD穴あけフライス加工の技術は精密さと効率性を求められ、2023年も注目を集めています。この加工技術の進歴は、切削工程の精度向上に貢献し、製造業の生産性向上に不可欠です。例えば、航空宇宙産業や自動車産業において、軽量化された部品を製作するために、SKD穴あけフライス加工は重要な役割を果たしています。これらの部品は、耐久性と強度を保ちながらも、極めて精密な穴加工が求められるため、SKD穴あけフライス加工は技術的なブレイクスルーとなっているのです。また、最新のCNC機械を導入することで、より複雑な形状の加工が可能になり、加工時間の短縮と品質の均一性が実現しています。2023年版のテクニックでは、これらの最新トレンドを踏まえ、高度な技術と最新機材の活用が必須となっています。SKD穴あけフライス加工のテクニックは今後も進化し続け、製造業の革新に寄与していくでしょう。
10. SKD穴あけフライス加工のFAQ
SKD穴あけフライス加工は、その高い精度と効率性から、2023年も引き続き多くの現場で利用されています。適切な技術を身に付けることで、作業の正確性を高め、コストを削減することが可能です。例えば、SKD材の硬さに適した刃の選択、冷却液の適切な使用、そして適正な送り速度と回転数の設定が重要です。特に、SKD材は耐摩耗性に優れているため、工具の選定を誤ると、工具の摩耗や損傷、作業効率の低下を招くことになります。実際の現場では、これらのポイントを考慮した上で、事前の計画と経験をもとに加工を進めることが求められます。このように、SKD穴あけフライス加工の精度と効率を高めるためには、適切な技術の習得が不可欠です。
11. 今後のSKD穴あけフライス加工の展望
2023年におけるSKD穴あけフライス加工のテクニックは、精密さと効率性を高めることで注目を集めています。フライス加工の精度を高めることは、工業製品の品質向上に直結し、それが製造業の競争力を決定づける一因となっているからです。たとえば、航空宇宙産業では、エンジン部品の冷却孔など、極めて高い精度が要求される穴あけが必要不可欠です。こうした部品では、マイクロメートル単位の誤差も許されず、SKD穴あけフライス加工の進化したテクニックが重宝されているのです。また、自動車産業においても、軽量化と強度の両立を求める中で、SKD穴あけフライス加工の技術がキーとなっています。結論として、高い技術力を要するSKD穴あけフライス加工は、日本の製造業における技術革新の推進力となり、今後もさらなる発展が期待されます。
まとめ
SKD穴あけフライス加工は工作機械を使用して精密な穴加工を行う技術です。このテクニックをマスターすることで、高精度な加工が可能となります。また、適切な切削速度や刃先形状を選ぶことで、加工時間の短縮や品質向上に繋がります。さらに、最新の2023年版の技術を取り入れることで、効率的な加工が実現できます。
プロフェッショナルが解説!SKD材を使った穴あけフライス加工の基本
SKD材という素材を使った穴あけフライス加工に興味はありませんか?この記事では、プロの解説で、その基本から応用までをカバーしています。穴あけフライス加工におけるSKD材の使用方法や技術について、詳しく知りたいと思っている方にぴったりの内容となっています。ぜひ、SKD材を使った穴あけフライス加工について理解を深めてみてください。
1. SKD材の基礎知識と特性
SKD材を使用した穴あけフライス加工は精密な作業が求められる一方で、工業生産において非常に重要なプロセスです。SKD材とは、耐摩耗性、耐熱性に優れ工具鋼の一種であり、金型などに使われることが多いです。穴あけフライス加工を行う際には、SKD材の硬度を考慮して、適切な切削条件を選ぶことが不可欠。例えば、硬い材質のため高速度鋼や超硬合金のドリルを使用し、低い切削速度で慎重に加工を進める必要があります。また、冷却液の使用は、発生する熱を抑え、工具の摩耗を防ぐためにも欠かせません。これらの工程を適切に管理することで、加工精度を高め、SKD材の利点を最大限に活かした製品作りが可能になります。総じて、プロフェッショナルによる適切な知識と技術があれば、SKD材の穴あけフライス加工は高品質な結果をもたらす重要な技術であると結論づけられます。
2. SKD 穴あけフライス加工のプロセス
SKD材を用いた穴あけフライス加工は、高い精密度と耐久性が要求される場面での使用が一般的であります。SKD材は特殊鋼の一種で、硬度が高く、耐摩耗性に優れているため、工具や金型の材料として広く利用されています。穴あけ加工の際は、SKD材の特性を生かし、対象物の破損を避けながら正確な穴を開ける技術が求められます。例えば、金型に穴をあける場合は、その精確さが製品の品質に直結するため、非常に高い技術力が必要とされます。適切な工具選び、切削条件の設定、冷却方法の選定など、細部にわたる様々な工夫が成功の鍵を握ります。再度強調しますが、SKD材を使った穴あけフライス加工は専門的な知識と経験を要する高度な技術であり、これによって製品の精度と寿命が大幅に向上します。
3. SKD11鋼CNCフライス加工の技術的要点
SKD材を使用した穴あけフライス加工は、精度と耐久性が求められる工業製品の製造において重要な工程である。SKD材は工具鋼の一種であり、優れた硬度と耐摩耗性を有しているため、フライス加工に適している。事例として、金型製作における穴あけ作業では、SKD材の特性を生かした切削工具が使用されることが多い。このような工具を用いることで、製品の寸法精度を高く保つことができる。また、SKD材を加工する際は、冷却液の適切な使用や切削速度の調整が必要になるが、これらに注意を払うことで長期にわたる安定した加工が可能となる。結論として、穴あけフライス加工においてSKD材を選択することは、製品の品質向上に直結する重要な判断である。
4. 木材学用語とSKD材の関連性
SKD材を使った穴あけフライス加工は、精密な加工が可能であり、多くのプロフェッショナルに支持されています。SKD材は、その耐摩耗性や経年変化に強い特性から、高品質な製品製造に適しているためです。例えば、金型の製造においてSKD材は頻繁に使用され、穴あけやフライス加工によって複雑な形状を実現しています。これには高度な技術が必要で、正確な加工が行えるSKD材は重宝されるのです。また、耐熱性も高く、加工時の発熱にも強いため、加工精度の維持に役立ちます。最終的に、SKD材を使った加工は、耐久性や精度が求められる場面での利用が見込まれ、それがプロフェッショナル間での高い評価につながっているのです。
5. 超ハイテン鋼板とSKD材の穴あけフライス加工
SKD材を用いた穴あけフライス加工は、精密な工業製品を作成する上で不可欠な技術です。この加工法は、耐摩耗性や耐熱性が求められるため、特に金型製造において重要とされます。例えば、自動車の部品製造などに使用される金型は、SKD材料で作られることが多く、その耐久性によって製品の品質が左右されます。この材料を正確に加工するには、適切な工具選択や加工条件が重要になってきます。たとえば、高速度鋼(HSS)や超硬合金など、材質に応じた切削工具を選び、加工速度や送り速度を調整する必要があります。また、穴あけ加工においては、冷却液の使用が効果的です。これらの対策により、SKD材を使った穴あけフライス加工は高い品質を持つ製品生産に寄与するプロセスであり、正確な手法を理解することが求められます。
6. 長野県の特色あるSKD 穴あけフライス加工技術
長野県におけるSKD材を用いた穴あけフライス加工は、その精密さと効率性から高い評価を受けています。この技術の主な魅力は、耐摩耗性や耐熱性に優れたSKD材が加工精度を高め、製品の信頼性を向上させることです。具体的な例として、金型製作や自動車部品の加工にこの技術が活用されています。金型では、高精度な穴あけが求められ、SKD材を使用することで精度の高い加工が可能になります。自動車部品では、耐久性が要求されるため、SKD材を利用した高精度のフライス加工が不可欠です。このように、長野県の技術者たちの優れた技術力と高品質なSKD材の組み合わせによって、穴あけフライス加工はさらなる発展を遂げることでしょう。
7. 機械加工の応用事例とSKD材の利用
SKD材を用いた穴あけフライス加工は、精密な機械加工において重要な技術です。この加工技術が重宝される理由は、SKD材の高硬度と耐摩耗性にあります。具体的な例として、金型の製造における穴あけ加工では、SKD材が必要な硬度を持つことで加工精度を高めることができます。また、耐摩耗性に優れているため、長時間の使用に耐えうる耐久性を金型に提供します。さらに、SKD材は熱処理後の寸法安定性も高いため、高精度な加工が可能となります。これらの特性から、SKD材は穴あけフライス加工において優れた成果をもたらし、製造業界での信頼性を高めています。結論として、SKD材を使用した穴あけフライス加工は、その特性を活かし、高品質な製品製造に不可欠な工程であり、その重要性は今後も高まることでしょう。
8. SKD 穴あけフライス加工におけるトラブルシューティング
SKD材を使用した穴あけフライス加工は、精密な加工が求められる業界で重宝されています。加工の際、優れた耐摩耗性と耐熱性を持つSKD材は、高い加工精度を実現します。たとえば、自動車や金型製造においてSKD材は欠かせない素材とされており、これらの分野での穴あけ加工に不可欠です。しかしながら、設定ミスや刃具の選択ミスなどによりトラブルが生じる場合もあります。具体的には、刃先の摩耗が早かったり、加工面にバリが発生したりといった問題が挙げられます。これらの問題に対処するためには、適切な刃具選定、切削条件の最適化、冷却剤の利用といった対策が効果的です。加工条件を適切に管理することで、SKD材の穴あけフライス加工はより精度高く、効率的に行えるようになるのです。
9. SKD材を活用した先進的成形加工技術
SKD材を使った穴あけフライス加工は、高い精度と効率性を要求される工程です。この加工においては、SKD材の硬さと耐熱性が重要な役割を果たしています。例えば、金型の製造においてSKD材は頻繁に使用される材料であり、精密な穿孔を行う際には、適切な切削工具と加工パラメータの選定が不可欠です。具体的には、SKD材の硬度に合わせた刃先の材質選びや、切削速度、送り速度、クーラントの使用等が挙げられます。これらの条件を最適化することで、材料の発熱を抑えつつ、寿命を伸ばしながらも細かく複雑な形状の穴あけが可能になります。結論として、SKD材を用いた穴あけフライス加工は、正確な工程設計と適切な工具選択が成功の鍵となり、これを実現することで、産業界における付加価値の高い製品製造に貢献しています。
まとめ
SKD材を使用した穴あけフライス加工は、高硬度の材料の加工に適しています。適切な切削速度や刃先形状を選定することが重要です。また、適切な切削液や工具の冷却方法を選ぶことで、加工精度を高めることができます。プロフェッショナルのアドバイスを参考に、適切な工具と工程を選定し、安全かつ効率的な加工を行いましょう。
【加工技術】SKD材の穴あけにフライス加工を用いるメリットとは?
穴あけ作業において、SKD材の利用は一般的に高い品質と耐久性をもたらします。さらに、これにフライス加工を組み合わせることで、さまざまな利点が生まれます。SKD材を使用し、フライス加工を用いることでどのようなメリットがあるのか、それを解説します。
1. SKD 穴あけ フライス加工の基礎
SKD材の穴あけにフライス加工を用いるメリットは大きく分けて、精度の向上、作業時間の短縮、および工具の耐久性の向上です。まず、フライス加工は非常に高い精度で穴を開けることが可能で、特にSKD材のような硬質材料でも、均一で滑らかな穴の表面を実現できます。次に、フライス加工機は一度に複数の穴を加工することができ、工程が複雑な穴あけ作業でも効率的に対応することができるため、作業時間を大幅に削減することができます。さらに、フライスのカッターは高硬度で設計されているため、SKD材のような硬い材料を加工しても摩耗しにくく、長期間にわたって使用することができ、コストパフォーマンスにも優れています。このように、SKD材の穴あけにフライス加工を選ぶことは、高い加工品質を実現し、加工効率を向上させ、かつコストを抑えるという、多角的なメリットがあります。
2. SKD11の切削加工の重要ポイント
SKD材における穴あけ作業にフライス加工を用いることは、多くのメリットがあると言えます。まず、フライス加工は高精度な加工が可能で、SKD材の硬度にも関わらず精密な穴の仕上げを実現します。例えば、一般的なドリル加工では生じやすいバリが少なく、仕上がりがきれいという利点があります。さらに、フライス加工では複雑な形状の穴や大きな直径の穴をあける際にも均一な品質を保つことができ、ドリル加工と比較しても工具の摩耗が少なく済むため、コストパフォーマンスも優れています。最後に、フライス加工による穴あけは加工速度が速く、大量生産にも対応可能であるため、生産効率も大幅に向上します。これらの点から、SKD材の穴あけにはフライス加工が適していると結論づけられます。
3. 炭素工具鋼の切削加工概要
SKD材の穴あけにおいて、フライス加工を用いることは多くのメリットがあります。まず、フライス加工は、高い精度と複雑な形状の穴あけが可能であり、SKD材のような硬度の高い材料でも安定して加工することができます。例えば、通常のドリル加工では難しい形状の穴や、深い穴もフライス加工だと比較的容易に作成することが可能です。これにより、製品の品質を向上させることができるだけでなく、工具の耐久性も高まります。さらに、フライス加工は切削スピードの向上にも寄与し、生産効率のアップが期待できます。結論として、SKD材にフライス加工を適用することは、加工の質を高め、生産性を向上させるための有効な手段であると言えるでしょう。
4. SKD11を用いた研削加工の比較分析
SKD材を用いた穴あけにフライス加工が選ばれる理由には、複数のメリットがあります。まず、フライス加工は高い精度と仕上がりの良さが特徴で、SKD材のような硬質の材料を加工する際にも均一な穴あけが可能です。また、複雑な形状や大きなサイズの穴あけにも対応でき、加工の柔軟性が高い点も大きな利点です。例えば、金型製作におけるSKD材への多様な穴形状の加工は、フライス加工ならではの技術で実現ができます。さらに、切削速度の調整が容易であり、生産性の向上にも寄与するため、コストパフォーマンスにも優れています。これらの利点から、SKD材の穴あけにはフライス加工が好適とされ、多くの現場で採用されています。
5. SKD11鋼のフライス加工部品の特徴
SKD材におけるフライス加工を活用した穴あけは、加工精度と効率の面で注目されています。この加工技術を用いることで、SKD材特有の硬度と耐摩耗性に対応した穴あけが可能となります。例えば、金型製造などで求められる微細な穴や複雑な形状の穴も、フライス加工を利用することで高精度に仕上げることができます。また、フライス加工は、一度のセットアップで多軸制御を用いた複雑な動きを実現し、一連の穴あけ加工を効率良く行うことが可能です。これにより作業時間の短縮が図れるだけでなく、製作コストの削減にもつながります。最終的には、フライス加工はSKD材の穴あけにおいて高い精度と生産効率の向上を実現し、加工コストの削減にも寄与します。
6. 高硬度鋼SKDの切削加工テクニック
SKD材の穴あけにフライス加工を用いるメリットは、精度と効率の両面で優れている点にあります。SKD材は高硬度であるため、従来のドリル加工では摩耗や熱影響による精度の低下が問題となりました。しかし、フライス加工はカッターの刃先が連続して材料に接触することで、均一にチップを削り取ることが可能です。このため、切削熱が分散され、材料への熱ダメージが抑えられ、加工精度が向上します。例えば、航空宇宙産業におけるエンジン部品などの精密な穴あけ加工が要求される場面では、フライス加工による利点が顕著に現れます。結果として、SKD材の穴あけにフライス加工を採用することは、耐久性と高品質を保ちつつ生産性を高めるのに役立ちます。
7. SKD 穴あけ フライス加工の応用事例
SKD材に穴あけ加工を施す際にフライス加工を採用することには大きなメリットがあります。SKDは耐摩耗性や熱処理後の硬さが特徴的な工具鋼で、従来の穿孔方法では工具の摩耗が激しく効率が低下してしまうことがしばしばありました。しかし、フライス加工を用いることで、SKDの硬さを生かしつつ、精度の高い穴あけが可能となります。例えば、フライス加工では多様なカッター形状を選択でき、複雑な形状の穴あけや大径の穴も正確に加工できるため、製品の多様化に対応することができます。加えて、フライス加工は一度に多量のチップを排出できるため、作業効率が向上し生産性の高い加工を期待できるのです。結果として、SKD材に対するフライス加工は加工精度や効率、経済性の面で優れ、現代の製造業における穴あけ加工の方法として推奨されています。
8. SKD 穴あけ フライス加工に関するよくある質問
SKD材における穴あけにフライス加工を選択することには、明確なメリットがあります。フライス加工を用いることで、SKD材の硬さに起因するドリル加工の問題点を大幅に軽減します。具体的には、フライス加工は切削抵抗が小さいため、加工時の摩耗を減らし、工具の寿命を延ばす効果があるのです。また、高い精度と滑らかな仕上がりの穴を実現できる点も大きなメリットと言えるでしょう。さらに、従来のドリルによる方法と比較して、フライス加工では複雑な形状や大きな穴の加工も容易になります。これらの理由から、SKD材の加工においてはフライス加工が穴あけの手段として非常に有効であり、最終的な製品品質の向上にも寄与します。
まとめ
SKD材のフライス加工は、高硬度であるため一般的なドリルでは穴を開けるのが難しいが、フライス加工を用いることで効率的に穴をあけることが可能です。また、フライス加工により精密な穴あけが実現できます。SKD材の特性を活かし、フライス加工を利用することで高品質な加工が可能となります。
プロフェッショナルが解説!SKD材を使った穴あけフライス加工の基本
あなたは工作機械に興味を持っていますか?または新しい技術とその応用について学びたいと考えていますか?本記事は、プロフェッショナルによるSKD材を使った穴あけフライス加工の解説です。SKD材を使った穴あけフライス加工の基本から応用までを学び、新たな知識と技術を得ることができるでしょう。工作機械やフライス加工に興味がある方、技術の向上を目指す方にとって、この記事はきっと興味深いものとなるでしょう。
1. SKD 穴あけ フライス加工の概要
SKD材を使用した穴あけフライス加工は、工業製品を製作する際に不可欠な技術の一つです。この加工技術によって、硬質で耐摩耗性に優れたSKD材でも、精密な穴を効率よく開けることが可能になります。例えば、金型の製造において、SKD材を使った部品はその高い耐久性から頻繁に使用されますが、これらの部品に必要な精密な穴を開けるには特殊な工具と技術が要求されます。フライス加工機を使用して行われるこの工程は、正確な位置決めと適切な速度設定が極めて重要で、加工後の仕上がりが製品の品質を左右するため、細部にわたる注意が求められます。最終的には、SKD材を使った穴あけフライス加工は、耐久性と精度を要求される製品には欠かせない工程であるという結論に至ります。このような加工技術の向上は、製品の品質向上に直結し、結果として日本の工業製品の国際競争力を高めることにも寄与しています。
2. 合金工具鋼(SKS・SKD・SKT)の特徴と用途
SKD材を使用した穴あけフライス加工は、その精度と効率性から多くの製造現場で基本とされています。SKD材は優れた耐摩耗性と硬度を持つため、工具としての寿命が長く、精密な加工が可能です。例えば、金型の製造において、SKD材から削り出された部品は、耐久性と品質の向上に大きく寄与します。また、穴あけ加工においても、SKD材を使うことで、一定の深さや形状を正確に再現することが可能となります。これは、摩耗しにくい特性があるためで、例として自動車部品の生産において、その精度が高く評価されています。最終的にSKD材を使った穴あけフライス加工は、耐久性と精密性が求められる場面での重要な選択肢となるのです。
3. SKD11の特性と熱処理による硬度の変化
SKD材を使用した穴あけフライス加工は、その優れた耐摩耗性と精度の高い加工により、産業界で広く採用されています。SKD材は特に硬度が高く、耐摩耗性に優れているため、金型製作などの分野での使用に適しております。例えば、SKD11は加熱処理により硬度を調整することが可能で、熱処理後は60HRC以上の硬度を持つことができるため、穿孔や切削工程での優れた性能を発揮します。しかし、この高硬度が加工時の課題ともなるため、適切な工具選びや加工条件の設定が重要となります。最終的には、SKD材の特性を十分に理解し、適した熱処理を施すことで、精度の高い穴あけフライス加工を行うことが可能となり、製品の品質向上に繋がります。
4. 特殊鋼の規格と成分の詳細解説
特殊鋼、特にSKD材を使った穴あけフライス加工は、精密な作業を要求される工程です。この加工手法が注目されているのは、SKD材の高硬度と耐摩耗性による長寿命が期待できるためです。例えば、金型製造における穴あけ加工では、SKD材を使用することで、高い精度と品質が保たれる穴が可能となります。金型の長期にわたる使用が求められる場合、SKD材のような強靭な材料を用いることは非常に有効です。また、フライス加工においても、SKD材はその耐久性から刃具の摩耗を抑え、精度の高い加工を継続的に実現しています。したがって、精密な穴あけが必要な場合、SKD材を用いたフライス加工は最適な選択と言えます。加工技術の進歩と共に、今後もSKD材を使用した高度な加工の需要はさらに高まるでしょう。
5. エラストマーブレンド率とシップリサイクルシステムの環境適合性
SKD材を用いた穴あけフライス加工は、精密な工業製品製作において不可欠です。SKD材は、その耐摩耗性や硬度が高いため、工具の磨耗を抑制し、長期間安定した加工精度を保つことができます。例えば、自動車産業や金型産業では、SKD材を使用して高精度の部品や金型を製造しています。これらの業界で求められる高い耐久性と精度は、SKD材によって達成されるのです。しかし、その硬さゆえに加工方法には特別な配慮が必要であり、適切な工具選びと加工条件の設定が成功の鍵となります。穴あけフライス加工で優れた結果を得るためには、SKD材の特性を理解し、それに見合った加工技術の選択が不可欠です。結論として、SKD材を使用した穴あけフライス加工は、選択される工具と技術によって、その効率と品質が大きく変わるため、プロフェッショナルによる解説が極めて重要であると言えます。
6. SKD11の硬度、成分、規格に関する総合情報
SKD材を用いた穴あけフライス加工は、精密な工業製品を生み出すための基本技術です。SKD材とは、高硬度で耐摩耗性に優れた鋼の一種であり、工具鋼として多くの産業で利用されています。特に、穴あけフライス加工ではその耐久性が要求されるため、SKD材の使用が選ばれるのです。例えば、金型の製造においては、細かい部品の穴開けにSKD材が使われることが多く、その正確な加工が製品の品質を大きく左右します。加工の際には、SKD材の硬度や成分を考慮した適切な工具選びや冷却方法が重要となります。このような専門知識を持つプロフェッショナルによる解説は、製品の品質向上に寄与するだけでなく、生産効率の向上にも繋がるため、業界内で非常に重要視されています。
7. SKD材の穴あけフライス加工における注意点とテクニック
SKD材を用いた穴あけフライス加工は、金型や工具製作において非常に重要な工程です。SKD材は耐摩耗性や硬度が高いため、通常の加工方法では加工が困難とされています。しかし、適切な工具選定と加工パラメータの設定により、精度の高い加工が可能となります。
特に、高品質なフライスを利用することで、SKD材の硬度にも関わらず、滑らかな加工面を実現できます。また、冷却剤の適切な使用は、工具の摩耗を減少させて、加工精度を維持するためにも必須です。実際の加工現場では、フライスの回転速度や送り速度などのパラメータを細かく調整し、材質の特性に応じた加工を行っています。
結論として、SKD材の穴あけフライス加工では、適切な工具選定と冷却剤の使用、パラメータ設定の最適化が成功の鍵を握ります。これらの基本を理解し実践することで、耐摩耗性に優れたSKD材でも、高い精度と滑らかな仕上がりの穴あけ加工が可能になるのです。
8. SKD 穴あけ フライス加工の最新技術とトレンド
SKD材を使用した穴あけフライス加工は、精密さと耐久性が求められる多くの産業で重宝されています。特に、SKD材はその硬度と耐摩耗性に優れ、工具寿命を延ばすことができるため、高いコストパフォーマンスを実現します。例えば、自動車産業においては、エンジン部品などの加工にSKD材を仕様した工具が使用され、精密かつ効率的な生産を実現しています。このようにSKD材を使った加工技術は、その利点を生かして広く応用されており、今後も加工精度や効率の向上を目指す動きが活発に行われることでしょう。
9. SKD 穴あけ フライス加工に関するよくある質問と回答
SKD材を使った穴あけフライス加工は、精密な製品製作に不可欠です。この加工方法は、硬度が高く、耐摩耗性に優れたSKD材に適しており、難削材を扱う際の基本中の基本とされています。そのため、安定した加工精度を得るためには、適切な工具選びと加工パラメータが重要です。例えば、SKD材の硬さに対応するために、超硬合金やコーティングされた工具が推奨されます。また、切削速度や送り速度も材質に合わせて調整する必要があります。実際の加工例として、金型のコアやキャビティの穿孔において、SKD材を使った穴あけフライス加工は一般的に採用されています。最適な工具と正確な設定で、SKD材は高い加工効率と優れた仕上がりを実現します。結論として、SKD材を用いた穴あけフライス加工は、適切な知識をもって臨めば、精度の高い製品を効率よく生産することが可能になります。
まとめ
SKD材を使った穴あけフライス加工は、高硬度であるため工具の選定が重要です。適切な切削条件を選び、十分な冷却・潤滑を行うことが加工のキモです。また、切削時には適切な刃先形状や進給量を選ぶことで、効率的な穴あけが可能となります。プロの技術と正しい機械設定をマスターすることで、高品質な穴あけ加工を実現しましょう。
プロフェッショナルが解説!SKD材を使った穴あけフライス加工の基本
穴あけフライス加工は、金属加工において重要な工程の一つです。本記事では、プロフェッショナルが解説する、SKD材を使った穴あけフライス加工の基本についてご紹介します。SKD材や加工方法についての理解が深まることで、より効率的かつ品質の高い加工が可能となるでしょう。穴あけフライス加工の基本について知りたい方や、SKD材を使った加工に興味がある方にとって、この記事は貴重な情報源となることでしょう。
1. SKD 穴あけ フライス加工の概要
SKD材を使った穴あけフライス加工は、精度と耐久性が要求される分野で重要な技術です。この加工には専門的な知識が必要であり、プロフェッショナルによる正確な操作が求められます。なぜならSKD材は炭素鋼や合金鋼を超える硬度を持つため、加工時には特別な工具選びや条件設定が不可欠だからです。例えば、適切な工具の選択では、硬質コーティングされたドリルやカーバイド製のエンドミルなどが挙げられます。また、切削速度や送り速度、冷却液の使用など、細部にわたる配慮が必要です。実際の例として、高硬度材料専用のフライスを使用した穴あけでは、切削抵抗を減らすために低い送り速度を採用することが一般的です。このように、専門家の知識を活かした正確な加工は、SKD材を用いた製品の品質を保つ上で不可欠と言えるでしょう。
2. SKD11鋼CNCフライス加工の基礎知識
SKD材を用いた穴あけフライス加工は精密な工業製品の製造に不可欠な工程であり、特にSKD11鋼の加工には高い専門知識が求められます。SKD11は耐摩耗性や耐熱性に優れ、金型などによく使われる鋼材です。これらの特性からSKD11鋼の穴あけには、専用の工具や条件設定が重要となってきます。例えば、適切な切削速度や冷却方法を選定することは、精度を保ちつつ工具の寿命を延ばすために不可欠です。また、SKD材の硬度に応じたドリルの選択も品質の向上を左右します。穴あけフライス加工は、こうした様々な要素を総合して最適な加工方法を見極めることが、長期的にもコスト効率の良い生産を実現する鍵となります。
3. 高張力鋼板(超ハイテン)の成形加工技術
SKD材を用いた穴あけフライス加工は、精密な部品製造に欠かせない重要な技術です。SKD材は耐摩耗性に優れ、特に金型などの工具材料に使われることが多いため、加工時の精度が求められます。この加工の基本は、適切な工具の選定と切削条件の設定にあります。例えば、材質に合わせたドリルやエンドミルの選択、切削速度や送り速度の調整が必須です。加工例を挙げると、小さい穴から大きな穴まで、異なるサイズや形状の穴あけには、それぞれに合うフライスカッターを用い、精度を保ちながら加工を行います。すると、耐久性と品質を保った部品を効率良く製造できるのです。結論として、SKD材を使った穴あけフライス加工は、適切な工具選定と条件設定により、高品質な製品製造に不可欠であることが理解できます。
4. 機械加工で扱う主要材料とその特性
SKD材を使用した穴あけフライス加工は、精密な加工が求められる場面で広く採用されています。SKD材は耐摩耗性や耐熱性に優れた特性を持っており、そのためドリルやエンドミルなどの切削工具の摩耗を抑えながら、長時間の加工に耐えうることが可能です。たとえば金型産業では、SKD材を使って複雑な形状の穴を加工することは日常茶飯事です。穴あけ加工では、材料の硬さに合わせた切削条件を設定する必要があり、SKD材の場合はその耐性の高さから、高い切削速度を維持しながらも細かな加工が要求されます。このようにして、SKD材はその優れた特性を活かしながら、多岐にわたる産業でのニーズに応え続けています。まとめると、SKD材の穴あけフライス加工は耐摩耗性や耐熱性が求められる高度な加工に不可欠であり、正確な切削条件の設定により、高品質な加工結果を得られるのです。
5. 長野県の特色ある加工技術を持つ企業の紹介
長野県は独自の伝統技術を持つ企業が多く存在し、特色ある加工技術で注目されています。それらの中でも、SKD材を使った穴あけフライス加工は重要な位置を占めています。SKD材は特殊工具鋼として知られ、優れた耐摩耗性と硬さを持つため、産業機械や自動車部品などの精密加工に適しています。このSKD材を使用した穴あけフライス加工では、材料の特性を理解した上で適切な切削速度や冷却方法を選ぶことが重要です。長野県には、このSKD材を駆使して独自の穴あけフライス加工技術を開発し、高品質な製品を提供している企業が存在します。例えば、精密な軸受けやエンジン部品を製造している企業などが挙げられます。これらの企業の技術力は、長野県の産業を支える基盤となっており、加工技術の進歩に大きく寄与しています。このように、SKD材を用いた穴あけフライス加工は、長野県特有の精密加工技術として、他の地域との差別化を図り、地域産業の更なる発展に寄与しています。
6. 材料の特殊成形加工技術と最新の研究動向
SKD材を使った穴あけフライス加工は、金属加工業界において非常に重要な技術です。この技術の基本を理解することは、高精度な加工を実現するために不可欠です。SKD材とは、耐摩耗性に優れた工具鋼の一種であり、その堅牢さから多くの産業で使用されています。穴あけフライス加工では、SKD材の硬さを考慮した専用の工具が必要であり、適切な切削条件を選定することが肝心です。例えば、適切な工具の選択や切削速度の調節により、効率的で精密な加工が可能になります。加工条件を間違えると、工具の摩耗が早まったり、加工物が破損する恐れがあります。したがって、正しい知識と技術がなければならないのです。この技術をマスターすることで、製品の品質を向上させ、製造コストを削減することができます。
まとめ
SKD材を使った穴あけフライス加工は、高硬度であるため加工には専用の切削工具が必要です。高速度での加工が可能であり、適切な冷却装置を使用することで品質を保つことができます。さらに、適切な切削条件を設定することで、高い精度の穴あけ加工を実現することができます。プロフェッショナルの指導のもと、正確な穴あけ加工を行うことで、高品質な製品を生産することが可能です。
穴あけ加工の王道!SKDフライス加工で求められる精度とは?
SKDフライス加工は、現代の製造業界で欠かせない技術の一つです。穴あけ加工においても、その精度は非常に重要です。しかし、その精度を求められる理由や具体的な要件は理解しにくいかもしれません。この記事では、SKDフライス加工における穴あけ加工の王道について掘り下げ、求められる精度やその重要性について解説します。加工技術に興味のある方や穴あけ加工の精度を向上させたい方は、是非ご覧ください。
Introduction
SKDフライス加工は穴あけ加工の中でも高精度が求められる分野です。特に、精度の要求される工業製品が多い日本では、SKDフライス加工の需要は高く、その理由にはいくつかのポイントがあります。まず、絶対的な精度の確保は、部品の互換性を保つ上で非常に重要であり、これによって組立ての際の手間が省け、生産効率が向上します。具体例としては、自動車や航空機の部品に見られるように、一貫した品質と正確な寸法が求められる場面では、SKDフライス加工が重宝されます。さらに、耐久性にも大きく寄与し、完成した製品の信頼性を高める要因となっています。したがって、精度を極めた穴あけ加工が求められるなかで、SKDフライス加工はその王道を行く技術と言えるでしょう。
1. SKD 穴あけ フライス加工の基本
SKDフライス加工は、機械部品製造において不可欠な技術であり、その精度は極めて高いレベルが求められます。フライス加工における穴あけ作業は、寸法精度や表面粗さといった品質が製品の性能に直結するため、その精度管理は製造現場において重要なポイントとなっています。具体的な例としては、自動車部品や精密機械のギアなど、微細ながらも高い耐久性を要する部品でSKDフライス加工が活用されています。こうした部品では、数マイクロメートル単位での誤差も許されないため、SKDフライスでの穴あけ加工は厳密な品質基準に従って行われます。結論として、SKDフライス加工で要求される精度は極めて高く、製品の信頼性を保証するためには、この高い水準を維持することが必須です。
2. マシニング加工とフライス加工の違い
SKDフライス加工は、穴あけ加工の分野で高い精度が要求される理由として、その信頼性と効率性が挙げられます。SKDとは特殊鋼の一種であり、耐摩耗性や強度が高いため、工具に用いられることが多いです。このSKDを使ってフライス加工を行う場合、精度が重要視されるのは、製品の品質や機能性を決定づけるためです。例えば、自動車業界では部品の寸法精度が極めて重要であり、わずかな誤差も許されません。SKDフライス加工によって、こうした高い要求を満たすことができるのです。また、耐久性の向上によりメンテナンスの頻度を低減し、コスト削減にも寄与します。したがって、SKDフライス加工で必要とされる精度は、産業全体の生産効率と品質向上に直結していると言えるでしょう。
3. 精度要求の見直しとコストダウン
SKDフライス加工は、その高精度さから穴あけ加工の最適解として広く認識されています。SKD加工において重要なのは、製品の品質を決定づける精度の高さです。特に、金型や機械部品などの製造において、ミクロン単位の公差で要求されることが一般的です。例えば、自動車産業におけるエンジン部品の加工などは、非常に厳しい寸法精度が求められる場合が多く、SKDフライス加工がその精度要求を満たす上で選ばれる理由となっています。しかしながら、この高精度を保ちつつコストを抑えることは、製造業者にとって大きな挑戦です。最新のCNC技術を使い、より効率的かつ経済的な方法で精度を守りながら加工を行うことが求められています。結論として、SKDフライス加工は精度が求められる穴あけ加工の分野において、その精度とコストのバランスに注意しつつ選択されるべき方法です。
4. 旋盤加工とSKD フライス加工の違い
SKDフライス加工が穴あけ加工で重宝されるのには明確な理由があります。この加工方法は、素材へのダメージを最小限に抑えつつ、高精度の穴を開けることが可能です。具体的には、SKDフライス加工で作成する穴は、その滑らかな表面と均一な寸法が求められます。例えば、精密機械の部品製作において、わずかな誤差も許されない状況下では、この高精度な加工技術が不可欠です。さらに、複雑な形状や狭いスペースの加工にも対応できる柔軟性を持っており、様々な産業でのニーズに応えることが可能です。結論として、SKDフライス加工が求められる精度は、極めて高いレベルであり、多岐にわたる用途において、精密かつ効率的な加工を実現するための王道技術であると言えるでしょう。
5. アルミニウム合金のSKD 穴あけ加工と切削剤の関係
穴あけ加工の中でも特に品質が求められるのがSKDフライス加工です。加工面の精度は製品の品質を大きく左右し、特に精密機械部品や自動車部品などの製造において重要視されます。SKDフライス加工で期待される精度は、公差±0.01mm程度と非常に高いレベルです。これは、紙の厚みがおよそ0.1mmであることを考えると、紙の十分の一の厚さの範囲で加工する必要があることを意味します。実際の製品例を見ても、自動車のエンジン部品や航空機の部品など、高い耐久性と信頼性が求められる分野で幅広く採用されています。これらの部品は、微細な寸法誤差が大きな問題を引き起こす可能性があるため、SKDフライス加工による高い精度が不可欠なのです。結論として、SKDフライス加工はその高い精度により、多くの産業分野で必須の技術とされており、精密な穴あけ加工を実現するためには、極めて緻密な工程管理が求められます。
6. 高硬度鋼のSKD 切削加工のコツ
穴あけ加工の分野で求められる精度の高さはSKDフライス加工においても重要です。SKD加工とは、工具鋼の一種であるSKD11やSKD61といった高硬度の鋼を用いた加工のことで、耐摩耗性や耐熱性が求められる部品作りに不可欠です。これらの材質を使い、一定の厚みを持つ板に複数の穴を空ける際には、穴のサイズや位置の精度が極めて重要になります。例えば、自動車や航空機の部品などでは、穴の位置が微妙にズレるだけで組み立てが不可能になったり、安全性に影響を及ぼす可能性があるため、高い精度が要求されます。そのため、SKDフライス加工では、加工機の精度はもちろん、刃物の選定、冷却剤の使用といった加工条件が徹底され、精度の高い加工が実現されています。穴あけ加工においてSKDフライス加工が王道たる所以は、このような高精度な成果を出すための細部にわたる注意とテクニックから成るのです。
7. SKD 穴あけ フライス加工の応用事例
SKDフライス加工において求められる精度は非常に高い。これは、工業製品の部品としての機能や耐久性を確保するためには、厳密な寸法と形状が求められるからである。例えば、自動車のエンジン部品や航空機のタービンブレードなど、要求される精度が非常に厳しい製品にはSKDフライス加工が不可欠であり、これにより、製品の寿命を延ばすと同時に安全性を高めることができる。穴あけ加工の一環として、SKDフライス加工は、その精密さから多くの製造業界で重宝されており、特に高精度が要求される機械の部品製造においては欠かせない技術の一つである。結論として、SKDフライス加工は製品品質の向上に直結し、産業全体の信頼性維持に寄与していると言える。
8. SKD 穴あけ フライス加工の将来展望
SKDフライス加工は、その高い精度が求められる加工方法の一つです。この加工技術は、特に要求される寸法精度や形状精度が非常に高く、工業製品の品質向上に不可欠です。例えば、自動車のエンジン部品や航空機の部品に用いられることが多く、ミクロン単位の精度が要求される場合があります。これらの部品が正確でなければ、製品全体の性能に影響を及ぼす可能性があるため、SKD加工には高い精度が求められるのです。また、耐摩耗性や熱処理による硬度の向上など、材料への要求も厳しいため、高品質なフライス加工を実現するためには、優れた技術と適切な工具選択が不可欠です。これにより、SKDフライス加工は精密な穴あけ加工の王道としての地位を確立し、今後も多くの分野での需要が見込まれます。
まとめ
SKDフライス加工は、穴あけ加工の王道として広く利用されています。この加工方法では、高い精度が求められます。穴あけの位置や深さ、直径など、厳密な仕様に応えるためには、適切な工具選びや工程管理が欠かせません。また、加工対象の素材によっても異なるため、それぞれの特性を理解し、適した操作を行うことが重要です。
【工業加工】SKDでの穴あけ・フライス加工のコツと注意点
加工業界でSKDでの穴あけやフライス加工を行う際、初心者から上級者まで必要とされるコツや注意点についてご紹介します。SKD加工は精密さが求められるため、正しい技術と知識が重要です。何をすべきか、どのように進めるべきか、この記事では初心者の方々にも分かりやすく解説します。加工技術を向上させ、より効果的で正確な作業を行いたい方は、ぜひお読みください。
1. SKD 穴あけ加工の基本
SKDでの穴あけ加工を行う際には、正確さと品質が求められます。SKDは工具鋼として広く利用されており、その耐摩耗性と硬度の高さから穴あけには特有の工夫が必要です。まず、適切なドリルの選択が重要であり、SKDの硬さに対応した超硬ドリルやコーティングドリルの使用が望ましいです。次に、適切な切削速度と送り速度の設定が成功のカギを握ります。速度が遅すぎると作業効率が落ち、速すぎると工具の磨耗や破断につながります。また、冷却剤の使用は、摩擦熱による影響を最小限に抑え、加工精度の向上に役立ちます。フライス加工では、カッターの選定にも注意が必要で、SKDの硬さに合わせた刃先の形状や材質を選ぶことが大切です。最後に、こまめな工具点検と交換を行い、常に良好な加工状態を保つことが求められます。これらのポイントを押さえることで、SKDにおける穴あけ・フライス加工の品質と効率を高めることができます。
2. 高硬度材料SKDにおける穴あけのテクニック
高硬度の金属材料であるSKDの加工においては、正確で丁寧な穴あけ・フライス加工が不可欠です。加工における最大のポイントは、適切な工具の選択と加工パラメータの調整にあります。SKD加工専用の工具を使用することで、材料の硬さに対応した切削が可能になり、摩耗や工具の破損リスクも軽減されます。特に、穴あけ加工では、スピンドルスピードやフィードレートを材質に合わせて慎重に設定する必要があります。例えば、小径のドリルビットを使用する際は高速回転を避け、切削油を適切に供給することで、熱の発生を抑え、仕上がりの精度を高めることができます。フライス加工では、切削抵抗を考慮した刃の数や形状を選定し、不規則な負荷がかからないようにすることも必要です。最終的には、これらのコツと注意点を踏まえた加工技術によって、SKDの穴あけ・フライス加工の質を高めることができるのです。
3. SKD11の穴あけ加工条件の選定
SKDの穴あけやフライス加工には特有のコツと注意点があります。SKDを使用した加工の際、耐摩耗性や硬度が高いため、工具への負担が非常に大きいです。したがって、切削工具の材質選びや刃の状態を常にチェックし、専用の硬質コーティングを施した工具の使用が推奨されます。さらに、SKD加工においては低切削速度と高トルクが必要であり、熱管理も重要です。適切な冷却液を使用し、加工中の熱を適切に逃がすことで、切削精度を保ちながら工具の寿命を延ばすことができます。例として、フライス加工の際には一貫した送り速度を保ちつつ、過度の加圧を避けることが重要です。最終的には、これらのコツと注意点を踏まえた上で、実際の加工条件を細かく調整することにより、SKDでの高品質な穴あけ・フライス加工が実現します。
4. 異なる種類のSKD 穴あけ加工手法
工業加工においてSKDでの穴あけやフライス加工は精密さと効率が求められる技術です。穴あけ加工では、事前に材質の硬さや切削速度を考慮することが重要であり、フライス加工では刃の選定や進行方向に注意が必要です。例えば、SKD材は硬いため通常の鋼材を加工する時よりも低い速度で加工する必要があり、また、耐熱性の高い刃を選ぶことが切削精度を保つコツです。加工時には、刃の摩耗を常にチェックし、必要に応じて交換することで、品質の高い加工を継続することが可能です。フライス加工では、刃の進行方向が反時計回りか時計周りかによっても仕上がりに差が出るため、目的に応じて適切な方法を選択することが大切です。最終的に、これらのコツと注意点を守ることで、SKDにおける穴あけ・フライス加工の品質を向上させることができます。
5. 熱処理済みSKD材の穴あけ加工
SKD材の穴あけ加工は、正確で美しい仕上がりを求められる工業加工の一環です。この作業のポイントは、熱処理によって硬度が増したSKD材を使用する際の適切な切削条件の選定にあります。まず、工具はSKD材の硬さに対応できるよう、超硬合金やコバルトハイスなどの耐久性の高いものを選ぶべきです。また、切削速度は適度に抑え、冷却液を適切に使用することが重要です。特に、熱処理後の材料はその硬さから、加工時の熱の影響を受けやすいため、冷却液を使用して熱を逃がしながら加工することが、品質を保つ秘訣と言えます。実際の事例として、冷却液を充分に使用しなかったことで工具の摩耗が早まり、加工精度が落ちたという報告は数多くあります。ですから、穴あけ加工においては冷却管理を徹底し、定期的な工具の点検を行うことが大切です。これらを守ることで、SKD材の穴あけ加工は効率よく、かつ高品質な結果を出すことが可能になります。
6. SKD 細穴加工の特別な考慮事項
SKDにおける穴あけ及びフライス加工は、耐摩耗性や強度などの特性を持つ材料を使用しているため、適切な加工方法と注意が必要です。処理を行う際は、適切な切削工具を選び、切削速度や送り速度を材料の硬さに応じて調整することが重要です。例えば、硬度が高い材料では低い切削速度を用いると工具の摩耗を減らすことができます。また、冷却液を適切に使用することで、切削面の仕上がりを良くし、加工時の熱ダメージを防ぐことができます。特にSKD材では、加工時に発生する熱により硬化する特性があるため、冷却には十分注意を払わなければなりません。最適な加工条件の下で加工を行うことにより、製品の品質を維持しながら効率的に作業を進めることができるのです。
7. SKD 穴あけ加工のトラブルシューティング
SKDでの穴あけやフライス加工は高精度な工業製品を生産する際に不可欠です。これらの加工の成功の鍵は、適切な工具選びと加工条件の調整にあります。特にSKD材は硬度が高いため、工具の摩耗が激しくなる傾向があります。効率的な加工のためには、耐摩耗性に優れたコーティングつきのドリルやエンドミルを使用すると良いでしょう。また、SKD材の加工には、低速での切削や、冷却液を適量使用するなど、熱による影響を抑える工夫も必要です。こういった専門的な加工を行う際には、加工前に材料の特性を理解し、ツールパスの設計を丁寧に行うことが重要です。最終的には、これらのポイントに注意しながら慎重に加工を進めることが、SKD加工の品質を決めると言えます。
8. SKD フライス加工の基礎と応用
SKDでの穴あけ・フライス加工は、金属加工における基本中の基本です。適切な加工がなされた場合、製品の精度や強度を大きく向上させることができます。そのためには、適切な工具選びと加工条件が重要です。具体的には、SKD材での作業には高速度鋼や超硬合金のドリルやエンドミルが適しており、切削速度や送り速度、切り込み量を材質や形状に応じて適切に設定する必要があります。また、切削油の使用は、摩擦熱を軽減し、工具の寿命を延ばす上でも重要です。例えば、硬い材質であるSKD11では、フライス加工する際には特に冷却効果の高い切削油を使用すると良いでしょう。最終的には、これらのポイントを押さえることで、SKDでの穴あけ・フライス加工の精度を高めることが可能です。
まとめ
SKDを使用した穴あけやフライス加工においては、適切な工具選びや切削条件の設定が重要です。適切な切削油を使用し、適正な切削速度や切削深さを設定することで、加工精度を向上させることができます。また、穴あけにおいては適切な冷却を行うことで工具の寿命を延ばすことができます。加工時の振動や刃先の摩耗にも注意が必要です。